
Основное технологическое оборудование нефтеперерабатывающих заводо
..pdf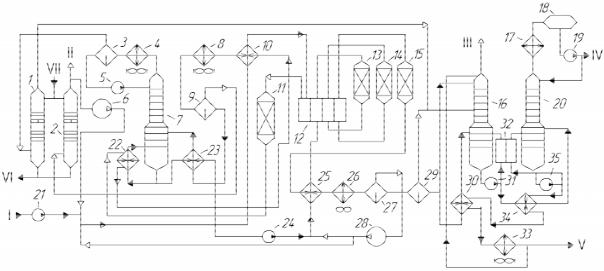
Рис. 58. Принципиальная технологическая схема установки каталитического риформинга: 1, 2, 7, 16, 20 – колонны; 3, 9, 27, 29 – сепараторы; 4, 8, 17, 26, 33 – холодильники; 5, 19, 21, 24, 31, 35 – насосы; 6, 28 – компрессоры; 10, 23, 25, 30, 34 – теплообменники; 11, 13–15 – реакторы; 12, 32 – печи; 18 – емкости; 22 – кипятильник. Потоки: I – сырье; II – избыточный водородсодержащий газ; III – сухой углеводородный газ; IV – стабильная «головка»; V – стабильный высокооктановый бензин; VI – раствор моноэтаноламина (15 %); VII – свежий раствор моноэтано-
ламина (15 %)
газа возвращается циркуляционным компрессором 6 на смешивание с сырьем, а меньшая часть – избыточный ВСГ – выводится с установки.
Жидкая фаза, отделяемая в сепараторе 9, содержит растворенные сероводород, углеводородный газ и воду, поэтому подвергается нагреву в теплообменнике 23 и отпарке в колонне 7 за счет теплоты потока, подводимого из реактора 11 в кипятильник 22. Из куба этой колонны стабильный гидрогенизат проходит теплообменник 23 и насосом 24 направляется на смешивание с ВСГ в объемных соотношениях 1:1500, 1:2000. Далее смесь нагревают в теплообменнике 25 и во второй секции печи 12, а затем она последовательно проходит реактор 13, третью секцию печи 12, реактор 14, четвертую секцию печи 12 и реактор 15.
Продукт риформинга из реактора 15 охлаждают в теплообменнике 25, аппарате воздушного охлаждения (АВО) 26 и направляют в сепаратор высокого давления 27, где из него отделяется ВСГ. Газ поступает в компрессор 28. Большая его часть возвращается на смешивание с гидрогенизатом, а остальное количество направляется в блок гидроочистки. Жидкий продукт из сепаратора 27 попадает в сепаратор низкого давления 29, где из него выделяют растворенный углеводородный газ. Окончательно риформат стабилизируется в колоннах 16 и 20. Углеводородный газ гидроочистки и риформинга из сепараторов 3 и 29 смешивают и подают во фракционирующий абсорбер 16.
Нестабильный бензин из сепаратора 29 двумя потоками поступает в абсорбер 16: часть холодного бензина подается на верх абсорбера, другая часть нагревается в теплообменнике 30 и подается в низ абсорбера. С верха абсорбера 16 отводится сухой углеводородный газ, с низа – бензин в колонну стабилизации 20 после предварительного нагрева в теплообменнике 34 за счет стабильного бензина. С верха колонны 20 с установки отводится «головка» стабилизации, с низа колонны 20 через теплообменники 30,
61
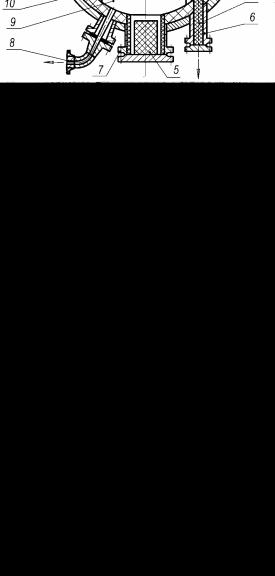
34 и холодильник 33 – стабильный бензин. Нагрев колонн 16 и 20 осуществляется методом горячей струи через двухкамерную печь 32.
