
Физические основы микро- и нанотехнологии
..pdfдут дрейфовать ионы. Однако так как их подвижность значительно ниже, чем у электронов, то они почти не будут изменять величину отрицательного заряда мишени. При достаточно большом высокочастотном напряжении мишень будет энергично бомбардироваться ионами и распыляться. Попадая на подложку и конденсируясь, распыленные частицы мишени будут создавать на ней пленку.
Процесс ионного распыления можно интенсифицировать не только путем увеличения числа электронов, эмиттируемых с катода, как при ионно-плазменном распылении, но и путем повышения эффективности ионизации электронами нейтральных атомов газа. Этого можно добиться с помощью использования магнитного поля, воздействующего на тлеющий разряд путем изменения характера движения электронов. Влиянием магнитного поля на существенно более тяжелые ионы можно в принципе пренебречь. Под воздействием магнитного поля электроны, вектор скорости которых не параллелен направлению магнитного поля, начинают двигаться по спиральным траекториям, вследствие чего возрастает эффективная длина пути, проходимого электроном. Это эквивалентно увеличению давления газа в рабочей камере.
Наложение магнитного поля также сильно уменьшает радиальную диффузию электронов из зоны действия газового разряда, что снижает потери электронов, способных осуществлять ионизацию. Реализующие этот процесс устройства называются магнетронами. С их помощью удается поддерживать газовый разряд до давлений 10–12 мм рт. ст., что существенно уменьшает загрязнение получаемых пленок.
Атомы, выбитые из мишени при ионном распылении, могут обладать значительной энергией (порядка десятков электрон-вольт), причем относительная доля таких атомов увеличивается с ростом энергии бомбардирующих ионов. Это определяет специфику процесса конденсации атомов на подложке при ионном напылении – отсутствие критической температуры и критической плотности атомного пучка. Вследствие высокой энергии бомбардирующих атомов они практически при любой температуре и любой плотности пучка «вбиваются» в поверхность под-
211
ложки и «застревают» там. По мере напыления доля напыляемых атомов в поверхностном слое непрерывно растет, и в конце концов на поверхностиобразуется пленка изчистого материала мишени.
При соударении атомов, выбитых из мишени, с атомами нейтрального газа в камере последние могут также приобретать высокую кинетическую энергию, достаточную для внедрения их в подложку. Концентрация таких атомов в напыленной пленке может достигать нескольких процентов. Кроме того, при ионном распылении возможно образование значительно большего числа разнообразных химических соединений активного газа с материалом мишени, чем при термическом распылении. Это является следствием того, что
вразряде возникают возбужденные атомы и молекулы; молекулы могут диссоциировать на нейтральные атомы либо ионы; образуются молекулярные ионы и т.д. Все эти частицы химически более активны, чем нейтральные, не возбужденные, молекулы. Это обстоятельство используется, в частности, для получения нитридов металлов,
иособенно нитрида кремния, в технологии интегральных схем. Существенным достоинством ионного напыления является воз-
можность получения пленок стехиометрического состава из сплавов
исложных химических соединений, а также высокая адгезия пленок к подложкам. Недостатком считаются относительно низкие скорости нанесения пленок, находящиеся в интервале 5–300 нм/мин. Если
вустановке используется не высококлассное вакуумное оборудование, а, в частности, откачные системы на силиконовом масле, то пары масла, попадая в рабочую камеру, под воздействием плазмы
ивысокочастотного поля образуют радикалы. Эти радикалы, оседая на поверхность подложки, очень сильно ее загрязняют. Это приводит к необходимости использования так называемой безмасляной откачки.
Стремление интенсифицировать процесс получения пленок; сохранить стехиометрический состав исходных материалов, осажденных в виде пленок; повысить чистоту пленок и адгезию их к подложкам привело к применению в субмикронной технологии импульсных плазменных ускорителей (ИПУ). При импульсно-
212
плазменном нанесении пленок используют более плотные потоки пара, чем при ионно-плазменном распылении. Создавая плотные потоки плазмы, можно на несколько порядков увеличить скорость осаждения, а следовательно, и производительность процесса, а используя высокий вакуум, можно получить более чистые пленки, чем при катодном распылении.
