
Плазменная обработка материалов
..pdf3. Получение навыков исследовательской работы по определению оптимальных режимов плазменной сварки проникающей дугой цветных металлов и высоколегированных сплавов.
Методика проведения работы
Основными параметрами режима, определяющими качество формирования шва при сварке проникающей дугой, являются: ток сжатой дуги Iсв; расход плазмообразующего газа Qп; диаметр плазмообразующего сопла dс; скорость сварки vсв; свободная длина сжатой дуги hс.и.
Исследования проводятся на образцах из различных материалов (табл. 9). Размеры образцов: толщина 5; 6; 8 и 10 мм, ширина не менее 50 мм, длина не менее 150 мм. Производится предварительная сборка стыковых швов с зазором (0 +0,5) мм.
Для проведения исследований используется стенд для плазменной сварки, скомпонованный на базе станка наплавочного; плазмотроны для сварки на прямой и обратной полярности конструкции кафедры сварочного производства и технологии конструкционных материалов Пермского государственного технического университета; источник питания сварочного тока типа ВДУ-505. В качестве плазмообразующего и защитного газов используется аргон.
|
|
Таблица 9 |
|
Образцы для сварки |
|
|
|
|
1 |
Алюминиевые сплавы |
АМг6, АМг5, АМц, Д16 |
2 |
Коррозионно-стойкие стали |
12Х18Н10Т |
3 |
Жаропрочные стали |
09Х16Н4Б |
4 |
Сплавы на никелевой основе |
ХН67ВМТЮ |
5 |
Титановые сплавы |
ВТ1, ОТ4 |
Порядок проведения работы
1. Подготавливается стенд плазменной сварки к работе:
–включается пускатель системы управления стенда;
–включается пускатель источника питания сварочного тока;
–включается система подачи воды в систему управления плазмотрона и система подачи газа, устанавливается нужный расход, контролируемый соответствующими ротаметрами.
2. На рабочий стол укладывается собранный под сварку образец.
101
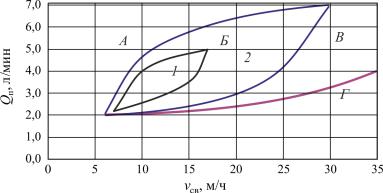
3.Устанавливаются требуемые параметры режима сварки (см. табл. 7, 8), включается сварочный ток и перемещение сварочной головки, при фиксированных режимах сварки меняется один из параметров. Проводится наблюдение за формированием шва.
4.После заварки шва производится оценка качества формирования шва, замеры геометрических параметров шва. Результаты фиксируются
вжурнале наблюдений.
5.Далее исследования проводятся последовательно по каждому параметру при поддержании остальных параметров постоянными.
6.Проводится анализ полученных результатов, строятся графики областей формирования сварных швов, составляются выводы по проведенным исследованиям (например, рис. 53).
Рис. 53. Области формирования сварного шва (сплав ЭП202, δ = 8 мм): 1 – сборка стыка без зазора; 2 – сборка стыка с зазором; А – выплавление, Б – стабильное формирование; В – рез; Г – непровар; Iсв = 200 А,
h = 4 мм, dc = 3,5 мм
Техника безопасности
1.Работа на стенде для плазменной сварки производится под контролем ведущего преподавателя или учебного мастера.
2.Наблюдение за зоной сварки в процессе работы производится через сварочный светофильтр.
3.Работа с образцами после сварки производится после их полного остывания.
4.Сварка производится при включенной вытяжной вентиляции.
5.При включении сварки высоковольтным высокочастотным разрядом не допускается касание плазмотрона.
102
Контрольные вопросы
1.Особенности процесса плазменной сварки проникающей дугой.
2.Особенности взаимодействия сжатой дуги с материалом при плазменной сварке проникающей дугой.
3.Возможные механизмы разрушения жидкой ванны при плазменной сварке проникающей дугой.
4.Основные параметры режима при плазменной сварке проникающей дугой.