Основное технологическое оборудование
Основным оборудованием являются реакторы. Реактор представляет собой цилиндрический вертикальный сосуд с эллиптическими или полушаровыми днищами. Внутренний диаметр колеблется от 2600 до 4500 мм. Высота слоя катализатора обычно составляет 1–3 диаметра. Реакторы работают под давлением до 5 МПа при темпе-
ратуре до 550 °С.
Реакторы изготавливаются в двух вариантах:
Рис. 59. Реактор риформинга аксиального типа с «холодным» корпусом: 1 – днище; 2 – корпус; 3, 16 – термопары; 4 – опорное кольцо; 5 – шамотный порошок; 6 – люк для выгрузки катализатора; 7 – люк-лаз; 8 – эжекция газов; 9 – опорная решетка; 10–12, 14 – шарики; 13 – катализатор; 15 – футеровка; 17, 19 – ввод и вывод парогазовой смеси; 18 – распредели-
тель парогазовой смеси
1)с «холодным» корпусом, теплоизолированным изнутри слоем торкрет-бетона (жаропрочным бетоном, нанесенным методом напыления);
2)с «горячим» корпусом, который изнутри не футеруется.
Кроме того, по способу распределения
идвижения сырья реакторы разделяют на аксиальные (осевые) и радиальные.
В первом случае газосырьевая смесь проходит через слой катализатора вдоль оси реактора сверху вниз. Благодаря этому исключается возможность вибрации слоя катализатора, особенно в моменты пуска
иостановок, и связанное с этим усиленное истирание катализатора. Во втором случае сырье движется радиально от краев реактора к центру.
На рис. 59 приведена конструкция реактора аксиального типа с «холодным» корпусом. Корпус реактора изготовлен из стали марки 16ГС, 22К или 09Г2ДТ и покрыт изнутри торкрет-бетонной футеровкой для защиты от высоких температур
иконтакта с водородом. В этих условиях может протекать водородная коррозия, которая заключается в диффузии водорода
в толщу металла и взаимодействии его с углеродом, содержащимся в стали. При этом образуется метан, и сталь теряет свою прочность.
Для уменьшения водородной коррозии необходимо использовать стали с ми-
62
нимальным содержанием углерода, а также ограничивать температуру нагрева стенки реактора. Качество футеровки должно быть высоким во избежание появления на ней трещин в процессе эксплуатации (особенно уязвимы в этом отношении верхние участки реактора в области штуцеров). Герметичность футеровки может нарушиться также из-за резких изменений температуры. Все внутренние устройства реактора выполнены из высоколегированной стали 08Х18Н10Т.
Сырье (парогазовая смесь) подается в реактор через верхний штуцер с помощью распределителя и проходит через слой фарфоровых шариков диаметром 20 мм, а также слой таблетированного алюмоплатинового катализатора высотой до 4 м. Катализатор удерживается на перфорированной опорной решетке, поверх которой для равномерного приема сырья насыпаны три слоя фарфоровых шариков диаметром 20, 13 и 6 мм.
Продукты реакции выводятся из реактора по парогазовому трубопроводу (стояку) через верхний штуцер диаметром 300 мм. На нижнем днище реактора имеется люк-лаз диаметром 500 мм для ремонта и два люка диаметром 100 мм, через которые эжектируют газы перед началом процесса регенерации и в случае необходимости проведения ремонтных работ.
Для защиты застойных зон реактора от высоких температур и водорода все свободные пространства люков и штуцеров заполнены шамотной мастикой.
При наличии внутренней футеровки, которая защищает стенки реактора от высоких температур, для изготовления корпуса используют углеродистую сталь. В другом случае применяют сталь 12ХМ или биметалл (сталь 12ХМ + 08Х18Н10Т).