В ИПУ плазма создается в парах распыляемого материала, испаряемого и ионизируемого любым способом, например в дуговом разряде. Испарение материала происходит как взрыв в вакууме. При длительности импульса порядка долей секунды материал поверхности распыляемого вещества в месте образования дуги превращается в пар высокой плотности с температурой порядка 105 К. Такое испарение является уникальным по скорости и энергии частиц и поэтому представляет особый интерес для получения пленок с высокой адгезией при большой производительности процесса. Вакуумный дуговой разряд является источником плазмы, состоящей из паров и ионов распыляемого вещества и электронов.
Конденсация пленок при ионном распылении происходит в сложных условиях: при относительно высоком давлении инертного газа, в присутствии химически активной и ионизированной в разряде фоновой атмосферы, при наличии электростатического поля. Причиной повышенной адгезии является значительный запас энергии у конденсирующихся атомов вещества. Она на порядок выше, чем при термическом испарении.
Присутствие в потоке вещества электрически заряженных атомов влияет на весь процесс роста пленки. Заряженные частицы, попадая на подложку, увеличивают площадь поверхности первичных гранул вследствие дополнительной электростатической энергии поверхности, увеличивают поверхностную диффузию между гранулами, ускоряют их объединение. Первичные образования, как и при термическом испарении, состоят из зародышей, которые перерастают в гранулы. Но с этого момента распыленные гранулы продолжают расти только в плоскости, в результате чего ионным распылением можно получить сплошные пленки при гораздоменьшихтолщинах, чемвслучаетермическогоиспарения.
213
Преимущества метода ионно-плазменного распыления:
1)большая площадь распыляемой пластины материала – мишени, выполняющей функции источника атомов осаждаемого вещества, позволяет получить равномерные по толщине пленки на подложках больших размеров, что обеспечивает эффективную реализацию группового метода обработки;
2)мишень представляет собой длительно не заменяемый источник материала (при толщине пластины 3 мм смена производится один раз в месяц при двухсменной работе), что облегчает автоматизацию, повышает однородность процесса;
3)обеспечивается высокая адгезия пленки к подложке благодаря большой энергии конденсирующихся атомов;
4)получение пленок из тугоплавких металлов протекает без перегрева вакуумной камеры;
5)возможно получение окисных, нитридных и других пленок,
втом числе легированных, в результате химических реакций атомов распыляемого металла с вводимыми в камеру газами;
6)возможность проведения окисленияплазменныманодированием;
7)возможность получения органических пленок;
8)потери материала минимизированы, так как весь процесс происходит в геометрическом промежутке мишень – подложка, исключая объем камеры, как это имеет место при методе ТВН.
4.2.4. Эпитаксия
Эпитаксия из газовой фазы. Ориентированной кристаллизацией, или эпитаксией (упорядочением), называется процесс роста слоев, решетка которых определенным образом ориентирована относительно исходного кристалла-подложки. Материал подложки в процессе выращивания играет роль затравочного кристалла, на котором и происходит рост уже соответствующим образом ориентированной пленки, причем ее рост осуществляется при температурах, меньших температуры плавления. Этого добиваются путем осаждения требуемого материала из парогазовой смеси. Если материалы подложки и растущего слоя идентичны, то процесс называется автоэпитаксиальным или го-
214
моэпитаксиальным; если материалы слоя и подложки различаются, то процесс называется гетероэпитаксиальным (но и в этом случае кристаллическая структура слоя и подложки должны быть сходными). Подложка и выращиваемый слой могут иметь различные типы проводимости, т.е. служить основой для создания p–n-структур.
Различают прямые и непрямые эпитаксиальные процессы. При прямых процессах атомы полупроводника от источника попадают на поверхность подложки и осаждаются на ней. С точки зрения физики нет препятствий для использования для этих целей методов ТВН или ионного распыления, но качество пленок при этом получается настолько неудовлетворительным, что эти методы практически не применяются.
При непрямых процессах атомы полупроводника достигают подложки не прямым путем, а с помощью среды-носителя (жидкой или газообразной). Стремление произвольной системы к минимуму свободной энергии приводит к тому, что в процессе эпитаксии растущие слои ориентируются с некоторым соответствием по отношению к соприкасающейся атомарной плоскости подложки. В случае совершенного сопряжения поверхность раздела называется когерентной. Существует несколько моделей, объясняющих характер сопряжений смежных атомных плоскостей двух веществ. Если параметры решетки сопрягающихся веществ различаются несущественно, то имеет место псевдоморфизм – результат приспособления межатомных расстояний растущего кристалла к межатомным расстояниям подложки. Однако в большинстве случаев наблюдается скачкообразное изменение параметра решетки на границе раздела и появление дислокаций, понижающих возникающие механические напряжения.
