
Экология производства химических продуктов из углеводородов нефти и
..pdfпарафинов: 2 т на 1 т суммарных олефинов и 3—4 т на 1 т детергентной фракции олефинов Сю—Сю.
Каталитическое дегидрирование высших нормальных пара финов протекает селективно лишь при невысокой степени прев ращения сырья. Для выделения олефинов из смеси с парафинами требуются существенные капитальные вложения и повышенные эксплуатационные затраты.
Первые промышленные установки синтеза высших а-олефи- иов на основе этилена в присутствии алкилов алюминия были пущены в середине 60-х годов. Известны многочисленные раз работки как в СССР, так и за рубежом процессов олигомериза ции этилена. Реализация их создала предпосылки для создания и внедрения ряда новых процессов.
Выбор той или иной технологии получения высших олефи нов определяется требованиями к качеству сырья, изменением цен на этилен и «-парафины, усовершенствованиями, вносимыми в технологические процессы.
Комбинирование процессов димеризации пропилена и содимеризации этилена и пропилена с целью получения разветвлен ных олефинов позволит эффективно использовать побочные продукты реакции, уменьшить расходы сырья и реагентов (рис. 57).
Диспропорционирование смесей Сб—Сю и Сго, полученных при высокотемпературной олигомеризации этилена, позволяет повысить выход детергентных фракций олефинов Сю—Си. Вначале осуществляют изомеризацию двойной связи при 30— 50 °С, объемной скорости до 2 ч- 1 над калием и натрием, нане
сенными на активный оксид алюминия, а затем проводят дис пропорционирование над алюмомолибденовым катализатором (12% МоОз) при 150 °С, давлении 0,5—0,7 МПа, в растворите
ле— гексане. Степень превращения олефинов 60—70%, селек тивность 65—90%.
