
Технология конструкционных материалов. Способы получения деталей (за
.pdf
Шириной срезаемого слоя b называют расстояние между обрабатываемой и обработанной поверхностями, измеренное
по поверхности резания, b sint .
Толщиной срезаемого слоя а называют расстояние меж-
ду двумя положениями главной режущей кромки за время одного полного оборота заготовки, измеренное в направлении, нормальном ширине срезаемого слоя, a so sinφ.
Номинальная площадь поперечного сечения срезаемого слоя f, мм2, определяется следующим образом:
f sot ab.
Действительное сечение срезаемого слоя и шерохова-
тость поверхности. За время одного оборота заготовки (см. рис. 75, б) действительное сечение срезаемого слоя fд (BCDE) отличается от номинального fн (ABCD), и на обработанной поверхности остаются неровности, так называемые остаточные гребешки, с площадью сечения fо = fн fд. Обработанная поверхность будет иметь бóльшую или меньшую шероховатость в зависимости от геометрической формы резца, подачи
идругих факторов. Шероховатость поверхности оказывает большое влияние на эксплуатационные свойства деталей: износостойкость, усталостную прочность, коррозионную стойкость
идругие, следовательно, она в значительной степени определяет надежностьработыи долговечностьдеталей машин.
5. Производительность процесса резания
Производительность обработки определяется количеством заготовок, изготовляемых в единицу времени, шт/мин: Q 1/Тшт, где Тшт штучное время, т.е. среднее время, затрачиваемое на изготовление одной детали,
Тшт = То + Тв + Тобсл + Тотд,
151
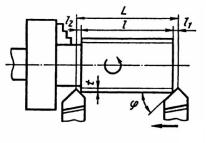
где То |
основное технологическое время, затрачиваемое |
|||||||||
на снятие припуска с заготовки; |
||||||||||
Тв |
вспомогательное время, затрачиваемое на уста- |
|||||||||
новку и съем детали, управление станком и т.д.; |
||||||||||
Тобсл время обслуживания рабочего места и станка; |
||||||||||
Тотд |
время перерывов на отдых. |
|||||||||
|
|
|
|
|
|
|
|
|
|
|
|
|
|
|
|
L |
|
|
|
|
|
|
l2 |
|
|
|
|
|
|
|
||
|
|
|
|
|
|
l1 |
|
|||
|
|
|
|
|
|
|
|
|
||
|
|
|
|
|
l |
|
Рис. 76. Схемакрасчетуосновного |
|||
|
|
|
|
|
|
|
|
|||
|
|
|
|
|
|
|
|
|
|
|
|
|
|
|
|
|
|
|
|
|
технологическоговремениприточе- |
|
|
|
|
|
|
|
|
|
|
ниицилиндров |
|
|
|
t |
|
|
|
|
|
|
|
|
|
|
|
|
|
|
|
|||
|
|
|
|
|
|
|
|
|
|
|
|
|
|
|
|
|
|
|
|
|
|
Sпр
При точении
To Li /(son) Lh /(sont),
где L расчетная длина, мм, пути режущего инструмента относительно заготовки в направлении подачи (рис. 76), L l l1 l2 , l длинаобрабатываемойповерхности, мм; l1 – путь
врезанияинструмента, мм; l2 путьвыхода(перебег) резца, мм;
i число рабочих ходов инструмента, необходимое для снятия всего припуска при работе с глубиной резания t, мм;
so величина продольной подачи, мм/об; n частота вращения заготовки, мин 1.
6. Некоторые явления, сопутствующие процессу обработки металлов резанием
Упрочнение при обработке металлов резанием. При резании металлов поверхностный слой обработанной детали пластически деформируется (рис. 7), что изменяет его структуру, вызывая упрочнение или наклеп. Повышается твер-
152
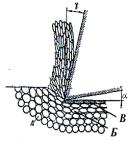
дость, прочность и снижается пластичность поверхностного слоя. Твердость вблизи обработанной поверхности в 2–3 раза выше твердости исходного металла. На степень упрочнения влияют свойства обрабатываемого материала, геометрические параметры рабочей части инструмента и его затупление, режим резания, наличие смазочно-охлаждающей жидкости и др. Чем пластичнее обрабатываемый материал, тем интенсивнее он упрочняется.
