
2527
.pdfКонвейерный транспорт применяют в протяженных тоннелях. В тоннеле для удаления породы от забоя устанавливают систему ленточных, скребковых или пластинчатых конвейеров шириной до 1,2 м и производительностью 600 800 т/ч. Этот вид транспорта имеет ряд недостатков: необходимость использования дробилок, бункеров и перегружателей, дополнительного вида транспорта для доставки оборудования и материалов, регулярного наращивания конвейеров, малую надежность. Вместе с тем он обладает высокой производительностью. В практике тоннелестроения известны случаи его успешного применения (в США, Японии, Швейцарии), когда скорости проходки достигали 300 м в месяц и более.
Г л а в а 6
ВРЕМЕННАЯ КРЕПЬ ТОННЕЛЕЙ
Временная крепь необходима для поддержания выработки в устойчивом состоянии, предохранения от возможных вывалов породы из кровли и стен тоннеля и обеспечения безопасности работ в забое до момента возведения постоянной обделки.
При сооружении тоннеля в крепких монолитных породах с f >12 временную крепь можно не устанавливать. В остальных случаях временная крепь обязательна. В качестве временной крепи в настоящее время используют анкеры, набрызг-бетон, металлические арки и рамы, как исключение – деревянные рамы.
Анкерную крепь применяют в трещиноватых скальных породах средней устойчивости и выше с f 4. Крепь из набрызгбетона выполняют в виде самостоятельной конструкции в скальных трещиноватых средней устойчивости и устойчивых породах, не проявляющих большого горного давления, с f >4. В скальных трещиноватых и выветрелых породах, проявляющих большое горное давление, используют набрызг-бетон, армированный металлической сеткой в сочетании с анкерами. В слабоустойчивых породах с f 2 набрызг-бетон применяют совместно с арками. Арочную и рамную металлическую крепь ставят в сильнотрещи-
258
новатых скальных и слабоустойчивых полускальных породах, а также в зонах с тектоническими нарушениями.
6.1.АНКЕРНАЯ КРЕПЬ
Впрактике тоннелестроения широкое распространение получила анкерная крепь. Она является крепью бесподпорного типа
ипо сравнению с обычными конструкциями имеет следующие преимущества: повышает безопасность ведения горных работ, так как анкеры лучше любой другой крепи противостоят взрывным работам: позволяет почти полностью механизировать процесс крепления; требует небольшого расхода крепежных материалов и затрат труда как на доставку, так и на установку крепи; позволяет уменьшить необходимое сечение выработки и ее аэро-
динамическое сопротивление при вентиляции на 18 25 %.
В зависимости от геологических условий анкерная крепь выполняет свою работу по сохранению выработки различно. Эффект от применения анкерной крепи проявляется в том, что анкеры, заглубленные в ненарушенную часть породного массива, с одной стороны, как бы подвешивают к ней породу в зоне возможного обрушения, предотвращая тем самым вывалы отдельных блоков, с другой – сшивают отдельные породные блоки, омоноличивая нарушенную зону породного массива и превращая его в несущую конструкцию. В крепких трещиноватых породах анкеры выполняют роль ограждающей конструкции, предохраняющей выработку от отдельных случайных вывалов (рис. 6.1).
Совершенно очевидно, что для включения анкерной крепи в работу по предотвращению деформаций контура выработки необходимо устанавливать ее сразу же, вслед за продвижением забоя.
По конструкции различают металлические клинощелевые и распорные, железобетонные и сталеполимерные анкеры.
Наиболее просты по конструкции и вместе с тем достаточно надежны клинощелевые анкеры (рис. 6.2). Комплект анкера состоит из стержня с резьбой и прорезью на концах, клина, опорной шайбы и гайки. Материал анкера – сталь 3. Диаметр стержня и замка 25 мм, диаметр шпура 30 32 мм. При установке в обыч-
259

Рис. 6.1. Схемы применения анкерной крепи: а – подвешивающая; б – сшивающая; в – ограждающая
ные шпуры диаметром 40 42 мм диаметр замка необходимо увеличивать до 36 мм. Для экономии металла стержни таких анкеров изготовляют из стали диаметром 25 мм и стыкуют их с замком с помощью сваркиилинарезьбе.
