
Плазменная обработка материалов
..pdf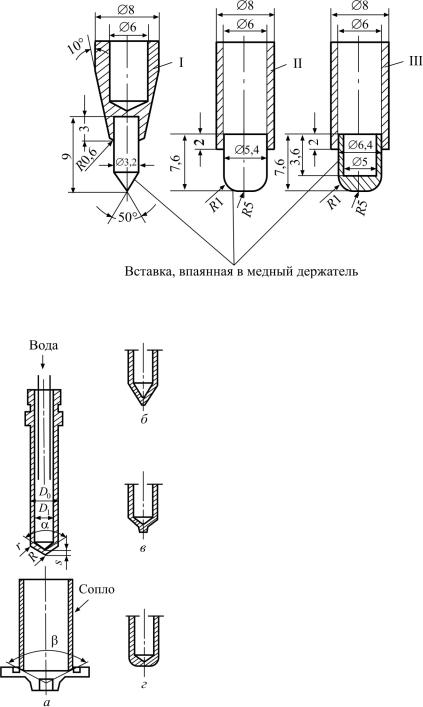
Рис. 13. Конструкции электродов–анодов из вольфрама
Рис. 14. Конструкции медных электродов–анодов
и токе возбуждения 50 А они разрушались меньше, чем за 23 мин, а при токе 200 А – за 2–3 мин. Это объясняется недостаточной теплопроводностью вольфрама.
Эксперименты, проведенные с медными анодами (теплопроводность в 3 раза выше, чем у вольфрама) различной конструкции (рис. 14), показали, что конструкции а и б при токе 200 А и токе возбуждения 50 А быстро разрушались. На электроде на рис. 14, в активное пятно располагалось на кромке электрода, что приводило к аварийной работе плазмотрона (двойной дуге).
Электрод конструкции 14, г при токе 200 А имел ресурс 300 мин при 60 возбуждениях дуги. Считается, что ростресурсаанодовсвязанс увеличением размеров электродов и улучшением их охлаждения. Предложен анодный узел,
31
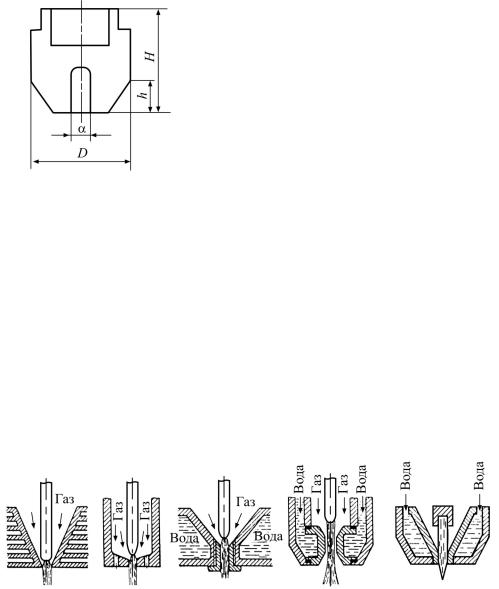
состоящий из медной водоохлаждаемой державки и активной вольфрамовой вставки (рис. 15). Диаметр державки 12; 17 и 25 мм, диаметр вставки 6; 6 и 8 мм соответственно. Высокая стойкость анода обеспечивается качественным соединением меди с вольфрамом и системой водяного охлаждения. Наилучшие результаты достигались при осадке расплавленной меди на вольфрамовую вставку. Стойкость таких анодов достигает до 100–300 ч при рабочем токе до 400 А при 100–500 включениях.
Плазмообразующие сопла воспринимают большие тепловые нагрузки и поэтому требуют тщательного конструктивного оформления. Опыт эксплуатации показал, что наилучшим материалом для изготовления сопел является медь высокой чистоты (марки М0, М1), обладающая высокой теплопроводностью и сравнительно невысокой стоимостью. Армирование стенок сопла теплостойкими материалами приводит к уменьшению срока его службы из-за снижения теплопроводности. Сопла малоамперных и ручных плазменных горелок могут иметь естественное или газовое охлаждение (рис. 16, а, б).
а |
б |
в |
г |
д |
Рис. 16. Конструкции плазмообразующих сопел.
В большинстве случаев применяется водяное охлаждение сопел, при этом участок сопла, контактирующий с плазменным столбом, может быть сменным (рис. 16, в, г, д).
