
Основное технологическое оборудование нефтеперерабатывающих заводо
..pdfМинистерство образования и науки Российской Федерации
Государственное образовательное учреждение высшего профессионального образования «Пермский государственный технический университет»
С.Х. Загидуллин, И.Г. Ложкин, А.В. Беляев
ОСНОВНОЕ ТЕХНОЛОГИЧЕСКОЕ ОБОРУДОВАНИЕ НЕФТЕПЕРЕРАБАТЫВАЮЩИХ ЗАВОДОВ
Утверждено Редакционно-издательским советом университета
в качестве учебного пособия
Издательство Пермского государственного технического университета
2011
УДК 665.63/64:66.02(075.8) З-14
Рецензенты:
канд. техн. наук Н.М. Рябчиков (ООО «Уралпромбезопасность»);
канд. техн. наук, доцент Е.Р. Мошев (Пермский государственный технический университет)
Загидуллин, С.Х.
З-14 Основное технологическое оборудование нефтеперерабатывающих заводов: учеб. пособие / С.Х. Загидуллин, И.Г. Ложкин, А.В. Беляев. – Пермь: Изд-во Перм. гос. техн. ун-та, 2011. – 94 с.
ISBN 978-5-398-00571-4
Кратко рассмотрены теоретические и технологические основы процессов первичной и вторичной переработки нефти. Подробно представлены конструкции и принцип действия основного технологического оборудования нефтеперерабатывающих предприятий.
Предназначено для студентов специальностей «Машины и аппараты химических производств» и «Оборудование нефтегазопереработки» очной и заочной форм обучения.
УДК 665.63/64:66.02(075.8)
ISBN 978-5-398-00571-4 |
© ГОУ ВПО |
|
«Пермский государственный |
|
технический университет», 2011 |
|
2 |
ОГЛАВЛЕНИЕ |
|
ВВЕДЕНИЕ.......................................................................................................................... |
4 |
1. ПЕРВИЧНАЯ ПЕРЕРАБОТКА НЕФТИ....................................................................... |
7 |
1.1. Обезвоживание и обессоливание нефти................................................................. |
7 |
1.2. Прямая перегонка нефти.......................................................................................... |
13 |
1.3. Меры борьбы с коррозией....................................................................................... |
41 |
2. ВТОРИЧНАЯ (ДЕСТРУКТИВНАЯ) ПЕРЕРАБОТКА НЕФТИ................................. |
43 |
2.1. Термокаталитические процессы ............................................................................. |
44 |
2.1.1. Каталитический крекинг................................................................................... |
44 |
2.1.2. Каталитический риформинг............................................................................. |
59 |
2.2. Коксование................................................................................................................ |
65 |
3. ПРОИЗВОДСТВО МАСЕЛ............................................................................................ |
73 |
3.1. Деасфальтизация масел............................................................................................ |
75 |
3.2. Фенольная очистка масел........................................................................................ |
79 |
3.3. Депарафинизация масел........................................................................................... |
81 |
СПИСОК РЕКОМЕНДУЕМОЙ ЛИТЕРАТУРЫ ............................................................. |
93 |
3
ВВЕДЕНИЕ
Сырая нефть является смесью химических веществ, состоящих из нескольких сотен компонентов. Однако основную массу нефти составляют углеводороды: алканы (парафин СnН2n+2); циклоалканы (нафтены СnН2n); арены (ароматические углеводороды СnНn (бензол, толуол)).
В основу классификации нефтей положено преимущественное содержание в них какого-либо класса углеводородов. Различают парафиновые нефти (грозненские, башкирские, татарские); нафтеновые (бакинские); парафинонафтеновые (сураханские); ароматические (чусовские) и др. Кроме того, в органическую часть нефти входят смолистые и асфальтеновые вещества, сернистые соединения, нафтеновые кислоты, фенолы и др. По содержанию серы нефти классифицируются на малосернистые (от 0,1 до 0,5 % серы); сернистые (до 2,5–3 % серы); высокосернистые (более 3 % серы). В нефти присутствуют также минеральные примеси (неорганические) – вода, которая представлена в виде стойких эмульсий, и растворенные в ней соли (NaCl, CaCl2 и др.). Кроме того, нефть содержит взвешенные механические примеси песка, глины, соли тяжелых металлов.
К важнейшим нефтепродуктам относятся:
1. Жидкие топлива, которые разделяются на моторные и котельные. Среди моторных топлив выделяют:
a)карбюраторное, включающее в себя авиационные и автомобильные бензины
итракторное топливо;
б) реактивное, представляющее собой фракции керосина различного состава или их смесь с бензиновыми фракциями (авиакеросин);
в) дизельное, включающее в себя газойли и соляровые фракции.
