
2381
.pdf
При проектировании процесса доводки выбирают метод доводки и оборудование, назначают режим и другие условия предварительной и окончательной доводки и рассчитывают наладку исполнительного механизма станка исходя из требований качества, производительности (съем материала детали в единицу времени) и себестоимость обработки.
Выходные показатели процесса доводки определяются технологическ ми, к немат ческими, геометрическими и динамическими факторами. Каждый з этих факторов позволяет осуществить стабилизацию параметров качества обработки и автоматическое управление процессом доводки по комплексу показателей.
таб л зац я параметров качества доведенной поверхности и управлен е точностью ее формы и размеров осуществляются созданием услов й равномерного изнашивания поверхности притира в процессе доводки, а также программированным перемещением детали по поверхности пр т ра.
Задан я и порядок выполнения работы
Задания предусматривают назначение технологических условий тонкого шлифования, хонингования и других процессов обработки деталей с использованием их чертежа, технических условий и норма- тивно-расчетных условий процессов обработки. Исходные условия процессов отделочной обработки абразивными инструментами приведены в табл. 2.11.
Таблица 2.11
Исходные условия задания
|
|
|
Исходные требования |
|
|
|
|
|
|
Деталь |
Вид условия |
Заготовка |
Деталь |
|
|||
|
|
Техниче- |
|
|
|
Ra, |
|
|
|
Эскиз |
предшествующей |
Припуск, |
Ra, |
Допуск, |
|
||
|
ские усло- |
обработки |
мм |
мкм |
мм |
Мк |
|
|
|
|
|
|
|
||||
|
|
СибАДИ |
|
м |
|
|||
|
|
вия |
|
|
|
|
|
|
|
|
|
|
|
|
|
|
|
Назначаемые условия отделочной обработки абразивными инструментами приведены в табл. 2.12. При этом выбор технологического
31
оборудования, схем наладки, и других условий выполняют с помощью нормативных данных (см. прил.).
Таблицы 2.12
Назначаемые требования обработки
|
|
|
|
|
|
|
|
|
|
СибАДИ |
|||||||||
|
|
|
|
Назначаемые условия |
|
|
|
||
|
Технолог че- |
|
Схема |
Режущий инструмент |
Технологи- |
Режим |
|
||
|
ское оборудо- |
|
налад- |
Вид аб- |
Зерно |
Связка |
ческая |
обра- |
|
|
ван е |
|
ки |
разива |
|
|
жидкость |
ботки |
|
|
Дополн тельного внимания со стороны исполнителя работы за- |
||||||||
|
служивает выявлен е других условий за |
пределами |
сведений |
||||||
|
табл. 2.12. |
|
|
|
|
|
|
|
|
|
|
|
Контрольные вопросы и задания |
|
|
||||
|
1.Технолог ческ е схемы и условия методов отделочной обработки |
||||||||
|
по требованиям производительности процессов и качества обработки. |
||||||||
|
2.Требования |
к предшествующей |
обработке и её влияния на |
последующую о ра отку.
3.Какие параметры относятся к выходным характеристикам отделочной абразивной обработки и их зависимость от назначаемых условий обработки?
4.Режимы резания рассматриваемых методов с учётом производительности процессов обеспечения требований качества.
5. Каковы характерные дефекты применения методов отделочной обработки, связанные с назначением условий обработки?
6.Условия теплового воздействия на материал детали в процессе обработки.
7.Оборудование для выполнения отделочной абразивной обработки, назначение, технологические возможности.
8.Применяемые абразивные материалы.
9. Роль смазочно-охлаждающих жидкостей в задачах повышения качества и увеличения производительности процессов обработки.
32
Лабораторная работа 3
ОБОСНОВАНИЕ ВЫБОРА СПОСОБА И УСЛОВИЙ ОТДЕЛОЧНОЙ АБРАЗИВНОЙ ОБРАБОТКИ
Цель работы: освоить методику и получить практические навыки
выбора способа и технологических условий отделочной обработки.
СибАДИна валок на деталь РВ = РД в их материале происходит пластическое деформирование на участках длиной lВ-С и l С . На детали формируются лунка глубиной tС и деформированный слой tД .