32
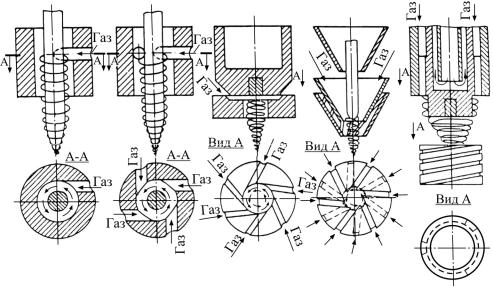
Узел завихрения рабочего газа определяет качество стабилизации столба сжатой дуги. Конструктивные варианты узлов завихрения можно разделить на группы, представленные на рис. 17.
Функции завихрителя может выполнять корпус плазмотрона (рис. 17, а, б), керамическая шайба, помещенная у входа в сопло (рис. 17, в), само сопло (рис. 17, г), при этом можно значительно сократить длину канала сопла, заменив большую часть его кольцами стабилизирующего газа, вращающимися вокруг столба дуги (очень сложное и трудоемкое в изготовлении), и сам электрод плазмотрона, на наружной поверхности которого выполняется винтовая нарезка (рис. 17, д).
а |
б |
в |
г |
д |
Рис. 17. Конструкции узлов завихрения плазмообразующего газа
Изоляторы. Плазмообразующее сопло и электродный узел должны быть электрически изолированы друг от друга. Одним из условий стабильного горения дуги является точная центровка электрода и сопла при сборке плазмотрона. Функции механической связи электродного узла и плазмотрона, их точной взаимоцентровки и электрической изоляции выполняет изолятор. К материалу изолятора предъявляются разнообразные, а иногда и противоречивые требования:
33
–достаточная механическая прочность;
–высокая электрическая прочность, так как возбуждение дежурной дуги осуществляется с помощью высоковольтного высокочастотного разряда;
–термостойкость, так как части изолятора подвергаются тепловому и световому воздействию сжатой дуги;
–возможность механической обработки (например, режущими инструментами);
–герметичность, поскольку через изолятор могут проходить коммуникации плазмообразующего газа и водяной системы охлаждения.
Материалы, наиболее применимые для изготовления изоляторов плазмотронов, можно условно разделить на две группы: обрабатываемые на универсальном оборудовании из заготовок (прутки, листы)
иполучаемые с использованием специальной технологической оснастки (пресс-формы, заливочные формы).
К первой группе относятся фторопласт Ф-4, иногда капролон, эбонит; ко второй – эпоксидная смола холодного отверждения ЭД-5 с кремнийорганическим наполнителем, стеклонаполненные пресс-материалы типов АГ-4В, ДСВ, КМК-218, КПС и др., а также высокоглиноземистые керамические типа кристаллокорунд и 22ХС.
Из материалов первой группы изоляторы изготовляются на универсальном оборудовании (токарные, фрезерные, сверлильные станки)
имогут быть достаточно сложными. К недостаткам их можно отнести низкую технологичность процесса изготовления и невысокую термостойкость. Из материалов второй группы детали можно изготовлять достаточно простым способом с минимальной трудоемкостью и потерями материала. Недостатком является трудность обеспечения точности размеров и формы изолятора. Это объясняется наличием литейных конусов и уклонов, а также изменением коэффициента усадки у одного
итого же материала. В связи с этим в пресс-формах изготовляют простые детали, не требующие высокой точности. Применение перспективных керамических материалов сдерживается двумя причинами. Первая – большой разброс коэффициента усадки шликерной массы при спекании, что не позволяет получать детали выше пятого класса точности. Вторая причина – для изготовления керамических деталей требуется набор специального технологического оборудования (шаровые мельницы, машины шликерного литья, водородные печи для спекания), это снижает рентабельность при мелкосерийном производстве.
34
2.3. УСЛОВИЯ БЕЗАВАРИЙНОЙ РАБОТЫ ПЛАЗМОТРОНОВ
Стабильная работа плазмотронов обеспечивается при соблюдении определенных соотношений между геометрическими параметрами катода и плазмообразующего сопла. В плазмотронах дугу можно сжимать до определенного предела. При предельном значении тока для установленного диаметра сопла образуется «двойная», или каскадная, дуга, горящая между электродом и соплом и между соплом и изделием. Это явление связано с тем, что при увеличении тока и уменьшении диаметра сопла увеличивается падение напряжения в столбе дуги и одновременно уменьшается пограничный холодный слой газа у стенки сопла, благодаря чему повышается его электропроводность и создаются условия для электрического пробоя. Режим двойной дуги является аварийным, так как при этом нарушается формирование шва и разрушается сопло. Величину допустимого тока в зависимости от диаметра вольфрамового катода рекомендуется определять из следующего соотношения:
Iд = 67dк3/ 2 ,
где dк – диаметр катода, мм.
