
Основное технологическое оборудование нефтеперерабатывающих заводо
..pdf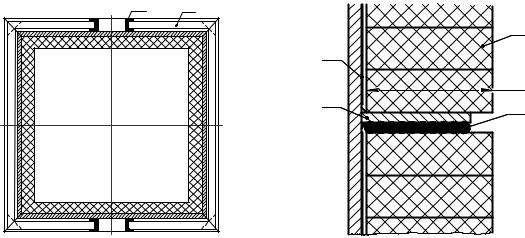
В аппарате по высоте имеется девять зон. Каждая зона включает коллекторы ввода воздуха 1, вывода дымовых газов 2, а также охлаждающие змеевики 3. К коллекторам присоединены короба воздухораспределительные 4 и газосборные 5, служащие для равномерного распределения воздуха и сбора дымовых газов.
Для катализатора на верху аппарата снаружи имеется распределительное устройство 10, выполненное из труб. Внизу установлено сборное выравнивающее устройство 7, по конструкции аналогичное выравнивающему устройству реактора. Над выравнивающим устройством установлена решетка 6, которая способствует задерживанию и раздроблению комков, образующихся при спекании катализатора.
Температура внутри аппарата достигает 700 °С, поэтому все внутренние устройства регенератора изготовлены из стали 12Х18Н10Т. Корпус аппарата (рис. 47) изготовлен из листов углеродистой стали толщиной 12–14 мм и укреплен ребрами жесткости – горизонтальными 1 и вертикальными 2 балками из швеллеров.
Корпус (рис. 48) футерован изнутри огнеупорным кирпичом 5 толщиной 250 мм и изолирован листовым асбестом 2. Футеровка установлена на специальных полках 3, приваренных к корпусу. Для обеспечения независимых деформаций корпуса и кладки под полкой оставлен температурный зазор, который заполнен асбестовым шнуром 4.
2 |
1 |
Рис. 47. Поперечное сечение реге- |
|
нератора: 1 – горизонтальная балка; |
|
2 – вертикальная балка |
|
1 5
2
|
250 |
3 |
4 |
|
Рис. 48. Кладка регенератора: 1 – корпус; 2 – асбестовая прокладка; 3 – полка; 4 – шнур асбестовый; 5 – кирпич огнеупорный
Система распределения воздуха и сбора дымовых газов выполнена разборной. Она состоит из центрального коллектора 1 и отходящих с каждой стороны четырнадцати коробов 4 и 5 (см. рис. 46).
Охлаждающие змеевики выполнены из бесшовных труб диаметром 60×5 мм, которые соединены между собой крутоизогнутыми фитингами с шагом 150 мм. Это обеспечивает свободный проход катализатора и эластичность змеевика. Каждый змеевик состоит из трех рядов труб. Внутри змеевика циркулирует пароводяная смесь с температурой около 230 ºС под давлением 3 МПа. Подключение отдельных змеевиков к общему коллектору параллельное, что позволяет отключить змеевик в случае его повреждения, не останавливая работу аппарата.
51
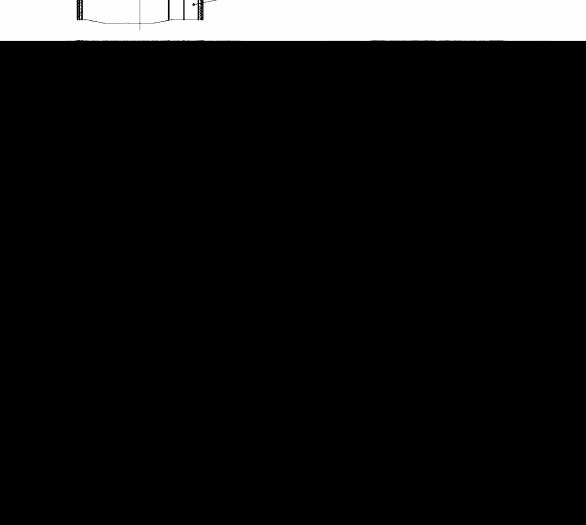
В последнее время используются более совершенные установки с однократным подъемом катализатора с использованием совмещенных реакторов-регенераторов различных конструкций. Один из них представлен на рис. 49.