Упрочнение |
поверхностного |
|
|
|
|
|
|
|
|
|
|
|
|
||||
|
|
|
|
|
|
|
|
|
|
|
|
||||||
слоя повышает |
износостойкость, |
|
|
|
|
|
|
|
|
|
|
|
|||||
|
|
|
|
|
|
|
|
|
|
|
|
||||||
|
|
|
|
|
|
|
|
|
|
|
|
||||||
усталостную |
прочность |
и |
другие |
|
|
|
|
|
|
|
|
|
|
|
|
||
эксплуатационные свойства обрабо- |
|
|
|
|
|
|
|
|
|
|
|
|
|||||
танной детали. Но это является |
|
|
|
|
|
|
|
|
|
|
|
|
|||||
вредным при ее обработке. |
|
|
|
|
|
|
|
|
|
|
|
|
|
||||
|
|
|
|
|
|
|
|
|
|
|
|||||||
Тепловые |
явления |
при |
реза- |
|
|
|
|
|
|
|
|
|
|||||
|
|
|
|
|
|
|
|
|
|
|
|
||||||
|
|
|
|
|
|
|
|
|
|
|
|
||||||
|
|
|
|
|
|
|
В |
|
|
||||||||
нии. При обработке резанием рабо- |
|
А |
|
|
|
|
|
|
|||||||||
|
|
|
|
|
Б |
|
|
|
|
||||||||
|
|
|
|
|
|
||||||||||||
|
|
|
|
|
|||||||||||||
та деформации срезаемого слоя, сил |
|
|
|
|
|
|
|
|
|
|
|
|
|||||
Рис. |
77. Упрочнение |
||||||||||||||||
трения стружки о переднюю по- |
|||||||||||||||||
поверхностного слоя: |
|||||||||||||||||
верхность инструмента и о поверх- |
А недеформирован- |
||||||||||||||||
ность резания заготовки ведут к об- |
ный слой; Б дефор- |
||||||||||||||||
разованию тепла, которое отводится |
мированныйслой; В |
||||||||||||||||
|
наплавленный слой |
||||||||||||||||
стружкой 8…25 |
% всей теплоты, |
|
|||||||||||||||
|
|
|
|
|
|
|
|
|
|
|
|
заготовкой 10…50 %, инструментом 2…8 % и около 1 % рассеивается в окружающую среду.
Повышение температуры режущего инструмента снижает его твердость, теплостойкость и износостойкость. Наибольшее влияние на повышение температуры в зоне резания оказывает увеличение скорости резания, а наименьшее увеличение глубины резания.
С повышением температуры заготовки и инструмента увеличиваются их размеры, что приводит к увеличению толщины снимаемогослоя иполучения бракованных деталей.
153
7. Применение смазочно-охлаждающих жидкостей
Для уменьшения трения и охлаждения режущего инструмента и обрабатываемой детали при их обработке применяют смазочно-охлаждающие жидкости: водные растворы минеральных солей, эмульсии, растворы мыла, минеральные, животные и растительные масла, скипидар, керосин и др.
Смазочно-охлаждающие жидкости снижают трение, препятствуют образованию нароста на передней поверхности резца (налипанию частиц стружки), уменьшают степень шероховатости обработанной поверхности. Мощность, необходимая для снятия стружки, уменьшается на 10…15 %, резко возрастает стойкость режущего инструмента, повышается точность обработанной поверхности и уменьшается степень шероховатости.
8. Износ и стойкость режущих инструментов
Большое количество тепла, большие контактные давления и интенсивное трение между инструментом, заготовкой
истружкой приводят к износу режущего инструмента.
Взоне резания начинают действовать силы молекуляр-
ного сцепления адгезия (слипание материала инструмента со стружкой). Это сопровождается вырыванием отдельных частиц материала инструмента сходящей стружкой и ускоряет процесс его изнашивания.
При обработке без смазочно-охлаждающих жидкостей преобладающим становится абразивное изнашивание инструментов по передней и задней поверхностям.
Износ режущего инструмента влияет на стойкость режущего инструмента, качество обработки и размеры деталей.
154
Стойкость это промежуток времени непрерывной работы инструмента, в течение которого его износ достигает установленной величины. Стойкость измеряется в минутах и обозначается буквой Т. Наибольшее влияние на износ, а соответственно, и на стойкость оказывает скорость резания V.
Обычно задаются такими режимами резания, чтобы стойкость инструмента была в пределах 30…90 мин.
9. Материалы для изготовления режущих инструментов
Режущая часть инструментов работает при высоких температурах, на нее действуют высокие статические и динамические нагрузки. Поэтому инструментальные материалы должны обладать высокими твердостью, прочностью, износостойкостью, теплостойкостью, теплопроводностью и др.