При токах более 100 А соотношение тока и диаметра катода предлагается следующее:
dк = 0, 0065Iд + 0, 7.
Вылет электрода из электрододержателя рекомендуется ограничивать в следующих пределах: dк ≤ l≤ 15 мм.
Диаметр плазмообразующего сопла не должен быть меньше диаметра катода– dс ≥ dк . Длина канала сопла не должна превышать диаметра
сопла lс ≤ dс для предельно допустимых токов. Величина предельного то-
ка для данного диаметра сопла зависит от состава и расхода плазмообразующего газа и длины сопла. Для lс ≈ dс при использовании аргона в ка-
чествеплазмообразующего газатокдуги
Iд ≈ (80...120)dс .
Такая величина тока устанавливается из условия отсутствия двойной дуги.
35
ЛАБОРАТОРНАЯ РАБОТА № 2 ИЗУЧЕНИЕ КОНСТРУКЦИЙ ДУГОВЫХ ПЛАЗМОТРОНОВ
Цели работы:
1.Изучить принципы классификации плазмотронов в зависимости от их назначения и особенностей конструкции.
2.Ознакомиться с конструктивными вариантами основных элементов плазмотронов в зависимости от их целевого назначения и материалами, применяемыми для изготовления плазмотронов.
3.Получить навыки конструирования плазмотронов различного назначения.
Порядок проведения работы
1.Студенту выдается реальный плазмотрон.
2.Производится разборка плазмотрона на главные узлы: электродный, сопловой, изолятор. Оценивается назначение плазмотрона.
3.Производится детальная разборка главных узлов плазмотрона (если таковая возможна). Проводится оценка устройства систем охлаждения и газоснабжения плазмотрона.
4.Вычерчивается эскиз плазмотрона с необходимыми разрезами
исечениями.
5.Составляется подробное описание конструкции плазмотрона
иотдельных его узлов, устройства систем охлаждения и газоснабжения. Проводится анализ преимуществ и недостатков устройства узлов плазмотрона и всей конструкции в целом.
6.Производится сборка плазмотрона.
Контрольные вопросы
1.Основы классификации плазмотронов.
2.Общие требования, предъявляемые к конструкции плазмотронов.
3.Основные узлы плазмотронов.
4.Способы стабилизации сжатой дуги.
5.Разновидности катодов плазмотронов, материалы катодов.
6.Конструкции анодов плазмотронов.
7.Устройство сопловых узлов плазмотронов.
8.Изоляторы, назначение, материалы изоляторов.
9.Системы охлаждения теплонагруженных узлов плазмотронов.
36
10.Системы газоснабжения плазмотронов.
11.Классификация плазмотронов по роду тока.
12.Классификация плазмотронов по плазмообразующей среде.
13.Плазмотроны для высокочастотных плазменных технологоий.
Список литературы
1. Эсибян Э.М. Плазменно-дуговая аппаратура. – Киев: Техника, 1971. – 164 с.
2.Донской А.В., Клубникин В.С. Электроплазменные процессы
иустановки в машиностроении. – Л.: Машиностроение, 1979. – 221 с.
3.Плазменно-дуговая технология в промышленном производстве / под ред. В.И. Макарова / ЦЭНДИСИ СССР. – М., 1991. – 183 с.
4.Щицын Ю.Д., Тыткин Ю.М. Компоновка плазмотронов на базе унифицированных узлов// Сварочное производство. – 1986. – №6. – С. 24.