Подложка оказывает существенное влияние на процесс кристаллизации растущего на ее поверхности слоя вещества. Атом, приходящий из внешней фазы, может передать ей свою кинетическую энергию. Силы связи между подложкой и адсорбированными атомами удерживают последние на поверхности; кристаллохимические особенности подложки влияют на скорость поверхностной диффузии адсорбированных атомов и тем самым – на кристаллографическую
215

ориентацию осаждаемой пленки. Несовершенства строения поверхности подложки также сказываются на характере распределения и строении растущего материала.
Рассмотрим эпитаксию из газовой фазы. Детальное изучение процессов эпитаксии подразумевает рассмотрение термодинамики и кинетики химических реакций и механизма течения газового потока в реакторе. Схема реактора для газофазной эпитаксии приведена на рис. 4.4. Подложка помещается в специальную капсулу – реактор 1, через которую прокачивается газовая смесь, состоящая из газаносителя (азот, водород или инертный газ) и газа-реагента. Подложкодержатель 3 вместе с комплектом подложек 4 тем или иным способом (чаще всего индукционным нагревом) нагревается до определенной температуры, при которой газ-реагент разлагается таким образом, что твердым продуктом разложения являются атомы полупроводника, которые и осаждаются на подложку. Процесс подобного разложения вещества под действием высокой температуры называется пиролизом.
Рис. 4.4. Схема реактора для газофазной эпитаксии:
1 – корпус реактора; 2 – нагреватели; 3 – подложкодержатель; 4 – подложки
Для кремния таким газом-реагентом является силан (SiCl4). Реакция разложения силана протекает по следующей схеме:
SiCl4 + 2Н2 ↔ Si↓ + 4НС1↑, |
(4.3) |
причем скорость роста W пленки кремния зависит от концентрации Q силана так, как это показано на рис. 4.5 (Q – отношение количества молекул силана к полному количеству молекул в газе).
216
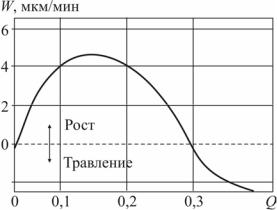
Рис. 4.5. Зависимость скорости роста W пленки кремния
от концентрации Q силана
Сростом содержания силана скорость роста достигает максимума
иначинает падать. В какой-то момент начинает преобладать обратная реакция и начинается травление подложки. Таким образом, имеется возможностьуправленияпроцессомобразованияэпитаксиальнойпленки.
Формула (4.3) описывает реакцию в первом приближении. На самом деле необходимо учитывать ряд промежуточных и конкурирующих реакций и исходить из того, что эпитаксиальный процесс далеко не всегда описывается приведенной равновесной реакцией.
Для легирования получаемой пленки донорными или акцепторными примесями к смеси газов добавляют различные компоненты, такие как фосфин (РН3) и диборан (В2Н3). Необходимо учитывать, что эти вещества являются сильнодействующими ядами.
Обычно в качестве газа-носителя используется водород, как самый недорогой. Пограничный слой образуется над подложкодержателем и на стенках при входе в реактор и по мере его продвижения вдоль реактора увеличивается так, что возможно его полное смыкание. Через пограничный слой исходные реагенты переносятся из газового потока к поверхности, а продукты реакции диффундируют от поверхности подложек и удаляются потоком основного газа.
217
Потоки реагентов, направляемые как к поверхности подложек, так и от нее, являются сложной функцией нескольких переменных (температура, давление, концентрация реагентов, толщина пограничного слоя). В первую очередь необходимо учитывать влияние толщины пограничного слоя на процессы массопереноса. Для достижения хорошей однородности получаемых эпитаксиальных пленок распределение толщины пограничного слоя по длине реактора должно быть согласовано с изменением температуры и концентрации реагентов.
Для легирования используются гидриды примесных элементов, которые устойчивы в водородной среде. Скорость роста пограничного слоя влияет на количество встраиваемой в эпитаксиальный слой примеси. При низких скоростях роста между твердой и газообразной фазами устанавливается равновесие, которого невозможно достичь при высоких скоростях роста.
В зависимости от диаметра подложек и типа реактора одновременно обрабатывают 10–30 подложек. Средняя производительность при длительности процесса около 1 ч составляет 20 подложек в час.