Краткие сведения
Доводка как способ размерной обработки с наиболее высокими выходными характер ст ками. Процесс удаления материала припуска, формирован я обра отки поверхности и поверхностного слоя при доводке
или пр т рке |
осуществляется |
при взаимодействии доводимой и |
||||
доводящей поверхностей, а разивных (алмазных) зерен, компонентов |
||||||
смачивающей технолог ческой среды. |
|
|
||||
На р с.3.1 |
пр ведена |
схема |
взаимодействия |
случайных |
||
поверхностей довод мой |
доводящей поверхностей с единичным зерном |
|||||
в условиях процесса |
есцентровой доводки. При движении |
в едином |
||||
направлении доводящей и доводимой поверхностей кинематика движения |
||||||
станка предусматривает меньшую скорость доводимой детали |
||||||
относительно |
поверхности |
валка |
VВ >V |
. За счет этого |
происходит |
процесс притирания одной поверхности по другой. Обе поверхности подвержены изнашиванию. Однако в задачу назначения условий доводки входит обеспечение наибольшего изнашивания доводимой поверхности относительно доводящей за счет подбора материала и размера зерен, смачивающей жидкости и других условий.
Роль зерен сводится к следующему. Отдельные зерна (рис. 3.1, а) перекатываются по поверхностям со скоростью VВ 3 . Под действием сил
Роль других зерен может быть представлена, как показано на рис. 3.1, б. В этом случае за счет шаржирования зерно неподвижно закреплено в материале валка (притира). Такое закрепление происходит за счет внедрения зерна в материал валка. Перемещения валка относительно детали обеспечивает скорость перемещения зерна V3 , при которой осуществляется процесс резания зерном на длине детали lД Р со снятия слоя припуска глубиной t.
33

А |
Г Б |
VB |
Д |
В |
1 |
|
|
|
|
2 |
|
|
|
VB>VД |
|
|
|
|
СибАДИ |
||||||||
|
3 |
|
|
|
|
|
|
|
|
|
|
PВ |
|
|
VД |
||
|
|
|
|
|
1 |
|
PВ = PД |
|
|
|
|
|
VВ-З |
3 |
|
t = 0 |
|
|
tC |
|
|
|
|
|
VВ-З ≤ VВ |
|
a |
|
|
|
|
2 |
|
VB-Д > VВ |
|
|
tД |
PД |
|
VД |
|
|
|
|
|
|
|
|
VB |
|
|
|
|
|
|
|
|
|
1 |
|
VЗ = VВ |
|
|
|
|
|
VЗ |
2 |
|
PZ = f(t) |
|
|
|
|
|
|
VВ-З = 0 |
|||
б |
t |
PZ |
PY |
|
3 |
|
VВ > V |
|
|
|
|
|
|
|
|||
|
|
|
|
|
|
|
|
|
|
tД |
|
R |
V |
|
|
|
|
|
|
|
VB |
PВ |
1 |
|
|
|
|
tЛ |
|
|
|
|
PВ = P |
||
|
|
|
|
|
|
|||
|
|
|
|
2 |
|
t = 0 |
||
|
|
|
|
|
|
|||
в |
|
|
|
VВ-З |
|
VВ-З ≤ VВ |
||
|
|
|
|
|
||||
|
|
|
PД |
PZ-Д |
3 |
|
VВ > V |
|
|
|
|
|
|
|
V
Рис.3.1. Схема взаимодействия случайных поверхностей обрабатываемой детали и доводящего валка с единичным зерном в процессе бесцентровой доводки: 1 – доводящий валок; 2 – обрабатываемая деталь; 3 – объемы материала детали и валка, подверженные действию химических и физических процессов; А – зерно, перекатывающееся между поверхностями; Б – зерно, шаржированное в валок, участвующее в резании припуска; В – зерно, удаленное с места шаржирования в валке; Г – стружка от срезанного припуска; Д – зерно, не участвующее в работе
34
На рис. 3.1,в приведено еще одно действие зерна. Под действием сил резания зерно удалено с места шаржирования в валке, после чего осталась лунка tЛ . Как в случае А, это зерно стало перекатываться со скоростью VВ 3 . При сочетании новых случайных поверхностей это зерно может выполнять действия, указанные на рис. 3.1,а ,б. Возможны еще два варианта. Первый из них – под действием сил РВ и РД зерно будет
СибАДИразрушено на более мелкие фрагменты. Второй, когда размер зерна меньше расстояния между поверхностями, – в рассматриваемый момент
зерно не будет участвовать в работе.
