
Основное технологическое оборудование нефтеперерабатывающих заводо
..pdf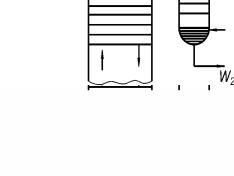
В сложной колонне вследствие отвода боковых погонов в стриппинг-секции количество паров ректификата увеличивается сверху вниз, а количество флегмы достигает максимума в верхней части. Чтобы более равномерно распределять потоки паров и флегмы по высоте сложной колонны, часть тепла для образования флегмы отбирают при помощи промежуточного циркуляционного орошения (рис. 41).
С этой целью с тарелки, расположенной ниже сечения отбора бокового погона, отбирают часть флегмы и прокачивают ее через теплообменник. Здесь она охлаждается, отдавая часть тепла, например, нефти. Охлаж-
денная флегма возвращается в колонну, где контактирует с горячими парами. При этом часть паров конденсируется, увеличивая количество стекающей вниз флегмы.
К преимуществам сложных колонн относятся меньшая громоздкость и металлоемкость по сравнению с блоком простых колонн, а также использование только одного насоса для подачи флегмы (рефлюкса) в верхнюю часть основной колонны. К недостаткам таких колонн относятся пониженная четкость ректификации многокомпонентных смесей и наличие так называемых температурных «налеганий» получаемых фракций продуктов.
1.3. Меры борьбы с коррозией
Сильная коррозия происходит на установках АТ и АВТ. Коррозию вызывают:
1)минеральные соли, содержащиеся в нефти. При нагреве нефти хлориды натрия, кальция и магния разлагаются с образованием хлористого водорода, который в присутствии влаги образует соляную кислоту. Скорость коррозии углеродных сталей в присутствии влажного хлористого водорода достигает 5–20 мм в год;
2)сернистые соединения, которые при переработке высокосернистых нефтей выделяют коррозионно-активные сероводород и меркаптаны;
3)нефтяные кислоты (нафтеновые кислоты), которые содержатся в нефти от 1,5 до
1,8 %;
4)хлорорганические соединения, которые содержатся в нефти и разрушаются при нагреве в печах установок первичной перегонки с выделением хлористого водорода.
Одновременное присутствие нескольких агрессивных компонентов приводит к ускорению коррозионных процессов. Например, при совместном присутствии хлористого водорода и сероводорода скорость коррозии возрастает в 3–4 раза и может достигать
15–50 мм в год.
Наиболее интенсивно коррозия протекает в конденсаторах-холодильниках, в верхних частях ректификационных колонн, в печных трубах и трубопроводах горячих нефтяных остатков.
Для борьбы с коррозией применяют:
1)глубокое обезвоживание и обессоливание нефти;
2)коррозионно-стойкие материалы;
41
3) нейтрализующие вещества и ингибиторы коррозии.
Для снижения стоимости аппаратуры ее изготавливают часто из двухслойного материала (с плакирующим внутренним слоем). Наибольший эффект достигается при использовании нейтрализующих добавок (содощелочной раствор, аммиачный раствор и др.). Они снижают скорость коррозии углеродистой стали до 0,1–0,2 мм в год. Еще более эффективны ингибиторы коррозии. Это специальные ПАВы, которые образуют на поверхности металла защитную пленку.
42
2. ВТОРИЧНАЯ (ДЕСТРУКТИВНАЯ) ПЕРЕРАБОТКА НЕФТИ
Применение методов вторичной переработки позволяет получать из нефти новые вещества, которые не входят в ее состав. Наиболее старыми из них являются термические, в том числе термический крекинг, пиролиз, коксование. Более современными являются процессы с использованием катализаторов (каталитический крекинг, риформинг и др.).
Механизм термических методов переработки очень сложен. Наряду с термическим распадом молекул осуществляются реакции синтеза, изомеризации и др. С повышением температуры термодинамическая устойчивость углеводородов (за исключением ацетилена) снижается. В гомологическом ряду она падает с ростом молекулярной массы. При высокой температуре арены (ароматические углеводороды) значительно более устойчивы, чем алканы и циклоалканы.
