
2527
.pdf
а)
б)
Рис. 16.10. Стыки между захватками монолитных железобетонных стен: а – нерабочий стык; б – рабочие стыки; 1 – траншея; 2 – ограничитель захваток; 3 – арматурный каркас ранее бетонируемой захватки; 4 – арматурный каркас по следующей захватке; 5 – диафрагма
(рис. 16.11, а – г).
лока, в результате чего образуются каверны; разновременностью осадок секций. Такие стыки делают при глубине траншеи до 12 м.
Рабочие стыки выполняют с перепуском арматуры из одной секции в другую длиной 30 диаметров через диафрагмы – железобетонные плиты или металлические листы, остающиеся в теле стены. Такие стыки обеспечивают равнопрочность стыкового соединения с прочностью основной конструкции стены, так как могут работать на сжатие, растяжение, изгиб и срез. Фигурная диафрагма увеличивает пути фильтрации воды через стык (см. рис. 16.10, б). Рабочие стыки обычно устраивают в том случае, когда «стена в грунте» входит в конструкцию сооружения и является несущей.
Извлекаемые ограничители изготавливают также из железобетонных или стальных балок
Втраншеях глубиной более 12 м применяют неизвлекаемые ограничители в виде стального листа, привариваемого с одной стороны армокаркаса и усиленного по краям швеллерами и уголками (рис. 16.12). Расстояние между швеллерами, служащими также направляющими, соответствует проектной толщине стены,
алист и уголки выступают на 2 3 см с каждой стороны с целью обеспечения непроницаемости стыка во время бетонирования.
Вкачестве неизвлекаемых ограничителей более простой конструкции используют железобетонные балки прямоугольного и фигурного поперечного сечения или стальные двутавровые балки (см. рис. 16.11, д – и). Иногда такие балки ставят в траншее
28
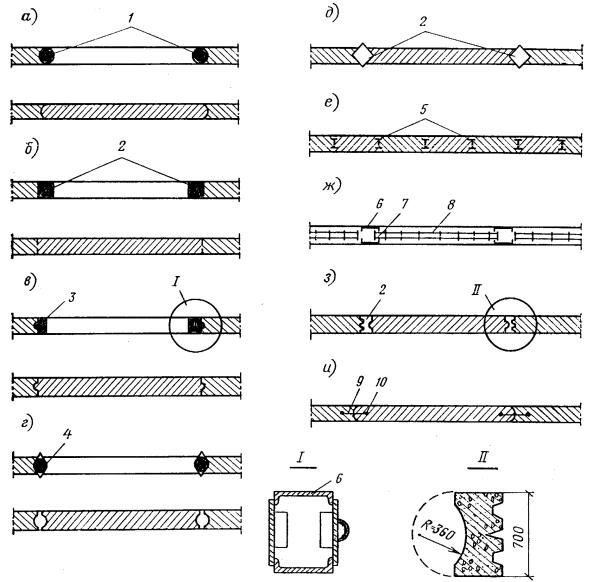
Рис. 16.11. Сопряжения траншейных стен с применением извлекаемых (а – г) и неизвлекаемых (д – и) ограничителей: 1 – трубы; 2 – железобетонные балки; 3 – стальные балки; 4 – труба с уголками; 5 – двутавры; 6 – швеллеры; 7 – фланец; 8 – арматурный каркас; 9 – полоса из полихлорвинила; 10 – стальные стержни
с шагом 1 1,5 м, и в этом случае они являются жесткой арматурой, заменяя обычные арматурные каркасы.
Бетонную смесь в траншею подают по вертикальным трубам на дно траншеи, заполненной глинистым раствором (рис. 16.13). Бетон, будучи тяжелее глинистого раствора, заполняя траншею снизу вверх, вытесняет раствор на поверхность. Основным условием применения метода ВПТ является непрерывность
29

|
бетонирования. Перерывы в бе- |
||
|
тонировании допускаются не бо- |
||
|
лее 2 3 ч. Для исключения |
||
|
расслаивания бетона и переме- |
||
|
шивания его с глинистым рас- |
||
|
твором нижний конец бетоно- |
||
|
литной трубы в течение всего |
||
|
времени бетонирования должен |
||
|
быть |
погружен |
в бетонную |
|
смесь на глубину до 2 м. Гли- |
||
|
нистый |
раствор, |
вытесненный |
Рис. 16.12. Ограничитель |
бетоном, самотеком переливает- |
||
из металлического листа: 1 – |
ся в следующую разрабаты- |
||
арматурный каркас; 2 – швел- |
ваемую захватку траншеи либо |
||
лер; 3 – металлическая диа- |
откачивается насосом в очист- |
||
фрагма |
ные устройства. |
Для бетониро- |
вания применяют бетон классов В15 В25 с крупностью заполнителя до 50 мм и осадкой конуса 16 20 см. Водоцементное отношение должно быть не менее 0,6,
Рис.16.13. Схемы бетонирования траншейных стен с использованием вибробункера (а), башенного крана (б), ков- ша-бункера (в) и укладчика с телескопической стрелой (г): 1 – вышка; 2 – вибробункер; 3 – бетонолитная труба; 4 – кран; 5 – кубло; 6 – ковш-бункер; 7 – автобетоновоз; 8 – бетоноукладчик с телескопической стрелой
30
асрок схватывания – не менее 2 ч. Бетонолитная труба (стальная цельнотянутая) имеет диаметр 200 300 мм. После бетонирования верхний слой бетона толщиной 30 40 см, загрязненный шламом и глинистым раствором, удаляют.
