
Оперативно-производственное планирование
..pdfставляет 0,2 ч/шт. Определите производственную мощность станка
сЧПУ.
14.Площадь для сборки изделия составляет 15 м2, полезная площадь цеха равна 1500 м2, производственный цикл сборки составляет 10 рабочих дней, в году – 248. Запланируйте производственную мощность сборочного цеха.
15.Определите трудоёмкость комплекта приведённого изделия и производственную мощность участка, если известно:
− на участке шестерён механического цеха установлено 5 токарных станков, на которых обрабатываются детали изделий А,
Би В в соотношении 48, 36 и 16 %;
−трудоёмкость обработки комплекта деталей изделия А равна
10 ст.-ч;
−трудоёмкость обработки комплекта деталей изделия Б равна
20 ст.-ч;
−трудоёмкость обработки комплекта деталей изделия В равна
15 ст.-ч;
−плановый фонд времени работы оборудования составляет
16 500 ч.
16. Полезная площадь сборочного цеха составляет 2200 м2. Цех работает 248 дн. в году. Площадь, отводимая под сборку одного изделия, составляет 15 м2, длительность цикла сборки – 3 дн. Производственной программой предприятия на плановый период предусмотрена сборка 15 тыс. шт. изделий. Определите полезную площадь сборочного цеха, необходимую для выполнения производственной программы.
17. Определите пропускную способность и коэффициент загрузки по каждой группе оборудования, если известно:
− в цехе установлено 17 ед. оборудования, в том числе токарного – 5, фрезерного – 8, шлифовального – 4;
91
−число рабочих дней в месяце – 20, режим работы оборудования – двухсменный, продолжительность смены – 8 ч;
−фактически отработано за месяц станко-часов (загрузка оборудования): по токарной группе – 1700, по фрезерной группе – 2000, по шлифовальной – 900.
18. Определите мощность сборочного цеха, загрузку, пропускную способность сборочных площадей и коэффициент загрузки производственной площади, если известно:
−площадь сборочного цеха равна 5000 м2, площадь, занимаемая проходами, проездами, под обслуживающие и бытовые помещения, составляет 40 % площади цеха;
−габаритные размеры собираемого изделия 10×2 м2, рабочая зонадлясборкиизделия равна 120 % площади, занимаемой изделием;
−длительность цикла сборки одного изделия – 10 рабочих
дней;
−число рабочих дней в году – 248;
− производственной программой предусмотрена сборка 3000 изделий в год.
19.Мощность цеха составляет 7 800 000 деталей в год, годовой планируемый объём выпуска равен 7 000 000 деталей. Определите плановый коэффициент использования мощности.
20.Определите плановый коэффициент использования производственной площади сборочного цеха, если известно:
− в течение квартала (66 рабочих дней) цех собирает 280 изде-
лий;
−длительность цикла сборки одного изделия – 9 дн.;
−площадь, занимаемая одним изделием при сборке, – 12 м2;
−общая площадь цеха – 640 м2, в том числе вспомогательная (под обслуживание, проходы, проезды) – 35 %.
92
21.Определите выпуск продукции в натуральном выражении
врасчёте на 1 м2 полезной производственной площади, если из-
вестно, что общая площадь цеха составляет 640 м2, в том числе вспомогательная (под обслуживание, проходы, проезды) – 15 %.
Втечение года в цехе производится сборка 1632 изделий.
22.Определите коэффициент экстенсивной нагрузки оборудования, если известно, что фактический фонд времени работы оборудования составил 3700 ч в год, а плановый действительный фонд времени – 3800 ч в год.
23.На токарном участке цеха имеется в наличии 10 станков, из них установлено и готово к работе 8 станков, фактически эксплуатируется 7. Определите удельный вес установленного оборудования во всём наличном парке оборудования, удельный вес фактически работающего оборудования по отношению к наличному оборудованию, удельный вес фактически работающего оборудования во всём установленном оборудовании.
24.Фактическая производительность оборудования по итогам отчётного года составила 50 дет./ч при максимально возможной производительности 65 дет./ч. Определите коэффициент интенсивной нагрузки оборудования.
25.Коэффициент экстенсивного использования оборудования составил 0,97, а коэффициент интенсивного использования оборудования – 0,77. Определите величину коэффициента интегральной нагрузки оборудования.