Котельное топливо используют в топках тепловозов, пароходов, ТЭЦ и в промышленных печах (прямогонный мазут, флотский мазут и различные крекинг-остатки). Флотский мазут имеет температуру замерзания не выше +4 ºС.
2.Газообразные топлива (это сжиженные газы), применяемые для коммунальнобытового обслуживания (смеси пропан-бутана в различных соотношениях).
3.Смазочные масла, которые подразделяются на масла общего назначения и специальные. Масла общего назначения применяют для смазывания трущихся поверхностей (моторные, компрессорные, турбинные и т.д.). К специальным маслам относятся трансформаторные (с температурой застывания не выше –40 ºС), конденсаторное, кабельное и др.
4.Консистентные смазки. Их насчитывается более ста наименований. Они представляют собой нефтяные масла, загущенные специальными мылами, твердыми углеводородами (парафинами, церезинами) и другими загустителями. Смазки делятся на две группы: универсальные и специальные.
5.Индивидуальные углеводороды – алканы (метан, этан, пропан, бутан и др.); алкены (этилен, пропилен, бутилен и др.); ароматические (бензол, толуол, ксилолы и др.). Кроме того, из нефти выделяют предельные углеводороды с большой молекулярной
массой (С16 и выше) – это твердые парафины и церезины. Они применяются в парфюмерии, в спичечной, пищевой промышленности, в качестве загустителей смазок, при изготовлении свеч и в других целях.
6.Нефтяные битумы, которые получают из тяжелых нефтяных остатков (гудронов, асфальтенов, экстрактов селективной очистки, слопов и др.) в основном путем их
4
частичного окисления. Они используются в дорожных, строительных, кровельных работах и т.д.
7. Нефтяной кокс и технический углерод. Их получают путем высокотемпературной обработки тяжелых нефтяных остатков без доступа кислорода, используют в металлургии для изготовления угольных электродов, абразивных материалов и др.
Важнейшими нефтяными продуктами являются моторные карбюраторные топлива – авиационные и автомобильные бензины. Основным свойством бензина, характеризующим его устойчивость против преждевременного воспламенения в камере сгорания, является его детонационная стойкость.
Детонация – это взрывоподобное сгорание топливной смеси со скоростью около 1,5 км/с, которое приводит к разрушению двигателей и снижению их мощности. Это свойство бензина начиная с 1927 года во всем мире измеряется октановым числом (ОЧ). Оно представляет собой условное число, равное процентному содержанию изооктана в его смеси с нормальным гептаном, эквивалентной по своей детонационной стойкости испытуемому бензину в стандартных условиях испытания.
При этом условно принимается, что ОЧ нормального гептана, имеющего цепочечное строение молекул и поэтому легко детонирующего, равно 0, а изооктана, имеющего разветвленную структуру молекул и поэтому обладающего высокой стойкостью к детонации, равно 100 пунктам. В настоящее время эта шкала уже устарела, так как найдены углеводороды, имеющие ОЧ выше 100 пунктов (например, этилбензол (104), толуол (107)). Поэтому сейчас октановая шкала расширена до 120 пунктов.
Определение ОЧ производится двумя методами – моторным и исследовательским. Для этого служит одна и та же испытательная установка, состоящая из одноцилиндрового двигателя, но при различных режимах работы. Моторный метод более «жесткий» (900 об/мин) и моделирует загородную езду. Исследовательский метод более «мягкий» (600 об/мин) и моделирует езду в черте города. Поэтому исследовательский метод дает завышенные значения ОЧ (до 4 пунктов).
Для характеристики детонационной стойкости дизельного топлива (tкип = = 200…350 °С) используется так называемое цетановое число. Цетановое число цетана (C16H34) принято равным ста пунктам, а α-метилнафталина (С10Н7СН3) – десяти.
Прямогонные бензины, получаемые при прямой перегонке нефти, характеризуются низким ОЧ (не выше 50–70 пунктов), что является совершенно недостаточным для использования в современных автомобильных двигателях. Это объясняется тем, что они состоят в основном из низкооктановых компонентов – цепочечных углеводородов.
Для повышения ОЧ прямогонных бензинов используют два основных метода. Первый и наиболее старый из них заключается во введении в состав бензинов ан-
тидетонационных присадок. Основной антидетонационной присадкой является тетраэтилсвинец в смеси с этилбромидом, дихлорэтаном, монохлорнафталином. Такой бензин называется этилированным. В зависимости от состава прямогонных бензинов их ОЧ повышается от 18 до 20 пунктов. Однако эта присадка высокотоксичная и ухудшает условия эксплуатации двигателей.
