
Основное технологическое оборудование нефтеперерабатывающих заводо
..pdf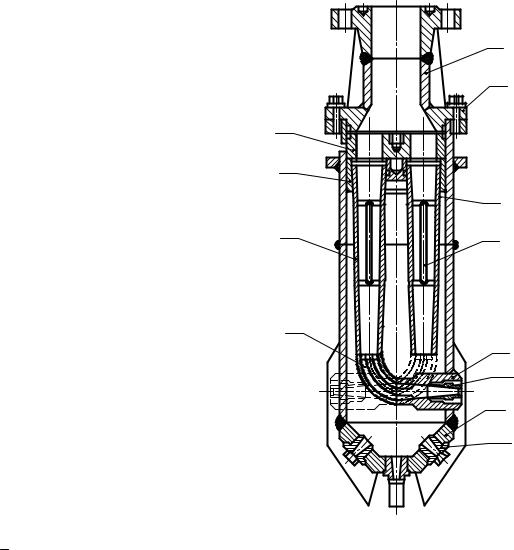
кальное перемещение гидрорезака. Сни- |
|
|
|
|
|
|||||
зу по стояку 9 и шлангу 10 через верт- |
|
|
|
|
1 |
|||||
люг и штангу к гидрорезаку подается |
|
|
|
|
||||||
вода под давлением 16–25 МПа. Штанга |
|
|
|
|
2 |
|||||
приводится во вращение ротором 6. Для |
|
|
|
|
||||||
|
|
|
|
|
||||||
предотвращения |
раскачивания |
штанги |
|
|
|
|
|
|||
вертлюг снабжен вертикальными на- |
|
4 |
|
|
|
|||||
правляющими |
11. |
Благодаря |
этому |
|
|
|
|
|
||
штанга имеет две опоры – ротор и верт- |
|
5 |
|
|
|
|||||
люг. Ротор и талевая лебедка 8 должны |
|
|
|
|
3 |
|||||
обеспечивать плавное изменение скоро- |
|
|
|
|
||||||
|
|
|
|
|
||||||
сти вращательного |
и поступательного |
|
6 |
|
|
7 |
||||
движения. Это достигается применени- |
|
|
|
|||||||
|
|
|
|
|
||||||
ем гидропривода. |
|
|
|
|
|
|
|
|||
При удалении кокса камеру откры- |
|
|
|
|
|
|||||
вают, гидравлически разбуривают на- |
|
|
|
|
|
|||||
чальную центральную скважину и затем |
|
8 |
|
|
|
|||||
высокоскоростными струями воды вы- |
|
|
|
|
9 |
|||||
полняют резку |
кокса, который |
выгру- |
|
|
|
|
10 |
|||
жают через нижний люк. Кокс в после- |
|
|
|
|
||||||
|
|
|
|
|
||||||
дующем подается на дробление, грохо- |
|
|
|
|
11 |
|||||
чение и складирование. |
|
|
|
|
|
12 |
||||
Конструкция опорного узла коксо- |
|
|
|
|
||||||
|
|
|
|
|
||||||
вой камеры должна обеспечивать работу |
|
|
|
|
|
|||||
при циклическом изменении температу- |
|
|
|
|
|
|||||
ры корпуса. |
|
|
|
|
|
|
|
|
||
В стадии реакции камера заполня- |
Рис. |
65. Универсальный гидрорезак |
||||||||
3 |
|
|
|
|
||||||
|
|
|
|
ГРУ-2: 1 – горловина; 2 – крышка; |
||||||
ется на 4 |
высоты сырьем, нагретым до |
|||||||||
3 |
– |
цилиндрическая часть |
ствола; |
|||||||
460–510 °С. Уровень |
заполнения кон- |
4 |
– |
золотник; 5 – распределитель; |
||||||
тролируют |
радиационным уровнеме- |
6 – коническая часть ствола; 7, 8 – |
||||||||
ром. Рабочее давление 0,4–0,6 |
МПа. В |
успокоители; 9 – переходные сопла; |
||||||||
конце стадии реакции для уменьшения |
10 – режущие |
сопла; 11 – |
корпус |
|||||||
гидродолота; |
12 – бурильные сопла |
|||||||||
количества летучих примесей в коксе в |
||||||||||
|
|
|
|
|
||||||
ряде случаев предусматривается цирку- |
|
|
|
|
|
ляция через камеру теплоносителя, в качестве которого служит нагретый в отдельной печи до 530 °С газойль. После завершения коксования удаляют нефтяные пары и охлаждают камеру водяным паром, затем водой.