Рис. 49. Реактор-регенератор совмещенного типа: 1 – реактор; 2 – зона реакции; 3 – сепарационная зона; 4 – зона отпарки; 5 – регенератор; 6, 7 и 8 – соответственно верхняя, средняя и нижняя зоны выжигания кокса; 9 – охлаждающие змеевики; 10 – сборно-выравнивающее устройство. Потоки: I – сырье; II, VI – катализатор; III – продукты реакций; IV – дымовые газы; V – воздух
Совмещенный реактор-регенератор такого типа имеет внутренний диаметр в верхней реакционной части 4500 мм, в нижней части 5500 мм. Общая высота аппарата 37 м. На верху аппарата размещена шлюзовая камера, куда подается катализатор и вводится водяной пар для создания гидрозатвора. Катализатор распределяется по сечению аппарата по трубам на периферии и по кольцевому каналу в центре так, чтобы изолировать катализатором внутренние поверхности корпуса от сырья. В этом случае предотвращается коксоотложение в верхней части аппарата при переработке тяжелого сырья. Для равномерного распределения парожидкостной смеси ее вводят через центробежный завихритель.
Сепарационное устройство (рис. 50) по высоте состоит из трех рядов горизонтальных коробов 1.
52
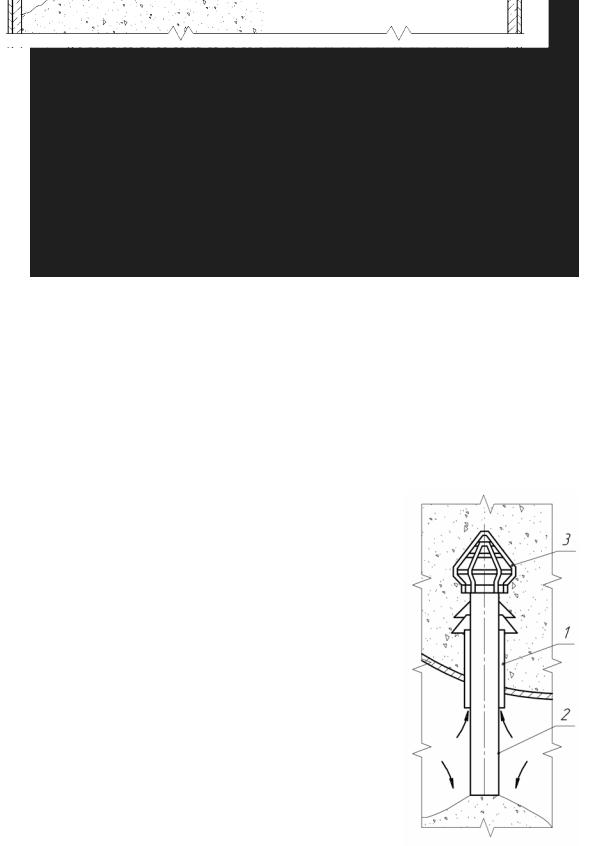
Рис. 50. Сепарационное устройство: 1 – короба; 2 – трубы переточные
Короба верхних рядов связаны вертикальными трубами 2 с коробами нижнего ряда. В трубах под коробами имеются отверстия для паров.
Пары собираются в нижних коробах и поступают в кольцевое пространство, откуда выводятся по четырем штуцерам.