Клинощелевые анкеры в породах крепостью f = 6 10 обеспечивают несущую способность (по данным исследования): при диаметре замка 25 мм – 90 кН и при диаметре замка 36 мм – 60 кН. Но в слабых породах, а также в очень крепких окварцованных породах клиновые анкеры не
Рис. 6.2. Конструкции клинощелевых анкеров: а – сплошной; б – составной; 1 – гайка; 2 – опорная шайба; 3 – хвостовик анкера (под насадку при установке); 4 – стержень; 5 – прорезь; 6 – клин; 7 – сварной шов
260
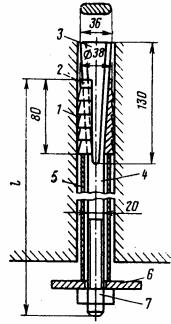
|
|
|
применяют, так как в этих условиях не |
|||
|
|
|
достигается достаточной расклинки зам- |
|||
|
|
|
ков, и анкеры могут проскальзывать. |
|||
|
|
|
В породах |
с f 5 |
(обычно при |
|
|
|
|
f = 3 4) применяют распорные анкеры, |
|||
|
|
|
которые в отличие от клиновых анкеров |
|||
|
|
|
имеют замок более сложной конструкции. |
|||
|
|
|
Замок имеет вид распорной гильзы или |
|||
|
|
|
муфты, расклинивающейся в шпуре при |
|||
|
|
|
натяжении или вращении стержня (рис. |
|||
|
|
|
6.3). Распорные анкеры изготовляют толь- |
|||
|
|
|
ко в заводских условиях. Прочность их за- |
|||
|
|
|
крепления в массиве сравнительно невели- |
|||
|
|
|
ка и составляет 30 40 кН. Из-за сложно- |
|||
Рис. 6.3. Кон- |
сти изготовления замков и установки рас- |
|||||
порные анкеры применяют редко. |
||||||
струкция распорного |
||||||
анкера |
СКШ: |
1 – |
Наиболее широко распространены в |
|||
проволочное кольцо; |
практике тоннелестроения |
железобетон- |
||||
2 – распорная раз- |
ные анкеры в диапазоне крепости пород |
|||||
резная |
муфта; |
3 – |
f = 3 12 (рис. 6.4). Они состоят из арма- |
|||
клин; |
4 – анкер; |
5 – |
турных стержней периодического профиля |
|||
установочная трубка; |
диаметром 25 мм, которые устанавлива- |
|||||
6 – шайба; 7 – гайки |
||||||
|
|
|
ются в шпуры диаметром 42 46 мм, |
|||
|
|
|
предварительно |
заполненные цементно- |
песчаным раствором. Раствор состоит из глиноземистого цемента и песка в соотношении 1 1 по массе и воды (при водоцементном отношении 0,3 0,4) с добавкой 5 6 % хлористого кальция (от массы цемента), вводимого для ускорения твердения раствора и увеличения несущей способности анкера. Железобетонные анкеры обеспечивают высокую прочность крепления – 70 100 кН (через 4 6 часов). Полная несущая способность этих анкеров может достигать до 170 кН. Их недостатком является невозможность нагружения анкеров до набора необходимой прочности омоноличивающего раствора.