Реакторный блок состоит из четырех реакторов, в том числе одного реактора для гидроочистки исходного сырья и трех – для риформинга. Количество катализатора, загружаемого в реакторы риформинга, возрастает от первого к третьему. Это объясняется тем, что реакции риформинга наиболее интенсивно протекают в первом реакторе, а затем, по мере приближения к состоянию равновесия, с меньшей скоростью.
На рис. 60 и 61 изображен реактор радиального типа для установки производительностью 1 млн т в год.
Он имеет внутренний диаметр корпуса 4500 мм. Реактор имеет эллиптические днища и изнутри изолирован слоем торкрет-бетона толщиной 100 мм. Кроме того, бетонное покрытие защищено от контакта с сырьем стаканом, в котором размещены внутренние устройства и катализатор. По периферии реактора размещается 60 вертикальных коробов. Стенки коробов, обращенные к катализатору, перфорированы и покрыты слоем мелкой плетеной сетки.
По центру реактора установлена вертикальная перфорированная труба. На трубе снаружи укреплен слой крупной и мелкой сетки, предупреждающий унос катализатора. В последнее время взамен малонадежных плетеных сеток начали использовать трубы, снабженные специальными щелевыми ситами.
Сырье вводится сверху реактора через распределитель, далее поступает в перфорированные короба, а затем, пройдя в радиальном направлении через слой катализатора, собирается в вертикальной трубе и выводится через штуцер снизу аппарата.
В верхней части слоя катализатора под тарелкой имеется цилиндрический стакан, который при оседании слоя катализатора во время эксплуатации аппарата остается погруженным в слой и предотвращает проход среды над слоем катализатора. Для выгрузки катализатора при его смене на нижнем днище предусмотрен наклонный штуцер. Для контроля температуры имеются три многозонные термопары. Для внутреннего осмотра,
63
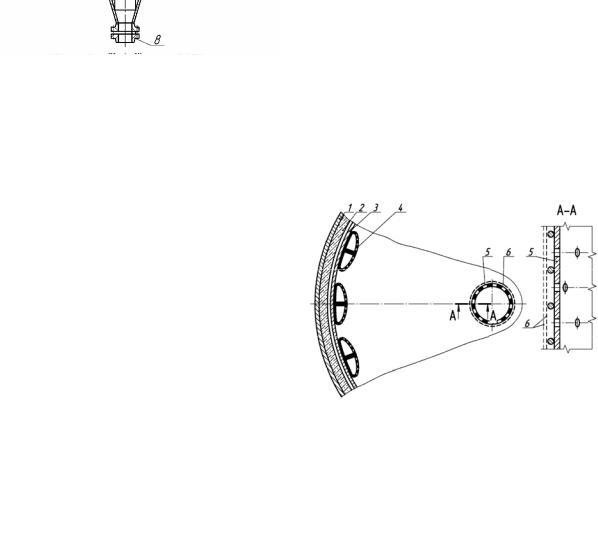
|
|
|
|
|
|
|
|
|
|
|
|
|
|
|
|
|
|
|
|
Рис. 60. Реактор риформинга радиального |
Рис. 61. Поперечное сечение реактора рифор- |
типа: 1 – штуцер; 2 – распределитель сы- |
минга радиального типа: 1 – корпус; 2 – тор- |
рья; 3 – корпус; 4 – стакан защитный; |
крет-бетон; 3 – стакан; 4 – короб; 5 – сборник; |
5 – короба; 6 – сборник продуктов реак- |
6 – сетка |
ции; 7 – штуцер выгрузки катализатора; |
|
8 – штуцер вывода продуктов; 9 – опора; |
|
10 – муфта для термопар; 11 – цилиндри- |
|
ческий стакан; 12 – гильзы для многозон- |
|
ных термопар |
|
монтажа внутренних устройств и загрузки катализатора служит верхний штуцер диаметром 800 мм.