Катализатор проходит между коробами и из сепарационной зоны по системе переточных труб 2 поступает в зону отпарки – в пространство между днищами. Туда подается водяной пар. Водяной пар поднимается по переточным трубам и опускается по за-
творным трубам, осуществляя отпарку и обеспечи- |
|
вая создание гидрозатвора между реактором и ре- |
|
генератором. |
|
Регенератор состоит из трех зон выжига: верх- |
|
ней и нижней противоточной и средней прямо- |
|
точной. Для ввода воздуха применяют распре- |
|
делительную систему, состоящую из днища с пат- |
|
рубками, каждый из которых выполнен в виде |
|
коаксиально расположенных труб (рис. 51). |
|
Часть воздуха, подаваемого под днище, подни- |
|
мается по кольцевому пространству патрубков про- |
|
тивотоком катализатору, а другая часть опускается |
|
прямотоком с катализатором. В нижнюю противо- |
|
точную зону регенерации воздух вводится через |
|
нижнее днище аппарата и систему патрубков с ко- |
|
ническими колпачками, которые укреплены в дни- |
|
ще сборно-выравнивающего устройства для катали- |
|
затора. |
|
Сборно-выравнивающее устройство (рис. 52) |
|
состоит из системы вертикальных и наклонных труб, |
Рис. 51. Воздухораспределительное |
равномерно собирающих и выводящих катализатор |
устройство: 1 – патрубок для возду- |
в систему коаксиальных конических воронок, распо- |
ха; 2 – переточная труба для катали- |
ложенных над общим выводным штуцером. |
затора; 3 – защитная сетка |
|
|
53 |
|
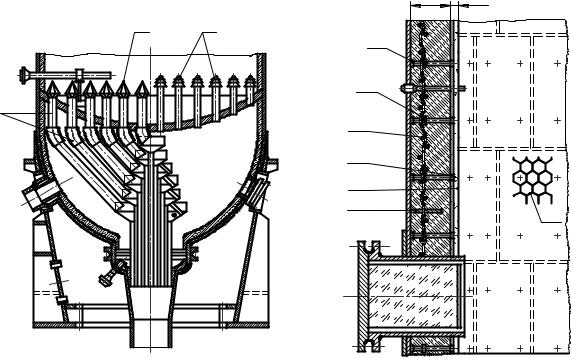
Катализаторные трубы выравнивающего устройства и переточные трубы газосборных и воздухораспределительных устройств снабжены защитными сетками, предохраняющими их от закупорки спекшимися кусками катализатора.
Для отвода избыточного тепла в средней части нижней противоточной зоны установлены два трехрядных змеевика, которые опираются на систему балок, воспринимающих силу давления катализатора. В змеевики поступает пароводяная смесь с температурой около 200 °С под давлением 1,5 МПа.
Корпус реактора-регенератора выполнен из стали 16ГС и изнутри теплоизолирован слоем торкрет-бетона. Толщина покрытия выбирается из расчета, чтобы температура стенки аппарата не превышала 150 °С, и находится в пределах от 100 до 200 мм.
Конструкция покрытия показана на рис. 53. Для удержания торкрет-бетонного покрытия с внутренней стороны корпуса приварены с шагом 250 мм шпильки 1 с поперечными планками 2, на которых на расстоянии 35 мм от стенки корпуса крепят армирующую сетку 3. Основной теплоизолирующий слой бетона наносят после установки шпилек. Затем к шпилькам приваривают шайбы 4, устанавливают панцирную сетку 5, защищающую бетон от эрозии, и наносят панцирный слой бетона, обладающий повышенной эрозионной стойкостью. Панцирная сетка, изготовляемая из стальных полос, имеет форму пчелиных сот. К стенке корпуса приварены также кольцевые перегородки 6 с некоторым шагом по высоте. Они препятствуют фильтрации паров и газов вдоль стенки аппарата в случае образования трещин в бетоне. Люки и лазы также изнутри надежно теплоизолируют.
3 1
2
Рис. 52. Сборно-выравнивающее устройство: 1 – патрубок для ввода воздуха; 2 – трубы для вывода катализатора; 3 – защитная сетка
130 |
20 |
1 |
|
2 |
|
3 |
|
4 |
|
5 |
|
6 |
5 |
|
Рис. 53. Конструкция торкрет-бетонного покрытия: 1 – шпилька; 2 – планка поперечная; 3 – сетка армирующая; 4 – шайба; 5 – сетка панцирная; 6 – перегородки кольцевые
54
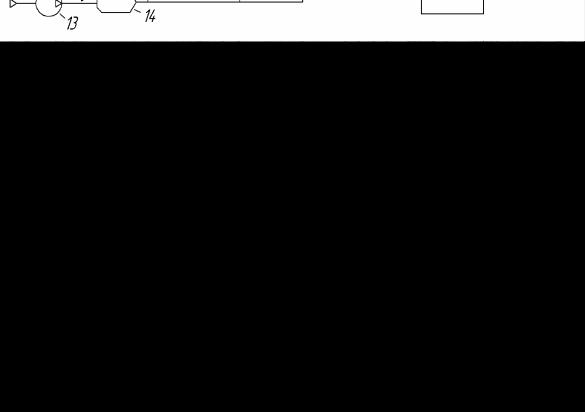
Каталитический крекинг с микросферическим катализатором
Принципиальная технологическая схема
Каталитический крекинг в установке с псевдоожиженным слоем микросферического катализатора (рис. 54) осуществляется следующим образом.