Углеродистые инструментальные стали для изго-
товления режущих инструментов содержат 0,9…1,3 % С (У10, У11, У12, У13). Увеличение его содержания в стали повышает ее твердость и хрупкость. Твердость закаленной и отпущенной углеродистой инструментальной стали 60…63 HRC. Эти стали обладают низкой теплостойкостью (до 200…250 С), применение их ограничено. Из них изготавливают инструменты, работающие со скоростями резания, не превышающими 15…18 м/мин: (метчики, плашки, ручные развертки, напильники, шаберы, ножовочные полотна и др.).
Легированные инструментальные стали имеют бо-
лее высокие прочность, прокаливаемость, вязкость, стойкость против износа, теплостойкость. Изготовленные из них инструменты обладают более высокими режущими свойствами, менее склонны к деформациям и появлению трещин при закалке. Теплостойкость легированных инст-
155
рументальных сталей не превышает 300 С, поэтому изготовленные из них инструменты можно использовать лишь для работы при умеренных скоростях резания (15…25 м/мин). Из них изготавливают сверла, развертки, метчики, плашки, протяжки и др.
Быстрорежущие стали легированные инструментальные стали, содержащие значительное количество вольфрама (8,5…19 %), хрома (3,8…4,4 %), молибдена, ванадия, кобальта и некоторых других элементов, имеют теплостойкость 600…650 С. Такие стали могут работать со скоростями резания, в 3–4 раза большими, чем инструментальные углеродистые стали. После закалки и отпуска твердость быстрорежущей стали достигает 62…65 HRC и сталь приобретает высокие режущие свойства.
Из вольфрамовых быстрорежущих сталей (Р9) изготавливают резцы, зенкеры, фрезы. При изготовлении сложных инструментов, которые должны обладать более высокой стойкостью (фасонные резцы, зубообрабатывающие инструменты и др.), используют сталь Р18.
Для изготовления инструментов, работающих в более тяжелых условиях (прерывистое резание, вибрации, обработка труднообрабатываемых нержавеющих и жаропрочных сталей), применяют кобальтовые быстрорежущие стали
(Р9К5, Р9К10, Р18К5Ф2).
Инструменты, используемые для чистовой обработки (протяжки, развертки, шеверы), изготавливают из ванадиевых сталей (Р9Ф5, Р14Ф4), а для черновой обработки из вольфрамомолибденовых быстрорежущих сталей (Р9М4, Р6М3).
Металлокерамические твердые сплавы. Высокая твер-
дость, износостойкость, прочность, теплостойкость, достигающая 900…1000 С, позволяют обрабатывать твердосплавными инструментами различные металлические и неметаллические материалысоскоростямирезаниядо800 м/мин.
156
Металлокерамические твердые сплавы изготавливают из мелкозернистых исходных порошков весьма твердых и тугоплавких карбидов вольфрама (WC), титана (TiC), тантала (TaC), смешанных в различных пропорциях с порошком кобальта, который служит связкой. Из полученной смеси прессуют стандартизованные пластинки и спекают при температуре 1500…1900 С. Их припаивают к державкам инструментов либо закрепляют механическим способом.
Твердые сплавы подразделяют на три группы: вольфра-
мовые (ВК), титановольфрамовые (ТК) и титанотантало-
вольфрамовые (ТТК). В сплавах группы ВК (ВК2, ВК3, ВК4, ВК6, ВК8 и др.) цифра после буквы К обозначает процентное содержание кобальта, остальное карбид вольфрама.
Для крупнозернистых твердых сплавов с величиной зерен исходного порошка 3…5 мкм к обозначению марки прибавляется буква В (например, ВК6В), а у мелкозернистых
свеличиной зерен 0,5…1,5 мкм буква М (например, ВК6М).
Всплавах группы ТК (Т5К10, Т5К12В, Т14К8, Т15К6, Т30К4 и др.) цифра после буквы Т обозначает процентное
содержание карбида титана, а после К процентное содержание кобальта, остальное карбид вольфрама.
В сплавах группы ТТК (ТТ7К12, ТТ7К15) цифра после второй буквы Т обозначает процентное содержание карбидов титана и тантала в сумме, после К содержание кобальта, остальное карбид вольфрама.
Сувеличением содержания кобальта в сплаве прочность
ивязкость его повышаются, а твердость и износостойкость снижаются. Поэтому сплавы с бóльшим содержанием кобальта применяют для инструментов, работающих в тяжелых условиях, при больших и неравномерных нагрузках. Сплавы с малым содержанием кобальта используют для инструментов, работающих при сравнительно небольшой и равномерной нагрузке, но с высокой скоростью резания.