Реакторы с радиальным движением являются наиболее прогрессивными. Они обеспечивают более равномерное распределение сырья по слою катализатора, а также имеют меньшее гидравлическое сопротивление. Очень важно, что это сопротивление в процессе эксплуатации катализатора практически не возрастает. Однако они несколько сложнее по своей конструкции, и их невозможно использовать для переработки исходного сырья, находящегося в двухфазном состоянии (газ-жидкость).
В настоящее время на установках каталитического риформинга проводится модернизация существующих реакторов с заменой аксиального вида движения сырья радиальным.
64
2.2. Коксование
Коксование является одной из разновидностей деструктивного процесса, протекающего при нагревании нефтепродуктов. При этом твердый углеродистый остаток (кокс) является целевым продуктом разложения и образуется в значительных количествах. Наряду с ним образуется также бензин, газойлевые фракции и углеводородный газ.
Нефтяной кокс широко применяется в различных отраслях промышленности. Он используется для производства угольных электродов, абразивных материалов, карбидов, углеграфитовых материалов, ферросплавов. При производстве Al расходуется кокса 0,6 т/т; карбида кремния – 1,4 т/т; карбида кальция – 0,7 т/т; графита – 1,25 т/т.
В зависимости от назначения к нефтяному коксу предъявляют различные требования. Основными показателями качества являются: содержание серы, золы, влаги, летучих примесей, гранулометрический состав, реакционная способность, пористость, удельное электрическое сопротивление и др.
Виды кокса. Выделяют следующие виды кокса:
1)по содержанию серы – малосернистый (до 1,0 %), среднесернистый (до 1,5 %), сернистый (до 4,0 %) и высокосернистый (больше 4,0 %);
2)по гранулометрическому составу – кусковой (больше 25 мм), «орешек» (6– 25 мм), мелочь (меньше 6 мм);
3)по содержанию золы – малозольный (меньше 0,5 %), среднезольный (0,5–0,8 %)
ивысокозольный (больше 0,8 %).
Качество кокса зависит как от свойств используемого сырья, так и от способа его получения. Для повышения качества кокса, используемого в производстве электродов (для уменьшения летучих примесей, устранения усадочных явлений и повышения электропроводимости), его подвергают дополнительной прокалке при 1200–1300 ºС у потребителя. Для этого пригодны только частицы размером больше 25 мм, а мелочь, которая составляет примерно 50 % продукта, в этих печах прокаливать нельзя.
Классификация установок коксования. Установки коксования бывают трех типов:
1.Установки периодического действия. Коксование проводят в обогреваемых кубах, представляющих собой горизонтальные аппараты диаметром 2–2,5 м и длиной 10–13 м с огневым обогревом через нижнюю часть. Сырье загружают в куб и постепенно подогревают. При 300 ºС начинается выделение дистиллятных паров. После того как температура в паровой зоне куба достигнет 445–460 °С, начинается ее снижение. Это свидетельствует о том, что образование коксового «пирога» в основном закончилось. Дальнейший подогрев куба необходим для завершения процесса коксования, прокалки
иподсушки кокса. После прокалки (2–3 ч) температуру постепенно снижают. Для охлаждения подают в куб сначала водяной пар, а затем воздух. Кокс выгружают при 150–200 °С с применением ручного труда. Этот процесс малопроизводителен, трудоемок, но позволяет получать высококачественный кокс с меньшим содержанием летучих примесей.
2.Установки полунепрерывного действия. В настоящее время они являются основными во всем мире. Процесс коксования производится в необогреваемых коксовых камерах (замедленное коксование). Сырье нагревают в трубчатых печах до 500 °С и направляют в полый необогреваемый вертикальный цилиндрический аппарат (коксовую камеру или реактор). В камере горячее сырье находится длительное время (24 ч) и за
65
счет аккумулированного им тепла коксуется. С верха камеры удаляются пары легких дистиллятов. После заполнения камеры коксом на 70–90 % поток горячего сырья переключают на другую камеру, а из отключенной камеры выгружают кокс. Процесс замедленного коксования имеет периодический характер по выгрузке кокса
инепрерывный по подаче сырья и выделению паров дистиллятных продуктов.
