
Технология конструкционных материалов. Способы получения деталей (за
.pdf1. Газовые раковины пузыри воздуха или газов в теле округленной формы отливки. Образуются при недостаточной газопроницаемости, повышенной влажности формовочных и стержневых смесей или чрезмерно плотной набивке формы.
2. Песчаные и шлаковые раковины открытые или за-
крытые полости в теле отливки, заполненные формовочной смесью или шлаком. Образуются из-за слабой набивки формы и неправильной конструкции литниковой системы.
3.Усадочные раковины, рыхлоты и пористость от-
крытые или закрытые пустоты в теле отливки. Образуются
вутолщенных местах отливки, при неправильном подводе металла в форму или из-за слишком высокой температуры заливаемого металла.
4.Холодные трещины разрывы тела отливки значительной длины. Образуются при охлаждении отливки в области невысоких температур. Причины: внутренние напряжения из-за неодинаковой скорости охлаждения различных сечений отливки; повреждения при выбивке, обрубке и очистке отливок.
5.Горячие трещины разрыв тела отливки небольшой
протяженности. Возникают при высоких температурах и имеют темную окисленную поверхность. Причины: недостаточная податливость стержней и формы; недостаточная выдержка отливок в форме перед выбивкой.
6.Заливы тонкие, не предусмотренные чертежом выступы на отливке вдоль разъема формы. Образуются при недостаточной нагрузке формы.
7.Недолив неполная отливка. Причины: плохая жидкотекучесть металла; низкая температура заливки; малое сечение питателей; утечка расплава из формы.
41
Исправление брака. Брак отливок исправляют наплавкой, заваркой, заделкой замазками или мастиками, пропиткой.
Газовой и электрической наплавкой и заваркой исправ-
ляют дефекты в отливках, предназначенных для больших нагрузок. Для избежания образования трещин отливку предварительно нагревают до 350…600 С, а после заварки медленно охлаждают.
Заделка дефектов замазками или мастиками является декоративным исправлением. После заполнения дефектов мастикой это место заглаживают, высушивают и затирают пемзой, графитом или коксом. Иногда применяют замазку из стиракрила, смешанного с чугунной стружкой с добавкой эфира, которая затвердевает при нормальной температуре за 3…4 ч.
Пропиткой устраняют пористость отливок, погружая их на 8…12 ч в водный раствор нашатыря, образующиеся окислы заполняют поры отливки. Применяют также пропитку под давлением раствором медного купороса, жидкого стекла или бакелитовым лаком (для цветного литья).
4. Специальные методы получения отливок
Отливки, полученные в разовых песчано-глинистых формах при машинной и особенно при ручной формовке, имеют невысокую точность и низкое качество поверхности, а также крупнозернистую структуру. Повышения точности и качества поверхности отливок достигают, используя специальные методы литья. Так, литье в оболочковые формы, литье по выплавляемым моделям, литье под давлением и в некоторых случаях кокильное литье не требуют механической обработки полученных отливок.
42

4.1. Изготовление отливок литьем в оболочковые формы
Разовую литейную форму изготовляют в виде оболочки, используя для формовочной смеси в качестве связующего материала фенольные термореактивные смолы, прочно цементирующие мелкий кварцевый песок. Изготовление оболочковой формы исключает потребность в опоках, резко снижает расход формовочной смеси, легко механизируется и автоматизируется, обеспечивает малую шероховатость поверхности и более высокую точность отливок, чем изготовленных в песчано-глинистых формах, так как оболочка твердеет на модели и сохраняет ее размеры.
Литье в оболочковые формы применяют в крупносерийном и массовом производствах при получении ответственных фасонных мелких и средних отливок из различных сплавов.
