
Технология конструкционных материалов. Способы получения деталей (за
.pdfIX. ТЕХНОЛОГИЧЕСКИЙ ПРОЦЕСС ИЗГОТОВЛЕНИЯ ДЕТАЛЕЙ ИЗ МЕТАЛЛИЧЕСКИХ ПОРОШКОВ
При разработке материалов и изготовлении деталей методом порошковой металлургии используют порошки металлов и их сплавов или неметаллических веществ. Технология порошковой металлургии включает в себя следующие этапы: получение порошков, подготовку их к формованию, изготовление смеси порошков, формование из них заготовок, спекание заготовок и при необходимости дополнительную обработку спеченных изделий. Метод порошковой металлургии позволяет получать материалы, которые другими методами получить невозможно: из металлов со значительной разницей в температуре плавления (например W Сu, W Ag, Мо Сu), из металлов и неметаллов (бронза графит), из химичеcких соединений (твердые сплавы из карбидов WC, TiC и др.), материалы с заданной пористостью (вкладыши подшипников, фильтры), электрическими, магнитными и другими свойствами.
Порошковая металлургия, кроме того, отличается минимальными отходами материалов, позволяет резко сократить станочный парк и число рабочих для производства деталей.
1. Получение порошков
Для изготовления спеченных изделий применяют порошки размером от 0,5 до 500 мкм. Получают такие порошки механическими и химическими методами.
Механические методы. К ним относятся: распыление жидкого металла, размол стружки и других отходов металлообработки, дробление в вибрационной мельнице.
221
Распыление жидкого металла осуществляется струей воды или газа под давлением 50...100 МПа. Этим методом получают порошки железа, ферросплавов, нержавеющей стали, жаропрочных сплавов, цветных металлов.
Размол отходов металлообработки осуществляют в вихревых или шаровых мельницах.
Дробление в вибрационной мельнице применяют для получения порошков из твердых и хрупких материалов (карбидов, оксидов, керамики и др.).
Химические методы заключаются в восстановлении металлов из оксидов или солей углеродом, водородом, природным газом. Восстановлением получают порошки железа (из окалины), вольфрама, молибдена, хрома, меди и других металлов. Сюда же относится метод термической диссоциации карбонилов – соединений типа Мех(СО)у (где Ме – один из металлов), обеспечивающий получение порошков высокой чистоты.
Этим методом получают порошки железа, никеля, кобальта и некоторых других металлов.
2. Подготовка порошков к формованию
Для получения качественных заготовок или деталей порошки предварительно отжигают, разделяют по размерам частиц, смешивают.
Отжиг порошка способствует восстановлению оксидов, удалению углерода и других примесей, а также устранению наклепа, что стабилизирует его свойства и улучшает прессуемость. Отжигу чаще подвергают порошки, полученные механическим измельчением.
Порошки размером более 50 мкм разделяют с помощью набора сит с различным сечением ячеек, а более мелкие – воздушной сепарацией. Конечные свойства порошковых из-
222

делий в значительной степени определяются качеством смешивания компонентов шихты. Эта операция обычно осуществляется в специальных смесителях, шаровых или вибрационных мельницах и другими способами.
В ряде случаев в порошковую массу вводят различные технологические наполнители, улучшающие прессуемость порошков (например, раствор каучука в бензине), обеспечивающие получение заготовок экструдированием (выдавливанием) или их механическую обработку (парафин, воск), получение заготовок литьем (спирт, бензол) и др.
3. Формовка заготовок
Процесс формования заготовок состоит в уплотнении порошка под действием приложенного давления с целью получения из него заготовок определенной формы. Формование
осуществляется |
прессованием, |
|
|
|
|
|
|
|
|
|
|
|
||
экструдированием, прокаткой. |
|
|
|
|
Р |
|
|
|
Р |
|
||||
Прессование обычно про- |
|
|
|
|
|
|
|
|
|
|
|
|||
изводится в холодных или го- |
4 |
|
|
|
|
|
|
|
|
|
||||
рячих пресс-формах. Крупные |
3 |
|
|
|
|
|
|
|
|
|
||||
заготовки |
получают гидроста- |
2 |
|
|
|
|
|
|
|
|
|
|||
тическим способом. |
1 |
|
|
|
|
|
|
|
|
|
||||
Холодное прессование за- |
|
|
|
|
|
|
|
|
|
|
|
|||
|
|
|
|
|
|
|
|
|
|
|
||||
|
|
|
|
|
|
|
|
|
Р |
|
||||
|
|
|
|
|
|
|
|
|
|
|||||
ключается |
в |
следующем |
|
|
|
|
|
|
|
|
|
|
|
|
|
|
|
|
|
|
|
|
|
|
|
||||
|
|
|
|
|
|
|
|
|
|
|
||||
|
|
а |
|
|
б |
|||||||||
(рис. 105). В стальную матрицу |
|
|
|
|
||||||||||
Рис. 105. Схемы холодного |
||||||||||||||
3 пресс-формы с поддоном 1 |
||||||||||||||
засыпают |
определенное коли- |
прессования: а – односторон- |
||||||||||||
чество порошковой шихты 2 |
|
|
неe; б – двустороннее |
|||||||||||
|
|
|
|
|
|
|
|
|
|
|
и прессуют ее пуансоном 4. При этом резко уменьшается объем порошка, увеличивается контакт между отдельными частицами, происходит механическое их сцепление. Поэтому прочность прессовки повышается, а пористость уменьшается.
