
Технология конструкционных материалов. Способы получения деталей (за
.pdf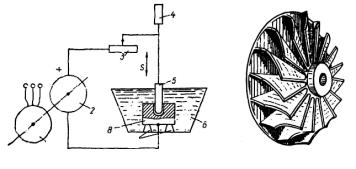
при изготовлении штампов, пресс-форм, кокилей, твердосплавных фильер, при извлечении поломанного инструмента и в некоторых иных случаях. Применение его ограничивается малой производительностью и довольно быстрым износом инструмента вследствие высокой температуры при разряде.
Электроимпульсный метод обработки
Метод заключается в последовательном возбуждении разрядов между инструментом 5 и заготовкой 8, которая на специальном приспособлении 7 размещена в ванне с диэлектрической жидкостью 6 (рис. 91, а). От приводного электродвигателя 1 движение передается генератору импульсов 2, который дает импульсы только одного направления (униполярные). Между электродом-инструментом 5 и заготовкой 8
|
|
|
|
|
|
4 |
|
|
|
|
|
|
|
|
|
3 |
|
|||
+ |
|
|
S |
|
|
|
|
|
|
5 |
|||
|
|
|
|
|
|
2 |
|
|
|
|
|
|
|
|
6 |
|
|
|
||
|
|
8 |
||
|
|
|
|
17
аб
Рис. 91. Схема установки для электроимпульсной обработки и колесо турбины, обработанное этим методом
возникают электрические разряды. Колебательное движение инструменту в направлении подачи S сообщает регулятор подачи 4. Для регулирования силы тока в цепь включено сопротивление 3. При электроимпульсной обработке заготовка является катодом, а инструмент анодом.
Температура в рабочей зоне (до 4000…5000 С) значительно ниже, чем при электроискровой обработке, поэтому
191
и инструмент срабатывается меньше. Электроды-инстру- менты изготавливают из меди, алюминия и его сплавов, чугуна, но наилучшими являются углеграфитовые электроды. Низкочастотная электроимпульсная обработка дает грубую поверхность с шероховатостью до 12,5, а высокочастотная (с частотой 7…25 кГц) 6,3…1,6. Применяется электроимпульсная обработка преимущественно при трехкоординатной обработке штампов, пресс-форм, турбинных лопаток, ручьев в валках периодического проката и др. На рис. 91, б показано обработанное электроимпульсным методом колесо турбины, обработка которого на металлорежущих станках чрезвычайно сложна.
13.2. Электрохимическая обработка
При протекании постоянного электрического тока между электродами, которые находятся в ванне с раствором электролита, происходят определенные физико-хими- ческие процессы. На одном из них анодном растворении основана электрохимическая обработка металлов. Анодное растворение заключается в том, что при прохождении постоянного тока через электролит электрод, соединенный с положительным полюсом источника тока (анод), растворяется. При этом металл анода (заготовки) на поверхности переходит в ионное состояние и выносится электролитом из рабочей зоны.
Электролитическое полирование
На поверхности детали 2, установленной в ванне 1 с электролитом 3 (рис. 92) на аноде, при прохождении тока образуется защитная пленка, предохраняющая впадины микронеровностей от его воздействия. Эта пленка не препятствует растворению микровыступов 4, 5 вследствие того, что на них действует более плотный поток электронов и поверхность детали сглаживается. Шероховатость обработанной
192

|
|
|
|
|
Вид А |
|
|
|||
|
|
|
|
|
|
|
|
|
||
|
|
|
|
увеличено |
|
|
|
|||
|
|
|
4 |
|||||||
|
|
|
|
|
|
|
|
|
|
|
|
|
|
|
|
|
|
|
|
5 |
|
|
|
|
|
|
|
|
|
|||
|
|
К |
||||||||
|
|
|
|
|
|
|
|
|
|
|
А |
|
3 |
|
|
|
|
|
|
|
|
2 |
|
|
|
|
|
|
|
|
|
|
|
|
|
|
|
|
|
|
|
|
|
1 |
|
|
|
|
|
|
|
|
|
|
Рис. 92. Схемыэлектрохимическойобработки
поверхности в производственных условиях Ra 0,8…0,1, но при обработке предварительно шлифованных поверхностей 0,05…0,012. Электролитическое полирование используется для окончательной обработки сложных по конфигурации деталей (лопатки турбин, клапаны для подачи горючего, режущие и измерительные инструменты и др.).
Полированию подвергают заготовки из черных и цветных сплавов. Его применяют для доводки поверхностей режущих мерительных инструментов, получения поверхностей под гальванические покрытия.