5.Характерные возможные области формирования сварных швов при плазменной сварке проникающей дугой.
6.Какие свойства металлов оказывают влияние на стабильность процесса формирования шваприплазменной сварке проникающейдугой?
7.Преимущества плазменной сварки проникающей дугой.
8.Чем определяется качество формирования сварного шва при плазменной сварке проникающей дугой?
9.Что описывают уравнения Лапласа и Юнга при рассмотрении процесса плазменной сварки проникающей дугой?
10.Для каких толщин возможно применение плазменной сварки проникающей дугой?
11.Чем отличается плазменная сварка проникающей дугой алюминиевых и жаропрочных сплавов на никелевой основе?
5.3. НИЗКОТЕМПЕРАТУРНОЕ МОДЕЛИРОВАНИЕ ПРОЦЕССА ПЛАЗМЕННОЙ СВАРКИ ПРОНИКАЮЩЕЙ ДУГОЙ
Непосредственно наблюдать процессы, происходящие в сварочной ванне при плазменной сварке проникающей дугой, не представляется возможным. Математическое моделирование сварочных процессов, позволяющее выявить влияние технологических факторов на свойства шва, требует выяснения физических явлений, происходящих всварочной ванне.
В связи с этим представляет интерес физическое моделирование процесса плазменной сварки проникающей дугой.
5.3.1. Оценка возможности физического моделирования процесса плазменной сварки проникающей дугой
Для максимального сходства модели с реальным процессом необходимо обеспечить подобие явлений, происходящих в газовой ижидкой фазах(геометрическое, кинетическое, динамическое итепловое подобие).
103
Вопросам низкотемпературного моделирования процессов сварки плавлением высококонцентрированными источниками нагрева посвящен ряд исследований. Однако в доступной литературе нет сведений о возможности низкотемпературного моделирования процесса плазменной сварки проникающей дугой. Это объясняется необходимостью соблюдения целого ряда условий подобия в газовой и жидкой фазе, обу-
словленной сложностью изучаемого процесса: |
|
|
|
|||||||||||
Нуссельта – Nu = αl |
; Прандтля – Pr = |
ν |
; |
|
|
|
||||||||
|
|
|
|
|||||||||||
|
|
|
|
|
λ |
|
|
|
|
a |
|
|
|
|
Пекле – Pe = |
vl |
; (Re Pr); Рейнольдса – Re = |
vl |
; |
||||||||||
|
|
ν |
||||||||||||
|
|
|
a |
|
|
|
|
|
|
|
|
|
||
Фруда – Fr = |
v2 |
; Стурхала – Sh = |
vt |
; |
|
|
|
|||||||
gl |
|
|
|
|
||||||||||
|
|
|
|
|
l |
|
|
|
||||||
|
|
|
ρ 2 |
|
|
|
|
p |
|
|
|
|||
Вебера – We = |
v l |
; Эйлера – Eu = |
|
; |
|
|
||||||||
σ |
ρ v2 |
|
|
|||||||||||
Бонда – Bo = ρ q l 2/σ ж и ряда других, |
|
|
|
|||||||||||
где α |
– коэффициент теплоотдачи; |
|
|
|
||||||||||
l – характерный размер; |
|
|
|
|||||||||||
λ |
– коэффициент теплопроводности; |
|
|
|
||||||||||
ν |
– кинематический коэффициент вязкости; |
|
a– коэффициент температуропроводности;
v– скорость;
g– ускорение свободного падения;
t– время;
ρ– плотность;
p– давление;
σ ж – поверхностное натяжение.
