
Экология производства химических продуктов из углеводородов нефти и
..pdfРис. 60. Схема производства ароматических углеводородов из сжиженных неф тяных газов (сайклер-процесс фирм ЮОП и «Бритиш Петролеум»):
1 печи для |
подогрева |
сырья; 2 — наборные |
реакторы; |
3 — секция непрерывной регене |
|||||
рации |
катализатора; |
4 |
— сепаратор низкого |
давления; |
5 — компрессор; |
6 — секция раз |
|||
деления контактного |
газа; 7 — пентаноотгонная |
колонна; / — свежее сырье; I I — рецикл |
|||||||
сырья; |
I I I |
контактный газ; I V — контактный |
газ, |
содержащий водород |
и легкие угле |
||||
водороды; V |
— жидкие |
углеводороды; V I — горючий |
газ; V I I — водород; |
V ///— пентано |
|||||
вая фракция; |
I X — ароматические углеводороды на разделение |
|
наибольшее распространение получил фосфорнокислотный ката лизатор фирмы ЮОП (табл. 19). Главное преимущество про цесса фирмы ЮОП — отсутствие сточных вод и коррозии обо рудования, изготовленного в основном из углеродистой стали.
Разработанный в СССР процесс алкилирования бензола пропиленом в присутствии фосфорнокислотного катализатора характеризуется более низкими энергозатратами, чем в присут ствии хлорида алюминия. Это достигается использованием теп ла реакции для подогрева шихты, подаваемой на алкилирова ние, выделением более 50% возвратного бензола, дросселиро ванием, упрощением схемы разделения алкилата и отсутствием затрат на отпарку углеводородов из сточных вод и азеотропную осушку. Внедрение этого процесса определяется производством фосфорнокислотного катализатора.
Разработана новая технология с использованием раствори мых количеств хлорида алюминия в высокотемпературном про цессе алкилирования бензола пропиленом.
Научно-технический прогресс в производстве изопропилбен зола направлен на совершенствование действующих производств (снижение расходных норм по сырью, реагентам, энергозатра там, сокращение сточных вод и утилизация побочных продук тов), реконструкцию действующих производств и строительство новых с использованием гетерогенного фосфорнокислотного ка тализатора, разработку и внедрение нового высокотемператур-
Процесс |
Температу |
Давление, |
Соотношение |
Выход изопропил |
Примечания |
бензол : пропи |
|||||
|
ра, °С |
МПа |
лен |
бензола. % |
|
|
|
|
Катализатор А1С13 |
|
Жидкофазный в присутствии ге |
90—130 |
0,5 |
(3 -6 ) :1 |
|
терогенного комплекса |
на основе |
|
|
|
хлорида алюминия |
|
|
|
|
Высокотемпературный в |
присутст |
|
|
|
вии растворимого количества хло |
|
|
|
|
рида алюминия |
|
|
' |
|
|
|
|
Катализатор |
Н3РО4 |
Парофазный процесс: |
|
|
2,8—4,2 |
|
на носителе (фирма |
ЮОП) |
200—250 |
(4—6): 1 |
|
на силикагеле (ВНИИолефин) |
230 |
2,5 |
6:1 |
|
На носителе (ВНИИОС) |
200—240 |
3,4 |
— |
97 (на пропилен) В изопропилбензоле отсутствуют олефины, катализатор деалкилирует полиалкилбензолы, коррози
онная среда, наличие сточных вод t
99 (от теоретичеКатализатор используют одноского расчетного) кратно
91—-92 (на пропиОтсутствуют сточные воды и корлен), 36—97 (на розионная среда бензол)
—Конверсия пропилена (количест венная)
—Низкие энергозатраты
/ — подогреватель; 2 — |
реакторы; |
3 — секция предварительного подогрева; |
4 — колонна |
||
рекуперации бензола; |
5 — колонна |
рекуперации |
этилбензола; |
5 — колонна |
рекуперации |
днэтнлбензола; 7 — промывка остаточных газов; |
/ — этилен; |
// — свежий |
бензол; / / / — |
||
топливо; I V — вода; V |
— отходы на сгорание; V I |
— этилбензол |
|
|
ного процесса алкилирования бензола пропиленом в присутст вии растворимых количеств хлорида алюминия.