Эта обработка благоприятно влияет на коррозионную стойкость, усталостную прочность и предел выносливости металла, так как в поверхностном слое не только не нарушается исходная структура, но и удаляется ослабленный при предварительной обработке слой.
Электрохимическая размерная обработка
Электрохимическую размерную обработку выполняют в струе электролита (растворы солей NaCl, NaNO3 и Na2SO4), прокачиваемого под давлением через межэлектродный промежуток, образуемый обрабатываемой заготовкой-анодом 2 и инструментом-катодом 1 (рис. 93).
193

|
|
S |
|
|
|
|
|
|
|
|
|
|
|
|||
|
|
|
|
V |
|
|
|
|
||||||||
|
|
|
|
|
|
|
||||||||||
|
|
|
|
|
|
|
|
|
|
|
|
|
|
|
|
|
|
|
|
|
|
|
1 |
|
|
|
|
||||||
|
|
|
|
|
|
|
Электролит |
|
|
|
|
|||||
|
|
|
|
|
|
|
|
|
|
|
|
4 |
|
|||
|
|
|
|
|
|
|
|
3 |
||||||||
|
|
|
|
|
|
|
|
|
|
|
|
|
|
|||
|
|
|
|
|
|
|
|
|
|
|
|
|
|
|
|
|
2 |
|
|
|
|
|
|
|
|
|
|
|
|
|
|
|
|
|
|
|
|
|
|
|
||||||||||
|
|
|
|
|
|
|
|
|||||||||
|
|
|
|
|
|
|
|
|
|
|
|
|
|
|
б |
|
|
|
|
а |
|
|
Рис. 93. Схема электрохимической размерной обработки
Струя электролита, непрерывно подаваемого в межэлектродный промежуток, растворяет образующиеся на заготов- ке-аноде соли и удаляет их из зоны обработки. При этом способе одновременно обрабатывается вся поверхность заготовки, находящаяся под активным воздействием катода, что обеспечивает высокую производительность процесса. Участки заготовки, не требующие обработки, закрывают изолятором. Инструменту придают форму, обратную форме обрабатываемой поверхности. Формообразование поверхности происходит по методу копирования.
Импульсное рабочее напряжение способствует повышению точности обработанной поверхности заготовки, которая повышается при уменьшении рабочего зазора между заготовкой и инструментом. Способ рекомендуют для обработки заготовок из высокопрочных сплавов карбидных и труднообрабатываемых материалов. Отсутствие давления инструмента на заготовку позволяет обрабатывать нежесткие тонкостенные детали с высокими точностью и качеством обработанной поверхности.
Электрохимической обработкой можно прошивать отверстия, получать поверхности сложной конфигурации, например турбинные лопатки, полости штампов, «фрезеровать»
194
детали из труднодеформируемых материалов с помощью металлического диска-катода 1 (см. рис. 93, а), проводить электроабразивное шлифование электроабразивным кругом, состоящим из абразивных зерен 3 и электропроводного наполнителя 4 (см. рис. 93, б).
По сравнению с обычным шлифованием этот процесс обеспечивает более высокую производительность, шероховатость поверхности 0,02…0,05, меньший износ шлифовального круга и не влечет за собой появления микротрещин в поверхностном слое.
13.3. Анодно-механическая обработка
Анодно-механическая обработка основана на одновременном действии электромеханического и электроискрового процессов, протекающих в среде электролита, которым является водный раствор жидкого стекла. При пропускании через ванну постоянного тока на поверхности заготовки (анода) образуются пленки продуктов растворения металла, которые механически удаляются инструментом (катодом). Так как вершины шероховатостей на обрабатываемой поверхности анода отделены от катода небольшим промежутком, через него проходит кратковременный дуговой разряд. При этом микроскопический участок поверхности детали оплавляется и расплавленные частицы также удаляются движущимся анодом, т.е. происходят электроэрозионные процессы. Заготовке или инструменту сообщается движение подачи. При мягком режиме, когда плотность тока меньше 15 А/мм2, обработка осуществляется в основном за счет электрохимического растворения и механического удаления пленки. Таким способом осуществляют так называемое анодно-меха- ническое шлифование и достигают шероховатости поверхно-
195

сти 0,4…0,05. При более жестком режиме удаление металла из зоны обработки осуществляется за счет электроэрозии, шероховатость обработанной поверхности достигает
Ra 200…25.