Так м образом, в соответствии с рис. 3.1 в каждый момент времени
между довод мой доводящей поверхностями находятся следующие
компоненты рабочей среды: зерна исходного размера; зерна с частичным
износом разрушен ем; разрушение зерна до размеров частиц, не
способных оказать заметного влияния на снятие припуска и формирован е состоян я о ра отанной поверхности и поверхностного слоя; част цы стружки материала детали; частицы материала притиры (валка) смач вающая технологическая среда, содержащая технолог ческую ж дкость заданного свойства, присадки, поверхностноактивные вещества и другие компоненты.
В соответствии со схемой рис. 3.1 выше рассмотрены давления I уровня. Их действие распространяется на глубину 5–20 мкм и более. Однако есть более тонкие процессы и явления II уровня, действие которых распространяется на глубину 0,000 3 мкм и менее. На рис. 3.1 такой силой 3 показан со стороны доводящей и доводимой поверхности.
Основными гипотезами, объясняющими механические, физические и химические явления в процессе доводки, являются:
- механическая теория, подготовленная Р. Гуком и в последующем доработанная А.В. Шубниковым;
- химико-механическая гипотеза И.В. Гребенщикова; - эффект П. . Ребиндера, в основу которого положено явление
понижения прочности поверхностного слоя твердых тел при адсорбции поверхностно-активных веществ.
В современном представлении разрушение материала припуска детали и притира при доводке и состояние поверхностного слоя обрабатываемой детали формируют преимущественно механические процессы (упругая и пластическая деформация, разрушение, трение). При этом значительным является влияние химических и физико-химических процессов, которые происходят под действием поверхностно-активных веществ. Слой 3 (см. рис.3.1) сформирован вследствие совместного действия указанных явлений.
В соответствии с вышеуказанными явлениями происходит
35

формирование поверхностного слоя детали. Укрупненное представление о структуре поверхностного слоя деталей, обработанных тонким шлифованием, суперфинишированием и доводкой, приведено в табл.3.1.
Таблица 3.1
Изменения в поверхностном слое
|
|
|
|
|
|
|
СибАДИ |
Доводка |
|||||
|
Толщина слоя, мкм |
Тонкое |
Суперфиниширование |
|
||
|
|
|
шлифование |
|
|
|
|
адсорбц онными |
0, 0004–0,0005 |
0,0003–0,0005 |
0,0001–0,0003 |
|
|
|
молекулами к слорода, |
|
|
|
|
|
|
азота |
|
|
|
|
|
|
Окислов |
н тр дов |
0,006–0,009 |
0,002–0,005 |
0,001–0,002 |
|
|
Упруго- |
пласт чески |
20–10 |
12–6 |
2–5 |
|
|
деформ рованного |
|
|
|
|
|
|
материала |
разрушен я |
|
|
|
|
Данные табл. 3.1 позволяют регулировать состояние поверхностного слоя детали за счет снят я слоя от предшествующей обработки.
Управлен е выходными параметрами доводки, место доводки в технологии изготовления деталей. К числу наиболее определяющих выходных параметров процесса доводки относятся следующие: удельный съем материала припуска (производительность), обеспечение заданных требований геометрической точности, обеспечение заданного состояния обработанной поверхности и поверхностного слоя, стабильность перечисленных параметров в изменяющихся производственных условиях. Последний параметр является наиболее важным, т.к. имеет значение не только первоначально освоить обработку в условиях с заданными выходными параметрами, но и обеспечить их в условиях смены производственного персонала, постепенного изнашивания узлов станков и технологической оснастки, изменений температуры в производственных помещениях т.д.