Промышленный процесс диспропорционирования высших олефинов осуществлен фирмой «Шелл». Содиспропорционированию подвергают фракции С6—Сю и Сго после изомеризации их во внутренние олефины. За один проход образуется 10—15% олефинов С4 —С)4. Углеводороды легче Сю й тяжелее Сю выде
ляют ректификацией и возвращают в производство. Небольшое количество олефинов Сг—С4 выводят из системы для поддержа
ния баланса. Получаемые олефины Сю—Си имеют достаточно высокую линейность. При общем содержании олефинов 99,5%' содержание линейных превышает 96%, содержание ароматичес ких углеводородов и сопряженных диолефинов — не более 0 ,1 %,
парафинов — не более 0,5%.
Комбинирование производств высших олефинов, включаю щих олигомеризацию этилена, изомеризацию и диспропорцио нирование олефинов, позволяет гибко реагировать на изменение потребностей в высших олефинах, например обеспечивать мак симальные выходы детергентной фракции.
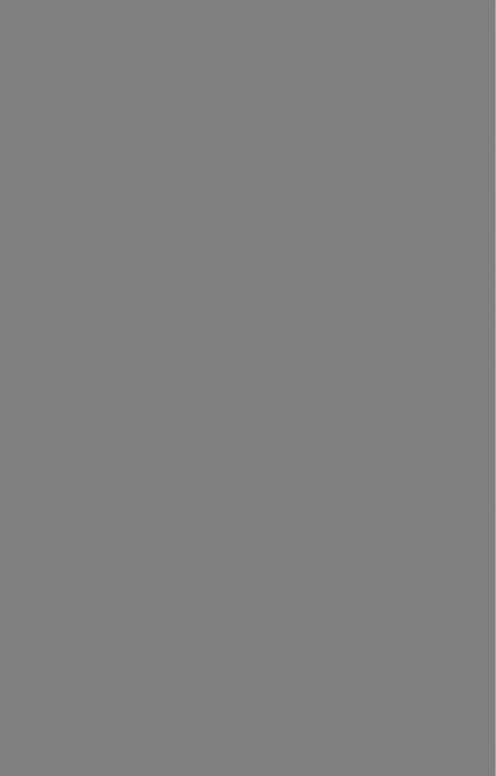
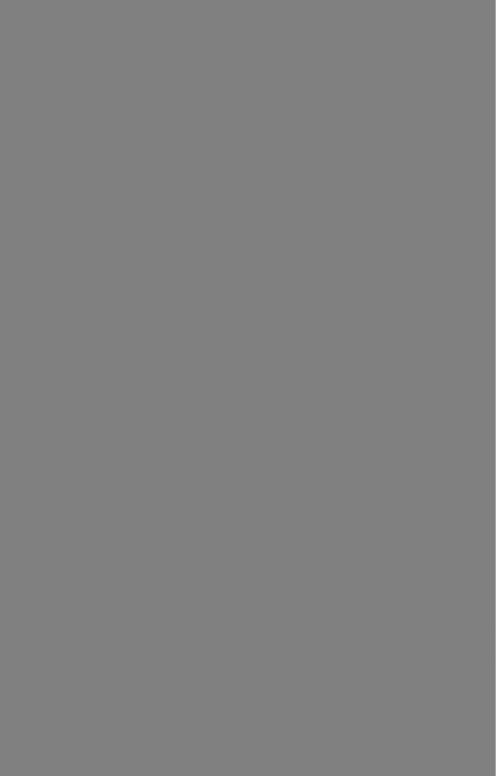
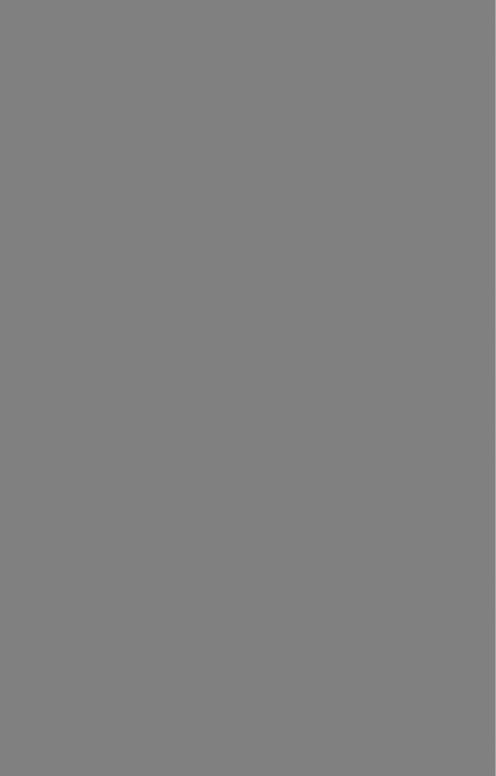
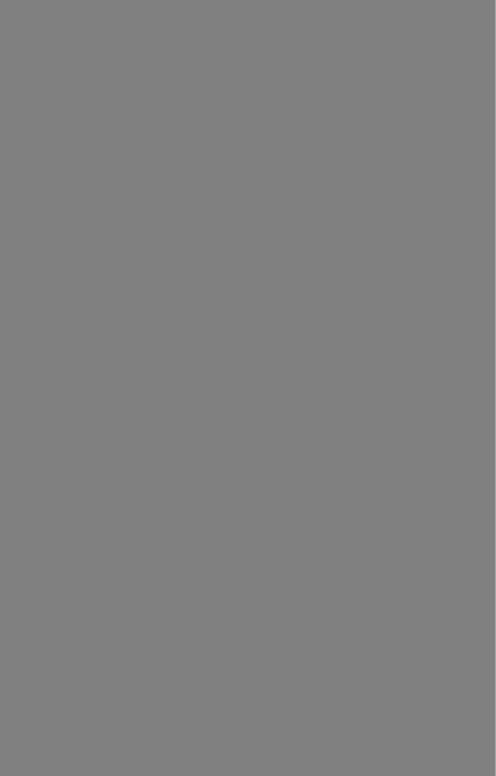
Рис. 59. Схема получения очищенного концентрата НМК:
/ — отстойник; |
2 — теплообменники; 3 — ректификационные |
колонны; -/ — емкости; |
5 — |
||
холодильники; |
/ — кислая вода; |
// — «парафиновое масло»; |
/// — бутанол; |
I V — сбросная |
|
вода; V — тяжелокнпящие продукты; V I — очищенный концентрат; V I I |
— легколетучие |
||||
компоненты |
|
|
|
|
|
ные азеотропы. Ввиду |
дефицитности изоамилового |
спирта |
в |
качестве антренера предложено использовать бутиловый спирт, образующий с водой азеотропную смесь с температурой кипе ния 92,4°С и содержанием воды 38% (масс.).