Этот метод эффективно используется при отрезании заготовки из труднообрабатываемых высокопрочных сплавов. На рис. 94, а показана схема анодно-механической отрезки.
|
|
|
|
|
|
|
|
|
|
|
|
|
|
|
|
|
|
|
|
1 |
|
|
|
|
|
|
|
|
|
|
|
|
|
|
|
|
|
|
|
|
2 |
||||
|
|
|
|
|
|
|
|
|
|
|
– |
|
|
|
|
|
||||||
|
|
|
|
|
|
|
|
|
|
|
|
|
|
|
|
|
|
|
|
|||
|
|
|
|
|
|
|
|
|
|
|
|
|
|
|
|
|
|
|
||||
|
|
|
|
|
|
|
|
|
|
|
|
|
|
|
|
|
V |
|
|
|
|
|
|
|
|
|
|
|
|
|
|
|
|
|
|
|
|
|
|
|
|
|
|
|
|
2 |
|
|
|
|
|
|||||||||||||||||
|
3 |
|
|
|
|
|
|
|||||||||||||||
|
|
|
|
|
Р |
|||||||||||||||||
|
|
|
|
|
|
|||||||||||||||||
|
|
|
|
|
|
|
|
|
|
|
|
|
|
|
|
|
|
|
|
|
|
|
|
|
|
|
|
|
|
3 |
|
|
|
|
|
|
|
|
|||||||
|
|
|
|
|
|
|
|
|
|
|
|
|
|
|
|
|
|
|
|
|
|
|
|
1 |
|
|
+ |
|
|
|
|
|
|
|
|
|
|
|
|||||||
|
|
|
|
|
|
|
|
|
|
|
|
|
|
|
|
|
|
|
|
|
|
|
|
|
|
|
|
|
|
|
|
|
|
|
|
|
|
|
|
|
|
||||
|
|
|
|
|
|
|
|
|
|
|
|
|
|
|
|
|
|
|
|
|
|
|
|
|
|
|
|
|
|
|
|
|
|
|
|
|
|
|
|
|
|
||||
а |
|
|
|
|
|
|
|
|
|
|
б |
|
|
|
|
|
Рис. 94. Схемы анодно-механической отрезки (а) и электроконтактной обработки (б)
Инструмент-катод 2, которым служит тонкий диск из мягкой стали, вращающийся с большой скоростью, соприкасается с заготовкой-анодом 1. В зону контакта по трубе 3 подается жидкое стекло. Диск и заготовка подключаются к генератору постоянного тока. Процесс ведут на жестких электрических режимах, поэтому наряду с анодным растворением и механическим воздействием существенную роль играют электротермические процессы.
13.4. Электроконтактная обработка
Съем металла с заготовки 1 (рис. 94, б) осуществляется в воздушной среде вращающимся диском электродом 2. Диск и заготовка соединены с источником питания понижающим трансформатором 3. При вращении диска, к кото-
196
рому заготовка прижимается под давлением (2…5)·104 Па, происходит периодический разрыв контактов, возникают электродуговые разряды, под воздействием которых и разрушается металл заготовки. Соприкосновение под небольшим давлением Р двух металлических электродов (инструмента и заготовки) приводит к образованию в месте контакта повышенного переходного сопротивления. Проходящий через место контакта электрический ток вследствие выделения джоулевого тепла нагревает, размягчает и плавит металл заготовки, облегчая его удаление. Во избежание сильного разогрева и плавления инструмента-электрода его вращают со скоростью, превышающей 30 м/с, при которой длительность соприкосновения контактирующего участка диска с заготовкой ничтожно мала. Вращающийся диск выбрасывает частицы раскаленного металла в виде снопа искр. Интенсивность процесса достаточно велика, но он не обеспечивает высокой точности и шероховатость поверхности не превосходит Ra 100…25. При большом съеме металла в поверхностном слое происходят значительные фазовые изменения, могут возникнуть трещины и другие пороки. Поэтому электроконтактная обработка используется главным образом для выполнения грубых инеответственных операций, например зачистки отливок иштамповокизтруднообрабатываемыхсплавов.
14. Ультразвуковая обработка
Ультразвуковые колебания (15…30 кГц), используемые для обработки заготовок, получают при помощи магнитострикционных излучателей. Принцип их действия основан на способности кобальта, никеля, их сплавов, других материалов укорачиваться под действием магнитного поля и принимать первоначальные размеры при его снятии.
197
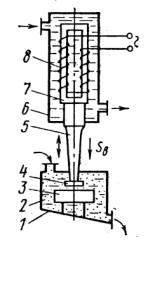
Сердечник 7 магнитострикционного преобразователя возбуждается от переменного магнитного поля катушки 8, подключенной к генератору ультразвуковой частоты (рис. 95).
