
Технология конструкционных материалов. Способы получения деталей (за
.pdf9 групп (табл. 3) (токарные, сверлильные и расточные, шлифовальные, полировальные и доводочные и т.д.).
3. Каждая группа разделена на 9 типов по таким основным признакам:
технологическое назначение (круглошлифовальный, плоскошлифовальный);
конструктивные особенности (универсально-фрезер- ные, продольно-фрезерные);
расположение рабочих органов в пространстве (верти- кально-сверлильные, горизонтально-сверлильные);
количество рабочих органов станка (одношпиндельные, многошпиндельные);
степень автоматизации (с ручным управлением, полуавтоматы, автоматы истанки с программнымуправлением).
4.По степени точности станки разделены на 5 классов: нормальной точности (Н), повышенной точности (П), высокой точности (В), особовысокой точности (А) и особоточные станки (С).
5.По массе станки разделяют на легкие (до 1 т), средние (до 10 т), тяжелые (до 100 т) и уникальные (свыше 100 т).
Обозначения металлорежущих станков. В соответст-
вии с принятой классификацией (см. табл. 3) каждому станку присваивается определенный шифр, состоящий из трех или четырех цифр. Первая цифра указывает номер группы станка,
вторая тип станка в этой группе. Третья или третья и четвертая цифры характеризуют основной параметр станка. Для токарных станков они указывают высоту центров; для револьверных станков и автоматов наибольший диаметр обрабатываемого прутка; для сверлильных наибольший диаметр отверстия, которое может быть просверлено на этом станке в стали средней твердости. Иногда это обозначение
161
162
Таблица 3
Классификация металлорежущих станков
|
|
|
|
|
|
|
|
|
|
|
Группа |
Шифр |
|
|
|
Тип станка |
|
|
|
|
|
станков |
груп- |
1 |
2 |
3 |
4 |
5 |
6 |
7 |
8 |
9 |
|
пы |
|
|
|
|
|
|
|
|
|
Токарные |
1 |
Автоматы |
Револьвер- |
Сверлиль- |
Кару- |
Токарные |
Много- |
Специа- |
|
|
|
|
и полуавтоматы |
ные |
но-отрез- |
сельные |
и лобовые |
резцовые |
лизиро- |
|
|
|
|
одношпин- |
много- |
|
ные |
|
|
|
ванные |
|
|
|
дельные |
шпиндель- |
|
|
|
|
|
|
|
|
|
|
ные |
|
|
|
|
|
|
группы |
Сверлиль- |
2 |
Вертикаль- |
Полуавто- |
Полуавто- |
Коорди- |
Ради- |
Горизон- |
Алмазно- |
Горизон- |
|
ные и |
|
но- |
маты од- |
маты мно- |
натно- |
ально- |
тально- |
расточ- |
тально- |
|
расточные |
|
сверлиль- |
ношпин- |
гошпин- |
расточные |
свер- |
расточные |
ные |
сверлиль- |
|
вальные, |
|
ные |
дельные |
дельные |
лизиро- |
лильные |
|
шлифо- |
ные |
станки |
|
шлифо- |
шлифо- |
но-шли- |
|
|
рочные |
||||
Шлифо- |
3 |
Кругло- |
Внутри- |
Обдироч- |
Специа- |
– |
Заточные |
Плоско- |
Прити- |
|
полиро- |
|
вальные |
вальные |
фовальные |
ванные |
|
|
вальные |
и полиро- |
Разные |
и дово- |
|
|
|
|
вальные |
|
|
|
вочные |
|
вальные |
|
|
|
|
шлифо- |
|
|
|
|
|
дочные |
|
|
|
|
|
|
|
|
|
|
Для элек- |
4 |
Универ- |
Полуавто- |
Автоматы |
Электро- |
Элек- |
– |
Электро- |
Анодно- |
|
трофизи- |
|
сальные |
маты |
|
химиче- |
троиск- |
|
эррози- |
механи- |
|
ческой и |
|
|
|
|
ские |
ровые |
|
онные, |
ческие |
|
электро- |
|
|
|
|
|
|
|
ультра- |
|
|
химиче- |
|
|
|
|
|
|
|
звуковые |
|
|
ской об- |
|
|
|
|
|
|
|
|
|
|
работки |
|
|
|
|
|
|
|
|
|
|
162
Окончание табл. 3
|
|
|
|
|
|
|
|
|
|
|
Группа |
Шифр |
|
|
|
Тип станка |
|
|
|
|
|
станков |
группы |
1 |
2 |
3 |
4 |
5 |
6 |
7 |
8 |
9 |
|
|
|
|
|
|
|
|
|
|
|
Зубо- |
5 |
Зубостро- |