Производство очищенного концентрата низкомолекулярных кислот (рис. 59) из кислых вод производства синтетических жирных кислот включает приготовление усредненного потока кислой воды с отстаиванием от парафиновых масел и механи
ческих примесей, азеотропную ректификацию кислой |
воды с |
получением 70%-ного концентрата, регенерацию |
антренера, |
очистку 70%-ного концентрата от тяжелых и легких примесей. Таким образом, очистка кислых вод производства синтети ческих жирных кислот позволяет выделить концентрат низко молекулярных кислот, очистить водные стоки и повторно ис пользовать их для промывки воздуха из колонн окисления, т. е. создать замкнутый водный цикл. Ниже приведены показа
тели качества |
очищенного |
концентрата |
низкомолекулярных |
||
кислот: |
|
|
|
|
|
Кислотное число, мг КОЫ/г, не менее |
650 |
||||
Эфирное число, мг КОН/г, не более |
25 |
||||
Содержание, |
% |
(масс.) |
|
65 |
|
кислот |
Ci—С4, не менее |
||||
в том |
числе: |
|
5,0 |
||
пропионовой, |
не менее |
|
|||
масляной, |
не |
более |
|
5,0 |
|
воды, не более |
|
35,0 |
|||
железа, |
не |
более |
более |
0,001 |
|
нелетучего |
остатка, не |
0,5 |
|||
Перманганатный |
индекс, не более |
700 |
Основной |
потребитель очищенного концентрата — сельское |
|
хозяйство, где его используют |
в качестве консерванта кормов |
|
и влажного |
фуражного зерна. |
По консервирующему действию |
концентрат аналогичен муравьиной и бензойной кислотам. При хранении силосуемой массы с добавлением на 1 т 3— 5 кг кон центрата питательная ценность кормов на 20'—-25% выше, чем при хранении без добавления консервантов. Очищенный кон центрат в смеси с фракцией кислот С 5— Сб можно использовать при консервировании высокобелковых морских продуктов, до быче нефти и в энергетической промышленности. Применение концентрата для обработки призабойных зон скважин вместо соляной и уксусной кислот обеспечивает более медленное их взаимодействие с породой по сравнению с сильными неорга ническими кислотами, предупреждает вторичные процессы и выпадение осадков гидрооксида железа. Одновременно увели чивается радиус обработки призабойных зон и дебит скважин. Концентрат используют как растворитель при промывке энер гетического оборудования для химической очистки деталей
систем охлаждения автомобильных и тракторных |
двигателей |
ст накипи, в производстве синтетического солидола |
и других |
областях. |
|
4.4. ЭНЕРГОСБЕРЕГАЮЩИЕ ТЕХНОЛОГИИ ПРОИЗВОДСТВА АРОМАТИЧЕСКИХ УГЛЕВОДОРОДОВ И МОНОМЕРОВ СИНТЕТИЧЕСКОГО КАУЧУКА
4.4.1. Производство ароматических углеводородов
В СССР более 50% ароматических углеводородов вырабаты вают методом каталитического риформинга.
Каталитический риформинг прямогонных бензиновых фрак ций осуществляют на стационарном алюмоплатиновом или полиметаллическом платиновом катализаторе в среде водород содержащего газа при температуре 480—530 °С и давлении 1,5—3,5 МПа. В качестве сырья в зависимости от целевого назначения процесса используют широкую фракцию 85—180°С (получение высокооктановых компонентов бензина) либо уз кие фракции 62—85, 62—105, 105—140, 120—140 °С (производ ство бензола, толуола, ксилолов). Технологические схемы дей ствующих отечественных установок практически одинаковы.
Более 82% прямогонного сырья, направляемого на рифор минг, расходуют в производстве высокооктановых компонентов автомобильных бензинов, около 18%— в производстве бензола, толуола и суммарных ксилолов.
В промышленности эксплуатируются установки Л-35-6, Л-35-12, Л-35-8/300Б, ЛГ-35-8/300Б, вырабатывающие бензол и толуол, и ряд установок по производству суммарных ксилолов. Мощность каждой установки по сырью 300 тыс. т/год.