Для охлаждения сердечника сквозь
|
|
|
|
|
кожух 6 пропускается вода. Инстру- |
|||||
|
|
|
|
|
мент 4 через волновод 5, связанный |
|||||
8 |
|
|
|
|
||||||
|
|
|
|
с сердечником, подводится |
к |
заго- |
||||
7 |
|
|
|
|
товке 3, которая находится в ванне 1 |
|||||
6 |
|
|
|
|
с абразивной |
суспензией 2, |
непре- |
|||
5 |
|
|
|
|
рывно прокачиваемой через ванну. |
|||||
|
|
|
|
|
Инструмент |
непосредственно |
не |
|||
|
|
Sв |
||||||||
4 |
|
|
|
|
контактирует |
с заготовкой, |
но, со- |
|||
|
|
|
|
|||||||
|
|
|
|
вершая ультразвуковые |
колебания, |
|||||
3 |
|
|
|
|
||||||
|
|
|
|
|||||||
2 |
|
|
|
|
ударяет по зернам абразива, которые |
|||||
1 |
|
|
|
|
направленно |
разрушают материал |
||||
|
Рис. 95. Схема |
заготовки. |
Увеличивая |
зернистость |
||||||
|
||||||||||
ультразвуковой |
абразива, |
повышают |
производи- |
|||||||
|
обработки |
|||||||||
|
тельность, но снижают точность об- |
|||||||||
|
|
|
|
|
работки.
Ультразвуковой обработке поддаются хрупкие материалы (стекло, керамика, твердые сплавы, драгоценные минералы), частицы которых скалываются от ударов абразивных зерен. Вязкие материалы обрабатываются плохо.
Ультразвуковой обработкой может быть получено отверстие любой формы. Перемещая заготовку в продольном и поперечном направлениях, можно разрезать ее по сложному контуру.
При соответствующих режимах ультразвуковая обработка обеспечивает квалитет точности IТ7 и шероховатость обработанной поверхности до Ra 0,8…0,1 мм.
198

15. Лучевые методы обработки
15.1. Электронно-лучевая обработка
Электронно-лучевая обработка ведется в глубоком ва-
кууме, электроны, излучаемые разогретым катодом 7, вследствие термоэлектронной эмиссии ускоряются в мощном электрическом поле и фокусируются в узкий пучок, направленный на обрабатываемую заготовку-анод (рис. 96, а). При этом кинетическая энергия преобразуется в тепловую. Попадая на обрабатываемую поверхность, такой луч мгновенно нагревает ее до температуры около 6000 С, в результате металл не только плавится, но и испаряется. Элек- тронно-лучевая обработка ведется на установке с электронной пушкой 6, обеспечивающей фокусирование электронного луча.
Размером и траекторией электронного луча можно управлять с помощью контрольной системы. В нее входят электростатическая система 12, электромагнитные катушки 5 для магнитной юстировки, корректор изображения 4, магнитные
|
|
|
|
|
|
|
|
|
|
9 |
|
|
|
|
|
|
|
|
|
|
|
|
|
|
|
|
|
|
8 |
|
|
|
|
|
|
|
|
|
|
|
|
|
|
|
|
|
|
|
|
|
|
|
|
|
|
|
|
|
|
|
|
|
|
|
|
|
|
|
|
|
|
|
10 |
|
|
|
|
|
|
|
|
|
|
|
|
|
|
|
|
|
|
|
|
|
|
|
|
|
|
|
|
|
|
|
|
|
|
|
|
|
|
|
|
|
|
|
|
|
|
|
|
|
|
|
|
|
|
|
|
|
|
|
|
|
|
|
|
|
|
|
|
|
|
|
|
7 |
|
|
|
|
|
|
|
|
|
|
|
|
|
|
|
|
|
|
|
|
|
||||||
|
|
|
|
|
12 |
|
|
|
|
|
|
|
|
|
|
|
|
|
|
|||||||||
|
|
|
|
|
|
|
|
|
|
|
|
|
|
|
|
2 3 4 5 |
|
|
|
|
|
|
|
|
||||
|
|
|
|
|
|
|
|
|
|
|
|
|
|
|
|
|
|
|
|
|
|
|||||||
|
|
|
|
|
|
|
|
|
|
11 |
|
|
|
|
|
|
||||||||||||
|
|
|
|
|
|
|
|
|
|
|
|
|
|
|
|
|
|
|
|
|