Впоследние годы стали внедрять сталеполимерные анкеры,
вкоторых вместо цементно-песчаных растворов используют
261
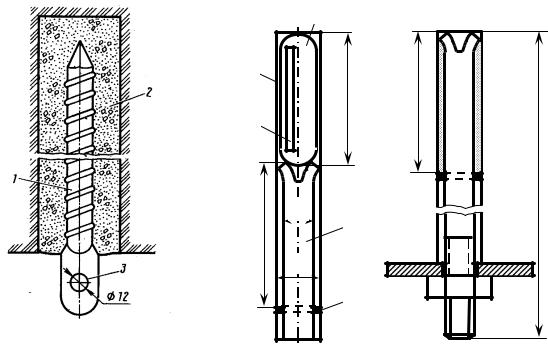
Рис. 6.4. Конструкция железобетонного анкера: 1 – армирующий стержень; 2 – раствор; 3 – отверстие для подвески сетки
а) |
|
1 |
б) |
|
|
||
|
2 |
280 |
|
|
|
з |
|
|
3 |
250- |
l |
|
|
|
|
|
|
|
l |
|
|
25 |
4 |
|
з |
|
|
|
|
|
|
|
l |
|
|
|
|
32 |
|
|
|
|
5 |
Рис. 6.5. Конструкция сталеполимерного анкера: 1 – стеклянная ампула со смолой; 2 – шпур; 3 – пробирка с отвердите-
быстросхватывающиеся химические составы – пласторастворы, представляющие собой клеевые составы на основе эпоксидных, фенольных или полиэфирных смол (рис. 6.5).
Компоненты пластораствора находятся в стеклянной ампуле длиной 250 300 мм. При раздавливании ампулы компоненты смешиваются, после чего раствор твердеет. Положительными качествами сталеполимерных анкеров являются быстрое твердение растворов и хорошая адгезия (прилипание) к стержню и стенкам шпура, что обусловливает высокую прочность закрепления анкера и возможность его нагружения через 1 2 часа после установки. Несущая способность сталеполимерных анкеров составляет не ниже 180 кН. Особенно целесообразно их применение в породах с f <3 4. Недостатками этих анкеров являются: необходимость заводского изготовления, сложность транспортировки стеклянных ампул, высокая стоимость смол.
В зависимости от степени устойчивости пород применяют различные виды анкерной крепи. В монолитных, слаботрещино-
262

Рис. 6.6. Схема анкерной
крепи с металлической сеткой
Рис. 6.7. Схема анкерной крепи с подхватами: 1 – анкеры; 2 – подхват из швеллера
Рис. 6.8. Комбинированная набрызг-бетонная крепь с ан-
керами и металлической сет-
263
ватых и весьма устойчивых породах (f > 8) применяют одиночные анкеры. В устойчивых породах крепостью f = 5 8, в которых возможны небольшие отслоения, выработки крепят анкерами с металлической сеткой с ячейками 50x50 или
100x100 мм (рис. 6.6).
В породах средней устойчивости, трещиноватых и слаботрещиноватых (f = 4 5) анкеры ставят с подхватами из швеллеров или полосовой стали (рис. 6.7). В некоторых случаях на поверхность выработки, закрепленной анкерами, наносят слой набрызг-бетона
(рис. 6.8).
При явно выраженном слоистом строении пород кровли анкеры располагают вкрест простирания слоев или как можно ближе к этому направлению (рис. 6.9). По длине выработки анкеры располагают рядами или в шахматном порядке.