Зуборез- |
Зубофре- |
Зубофрезер- |
Для |
Резьбо- |
Зубоот- |
Зубо- |
|
и резь- |
|
гальные |
ные для |
зерные |
ные для чер- |
обра- |
фрезер- |
делоч- |
и резь- |
|
бо- |
|
для ци- |
кониче- |
для ци- |
вячных колес |
ботки |
ные |
ные |
бошли- |
|
обраба- |
|
линдриче- |
ских колес |
линдриче- |
|
торцов |
|
|
фоваль- |
|
тываю- |
|
ских колес |
|
ских колес |
|
зубьев |
|
|
ные |
|
щие |
|
|
|
и шлице- |
|
колес |
|
|
|
|
|
|
|
|
вых вали- |
|
|
|
|
|
|
|
|
|
|
ков |
|
|
|
|
|
|
Разные |
9 |
Муфто- и |
Пилонасе- |
Правиль- |
|
Для |
Дели- |
Баланси- |
– |
|
|
|
трубооб- |
кательные |
но- и бес- |
|
испыта- |
тельные |
ровоч- |
|
|
|
|
рабаты- |
|
центрово- |
|
ния |
машины |
ные |
|
|
|
|
вающие |
|
обдироч- |
|
инстру- |
|
|
|
|
|
|
|
|
ные |
|
мента |
|
|
|
|
163
163
дополняется буквами, дополнительно характеризующими станок. Буква между цифрами указывает на модернизацию базовой модели станка, а буква после всех цифр ее модификацию (видоизменение) или технологические особенности станка (например, его точность).
Пример: обозначение станка с индексом 162 свидетельствует, что станок относится к группе токарных станков (1), к шестой подгруппе (6), имеющей горизонтальное расположение шпинделя токарно-винторезный. Высота центров станка (расстояние от станины до оси шпинделя) составляет 200 мм (2), что позволяет обрабатывать детали максимальным диаметром 400 мм.
Индекс модели станка 1К62 показывает, что это модернизированный (улучшенный) станок, выполненный на базе модели станка 162. Индекс 1К62ПУ говорит о том, что это модернизированный станок, выполненный на базе станка 1К62, в отличие от которого он оснащен системой программного управления.
11.Работы, выполняемые на металлорежущих станках
иприменяемый инструмент
В данном учебном пособии будут приведены только работы, выполняемые на основной группе станков.
11.1. Обработка на токарных станках
Типы токарных станков
Токарно-винторезные станки предназначены для вы-
полнения всех основных видов токарных работ в условиях единичного и мелкосерийного производства.
Лобовые и токарно-карусельные станки применяются для обработки крупных деталей большого диаметра и относительно малой высоты.
164
Многорезцовые токарные станки применяются для из-
готовления деталей, на которых возможна одновременная обработка разных поверхностей несколькими резцами в условиях крупносерийного и массового производства.
Токарно-револьверные станки используют при обработ-
ке некрупных деталей, преимущественно с центральными отверстиями в условиях серийного производства.
Токарные автоматы и полуавтоматы применяются для обработки при крупносерийном и массовом производствах.
Токарные станки с числовым программным управлением
наиболее перспективны для автоматизации производства при мелкосерийном выпуске продукции и являются основным типом станков, предназначенных для построения гибких автоматических производств (ГАП).
Типы токарных резцов и их применение при различных видах обработки
По материалу режущей части различают резцы сталь-
ные, твердосплавные и минералокерамические.
По конструкции резцы подразделяют на цельные и составные. Цельный резец изготавливают из одной инструментальной стали. У составного резца режущая часть выполнена из твердого сплава или другого высококачественного материала, а державка – из конструкционной углеродистой или легированной стали.
