
Оперативно-производственное планирование
..pdf
К |
|
= |
Кр |
, |
(3.5) |
|
з |
Кп |
|||||
|
|
|
|
где Кр – расчётное количество рабочих мест; Кп – принятое количество рабочих мест.
Пример. Такт поточной линии составляет 0,5 ч на изделие. Длительность операции по покраске изделия равна 0,75 ч, следовательно, необходимое количество рабочих мест для этой операции на поточной линии
Кр = 0,75 =1,5. 0,5
Принятое количество рабочих мест равняется целому числу, следовательно, составит 2 рабочих места. Тогда коэффициент загрузки рабочего места
Кз = 1,5 = 0,75, или75 %. 2,0
При непрерывном движении конвейера ему придаётся скорость (v, м/мин), определяемая по формуле
v = |
l0 |
, |
(3.6) |
|
|||
|
r |
|
где l0 – расстояние между осями двух соседних изделий на конвейере, м.
Пример. Расстояние между осями двух соседних изделий на конвейере составляет 3 м. Такт конвейера составляет 0,25 ч на изделие. Скорость конвейера
v = 3,0 = 0,2 м/мин. 15
На машиностроительных предприятиях скорость движения конвейера колеблется в пределах 0,1–4 м/мин. При более высоких скоро-
101

стях работа на конвейере может стать опасной для рабочих. Рациональными скоростями рабочего конвейера считаются 0,5–2,5 м/мин при сборке относительно небольших объектов1. Если требуется большая скорость движения конвейера, то применяют конвейер пульсирующего типа.
Расчёт объёма производственной партии (серии)
Партия деталей – это число одноимённых деталей, которые непосредственно обрабатываются в производстве с однократной затратой подготовительно-заключительного времени, т.е. без переналадки оборудования. Партия (серия) изделий – это количество единовременно (или беспрерывно) запускаемых на сборку или выпускаемых готовых изделий.
Размер партии является одним из основных календарно-пла- новых нормативов в серийном производстве, оказывающих существенное влияние на экономические показатели производства, в том числе на себестоимость изделия, производительность труда, длительность производственного цикла, оборачиваемость оборотных активов, рентабельность продукции.
В условиях серийного производства изготовление деталей или изделий разных наименований на рабочем месте происходит в порядке их чередования. Запуск и выпуск каждого вида деталей (изделий) также производится через некоторые интервалы времени. Изготовление партий деталей на каждом рабочем месте связано с переналадкой его на данную работу. Чем больше размеры запускаемых в производство партий, тем большими становятся периоды между переналадками рабочего места, а также между запусками очередных партий деталей.
К положительным экономическим последствиям увеличения производственной (обработочной) партии относятся:
а) сокращение затрат времени на переналадку оборудования и, как следствие, заработной платы наладчиков;
1 Шепеленко Г.И. Организация и планирование производства… С. 51.
102
б) увеличение действительного фонда времени работы оборудования;
в) повышение производительности труда основных производственных рабочих;
г) упрощение процедуры планирования и сокращение учётных операций.
Отрицательными экономическими последствиями увеличения партии деталей являются:
а) увеличение запасов продукции (деталей, заготовок) на складах и, как следствие, увеличение размеров складских площадей, затрат на хранение продукции (деталей, заготовок) и оборотных средств;
б) увеличениедлительностипроизводственногоциклавцехах. Учитывая положительные и отрицательные моменты, необхо-
димо производить расчёт оптимального размера партии деталей (изделий), запускаемых в производство. Данный расчёт может производиться тремя способами.
Первый способ расчёта основывается на минимизации затрат. С использованием расчётно-аналитического метода находится такое количество деталей в партии, при котором общая сумма затрат на одну деталь принимает минимальное значение. В соответствии с этим методом все затраты по изготовлению партии деталей можно разделить на две категории:
1)постоянные затраты, абсолютная величина которых не зависит от размера партии, а при пересчёте на одну деталь снижается по мере увеличения размера партии. К ним относят затраты по запуску партии деталей в производство, в том числе затраты на переналадку оборудования, на оформление документации, планирование и учёт производства, затраты на выполнение подготовительнозаключительных работ и т.п.;
2)переменные затраты, величина которых неизменна в расчёте на одну деталь, но увеличивается в общей своей сумме по мере увеличения размера партии (удельные затраты материалов, величина сдельной оплаты труда и т.д.).
103
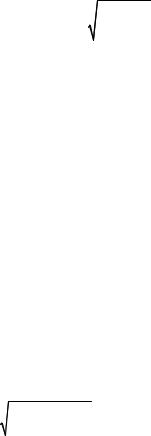
Экономически целесообразный размер партии деталей (nопт), минимизирующий суммарную величину этих затрат, определяется по формуле
nопт = |
2Сзап N |
, |
(3.7) |
|
Cизг η |
||||
|
|
|
где Сзап – постоянные затраты по запуску партии деталей в обработку (затраты на наладку, оформление документации, включение партии в график запуска и выдачу нарядов исполнителям, учёт движения партии в ходе обработки и т.п.), руб.; Сизг – переменные затраты по изготовлению одной детали (материалы, сдельная заработная плата и др.), руб.; N – количество деталей, которое необходимо изготовить согласно производственной программе на плановый период, шт.; η – коэффициент потерь от связывания средств в незавершённом производстве, равный норме прибыли на капитал.
