
Основное технологическое оборудование нефтеперерабатывающих заводо
..pdfРаствор экстракта освобождается от фенола в три ступени. Он забирается насосом 19 с низа колонны 5. Часть его через холодильник 20 возвращается в низ колонны для поддержания требуемого температурного режима низа колонны. Другая часть через теплообменник 26 вводится в колонну 10. Здесь отгоняется азеотропная смесь паров воды
ифенола (температура кипения азеотропа 99,6 °С при атмосферном давлении, содержании фенола в азеотропной смеси составляет 9,2 %). Подогрев колонны 10 осуществляется кипятильником 28.
Из колонны 10 осушенный экстрактный раствор насосом 29 через трубчатую печь 31 с температурой 260–280 °С подается в колонну 11. Здесь отгоняется большая часть сухого фенола. Подогрев низа колонны 11 проводят горячей струей при помощи насоса 33 и печи 32. Температура горячей струи 350–360 °С. С низа колонны 11 экстракт со следами фенола поступает в колонну 12, где окончательно отпаривается острым водяным паром.
Из колонн 6 и 11 уходят пары сухого фенола, которые конденсируются и охлаждаются в теплообменниках 15, 26 и холодильнике 17, затем поступают в емкость сухого фенола 18. Отсюда он подается насосом 36 через пароподогреватель 21 на орошение колонны 5. С верха колонн 22 и 12 уходит смесь паров фенола и воды, ее конденсируют в холодильнике-конденсаторе 7, собирают в емкости 8, откуда насосом 9 подают в середину колонны 10. Несконденсированные пары из емкости 8 и азеотропная смесь из колонны 10 поступают частично в холодильник 4 для конденсации и далее в виде фенольной воды в низ колонны 5 в качестве антирастворителя. Другая часть паров поступает в низ абсорбера 2 для улавливания фенола. Для уменьшения испарения масла
иустранения так называемого замасливания фенола колонны 6, 12 и 22 орошаются безводным фенолом. Колонна 10 орошается фенольной водой.
Основное технологическое оборудование
Основным оборудованием данной установки являются колонны. Конструкции экстракционных колонн отличаются простотой и поэтому здесь подробно не рассматриваются.
Они представляют собой вертикальные аппараты внутренним диаметром до 5 м и высотой около 40 м. В средней части располагаются слои насадки из колец Рашига или пакетная насадка из мелкой металлической сетки. В верхней и нижней частях колонн расположены отстойные зоны. Ввод сырьевых потоков осуществляется через специальные распределительные маточники.
Колонны для отгонки растворителя снабжены 12–20 тарелками с S-образными элементами.
3.3. Депарафинизация масел
Для получения масел, пригодных к применению при температурах от минус 15 до минус 30 ºС и более низких, рафинаты селективной очистки подвергают депарафинизации. Это осуществляется путем кристаллизации твердых углеводородов при охлаждении раствора рафината в специально подобранном растворителе.
Рафинаты селективной очистки дистиллятных фракций содержат, в основном, твердые высокомолекулярные алканы (парафины) нормального или слаборазветвленного строения (С16 и выше). При охлаждении они кристаллизуются в виде крупных
81
хорошо фильтруемых кристаллов правильной формы. Получаемый осадок называется гачем.
Рафинаты селективной очистки остаточных масляных фракций содержат, в основном, твердые высокомолекулярные нафтеновые и ароматические углеводороды с длинными боковыми цепями. Они при охлаждении осаждаются в виде мелких игольчатых кристаллов, которые трудно фильтруются. Образующийся осадок называется петролатумом.
Одной из важнейших задач депарафинизации является получение возможно более крупных и правильных по форме кристаллов, которые легче фильтруются и промываются от остатков масла. На рост кристаллов влияют следующие основные факторы:
1.Вязкость раствора. Высокая вязкость препятствует росту кристаллов и способствует образованию большего числа мелких кристаллов.
2.Скорость охлаждения раствора. При большой скорости кристаллы не успевают вырасти и вместо малого количества крупных кристаллов образуется большое число мелких кристаллов.