По расположению главной режущей кромки резцы подразделяют на правые 1 и левые 2 (рис. 78).
По расположению оси головки резца в плане относительно оси его тела различают резцы прямые 3, 4, 5, 6, 7, 8, 10, 11, отогнутые 9, 13, 14, 15 и резцы с оттянутой головкой 3, 5.
165

По характеру обработки, для которой они предназначены, различают резцы черновые и чистовые.
Рис. 78. Типы токарных резцов
По назначению резцы подразделяются на проходные 4, 7, 8, 9 и проходные упорные 11, применяемые при обработке наружных поверхностей тел вращения; подрезные 12, используемые при обработке торцевых поверхностей; отрезные 3, 5, предназначенные для разрезания заготовок или отрезания готовой детали от заготовки. Если отрезной резец при своем перемещении не доведен до оси, то на детали будет образована канавка различного профиля (прямоугольного резец 5, трапецеидального резец 6). Такие резцы, называемые еще и канавочными, имеют ширину, соответствующую ширине нарезаемой канавки.
Расточные резцы 13, 14 применяются для растачивания в заготовке соответственно сквозных и глухих отверстий.
Фасонные 17, 18 резцы имеют специально спрофилированную режущую кромку, профиль которой копируется на обрабатываемой заготовке 16. В качестве одной из разновидностей фасонных резцов можно назвать резьбовые резцы для нарезания наружной 10 и внутренней 15 резьб.
166

Наружные короткие конические поверхности, в том числе и фаски, обрабатываются широким резцом, главный угол в плане которого равен углу уклона обрабатываемого конуса (рис. 79, а, б). При этом резец перемещают с поперечной или продольной подачей. Максимальная длина конуса не более 20 мм и определяется шириной резца.
Обработка наружных и внутренних конусов с большим углом уклона и шириной более 20 мм производится за счет поворота верхнейчасти суппорта срезцедержателем (рис. 79, в).
|
|
|
|
|
|
|
|
|
|
|
|
|
|
|
|
|
|
|
|
|
|
|
|
|
|
|
|
|
|
|
|
|
|
|
|
|
|
||
|
|
|
|
|
|
|
|
|
|
|
|
|
|
|
|
|
|
|
|
|
|
|
|
|
|
|
|
|
|
|
|
|
|
|
|
|
S |
||
|
|
|
|
|
|
|
|
|
|
|
|
|
|
|
|
|
|
|
|
|
|
|
|
|
|
|
|
|
|
||||||||||
V |
|
|
|
|
|
|
|
|
|
|
|
|
|
|
|
|
|
L |
|
|
|
|
|
|
|
|
|
|
|||||||||||
|
|
|
|
|
|
|
|
|
|
|
|
|
|
|
|
|
|
|
|
|
|
|
|
|
|
|
|
|
|
|
|
|
|
||||||
|
|
|
|
|
|
|
|
|
|
|
|
|
|
|
|
|
|
|
|
|
|
|
|
|
|
|
|
|
|
|
|
|
|
|
|
|
|||
|
|
|
|
|
|
|
|
|
|
|
|
|
|
|
|
|
|
|
|
|
|
|
|
|
|
|
|
|
|
|
|
|
|
|
|
|
|
||
|
|
|
|
|
|
|
|
|
|
|
|
|
|
|
|
|
|
|
|
|
|
|
|
|
|
|
|
|
|
|
|
|
|
|
|
|
|
|
|
|
|
|
|
|
|
|
|