93
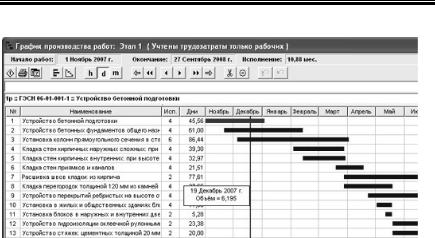
Глава 3
ОПЕРАТИВНО КАЛЕНДАРНОЕ ПЛАНИРОВАНИЕ
ПРОИЗВОДСТВА
Система оперативно-календарного планирования производства (ОКП). Позаказная система ОКП. Покомплектная система ОКП. Подетальная система ОКП. Такт, темп и ритм поточной линии. Расчётное количество рабочих мест на поточной линии. Коэффициент загрузки рабочего места. Расчёт скорости конвейера. Партия деталей. Серия изделий. Планирование оптимального размера партии деталей (серии изделий). Частота и периодичность запуска партии деталей в производство. Последовательный, параллельный и параллель- но-последовательный виды движения деталей. Расчёт длительности технологического цикла изготовления партии деталей. Длительность производственного цикла изделия. Расчёт сроков опережения запуска-выпуска изделий по цехам. Массовое производство. Внутрилинейные и межлинейные заделы. Технологический, транспортный, оборотный и резервный (страховой) заделы. Подетальный стандарт-план. Серийное производство. Единичное производство. Прямое и обратное планирование. Цикловой график выполнения заказа. Карта заказа.
94

3.1. Системы оперативно календарного планирования производства
Выбор системы планирования, как совокупности методик и способов ведения плановой работы на предприятии, определяется внутреннимиособенностями ивнешнимиусловиями его деятельности.
Система оперативно-календарного планирования производст-
ва (ОПК) – это методика и техника выполнения плановых работ, служащая основой реализации функций оперативного планирования производства1.
Систему ОКП характеризуют следующие параметры:
−планово-учётная единица, т.е. первичный объект планирования и учёта объёма производства продукции (работ, услуг);
−состав календарно-плановых нормативов;
−порядок оформления плановой и учётной документации. Главным параметром системы ОКП является планово-учётная
единица, в соответствии с которой определяется тип системы ОКП. Выбор планово-учётной единицы системы ОПП зависит от типа производства, который оказывает существенное влияние на степень централизации функций планирования, состав календарно-плано- вых нормативов, порядок оформления плановой и учётной документации.
Вне зависимости от типа, каждая система ОКП должна отвечать следующим требованиям:
1)обеспечивать взаимосвязь с технико-экономическим планированием;
2)гарантировать взаимосвязь календарного планирования
иоперативного управления производством;
3)комплексно охватывать все вопросы оперативно-планового руководства, включающего в себя составление заданий и графиков производства, их обеспечение и доведение до непосредственных
1 Одинцова Л.А. Планирование на предприятии… С. 164.
95
исполнителей, оперативный учёт, контроль и регулирование производства.
Несмотря на некоторые различия в трактовках систем ОКП у разных авторов (см., например: Загородников С.В., Сивчикова Т.Ю., Носова Н.С. Оперативно-производственное планирование: учеб. пособие. М.: Дашков и К°; Саратов: БизнесВолга, 2009. 288 с.; Ильин А.И. Планирование на предприятии: учеб. пособие. Минск: Новое знание, 2005. 656 с.; Одинцова Л.А. Планирование на предприятии: учеб. для студ. высш. учеб. заведений. М.: Академия, 2007. 272 с. и др.), в теории и практике планирования выработаны три основные системы ОКП:
1)позаказная;
2)покомплектная;
3)подетальная.
Рассмотрим основные особенности каждой из систем ОКП.
Позаказная система оперативно-календарного планирова-
ния применяется в единичном производстве для разовых и редко повторяющихся заказов. Планово-учётной единицей является заказ.
При этом под заказом понимается заявка покупателя (заказчика) на определённое количество специально созданных или изготовленных для него изделий. Вид заказа, его стоимость, порядок расчётов, передачи продукции, срок выполнения заказа определяется в договоре с заказчиком.
При этой системе разрабатывают следующие календарно-
плановые нормативы:
−длительность производственного цикла изготовления изделий или выполнения заказа;
−сроки опережения запуска-выпуска изделий по цехам – исполнителям заказа;
−срокзапуска заказавпроизводствои срок еговыполнения. Основу позаказной системы планирования составляет цикло-
вой сквозной график, в котором указываются очерёдность работ над изделием, сроки их выполнения и исполнители.
96

Покомплектная система оперативно-календарного плани-
рования характерна для серийного производства. Планово-учётной единицей является комплект узлов и деталей.
При комплектной системе разрабатывают следующие кален-
дарно-плановые нормативы:
−длительностьпроизводственногоциклаизготовленияизделий;
−сроки опережения запуска-выпуска изделий по цехамисполнителям;
−такт поточных линий;
−размер заделов изделий на поточных линиях (межоперационных, страховых, транспортных);
−размер партий изделий;
−норматив НЗП;
−сроки запуска-выпуска изделий.
В зависимости от состава комплекта различают следующие разновидности комплектной системы1:
1.Комплектно-узловая система применяется в условиях дли-
тельных циклов сборки изделий, планово-учётной единицей является комплект деталей, образующих конструкторский (сборочный) узел; планирование осуществляется таким образом, что все детали подаются к моменту сборки данного узла изделия.