37
3. ЯВЛЕНИЕ КАТОДНОЙ ОЧИСТКИ ПОВЕРХНОСТЕЙ ПРИ ПЛАЗМЕННОЙ ОБРАБОТКЕ МЕТАЛЛОВ НА ОБРАТНОЙ ПОЛЯРНОСТИ
Качество сварного и паяного соединения во многом определяется качеством подготовки поверхностей изделий. Поверхность металлов загрязнена средствами консервации, остатками смазочно-охлаждающих жидкостей, окалиной, адсорбированными газами и пр. Кроме того, легкие цветные металлы (Al, Mg) и их сплавы обладают специфическим отличием, затрудняющим процессы их сварки и пайки – наличием на поверхности прочной, тугоплавкой окисной пленки (например, Al2O3 имеет температуру плавления Тпл ≈ 2050 °C, а у алюминия Тпл ≈ 660 °С). Наличие такого окисла на свариваемых (паяемых) поверхностях затрудняет их смачивание жидким металлом (припоем), образование общей сварочной ванны и качественного сварного (паяного) соединения. Существует ряд способов удаления загрязнений и окисной пленки с рабочих поверхностей перед сваркой или пайкой: механические, химические, электрохимические, физические. Среди них флюсовый, абразивный, ультразвуковой, использование моющих и растворяющих средств, химическое травление, вакуумный, гальванический. Перечисленные способы очистки поверхностей имеют свои специфические недостатки. Общими для них являются высокая трудоемкость, значительная длительность процесса, сложность оборудования, загрязнение окружающей среды. Особенно недостатки таких способов очистки проявляются при обработке сложных изделий с использованием различных материалов и технологических операций. Кроме того, необходимо учитывать разнообразие загрязнителей изделий. Ими могут быть окисные пленки, масляные загрязнения, адсорбированная влага, технологические пленки (например, электронно-лучевое осаждение) и др.
При контакте очищенных поверхностей с атмосферой на них происходит быстрое повторное образование окисной пленки вследствие высокого сродства к O2 (кислороду). Поэтому удаление окисла предпочтительней проводить непосредственно в процессе сварки (пайки), а зону обработки необходимо защищать от окисления вновь, пока не произойдет образование соединения. Использование обратной поляр-
38
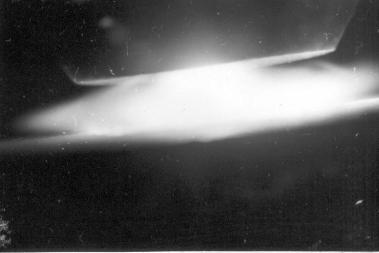
ности при плазменной обработке металлов дает такую возможность. На изделие воздействуют сжатой дугой обратной полярности (изделие при этом является катодом), зона обработки защищается подачей аргона через защитное сопло плазмотрона. За счет явления «катодной очистки» с поверхности изделия удаляются оксидные пленки и другие загрязнители.
3.1. МЕХАНИЗМ ПРОЦЕССА КАТОДНОГО РАСПЫЛЕНИЯ
До сих пор нет устоявшегося представления о природе процесса катодного распыления. Поверхность изделия при обработке дугой обратной полярности для большинства конструкционных металлов является «холодным катодом». Термин «холодный катод» принято применять к катодам из металлов, температура кипения которых ниже точки, при которой можно рассчитывать на заметную термоэлектронную эмиссию. К особенностям этих катодов относятся кратковременность существования катодных пятен, высокая плотность катодного тока, беспорядочное движение конца дуги по поверхности катода, а часто одновременное или последовательное существование нескольких катодных пятен. Скорость перемещения катодного пятна так высока, что визуально дуга имеет форму усеченного конуса между соплом плазмотрона и поверхностью изделия (рис. 18).
Рис. 18. Процесс катодной очистки при работе плазмотрона на обратной полярности
39
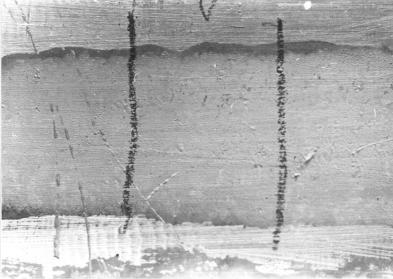
Ширина зоны движения катодных пятен (и ширина зоны катодной очистки) может превышать диаметр защитного сопла плазмотро-
на (рис. 19).
Рис. 19. Внешний вид очищенного слоя ( × 2)
До сих пор нет общепринятой теории катодных процессов на холодных катодах и механизма катодного распыления. Предположительно считается, что разрушение и удаление окисной пленки и загрязнений
взоне воздействия дуги обратной полярности происходит в результате эмиссии электронов и бомбардировки положительными ионами поверхности металла, при этом может протекать ряд процессов: вторичная электронная эмиссия, эмиссия отрицательных ионов и нейтральных атомов, отражение падающих ионов и распыление.
Эффективность катодного распыления существенно повышается при использовании в качестве защитного газа аргона и является незначительной при применении гелия.
Эмиссия электронов. Предполагается, что выход электронов с поверхности холодного катода может происходить вследствие электростатической эмиссии. Сильное электростатическое поле, необходимое для выхода, создается пространственным зарядом положительных ионов
взоне катодного падения потенциала. Величина электрического поля должна достигать порядка 106 В/см. Достоверных данных о наличии поля такой силы на сегодняшний день нет. Кроме того, при работе дуги
40