|
|
|
|
|
|
|
|
|
|
|
|
|
|
|
|
|
|
|
|
|
|
|
|
|
|
||||||
|
|
|
|
|
|
|
|
|
|
|
|
|
|
|
|
|
|
|
|
|
S |
|
|
|
|
|
|
|
|
|
|
|
|
|
|
|
|||
|
|
|
|
|
|
|
|
|
|
|
|
|
|
|
|
|
|
|
|
|
|
|
|
|
|
|
|
|
|
|
|
|
|
|
|
|
|||
|
|
|
|
|
|
|
|
|
|
|
|
|
|
Sп |
|
|
|
|
|
|
|
|
|
|
|
|
|
|
|
|
|
|
|
|
|
|
|||
|
|
|
|
|
|
|
|
|
|
|
|
|
|
|
|
|
|
|
|
|
|
|
|
|
|
|
|
|
|
|
|
|
|
|
|||||
|
|
|
|
|
|
|
|
|
|
|
|
|
S |
|
|
|
|
|
|
|
|
|
|
|
|
|
|
|
|
|
|
||||||||
|
|
|
|
|
|
|
|
|
|
|
Sпр |
|
|
|
|
|
|
|
|
|
|
|
|
|
|
|
|
|
|
|
|
|
|||||||
|
|
|
|
|
|
|
|
|
|
|
|
|
|
|
|
|
|
|
|
|
|
|
|
|
|
|
|
|
|||||||||||
|
|
|
|
|
|
|
|
|
|
|
|
|
|
|
|
|
|
|
|
|
|
|
|
|
в |
|
|
|
|
|
|
||||||||
|
|
|
|
|
|
|
|
|
|
|
|
|
|
|
|
|
|
|
|
|
|
|
|
|
|
|
|
||||||||||||
|
|
а |
|
|
|
|
|
|
|
|
|
|
|
|
|
|
|
|
|
|
|
||||||||||||||||||
|
|
|
|
б |
|
|
|
|
|
|
|
|
|
|
|
|
|
|
|
|
|||||||||||||||||||
|
|
|
|
|
|
|
|
|
|
|
|
|
|
|
|
|
|
|
|
|
|
|
|
|
|
|
|||||||||||||
|
|
|
|
|
|
|
|
|
|
|
|
|
|
|
|
|
|
|
|
|
|
|
|
|
|
|
|
|
|
|
|
|
|
|
|
||||
|
|
|
|
|
|
|
|
|
|
|
|
|
|
|
|
|
|
|
|
|
|
|
|
|
|
|
|
|
|
|
|
|
|
|
|
|
|
|
|
|
|
|
|
|
|
|
|
|
|
|
|
|
|
|
|
|
|
|
|
|
|
|
|
|
|
|
|
|
|
|
|
|
|||||||
|
|
|
L |
|
|
|
|
|
|
|
|
|
|
|
|
|
|
|
|
|
|
|
|
|
|
|
|
|
|
|
|
|
|
|
|||||
|
|
|
|
|
|
|
|
|
|
|
|
|
|
|
|
|
|
|
|
|
|
|
1 |
|
|
|
|
|
|||||||||||
|
|
|
|
|
|
|
|
|
|
|
|
|
|
|
|
|
|
|
|
|
|
|
|
|
|
|
|
||||||||||||
|
|
|
|
|
|
|
|
|
|
|
|
|
|
|
|
|
|
|
|
|
|
|
|
|
|
3 |
|
|
|
|
|
|
|
|
|
|
|
|
|
|
|
|
|
|
|
|
|
|
|
|
|
|
|
|
|
|
|
|
|
|
|
|
|
|
|
|
|
|
|
|
|
|
|
|
|
|
|
|
|
|
|
|
|
|
|
|
|
|
|
|
|
|
|
|
|
|
|
|
|
|
|
|
|
|
|
|
|
|
|
|
|
|
|
|
|
|
|
||
|
|
|
|
|
|
|
|
|
|
|
|
|
|
|
|
|
|
|
|
|
|
|
|
|
|
|
|
|
|
|
|
|
|
|
|||||
|
|
|
|
|
|
|
|
|
|
|
|
|
|
|
|
|
|
|
|
|
|
|
|
|
|
|
2 |
|
|
|
|||||||||
|
|
|
|
|
|
|
|
|
|
|
h |
|
|
|
|
|
|
|
|
|
|
|
|
|
|
|
|
|
|
|
|
|
|
||||||
|
|
|
|
|
|
|
|
|
|
|
|
|
|
|
|
|
|
|
|
|
|
|
|
|
|
|
|
|
|
|
|
||||||||
|
|
|
|
|
|
|
|
|
|
|
|
|
|
|
|
|
|
|
|
|
|
|
|
|
|
|
|
|
|
|
|
|
|||||||
|
|
|
|
|
|
|
|
|
|
|
|
|
|
|
|
|
|
|
|
|
|
|
|
|
|
|
|
|
|
|
|
|
|
|
|
|
|
|
|
|
|
S |
|
|
|
|
|
|
|
|
|
|
|
|
|
|
|
|
|
|
|
|
|
|
|
|
|
|
|
|
|
|
|
|
|
||||
|
|
|
|
|
|
|
|
|
|
|
|
|
|
|
|
|
|
|
|
|
|
|
|
|
|
|
|
|
|
|
|
|
|
|
|
|
|||
|
|
|
|
|
|
|
х |
|
|
|
|
|
|
|
|
|
|
|
|
|
|
|
|
|
|
|
|
|
|
|
|
|
|
|
|
||||
|
|
|
|
|
|
|
х |
|
|
|
|
|
|
|
|
|
|
|
|
|
|
|
|
|
|
|
|
|
|
|
|
|
|
|
|
|
|||
|
|
|
|
|
|
|
|
|
|
|
|
|
|
|
|
|
|
|
|
|
|
|
|
|
|
|
|
|
|
|
|