3.Концентрация твердых углеводородов в растворе. Слишком большое разбавление сырья растворителем замедляет рост кристаллов, так как при этом увеличивается длина пути молекул твердых углеводородов до встречи друг с другом, а следовательно,
ивремя образования и роста кристаллов. Однако недостаточное разбавление также нежелательно, так как вызывает увеличение вязкости жидкой фазы и торможение процессов диффузии. Большое число мельчайших центров кристаллизации, содержащихся в исходном сырье, также способствует образованию мелких кристаллов. Для уничтожения этих центров сырье перед началом процесса депарафинизации подогревают до температуры, которая на 15–20 ºС выше температуры плавления этих кристаллов.
Селективные растворители должны хорошо растворять ценные углеводороды сырья, но не растворять твердые углеводороды. Кроме того, к этим растворителям предъявляют и специфические требования. Они должны допускать высокие скорости охлаждения и фильтрования раствора масла от осадков и иметь минимальный температурный эффект депарафинизации (ТЭД). ТЭД – это разность между требуемой температурой застывания депарафинированного масла и требуемой температурой охлаждения раствора, которая обеспечивает достижение заданной температуры застывания. Минимальный ТЭД позволяет уменьшить расходы на переохлаждение растворов, а высокие скорости охлаждения и фильтрования позволяют уменьшить размеры аппаратов – кристаллизаторов и фильтров.
В качестве растворителей могут применяться легкий бензин, сжиженный пропан, дихлорэтан и различные кетоны. В настоящее время наиболее широко используются
следующие кетоны: ацетон СО(СН3)2, метилэтилкетон (МЭК) (СН3)СО(С2Н5) и др. Кетоны практически не растворяют твердые углеводороды, однако плохо раство-
ряют и масло, т.е. обладают высокой селективностью, но низкой растворяющей способностью. Для повышения растворяющей способности по отношению к маслу к кетонам добавляют толуол или его смесь с бензолом. Величина ТЭД смеси кетонов с толуолом может колебаться от 10 до 0 ºС (чем больше в смеси толуола, тем больше ТЭД).
Изменение состава растворителя, т.е. соотношения толуола и МЭКа, позволяет варьировать его свойства. Увеличение содержания кетонов обеспечивает понижение температуры застывания масла, но его выход при этом снижается, и наоборот, увеличе-
82
ние содержания толуола повышает температуру застывания, но способствует увеличению выхода масла. Обычно парный растворитель содержит от 25 до 50 % МЭКа.
Важным параметром является также кратность разбавления сырья. Чем больше вязкость сырья, тем больше должна быть кратность разбавления. Для маловязких дистиллятных масел она составляет 1,5 : 1, а для вязких остаточных масел 4,5 : 1.
Более перспективными растворителями являются высокомолекулярные кетоны, например метилизобутилкетон. Они одновременно имеют высокую селективность и растворяющую способность, поэтому не нуждаются в добавках толуола.
Принципиальная технологическая схема
Установка депарафинизации масел (рис. 72) состоит из двух отделений: отделения кристаллизации и отделения регенерации растворителя.
Вотделении кристаллизации (рис. 72, а) исходное сырье (рафинат селективной очистки) насосом 1 через подогреватель 2 и холодильник 3 подается в регенеративный кристаллизатор 4, где охлаждается раствором депарафинированного масла. Подогрев сырья в подогревателе 2 до 60–80 ºС обеспечивает полное расплавление мелких студнеобразных кристаллов парафинов. В холодильнике 3 сырье охлаждают, не допуская его помутнения. Далее сырье смешивают с охлажденным влажным растворителем
ициркулирующим фильтратом со второй ступени фильтрования и подают в кристаллизатор 5, где оно охлаждается жидким аммиаком или пропаном, после чего смешивается с определенными порциями охлажденных влажного и сухого растворителей.