Согласно радикально-цепному механизму, термические процессы состоят из следующих стадий: инициирование цепи, продолжение цепи и обрыв цепи. При этом для нефтяного сырья в условиях термических процессов характерны следующие основные реакции: деалкилирование, полимеризация, циклизация алкенов, дециклизация циклоалканов, деструктивная конденсация алкенов, конденсация аренов, реакции глубокого уплотнения до кокса. Например:
С4Н10 → СН4 + С3Н6,
С4Н10 → С2Н6 + С2Н4, С4Н10 → С4Н8 + Н2.
Термический крекинг осуществляется при 470–540 °С и давлении 2–7 МПа. С увеличением температуры скорость крекинга сильно возрастает, увеличивается выход легких компонентов (газа) и снижаются выходы тяжелых фракций и кокса.
Увеличение давления повышает температуру кипения сырья и продуктов крекинга. За счет этого можно менять фазовое состояние в зоне крекинга и проводить его в паровой, жидкой и смешанной фазах.
В паровой фазе обычно проводится крекинг бензина, керосиногазойлевых фракций. На эти процессы давление оказывает значительное влияние. Влияние давления на жидкофазный крекинг тяжелых видов сырья (мазута, гудрона) невелико.
Основным продуктом термического крекинга является углеводородный газ – сырье для нефтехимического синтеза, крекинг-бензин, керосиногазойлевая фракция, термогазойль и крекинг-остаток. Для термического крекинга используют различные виды исходного сырья: от легкого бензина до гудрона.
Крекинг-остаток (выше 350 °С) используется в качестве котельного топлива. Качество его выше, чем качество прямогонного мазута, так как он имеет большую теплотворную способность, меньшую вязкость и более низкую температуру застывания.
С целью получения максимального выхода крекинг-остатка некоторые установки реконструированы и работают в режиме легкого крекинга или так называемого висбрекинга.
Общим для различных схем термического крекинга является наличие трубчатой печи. В ней проводится нагревание, частичное испарение сырья и его химическое превращение. Крекинг протекает непосредственно в трубах печи. На современных установках используется рециркуляция сырья.
43
В настоящее время более 90 % нефти перерабатывается с использованием термокаталитических процессов, таких как каталитический крекинг, риформинг, гидрогенолиз сернистых соединений и др. Использование катализаторов позволило резко увеличить выход из нефти ценных продуктов (бензина) и повысить их качество. Термокаталитические процессы менее энергоемки и протекают при меньших температурах и давлениях, чем термические.
Пиролиз – это наиболее жесткий процесс термической обработки нефти. Процесс проводится при температуре 700–1000 °С и давлении, близком к атмосферному. Он служит для получения низших алкенов – ценного сырья для нефтехимического синтеза (этилен, пропилен и др.).
В качестве сырья для пиролиза чаще всего используются алканы. В процессе пиролиза протекают следующие превращения: этан практически полностью превращается в этилен; из пропана и бутана образуются этилен и пропилен; из углеводородов С4 и выше получают смесь этилена, пропилена и алкенов С4 и выше.
Глубину пиролиза определяют температура, время контакта и давление. Повышение температуры благоприятно сказывается на пиролизе. Снижение давления также благоприятно, поэтому процесс проводят при 0,03–0,12 МПа. Часто используется разбавление сырья водяным паром. При этом заметно возрастает выход этилена и снижается коксообразование на стенках труб печи.
Коксование – это процесс глубокого разложения нефтяных фракций без доступа воздуха с целью получения нефтяного кокса и дистиллята широкого фракционного состава. Этот метод позволяет перерабатывать менее ценные нефтепродукты – мазуты, полугудроны, гудроны, асфальты и т.п. – в более ценные светлые нефтепродукты (газ, бензин, дизельное топливо и котельное топливо) и беззольный нефтяной кокс. Он применяется в качестве восстановителя в химической промышленности, для изготовления анодов в металлургии, абразивов и огнеупоров (SiC, B4С, TiC) и др. Чаще всего процесс коксования осуществляют в полунепрерывных условиях (периодическая выгрузка кокса и непрерывная подача сырья и выделение светлых дистиллятов) при температуре
505–515 °С и давлении 0,2–0,3 МПа.