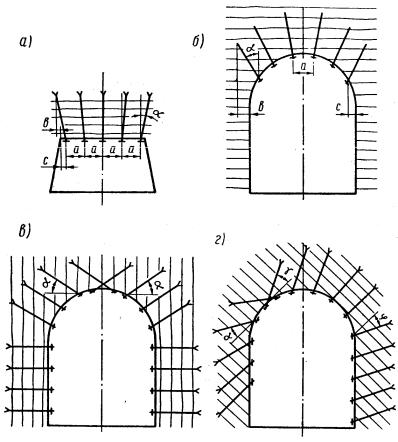
Рис. 6.9. Схемы расположения анкеров при различной слоистости пород кровли: а – трапециевидная выработка при горизонтальном напластовании пород (а 30°, b 40 см, с 0,5 а);
б – сводчатая вы-
работка при |
верти- |
||
кальной |
слоистости |
||
(а |
30°, |
b |
40 см, |
с 0,5 а); |
в – свод- |
||
чатая |
выработка при |
||
вертикальном |
напла- |
||
стовании |
(а 30°); |
г – сводчатая выработка при наклонной слоистости ( 30°,
а30°, 30°)
Всильнонарушенных породах иногда применяют опережающую анкерную крепь, когда в дополнение к обычной арочной крепи устанавливают анкеры в лоб забоя веерообразно по периметру свода выработки до начала разработки породы. Породу разрабатывают под защитой опережающих анкеров заходками,
не доходящими по 0,2 0,5 м до конца анкеров, а хвостовики опережающих анкеров заводят за металлические арки (рис. 6.10).
Анкеры в сводах тоннелей устанавливают с верхних платформ буровых рам или подъемных площадок самоходных бурильных установок, а также со специальных гидроподъемников типа МШТС. В штольнях применяют специальные установки. Шпуры под анкеры бурят бурильными машинами, смонтированными на верхних ярусах буровых рам и бурильных установок,
264
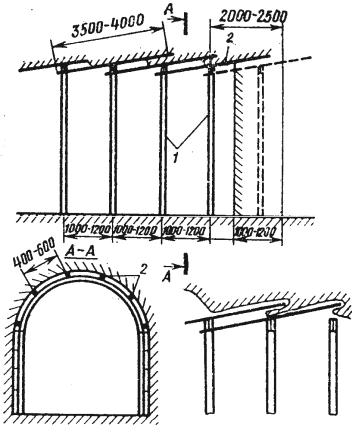
либо телескопными или ручными перфораторами на пневмопод-
|
|
держках. |
|
|
|
|
|
|
Клиновые |
анкеры |
|
|
|
устанавливают путем за- |
|||
|
|
бивки в шпур отбойным |
|||
|
|
молотком через специаль- |
|||
|
|
ную насадку. Сразу же |
|||
|
|
после установки |
произ- |
||
|
|
водят натяжение анкеров |
|||
|
|
с усилием более 40 кН |
|||
|
|
для |
|
предотвращения |
|
|
|
расслоений и частичного |
|||
|
|
восстановления |
напря- |
||
|
|
женного |
состояния гор- |
||
|
|
ного массива путем за- |
|||
|
|
винчивания гаек ключом |
|||
|
|
либо пневматическим или |
|||
|
|
электрическим |
гай- |
||
|
|
ковертом. Железобетон- |
|||
|
|
ные |
анкеры устанавли- |
||
|
|
вают |
в |
шпур, |
пред- |
Рис. |
6.10. Опережающее |
варительно |
запол- |
||
анкерное |
крепление: 1 – ар- |
ненный раствором с по- |
|||
|
|
мощью растворонагнетателя |
и закрепляют их в устье шпура до затвердения раствора клином, манжетой и т.п. Металлическую сетку или подхваты навешивают на клиновые анкеры сразу, а на железобетонные – после достижения раствором 20 % проектной прочности. Взрывные работы разрешается проводить при достижении 60 % проектной прочности раствора.
6.2. КРЕПЬ ИЗ НАБРЫЗГ-БЕТОНА
Набрызг-бетон изготавливается из тех же материалов, что и монолитный бетон: используют портландили шлакопортландцемент марок 300 600 с оптимальным В/Ц = 0,35 0,4. Расход
265
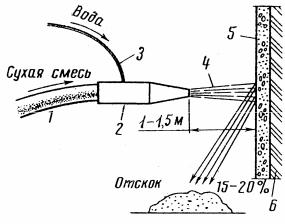
цемента составляет 210 380 кг/м3. Заполнителем служат чистый песок, а также щебень или гравий крупностью до 20 мм.