При охлаждении выпадают в осадок кристаллы твердых углеводородов, далее полученная суспензия направляется в емкость первой ступени фильтрования 6, откуда самотеком идет в барабанный фильтр первой ступени 7. Здесь кристаллы осаждаются в виде лепешки на барабане фильтра, а фильтрат просачивается через фильтрующую ткань внутрь барабана под действием вакуума и собирается в емкости депарафинированного масла 17. Далее фильтрат прокачивается через кристаллизаторы 4, 12 и теплообменники 10, 11 и 15, где нагревается за счет охлажденного сырья, сухого и влажного растворителей, и направляется в отделение регенерации растворителя.
Осадок гача (петролатума) на барабане фильтра 7 промывается от остатка масла сухим охлажденным растворителем, и образующийся промывной фильтрат собирается в емкости некондиционного масла 20. Срезанный ножом осадок шнеком выгружается в емкость 18, куда также подают порцию сухого охлажденного растворителя.
Из емкости 18 суспензия насосом 19 перекачивается в емкость 8, откуда самотеком перетекает в фильтр второй ступени 9. Образующийся фильтрат собирается в емкости некондиционного масла 20, а осадок промывается охлажденным сухим растворителем от остатков масла. Некондиционное масло насосом 21 возвращают к потоку сырья перед кристаллизатором 5.
Суспензия гача собирается в емкости 23 и насосом 22 через кристаллизатор 14 направляется в отделение регенерации растворителя. В ней содержатся кристаллы льда, попавшие из влажного растворителя. На современных установках имеются также трехступенчатые схемы фильтрования.
Вотделении регенерации (рис. 72, б) отгон растворителя от депарафинированного масла проводится в четыре ступени. Для этого раствор масла проходит теплообменники 17–20 и пароподогреватель 22, а затем последовательно колонны 24, 4, 7 и 28.
83
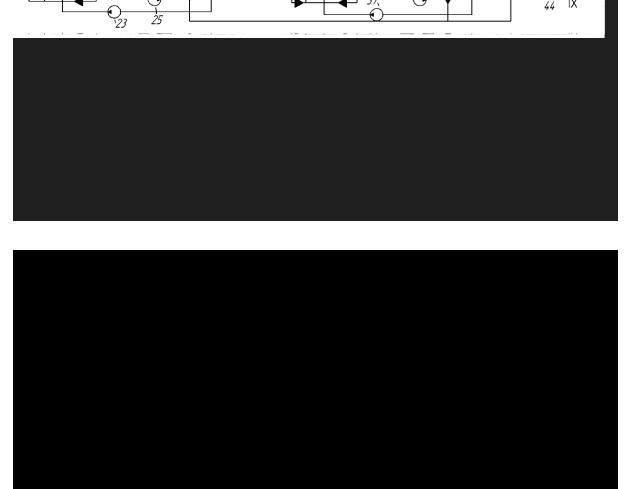
В низ колонны 28 подается острый водяной пар. Депарафинированное масло с низа колонны 28 через теплообменник 19 и холодильник 1 отводится с установки. С верха колонн 4, 24 и 7 уходят пары сухого растворителя, которые конденсируются, охлаждаются и поступают в емкость сухого растворителя 3, откуда насосом 2 сухой растворитель откачивается в отделение кристаллизации.
а
б
Рис. 72. Принципиальная технологическая схема установки депарафинизации масел: а – отделение кристаллизации: 1, 16, 19, 21, 22 – насосы; 2 – пароподогреватель; 3 – холодильник; 4, 5, 12 – 15 – кристаллизаторы; 6, 8, 17, 18, 20, 23 – емкости; 7, 9 – фильтры; 10, 11, 15 – теплообменники; б – отделение регенерации растворителя: 1, 5, 10, 15, 18, 21, 27, 31, 34, 40 – холодиль-
ники; 2, 8, 14, 23, 25, 37, 38, 44 – насосы; 3, 9, 43 – емкости; 4, 7, 11, 13, 16, 24, 28, 36, 41 – ко-
лонны; 6, 12, 22, 26, 29, 35, 39, 42 – пароподогреватели; 17 – 20, 30, 32, 33 – теплообменники. Потоки: I – сырье, II – влажный растворитель; III – сухой растворитель; IV – раствор депарафинированного масла; V – раствор гача; VI – аммиак; VII – депарафинированное масло; VIII – гач; IX – вода; X – водяной пар
Отгон растворителя из суспензии гача также происходит в четыре ступени в колоннах 11, 36, 13 и 41. С верха колонн 11, 36 и 13 уходят пары влажного растворителя, которые конденсируются, охлаждаются и собираются в емкости 9, откуда насосом 8 возвращаются в отделение кристаллизации. Увлажнение растворителя вызвано присутствием в гаче кристаллов льда.
