
Технология конструкционных материалов. Способы получения деталей (за
.pdf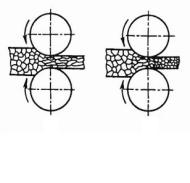
высить сжимающие напряжения при обработке давлением можно, например, оказывая боковое давление на металл жесткими стенками инструмента (рис. 23, б, в, г). Схема напряжений, представленная на рис. 23, а, реализуется при прессовании металлов и горячей объемной штамповке.
По мере повышения температуры нагрева пластичность металлов возрастает, а прочность уменьшается. Однако в углеродистых сталях при температурах 100…400 С пластичность уменьшается, а прочность возрастает.
3. Влияние обработки давлением на структуру и свойства металла
Исходной заготовкой для обработки металлов давлением (прокатки, прессования) является слиток. Кристаллическое строение слитка неоднородно. Кроме того, в нем имеется пористость, газовые пузыри и т.п. Обработка давлением слитка при нагреве его до достаточно высоких температур приводит к деформации кристаллитов и частичной заварке пор и раковин, что увеличивает и плотность металла.
В зависимости от тем- пературно-скоростных условий различают холодную и горячую деформацию.
При холодной деформации зерна вытягиваются в направлении наиболее интенсивного течения металла (рис. 24, а). Металл становится более твердым, но ме-
нее пластичным. Это явление называют упрочнением (наклепом). Наклеп, вызванный холодным пластическим деформированием металла, может быть устранен отжигом.
61
При нагреве наклепанного металла до температур, составляющих 0,2…0,3 от температуры плавления Тпл (возврате), частично уменьшаются искажения кристаллической решетки и внутренние напряжения без изменения микроструктуры деформированного металла. Повышается электрическая проводимость, сопротивление коррозии холоднодеформированного металла.
При нагреве деформированных металлов выше 0,4Тпл образуются новые равноосные зерна (рис. 24, б). Процесс образования новых центров кристаллизации и новых равноосных зерен в деформированном металле, при нагреве сопровождающийся уменьшением прочности, увеличением пластичности и восстановлением других свойств, называется рекристаллизацией. Наименьшая температура, при которой начинается процесс рекристаллизации и разупрочнения металла, называется температурой начала рекристаллизации Тр. Размер зерна после рекристаллизации зависит от степени и скорости деформации, а также температуры и длительности нагрева. При увеличении степени деформации до критического значения размер зерна увеличивается, а при степенях деформации выше критической зерно измельчается, причем эти размеры примерно одинаковы по всем направлениям (равноосная структура), что благоприятно влияет на механические характеристики металла.
4. Холодная и горячая деформация
Различают холодную и горячую деформацию. Холодное деформирование производится при температурах ниже температуры рекристаллизации и сопровождается наклепом металла. Горячее деформирование протекает при температурах выше температуры рекристаллизации, при котором также происходит упрочнение металла (горячий наклеп), но оно полностью снимается в процессе рекристаллизации, что при-
62
водит к повышению пластичности и уменьшению сопротивления деформации.
Если слиток загрязнен неметаллическими включениями, обычно располагающимися по границам кристаллитов, то в результате обработки давлением образуется так называемая волокнистая макроструктура (см. рис. 22, в, г), которая не может быть изменена ни термической обработкой, ни последующей обработкой давлением.
Волокнистость оказывает влияние на механические характеристики, вызывает их анизотропию. В поперечном направлении ударная вязкость меньше, чем вдоль волокон, на 50…70 %, относительное сужение на 40 %, относительное удлинение на 20 %. Поэтому в деформированных заготовках нужно создать такое расположение волокон, чтобы наибольшие растягивающие напряжения действовали вдоль, а перерезывающие усилия поперек волокон. Важно также, чтобы волокна не перерезались при обработке резанием.
Если у поверхности детали волокна повторяют ее очертания (см. рис. 22, г), то повышаются прочность и эксплуатационные свойства материала детали.
5. Нагрев металлов перед обработкой давлением
Для повышения пластичности и уменьшения сопротивления деформированию металлы и сплавы перед обработкой давлением нагревают до определенной температуры (рис. 25).
При нагревании стали выше 700 С происходит интенсивное окисление поверхностного слоя с образованием окалины, что приводит к потере металла. Кроме этого, образование окалины в 1,5–2 раза повышает интенсивность изнашивания деформирующего инструмента.
При высоких температурах происходит также обезуглероживание поверхностного слоя стали.
Для уменьшения окисления металла применяют электронагрев, а также нагрев заготовок в защитной атмосфере.
63