Технология изготовления оболочковой формы (рис. 13)
начинается с нанесения пульверизатором на металлическую модельную плиту разделительного состава, облегчающего снятие оболочки. Затем модельную плиту нагревают в электрической печи до температуры 200…220 С (см. рис. 13, а), устанавливают над бункером и закрепляют моделью вниз (см. рис. 13, б). Бункер переворачивают на 180 С, и формовочная смесь падает на нагретую модельную плиту (см. рис. 13, в).
|
|
|
|
|
|
|
|
|
|
|
|
|
|
|
|
|
|
|
|
|
|
|
|
|
|
|
|
|
|
|
|
|
|
|
|
|
|
|
|
|
|
|
|
а |
|
|
б |
в |
|
|
г |
д |
|
|
|
|
|
|
|||||||
|
Рис. 13. Схема изготовления оболочковых форм |
|
|
43

При выдержке в течение 20…30 с смола размягчается и, обволакивая тонкой пленкой зерна песка, образует оболочку толщиной 6…8 мм. Бункер возвращают в исходное положение, аоставшаяся формовочная смесь падает на его дно (см. рис. 13, г). Снятую с бункера модельную плиту с непрочной оболочкой нагревают до температуры около 350 С (см. рис. 13, д). Смола в течение 90…180 с полимеризуется и необратимо твердеет, образуя прочную оболочковую полуформу. По такой же технологии изготавливают другую полуформу.
Для снятия готовой оболочковой полуформы (рис. 14) с закрепленной на плите 1 полумоделью 3 служат толкатели 2 и 4. При нажатии на плиту 6 толкатели снимают полуформу 5 с модельной плиты. В одной из полуформ на стержневые знаки устанавливают стержень, закрывают другой полуформой, скрепляют их скобами, струбцинами или склеивают по
Рис. 14. Модельная плита с оболочковой полуформой и собранная форма
плоскости разъема. Собранную оболочковую форму 7 помещают в металлический ящик 8, для жесткости засыпают крупным песком или чугунной дробью 9 и заливают металлом. К моменту полной кристаллизации металла отливки смола из смеси выгорает, форма и стержни разупрочняются и легко разрушаются, освобождая отливку при выбивке.
44

4.2. Изготовление отливок литьем по выплавляемым моделям
Литье по выплавляемым моделям применяют при производстве отливок очень сложной конфигурации из любых литейных сплавов, в том числе из высоколегированных сталей, трудно поддающихся механической обработке и ковке. Отливки получают массой 0,02…100 кг, с толщиной стенок до 0,5 мм и отверстиями диаметром до 2 мм. Отливки имеют высокую точность и качество поверхности.
Разъемные пресс-формы изготовляют из стали или алюминиевых сплавов. Полость пресс-формы имеет размеры будущей отливки с учетом усадки модельного состава.
Неразъемные легкоплавкие модели получают запрессовкой в пресс-форму модельного состава из легкоплавких материалов: парафина, стеарина, воска, церезина, канифоли и др., нагретых до тестообразного состояния. Легкоплавкая модель неразъемна, имеет все внутренние полости, отверстия, резьбу и не имеет стержневых знаков.
На рис. 15 приведен чертеж отливки 1 и неразъемной модели с питателем 2. Модели с питателями «припаивают» к общему легкоплавкому стояку 3 и получают блок моделей.
3 |
|
|
|
|
|
|
|
|
5 |
|
|
||
4 |
|
|
||||
|
|
6 |
||||
|
|
|
||||
|
|
|
|
|||
|
|
|
|
|
|
1
2
Рис. 15. Литье по выплавляемым моделям
45

Готовый блок окунают в огнеупорную смесь. После окунания на моделях, питателях и стояке остается тонкая огнеупорная пленка смеси 4. Смесь заполняет все полости и отверстия в моделях, образуя стержни. Для упрочнения огнеупорной пленки блок моделей посыпают мелким сухим кварцевым песком 5. Прилипая к сырой пленке, песок образует огнеупорный слой, который сушат. Когда слой высыхает, операция окунания, посыпания песком и сушки повторяется от 3 до 5 раз. После сушки последнего огнеупорного слоя получают форму в виде многослойной оболочки с заформованными легкоплавкими моделями. Форму нагревают до температур более 100 С или погружают в горячую воду. Модели и элементы литниковой системы плавятся и вытекают из формы. Для выжигания остатков модельного состава из полости и для упрочнения оболочки форму помещают в металлический ящик 6, засыпают металлической дробью и в термической печи обжигают при температуре 800…900 С.