Образование кокса в жидкофазных процессах проходит по схеме: арены → смолы → асфальтены → кокс → графит.
2.1. Термокаталитические процессы
Рассмотрим подробнее два термокаталитических процесса – каталитический крекинг и риформинг.
2.1.1. Каталитический крекинг
Каталитический крекинг – это процесс получения дополнительных количеств светлых нефтепродуктов (высокооктанового бензина и дизельного топлива) разложением тяжелых нефтяных фракций в присутствии катализатора.
В качестве сырья чаще всего используются вакуумные газойли, получаемые при первичной переработке нефти, а также газойли коксования, термического крекинга
игидрокрекинга.
Спомощью каталитического крекинга получают следующие продукты:
– углеводородный газ (содержит 80–90 % предельных и непредельных углеводородов С1–С4), который направляется для разделения на ГФУ;
44
–бензиновую фракцию (конец кипения 195 °С), которая используется как компонент автомобильного и авиационного бензинов;
–легкий газойль (интервал кипения 195–280 °С), применяемый как компонент дизельного и газотурбинного топлива;
–фракцию с интервалом кипения 280–420 °С, используемую в качестве сырья для получения технического углерода;
–тяжелый газойль (начало кипения 420 °С), который используется как компонент котельного топлива.
В настоящее время преимущественно применяются синтетические алюмосиликатные катализаторы, содержащие в своем составе 5–20 % цеолитов. При этом выход бензина достигает 45–50 %. Катализаторы должны быть устойчивыми к истиранию, к действию водяного пара, высоких температур и т.д.
Особенностью катализаторов является их быстрая дезактивация за счет закоксовывания пор – всего за 10–15 минут работы. Поэтому крекинг чередуют с непрерывной регенерацией катализатора, которая заключается в выжигании кокса и смолистых отложений с поверхности катализатора воздухом при 540–580 °С. Для предотвращения местных перегревов воздух разбавляют инертными газами.
Наряду с крекингом углеводороды в условиях процесса вступают в реакции алкилирования, деалкилирования, изомеризации, полимеризации и гидрирования. Механизм каталитического крекинга, который экспериментально доказан, можно представить в виде цепных реакций. Зарождение цепи происходит под действием иона водорода катализатора:
НА → Н+ + А–,
где НА – условное изображение алюмосиликатного катализатора в виде кислоты. При взаимодействии Н+ с алкенами образуются ионы карбония:
RСН=СН2 + Н+ → RС+Н–СН3.
Образующиеся ионы карбония могут участвовать в различных процессах, основными из которых являются:
а) скелетная изомеризация:
|
|
|
CH3 |
|
+ |
|
+ |
| |
|
– CH3 |
→ R– C – CH3; |
|||
R–CH – CH2 |
→ R–CH–CH2 |
|||
|
|
| |
+ |
|
|
|
|
CH3
б) взаимодействие с нейтральными молекулами с образованием новых ионов кар-
бония:
+
R–CH–CH3 + C4H10 → C4H9+ + R–CH = CH2;
в) распад иона карбония с большим числом углеродных атомов:
+
СН3–СН–СН2–R → CH3 – СН = СН2 + R+;
г) обрыв цепи в результате реакции между ионами карбония и анионом катализатора:
+
R – CH – CН3 + A– → R – CH = CH3 + HA.
45
В итоге катализатор восстанавливает свой состав, и процесс может начинаться сначала. Последовательность реакции при каталитическом крекинге иная, чем при термическом: алкены → арены с большим числом боковых цепей → циклоалканы → → алканы.
Такая последовательность объясняется тем, что в первую очередь на катализаторе адсорбируются ненасыщенные водородом соединения. Ускорение реакций крекинга для алкенов и аренов в сотни и тысячи раз превышает ускорение крекинга алканов.
Одной из особенностей каталитического крекинга является также развитие процессов перераспределения водорода. Так, молекулы углеводородов, адсорбированные на катализаторе, склонны к дегидрированию, что приводит к увеличению их ненасыщенности и, как следствие, к усилению их связи с катализатором. В результате вновь получаемые на поверхности катализатора алкены начинают полимеризоваться с превращением в конечный продукт процесса – кокс. Постепенно все активные центры катализатора покрываются коксом, что вызывает необходимость регенерации катализатора.