3.Установки непрерывного действия. При непрерывном коксовании нагретое сырье вступает в контакт с подвижным, нагретым до более высоких температур инертным твердым измельченным теплоносителем и коксуется на его поверхности. Затем кокс вместе с теплоносителем поступает в регенератор, где часть кокса выжигается. За счет этого температура теплоносителя возрастает, и он вновь возвращается в зону коксования. Процесс проводится в псевдоожиженном слое. В качестве теплоносителя служит порошкообразный кокс с размером частиц до 0,3 мм. Благодаря повышенной температуре получаемый порошкообразный кокс имеет меньшее количество летучих примесей, однако выход кокса понижен в 1,5–1,6 раза, так как часть его сжигается в регенераторе.
Поэтому эти установки применяют, когда основным продуктом является не кокс, а светлые нефтепродукты.
Чаще всего коксованию подвергаются высокомолекулярные нефтяные остатки: гудроны, крекинг-остатки термического крекинга, асфальты и экстракты с установок масляного производства, смолы пиролиза.
Основными показателями качества сырья являются его коксуемость, содержание серы и золы, а также вязкость. Коксуемость тем выше, чем больше в сырье смолистоасфальтеновых веществ. Как правило, коксуемость крекинг-остатка выше, чем гудрона. Экономически необходимо, чтобы коксуемость была не менее 10 %. Однако, если коксуемость превышает 20 %, это приводит к быстрому закоксовыванию труб трубчатых печей, в которых нагревается сырье.
Основные потребители нуждаются в малосернистом коксе, поэтому в исходном сырье должно быть не более 0,5–0,8 % серы, так как в коксе ее содержание повышается в 1,5 раза.
Кроме кокса образуются также газ, бензин, керосино-газойлевые фракции (180– 350 °С и 350–450 °С), тяжелый газойль (больше 450 °С). Бензин недостаточно стабилен, и октановое число его не превышает 68–72 пунктов. Керосино-газойлевые фракции служат в качестве компонентов газотрубного топлива и сырья каталитического крекинга. Фракция 180–350 °С может быть использована в дизельном топливе. Тяжелый газойль используют как компонент котельных топлив.
Подробнее рассмотрим установку замедленного коксования.
Ниже приводятся нормы технологического режима данной установки:
Температура, °С: |
|
первичного сырья на выходе из печи |
375–390 |
вторичного сырья на выходе из печи |
495–505 |
паров на выходе из камеры |
440–455 |
Давление в коксовой камере, МПа |
0,18–0,4 |
Коэффициент рециркуляции |
1,2–1,6 |
Общая длительность цикла, ч |
48 |
66
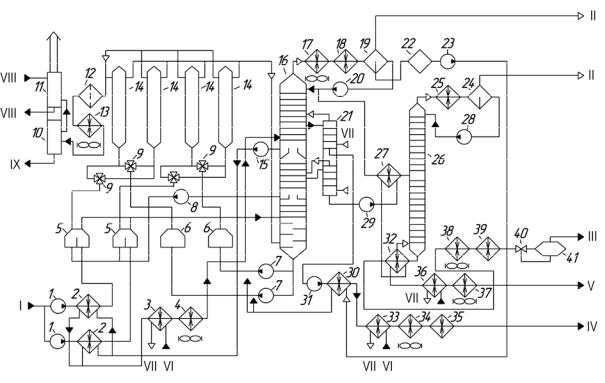
Принципиальная технологическая схема
Замедленное коксование в установке полунепрерывного действия (рис. 62) производится следующим образом.
Исходное сырье подается насосом 1 через теплообменники 2 и правую часть змеевиков трубчатых печей 6 на каскадные тарелки ректификационной колонны 16 (375– 390 °С).