В настоящее время найдены и используются другие, менее токсичные, присадки (метанол, метилтретбутиловый эфир (МТБЭ) и др.). Они содержат в своем составе кислород, который способствует более полному сжиганию топлива и снижению токсичности выхлопных газов. Метанол является эффективной добавкой, но ядовит и плохо
5
растворим в бензинах при низких температурах. Поэтому более предпочтительной присадкой в настоящее время считается МТБЭ.
Второй, более современный и радикальный метод основан на изменении структуры цепочечных молекул с малой детонационной стойкостью, входящих в состав прямогонных бензинов, с целью их разветвления (изомеризации) без изменения молекулярной массы, а также структурной перестройки с изменением числа атомов водорода (риформинга). Оба эти процесса относятся к группе вторичных каталитических процессов переработки нефти.
Одной из важнейших интегральных характеристик технического совершенства нефтеперерабатывающих заводов (НПЗ) является показатель глубины переработки нефти. Он рассчитывается как отношение объема всех нефтепродуктов, вырабатываемых предприятием в качестве товарных продуктов, за вычетом механических потерь и мазута к объему перерабатываемой нефти. Таким образом, чем меньше на предприятии выпускается в качестве товарного продукта мазута и больше вовлекается его в дальнейшую переработку, тем выше глубина переработки нефти. На современных НПЗ глубина переработки достигает 87–90 % и даже больше.
6
1. ПЕРВИЧНАЯ ПЕРЕРАБОТКА НЕФТИ
Первичная переработка включает в себя процессы подготовки добытой на нефтепромыслах нефти и прямой ее перегонки.
При добыче нефти ее всегда сопровождает пластовая вода, в которой растворены различные соли, хлориды, сульфаты, карбонаты, натрий, кальций, магний. Содержание этих солей может достигать 30 %. Наличие воды и солей в нефти мешает эффективной работе НПЗ. При повышенном содержании воды увеличивается давление в установках перегонки нефти, возрастает расход тепла и снижается производительность оборудования. Еще больший вред приносят хлориды кальция и магния. При высоких температурах в присутствии воды эти соли гидролизируются с образованием летучего хлористого водорода (HCl) по схеме:
CaCl2 + 2H2O ↔ Ca(OH)2 + 2 HCl;
MgCl2 + 2H2O ↔ Mg(OH)2 + 2 HCl.
Хлористый водород при дальнейшем охлаждении растворяется в воде с образованием соляной кислоты, которая вызывает сильную коррозию. Поэтому воду и соли начинают удалять из нефти на нефтепромыслах, а завершают этот процесс на НПЗ.
Обезвоживание и обессоливание – это процессы извлечения из нефти воды и солей путем разрушения водонефтяных эмульсий.
Далее на НПЗ обезвоженная и обессоленная нефть подвергается перегонке. Прямая перегонка нефти – это процесс разделения ее на фракции, различающие-
ся по температуре кипения. Нефть нагревают и частично испаряют с получением дистиллята и остатка, которые отличаются по своему составу от исходной нефти.
1.1. Обезвоживание и обессоливание нефти
Существует два типа процессов удаления воды и солей: обезвоживание и обессоливание. В их основе лежат процессы разрушения водонефтяных эмульсий.
При обезвоживании разрушаются только природные эмульсии, которые образуются при интенсивном перемешивании нефти с буровой водой. При обессоливании предварительно обезвоженную нефть дополнительно смешивают с пресной водой, создавая тем самым искусственную эмульсию, которую затем разрушают.
Нефтяные эмульсии представляют собой эмульсии типа «вода в нефти», которые практически не разрушаются в естественных условиях (разрушаются при длительном отстаивании в течение одного года и более). По внешнему виду это густые мазеобразные смеси, вязкость которых значительно выше вязкости самой нефти.
Существуют следующие способы разрушения нефтяных эмульсий:
1)механические – фильтрование, применение ультразвука и др.;
2)термические – подогрев и отстаивание нефти от воды, промывка нефти горячей водой и др.;
3)электрические – обработка сырой нефти в электрическом поле переменного или постоянного напряжения;
4)химические – обработка сырой нефти специальными поверхностно-активными веществами (ПАВ) (деэмульсаторами).