Процесс собственно каталитического риформинга и стадия выделения ароматических углеводородов из катализатов ри форминга энергоемки. Доля энергозатрат составляет 20%, из
них больше половины приходится на экстракцию ароматичес ких углеводородов. Энергоемкость каталитического риформинга определяется фракционным и углеводородным составами ис ходного сырья, технологическим режимом, видом применяемого катализатора, типом и мощностью установки.
Основной путь снижения энергоемкости и повышения эф фективности работы установок каталитического риформинга — обеспечение их сырьем в проектном количестве и соответствую щего качества, а также применение вместо катализаторов АП-64, стабильных и эффективных полиметаллических катали
заторов |
серии КР. |
Эти катализаторы |
позволяют |
снизить |
||
давление |
в системе, |
сократить |
объем циркуляционного |
газа, |
||
повысить |
степень ароматизации |
целевого |
продукта, |
что при |
||
водит к |
снижению |
удельных энергозатрат. Установки |
Л-35-8 |
и ЛГ-35-8 работают только на катализаторе КР-108 и КР-110. Выделение ароматических углеводородов включает собст венно экстракцию ароматических углеводородов из стабильного катализата риформинга растворителем, регенерацию раствори теля, ректификацию экстракта с целью получения товарных
продуктов высокой степени чистоты.
В качестве экстрагента ароматических углеводородов из смеси их с парафиновыми углеводородами до недавнего време ни применяли 93%-ный водный раствор диэтиленгликоля. Для экстрагирования ароматических углеводородов с различной молекулярной массой требуется соответствующее массовое соотношение экстрагент: сырье, равное при использовании ди этиленгликоля (8—15) 1. Чем больше молекулярная масса ароматических углеводородов, содержащихся в катализате, тем выше это соотношение. Замена диэтиленгликоля более эффек тивным триэтиленгликолем позволяет снизить соотношение
экстрагент: сырье до (7— 10) |
1 и, следовательно, обеспечить |
||
значительную экономию |
пара, |
особенно при |
экстрагировании |
ксилолов. При переходе |
на триэтиленгликоль |
основное техно |
логическое оборудование блока экстракции и вторичной рек тификации то же, а с сокращением количества циркулирующего растворителя появляются резервные мощности оборудования, позволяющие увеличить производительность блока.
ВСША с применением в качестве экстрагента триэтиленгликоля (по методу фирмы «Юнион карбайд») при сохранении мощности установок энергозатраты снижены на 40—60%. При меняют также другие эффективные экстрагенты — сульфолан, диметилсульфоксид и др.
Всвязи с высокой энергоемкостью экстракции ксилолов из катализатов риформинга разработан новый метод их выделе ния— четкая ректификация. По этому методу на риформинг подают узкую прямогонную фракцию 105— 124 °С. Из получае мого катализата с высокой концентрацией ароматических углеводородов четкой ректификацией в чистом виде выделяют суммарные ксилолы. Образующиеся незначительные количества
бензола и толуола выводят в смеси с парафиновыми углеводо родами в виде доксилольной фракции, применяемой как ком понент автобензина.
В настоящее время в производственном объединении «Киришинефтеоргсинтез» внедрен процесс безэкстрактивного выделения ксилолов. На его реализации дополнительно затра чено 7,5 млн. руб. при годовом экономическом эффекте 5,5 млн. руб.
В процессах каталитического риформинга основными вто ричными энергетическими ресурсами являются топливные газы и тепло отходящих дымовых газов печей и продуктовых пото ков. Наиболее полно используют топливные газы: их либо сжигают как топливо, либо отпускают сторонним организациям. В зависимости от перерабатываемого сырья и выпускаемой продукции выход этих газов колеблется от 1,5 до 5,5% (масс.) на перерабатываемое сырье.