При изготовлении ответственных отливок 1 (рис. 16) массой до 3,5 т из чугуна, стали и цветных сплавов в единичном производстве используют выжигаемые модели 3 из пенополистирола, который легко режется горячей проволокой
|
|
2 |
|
3 |
|
4 |
|
5 |
|
6 |
|
1 |
|||||||||||
|
|
|
|
|
|
|
|
|
|
Рис. 16. Литье по выжигаемым моделям
и склеивается, заформовывают песчано-глинистой смесью 4 в металлическом ящике 6. Во время заливки модель с литниковой системой остается в форме, и жидкий металл 5 выжигает их и одновременно заполняет полость формы.
46

Этот способ позволяет получать отливки сложной формы, отличается большой точностью и экономией металла из-за отсутствия формовочных уклонов.
4.3. Изготовление отливок литьем под давлением
Литье под давлением осуществляют на компрессорных и поршневых машинах высокой производительности, дающих 200…400 отливок в час. Поршневые машины выпускают сгорячей(рис. 17, в) илихолоднойкамеройсжатия(рис. 17, а, б), расположенной горизонтально или вертикально. Машины с горячей камерой сжатия, в которых камера находится непо-
6
|
|
|
|
|
|
|
|
|
|
|
|
|
|
|
|
5 |
|
|
|
|
|
|
|
|
|
|
|
|
|
|
|
|
|
|
|
|
|
|
|
|
|
|
|
|
|
|
|
|
|
|
|
|
|
|
|
|
|
|
|
|
2 |
|
|
||||
2 |
|
|
|
|
|
|
|
|
||||||||
|
|
|
|
|
|
|
|
1 |
||||||||
|
|
|
|
|
|
|
||||||||||
|
|
3 |
|
|
|
|
||||||||||
|
|
|
|
|
|
|
|
|
|
|
||||||
|
|
|
|
|
|
|
|
|
|
|
|
|
|
|
||
|
|
|
|
|
|
|
|
|
|
|
|
|
|
|
||
|
|
|
|
|
|
|
|
|
|
|
|
|||||
|
|
|
3 |
|
|
|
||||||||||
|
|
|
|
|
3 |
|
|
|
||||||||
1 |
|
|
|
|||||||||||||
|
|
|
|
|
|
|||||||||||
|
|
|
|
|
|
|
|
|
|
|
|
|||||
|
|
|
|
|
|
|
|
|
|
|
|
|
|
|
|
|
|
|
|
|
|
|
|
|
|
|
|
|
|
|
|||
|
|
|
|
|
|
|
|
|
4 |
|
|
|
а 4 5 |
4 |
1б |
2 |
в |
Рис. 17. Схемыпоршневыхмашиндлялитьяподдавлением: а машинасвертикальнойхолоднойкамеройсжатия; б машинасгоризонтальнойхолоднойкамеройсжатия; в машинасгорячейкамеройсжатия
средственно в расплаве, применяют для получения отливок из сплавов с низкой температурой плавления на основе цинка, олова и свинца. Машины с холодной камерой сжатия, в которых камера вынесена за пределы расплава, используют для получения отливок из более тугоплавких цветных сплавов на основе меди, алюминия и магния.
На машинах с вертикальной холодной камерой сжатия (см. рис. 17, а) расплав заливают в камеру сжатия 1. Верхний поршень 2, опускаясь, давит на расплав и на нижний поршень 4, который при движении вниз открывает литниковый канал 5. Металл заполняет полость 3 пресс-формы, состоя-
47
щей из двух половин. Давление верхнего поршня поддерживают до полной кристаллизации отливки, после чего прессформу раскрывают и отливку вместе с литником выталкивают из формы толкателями. Нижний поршень выталкивает наружу избыток металла, и его отправляют в переплав.