На практике эти методы часто комбинируют друг с другом. Перемешивание и воздействие электрического поля создает благоприятные условия для увеличения вероят-
7
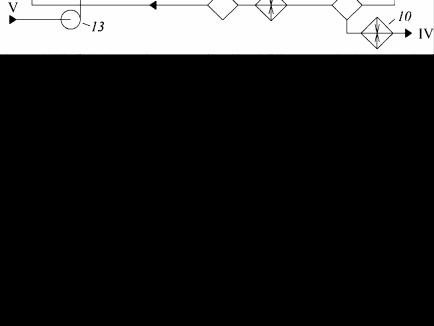
ности столкновения мельчайших частиц воды. Отрицательно заряженные частицы воды начинают передвигаться внутри капли, которая при этом приобретает грушевидную форму, обращенную острым концом к положительно заряженному электроду. При смене полярности происходит изменение конфигурации капли. Отдельные капли стремятся перемещаться к катоду, сталкиваются друг с другом, укрупняются и осаждаются.
Для повышения эффективности укрупнения (коалесценции) в сырую нефть добавляют деэмульсаторы. Принцип действия деэмульсаторов (ПАВ) заключается в ослаблении структурно-механической прочности слоев, обволакивающих капли воды. Наилучшими деэмульсаторами являются неионогенные ПАВы (ОЖК, ОП-10 и др.).
За счет обезвоживания на нефтепромыслах содержание воды в нефти снижается до 0,5–1 %. Одновременно с этим удаляется и основное количество растворенных солей. Однако на НПЗ производится дополнительное более глубокое обезвоживание и обессоливание путем сочетания термохимического отстаивания с обработкой в электрическом поле переменного напряжения. Эти установки называются электрообессоливающими (ЭЛОУ).
Принципиальная технологическая схема
Принципиальная технологическая схема ЭЛОУ приведена на рис. 1.
Сырая нефть, в которую введены расчетные количества деэмульсатора и щелочи, насосом 1 прокачивается через теплообменник 2 и пароподогреватель 3, где нагревается до температуры 110–160 °С, и подается в регулируемый смеситель 4, в котором к нефти добавляется вода. Образовавшаяся в результате перемешивания искусственная
Рис. 1. Принципиальная технологическая схема электрообессоливания нефти: 1, 13 – 16 – насосы; 2 – теплообменник; 3 – пароподогреватель; 4, 7 – смесители; 5, 6 – электродегидраторы; 8, 10, 11 – холодильники; 9 – нефтеотделитель; 12 – емкость. Потоки: I – сырая нефть; II – обессоленная нефть; III – деэмульсатор; IV – солевой раствор; V – свежая вода; VI – пар водяной; VII – конденсат; VIII – содощелочной раствор
8
водонефтяная эмульсия поступает в электродегидратор первой ступени 5. Здесь удаляется основная масса воды и солей (их содержание снижается в 8–10 раз). Далее нефть поступает в электродегидратор второй ступени 6, для чего в нефть вновь подается пресная вода. Общий расход воды составляет около 10 % от массы перерабатываемой нефти.
На некоторых заводах реализована схема противоточной промывки (ПТП), при которой свежая вода вводится только перед электродегидратором 6, а перед электродегидратором 5 используются промывные воды со второй ступени. Это дает возможность сократить расход воды примерно на 10 %.
После ЭЛОУ содержание воды в нефти снижается от 0,5–1,5 до 0,1 % и менее, а содержание солей от 40–3000 мг/л до 3–20 мг/л. Обессоленная и обезвоженная нефть проходит через теплообменник 2, где отдает свое тепло сырой нефти, и через холодильник 8 подается в резервуары обессоленной нефти. Вода, отделенная в ЭЛОУ, поступает в нефтеотделитель 9 для дополнительного отстоя, уловленная нефть через емкость 12 возвращается на прием сырьевого насоса 1, а вода после охлаждения сбрасывается в канализацию и передается на очистку.
Легкие нефти обессоливают при 80–100 °С, однако для большинства нефтей требуется 120–130 °С и выше. Необходимо отметить, что с повышением температуры эффективность работы аппаратов возрастает, но при этом повышается электрическая проводимость нефти, повышается сила тока и усложняется работа изоляторов.
Расход деэмульсаторов колеблется от 10 до 30 г/т и зависит от устойчивости эмульсий воды и нефти. Иногда в сырую нефть вводят щелочь для нейтрализации Н2S и органических кислот.
Основное технологическое оборудование
К основному оборудованию, входящему в состав ЭЛОУ, относятся дегидраторы. В настоящее время в промышленности используются вертикальные, шаровые и го-
ризонтальные электрические дегидраторы.
Вертикальный дегидратор (рис. 2) представляет собой вертикальный цилиндрический сосуд с эллиптическими днищами диаметром 3000 мм, высотой 5000 мм и объемом 30 м3.