223
Недостатком такой схемы прессования является неравномерность распределения давления по высоте заготовки из-за трения ее о стенки матрицы 3. Поэтому заготовки, полученные в таких пресс-формах, обладают различной прочностью, плотностью и пористостью по высоте. Таким способом получают заготовки простой формы и небольшой высоты.
Для устранения этого недостатка применяют двустороннее прессование с помощью двух подвижных пуансонов 4. При такой схеме, кроме того, давление прессования умень-
шается на 30...40 %.
В зависимости от требуемой пористости и прочности материала заготовки, а также ее формы давление прессования составляет 0,1...1 ГПа.
Горячее прессование совмещает формование и спекание заготовок. Этот процесс осуществляется в графитовых прессформах при индукционном или электроконтактном нагреве. Благодаря высокой температуре давление при горячем прессовании можно значительно уменьшить.
Горячее прессование отличается малой производительностью, большим расходом пресс-форм, поэтому применяется, главным образом, для получения заготовок из жаропрочных материалов, твердых сплавов, чистых тугоплавких металлов (W, Мо).
Гидростатическое прессование заключается в обжатии порошка, помещенного в эластичную (например, резиновую) оболочку, с помощью жидкости в гидростате под давлением до 2 ГПа. Этот метод позволяет получать крупногабаритные заготовки типа цилиндров и труб с равномерной плотностью по всему объему.
Экструдированием называется процесс формования заготовок выдавливанием шихты через матрицу с отверстиями различного сечения (рис. 106). Для этого исходный порошок
224
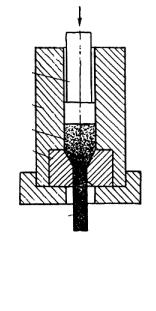
замешивают с пластификатором (парафином, воском) в количестве, обеспечивающем шихте консистенцию пластилина. Этим способом получают прутки, Р профили различного сечения. Для получения полых изделий (труб и др.) в матрице располагают соответствующую оправку.
Прокатка осуществляется путем обжатия порошковой шихты между горизонтально расположенными валками. Этим способом получают пористые и компактные ленты, полосы и листы толщиной 0,02...3 мм и шириной до 300 мм из железа, никеля, нержавеющей стали, титана и других металлов. Процесс прокатки легко совмещается со спеканием и другими видами обработки. Для
этого полученную заготовку пропускают через проходную печь и затем подают на прокатку с целью калибровки.
Прокаткой можно получать и двухслойные заготовки (например, железо медь). Для этого в бункере необходимо установить перегородку для разделения его на две секции вдоль вaлков.
4. Cпeканиe и дополнительная обработка заготовок
Для повышения прочности сформованные из порошков заготовки подвергаются спеканию. Эта операция осуществляется в печах электросопротивления или индукционных с нейтральной или защитной средой в течение 30...90 мин при температуре около 2/3 температуры плавления основного
225
компонента. В процессе спекания происходит восстановление поверхностных оксидов, развиваются диффузионные явления, образуются новые контактные поверхности.
При необходимости повышения точности размеров и уплотнения поверхностного слоя спеченные детали подвергают калиброванию – дополнительному прессованию в стальных пресс-формах или продавливанию прутка через калиброванное отверстие в матрице.
Спеченные заготовки можно обрабатывать резанием – точением, фрезерованием, сверлением. В связи с их пористостью не следует применять смазывающе-охлаждающие жидкости, которые, проникая в поры, могут вызвать внутреннюю коррозию материала. Если выход пор на поверхность необходимо сохранить (например, у вкладышей подшипников), обработку спеченных деталей нужно производить хорошо заточенным режущим инструментом.
Спеченные детали из сплавов на основе железа, титана, никеля и других металлов могут также подвергаться различным видам термической или химико-термической обработки.
При конструировании деталей из порошков следует не допускать значительной разностенности, так как вследствие большой усадки может произойти коробление детали. Необходимо избегать выступов, пазов и отверстий, расположенных перпендикулярно к оси прессования, а также острых углов. В местах сопряжения элементов детали типа фланец цилиндр предусматривают закругления радиусом не менее 0,25 мм. Наружные и внутренние резьбы получают обработкой резанием.
Толщина стенок детали должна быть не менее 1 мм.
226
X. ТЕХНОЛОГИЧЕСКИЕ ОСОБЕННОСТИ ИЗГОТОВЛЕНИЯ ДЕТАЛЕЙ ИЗ КОМПОЗИЦИОННЫХ МАТЕРИАЛОВ
Процесс формообразования деталей из композиционных материалов сопровождается значительной усадкой, поэтому в их конструкциях нельзя допускать значительной разностенности, которая вызывает коробление и образование трещин. Разностенность не должна превышать 1 : 3. В зависимости от габаритных размеров детали, используемого материала и других факторов оптимальной толщиной стенок считается 0,5…5 мм, а минимальными радиусами сопряжений 0,5…2 мм.