Рис. 62. Принципиальная технологическая схема установки замедленного коксования: 1, 7, 8, 15, 20, 23, 28, 29, 31 – насосы; 2, 27, 30 – теплообменники; 3, 33, 36 – испарители; 4, 34, 35, 37– 39 – холодильники; 5, 6 – трубчатые печи; 9 – четырехходовые краны; 10, 19; 22, 24, 41 – емкости; 11 – скруббер; 12 – фильтр; 14 – камеры; 16, 21, 26 – колонны; 13, 17, 18, 25 – конденсато- ры-холодильники; 32 – кипятильник; 40 – инжектор. Потоки: I – сырье; II – газ; III – бензин; IV – легкий газойль; V – тяжелый газойль; VI – химически очищенная вода; VII – пар водяной;
VIII – вода; IX – тяжелый нефтепродукт
Под нижнюю (каскадную) тарелку этой же колонны подаются горячие пары продуктов коксования из коксовых камер. За счет контакта паров, имеющих температуру около 430 ºС, с менее нагретым сырьем последнее подогревается до 400 ºС, при этом часть паров конденсируется.
Сконденсировавшиеся продукты коксования служат рециркулятом. Вместе с исходным сырьем они уходят в низ колонны 16 и далее насосами 7 направляются в радиационную камеру трубчатых печей 5, где подогреваются дополнительно до температуры начала коксования (500–510 ºС). Далее сырье через нижнюю часть поступает в коксовые камеры 14. Для улучшения качества кокса в камеры подается дополнительное количество теплоты в виде паров тяжелого газойля коксования. Тяжелый газойль забирается из колонны 16, насосом 8 прокачивается через левую часть змеевика печей 5, где нагревается до 525 ºС, и направляется на смешение с сырьем в переключающие краны 9. Тяжелый газойль подается в камеры не только в смеси с сырьем, но и самостоя-
67
тельно в течение шести часов после прекращения подачи сырья – в период «томления» кокса. Благодаря подаче тяжелого газойля кокс приобретает высокую механическую прочность и содержит мало летучих примесей.
В конце цикла коксования в камеру коксования вводят антипенную присадку, что позволяет уменьшить вспенивание сырья и тем самым исключить отложение кокса в колонне, печных насосах и трубах печей. Для снижения температуры паров, выходящих из коксовых камер, в верхнюю часть коксовых камер подается легкий газойль.
На установке имеются четыре камеры, работающие попарно и независимо друг от друга. Каждую пару можно отключить, не останавливая установки. Из верхней части камер парообразные продукты коксования выводят в ректификационную колонну 16. Нижняя часть этой колонны снабжена каскадными тарелками, устойчивыми при работе с загрязненными парами.
Бензиновые фракции и газы уходят из верха колонны в воздушный конденсаторхолодильник 17 и водяной конденсатор-холодильник 18. Конденсат из холодильника 18 поступает в сепаратор 19, где отделяется газ от бензина и бензин от воды. Вода поступает в емкость 22 и далее в трубчатую печь 6 в качестве турбулизатора потоков (после предварительного нагрева в теплообменнике 30).
Из колонны 16 выводятся два боковых погона – легкий и тяжелый газойли, которые поступают в секции отпарной колонны 21. Легкий газойль забирается из верхней секции колонны 21 насосом 31, прокачивается через теплообменник нагрева турбулизатора 30, испаритель 33, воздушный 34 и водяной 35 холодильники, а затем выводится с установки.
Тяжелый газойль из нижней секции отпарной колонны 21 прокачивается насосом 29 через теплообменник нагрева сырья стабилизатора 27, рибойлер стабилизатора 32, испаритель 36, воздушный холодильник 37, а затем выводится с установки.
Избыточная теплота колонны 16 снимается циркуляционным орошением, которое забирается насосом 15 с десятой тарелки, прокачивается через теплообменник нагрева сырья 2, испаритель 3 и воздушный холодильник 4, а затем возвращается в колонну.
Бензиновая фракция из сепаратора 19 насосом 20 через теплообменник 27 направляется в стабилизационную колонну 26. В ней происходит дебутанизация бензина. Пары с верха колонны 26 поступают в конденсатор-холодильник 25, откуда парожидкостная смесь направляется в газосепаратор 24, где разделяется на газ стабилизации и «головку» стабилизации. Газ выводится с установки, а «головка» возвращается в колонну 26 в качестве флегмы.