Степень использования тепловых ВЭР составляет в сред нем менее 50% потенциала. Оборудование для утилизации теп ла отходящих дымовых газов подвергается сильной сероводо родной коррозии, так как основное топливо в печах — мазут с содержанием серы 2—2,5%. За рубежом используют регенера тивные вращающиеся воздухоподогреватели, способные рабо тать в условиях сероводородной коррозии. Опыт эксплуатации
такого воздухоподогревателя в СССР на |
установке |
Л-35-11/600 показал, что в результате утилизации |
тепловых |
ВЭР можно экономить 6 тыс. т у. т. |
|
Разработка новых методов получения ароматических угле водородов связана с поиском нетрадиционных доступных видов сырья (газы вторичных процессов НПЗ; побочные фракции нефтехимических процессов, сжиженные нефтяные газы) и но вой технологии (табл. 18).
Многие зарубежные фирмы в течение ряда лет ведут иссле дования по применению сжиженных нефтяных газов (пропан, смесь бутанов) для получения органических продуктов вместо традиционного использования их в качестве топлива. Ряд фирм работает над созданием процессов и катализаторов ароматиза ции низкомолекулярного сырья.
Фирмами «Бритиш петролеум» (БП) ц ЮОП разработан одностадийный каталитический процесс сайклер (циклар), ос нованный на дегидроциклодимеризации пропана и бутанов в присутствии катализатора, созданного фирмой ЮОП для про цесса риформинга (рис. 60). Активность и селективность ката лизатора поддерживается на высоком уровне благодаря его непрерывной регенерации.
Процесс сайклер проверен для разных сырьевых смесей. При использовании в качестве сырья бутана выход ароматических
углеводородов |
С6—Се |
составляет 54,2% |
(масс.) и водорода |
|
4,1% (масс.) на |
свежее |
сырье; |
пропана — 51,4 и 5,6% (масс.) |
|
соответственно; |
смеси пропана |
и бутана (1 |
1)— 57,8 и около |
isq
Фирма |
Сырье |
Катализатор |
Температу °Сра. |
Давление, МПа |
|
|
БП и ЮОП |
Парафины |
Цеолит с |
добавками |
420 |
0,1 |
|
(процесс |
С3 -—С4 |
металлов |
группы |
|
|
|
«сайклер») |
|
алюминия |
(преиму |
|
|
|
|
|
щественно |
галлия) |
|
|
|
Шелл |
Парафины |
Кристаллические |
гал* |
575 |
0,15 |
|
|
С2—С4, олефи-лийсодержащие |
сили- |
|
|
||
|
ны С2—С4 |
или каты |
|
|
|
|
|
смесь углеводо |
|
|
|
|
|
|
родов С2 (50%) |
|
|
|
|
Конверсия, % |
Выход аро матических углеводо родов |
90 |
50 |
95 |
|
Мобил ойл Этан
Университет Пропан (г. Киото)
Цеолит, активирован 590— ный соединениями 680
галлия
Цеолит, активирован 500 ный платиной, 0,5% (масс.)
О |
1 |
|
00 |
0,1
33 50
90 —
5% (масс.). При использовании олефинов в процессе сайклер выход ароматических углеводородов увеличивается.
Фирмой «Кинетике технолоджи интернэшнл» разработан про цесс пироформ в термическом, каталитическом и термокатали тическом вариантах. Этот процесс можно комбинировать с пи ролизом, что позволяет расширить возможности пиролиза как по используемому сырью, так и по получаемым продуктам. Про цесс пироформ можно применять также для переработки побоч ных фракций С2—С3 каталитического крекинга и риформинга с получением дополнительного количества высокооктановых ком понентов бензина.
Изопропилбензол и этилбензол — сырье для получения их гидропероксидов, а-метилстирола, стирола, фенола и ацетона, оксида пропилена, оксидов высших олефинов и др. Их произво дят алкилированием бензола пропиленом и этиленом в присут ствии хлорида алюминия или фосфорнокислотных катализато ров.
Производство изопропилбензола (кумола) в мире исчисля ется миллионами тонн. Основной его производитель — США:
|
США |
Италия |
Общее число действующих установок |
11,0 |
3,0 |
Суммарная производительность, тыс. т |
1898,0 |
620,0 |
Производительность установки, тыс. т: |
172,5 |
206,7 |
средняя |
||
максимальная |
360,0 |
270,0 |
В СССР изопропилбензол получают алкилированием бензо ла пропиленом в присутствии хлорида алюминия. За рубежом