Пример. Затраты по запуску партии деталей в обработку составляют 2000 руб., количество деталей, которое необходимо изготовить согласно производственной программе на плановый период, равно 7000 шт., переменные затраты по изготовлению одной детали составляют 100 руб., коэффициент потерь от связывания средств в незавершённом производстве равен 110 %.
Экономически целесообразный размер партии деталей составит:
n |
= |
2 2000 7000 |
= 505 дет. ≈ 500 дет. |
|
|||
опт |
|
100 1,1 |
|
|
|
Рассчитанный экономически целесообразный размер партии в последующем корректируется в зависимости от конкретных производственных условий (количество наименований деталей и изделий, подлежащих изготовлению в плановом периоде, пропускная способность оборудования, трудоёмкость производственной программы и т.д.).
104

Основной недостаток первого способа расчёта партии деталей заключается в том, что он не учитывает степень загрузки оборудования и продолжительность производственного цикла.
Второй способ расчёта партии деталей основывается на наиболее полном использовании оборудования и предусматривает расчёт предельно допустимого соотношения между подготовительнозаключительным временем и штучным временем ведущей операции.
Размер партии рассчитывается по ведущей операции детали и является обязательным для других операций. Ведущей при этом считается операция с самым длительным подготовительнозаключительным временем:
−в литейных цехах – по формовке;
−в кузнечно-штамповочных цехах – по ковке или штамповке;
−в механических цехах – по операциям с наиболее трудоёмкой наладкой;
−в сборочных цехах – по операциям, оснащённым наиболее сложными приспособлениями.
Расчёт оптимального размера партии деталей может производиться по формуле, рекомендуемой А.И. Ильиным1:
n = |
tп.з |
, |
(3.8) |
|
tоп a |
||||
опт |
|
|
||
|
|
|
где tп.з – подготовительно-заключительное время, мин; tоп – норма времени на операцию, мин; a – коэффициент допустимых потерь времени на переналадку оборудования.
Коэффициенты допустимых потерь времени на переналадку оборудования определяются с учётом типа производства, материалоёмкости деталей. Коэффициент наладки составляет для крупносерийного производства от 0,02 до 0,05, для среднесерийного – от 0,03 до 0,08, для мелкосерийного – от 0,05 до 0,12.
1 Ильин А.И. Планирование на предприятии : учеб. пособие. – Минск: Новое знание, 2005. – С. 634.
105

Пример. Подготовительно-заключительное время на выпуск партии деталей составляет 40 мин, норма времени на выполнение операции – 4 мин. Коэффициент допустимых потерь времени на переналадку оборудования равен 0,1. Оптимальный размер партии составит:
nопт = |
|
40 |
|
= 100 дет. |
|
|
|
|
|
|
|||
4 |
0,1 |
|
||||
Л.А. Одинцова1 предлагает рассчитывать размер минимальной |
||||||
и ориентировочной партий деталей. |
|
|||||
Расчёт минимального размера партии nmin |
производится по |
|||||
формуле |
|
|
|
|
|
|
nmin = |
tп.з (1 − a) |
, |
(3.9) |
|||
|
||||||
|
|
|
|
tшт a |
|
где tп.з – подготовительно-заключительное время на переналадку оборудования по ведущей операции (операции с наиболее сложной и трудоёмкой переналадкой оборудования), мин; tшт – штучное время по той же ведущей операции, мин/шт.; а – коэффициент допустимых потерь времени на переналадку оборудования.
Пример. Подготовительно-заключительное время на переналадку оборудования по ведущей операции составляет 40 мин, штучное время по той же ведущей операции – 4 мин. Коэффициент допустимых потерь времени на переналадку оборудования равен 0,1. Минимальный размер партии составит:
nmin |
= |
40 (1− 0,1) |
= 90 дет. |
|
|||
|
|
4 0,1 |
Размер ориентировочной партии (nор, шт.) учитывает лишь допустимые потери от связывания оборотных средств и пригоден для самых предварительных расчетов:
1 Одинцова Л.А. Планирование на предприятии… С. 169–171.
106
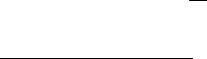
nop = ϕ N , |
(3.10) |
где ϕ – коэффициент, определяющий максимальное отношение
размера партии к годовой программе выпуска деталей. Принимается для мелкосерийного производства в диапазоне от 0,05 до 0,12, для крупносерийного – от 0,02 до 0,06.
Пример. Коэффициент, определяющий максимальное отношение размера партии к годовой программе выпуска деталей, равен 0,1. Производственной программой предусмотрен выпуск 7000 деталей. Ориентировочный размер партии
nор = 0,1 7000 = 700 шт.