Бетонную смесь наносят на поверхность выработки специальными набрызг-бетонмашинами, которые с помощью сжатого воздуха подают сухую смесь по трубопроводу к месту укладки. В тоннелестроении применяют набрызг-бетонмашины роторного
типа БМ-68 и БМ-70 производительностью 5 14 м3/ч. Набрызг производится через насадку-со- пло, устанавливаемое в 1 1,5 м от поверхности выработки. В сопло по материальному
шлангу подается сухая смесь, по |
Рис. 6.11. Схема нанесения |
||
водяному шлангу – вода. Про- |
|||
набрызг-бетона на поверхность |
|||
исходит затворение смеси водой |
породы: 1 – шланг для сухой |
||
в сопле, и эта смесь наносится |
смеси; 2 – сопло-смеситель; 3 – |
||
на поверхность выработки |
с |
шланг для воды; 4 – влажная |
|
большим скоростным напором |
бетонная смесь; 5 – слой на- |
||
(рис. 6.11). Скорость струи дос- |
брызг-бетона; 6 – поверхность |
||
тигает 60 80 м/с. Вначале |
к |
выработки |
поверхности прилипают легкие цементные частицы, смоченные водой, которые образуют тонкую
пленку. В этой пленке задерживаются мелкие частицы песка, а затем по мере возрастания толщины покрытия – крупные фракции заполнителя. Набрызг-бетон наносят слоями по 5 10 см. Нанесенный таким способом слой бетона обладает высокой прочностью и хорошим сцеплением с породой. Затвердевший на- брызг-бетон составляет единое целое с породами, окружающими выработку, так как частицы его под напором внедряются в трещины и разрывы породной поверхности, восстанавливая нарушенный приконтурный слой пород и сглаживая неровности. Этим снижаются возможность сдвижения блоков породы и опасные концентрации напряжений в породе.
266
Достоинства набрызг-бетона: он быстро включается в работу, не допуская расслоения пород, и повышает безопасность проходческих работ; защищает поверхность пород от выветривания. Его можно применять в качестве временной и постоянной крепи. Более высокая механическая прочность набрызг-бетона позволяет уменьшить толщину крепи в 2 раза по сравнению с бетонной, тем самым снижается жесткость крепи, лучше используется упругий отпор породы. На 30 40 % сокращается стоимость обделки, и на 10 25 % уменьшается сечение выработки в проходке. Высокий уровень механизации процесса крепления и отсутствие необходимости в устройстве опалубок позволяют увеличить производительность труда проходчиков в 2 3 раза. К недостаткам набрызг-бетонной крепи можно отнести: большие потери бетонной смеси в результате отскока от поверхности при набрызге, которые могут достигать 20 25 %; необходимость индивидуальной защиты рабочих при набрызге от отскока смеси и запыленности воздуха; неровность внутренней поверхности выработки.
Величина отскока по нормам не должна превышать 15 % массы сухой смеси при нанесении на стены и 20 % – на свод выработки. При превышении этих величин необходимо уменьшать количество крупного заполнителя. Для обеспечения быстрого роста прочности набрызг-бетона в него добавляют специальные ускорители (хлористый кальций, жидкое стекло, алюминат, фтористый натрий), которые, кроме того, повышают адгезию и уменьшают степень отскока. При включении добавок сроки схватывания набрызг-бетона составляют порядка 10 мин.
В крепких слаботрещиноватых породах с f = 10 и более толщина набрызг-бетонного покрытия, равная 3 5 см, оказывается вполне достаточной. В более слабых породах (f = 4 8) целесообразно применять набрызг-бетон по металлической сетке в сочетании с анкерами. Тогда укрепленная анкерами порода работает как несущий свод, воспринимая нагрузку от горного давления и собственного веса, а слой набрызг-бетона по сетке служит для восприятия давления от возможных вывалов отслаивающихся между анкерами кусков породы. Сетку обычно применяют из проволоки диаметром 6 мм с ячейками не менее 100x100 мм (см.
267