Для максимального повышения пластичности металла температура начала обработки должна быть высокой, но невызывающей перегрева ипережога. Перегрев ведет к интенсивному росту зерна и к уменьшению пластичности и ударной вязкости. Структуруперегретойсталиможноисправитьотжигом.
t,°С
1500
1400
1300
900
800
727
600
0
Область температур
нагрева
0,8 |
2,14 С, % |
Рис. 25. Температурный интервал и режим нагрева
При пережоге стали при температуре, близкой к температуре плавления, происходит интенсивная диффузия в нее кислорода, образование оксидов по границам зерен и расплавление легкоплавких межзеренных прослоек, что приводит к появлению трещин и потери пластичности. Пережог не устраняется термической обработкой, и пережженный металл приходится отправлять на переплавку.
Температура начала обработки давлением Тн = = 0,85…0,95 Тпл, Тпл температура плавления сплава. Температура окончания обработки должна быть выше температуры рекристаллизации и фазовых превращений: Тк = 0,7 Тпл.
Режим нагрева. Нагрев заготовок происходит неравномерно. Вначале нагреваются наружные слои, а затем сердцевина. Из-за разности температур возникают температурные напряжения, которые могут привести к образованию трещин.
64

Опасность их появления больше у легированных и литых сталей (у которых теплопроводность меньше), и она возрастает сувеличением сечения заготовки. Продолжительность нагрева связана с размером заготовки. Чем больше сечение заготовки, тем большее время ее нагрева. На продолжительность нагрева влияет и форма заготовки. При равных объемах круглая заготовканагревается быстрееквадратнойили прямоугольной.
Влияние способа укладки заготовок учитывают поправочным коэффициентом (рис. 26). Нагреву одной круглой
заготовки соответствует коэффициент = 1. Круглые заготовки, уложенные плотно друг к другу, требуют в два раза
больше времени нагрева ( = 2), тесно уложенные квадратные заготовки нагреваются в четыре раза медленнее ( = 4).
|
Расположение |
коэффициент d |
|
Расположение |
коэффициент d |
||
|
заготовок |
|
заготовок |
||||
|
|
|
|
|
|
||
|
|
|
|
|
|
|
|
|
|
|
1 |
|
|
|
1 |
|
|
|
|
|
|
|
|
|
|
|
1 |
|
|
|
1,4 |
|
|
|
|
|
|
|
|
|
|
|
2 |
|
|
|
4 |
|
|
|
|
|
|
|
|
|
|
|
1,4 |
|
|
|
2,2 |
|
|
|
|
|
|
||
|
|
|
|
|
|
|
|
|
|
|
|
|
|
|
|
|
|
|
|
|
|
|
|
|
|
|
1,3 |
|
|
|
2 |
|
|
|
|
|
|
|
|
Рис. 26. Влияние способа размещения заготовок на поду печи на продолжительность нагрева (коэффициент )
65

Для ориентировочного нахождения продолжительности нагрева стальных заготовок сечением свыше 100 мм пользуются эмпирической формулой Н.Н. Доброхотова:
kd d,
где полная продолжительность нагрева, ч;коэффициент, учитывающий способ укладки загото-
вок, = 1…4;
k коэффициент, зависящий от марки стали, для углеродистых и низколегированных сталей k = 12,5, для высокоуглеродистых и высоколегированных сталей k = 25;
d диаметр или сторона квадрата заготовки, м.
6. Основные типы нагревательных устройств
Устройства для нагрева заготовок перед обработкой давлением разделяют на нагревательные печи и электронагреватели. Первые используют для нагрева слитков, крупных и иногда средних заготовок. Электронагревательные устройства наряду с печами применяют для нагрева мелких и средних заготовок.
Типы печей. В зависимости от источника энергии нагревательные печи бывают пламенные и электрические. В пламенных печах тепло образуется при сгорании жидкого (мазута) или газообразного топлива. В электрических печах тепло образуется при прохождении тока через металлические или карборундовые сопротивления, вмонтированные в стенках нагревательной камеры. Они используются преимущественно для нагрева цветных сплавов.
По принципу действия различают печи камерные и методические.
В камерных печах рабочее пространство (камера), выложенное огнеупорным кирпичом, нагревается при сжигании
66