На рис. 65 изображен универсальный гидрорезак ГРУ-2, в котором образуются высоконапорные компактные водяные струи, с помощью которых проводятся операции бурения центрального ствола и гидравлической отбойки (выгрузки) кокса.
Ректификационная колонна предназначена для разделения продуктов коксования, поступающих из коксовых камер, на отдельные фракции: газ, бензин, легкий и тяжелый газойли. Кроме того, в колонне проводят нагрев исходного сырья и его разбавление газойлевыми фракциями путем непосредственного контакта с горячими парами, выходящими из коксовых камер.
71
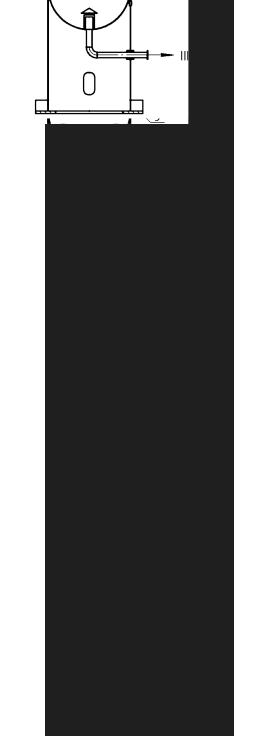
Одна из конструкций колонн представлена на рис. 66. Она представляет собой сварной цилиндрический аппарат переменного сечения с коническим переходом. Диаметр корпуса в нижней части составляет 4500 мм, а в верхней – 2600 мм. Широкая часть корпуса биметаллическая (стали 16ГС и 08Х13), переходная и узкая части – из стали 16ГС. Толщина стенки корпуса в верхней части 20 мм,
внижней 32 мм. Толщина верхнего эллиптического днища составляет 20 мм, нижнего полушарового – 26 мм.
Внутри колонны имеется 37 тарелок. Четыре каскадные тарелки, на которых первичное сырье контактирует с парами, выходящими из коксовых камер, расположены в нижней части колонны.
Над верхней каскадной тарелкой установлен распределитель для равномерного распределения сырья. Предусмотрен также ввод сырья под нижнюю каскадную тарелку.
Над каскадными тарелками в широкой части колонны расположены 13 тарелок с S-об- разными элементами, из них нижние девять тарелок двухпоточные, остальные – однопоточные.
Вузкой части колонны расположены 20 прямоточных однопоточных клапанных тарелок. Они обеспечивают работу колонны
всравнительно широком диапазоне изменения нагрузок по пару и жидкости. Однако их недостаток состоит в возможности засорения и закоксовывания.
Рис. 66. Ректификационная колонна установки замедленного коксования: 1 – штуцер для предохранительного клапана; 2 – люк; 3 – штуцер для регулятора уровня. Потоки: I – сырье; II – пары из коксовых камер; III – остаток; IV – пусковой газойль; V – легкий газойль; VI – пары; VII – орошение; VIII – пары легкого газойля; IX – верхнее циркуляционное орошение; X – фракция тяжелого газойля; XI – пары
тяжелого газойля
72
3. ПРОИЗВОДСТВО МАСЕЛ
Основное назначение масел – смазка трущихся твердых поверхностей. Кроме того, они используются в других целях, например для охлаждения и специальных технических целей.
Характеристики масел.
В зависимости от условий эксплуатации основными характеристиками масел являются:
1.Вязкость. Требования к вязкости различны: легкие индустриальные масла должны иметь кинематическую вязкость при 50 °С от 4 до 8,5 мм2/с, а наиболее вязкие остаточные масла – 60–70 мм2/с.