Сырье насосом 18 через теплообменники 19, 22 и 26 подается в печь 27. Нагретое сырье сначала смешивается с циркулирующим газойлем, поступающим с низа ректификационной колонны 7, затем смешивается с водяным паром, поступает в подъемный стояк катализаторопровода, подхватывая частички регенерированного катализатора,
идалее в реактор 6. Процесс каталитического крекирования начинается еще в стояке
изаканчивается в псевдоожиженном слое реактора.
Рис. 54. Принципиальная технологическая схема каталитического крекинга с микросферическим катализатором: 1 – сепаратор; 2, 11, 15, 17, 18, 23 – насосы; 3 – котел-утилизатор; 4 – электрофильтр; 5 – регенератор; 6 – реактор; 7, 16, 21 – колонны; 8, 20, 25 – холодильники; 9 – сепаратор; 10 – компрессор; 12 – бункер катализатора; 13 – воздуходувка; 14 – топка; 19, 22, 24, 26 – теплообменники; 27 – печь. Потоки: I – сырье; II – катализатор; III – бензин; IV – жирный газ; V – фракция 195–350 °С; VI – фракция выше 350 °С; VII – вода; VIII – воздух; IX – пар водяной; X – дымовые газы; XI – топливный газ; XII – циркулирующее орошение колонны 7
Пары продуктов реакции и водяной пар, подаваемый в отпарную зону реактора, уходят через верхний штуцер реактора и поступают в нижнюю часть ректификационной колонны 7. С верха этой колонны газ, пары бензина и водяные пары поступают в конденсатор-холодильник 8, а оттуда после конденсации – в сепаратор 9. Здесь смесь разделяется на водный слой, бензиновый слой и газ. Газ компрессором 10 подается на газофракционирование, часть бензина насосом 11 направляется на орошение верха ко-
55
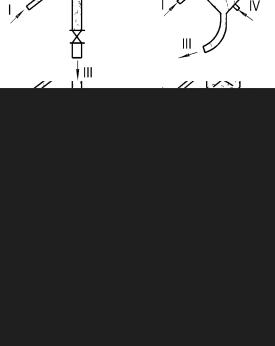
лонны 7, а остальная часть выводится с установки для дополнительной стабилизации (освобождения от остатков растворенных углеводородных газов).
Боковые погоны колонны 7 (фракция 195–350 °С и выше 350 °С) поступают
всоответствующие отпарные секции 16 и 17, где отпариваются водяным паром. Фракция с интервалом кипения 195–350 °С забирается насосом 17, охлаждается последовательно в теплообменнике 19, холодильнике 20 и выводится с установки. Фракция с температурой кипения выше 350 °С забирается насосом 23, охлаждается в теплообменнике 24 и холодильнике 25 и также выводится с установки. С низа колонны 7 насосом 15 в реактор откачивается шлам – смесь тяжелого газойля со взвешенной катализаторной пылью.
Катализатор из псевдоожиженного слоя реактора медленно опускается в отпарную зону, куда подается водяной пар. Нефтяные пары, адсорбированные поверхностью катализатора, удаляются с помощью водяного пара. Далее катализатор поступает в катализаторопровод и опускается в узел смешения с воздухом. Воздушный поток поднимает катализатор в регенератор 5 по восходящей линии катализаторопровода. Основная часть воздуха для выжига кокса подается непосредственно в регенератор. В змеевики регенератора подводится водяной пар или вода для отвода избыточной теплоты. Дымовые газы, образовавшиеся при выжиге кокса с поверхности катализатора, поступают
вкотел-утилизатор 3, отдают свое тепло, направляются в электрофильтр 4 для улавливания катализаторной пыли и затем выбрасываются в атмосферу. Для подогрева воздуха и разбавления его топочными газами применяется топка 14, работающая под давлением.
Основное технологическое оборудование
Основное оборудование данной установки также составляют реактор и регенератор.
Реакторы для этой установки имеют несколько конструкций. Схемы выполнения некоторых конструкций приведены на рис. 55, а конструкция одного из них – на рис. 56.