Стабильный бензин с низа колонны 26 проходит кипятильник 32, воздушный 38 и водяной 39 холодильники. В инжекторе бензин смешивается с циркулирующей щелочью, от которой затем отделяется в емкости 41.
Реакционные камеры установок замедленного коксования работают по циклическому графику. По этому графику в них чередуются циклы: реакция, охлаждение кокса, выгрузка кокса и разогрев камеры.
Коксовую камеру опрессовывают и прогревают водяным паром, удаляя одновременно из нее воздух. Затем через нее пропускают горячие пары продуктов коксования из соседней камеры (до 360 °С) и начинают загрузку сырья.
При подаче горячего сырья в пустую разогретую камеру происходит дополнительный подогрев ее стенок. В этот период преобладают процессы испарения, и в нижней части камеры накапливается жидкая масса, представляющая собой тяжелые фракции
68
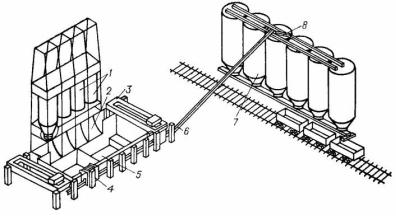
сырья. В зависимости от температуры и типа сырья длительность этой стадии колеблется от 2 до 6 ч. При дальнейшей работе сырье проходит через все более высокий слой этой массы и при этом происходит интенсивное коксообразование. Этот период характеризуется относительным постоянством выхода и состава парообразных продуктов разложения.
Когда камера заполнена на 75–80 %, сырье переключают на другую камеру. Из-за постепенного понижения температуры в отключенной камере процесс коксования замедляется. Всего по высоте камеры насчитывается три слоя кокса:
–нижний, образовавшийся в первый период;
–средний, образовавшийся во второй период;
–верхний, который откладывается в отключенной камере.
Кокс верхнего слоя наименее прочен, содержит много летучих примесей и обладает повышенной зольностью.
Отключенную камеру в течение 2,5 ч продувают водяным паром для удаления жидких продуктов и нефтяных паров. Они поступают сначала в колонну 16. После охлаждения кокса до 400–405 °С поток паров направляют через фильтр 12 и конденсаторхолодильник 13 в емкость 10.
Водяным паром кокс охлаждают до 200 °С, после этого в камеру подают воду (4 ч). Образующиеся пары конденсируются в скруббере 11. Далее начинают выгрузку коксового «пирога». Над каждой камерой установлены буровые вышки высотой около 40 м, предназначенные для подвешивания бурового оборудования.
Выгрузка кокса производится в две стадии. На первой стадии осуществляется гидравлическое бурение центрального ствола (скважины) в слое кокса. Для этого в камеру через верхний люк опускают гидрорезак, переведенный в положение «бурение», и с помощью водяного насоса под давлением до 18 МПа подают воду.
Три мощные струи, истекающие из бурильных сопел, разрушают слой кокса, создавая сквозной канал диаметром от 0,6 до 1,8 м. После окончания первой стадии гидрорезак вынимают из камеры, переключают в положение «отбойка» и приступают ко второй стадии выгрузки. В этом режиме вода истекает горизонтально из двух боковых сопел гидрорезака, который перемещается по камере, полностью удаляя кокс.
На установках замедленного коксования чаще всего эксплуатируют систему обработки и транспортирования кокса, приведенную на рис. 63.