2.Вязкостно-температурная характеристика (индекс вязкости). Она имеет большое значение для масел, работающих в широком диапазоне изменения температур.
При высоких температурах масла не должны сильно разжижаться, а при низких – терять свою текучесть. Природные вязкостно-температурные свойства нефтяных масел даже лучших месторождений не соответствуют требованиям к современным моторным маслам. Значительное улучшение свойств масел достигается путем удаления из них низкоиндексных компонентов и применения специальных присадок.
3.Маслянистость (смазывающая способность). Когда масло работает при больших нагрузках и малых скоростях движения, даже высокая вязкость масла не обеспечивает режима жидкостной смазки. При этом масло полностью выжимается из-под трущихся поверхностей. В этом случае важнейшей характеристикой становится маслянистость – способность создавать на металлической поверхности весьма прочный, хотя и тонкий смазочный слой толщиной, не превышающей одного микрона, т.е. от 50 до 500 молекулярных слоев. Такой тип смазки получил название полусухой (или граничной) смазки. Несмотря на ничтожную толщину такого слоя, износ материалов уменьшается в несколько тысяч раз по сравнению с сухим трением.
4.Температура застывания. Масла для холодильных машин, трансформаторов, приборные, моторные и другие не должны терять подвижность при низких температурах до минус 18–30, и даже минус 60 °С. Величина температуры застывания масел зависит от присутствия в них высокомолекулярных твердых углеводородов (парафинов
ицерезинов). При низких температурах они кристаллизуются, образуя пространственные структурные сетки, в результате масло теряет текучесть. Для понижения температур застывания проводят депарафинизацию масел с отделением твердых кристаллов углеводородов, после этого в масло вводят специальные присадки (депрессоры).
5.Химическая стойкость по отношению к кислороду воздуха. Эта характеристика наиболее важна для масел, которые эксплуатируются в условиях циркуляционной смазки, т.е. многократно прокачиваются через узлы трения. Окисление может происходить либо во всем объеме масла, либо в тонком слое, когда масло прокачивается через цилиндропоршневые узлы трения. В последнем случае масло работает в особо тяжелых условиях. Радикальным способом повышения антиокислительных свойств является использование процессов каталитического гидрирования масел. Для этих целей используются также специальные антиокислительные присадки.
Кроме указанных выше, к маслам добавляются и другие присадки: антикоррозионные, противозадирные, моющие, антинагарные, антипенные и др. В настоящее время используются многофункциональные присадки, которые улучшают одновременно различные свойства масел. Это либо смесь присадок одностороннего действия, либо спе-
73
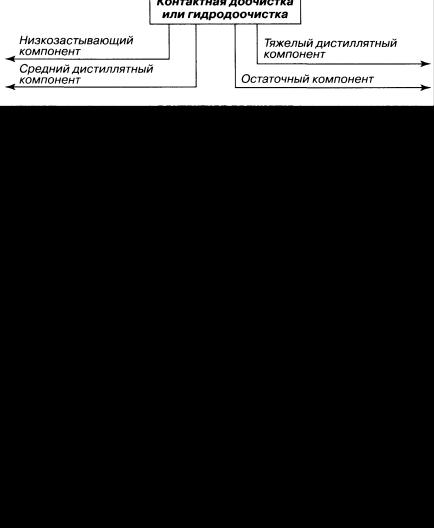
циальные сложные органические соединения, содержащие серу, фосфор, металлы и различные полярные группы.
Получение масел. Все нефтяные масла получают из мазута в три этапа (рис. 67):
1.Подготовка сырья. Это получение исходных масляных фракций, которое состоит
ввакуумной перегонке мазута по масляной схеме. Получаемые фракции делят на две группы:
– дистиллятные (300–400; 350–420 и 420–450 °С),
– остаточные – остаток перегонки мазута (гудрон или полугудрон). Соответственно этому масла, получаемые из дистиллятных масляных фракций, на-
зываются дистиллятными, а из гудрона – остаточными.