Недостатками сооружения стен из монолитного железобетона являются: невозможность контроля качества бетона, укладываемого в глинистом растворе; трудность соблюдения точного расположения арматурных каркасов относительно поверхности стены и сохранения защитного слоя бетона; необходимость выравнивания и подчистки внутренней поверхности бетонных стен,
атакже скалывания и выравнивания верха стены на конечном этапе работ.
Кроме того, необходимо учитывать некоторые особенности применения глинистого раствора при бетонировании стены. Исследования показали, что при бетонировании под глинистым раствором силы сцепления бетона с арматурой уменьшаются по
сравнению с обычным бетонированием в 1,5 2,5 раза, в результате чего ухудшаются прочностные и деформативные свойства конструкции, ширина раскрытия трещин увеличивается выше нормируемой. Для обеспечения проектных деформативных свойств конструкции необходимо увеличивать процент армирования или повысить класс бетона, что экономически нецелесообразно. Поэтому на практике применяют более экономичные и простые способы повышения сил сцепления:
1)предварительное смачивание арматурного каркаса водой перед опусканием его в траншею с глинистым раствором. На поверхности арматурных стержней образуется водяная пленка, которая препятствует налипанию глинистых частиц. Это позволяет повысить силу сцепления на 15 %;
2)барботаж – подача сжатого воздуха в зону укладки бетонной смеси. За счет подъема пузырьков воздуха происходит интенсивное перемешивание раствора и разрушение глинистой пленки на арматуре. Сила сцепления увеличивается до 25 %;
3)электроосмос – подключение отрицательного потенциала напряжения к арматурному каркасу. Вследствие однополюсности зарядов происходит разрушение пленки и отталкивание глинис-
31
тых частиц от арматуры, вокруг которой образуется водяная пленка. Сила сцепления увеличивается в 1,5 2 раза.
Кроме того, для улучшения сцепления арматуры с бетоном рекомендуются следующие технологические решения: арматурный каркас должен находиться в глинистом растворе менее 4-х часов; вязкость раствора может быть не свыше 30 с; глинистый раствор необходимо выдерживать в траншее не более 24-х часов.
16.5. ВОЗВЕДЕНИЕ «СТЕН В ГРУНТЕ» ИЗ СБОРНОГО ЖЕЛЕЗОБЕТОНА
В практике строительства стал более широко применяться сборный железобетон, обладающий рядом преимуществ по сравнению с монолитными конструкциями.
Основные достоинства сборных конструкций: высокая индустриальность строительства, возможность обеспечения необходимого качества работ, отсутствие жестких требований к качеству глинистого раствора, а также возможность снижения толщины монолитных железобетонных стен с 0,6 до 0,25 м. Сборные элементы обеспечивают хорошее качество поверхности и не требуют дополнительной обработки в отличие от монолитных стен, повторяющих все неровности стен траншеи.
К недостаткам сборных конструкций следует отнести значительную стоимость и трудоемкость заводского изготовления и транспортирования элементов больших размеров. Ограничением для их применения пока являются глубины свыше 20 25 м, так как при этом масса сборных элементов становится слишком большой и монтаж их затрудняется. Обычно применяют железобетонные панели высотой до 10 15 м, толщиной 30 50 см и массой до 30 т.
Возведение сборных конструкций, как показывает мировая практика, осуществляется по трем основным технологическим схемам, отличающимся заделкой стыков между стеновыми панелями в траншее.