Основными преимуществами каталитического крекинга перед термическим являются более высокая скорость реакций и большая ценность получаемых продуктов.
На российских НПЗ эксплуатируются установки каталитического крекинга с реактором и регенератором непрерывного действия двух типов:
–с плотным слоем циркулирующего шарикового катализатора;
–с псевдоожиженным слоем циркулирующего микросферического катализатора. Ниже приводятся показатели технологического режима установок каталитического
крекинга с микросферическим цеолитсодержащим (I) и шариковым аморфным (II) катализаторами:
Температура, ○С: |
I |
II |
|
|
|
в реакторе |
490–505 |
470–485 |
в регенераторе |
590–670 |
590–650 |
низа колонны ректификации |
280 |
250 |
Давление, кгс/см2: |
|
|
в реакторе |
0,6–2,4 |
0,7–0,8 |
в регенераторе |
2,4 |
2,0 |
Кратность циркуляции катализатора |
6–8 |
1,8–2,5 |
Содержание остаточного кокса в катализаторе |
|
|
на выходе из генератора, % |
0,15 |
0,6–0,8 |
Установки с шариковым катализатором по основным характеристикам уступают установкам с микросферическим катализатором. Это объясняется меньшей удельной поверхностью шарикового катализатора по сравнению с микросферическим.
Каталитический крекинг с циркулирующим шариковым катализатором
Принципиальная технологическая схема
Установка, схема которой приведена на рис. 42, работает следующим образом. Сырье (вакуумный газойль – продукт вакуумной перегонки мазута по топливной схеме) насосом 14 через теплообменники 15, 16 подают в трубчатую печь 17. Здесь сырье нагревается, испаряется и с температурой 520–550 °С направляется в реактор 7, где контактирует в режиме прямотока с медленно движущимся сверху вниз слоем катализато-
46
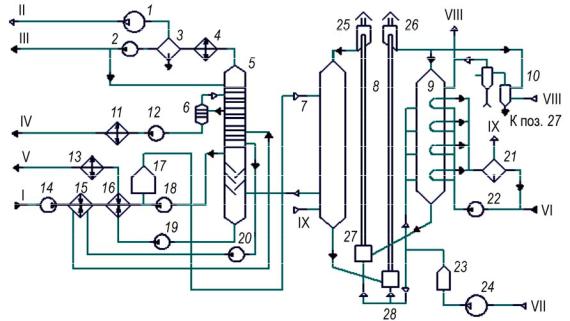
ра. В нижнюю часть реактора подают острый водяной пар для удаления из катализатора остатков нефтепродуктов.
Продукты крекинга в парообразном состоянии выводятся из реактора и поступают в нижнюю часть ректификационной колонны 5. Эти пары загрязнены взвешенными частицами кокса и катализаторной пыли. Поэтому в нижней части колонны 5 установлены специальные каскадные тарелки, имеющие угол наклона в сторону движения жидкой фазы. Из верхней части колонны 5 выводятся пары бензина, водяные пары и жирный газ, которые поступают в холодильник 4 и сепаратор 3. Часть бензина после конденсации и отделения от жирных газов и воды в сепараторе 3 возвращается в виде флегмы (рефлюкса) обратно в колонну.