|
|
|
|
|
|
|
|
|
|
|
|
|
|
|
г |
|
|
|
|
|
|
|
|
|
|
Sпр |
|
|
|
|
|
|
|
|
|
|
|
|
|
|
|||||||
|
|
|
|
|
|
|
|
|
|
|
|
|
|
|
|
д |
|
|
|
|
|
|
|
|
|||||||||||||||
|
|
|
|
|
|
|
|
|
|
|
|
|
|
|
|
|
|
|
|
|
|
|
|
|
|
|
|
|
|
|
Рис. 79. Обработка конических поверхностей
Длинные конические поверхности с малым углом конусности (2 8 ) обрабатываются способом смещения задней бабки станка, в которой закреплено сверло (рис. 79, г). При этом величина смещения задней бабки
h L D d 2l или h Ltgα,
где L, l длина обрабатываемой детали и длина ее конической части, мм;
D, d больший и меньший диаметр конуса, мм;
αугол наклона конуса, град.
167
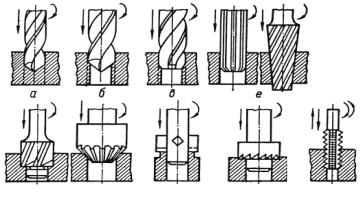
Для обработки длинных конусов с углом наклона до 10 12 применяется обработка с помощью копировальной линейки 1 (рис. 79, д), закрепляемой на станине станка 2. Суппорту дают продольную подачу, обеспечивающую перемещение резца. Заданный угол обеспечивается углом установки копировальной линейки, по прорези которой скользит ползун 3, связанный с суппортом и резцедержателем станка.
11.2. Обработка заготовок на сверлильных станках
Основные работы, выполняемые на сверлильных станках
На сверлильных станках выполняют следующие виды работ:
сверление (рис. 80, а) один из самых распространенных способов образования отверстий в сплошном материале
спомощью сверл;
рассверливание (рис. 80, б) процесс увеличения диаметра имеющихся отверстий сверлом;
– зенкерование (рис. 80, в) – обработка цилиндрических, литых, штампованных или предварительно просверленных
а |
|
б |
|
в |
|
г |
|
|
д |
е |
ж |
з |
|
Рис. 80. Схемы обработки отверстий |
|
168

зенкером отверстий для придания им правильной геометрической формы, необходимых размеров и малой шероховатости поверхности;
– развертывание (рис. 80, г) – обработка отверстий для получения точных размеров и малой шероховатости поверхности;
зенкование (рис. 80, д) образование цилиндрических или конических углублений в предварительно просверленных отверстиях под головки болтов, винтов или других деталей
спомощью цилиндрическихи конических зенкеров(зенковок);
цекование (рис. 80, е, ж) обработка торцевых поверхностей под гайки, шайбы и кольца ножами (пластинами) или торцевыми зенкерами;
нарезание резьбы в отверстиях метчиками (рис. 80, з).
Инструменты для обработки отверстий
Для обработки отверстий на сверлильных станках применяют следующий инструмент: сверла, зенкеры, зенковки, развертки, метчики. Основным инструментом является сверло.