Обеспечение равенства всех критериев подобия реального процесса и модели является невыполнимой задачей, однако при определенных допущениях задача может быть упрощена. Сжатая дуга может рассматриваться как затопленная неизотермическая турбулентная струя. При выборе материала модели необходимо обеспечение основного требования – равенства числа Pe жидкости – натуры и модели. Установлено, что числа Pe для парафина и алюминия приближенно равны. Моделирование процесса плазменной сварки проникающей дугой алюминиевых сплавов возможно осуществлять воздействием струи горячего воздуха
104
на модель из парафина. В процессе моделирования плазменной сварки проникающей дугой должны соблюдаться следующие условия: воздействие струи горячего воздуха на материал модели при определенной скорости перемещения должно вызывать сквозное проплавление с образованием отверстия в нижней части полости кратера, образование и стабильное удержание жидкой ванны (в хвостовой части) до ее затвердевания. Следует добавить, что сама возможность стабильного ведения процесса сквозного проплавления модели струей горячего воздуха со стабильным удержанием жидкой ванны говорит об одинаковости физических процессов, происходящих в сварочной ванне, при плазменной сварке проникающей дугой и на модели.
В табл. 10 представлены основные теплофизические свойства парафина.
|
|
|
|
Таблица 10 |
|
Теплофизические свойства парафина |
|
||
|
|
|
|
|
|
Температура, °С |
|
ρ , кг/м3 |
µ, Па·с |
плавления |
кипения |
перехода |
при Тпл +50 °С |
при Тпл |
56 |
416 |
53 |
758,5 |
0,22755 |
Из условия равенства критериев подобия были определены геометрические параметры модели, параметры газовой струи и скорость относительного перемещения модели и сопла.
Целью проведения экспериментов является изучение, с помощью физического моделирования, качественных закономерностей явлений, происходящих в сварочной ванне при изменении основных параметров процесса плазменной сварки проникающей дугой.
Порядок проведения экспериментов следующий: струей горячего газа добивались сквозного проплавления модели и проводили наблюдение процессов, происходящих в полости кратера.
Модель шва представляет собой кювету, состоящую из двух кварцевых пластин, собранных при помощи зажимов, заполненную материалом модели.
Для визуализации движения расплава по полости кратера и в хвостовой части ванны используется угольная пудра, нанесенная на поверхность модели.
Процессы, происходящие в полости кратера, могут непосредственно наблюдаться исследователями ификсироваться видеоилифотокамерой.
105
Угол наклона передней стенки полости кратера (фронта плавления), длина полости, диаметр отверстия в корневой части кратера, форма передней стенки жидкой ванны являются параметрами, которые характеризуют особенности протекания процессов в полости кратера. В экспериментах появляется возможность определить зависимость этих параметров от изменения параметров моделирования.
5.3.2. Моделирование процесса плазменной сварки проникающей дугой
Проведенные эксперименты показывают, что струя воздействует на полость кратера не симметрично – на фронте плавления (рис. 54), плавление материала и унос расплава с фронта плавления происходит непрерывно. Полость кратера в установившемся режиме отличается стабильностью формы и размеров. Угол наклона фронта плавления однозначно характеризует форму и размеры полости кратера. В хвостовую часть ванны расплав также поступает непрерывно. Изменение расхода газа или изменение скорости перемещения кюветы «сварки» ведет к изменению угла наклона фронта плавления (см. рис. 54) и соответствующим изменениям формы и размеров полости кратера (рост расхода газа ведет к возрастанию угла наклона фронта плавления, аналогично происходящему при уменьшении «скорости сварки»). Увеличение расхода газа (снижение «скорости сварки») вызывает ускорение плавления материала и унос расплава в хвостовую часть, при этом происходит рост угла наклона фронта плавления α до 80° (рис. 54, а). Форма полости кратера приближается к цилиндрической. При достижении критических значений угла наклона α = 76…80° начинается сброс расплава через сквозное отверстие (рис. 54, б), снижение и прекращение перемещения расплава по боковым стенкам в хвостовую часть, происходит разрыв жидкой ванны и начинается режим реза. В районе режимов стабильного существования полости кратера при α = 55…75° (рис. 54, в, г, д), форма полости кратера имеет характерную конусообразную конфигурацию
сискривленной (S-образной) передней стенкой жидкой ванны. Расплав
сфронта плавления по боковым стенкам поступает в хвостовую часть, образуя жидкую ванну, которая удерживается силами поверхностного натяжения и давлением, создаваемым струей в полости кратера. Плав-
ление материала и унос расплава наиболее интенсивно происходит в зоне приложения максимального давления струи.