Внутри находятся электроды в виде металлических горизонтальных пластин, подвешенных на фарфоровых изоляторах. Сверху аппарата расположены два трансформатора мощностью 5 кВА и напряжением 15–33 кВ.
Снаружи аппарат теплоизолирован, а внутри в нижней части, контактирующей с отстоявшейся водой, футерован слоем торкрет-бетона. Материал корпуса – сталь
16ГС.
Сырая нефть в смеси с водой через вертикальную центральную трубу с распределительной головкой в виде тонкой веерообразной горизонтальной струи вводится в межэлектродное пространство. Обессоленная нефть выводится через верхнее днище, а вода – через нижнее. Для поддержания нагретой сырой нефти и воды в жидком виде внутри электродегидраторов поддерживается повышенное давление. Нагрев, согласно закону Стокса, снижает вязкость нефти и улучшает условия осаждения воды.
Недостатком вертикальных аппаратов является малая площадь осаждения, а следовательно, низкая удельная производительность, поэтому число необходимых аппаратов, соединенных между собой параллельно, достигает 10–12 штук.
9
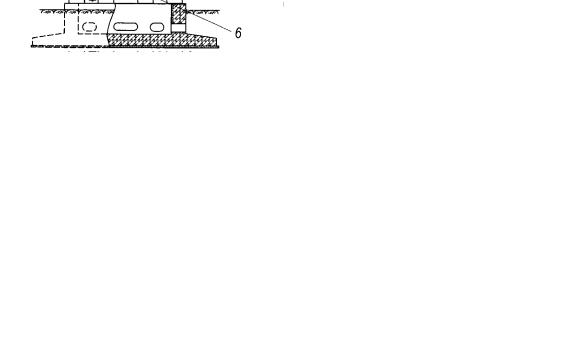
|
|
|
|
|
|
|
|
|
|
|
|
|
|
|
|
|
|
|
|
|
|
|
|
|
|
|
|
|
|
|
|
|
|
|
|
|
|
|
|
|
|
|
|
|
|
|
|
|
|
|
|
|
|
|
|
|
|
|
|
|
|
|
|
|
|
|
|
|
|
|
|
|
|
|
|
|
|
|
|
|
|
|
|
Рис. 2. Вертикальный электродегидратор: |
Рис. 3. Шаровый электродегидратор: 1 – элек- |
||||
1 – корпус; 2 – электроды; 3, 4 – изоляторы; |
троды; 2 – распределительная головка; |
||||
5 – трансформаторы; 6 – манометр; 7 – сиг- |
3 – |
устройство для регулирования расстоя- |
|||
нальные лампы; 8 – распределительная голов- |
ния |
между электродами; 4 – трансформатор; |
|||
ка; 9 – мерное стекло |
|
5 – теплоизоляция; 6 – дренажное отверстие |
На современных установках применяются шаровые электродегидраторы диаметром 10 462 мм, объемом 600 м3 и производительностью 300–500 м3/ч (рис. 3). По принципу действия они аналогичны вертикальным аппаратам. Подача смеси сырой нефти с промывочной водой осуществляется одновременно через три трубы.
Наиболее современными являются горизонтальные аппараты диаметром от 3000 до 3400 мм, длиной от 8240 до 18 650 мм и объемом от 50 до 200 м3. Например, электродегидратор 2ЭГ 160-2 (рис. 4) представляет собой цилиндрический горизонтальный аппарат емкостью 160 м3, внутренним диаметром 3400 мм и длиной около 18,7 м.
Материал корпуса – сталь 16ГС, расчетное давление в аппарате 1,8 МПа, температура 160 °С. Нижняя половина аппарата изнутри защищена от коррозии слоем торкретбетона. В корпусе 1 по длине размещены два одинаковых комплекта устройств, включающие распределитель сырья 8, три плоских горизонтальных электрода 4, 5 и 6, сборник обессоленной нефти 2 (см. рис. 4).
Распределитель сырья представляет собой центральный коллектор с горизонтальными и вертикальными отводами. Горизонтальные отводы имеют перфорацию, вертикальные отводы на концах снабжены распределительными головками, расположенными между нижним и средним электродами. Расстояние между этими электродами (200 мм) меньше расстояния между средним и верхним электродами, равного 300 мм.
Взависимости от характера нефтяной эмульсии аппарат может быть подготовлен
кработе с использованием только вертикальных отводов (горизонтальные заглушены), только горизонтальных отводов, тех и других одновременно. Работа с использованием только вертикальных отводов рекомендуется при переработке стойких эмульсий.
10