2.Получение базовых масляных компонентов из исходных масляных фракций. Это сложный многоступенчатый процесс очистки. Необходимо удалить все кислые соединения, непредельные углеводороды, частично сернистые соединения, полициклические ароматические углеводороды с короткими боковыми цепями и твердые углеводороды. Для этого используют различные методы очистки: экстракцию селективными растворителями, кристаллизацию при пониженной температуре, адсорбцию, взаимодействие с серной кислотой, гидроочистку и другие процессы.
Рис. 67. Блок-схема производства масел из нефтей восточных районов
74
Производство остаточных масел сложнее, чем дистиллятных, из-за высокого содержания смолисто-асфальтеновых примесей в исходном сырье (гудроне), составляющих до 50 % и более. Гудрон прежде всего подвергают деасфальтизации, т.е. освобождению от смолисто-асфальтеновых примесей. Очищенный гудрон (деасфальтизат)
направляют далее на селективную очистку фенолом или фурфуролом для доизвлече-
ния оставшихся смолисто-асфальтеновых примесей, но в основном для удаления низкоиндексных полициклических ароматических углеводородов с короткими боковыми цепями с целью повышения индекса вязкости. Иногда деасфальтизацию и селективную очистку объединяют с использованием парных растворителей (доусол-процесс).
Рафинаты селективной очистки (масляные фракции) подвергают депарафинизации, т.е. осаждают твердые углеводороды при помощи специальных избирательных растворителей (метилэтилкетона, толуола и др.) при охлаждении. Масляные фракции после отделения выпавших кристаллов твердых углеводородов (депарафинизат) окончательно доводят до кондиции путем адсорбционной очистки или гидроочистки. Дистиллятные масляные фракции в деасфальтизации не нуждаются, а в остальном схемы производства дистиллятных и остаточных масел совпадают.
3. Компаундирование. Масла товарных марок готовят смешиванием отдельных компонентов базовых масел в строго определенных соотношениях с добавлением присадок. Это происходит на установках компаундирования.
Рассмотрим подробнее получение базовых масляных компонентов.
3.1. Деасфальтизация масел
Остаточные масла получают из гудронов и полугудронов, которые содержат в своем составе более 50 % высокомолекулярных смол и асфальтенов, подлежащих удалению. Сложный состав этих примесей затрудняет подбор для них избирательных растворителей, поэтому на практике подбирают такие селективные растворители, в которых хорошо растворяются ценные углеводороды масла, а примеси не растворяются и поэтому выпадают в осадок (так называемый метод обратной экстракции). В качестве такого растворителя в настоящее время наиболее широко используется жидкий пропан.
К важнейшим параметрам процесса экстракции относятся:
1.Температура. Осадок смол и асфальтенов легко отделяется от раствора масла
впропане при температуре 50–85 °С. Верхний предел ограничен критической темпера-
турой сжижения пропана (tкрит = 96,8 ºС). Чем ближе температура пропана к критической, тем выше его селективность, но меньше растворяющая способность. Это приводит к ухудшению растворения масла и к увеличению его потерь вместе со смолами и асфальтенами, т.е. при этом снижается выход деасфальтизата. Напротив, при снижении температуры растворяющая способность жидкого пропана растет, но селективность падает. Это приводит к увеличению выхода, но связано с ухудшением качества деасфальтизата.
Этот недостаток жидкого пропана преодолевается путем организации его взаимодействия с исходным сырьем в колонных аппаратах в режиме противотока в неизотермических условиях. При этом жидкий пропан подается в низ колонны и поднимается навстречу более плотному сырью, подаваемому сверху.
В верхней части колонны поддерживают температуру 75–85 ºС, а в нижней 50– 60 ºС. Этот температурный перепад, равный 15–20 ºС (так называемый температурный градиент деасфальтизации), позволяет в нижней части колонны максимально извлечь
75
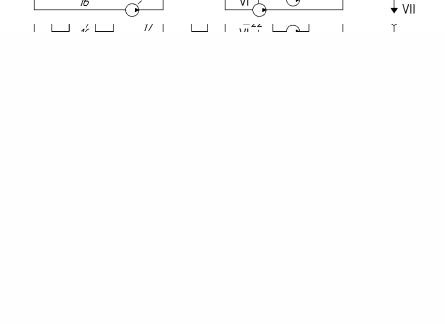
масло из смол и асфальтенов, а в верхней части повысить качество раствора деасфальтизата за счет уменьшения растворимости примесей смол и асфальтенов. Для поддержания пропана в сжиженном состоянии используется давление 4–4,5 МПа.