106
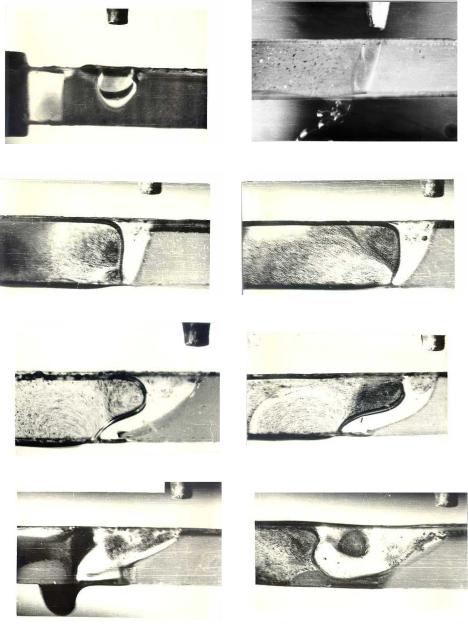
а |
б |
в |
г |
д |
е |
ж |
з |
Рис. 54. Изменение полости кратера в зависимости от скорости перемещении кюветы: а – v = 0 мм/с; б – v = 0,10 мм/с; в – v = 0,15 мм/с;
г– v = 0,40 мм/с; д – v = 0,50 мм/с; е – v = 0,60 мм/с; ж – v = 0,65 мм/с;
з– v = 0,70 мм/с
107
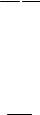
При моделировании наблюдались визуально и зафиксированы на видео- и фотоснимках вихревые движения расплава в хвостовой части ванны (см. рис. 54). Наблюдения показали, что из тонкого слоя угольной пудры, нанесенной на поверхность модели, частицы, пройдя через полость кратера, попадают в вихревые движения в жидкой ванне, удерживаются некоторое время в них, вращаясь, а затем равномерно заполняют весь объем жидкой ванны. В жидкой ванне существует два вихря: в верхней части ванны и в нижней части вблизи сквозного отверстия. Угловая скорость (оценивалась по движению частиц угольной пыли) вихрей находится в пределах 6,28–31,4 с–1.
Источником движения расплава в жидкой ванне следует считать наличие касательных напряжений на передней стенке ванны, возникающих при воздействии на нее струи газа. Интенсивность вихревого движения можно оценить по формуле
ω= µг du ,
µж dh
где µг – вязкость воздуха при 150 °С, µг = 22·10–6 Па·с.
Среднюю скорость струи можно определить, зная расход Qc, как
v = Qc .
πr 2
При изменении Qс по условиям моделирования скорость газового потока находится в пределах u = 2,7…10,8 м/с. Учитывая, что максимальная скорость струи umax = 2u, и приняв толщину пограничного слоя равной половине ширины полости кратера, можно рассчитать угловую скорость вихревого движения расплава: ω = 5…21 с–1. При радиусе вихря 1–2 мм линейная скорость перемещения v = 0,15…2,5 м/мин, что
в15–20 раз выше скорости «сварки». Размеры и направления вихрей определяются формой полости кратера. При больших углах наклона фронта плавления (65–75°) полость кратера имеет характерную узкую воронкообразную форму, верхний вихрь имеет значительно большие размеры, чем нижний (см. рис. 54, в). Направления вращения вихрей
вэтом случае одинаковы и совпадают на передней стенке жидкой ванны с направлением струи, сбрасываемой через отверстие в корне шва. При уменьшении угла наклона (50–60°) фронта плавления полость кратера расширяется, происходит выравнивание размеров вихрей, направления
108
вращения вихрей при этом остаются такими же, как и в предыдущем случае (см. рис. 54, г).