2.Комплектно-групповая система, при которой планово-
учётной единицей является групповой комплект. Детали группируются по технологическому признаку. В групповой комплект входят детали, имеющие одинаковый технологический маршрут обработки, применяемое оборудование и технологическую оснастку, одну и ту же периодичность запуска и очерёдность подачи на сборку.
3.Машинокомплектная система основана на том, что задания цехам выдаются в виде перечня номеров изделий с указанием времени их комплектования деталями и сборорчными единицами данного цеха. За планово-учётную единицу принимают комплект дета-
лей, относящихся к определённому изделию и обрабатываемых в данном цехе. Разновидностью этой системы является условный
1 Одинцова Л.А. Планирование на предприятии… С. 165.
97
машинокомплект, в который включают детали, относящиеся к различным по наименованию изделиям и обрабатываемые в данном цехе. При формировании условного машинокомплекта выбирается одно изделие, имеющее наибольший удельный вес в программе предприятия и выпускаемое в течение всего планового периода. По отношению к этому изделию определяется удельный вес (по количеству штук) всех остальных изделий программы.
4. Суткокомплектная система, при которой планово-учетной единицей является комплект деталей разных изделий, подлежащих изготовлению в плановом периоде. Суткокомплект формируется исходя из суточной потребности в деталях, входящих в данный комплект.
Подетальная система оперативно-календарного планиро-
вания наиболее эффективна в условиях массового и крупносерийного производства. Она является одной из самых сложных. Объект планирования – каждое рабочее место, каждая деталь, сборочная единица. Планово-учётной единицей выступает деталь.
При этой системе рассчитывают следующие календарно-
плановые нормативы:
−длительностьпроизводственногоциклаизготовленияизделий;
−срок опережения запуска-выпуска изделий по цехам-испол- нителям;
−такт поточных линий;
−размер заделов на поточных линиях (межоперационных, страховых, транспортных);
−сроки запуска-выпуска изделий по цехам;
−норматив НЗП.
Рассмотренные выше основные системы ОКП отличаются друг от друга по объектам планирования, планово-учётным единицам, составу календарно-плановых нормативов. Выбор системы ОКП производится в зависимости от типа производства, характера выпускаемой продукции и других факторов. Правильный выбор системы ОКП позволяет осуществлять оперативное планирование наиболее эффективным образом.
98
3.2. Расчёт календарно плановых нормативов
Основными календарно-плановыми нормативами являются нормативный размер партии деталей и изделий, периодичность запуска изделий в производство, длительность производственного цикла, сроки опережения запуска-выпуска изделий по цехамизготовителям, ритм и такт производства и т.д.
Расчёт такта поточной линии
Основной расчётной величиной поточной линии является такт потока. Тактом поточной линии называется интервал времени между выпуском и запуском двух очередных изделий на каждом рабочем месте. Такт поточной линии показывает количество времени, необходимое для выпуска единицы изделия. Величина расчётного такта поточной линии (r) находится в зависимости от её производственной программы и определяется по формуле
r = |
Fд |
, |
(3.1) |
|
|||
|
Nвып |
|
где Fд – действительный (полезный) фонд времени работы линии за планируемый период (месяц, сутки, смену), ч; Nвып – производственная программа линии за этот же период, шт.
Показатель, обратный такту поточной линии, характеризующий интенсивность процесса производства, называется темпом поточной линии. Темп поточной линии (R) показывает количество изделий, выпускаемых в единицу времени:
R = |
1 |
. |
(3.2) |
|
|||
|
r |
|
При передаче деталей с операции на операцию передаточными (транспортными) мини-партиями (nтр), например, когда детали очень малы или когда величина такта измеряется секундами, рассчитывают ритм поточной линии (rп) по формуле
rп = r · nтр. |
(3.3) |
99

Пример. Действительный годовой фонд времени работы поточной линии составляет 3500 ч. Производственной программой предусмотрен выпуск 7000 изделий в год.
Такт поточной линии
r = 3500 = 0,5 ч наизд. 7000
Темп поточной линии
R = 1 = 2 изд. / ч 0,5
На основе расчётного такта определяется необходимое расчётное количество рабочих мест для каждой операции линии (РМi):
РМi |
= |
ti |
, |
(3.4) |
|
||||
|
|
r |
|
где ti – норма времени на выполнение i-й операции.
Пример. Такт поточной линии составляет 0,5 ч на изделие. Длительность операции по покраске изделия равна 1 ч, следовательно, необходимое количество рабочих мест для этой операции на поточной линии
РМi = 1,0 = 2 рабочих места. 0,5
При полной синхронизации потока расчётное количество рабочих мест всегда целое число, загрузка оборудования полная, т.е. длительность операции равна такту. При частичной синхронизации операций расчётное количество рабочих мест не равно целому числу, поэтому результат расчёта числа рабочих мест округляется в большую сторону (принятое количество рабочих мест). Коэффициент загрузки рабочего места (Кз) по каждой операции определяется по формуле
100