Рис. 42. Принципиальная технологическая схема установки каталитического крекинга с плотным слоем циркулирующего шарикового катализатора: 1 – компрессор; 2, 12, 14, 18–20, 22 – насосы; 3, 10 – сепараторы; 4, 11, 13 – холодильники; 5, 6 – колонны; 7 – реактор; 8 – пневмоподъемники; 9 – регенератор; 15, 16 – теплообменники; 17, 23 – печи; 21 – паросборник; 24 – воздуходувка; 25, 26 – бункеры-сепараторы; 27, 28 – дозаторы пневмоподъемников. Потоки: I – сырье; II – углеводородный газ; III – бензин; IV – фракция 195–350 °С; V – фракция выше
350 °С; VI – вода; VII – воздух; VIII – дымовые газы; IX – пар водяной
Шариковый катализатор из бункера 25 самотеком непрерывно поступает в верхнюю часть реактора, равномерно распределяется по его сечению и плотным слоем последовательно проходит реакционную зону, зону сепарации и зону отпарки. После этого закоксованный катализатор пневмотранспортом при помощи горячих топочных газов поднимается вверх и поступает в регенератор 9. Здесь катализатор движется плотным слоем сверху вниз, а сбоку подается горячий воздух, разбавленный топочными газами, для выжигания кокса. Для исключения перегрева и спекания катализатора внутри регенератора имеются водоохлаждаемые змеевики. Регенерированный катализатор при помощи пневмотранспорта возвращается в реактор. Разрушенные частицы катализатора отделяются от отработанных топочных газов в сепараторе 10 и утилизируются.
47
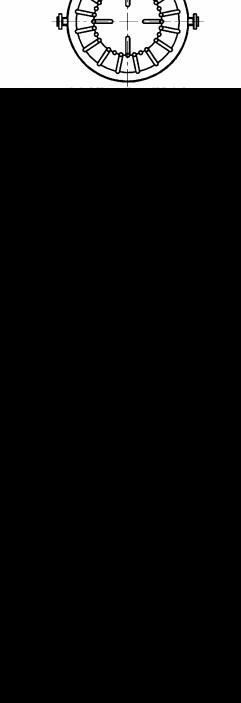
Основное технологическое оборудование
Рис. 43. Реактор каталитического крекинга с шариковым движущимся катализатором: 1 – верхнее распределительное устройство; 2 – реакционная зона; 3 – сепарационное устройство; 4 – зона отпарки; 5 – нижнее сборно-выравни- вающее устройство. Потоки: I – сырье; II – катализатор; III – продукты крекинга; IV – катализатор закоксованный;
V – пар водяной
К основному оборудованию данной установки относятся реактор каталитического крекинга и регенератор.
Реактор представляет собой вертикальный цилиндрический аппарат (рис. 43) с внутренним диаметром 3900 мм, высотой 15,4 м, толщиной стенки корпуса 16 мм. Стенка корпуса биметаллическая: наружная часть из углеродистой стали, внутренняя – из легированной стали.
Верхнее распределительное устройство 1 служит для равномерного распределения потока катализатора по сечению аппарата. Оно представляет собой цилиндрическую обечайку, внутри которой расположена контрольная сетка, из нижней части обечайки выводятся распределительные трубы, которые равномерно распределяют катализатор по сечению. Катализатор движется со скоростью 4–8 мм/с. Для регулирования высоты реакционной зоны 2 трубы выполнены телескопическими. Сырье подают по двум штуцерам в пространство над распределительным устройством.
Под реакционной зоной расположено сепарационное устройство 3, которое служит для отделения паров продуктов реакции от катализатора. Это устройство (рис. 44) представляет собой две тарелки с трубами 3 для вывода паров и катализатора. Трубы, расположенные по вершинам равносторонних треугольников, чередуются рядами: для вывода катализатора и вывода паров. Продукты крекинга уходят из реактора через трубы с колокольчиками 4. Под каждым колокольчиком находятся отверстия для вывода паров. Колокольчики служат для предотвращения попадания катализатора внутрь труб. Для выравнивания гидравлического сопротивления при проходе паров в нижних рядах под колокольчиками сделано больше отверстий, чем в верхних рядах. На нижнем конце трубы 3 для изменения направления скорости потока выходящих из нее паров приваривают отбойники 5.