Отверстия в деталях получают при формообразовании (литьем, прессованием и т.д.) соответствующими стержнями, устанавливаемыми в технологической оснастке (прессформах). Отверстия лучше располагать не в сплошных массивах, а в специальных бобышках с тонкими стенками, что снижает усадку и силу обхвата стержней.
В деталях из композиций на основе пластмасс литьем под давлением и прессованием получают наружные и внутренние резьбы, не требующие дальнейшей обработки.
Использование металлической арматуры значительно расширяет область применения деталей из композиционных материалов (особенно на основе пластмасс и резины). Например, в электро-, радиопромышленности прессованием и литьем под давлением получают электрические разъемники, колодки, панели и т.д.
Формообразование заготовок из композиционных материалов в большинстве случаев осуществляется методом копирования, т.е. форма и размеры оснастки (пресс-формы) переносятся (копируются) изготовляемой деталью. Получаемые
227
детали, как правило, не требуют дальнейшей механической обработки.
Иногда возникает необходимость в дополнительной обработке заготовок, полученных литьем, прессованием и другими методами формообразования.
Обработку резанием (точение, сверление, фрезерование, нарезание резьбы и т.д.) применяют в тех случаях, когда при формообразовании нельзя получить деталь заданных размеров и формы.
Для обработки тугоплавких и жаропрочных материалов применимы электрофизические и электрохимические методы обработки аналогичных литых материалов.
Значительные сложности возникают при обработке металлических композиционных материалов (МКМ), так как они в своем составе содержат относительно «мягкий» материал матрицы и сверхпрочные и твердые волокна и нитевидные кристаллы. Традиционные способы механической обработки оказываются непригодными. В отдельных случаях для обработки таких материалов применяют лазерные, плазменные, электроэрозионные и другие специальные методы обработки.
При обработке резанием композиционных материалов на основе полимеров происходит разрушение поверхностной смоляной пленки. Это приводит к снижению химической стойкости и повышению влагопоглощения обработанных деталей. Поэтому обработку резанием следует применять только в необходимых случаях.
По способу изготовления композиционные материалы (КМ) подразделяют на полученные жидко- и твердофазными методами, методами осаждения-напыления и комбинированными методами. К жидкофазным методам относят пропитку арматуры полимером или жидким металлом, а также направ-
228

ленную кристаллизацию. К твердофазным методам относятся прессование, прокатка, экструзия, ковка, сварка взрывом, волочение, диффузионная сварка, при которых компоненты формируются в КМ, где в качестве матрицы используют порошки или тонкие листы (фольги). При получении КМ осаждением-напылением матрица наносится на волокна из раствора солей, парогазовой фазы, плазмы. Комбинированные методы предусматривают совмещение нескольких методов. Например, пропитку или плазменное распыление используют в качестве предварительной операции, а прокатку, прессование или диффузионную сварку окончательной.
Пропиткой волокон расплавленным металлом или термореактивными смолами получают изделия любой конфигурации без дополнительной механической обработки (рис. 107). Прочность связи компонентов определяется сма-
Рис. 107. Схема устройства для укладки волокон: 1 непрерывные волокна; 2 бункер для подачи пластмассы; 3 формирующий ролик; 4 нагреваемая поверхвность; 5 направляющие пазы
чиваемостью поверхности армирующего элемента жидкой матрицей. Пропитку проводят при нормальном давлении, вакуумным всасыванием, под давлением и комбинированным методом.
229
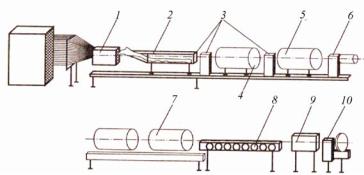
Наиболее перспективный метод это непрерывная пропитка волокон расплавленным металлом или термореактивными смолами с формованием профиля протягиванием КМ через фильеру (рис. 108).
В твердофазных методах получения КМ материал матрицы имеет вид порошка, фольги, листов, ленты; волокна могут быть непрерывные, дискретные, в виде ткани и жгутов. Для получения КМ используют высокопроизводительные процессы обработки давлением: прокатку (теплую и горячую), прессование в пресс-формах с обогреваемыми плитами, динамическое горячее прессование, горячее прессование, экструзию, взрывное компактирование, диффузионную сварку. В качестве исходных заготовок для обработки в твердой фазе могут использоваться КМ, полученные литьем или методом осаждения-напыления.
Рис. 108. Схема изготовления пропиткой волокнистых КМ с полимерной матрицей: 1 предварительная сушка волокон; 2 ванна с термореактивной смолой; 3 формующие фильеры; 4 полимеризатор; 5 печь; 6 формующая фильера; 7 печь; 8 охладитель; 9 тянущееустройство; 10 устройство длярезкинамерныедлины
Кроме волокон в качестве армирующих элементов используют также нитевидные кристаллы, получаемые осаждением из газовой фазы, выращиванием в электрическом поле,
230