84
С верха колонн 28 и 41 уходит смесь паров растворителя и водяного пара. После охлаждения и конденсации эта смесь поступает в емкость 43, где происходит расслаивание жидкости. Верхний слой влажного растворителя (содержание воды 0,6 – 0,8 %) насосом 14 перекачивается в емкость 9. Нижний водный слой, содержащий до 15 % растворенного МЭКа, насосом 44 подается в кетоновую колонну 16.
В низ этой колонны подают острый пар. С верха этой колонны отгоняется низкокипящая азеотропная смесь, обогащенная МЭКом, которая конденсируется в холодильнике 15 и поступает обратно в емкость 43, где происходит ее расслаивание. Вода из низа колонны 16 отводится в канализацию.
Основное технологическое оборудование
К основному оборудованию установок депарафинизации можно отнести кристаллизаторы и фильтры.
Кристаллизаторы. На установках депарафинизации эксплуатируют различные типы кристаллизаторов, отличающихся конструктивным оформлением, площадью поверхности охлаждения, типом привода скребков. Площадь поверхности теплообмена составляет от 70 до 100 м2. В настоящее время разрабатываются кристаллизаторы с площадью поверхности до 340 м2.
Рассмотрим два типа кристаллизаторов: «труба в трубе» и кожухотрубчатый. В аппаратах типа «труба в трубе» по внутренним трубам движется охлаждаемый раствор масла, из которого выкристаллизовываются твердые углеводороды, а по межтрубному пространству противотоком движется охлаждающая среда (фильтрат депарафинированного масла). В кожухотрубчатом кристаллизаторе по трубам также движется охлаждаемый раствор масла, а в межтрубное пространство подается испаряющийся хладагент с низкой температурой кипения (аммиак, пропан, этан).
Как правило, кристаллизаторы «труба в трубе» используют на первой ступени (в качестве регенеративных). В них за счет противоточного движения раствора и хладагента обеспечиваются более мягкие условия охлаждения, что очень важно на начальных стадиях кристаллизации. В кожухотрубчатых кристаллизаторах режим охлаждения более жесткий, поэтому их целесообразно использовать на заключительных стадиях процесса, когда допускаются большие скорости охлаждения.
Кристаллизатор типа «труба в трубе» (рис. 73) в зависимости от площади поверхности охлаждения включает от 10 до 48 элементов «труба в трубе» (поверхность охлаждения от 70 до 340 м2). Элементы укреплены на металлоконструкции, состоящей из стоек с горизонтальными связями из швеллеров и уголков.
Элемент «труба в трубе» (рис. 74) состоит из наружной трубы 1 диаметром 219×8 мм и внутренней трубы 2 диаметром 168×10 мм. Общая длина элемента 13,8 м.
Во внутренней трубе для удаления оседающего на стенке парафина устанавливают полый вал 3 со скребками 4. Из-за значительной длины трубы вал выполняют из отдельных частей длиной по 2,7 м. Отдельное звено вала представляет собой трубу 3 с вваренными в нее цилиндрическими втулками для установки скребков 4. Звенья вала соединяют вставным стержнем 9 и болтами 8.