В зависимости от назначения сверла по конструкции подразделяются на следующие типы:
1) спиральные для работы на сверлильных, токарных, револьверных и других металлорежущих станках (рис. 81, а);
|
|
|
|
|
|
|
|
|
|
|
|
|
|
|
|
l3 |
|
|
|
|
|
|
|
|
|
|
|
|
|
|
|
|
|
|
|
|
|
|
|
|
|
|
|
|
|
|
|
|
|
|
|
l1 |
|
|
|
|
|
|
|
|
|
|
l4 |
|
l5 |
|
|
|
|
|
|
|
|
|
|
|
|
|
|
|
|
||||
|
|
|
l2 |
|
|
|
|
|
|
|
|
|
|
|
|
|
|
|
|
|
|
|
|
|
|
|
|
|
|
|
|
|
||||||||||
2 |
|
|
|
|
|
|
|
|
|
|
|
|
|
|
|
|
|
|
|
|
|
|
|
|
|
|
|
|
|
|
|
|
|
|
|
|
|
|
|
|
|
|
|
|
|
|
|
|
|
|
|
|
|
|
|
|
|
|
|
|
|
|
|
|
|
|
|
|
|
|
|
|
|
|
|
|
|
|
|
|
|
|
|||
|
|
|
|
|
|
|
|
|
|
|
|
|
|
|
|
|
|
|
|
|
|
|
|
|
|
|
|
|
|
|
|
|
|
|
|
|
|
|
|
в |
|
|
|
|
|
|
|
|
|
|
|
|
|
|
|
|
|
|
|
|
|
|
|
|
|
|
|
|
|
|
|
|
|
|
|
|
|||||||||
|
|
|
|
|
|
|
|
|
|
|
|
|
|
|
|
|
|
|
1 |
|
|
|
|
|
|
|
|
|
|
|
|
|
|
|
|
|
|
|
|
|||
|
|
|
|
|
|
|
|
|
|
|
|
|
|
|
|
|
|
|
|
|
|
|
|
|
|
|
|
|||||||||||||||
|
|
|
|
|
|
|
|
|
|
|
|
|
|
|
|
|
|
|
|
|
|
|
|
|
|
|
|
|
|
|
|
|
|
|
|
|||||||
|
|
|
|
|
|
|
|
|
|
|
|
|
|
|
|
|
|
|
|
|
|
|
|
|
|
|
|
|
|
|
|
|
|
|
|
|
|
|
|
|||
|
|
|
|
|
|
|
|
В-В |
|
|
|
|
|
|
|
|
|
|
|
|
|
|
|
|
|
|
|
|
|
|
|
|
|
|
|
|
||||||
|
|
|
|
|
|
|
|
|
|
|
|
|
|
|
|
|
|
|
|
|
|
|
|
|
|
|
|
|
|
|
|
|
|
|||||||||
|
|
|
|
|
|
|
|
|
|
|
|
|
|
|
|
|
|
|
|
|
|
|
|
|
|
|
|
|
|
|
|
|
|
|
|
|
|
|
||||
|
|
|
|
|
|
|
|
|
|
|
|
|
|
|
|
|
|
|
|
|
|
|
|
|
|
|
|
|
|
|
|
|
|
|
|
|
|
|
||||
|
А-А |
|
|
|
|
|
|
|
|
|
|
|
|
|
|
|
|
|
|
|
|
|
3 |
|
|
|
|
|
|
|
|
|
|
|
|
|
|
|||||
|
|
|
|
|
|
|
|
|
|
|
|
|
|
|
|
|
|
|
|
|
|
|
|
|
|
|
|
|
|
|
|
|
|
|
|
|
|
|
|
|||
|
|
|
|
|
|
|
|
|
|
|
|
|
|
|
|
|
|
|
|
|
|
|
|
|
|
|
|
|
|
|
|
|
|
|
|
|
|
|
|
|
|
|
|
|
|
|
|
|
|
|
|
|
|
|
|
|
|
|
|
|
|
|
|
|
|
|
|
|
|
|
|
|
|
|
|
|
|
|
|
|
|
|
|
|
|
|
|
|
|
|
|
|
|
|
|
|
|
|
|
|
|
|
|
|
|
|
|
|
|
|
|
|
|
|
|
|
|
|
|
|
|
|
|
|
|
|||
|
|
|
|
|
|
|
|
|
|
|
|
|
|
|
|
|
|
|
|
|
|
|
|
|
|
|
|
|
|
|
|
|
|
|
|
|
|
|
|
|||
|
|
|
|
|
|
|
|
|
|
|
|
|
|
|
|
|
|
|
|
|
|
|
4 |
|
|
|
|
|
2 |
|
|
|
|
|
|
|
||||||
|
|
|
|
В |
|
|
|
|
|
|
|
4 |
|
|
|
|
|
|
|
|
|
|
|
|
|
|
|
|
2 |
|
|
|
|
|
|
|
|
|||||
|
|
|
|
|
А |
|
|
|
|
|
|
|
|
|
1 |
|
|
|
|
5 |
|
|
|
|