Этилбензол в СССР производят алкилированием бензола эти леном в присутствии хлорида алюминия по технологии, анало гичной двухфазному алкилированию бензола пропиленом. За рубежом получили развитие процессы высокотемпературного гомофазного алкилирования бензола этиленом в присутствии растворимых количеств хлорида алюминия (фирма «МонсантоЛуммус») и в присутствии цеолитного катализатора, промотированного фосфором (фирма «Мобил-Баджер»).
Процесс фирмы «Мобил-Баджер» осуществляется при тем пературе выше 270 °С (катализатор стабилен до 565 °С), давле нии около 2 МПа, соотношении бензол : этилен 6—7:1, объем ной скорости 3 ч-1; селективность по этилену 99% (рис. 61). Блок алкилирования может состоять из двух и более реакторов, работающих в режиме алкилирование — регенерация. Регене рацию проводят в азотно-воздушной среде для исключения из лишнего подъема температуры. Остаток из колонны выделения днэтнлбензола вместе с отходящими газами может обеспечить 60% потребности установки в топливе. Кроме того, 95% тепла, затрачиваемого на проведение процесса, регенерируется в виде пара. Этот процесс позволяет использовать низкоконцентриро ванную этиленовую фракцию, обеспечивает повышенный выход целевого продукта. Для него характерны низкая энергоемкость, обусловленная высокой степенью утилизации тепла, отсутствие коррозии и вредных выбросов в атмосферу.
Процесс фирмы «Монсанто-Луммус» — гомофазный, осуще ствляемый при 200 °С. Расход катализатора, сырья, энергоза
трат значительно сокращен, уменьшена коррозия оборудования; возможно использование низкоконцентрированной этиленовой фракции.
Процесс высокотемпературного газофазного алкилирования; бензола этиленом, разработанный ВНИИолефин, характеризу ется более высокими технико-экономическими показателями,, чем лучшее действующее в СССР производство по двухфазной, технологии. Конверсия этилена 99,6%, температура 200 °С, дав ление в алкилаторе 2,1 МПа, соотношение бензол : этилен равна 3:4, съем этилбензола с 1 м3 реакционного объема 400 кг. Ве дутся исследования по улучшению технико-экономических пока зателей действующих производств (двухфазный процесс в при сутствии хлорида алюминия), уменьшению образования побоч ных продуктов, их переработке и утилизации.
Полиалкилбензольная смола — отход производства этилбен зола, горючая жидкость темно-коричневого цвета. Примерный;
состав, |
% (масс.): ди'этилбензол — 20, |
триэтилбензол — 30^ |
высшие |
полиалкилбензолы и смолы — 50. |
На отдельных пред |
приятиях образуется до 75 кг на 1 т этилбензола. На выход, полиалкилбензольной смолы влияют чистота исходного сырья — этилена и бензола (отсутствие ацетиленовых, сернистых и дру гих вредных примесей), качество катализатора- - хлорида алю миния, а также режим алкилирования — температура и продол жительность пребывания в реакторе, соотношение бензол : эти лен.
Применение кондиционного сырья, совершенствование тех нологии процесса позволяют сократить образование смолы до 25 кг/т. На новых заводах она может быть сокращена до 15 кг.
Полиалкилбензольную смолу используют в качестве сырья для пиролиза (совместно с продуктами и отходами нефтепере работки, в общем объеме которых она составляет 1%) и сжи гают для получения водяного пара.
Шлам гидроксида алюминия или концентрированный раст
вор хлорида алюминия — отходы производства |
этилбензола.. |
Для удаления катализатора (хлорида алюминия) |
из продуктов |
алкилирования алкилат промывают водой. В зависимости от применяемой технологии переработки промывных вод из них. может быть выделен шлам гидроксида алюминия либо получен концентрированный раствор хлорида алюминия.
Шлам гидроксида алюминия можно использовать для полу чения строительных материалов — высокоглиноземистого цемен та, опудривателя для керамзита и расширяющей добавки для заделки швов железобетонных конструкций. Капитальные вло жения в создание установок выделения и сушки шлама при мощности установок по этилбензолу 300 тыс. т/год составляют примерно 1,7 млн. руб.
Концентрированный раствор хлорида алюминия рекомендо вано применять в качестве коагулянта в системах водоочистки, и водоподготовки.
Экономический эффект от использования промывных вод производства этилбензола для получения 25%-ного раствора хлорида алюминия на 1 т отхода — 100 руб.