2.Соотношение пропана и сырья. Оно зависит от концентрации примеси смол
иасфальтенов в исходном сырье. Чем больше этих примесей, тем это соотношение должно быть меньше. На практике оно колеблется в широких пределах от 4–8 к одному. Увеличение этого соотношения до определенных пределов снижает вязкость раствора, улучшает условия осаждения примесей и повышает качество масла. Но при чрезмерном увеличении избытка пропана в нем начинают растворяться также нежелательные примеси, что вызывает снижение качества масла.
Процесс деасфальтизации часто проводят в две ступени: раствор асфальта, полученный на первой ступени, подвергают дополнительной деасфальтизации пропаном на второй ступени. За счет этого извлечение масла из сырья повышается на 10 %.
Принципиальная технологическая схема
Двухступенчатая деасфальтизация гудрона осуществляется следующим образом
(рис. 68).
Исходное сырье (гудрон) сырьевым насосом 1 подается в пароподогреватель 2 и далее в среднюю часть экстракционной колонны первой ступени 3. В низ этой колонны насосом 10 подается жидкий пропан. Раствор деасфальтизата первой ступени в пропане уходит с верха колонны 3 с температурой 86–87 ºС, а раствор асфальта первой ступени с низа колонны 3 с температурой 63–64 ºС направляется в середину экстракционной колонны второй ступени 4. В нижнюю часть этой колонны также поступает жидкий пропан.
Рис. 68. Принципиальная технологическая схема двухступенчатой деасфальтизации масел пропаном: 1, 10, 13, 17, 22, 24 – насосы; 2 – пароподогреватель; 3, 4, 14, 15, 20, 21, 23, 27 – колонны; 5–7 – испарители; 8, 11, 18, 25, 26 – холодильники; 9, 12 – емкости; 16 – печь; 19 – теплообменник; 28 – компрессор. Потоки: I – сырье; II – пропан; III – деасфальтизат первой ступени; IV – деасфальтизат второй ступени; V – асфальт; VI – водяной пар; VII – вода
76
С верха колонны 4 уходит раствор деасфальтизата второй ступени в пропане с температурой 81–82 ºС. Пропан из растворов деасфальтизатов первой и второй ступеней регенерируется раздельно. Раствор деасфальтизата первой ступени входит в испаритель 5, где испаряется основная доля пропана. Далее раствор деасфальтизата подогревается в теплообменнике 19 и поступает в колонну 20, где дросселируется до 1,8 МПа с выделением газообразного пропана. С низа колонны 20 деасфальтизат первой ступени поступает в колонну 21, где окончательно дросселируется и отпаривается от остатков пропана острым водяным паром, и насосом 22 откачивается с установки через холодильник 26.
Раствор деасфальтизата второй ступени с верха колонны 4 отпаривается последовательно в двух ребойлерах 6 и 7. Окончательно пропан отпаривается острым водяным паром в колонне 23, после этого деасфальтизат второй ступени насосом 24 через холодильник 25 откачивается с установки.
Раствор асфальта второй ступени с низа колонны 4 подается в трубчатую печь 26, где нагревается до 200–250 °С, и поступает в колонну 15. Здесь отделяется основная масса пропана. С низа колонны 15 раствор направляется в колонну 14 для окончательной отпарки острым водяным паром. С низа колонны 14 асфальт насосом 17 откачивается через теплообменник 19 и холодильник 18 с установки.