На поршневой машине с горячей камерой сжатия 2 (см. рис. 17, в) чугунный тигель 3 с жидким металлом подогревают снизу газом. Перед заливкой пресс-форму закрывают. При верхнем положении поршня 1 через отверстие 4 сплав заполняет камеру сжатия 2 и канал 5. При движении вниз поршень впрессовывает жидкий металл в полость формы 6. После затвердевания металла давление снимают, поршень движется вверх, форму раскрывают и отливку выталкивают толкателями. Машины с горячей камерой сжатия более производительны и расходуют меньше жидкого металла.
Компрессорные машины, работающие на сжатом воздухе, применяются редко.
Литье под давлением дает возможность полученияотливок из материалов с плохой жидкотекучестью, обеспечивает быстрое и хорошее заполнение формы, высокую точность и малую шероховатость поверхности отливки, отсутствие усадочных раковин, пористости, образование мелкозернистой структуры. Литьем под давлением получают отливки сложной конфигурации с толщиной стенки до 0,5 мм и с отверстиями диаметром до 1 мм. Это способ получения наиболее точных отливок, не требующих последующеймеханическойобработки.
4.4. Изготовление отливок центробежным литьем
Жидкий металл заливают во вращающуюся с определенной скоростью литейную форму. Центробежной силой металл прижимается к стенкам формы, что обеспечивает получение плотных и прочных отливок. Газы и шлак, обла-
48

дающие меньшей плотностью, вытесняются во внутренние полости отливки. Их удаляют механической обработкой.
Ось вращения формы может быть горизонтальной (рис. 18, а), если диаметр отливки значительно меньше ее длины, вертикальной (рис. 18, б), если диаметр отливки значительно больше ее длины, и наклонной. Внутренняя полость отливки получается без стержней, а толщина стенки отливки определяется количеством заливаемого металла.
а |
б |
Рис. 18. Схемы центробежного литья
Использование центробежных установок, отсутствие стержней повышают производительность труда, а отсутствие литниковойсистемыи прибылей значительно экономит металл.
Центробежное литье применяют при производстве отливок из различных сплавов в металлических и песчаных формах. Этим способом отливают трубы, цилиндровые втулки, гильзы автотракторных двигателей, заготовки для поршневых колец, шестерни, шкивы, орудийные стволы, а также получают двухслойные (биметаллические) отливки, поочередно заливая форму различными сплавами.
4.5. Изготовление отливок в металлических формах
Металлические формы называются кокилями. Они обладают высокой теплопроводностью, что обеспечивает образование мелкозернистой структуры отливок и повышает их прочность. При кокильном литье отпадает необходимость в модельно-опочной оснастке, в формовочных и стержневых
49
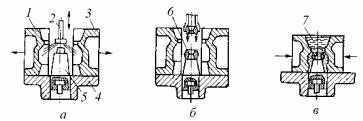
смесях, улучшаются санитарные условия труда, повышаются точность и качество поверхности отливки, а также производительность.
Высокая стоимость кокилей позволяет использовать их только в серийном и массовом производстве; есть опасность образования трещин в отливках из-за неподатливости металлического кокиля; чугунные отливки в кокиле получаются отбеленными и требуют длительного отжига.
Кокильное литье применяют при изготовлении несложных по конфигурации отливок с толщиной стенок 3…100 мм из чугуна, стали и цветных металлов.
По конструкции кокили бывают простые и сложные. В зависимости от расположения плоскости разъема кокили делятся на неразъемные (вытряхные); с вертикальной, горизонтальной и сложной (комбинированной) плоскостями разъема.
Перед изготовлением отливки в кокиле сначала очищают поверхности полуформ 1 и 3 (рис. 19, а), плиты 4 и разъемов от следов загрязнений и масла, проверяют возможные
Рис. 19. Схема изготовления отливки в металлической форме (кокиле)
смещения, центрирование и крепление подвижных частей кокиля. Кокиль нагревают до 150…200 С и наносят на рабочую поверхность кокиля и металлического стержня 5 огнеупорные покрытия в виде водной суспензии 2 распылителем
50