|
|
|
|
|
|
|
|
||||||||||
|
|
|
|
|
|
|
|
|
|
|
|
|
|
|
|
|
|
|
|
|
|
|
|
|
|
|
|
|
|
|
||||||||||||
|
|
|
|
|
|
а |
|
|
|
|
|
|
|
|
|
|
|
|
|
|
|
|||||||||||||||||||||
|
|
|
|
|
|
|
|
|
|
|
|
|
|
|
|
|
|
|
|
|
|
|
|
|
|
|
||||||||||||||||
|
|
|
|
|
|
|
|
|
|
|
|
|
||||||||||||||||||||||||||||||
|
|
|
|
|
|
|
|
|
|
|
б |
г |
||||||||||||||||||||||||||||||
|
|
|
|
|
|
|
|
|
|
|
|
|
|
|
|
|
|
|
|
|
|
|
|
|
|
|
|
|
|
|
|
|
|
|
|
|
|
|||||
|
|
|
|
|
|
|
|
|
|
|
|
|
|
|
|
|
|
|
|
|
|
|
|
|
|
|
|
|
|
|
|
|
|
|
|
|
|
|||||
|
|
|
|
|
|
|
|
|
|
|
|
|
|
|
|
|
|
|
|
|
|
|
|
|
|
|
|
|
|
|
|
|
|
|
|
|
|
|||||
|
|
|
|
|
|
|
|
|
|
|
|
|
|
|
|
|
|
|
|
|
|
|
|
|
|
|
|
|
|
|
|
|
|
|
|
|
|
|||||
|
|
|
|
|
|
|
|
|
|
|
|
|
|
|
|
|
|
|
|
|
|
|
|
|
|
|
|
|
|
|
|
|
|
|
|
|
|
|
Рис. 81. Сверла
169
2)перовые для сверления отверстий в твердых поковках
иотливках, обработке ступенчатых отверстий (рис. 81, б);
3) центровочные для образования центровых гнезд в заготовках, закрепляемых в центрах станка (рис. 81, в);
4) сверла для глубокого сверления однолезвийные и двухлезвийные для сверления отверстий, глубина которых превышает диаметр в 5 и более раз (рис. 81, г).
Сверла изготавливаются из быстрорежущих и инструментальных сталей, оснащаются пластинками из твердого сплава, а иногда изготавливаются целиком из твердого сплава.
Наиболее широко применяются спиральные сверла диаметром 0,1…80 мм.
Сверло состоит из рабочей части l1, шейки l3, хвостовика
l4 и лапки l5 (см. рис. 81, а).
На рабочей части различают режущую l2 и направляющую (l1 l2) части. По всей длине направляющей выполнены узкие направляющие ленточки, которые служат для направления инструмента в отверстии.
Шейка соединяет рабочую часть и хвостовик и служит для вывода шлифовального круга при обработке хвостовика и направляющих ленточек.
Хвостовик служит для закрепления сверла в шпинделе станка, а лапка упором для клина при выбивании сверла из шпинделя.
На рабочей части сверла расположены все режущие элементы: главные режущие кромки 1, поперечная режущая кромка 2, передние 3 и задние поверхности 4.
Вспомогательными режущими кромками, улучшающими качество поверхности, являются винтовые кромки направляющих ленточек 5.
170