Рис. 55. Схемы реакторов с микросферическим катализатором: 1 – зона размещения циклонов; 2 – сепарационная зона; 3 – реакционная зона; 4 – зона ввода и распределения сырья и катализатора; 5 – отпарная зона. Потоки: I – смесь сырья и катализатора; II – продукты крекинга; III – закоксованный катализатор;
IV – водяной пар
56
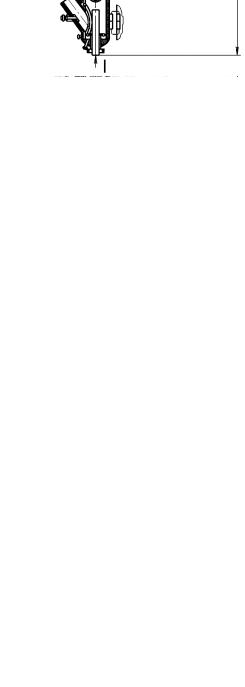
Реакторы представляют собой цилинд- |
|
|
|
||
|
|
|
|||
рические аппараты с полушаровым и ко- |
|
|
|
||
ническим днищами. Диаметр реактора в за- |
|
|
|
||
висимости от производительности составля- |
|
|
|
||
ет 2,5–12 м, высота цилиндрической части |
|
|
|
||
10–16 м. |
|
|
|
|
|
При температуре стенки до 475 °С кор- |
|
|
|
||
пус изготавливают из углеродистой стали, |
|
|
|
||
|
|
|
|||
при коррозионно-активном сырье использу- |
|
|
|
||
ют биметаллические стенки. Часто внутрен- |
|
|
|
||
нюю поверхность защищают теплоизоляци- |
|
|
|
||
онной футеровкой. |
|
|
|
|
|
|
|
|
|
||
Реактор работает следующим образом. |
|
|
|
||
Поток сырья и катализатора поступает в ре- |
|
|
|
||
актор под распределительное устройство 4. |
|
|
|
||
Оно представляет собой решетку толщиной |
|
|
|
||
|
|
|
|||
20–40 мм с отверстиями диаметром 35–50 мм |
|
|
|
||
и долей свободного сечения 2–5 %. Обычно |
|
|
|
||
реакционная зона является пустотелой, ино- |
|
|
|
||
гда в ней размещают решетки из труб, |
|
|
|
||
уменьшающих вероятность проскока непро- |
|
|
|
||
реагировавшего сырья из реактора. |
|
|
|
||
В сепарационной зоне, высота которой |
|
|
|
||
составляет не менее 4,5 м, оседает катализа- |
|
|
|
||
торная мелочь, вынесенная из псевдоожи- |
|
|
|
||
женного слоя. В верхней части размещены |
|
|
|
||
одноступенчатые или двухступенчатые ци- |
|
|
|
||
|
|
|
|||
клоны. Уловленные частицы катализатора по |
|
|
|
||
специальным трубопроводам (стоякам) воз- |
|
|
|
||
вращаются обратно в |
псевдоожиженный |
|
|
|
|
слой. На нижних концах этих стояков име- |
|
|
|
||
|
|
|
|||
ются клапаны, которые предотвращают про- |
|
|
|
||
ход паров по стояку в циклон. Изнутри ци- |
|
|
|
||
клоны обычно защищают от эрозионного из- |
|
|
|
||
носа слоем износостойкого бетона. |
Рис. 56. Конструкция реактора с пылевид- |
||||
Отпарная зона, куда подают водяной пар, |
|||||
ным катализатором: 1 – корпус; 2 – цикло- |
|||||
расположена в нижней части реактора, имею- |
ны; 3 – стояки циклонов; 4 – распредели- |
||||
щей меньшее поперечное сечение. Для по- |
тельная решётка; 5 – форсунки для шлама; |
||||
вышения эффективности отпарки в этой зоне |
6 – десорбер; 7 – ствол; 8 – штуцер для пре- |
||||
могут быть размещены каскадные тарелки. |
дохранительного клапана. Потоки: I – сы- |
||||
рье; II – катализатор; III – продукты крекин- |
|||||
Реактор установки средней производи- |
|||||
га; IV – закоксованный катализатор; V – во- |
|||||
тельности (см. рис. 56) имеет внутренний |
|
дяной пар |
|||
диаметр верхней части |
8000 мм, средней |
|
|
|
4500 мм и нижней (ствола) 1600 мм. Общая высота аппарата 55 м. Корпус изготовлен из стали 16ГС, внутренние устройства – из стали 08Х13. Изнутри реактор футерован слоем жаростойкого торкрет-бетона толщиной 150 мм.