Пары пропана с температурой 50–100 °С под давлением 2,7 МПа из испарителей 5
и6 и колонны 15 конденсируются в холодильнике 8 и собираются в емкости 9. Пары пропана под давлением 1,8 МПа из испарителя 7 и колонны 20 конденсируются в холодильнике 11 и собираются в емкости 12, откуда насосом 13 перекачиваются в емкость 9. Газообразный пропан и водяные пары из колонн 14, 21 и 23 подвергаются осушке в колонне 27, орошаемой холодной водой. Пропан не растворяется в воде
ис верха колонны 27 поступает в компрессор 28, сжимается до 1,9 МПа и возвращается в систему жидкого пропана.
Основное технологическое оборудование
Вкачестве примера основного оборудования рассмотрим экстракционную колонну для деасфальтизации пропаном (рис. 69). Она представляет собой колонный аппарат
сверхним и нижним полусферическими днищами. Внутренний диаметр колонны 3400 мм, толщина стенки 70 мм, высота 19 200 мм, полный объем 119 м3. Сравнительно высокое давление в колонне (3–4 МПа) вызвано необходимостью поддерживания пропана при температуре 70–90 °С в жидкой фазе.
Взоне экстракции для улучшения условий контактирования пропана с сырьем установлены девять жалюзийных тарелок 1. Между ними имеются коллекторы из перфорированных труб для ввода и распределения сырья 2 и жидкого пропана 3. Образующаяся при экстракции тяжелая фаза (раствор асфальтовых веществ в пропане) опускается вниз, а легкая фаза (раствор деасфальтизата в пропане) поднимается вверх.
Вверхней и нижней частях колонны (20 % объема) расположены отстойные зоны. В верхней отстойной зоне имеются шесть встроенных пароподогревателей для поддержания температурного градиента процесса и две тарелки для укрупнения мельчайших капелек примесей асфальтенов, выделяющихся при нагреве раствора масла.
Жалюзийная тарелка (рис. 70) состоит из секций, которые опираются на каркас из пластин-балок 3 и распорных стержней 4. Секция состоит из наклонно установленных
77
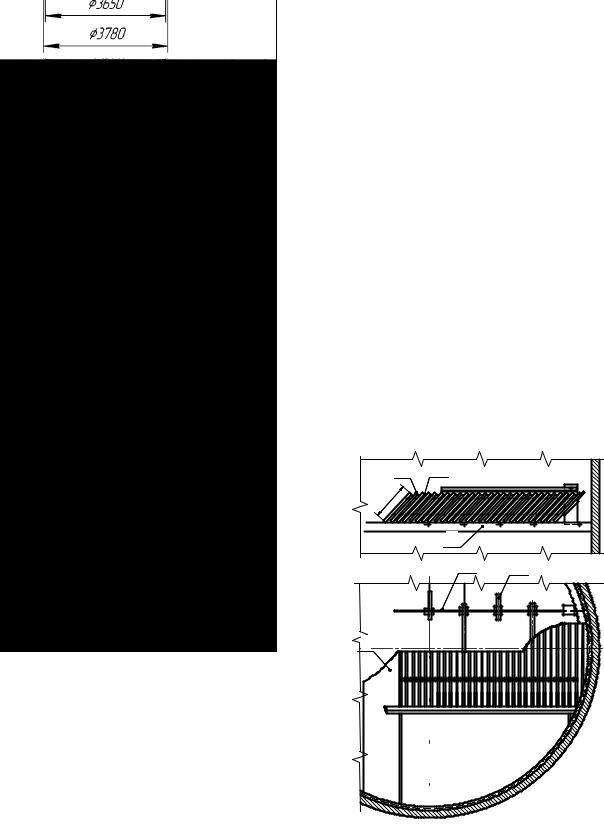
1 2
3 5 3
3
3 4
1
|
|
|
|
|
|
|
|
|
|
|
|
|
|
|
|
|
|
|
|
|
|
|
|
|
|
|
|
|
|
|
|
|
|
|
|
|
|
|
|
|
|
|
|
|
|
|
|
|
|
|
|
|
|
|
|
|
|
|
|
|
|
|
|
|
|
|
|
|
|
|
|
|
|
|
|
|
|
|
|
|
|
|
|
|
|
|
|
|
|
|
|
|
|
|
|
|
|
|
|
|
|
|
|
|
|
|
|
|
|
|
|
|
|
|
|
|
|
|
|
|
|
|
|
|
|
|
|
|
|
|
|
|
|
|
|
|
|
|
|
|
|
|
|
|
|
|
|
|
|
|
|
|
|
|
|
|
|
|
|
|
|
|
|
|
|
|
|
|
|
|
|
|
|
|
|
|
|
|
|
|
|
|
|
|
|
|
|
|
|
|
|
|
|
|
|
|
|
|
|
|
|
|
|
|
|
|
|
|
|
|
|
|
|
|
|
|
|
|
|
|
|
|
|
|
|
|
|
|
|
|
|
|
|
|
|
|
|
|
|
|
|
|
|
|
|
|
|
|
|
|
|
|
|
|
|
|
|
|
|
|
|
|
|
|
|
|
|
|
|
|
|
|
|
|
|
|
|
|
|
|
|
|
|
|
|
|
|
|