Скребки вставлены в пазы «пальцев» 5 и могут быть приварены к ним. «Пальцы» свободно входят в цилиндрические втулки вала и распираются пружинами 6. Это создает возможность перемещения скребка в радиальном направлении. Длина скребка от
85
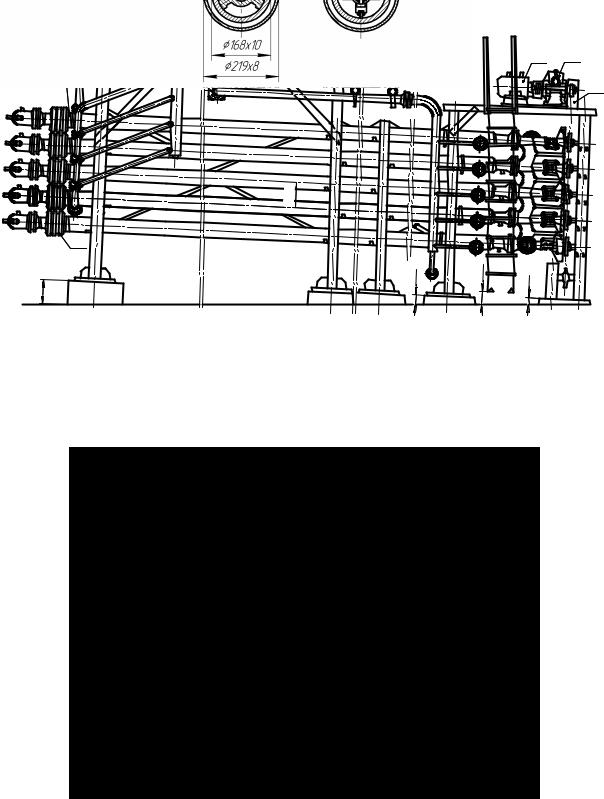
2
3 4
1
5
0 8 3
6
|
0 |
0 |
|
|
0 |
0 |
|
|
4 |
2 |
|
0 |
1 |
|
9 |
0 |
|
|
|
6 |
|
|
|
Рис. 73. Кристаллизатор типа «труба в трубе»: 1 – секция кристаллизатора; 2 – емкость хладагента; 3 – электродвигатель; 4 – редуктор; 5 – передача цепная; 6 – волнистый (линзовый) компенсатор
Рис. 74. Элемент секции кристаллизатора: 1 – труба наружная; 2 – корпус внутренней трубы; 3 – вал; 4 – скребок; 5 – «палец»; 6 – пружина; 7 – подшипник скольжения; 8 – болт; 9 – стержень
86
545 до 600 мм. Скребки на валу располагаются попарно под углом 90º относительно друг друга. Каждый скребок имеет три подпружиненных опоры, а каждое скребковое устройство – 24 пары скребков.
Вал устанавливают внутри трубы в подшипниках скольжения 7. Передние концы валов, выходящие через двойники, уплотняются сальниковыми устройствами. Разность тепловых расширений внутренних и наружных труб воспринимается волнистыми (линзовыми) компенсаторами. Привод валов осуществляется от мотор-редуктора через ведущую звездочку. Ведомые звездочки крепятся на приводных валах скребковых устройств. Для передачи крутящего момента используется двухрядная цепь. Передача крутящего момента от ведомой звездочки к скребковому устройству каждой секции осуществляется через два болта М12, соединенных со ступицей вала. Общая длина вала 13 125 мм, частота вращения 25–32 об/мин.
Наружные трубы также соединены при помощи штампованных переходников в общий змеевик. Трубы изготовлены из стали 09Г2С. Масса кристаллизаторов состав-
ляет 18,1–24,6 т.
Вне корпуса аппарата в каком-либо звене привода (шестерне, муфте) предусматривают предохранительный штифт, который срезается при чрезмерных усилиях, возникающих при заедании или других неполадках в скребковом устройстве. В результате отключается скребковое устройство одной трубы, а остальные продолжают работать.
Кожухотрубчатый кристаллизатор с поверхностью охлаждения 90 м2 (рис. 75) состоит из двух рядов горизонтальных кожухотрубчатых секций, над которыми расположен аккумулятор испаряющегося хладагента (аммиака или пропана) 2.