157
Инструменты из сплавов ВК предназначены для обработки чугуна, цветных сплавов, пластмасс, а из сплавов группы ТК для обработки сталей и других вязких материалов. Сплавы ТТК по своим свойствам занимают промежуточное место между сплавом Т5К10 и быстрорежущей сталью и предназначены для черновой обработки сталей с загрязненной коркой. Стойкость резца с пластинкой из сплава ТТК в 3,5 раза превышает стойкость резца из быстрорежущей стали Р18. Некоторые сплавы группы ТТК используют при обработке труднообрабатываемых жаропрочных сталей.
Сложные по форме инструменты небольших размеров (сверла, прорезные фрезы, коронки концевых фрез и др.) часто изготавливают из пластифицированных твердых сплавов, получаемых спеканием порошка карбида титана с металлическими сплавами.
Описанные твердые сплавы содержат в значительном количестве дефицитный вольфрам. Поэтому начат промышленный выпуск безвольфрамовых твердых сплавов (БТТС) на основе карбидов и карбидонитридов титана с никельмолибденовой связкой (КНТ16, ТН20, ТН50).
Разработан гексанит-Р, являющийся монокристальным нитридом бора. Гексанит-Р изготавливают в виде вставок к проходным, расточным, подрезным резцам и торцевым фрезам. Гексанит-Р способен работать в условиях больших ударных нагрузок при обработке закаленных сталей, чугунов, сплавов высокой твердости.
Широко применяются износостойкие покрытия режущих лезвий инструментов, например, ионно-плазменное напыление карбонитридом титана используют на многих машиностроительных предприятиях.
Минералокерамические материалы. Основой минера-
локерамических материалов является оксид алюминия Al2O3, из порошка которого прессованием с последующим спекани-
158
ем изготовляют пластинки нужных размеров и формы, которые затем закрепляют на державках режущего инструмента. Высокая теплостойкость (1200 С) инструментов из минералокерамики, их высокая твердость, тепло- и износостойкость, высокие режущие способности дают возможность обрабатывать материалы со значительно большими скоростями, чем инструментами из твердых сплавов. Но минералокерамика имеет высокую хрупкость и малое сопротивление изгибающим нагрузкам, поэтому ее используют для инструментов, работающих при чистовой обработке без ударов. Для повышения прочности пластин в минералокерамику добавляют вольфрам, молибден, бор, титан и др. Такие материалы называют керметами, используют их при обработке труднообрабатываемых материалов.
Абразивные материалы. Для изготовления абразивного инструмента используют искусственные материалы.
Электрокорунд используется для обработки закаленной итермическинеобработаннойстали, ковкогочугуна, бронзыидр.
Карбид кремния по сравнению с электрокорундом обладает более высокой твердостью и меньшей вязкостью, поэтому его используют для шлифования более хрупких материалов, а также некоторых цветных сплавов. Черный карбид кремния, имеющий в составе не менее 95 % SiC, применяют при шлифовании чугуна, латуни, бронзы, алюминиевых сплавов. Зеленый карбид кремния, содержащий не менее 97 SiC и имеющий еще большую твердость, используют для обработки инструментов из металлокерамическихтвердыхсплавов.
После выплавки в электропечах электрокорунд и карбид кремния дробят, просеивают и получают шлифпорошки, шлифзерна и микропорошки, которые используют для изготовления абразивного инструмента.
Синтетические алмазы высокой твердости получают из графита при температурах порядка 2500 С и давлении свы-
159
ше 104 МПа. Используют для изготовления кругов, брусков, надфилей, напильников и др. Применяются они для окончательного шлифования (доводки) твердосплавного инструмента, а также для особо тонкой чистовой обработки.
Эльбор кубический нитрид бора – получают при давлении свыше 105 МПа и температуре, близкой к 1700 С. Твердость его приближается к твердости алмаза. Эльбор сохраняет свою прочность при температуре до 930 С. Стальные детали гораздо лучше шлифуются абразивными инструментами из эльбора, чем из алмаза, так как теплостойкость его выше.
10. Классификация и условные обозначения металлорежущих станков
1. По уровню специализации станки подразделяют на
универсальные, специализированные и специальные.
Универсальные, станки общего назначения, применяют для обработки небольших партий деталей широкой номенклатуры (разных по форме и размерам) в условиях единичного и серийного производства.
Специализированные используются для обработки однотипных деталей узкой номенклатуры в условиях крупносерийного производства (токарные станки для обработки коленчатых валов и др.).
Специальные предназначены для обработки одной определенной или нескольких почти одинаковых деталей (одного типоразмера) в условиях массового, иногда крупносерийного производства.
2. По технологическому признаку в зависимости от характера обработки все металлорежущие станки делятся на
160