По первой схеме сборные элементы устанавливают в траншею, заполненную специальным медленнотвердеющим раствором, который за-
полняет стыки между сборными элементами и за-
32

стенное пространство между бортами траншеи и сборными элементами. Сборные элементы выполняют в виде вертикальных панелей с пазами и гребнями на их торцах или же в виде свай с пазами, в которые вставляются панели (рис. 16.14).
В первом случае конструкция собирается из одинаковых стеновых панелей, причем гребень одной панели входит в паз другой. Слой затвердевшего раствора с внутренней стороны сооружения снимается при разработке грунта, и для облегчения этой операции панели с внутренней стороны покрываются специальной обмазкой или слоем пластика. Разработка грунта при этом ведется в траншее без разделения ее на захватки, т.е. участками длиной 25 30 мм.
Во втором случае разработка грунта ведется отдельными захватками – секциями через одну. В первую очередь разрабатывают секции, в которых устанавливают сваи-балки, заделываемые в грунт, а во вторую очередь – секции, в которых устанавливают панели-плиты. Толщина свай обычно 500 мм, плит – 250 мм.
Траншея разрабатывается под защитой обычного глинистого раствора. Затем, непосредственно перед монтажом сборных элементов, производят замену глинистого раствора специальным медленнотвердеющим раствором, который должен отвечать следующим требованиям: его прочность должна быть не меньше прочности грунта; он должен быть достаточно подвижным, что-
Рис. 16.14. Конструкции сборных элементов: 1 – стеновые панели; 2 – раствор; 3 – балка; 4 – плита
33
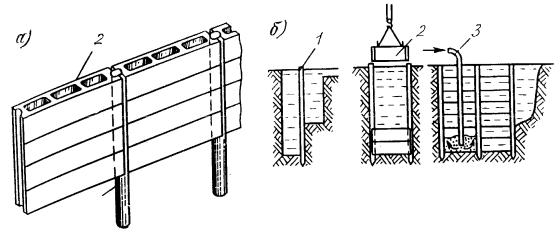
бы обеспечить надежное заполнение полости и зазоров между стенами траншеи и сборными элементами. Этот раствор вводится с помощью инъекционной колонны – трубы диаметром 100 мм, наверху с воронкой, внизу с перфорированным патрубком. Медленнотвердеющий цементно-песчано-глинистый раствор плотностью 1,3 г/см3 вытесняет более легкий глинистый раствор (1,05 г/см3), который откачивают в емкость для вторичного использования.
По второй технологической схеме сборные элементы, имеющие открытые для доступа сверху, полости стыков монтируют в траншее, заполненной глинистым раствором. Заделка стыков между сборными элементами осуществляется после их монтажа в траншее путем подачи твердеющего раствора в открытые сверху полости замоноличиваемых конструкций (рис. 16. 15). Твердеющий раствор, поднимаясь снизу вверх, вытесняет более легкий глинистый раствор из полости стыка, а также проникает в застенное пространство. Характерной особенностью является горизонтальная разрезка сборных стен на отдельные элементы, а также применение комбинированных конструкций «свая-панель».
Вначале по трассе траншеи через определенные промежутки устраивают буронабивные или забивные сваи диаметром, несколько меньшим, чем ширина траншеи, и длиной, большей глубины заложения стен. Затем в промежутках между сваями под
|
|
|
|
б) |
|
|
|
|
|
|
|
|
|
|
|
|
2 |
|
|
||
а) |
|
|
|
|
|
|||||
|
|
|
|
|
4 |
|||||
|
3 |
|
|
|
|
|
||||
|
|
1 |
||||||||
|
|
|
|
|
|
|
|
|
||
|
|
|
|
|
|
|
||||
|
|
|
|
|
|
|
|
|
|
|
1
Рис. 16.15. |
Конструкции стен с горизонтальной разрезкой: |
1 – буронабивная |
(забивная) свая; 2 – панель; 3 – установка пане- |
лей в траншее; 4 – бетонолитная труба
34

защитой глинистого раствора производят разработку грунта и монтаж панелей. Заделку стыков и швов между сваями и панелями осуществляют путем инъекции замоноличивающего цементного раствора по трубам, оставленным в стыках между панелями. Этим способом возводят подземные сооружения на глубину свыше 20 25 м. Недостатком данной схемы является невозможность создания равнопрочной конструкции стыка со сборными элементами. Кроме того, в местах стыков панелей и замоноличивающего бетона из-за неплотности возможна контактная фильтрация подземных вод внутрь тоннеля.