4.4.2. Производство мономеров синтетического каучука
Бутадиен, изопрен и стирол — мономеры для получения синте
тических каучуков. Выработка их достигает 75—80%. от общего выпуска каучуков. Производство изопрена, бутадиена и стирола относится к крупнотоннажным. Мировая выработка стирола превышает выпуск бутадиена, так как стирол применяют и для получения крупнотоннажного пластика — полистирола.
Бутадиен в 'СССР получают из этанола, одно- и двухстадий ным дегидрированием я-бутана, выделением из газов пиролиза и окислительным дегидрированием я-бутиленов. Производство его энергоемко. Расход топливно-энергетических ресурсов на 1 т бутадиена при контактном разложении этилового спирта состав ляет 1,77 т у. т., двухстадийном дегидрировании я-бутана — 5,67; одностадийном дегидрировании я-бутана— 1,88, выделении из пиролизной фракции — 0,3 т у. т. Внедрение в производственном объединении «Нижнекамскнефтехим» окислительного дегидри рования позволяет экономить ежегодно 500 тыс. т топлива.
В 1991—2000 гг. производство бутадиена планируется раз вивать путем внедрения одностадийного дегидрирования я-бу тана под вакуумом с применением новых эффективных катали заторов (около 70% общего прироста вводимых мощностей), окислительного дегидрирования я-бутенов (18%), выделения из пиролизной фракции С4 (12%).
Изопрен в СССР производят двустадийным дегидрированием изопентана и из изобутилена и формальдегида. Расход топлив но-энергетических ресурсов в первом случае составляет 7,46—
9,04 т у. т. на |
1 |
т изопрена, во втором — 3,84 т у. т. |
Наиболее энергоемкая стадия в производстве изопрена из |
||
изобутилена |
и |
формальдегида — синтез диметилдиоксана. На |
установке мощностью 120 тыс. т целевого продукта в год на данную стадию приходится 51% общего энергопотребления; на стадию разложения диметилдиоксана — 38,8%; на стадию вы деления и очистки изопрена — около 10%.
Важнейшее направление снижения энергопотребления в про изводстве изопрена из формальдегида и изобутилена — внедре ние принципиально новой энергосберегающей технологии полу чения изопрена через метилбутандиол.
Обе реакции — синтез метилбутандиола и его дегидратация проходят в мягких условиях в жидкой фазе (температура 60— 120 °С, давление 0,6—1,5 МПа) с использованием гомогенного кислотного катализатора, который рециркулирует в процессе. Этот процесс по сравнению с получением изопрена через диметилдиоксан, характеризуется меньшим расходом сырья, позво ляет упростить аппаратурное оформление, устранить сложную
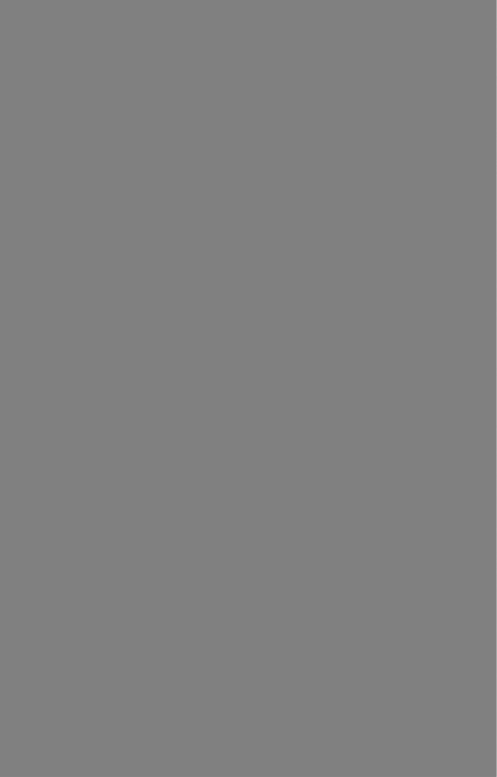

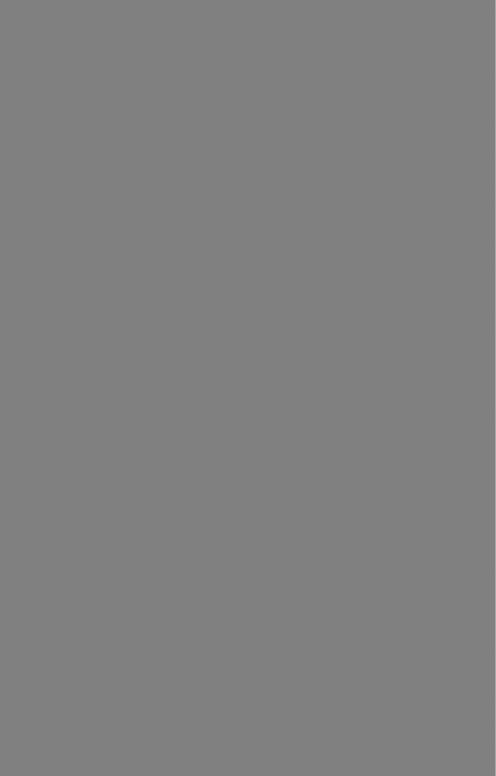
продукции, а ускоренный Выпуск новых продуктов дает значи
тельный экономический эффект без ухудшения экологическою обстановки.