57
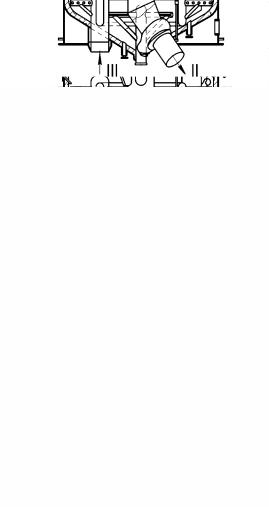
Катализатор поступает из регенератора в нижний узел ствола, где предварительно смешивается с водяным паром и затем с сырьем. Далее эта смесь поднимается по стволу и, пройдя конус с газораспределительной решеткой 4, поступает в зону форсированного псевдоожиженного слоя. От эрозии ствол и конус защищены слоем жаростойкого торкрет-бетона, нанесенного на панцирную сетку.
В верхней части реактора установлены четыре блока двухступенчатых циклонов 2 диаметром 1400 мм. Изнутри они футерованы слоем эрозионно-стойкого бетона на фосфатной связке с корундовым наполнителем толщиной 20 мм, нанесенным на панцирную сетку. Уловленный катализатор возвращается обратно в реактор через вертикальные стояки с обратными клапанами 3.
Рис. 57. Регенератор микросферического катализатора: 1 – корпус; 2 – цилиндрическая перегородка; 3 – радиальная перегородка; 4 – топливная форсунка; 5 – форсунка для конденсата; 6 – циклоны; 7 – переточное окно. Потоки: I – катализатор из реактора;
II– регенерированный катализатор; III – воздух; IV – водяной пар; V – дымовые газы
Катализатор из псевдоожиженного слоя опускается в десорбер, где отпаривается в противотоке с потоком водяного пара. Десорбер секционирован семью каскадными перфорированными конусами, препятствующими созданию поршневого режима. В нижней части десорбера установлены кольцевые коллекторы для ввода водяного пара, в верхней части – форсунки для ввода шлама, т.е. части остатка из ректификационной колонны, содержащего унесенный из реактора катализатор.
Регенератор представляет собой цилиндрический аппарат с коническим и полушаровым днищами (рис. 57).
Диаметр регенератора больше диаметра реакторов и колеблется от 6 до 17 м. В отдельных случаях для отвода избыточного тепла внутри регенераторов устанавливают змеевики пароводяного охлаждения, однако чаще все тепло используется для нагрева катализатора. Внутренний диаметр верхней части регенератора той же установки 11 000 мм, нижней части (зона выжигания) 9000 мм. Общая высота аппарата 27,2 м.
Корпус выполнен из стали 16ГС и изнутри теплоизолирован слоем жаростойкого торкрет-бетона толщиной 200 мм с панцирной сеткой. Внутренние устройства изготовлены из сталей 12Х18Н10Т и 08Х13.
В нижней части, где происходит выжигание кокса с катализатора в псевдоожиженном слое, регенератор секционирован цилиндрической перегородкой на две зоны: внешнюю кольцевую и центральную.
58
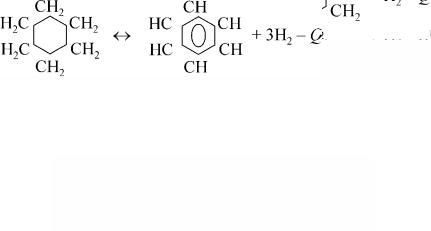
Катализатор движется по кольцу и перетекает через два переточных окна в верхней части цилиндрической перегородки в центральную зону, откуда по наклонному трубопроводу направляется в реактор. Для выжигания кокса и поддержания псевдоожиженного слоя во внешнюю и центральную зоны снизу подается воздух по двум независимым коллекторам. Отработанные дымовые газы из псевдоожиженного слоя поступают в зону сепарации, которую для улучшения улавливания катализатора выполняют с большей площадью сечения.
В зоне сепарации сверху установлены шесть групп двухступенчатых циклонов диаметром 1600 и 1400 мм. Внутренние поверхности защищены слоем эрозионностойкого бетона на панцирной сетке.
Для предотвращения догорания оксида углерода до диоксида предусмотрен ввод конденсата через восемь форсунок в зону сепарации и водяного пара под днище сборной камеры и в циклоны первой ступени. Для разогрева катализатора при пуске установлены шесть топливных форсунок по окружности внешней зоны псевдоожиженного слоя.