Пары из реактора выводят по двум штуцерам с отбойными листами. Эти листы должны быть нижними краями погружены в слой катали-
48
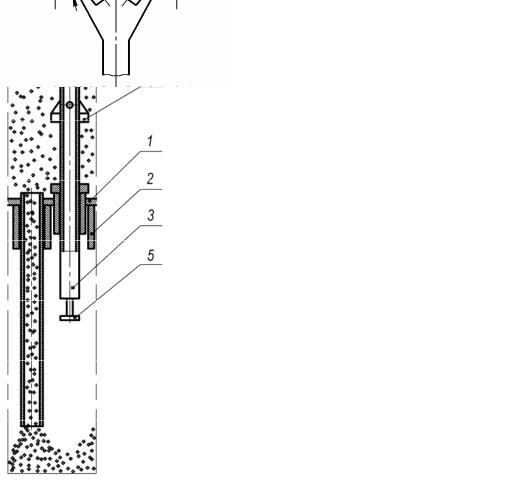
|
|
|
|
|
|
Рис. 44. Узел сепарационного устрой- |
Рис. 45. Узел сборно-выравни- |
ства: 1 – трубная решетка; 2 – ребра |
вающего устройства с прямыми |
жесткости; 3 – газоотводная труба; 4 – |
трубами |
колокольчик; 5 – отбойник |
|
затора, чтобы пары проходили сверху отбойных листов. Это уменьшает унос катализатора.
Из труб сепарационного устройства закоксованный катализатор попадает в зону отпарки 4, где продувается водяным паром для извлечения остатков нефтяных паров.
Отпаренный катализатор далее стекает в нижнее сборно-выравнивающее устройство 5 (см. рис. 43), которое обеспечивает равномерный вывод катализатора по всему сечению аппарата. Оно состоит из трех ярусов воронок, в верхнем ярусе расположено 60 воронок для сбора катализатора, во втором – 16, в третьем – 4.
Воронки соединяются при помощи прямых или гнутых труб. Устройство с прямыми трубами (рис. 45) меньше изнашивается. Однако оно обеспечивает менее равномерный выход катализатора. Более совершенными являются устройства с гнутыми трубами, обеспечивающими лучший эффект, однако они быстрее изнашиваются.
Корпус реактора может быть выполнен из легированной стали 1Х18Н9Т или биметалла 12ХМ + 08Х13. Все внутренние устройства выполнены из стали 1Х18Н9Т.
Регенератор представляет собой вертикальный аппарат квадратного сечения размером 3500×3500 мм и высотой 24,4 м (рис. 46). Квадратное сечение регенератора обеспечивает наилучшие условия для размещения в нем змеевиков и коробов для подачи воздуха и вывода дымовых газов.
49
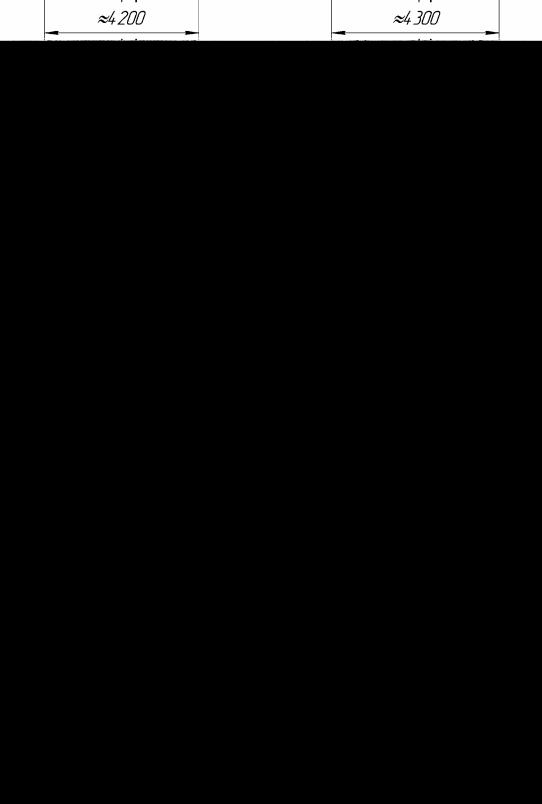
Рис. 46. Регенератор: 1 – коллекторы ввода воздуха; 2 – коллекторы вывода дымовых газов; 3 – охлаждающие змеевики; 4, 5 – короба воздухораспределительные и газосборные; 6 – решетка; 7 – сборное выравнивающее устройство; 8 – футеровка; 9 – листовой асбест; 10 – распределительное устройство. Потоки: I – катализатор; II – дымовые газы; III – воздух, IV – пароводяная смесь
50