Высокая стоимость ГТС по сравнению с традиционными ви дами технологического оборудования предопределила в миро вой практике внедрение более дешевых средств по сравнению- с ГТС — таких, как гибкие производственные модули или ячей
ки, являющиеся составными частями гибких технологических систем.
Примером ГТС в химической промышленности являются, многоассортиментные производства по выпуску целых классов, химических продуктов на базе унифицированных технологиче ских схем.
Такие схемы включают оборудование, позволяющее прово дить сульфирование, сульфохлорирование, нитрование, аммонолиз, щелочное плавление, каталитическое гидрирование, ал килирование и др. Большинство узлов могут быть общими при производстве всех продуктов, например узел каталитического гидрирования, узел фильтрации. Типовой узел каталитического гидрирования с пленочным движением гидрируемой жидкой фазы по стационарному слою катализатора, рециклом жидкой фазы через выносной теплообменник можно использовать при: переработке первичного и вторичного, сырья. Узел обладает до статочным запасом гибкости при изменении интенсивности ре цикла и давления, поэтому его можно использовать для произ водства многих продуктов. Он проверен в производстве изопро пилового спирта, тетрагидрофурана, фурилового спирта ю других веществ. Узлы подготовки сырья, а также выделения, очистки, упаковки готовых продуктов требуют более разнооб разного набора оборудования с меньшим коэффициентом ис пользования.
Для переработки отходов, различающихся по составу и ко личеству, можно использовать ГТС, создаваемые по блочно-мо дульному принципу.
В настоящее время при создании химико-технологических производств традиционным является подход, при котором опе рационными единицами являются аппараты.
Применение унифицированных технологических элементов*, стандартных и нестандартных модулей значительно упрощает разработку высокоэффективных ГТС путем создания новых комбинированных аппаратов, блоков, автоматизированных ком плексов.
* Элемент — устройство, несущее определенную функциональную нагруз ку (привод, форсунка, тарелка и т. д.). Модуль — автономное устройство, выполняющее определенные операции (фильтрующий аппарат, сушилка, вы парной аппарат). Блок — отдельная технологическая стадия производства^ состоящая из модулей комбинированных аппаратов. Автоматизированный технологический комплекс — компактная блочно-модульная установка.
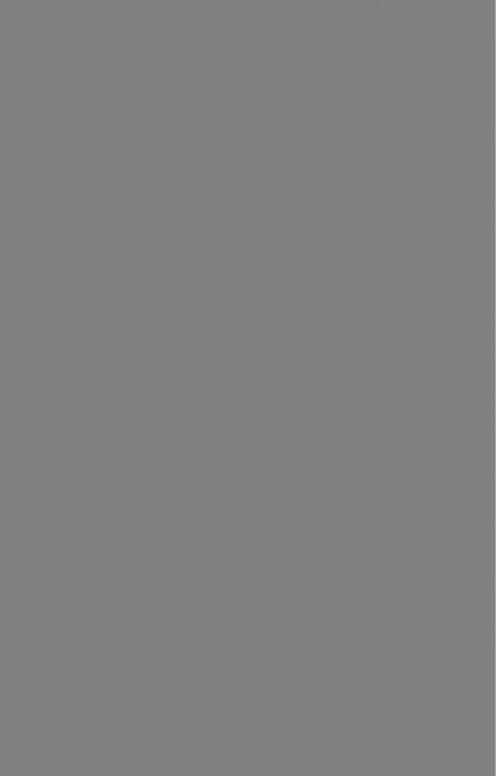