В каждом ряду размещены одна над другой две секции 1, соединенные переточными устройствами. В каждой секции установлено семь труб диаметром 168×8 мм со встроенными скребковыми устройствами. Внутри кожуха диаметром 800 мм размещены шесть труб по окружности диаметром 580 мм и одна в центре. Все трубы закрепляются в трубных решетках. Трубы соединяются между собой передними и задними переходниками на фланцевых соединениях, образуя непрерывный змеевик. Кожух и трубы изготовлены из стали 09Г2С. Масса аппаратов достигает 21,2–21,7 т .
Каждая секция имеет автономный привод от мотор-редуктора (рис. 76). Скребковое устройство получает вращение через шестеренчатую передачу, уплот-
нение валов осуществляется с помощью сальниковых устройств.
Барабанные вакуум-фильтры. В эксплуатации находятся фильтры различной конструкции с поверхностью фильтрования 50–80 м2, диаметром барабана 3000– 3450 мм, длиной барабана 5300–10100 мм и регулируемой частотой вращения (0,3–1,3 об/мин). Схема одного из таких барабанных вакуум-фильтров приведена на рис. 77.
Фильтрующая поверхность размещена на горизонтальном барабане 3, который медленно вращается на двух цапфах от привода 1. На боковой поверхности барабана крепится металлическая сетка и фильтровальная ткань 4, обмотанная проволокой в направлении по спирали.
Изнутри по образующим фильтрующая поверхность разделена продольными перегородками на отдельные секции в количестве от 12 до 32 штук. Каждая из секций соединена отводными трубками 5 с вращающимся диском 7, укрепленным на цапфе. Число отверстий в диске равно числу секций барабана. К диску прижата пружинами неподвижная распределительная головка со сменным диском 8.
87
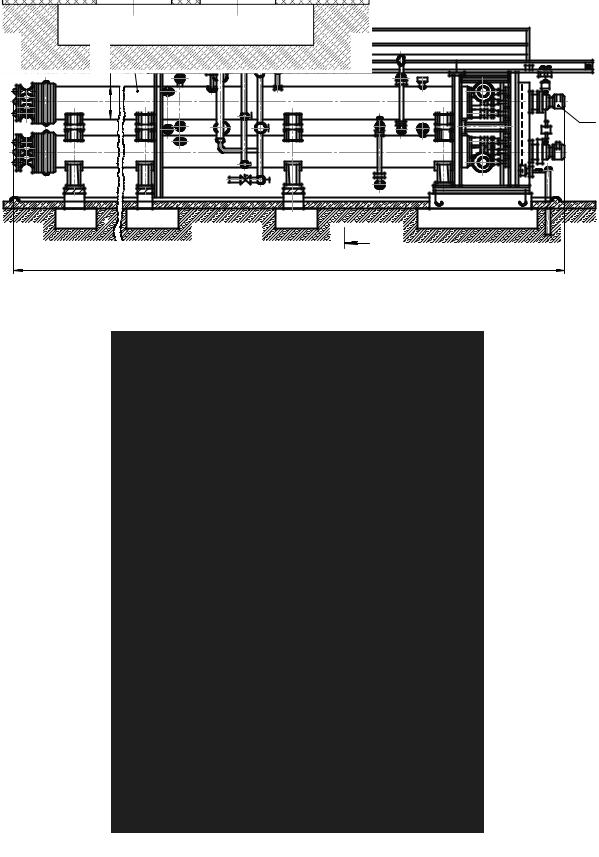
|
|
2 |
À |
|
|
|
|
8 |
1 |
|
|
x8800 |
|
|
|
|
|
|
|
|
|
|
3 |
|
15100 |
|
À |
Рис. 75. Кристаллизатор кожухотрубчатый: 1 – секция кристаллизатора; 2 – емкость испаряющегося хладагента; 3 – мотор-редуктор