|
|
|
|
|
|
|
|
|
|
|
|
|
|
|
|
|
|
|
|
|
|
|
|
|
|
|
|
|
|
|
|
|
|
|
|
|
|
|
|
|
|
|
|
|
|
|
|
|
|
|
|
|
|
|
|
|
|
|
|
|
|
|
|
|
|
|
|
|
|
|
|
|
|
|
|
|
|
|
|
|
|
|
Рис. 69. Экстракционная колонна: 1 – та- |
Рис. 70. Жалюзийная тарелка: 1 – пла- |
|||||||||||||||||||||||||||||
релки жалюзийные; 2 – штуцеры для по- |
стины наклонные (жалюзи); 2 – ребро |
|||||||||||||||||||||||||||||
дачи сырья (гудрона); 3 – штуцеры для |
дистанционное; 3 – пластины-балки; 4 – |
|||||||||||||||||||||||||||||
подачи пропана |
|
|
|
|
стержни распорные |
78
пластин (жалюзи) 1 и дистанционных ребер 2. Сверху жалюзи прижимаются специальными планками.
Корпус колонны выполнен из стали 09Г2С или 16ГС, расчетное давление в колонне 50 кг/см2, расчетная температура 100 °С.
Подача жидкого пропана в экстракционную колонну осуществляется двухступенчатым центробежным насосом Н-500-420СГ с торцевым уплотнением (подача 420 м3/ч, напор 5 МПа). Подача газообразного пропана проводится двухступенчатым компрессором 305ГП20/18 (подача 1200 м3/ч, давление после первой ступени сжатия 3,6 кгс/см2, мощность двигателя 200 кВт).
3.2. Фенольная очистка масел
Фенольная (селективная) очистка проводится как для дистиллятных, так и для остаточных масляных фракций. Целью очистки является окончательное удаление из сырья смолисто-асфальтеновых соединений, но главным образом удаление низкоиндексных полициклических ароматических углеводородов с короткими боковыми цепями.
Врезультате улучшается цвет масла, повышается индекс вязкости, снижается коксуемость и уменьшается содержание сернистых примесей. Наиболее распространенными селективными растворителями являются фенол и фурфурол. В последние годы найден более эффективный растворитель N-метилпирролидон.
При взаимодействии с масляной фракцией эти растворители хорошо растворяют нежелательные примеси и относительно плохо – ценные углеводороды (прямая экстракция). При этом образуется две фазы: верхняя фаза – рафинатный раствор, который содержит очищенное масло с небольшим количеством растворителя, нижняя фаза – экстрактный раствор, который содержит основную массу растворителя и нежелательные примеси. Соотношение растворителя и масла должно быть (1,5…2,2) : 1 для дистиллятных масел и (4…4,5) : 1 для остаточных масел. Чрезмерное увеличение этого соотношения приводит к уменьшению концентрации экстрактного раствора и переходу в него части ценных углеводородов. При этом степень очистки возрастает, но уменьшается выход рафинатного раствора. Чрезмерное уменьшение этого соотношения приводит к обратному эффекту.