2.1.2. Каталитический риформинг
Риформинг применяется для повышения октанового числа бензиновых фракций, а также для получения ароматических углеводородов (бензол, толуол и ксилолы), являющихся ценным сырьем для нефтехимического синтеза, а также использующихся в качестве растворителей.
При риформинге молекулы углеводородов перестраиваются (реформируются) с выделением водорода, но без изменения числа углеродных атомов в молекуле. При этом протекают следующие основные реакции:
а) реакция дегидроциклизации алканов – реакция Казанского (обратимая при температуре и катализаторе)
б) реакция дегидрирования циклоалканов (нафтенов) – реакция Зелинского (обратимая при температуре и катализаторе)
Реакция дегидрирования циклоалканов может развиваться дальше вплоть до образования углерода (кокса). Эти реакции обратимые эндотермические, и для смещения равновесия вправо необходимо подводить тепло и снижать давление. Для удержания равновесия в заданном состоянии с целью исключения коксообразования температуру понижают до температуры зажигания катализатора, а давление увеличивают. С этой целью большую часть образующегося водорода возвращают в реакционную зону в виде рецикла и процесс проводят под давлением около 4,5 МПа.
59
Балансовый излишек водорода используют в других процессах (в гидроочистке от сернистых и азотистых примесей). Помимо названных реакций могут протекать и побочные (крекинг с образованием углеводородных газов), поэтому при риформинге образуется не чистый водород, а водородсодержащий газ (ВСГ), в состав которого входят метан, этан и пропан в количествах до 5 %.
При риформинге применяются следующие катализаторы:
– платиновые, нанесенные на оксид алюминия и промотированные фтором
ихлором;
–полиметаллические, которые содержат помимо платины рений, иридий, кадмий, свинец, палладий и германий, нанесенные на те же носители.
Содержание платины на катализаторе не превышает 0,3–0,5 %, срок службы такого катализатора до 1 года. Сернистые и азотистые соединения, а также влага являются нежелательными примесями, поэтому исходное сырье подвергают предварительной гидроочистке от сернистых примесей в присутствии Al-Co-Mo-катализатора и осушке:
RHS + H2 = RH + H2S.
Образующийся сероводород извлекают при помощи специальных поглотителей (моноэтаноламин, диэтаноламин и др.). В настоящее время разрабатывают новые катализаторы, которые более устойчивы к ядам.
Платиновый катализатор постепенно покрывается коксом и сернистыми соединениями и со временем теряет свою активность. Регенерацию производят выжиганием кокса и сернистых отложений смесью инертного газа и воздуха под давлением 1 МПа. Выжигание проводят в тех же реакторах в три ступени при температуре 300–350 °С на первой ступени, 380–420 °С на второй и 450–500 °С на третьей.
Основными продуктами риформинга являются ВСГ и жидкая фракция (риформат или катализат). Риформат используют как высокооктановую добавку к моторным топливам. Путем его разделения на отдельные компоненты получают индивидуальные арены (бензол, толуол, ксилолы и др.). Процесс проводят при температуре 470–540 ºС и давлении 2–4 МПа. Процессы идут в трех последовательных реакторах. Так как реакции риформинга являются эндотермическими, перед каждым реактором сырье подогревают в трубчатой печи.
Принципиальная технологическая схема
Установка каталитического риформинга состоит из трех блоков (рис. 58): гидроочистки сырья, платформинга гидроочищенного сырья и стабилизации продуктов. Кроме того, если на установке получают индивидуальные углеводороды, то она включает и блок выделения.
Исходное сырье (низкооктановые бензиновые фракции) подается насосом 21 на смешивание с циркулирующим ВСГ гидроочистки и избыточным ВСГ риформинга. Полученная газосырьевая смесь после нагрева в теплообменнике 10 и печи 12 поступает в реактор гидроочистки 11, заполненный алюмокобальтмолибденовым катализатором. Далее смесь отдает свое тепло в кипятильнике 22, теплообменнике 10, холодильнике 8 и направляется в сепаратор высокого давления гидроочистки 9, где гидрогенизат отделяется от отработанного ВСГ. Его отмывают от сероводорода в колонне 2 водным раствором моноэтаноламина (МЭА) с концентрацией 15 %. После этого большая часть
60