При дальнейшем уменьшении угла наклона фронта плавления (до 40–45°) (полость кратера характеризуется широкой верхней частью с нависанием жидкой ванны) происходит увеличение размеров вихря
внижней части и уменьшение в верхней части ванны, причем направление вращения вихря в верхней части изменяется на противоположное (рис. 54, д, е). В зависимости от соотношения размеров струи и полости кратера растекание струи по полости кратера имеет особенности. При узкой полости кратера разворот периферийной части струи происходит
вверхнем объеме полости кратера (в приповерхностном слое) и по полости кратера часть струи с расходом Qк распространяется как стесненная струя. С уменьшением угла наклона фронта плавления (расширением приемной части полости) зона разворота струи заглубляется в полость кратера, при этом происходит перераспределение расходов: Qк – уменьшается, Qоб – возрастает. Мощность потока, индуцирующего
вихрь в верхней части ванны, падает, уменьшается и размер вихря в верхней части ванны. При дальнейшем уменьшении угла наклона фронта плавления и расширении приемной части полости кратера зона разворота струи находится в глубине полости кратера при этом значительно возрастает мощность обратного потока струи, вследствие чего происходит изменение направления вращения верхнего вихря (на передней стенке жидкой ванны вверх). В зоне взаимодействия верхнего и нижнего вихря потоки расплава имеют одинаковое направление движения, что способствует увеличению размеров нижнего вихря.
Дальнейшее уменьшение угла фронта плавления (до значений меньше критического) приводит к закрытию сквозного отверстия и переходу к режиму без сквозного проплавления. Газовый поток, обтекая полость кратера, как полуограниченная струя, индуцирует в хвостовой части ванны гидродинамический вихрь с направлением вращения, совпадающим с направлением движения газовой струи на передней стенке жидкой ванны (рис. 54, з).
Характер движения расплава в хвостовой части сварочной ванны определяет степень однородности металла шва, механизм насыщения жидкого металла газами, оказывает влияние на перенос тепла и особенности кристаллизации металла. Наличие интенсивного вихревого движения расплава, выявленного при моделировании, объясняет высокую однородность металла шва иотсутствие порприсварке проникающейдугой.
109

ЛАБОРАТОРНАЯ РАБОТА № 5 НИЗКОТЕМПЕРАТУРНОЕ МОДЕЛИРОВАНИЕ ПЛАЗМЕННОЙ СВАРКИ ПРОНИКАЮЩЕЙ ДУГОЙ
Цели работы:
1.Ознакомление с теоретическими и практическими основами физического моделирования сложных технологических процессов на примере низкотемпературного моделирования плазменной сварки проникающей дугой цветных металлов и высоколегированных сплавов.
2.Получение навыков практической работы с оборудованием для моделирования плазменной сварки проникающей дугой.
3. Визуальное наблюдение динамики процессов, происходящих в полости кратера и в жидкой ванне при моделировании плазменной сварки проникающей дугой.
Методика проведения работы
Основными параметрами режима являются геометрические параметры модели, параметры газовой струи и скорость относительного перемещения модели и сопла («сварки») (табл. 11).
Таблица 11
Условия проведения экспериментов низкотемпературного моделирования плазменной сварки проникающей дугой*
Наименование |
|
|
Параметры |
|
|
v, |
Q, |
Угол наклона |
Угол наклона |
||
|
см/мин |
л/мин |
сопла, град |
модели, град |
|
Влияние расхода газа на пара- |
1,6 |
0,5–2 |
90 |
0 |
|
метры полости кратера |
|||||
|
|
|
|
||
Влияние скорости сварки |
0–6 |
1,2 |
90 |
0 |
|
Влияние «угла» наклона сопла |
0–6 |
1,2 |
75; 115 |
0 |
|
Влияние «угла» наклона модели |
0–6 |
1,2 |
90 |
±8 |
*dс = 1,5…2 мм; h = 1,5…3 мм; толщина модели δ = 6 мм; температура газовой струи 150–180 °С.
Для проведения исследований используется установка для моделирования процесса плазменной сварки проникающей дугой, представленная на рис. 55.
110