Большое значение имеет также температурный режим очистки. С повышением температуры растворяющая способность растворителей возрастает, но избирательность снижается, и при критической температуре получается однородный раствор. Поэтому к растворителям предъявляется следующее требование: критическая температура растворителя должна быть достаточно высокой, чтобы можно было вести очистку в интервале сравнительно высоких температур 80–150 °С. Это вызвано тем, что при понижении температуры возрастает вязкость системы и ухудшаются условия массообмена.
Процесс экстракции фенолом проводят в колонных аппаратах. Фенол, который имеет большую плотность, чем сырье, подают в колонну сверху, а сырье – снизу.
Впроцессе противоточного контактирования сырье освобождается от нежелательных примесей. По мере подъема рафината его критическая температура повышается, поэтому для улучшения процесса вверху колонны поддерживают более высокую температуру, чем в нижней части в месте ввода сырья. Разность этих температур, зависящая как от свойств растворителя, так и от характеристики сырья, называется температурным градиентом экстракции.
79
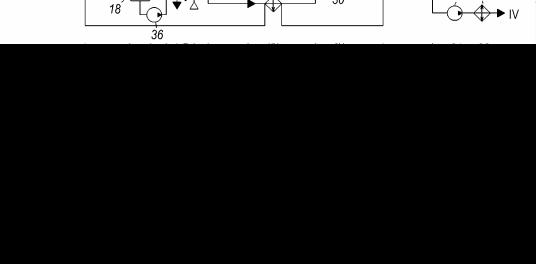
Фурфурол имеет перед фенолом ряд преимуществ. Он менее токсичен, дает больший выход рафината и благодаря меньшей температуре кипения и теплоте испарения более экономичен. Но он более дорог и не обеспечивает достаточной степени очистки остаточных масел. Кроме того, он хуже растворяет смолы, и поэтому получаемое масло имеет более темный цвет.
На современных предприятиях фенол и фурфурол заменяют N-метилпирролидоном.
Принципиальная технологическая схема
Установка селективной очистки масел фенолом (рис. 71) работает следующим образом.
Сырье насосом 13 через теплообменник 15 и пароподогреватель 3 с температурой 110–115 °С подается в верх абсорбера 2. В нижнюю часть абсорбера вводится смесь паров воды и фенола. Пары фенола хорошо растворяются в масле, а пары воды не конденсируются в горячем масле и попадают в холодильник 1 и далее в канализацию. Масло с низа абсорбера 2 насосом 14 через холодильник 16 подается в среднюю часть экстракционной колонны 5. В верхнюю часть этой колонны поступает безводный расплав фенола, а в нижнюю – фенольная вода с целью выделения из экстракта вторичного рафината. Таким образом, фенольная вода является антирастворителем.
Рис. 71. Принципиальная технологическая схема селективной очистки масел фенолом: 1, 4, 7, 16, 17, 20, 30, 35 – холодильники; 2, 5, 6, 10 – 12, 22 – колонны; 3, 21 – пароподогреватели; 8,
18 – емкости; 9, 13, 14, 19, 24, 25, 29, 33, 34, 36 – насосы; 15, 26, 27 – теплообменники; 23, 31,
32 – печи; 28 – кипятильник. Потоки: I – сырье; II – фенол; III – рафинат; IV – экстракт; V – во-
дяной пар; VI – вода
Температура верха колонны 58–88 °С, соотношение фенола и сырья составляет (1,5…2,2) : 1 для дистиллятного сырья и (4…4,5) : 1 для остаточного.
Регенерацию фенола из рафинатного раствора ведут в две стадии. Рафинатный раствор с верха колонны 5 насосом 25 через теплообменник 27 и печь 23 с температурой 270–290 °С подается в колонну 6, где испаряется основная часть фенола. С низа колонны 6 раствор перетекает в колонну 22, где окончательно отпаривается от остатков фенола острым водяным паром. Рафинат отводится с низа колонны 22 насосом 24 через теплообменник 27 и холодильник 30 с установки.
80