топлива и имеет одинаковую температуру. Заготовки, устанавливаемые на под печи, загружаются и выгружаются через окно. Продукты сгорания отводятся через дымоход и используются для нагрева до 200…300 С поступающего в печь воздуха, что повышает КПД печи.
Разновидностью камерных печей являются нагревательные колодцы, которые применяют для нагрева крупных слитков при прокатке и ковке. В них заготовки располагаются вертикально и загружаются сверху краном.
Методические печи предназначены для нагрева крупных заготовок под прокатку и в крупносерийном производстве. Печи характеризуются наличием трех зон с различной температурой. Заготовки 1 (рис. 27), перемещаясь навстречу горячим газам, проходят зоны подогрева I (600…800 С), максимального нагрева II (1350 С), где происходит основное сгорание топлива с помощью форсунок или горелок 2, и зону выдержки III (1200…1300 С), в которой выравнивается температура по сечению заготовки. Заготовки с помощью толкателя 3 проталкиваются через печь по охлаждаемым водой направляющим трубам 4 и выгружаются через окно 5.
Рис. 27. Пламенные печи для нагрева заготовок
Печи для нагрева заготовок диаметром до 120 мм имеют две зоны нагрева (600…700 и 1250…1300 С) и называются полуметодическими.
Электрические нагревательные устройства. Индук-
ционный нагрев основан на возникновении в заготовке, помещенной в переменное электромагнитное поле, вихревых
67
токов, которые и нагревают заготовку. Индуктор в виде многовиткового соленоида по диаметру заготовки выполняют из медной трубки, охлаждаемой водой.
Электроконтактный нагрев, основанный на выделении тепла при прохождении тока через заготовку (по закону Джоуля Ленца), применяют при нагревании стальных заготовок диаметром до 75 мм. Используемое напряжение 5…15 В, сила тока до 5000 А. Концы заготовки, зажатые между медными токоподводящими контактами, нагреваются ниже средней ее части на 200…300 С. Поэтому данный метод рационально использовать для нагрева стальных заготовок постоянного сечения и значительной длины.
Скорость электронагрева в 8–10 раз выше, а интенсивность образования окалины в 4–5 раз меньше, чем при нагреве в печах.
7. Способы обработки металлов давлением
Процессы обработки металлов давлением по назначению подразделяют на два вида:
для получения заготовок постоянного поперечного сечения по длине (прутков, проволоки, лент, листов), применяемых в строительных конструкциях или в качестве заготовок для последующей обработки резанием или давлением. Основными разновидностями таких процессов являются прокатка, прессование и волочение;
для получения деталей или заготовок (полуфабрикатов), имеющих формы и размеры готовых деталей и требующих обработки резанием лишь для придания им окончательных размеров и получения поверхности заданного качества. Основными разновидностями таких процессов являются ковка и штамповка.
68

7.1. Прокатное производство
Сущность процесса прокатки
Прокатка вид обработки давлением, при котором заготовка обжимается двумя вращающимися навстречу друг другу валками прокатного стана (рис. 28).
Деформация металла при прокатке происходит на небольшом участке АВВ1А1 (см. рис. 28, а), который называется зоной деформации.
Рис. 28. Схемы основных видов прокатки
Дуга АВ называется дугой захвата, а центральный угол, отвечающий дуге АВ, углом захвата.
При прокатке увеличиваются длина и ширина заготовки и уменьшается ее толщина. Относительное уменьшение тол-
щины заготовки в процессе прокатки h0 h1 называется h0
относительным обжатием или степенью деформации (%).
Максимальное значение относительного обжатия в зависимости от типа изделия составляет 0,2…0,5. Уширение заготовки в процессе прокатки составляет 5…10 % от обжатия.
Отношение длины заготовки после прокатки l1 к исходной l0 , равное отношению площадей поперечного сечения
первоначального F0 к полученному F1, называется коэффи-
циентом вытяжки :
69
μ = l1/l0 = F0 /F1.
Это одна из основных характеристик процесса прокатки. Значение за один проход заготовки составляет обычно 1,1…1,6, а иногда достигает 2…2,5.
Условия захвата заготовки валками. При прокатке ме-
талл втягивается в зазор между валками силами трения между заготовкой и валками. В точках А и А1 действуют силы давления валков на металл N и силы трения Т, проекции которых на ось х соответственно Nx N sin α, Tx = cos α
(см. рис. 28, а). Валки захватят металл тогда, когда втягивающее усилие будет больше, чем выталкивающее: Tx Nx .
Учитывая, что сила трения T fN, где f коэффициент
трения, который зависит от состояния поверхности валков и заготовки и уменьшается с ростом температуры, условие захвата заготовки примет вид sin α < f cos α, или tg α f .
При горячей прокатке на гладких валках угол захвата составляет 15…24 , а на валках с вырезами (ручьями) 32…33 . При холодной прокатке листов α = 3…10 .
Основные виды прокатки. Различают продольную, поперечную и поперечно-винтовую прокатку.
При продольной прокатке (см. рис. 28, а) заготовка перемещается перпендикулярно к осям валков, которые вращаются в противоположных направлениях. До 90 % всего проката изготовляютпродольнойпрокаткой (листы, полосы, прутки).
При поперечной прокатке (см. рис. 28, б) валки с параллельными осями вращаются в одном направлении и вращают заготовку, котораядеформируется, перемещаясьвдольосивалков.
Поперечно-винтовая прокатка (см. рис. 28, в) осуществляется вращающимися в одном направлении и расположенными под углом один к другому валками. Такое расположение валков обеспечивает возникновение осевого усилия, перемещающего заготовку.
70