88
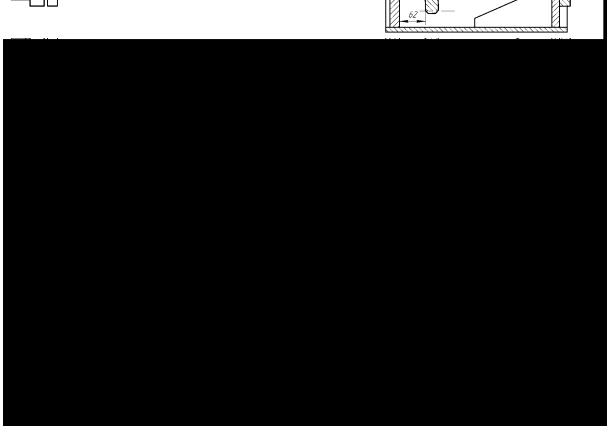
Рис. 76. Узел привода кожухотрубчатого кристаллизатора: 1 – крышка; 2 – шестерня; 3 – муфта привода; 4 – палец; 5 – сухарь; 6 – втулка распорная; 7 – вал; 8 – крышка сальника; 9 – кольцо сальника; 10 – кольцо; 11 – пружина; 12 – втулка; 13 – корпус подшипника; 14 – шайба; 15 – колесо зубчатое; 16 – штифт; 17 – ступица; 18 – планка стопорная
Распределительная головка разделена на три камеры, соответствующие основным стадиям процесса: фильтрованию, промывке и продувке. Каждая камера имеет штуцер и через щель в сменном диске 8 распределительной головки сообщается с соответствующим участком фильтрующей поверхности. Нижняя часть барабана погружена в суспензию, которая постоянно подается в корыто фильтра.
Над барабаном установлен коллектор 6 для подачи промывной жидкости. Сбоку размещен нож для срезания осадка с поверхности фильтра и шнек для удаления осадка из фильтра.
Особенностью барабанных вакуум-фильтров, используемых для депарафинизации, является полная герметизация кожуха, а также отсутствие в корыте качающейся мешалки для перемешивания суспензии. Внутри кожуха для исключения возможности проникновения воздуха поддерживается небольшое избыточное давление, создаваемое инертным газом (азотом). Выгрузка осадка из фильтра осуществляется при помощи специального шнека.
На рис. 78 представлен сборочный чертеж барабана.
89
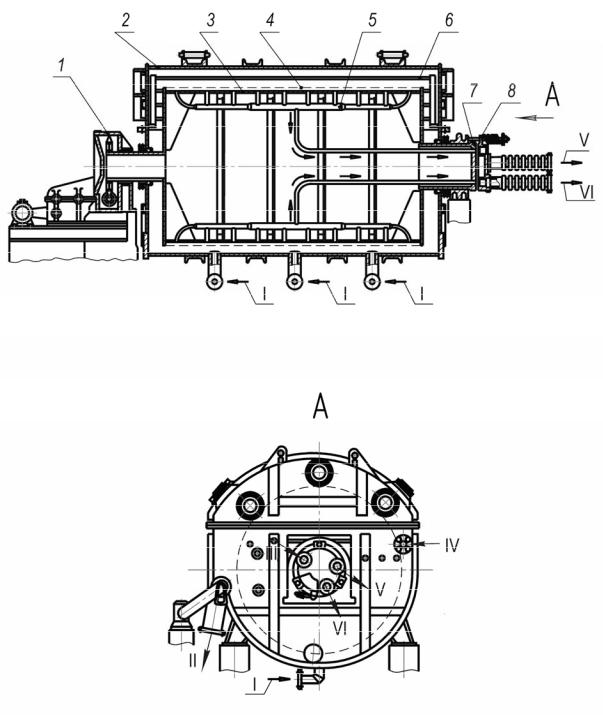
Рис. 77. Барабанный вакуум-фильтр с наружной фильтрующей поверхностью: 1 – привод; 2 – корпус; 3 – барабан; 4 – фильтровальная ткань; 5 – отводные трубки; 6 – коллектор для подачи промывной жидкости; 7 – вращающийся диск; 8 – сменный диск распределительной головки. Потоки: I – суспензия; II – осадок; III – газ для отдувки осадка; IV – инертный газ; V – промывной фильтрат; VI – фильтрат
90