Эпитаксиальные слои редко получают с концентрацией примеси выше 1017 см–3, хотя имеется техническая возможность легирования эпитаксиальных слоев фосфором до более высоких концентраций, близких к пределу растворимости. Наиболее широкое применение находят слои с концентрацией примеси от 1014 до 1017 см–3.
Для получения высокоомных слоев необходимы очень чистый реактор и кремнийсодержащее соединение с малым содержанием примеси. Автолегирование с обратной стороны зачастую устраняется маскированием этой стороны слоем окисла или нитрида кремния.
Жидкостная эпитаксия. Поскольку для получения сложных структур метод газовой эпитаксии не вполне пригоден, для этих целей применяют жидкостную эпитаксию. Подложка находится в термодинамическом равновесии с раствором (расплавом), и процесс наращивания происходит вследствие перенасыщения при уменьшении температуры.
Для улучшения контроля процесса применяют жидкостную эпитаксию, управляемую электрическим током, – электроэпитаксию. При этом через выращиваемый граничный слой пропускают элек-
218
трический ток и вследствие эффекта Пельтье (выделение или поглощение теплоты на контакте двух разнородных проводников в зависимости от направления протекания электрического тока) происходит охлаждение или нагрев границы раздела двух фаз.
Кинетика роста пленки обусловлена охлаждением за счет эффекта Пельтье границы раздела расплав – подложка. Охлаждение приводит к локальному перенасыщению расплава на границе, что обеспечивает контролируемый рост пленки, так как скорость процесса напрямую связана с величиной протекающего электрического тока. При изменении полярности будет наблюдаться обратный процесс – растворение верхнего слоя подложки в расплаве.
Стандартные реакторы для жидкостной эпитаксии легко модернизируются для реализации возможности пропускания тока через расплав или раствор. Ввиду того, что подложка и раствор имеют разные термоэлектрические коэффициенты, протекание тока через их границу сопровождается нагревом или охлаждением Пельтье, а количество выделяемой или поглощаемой теплоты равно произведению разницы коэффициентов Пельтье на плотность тока. Кинетика роста пленки зависит от толщины граничного слоя, образующегося на границе расплава-раствора. Метод является удобным и достаточно практичным. Поскольку процесс проходит в закрытом реакторе, уменьшается вероятность загрязнения пленок. Однако необходимость контакта с раствором-расплавом и загрязнение его за счет контакта со стенками реактора не позволяет получать пленки очень высокого качества.
Молекулярно-лучевая эпитаксия. При газофазной и жидкостной эпитаксии выращиваемая пленка все время находится в контакте со средой-носителем, поэтому возможно ее неконтролируемое загрязнение. Идеальной средой с этой точки зрения является высокий вакуум. Поэтому для выращивания особо чистых пленок применяется метод молекулярно-лучевой эпитаксии (МЛЭ), использующий конденсацию молекулярных пучков в сверхвысоком вакууме. Метод МЛЭ является аналогом метода ТВН на следующем витке развития техники и технологии, однако существуют и принципиальные отличия. В методе ТВН
219

используются испарители с открытым зеркалом расплава, поэтому испарение происходит по косинусоидальному закону (со всеми вытекающими отсюда недостатками). В методе МЛЭ испаряемое вещество движется к подложке врежиме свободного молекулярного потока.
Испаряемый материал нагревается в специальном тигле, а затем врежиме свободного молекулярного потока напыляется на подложку. Тигель, из которого производится испарение материала (рис. 4.6), представляет собой цилиндр, чаще всего из нитрида бора, в котором испаряемое вещество находится в твердом или жидком состоянии. В тигле диаметром D на расстоянии L от края тигля расположено испаряемое вещество. Диаграмма направленности парового потока при различных соотношениях L: D будет иметь различную форму. При соотношении, равном 0 (расплав находится вровень с краем тигля), имеем обычный косинусоидальныйзаконраспределения.
Рис. 4.6. Угловое распределение
парового потока |
из тигля: 1, 2, |
3 – диаграммы |
направленности; |
4 – тигель; 5 – расплав
Приведенный на рис. 4.6 тигель является самой примитивной конструкцией эффузионных истосников. При увеличении этого соотношения диаграмма направленности будет изменяться – диаграммы 2 и 3 соответственно – приближаясь к режиму молекулярного потока. Источники подобного типа и получили название эффузионных.
Эффузионные источники позволяют генерировать пучки с контролируемой интенсивностью и известным угловым распределением. Состояние частиц в пучке тождественно состоянию частиц в объеме источника, что облегчает проведение диагностики пучков.
220