По третьей технологической схеме в разработанной под защитой глинистого раствора траншее монтируют сборные стеновые панели с помощью кондукторов. Их закрепляют путем бетонирования зазора между ними и стенками траншеи на высоту до 1 м с последующей забутовкой до верха панелей (рис. 16.16). Снаружи забутовка производится тампонажным глиноцемент-
7
Рис. 16.16. Технологическая схема устройства стен по методу, разработанному НИИСП и Укрводоканалпроектом: 1 – кран для подачи бетона нижнего защемления; 2 – монтажный кран; 3 – стеновая панель; 4 – штанговый экскаватор на разработке траншеи; 5 – бетон нижнего защемления; 6 – обратная засыпка пазухи; 7 – кондуктор
35

Рис. 16.17. Стыки панелей открытого типа: а – нерабочий; б – рабочий открытый; в – то же типа «ласточкин хвост»; г – рабочий, с применением двутавра; 1 – цементный раствор; 2 – стальная сплошная накладка; 3 – торкретбетон; 4 – двутавр; 5 – кондуктор
ным раствором, она создает вокруг тоннеля водонепроницаемый экран, внутри обеспечивает жесткую заделку стеновой панели путем засыпки легкоразрабатываемым несвязным грунтом: песком, щебнем, дресвой. После твердения тампонажного раствора и разработки грунта внутри тоннеля заделывают стыки насухо по мере их обнажения и очистки полостей стыка от песка и остатков глинистого раствора.
Панели соединяют с помощью стальных накладок, привариваемых изнутри к специальным уголкам в панелях, или с помощью двутавров и уголков, омоноличиваемых глиноцементным раствором (рис. 16.17).
16.6. ВОЗВЕДЕНИЕ «СТЕН В ГРУНТЕ»
БУРОВЫМИ МЕТОДАМИ
«Стены в грунте» возводят также путем последовательного бурения скважин, примыкающих друг к другу, при помощи ли- дерно-направляющих обсадных труб диаметром 500 600 мм (рис. 16.18). При этом, в зависимости от горно-геологических условий, различают следующие варианты возведения стен: в мало-
36
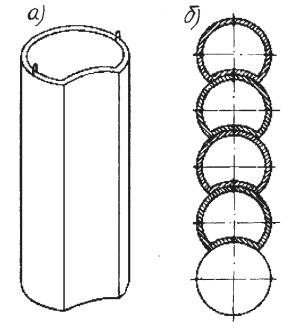
влажных скальных и полу- |
|
|
|
||||||
скальных породах – корот- |
|
|
|
||||||
кими |
траншеями, |
|
раз- |
|
|
|
|||
рабатываемыми бурением се- |
|
|
|
||||||
кущихся скважин без подачи |
|
|
|
||||||
глинистого раствора; |
в |
во- |
|
|
|
||||
донасыщенных |
грунтах |
при |
|
|
|
||||
наличии валунов, |
камней и |
|
|
|
|||||
других |
твердых включений |
|
|
|
|||||
– так же, но с применением |
|
|
|
||||||
глинистого раствора; в неус- |
|
|
|
||||||
тойчивых |
оплывающих |
|
|
|
|||||
грунтах, |
а также |
в |
непо- |
|
|
|
|||
средственной |
близости |
от |
|
|
|
||||
зданий и сооружений, когда |
Рис. |
16.18. |
Лидерно- |
||||||
глинистый раствор не может |
|||||||||
обеспечить |
устойчивость |
направляющие трубы; а – общий |
|||||||
вид; б – план расположения ли- |
|||||||||
стен траншеи, |
– |
последова- |
|||||||
дерно-направляющих труб при |
|||||||||
тельным |
устройством |
секу- |
разработке траншей |
|
щихся буронабивных свай (с обсадными трубами).
Для устройства несущих «стен в грунте», противофильтрационных завес, железобетонных свай большого диаметра используют также струйную технологию, когда в заранее пробуренные скважины опускают мониторы, которые укрепляют грунт путем подачи в него твердеющих растворов. В России разработаны установки струйной технологии для сооружения стен глубиной до 25 м, а в Японии – до 45 м (см. рис. 8.31). Опыт применения струйной технологии в России показал ее эффективность и преимущества: экономичность, высокую производительность, простоту, отсутствие шума и вибрации при работе, а также возможность выполнения работ под существующими наземными зданиями и сооружениями без их усиления или разборки. Техникоэкономический анализ опыта строительства показал, что при возведении подземных стен, сооружаемых по струйной технологии, стоимость 1 м2 стены в 2 3 раза ниже стоимости 1 м2 стены, сооружаемой по традиционной траншейной технологии.
37