Рис. 63. Система обработки и транспортирования кокса: 1 – камера коксования; 2 – рампа; 3 – грейферный мостовой кран; 4 – узел дробления; 5 – яма-накопитель; 6 – ленточный конвейер; 7 – склад кокса; 8 – грохот
69
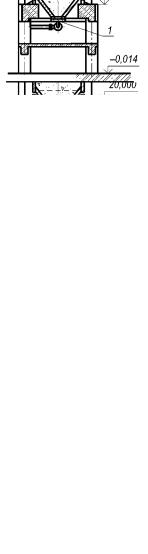
Из камер 1 кокс выгружается в яму-накопитель 5, где в течение определенного времени отстаивается от воды. Затем кокс грейферным краном 3 подается в дробилку и конвейерами 4 отгружается на склад силосного типа 7. Перед силосами проводится контрольная классификация кусков кокса на грохоте 8.
Основное технологическое оборудование
К основному оборудованию установки замедленного коксования относятся коксовые камеры, трубчатые печи и ректификационная колонна.
|
|
|
Коксовые камеры являются основными реак- |
|
|
|
|
ционными агрегатами и работают периодически при |
|
|
|
|
циклическом изменении температуры до 500 °С. Ра- |
|
|
|
|
бочий цикл длится около 48 ч и включает стадии ре- |
|
|
|
|
акции, пропаривания, охлаждения, выгрузки кокса |
|
|
|
|
и разогрева. Число и размер камер зависят от произ- |
|
|
|
|
||
|
|
|
водительности установки, качества сырья и давления |
|
|
|
|
в камере. Повышение давления способствует увели- |
|
|
|
|
чению выхода кокса и газа, позволяет повысить ско- |
|
|
|
|
рость загрузки жидкого сырья и использовать избы- |
|
|
|
|
точное давление в системе для подачи газа на газо- |
|
|
|
|
||
|
|
|
вый блок. |
|
|
|
|
Коксовая камера (рис. 64) представляет собой |
|
|
|
|
пустотелый аппарат диаметром 3000–7000 мм и вы- |
|
|
|
|
сотой 22–30 м с полушаровым и коническим днища- |
|
|
|
|
ми. В верху камера снабжена горловиной 4 для ввода |
|
|
|
|
гидрорезака. К обечайке этой горловины приварены |
|
|
|
|
штуцеры для вывода нефтяных паров в ректифика- |
|
|
|
|
ционную колонну при коксовании и подачи этих па- |
|
|
|
|
ров из соседней камеры при разогреве. Внизу имеет- |
|
|
|
|
||
|
|
|
ся люк 1 для выгрузки кокса. В верхней части корпу- |
|
|
|
|
са установлены четыре штуцера 3 для форсунок, |
|
|
|
|
через которые разбрызгивается антипенная присад- |
|
|
|
|
ка, предотвращающая образование и выброс пены. |
|
|
|
|
Корпус камеры изготовлен из биметалла 12ХМ + |
|
|
|
|
||
|
|
|
+ 08Х13 или 16ГС + 08Х13 или из стали 12Х18Н10Т. |
|
|
|
|
Снаружи камера покрыта слоем теплоизоляции тол- |
|
|
|
|
щиной 250 мм. |
|
|
|
|
Камера установлена на постаменте высотой |
|
|
|
|
||
Рис. 64. Схема коксовой камеры: |
20 м. На этом же постаменте смонтированы метал- |
|||
1 – люк для выгрузки кокса; 2 – |
локонструкции 7 с оборудованием для гидравличе- |
|||
коксовая камера; 3 – штуцеры для |
ского разрушения и выгрузки кокса. Это оборудова- |
|||
ввода антипенной добавки; 4 – гор- |
ние включает системы вращения и вертикального |
|||
ловина; 5 – гидрорезак; 6 – ротор; |
перемещения гидроинструмента. |
|||
7 – металлоконструкции; 8 – лебед- |
Гидрорезак 5, снабженный соплами для бурения |
|||
ка; 9 – стояк; 10 – шланг высокого |
||||
и резки, прикреплен к полой штанге 12 квадратного |
||||
давления; 11 – направляющие для |
||||
вертлюга; 12 – штанга; 13 – верт- |
сечения, подвешенной через вертлюг 13 к блоку 14 |
|||
люг; 14 – блок талевой системы |
талевой системой. Последняя обеспечивает верти- |
|||
|
|
|
70 |