Третий способ расчёта партии деталей основывается на производительности труда, учитывает минимальное штучное время операции (ti), затрачиваемое при изготовлении детали в данном цехе. Он базируется на том, что продолжительность обработки данной партии на любом рабочем месте не должна быть менее смены. Это условие объясняется стремлением не допустить переналадки оборудования для обработки других деталей в течение одной смены. Расчёт партии деталей ведётся по формуле1
n = |
Fсм |
, |
(3.11) |
|
ti
где Fсм – сменный фонд времени оборудования, ч.
Пример. Минимальное штучное время на выполнение операции составляет 0,1 ч. Сменный фонд времени оборудования составляет 7 ч. Размер партии
n = 7 = 70 дет. 0,1
1 Шепеленко Г.И. Организация и планирование производства… С. 68.
107
Расчёт размера партии деталей по второму способу целесообразно проводить при больших потерях времени на переналадку, а по третьему способу – при отсутствии или незначительном времени переналадки техники.
Расчётный размер партии деталей при любом способе должен рассматриваться как предварительный. В последующем он корректируется с учётом организационно-производственных и экономических факторов, среди которых наиболее важными являются:
1)количество деталей в партии должно обеспечивать полносменную загрузку рабочего места;
2)размер партии деталей должен быть кратен месячной программе выпуска;
3)размер партии деталей должен соответствовать стойкости технологической оснастки;
4)для крупногабаритных, тяжёлых деталей размер партии должен варьироваться в зависимости от наличия производственных, складских площадей и грузоподъёмности транспортных средств;
5)размеры партий деталей в предшествующих по технологическому маршруту цехах должны быть равны размерам партий в последующих цехах или в кратном отношении больше, так как себестоимость единицы продукции и время связывания оборотных средств увеличиваются от заготовительной к сборочной фазе производственного цикла;
6)размер партии деталей должен рассчитываться с учётом срочности выполнения заказа, необходимости обеспечения экономически целесообразной загрузки дорогостоящего уникального оборудования.
Расчёт частоты и периодичности запуска деталей (изделий) в производство
Если производственная программа изготовления деталей (N) больше оптимальной партии (nопт), то определяют частоту (количество повторений) запуска партий в производство (k) по формуле
k = |
N |
. |
(3.12) |
|
|||
|
nопт |
|
108

Периодичность запуска партии деталей в производство (τ) определяется по формулам:
τ = |
|
nопт |
|
(3.13) |
||
Nсут |
||||||
|
|
|||||
или |
|
Др |
|
|
|
|
τ = |
|
, |
(3.14) |
|||
|
|
|||||
|
|
k |
|
где nопт – размер оптимальной партии деталей, шт.; Nсут – суточная (дневная) программа выпуска деталей (или суточная потребность в деталях), шт.; Др – число рабочих дней, дн.
Пример. Производственной программой предусмотрен выпуск 7000 изделий. Оптимальный размер партии равен 1000 изделий. Предприятие работает 250 дн. в году.
Частота запуска партий в производство
k= 7000 = 7 запусковвгод. 1000
Суточная программа выпуска
Nсут = 7000 = 28 шт.
250
Периодичность запуска изделий в производство составит:
τ = |
1000 |
= 36 дн. |
или τ = |
250 |
= 36 дн. |
|
|
||||
28 |
|
7 |
|
В многономенклатурном производстве установление для каждой детали индивидуального размера партии усложняет ОКП, поэтому всю номенклатуру деталей изделия распределяют по равным периодам запуска партий в производство (один раз в 3 мес., в 2 мес. и т.д.). В соответствии с принятой периодичностью запуска размер партий деталей (nк) корректируют:
nк = τ Nсут . |
(3.15) |
109
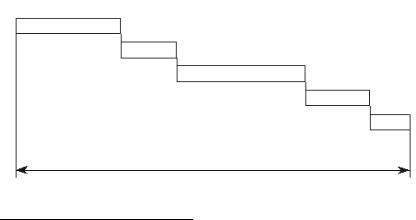
Пример. Учитывая данные предыдущего примера, откорректируем размер оптимальной партии, принимая во внимание, что её запуск в производство осуществляется один раз в 30 дн.:
nк = 30 28 = 840 шт.
Расчёт длительности технологического цикла изготовления партии деталей
Определение длительности технологического цикла изготовления партии деталей можно проиллюстрировать применительно к механической обработке партии деталей. Этот расчёт является типовым и применяется с учётом специфики технологий во всех цехах промышленных предприятий1.
Длительность совокупного цикла механической обработки партии деталей зависит от способа календарной организации процесса. Возможны три вида движения партии деталей по операциям процесса: последовательный, параллельный и параллельно-после- довательный. При последовательном виде движения партия из n деталей целиком передаётся на последующую операцию после окончания её обработки на предыдущей операции. График последовательного вида движения представлен на рис. 3.1.
nt1
nt2
nt3
nt4
nt5
Tц пос
Рис. 3.1. График последовательного вида движения партии деталей
1 Логистика: учеб. / под ред. Б.А. Аникина. – М.: ИНФРА-М, 2000. – С. 168.
110