||||||||
|
|
|
|
|
6 |
|
|
|
|
|
|
|
|
|
|
|
|
|
|
|||||||||
|
|
|
|
|
|
|
|
|
|
|
|
|
|
|
|
|
|
|
|
|
|
|||||||
|
|
|
|
|
|
|
|
|
|
|
|
|
|
|
|
|
|
|
|
|
|
|||||||
|
|
|
|
|
|
|
|
|
|
|
|
|
|
|
|
|
|
|
|
|||||||||
|
|
|
|
|
|
|
|
|
|
|
|
|
|
|
|
|
|
|
|
|
|
|
|
|
|
|||
|
5 |
|
|
|
|
|
|
|
|
|
|
|
|
|
|
|
|
|
|
|
|
|
|
|||||
|
|
|
|
|
|
|
|
|
|
|
|
|
|
|
|
|
|
|
|
|
|
|
|
|
|
|
|
|
|
4 |
|
|
|
|
|
|
|
|
|
|
|
|
|
|
|
|
|
|
|
|
|||||||
|
|
|
|
|
|
|
|
|
|
|
|
|
|
|
|
|
|
|
|
6 |
||||||||
|
|
|
|
|
|
|
|
|
|
|
|
|
|
|
|
|
|
|
|
|
||||||||
|
|
|
|
|
|
|
|
|
|
|
|
|
|
|
|
|
|
|
|
|
|
|
|
|
||||
|
3 |
|
|
|
|
|
|
|
|
|
|
|
|
|
|
|
|
|
|
|
|
|
||||||
|
|
|
|
|
|
|
|
|
|
1 |
|
|
|
|
|
|
|
|
|
|
||||||||
2 |
|
|
|
|
|
|
|
|
|
|
|
|
|
|
|
|
|
|
|
|
|
|
|
|
|
|
|
|
|
|
|
|
|
|
|
|
|
|
|
|
|
|
|
|
|
|
|
|
|
|
|
|
|
|
|
||
|
|
|
|
|
|
|
|
|
|
|
|
13 |
|
|
|
|
|
|
|
8 |
|
|
|
|
|
|||
|
|
|
|
|
|
|
|
|
|
|
|
|
|
|
|
|
|
|
|
|
7 |
|
|
|||||
|
|
|
|
|
|
|
|
|
|
|
|
|
|
|
|
|
|
|
|
|
|
|
||||||
|
|
|
|
|
|
|
|
|
|
|
|
|
||||||||||||||||
|
|
|
|
|
|
|
|
|
|
|
|
|
|
|
|
|||||||||||||
|
|
|
|
|
|
|
|
|
|
|
|
|
|
|
|
|
|
|
|
|
|
|
|
|
||||
|
|
1 |
|
|
а |
|
|
|
|
|
|
|
|
|
|
|
|
|
|
|
|
|
||||||
|
|
|
|
|
|
|
|
|
|
|
|
|
|
|
б |
|||||||||||||
|
|
|
|
|
|
|
|
|
|
|
|
|
|
|
|
|
||||||||||||
|
|
|
|
|
|
|
|
|
|
|
|
|
|
|
|
|
|
|
|
|
||||||||
|
|
|
|
|
|
|
|
|
|
|
|
|
|
|
|
|
|
|
|
|
|
|
Рис. 96. Принципиальные схемы установок для лучевой обработки: а электронно-лучевой; б лазерной
199
линзы 3, контрольный контур 2 и др. Заготовка 13 устанавливается на столе 1, который можно перемещать. С помощью управляющих электромагнитных катушек и контрольного контура 2 (профилирующее управление) электронный луч может отклоняться по поверхности заготовки 13.
Важными элементами электронной пушки являются генератор высокого напряжения 11, генератор напряжения накала и напряжения возбуждения 10, импульсный генератор 8, импульсный трансформатор 9 и вольфрамовый электрод 7.
Электронно-лучевым методом получают отверстия, пазы малых размеров (от 0,005 мм и ниже) в труднообрабатываемых сплавах.
15.2. Обработка световым лучом (лазерная)
Способ основан на том, что мощный световой луч, проходя через специальное оптическое устройство, фокусируется на обрабатываемой поверхности заготовки на площади диаметром до 0,01 мм. Поэтому в зоне его действия возникают температуры порядка нескольких тысяч градусов и высокие давления. Концентрация энергии может быть порядка 105 кВт/см2, поэтому происходит мгновенное расплавление и испарение металла. В качестве источника энергии используются квантовые генераторы света или лазеры, чаще всего кристаллические рубиновые (рис. 96, б).
Основой лазера служит стержень синтетического рубина 4, помещенный внутрь наполненной ксеноном спиральной лампы (лампы подкачки) 5. Лампа питается от батареи конденсаторов 8 и при разрядке их периодически вспыхивает. Стержень заключен внутри стеклянной трубки 3, через которую непрерывно прокачивается охлаждающая
200