При обеспечении требования качества и производительности процессов доводки, когда характеристики этих параметров измеряются в долях мкм, существуют десятки факторов, влияющих на указанные параметры. Условия формирования выходных параметров процесса доводки в производственных условиях приведены на рис. 3.2. Выбор условий формирования выходных параметров доводки и их оптимального сочетания применительно к разным видам доводки позволяет установить
параметры, |
соответствующие |
заданным |
требованиям |
качества |
|||
при |
сохранении |
необходимой |
производительной |
обработки. |
36
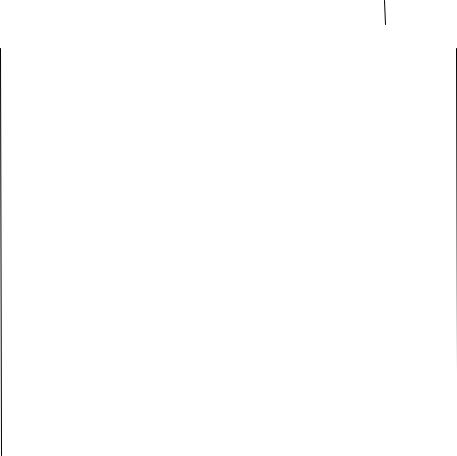
|
|
|
|
|
|
|
|
|
|
|
|
|
|
|
|
|
|
|
|
|
|
|
СибАДИ |
|
|
|
|
|
|||||||||
|
|
|
|
Услов я форм рования выходных параметров доводки |
|
|
|
|
|
|||||||||
|
Физико- |
|
|
Технолог че- |
|
|
К нематиче- |
|
|
Динамиче- |
|
|
Геометриче- |
|
Организацион- |
|
||
|
химические |
|
|
ск е |
|
|
ские |
|
|
ские |
|
|
ские |
|
|
ные |
|
|
|
Физические, |
|
|
остав |
|
|
Соотношение |
|
|
Закономерно- |
|
|
Геометрическая |
|
Квалификация |
|
||
|
химические |
|
|
рабочей среды |
|
|
скоростей |
|
|
сти сил |
|
|
форма |
|
производствен- |
|
||
|
свойства |
|
|
в зоне |
|
|
довод мой и |
|
|
системы |
|
|
поверхностей |
|
ного персонала |
|
||
|
материала |
|
|
обработки |
|
|
доводящей |
|
|
«деталь – |
|
|
притира и |
|
|
|
|
|
|
детали |
|
|
|
|
|
поверхностей |
|
|
прослойка – |
|
|
детали |
|
Состояние |
|
||
|
|
|
|
Обрабатываем |
|
|
|
|
|
притир» |
|
|
|
|
|
|
||
|
Наличие |
|
|
ость |
|
|
Взаимное |
|
|
|
|
|
Форма и |
|
оборудования, |
|
||
|
химических и |
|
|
материала |
|
|
расположение |
|
|
Закономерно- |
|
|
размеры |
|
оснастки |
|
||
|
|
|
детали |
|
|
доводимой и |
|
|
сти |
|
|
|
|
|||||
|
поверхностно- |
|
|
|
|
|
|
|
|
канавок подвода |
|
|
||||||
|
|
|
|
|
доводящей |
|
|
|
|
|
|
|
|
|||||
|
|
|
|
|
|
|
контактных |
|
|
|
|
|
|
|||||
|
активных |
|
|
|
|
|
|
|
|
|
суспензии |
|
|
|
|
|||
|
|
|
|
|
|
поверхностей |
|
|
напряжений в |
|
|
|
Состояние и |
|
||||
|
веществ |
|
|
Размеры |
|
|
|
|
|
|
|
|
|
|
||||
|
|
|
|
|
|
|
|
зоне |
|
|
|
|
|
рациональное |
|
|||
|
|
|
|
снимаемого |
|
|
Траектория |
|
|
|
|
Масштабное |
|
|
||||
|
|
|
|
|
|
|
|
обработки |
|
|
|
применение |
|
|||||
|
Состояние |
|
|
|
||||||||||||||
|
|
|
припуска и |
|
|
движения |
|
|
|
|
|
соотношение |
|
средств |
|
|||
|
среды для |
|
|
|
|
|
|
|
|
|
|
|
||||||
|
|
|
заготовки |
|
|
детали |
|
|
|
|
|
размеров детали |
|
измерений |
|
|||
|
|
|
|
|
|
|
|
|
|
|
|
|||||||
|
перемещения |
|
|
|
|
|
|
|
|
|
|
|
||||||
|
|
|
|
|
|
относительно |
|
|
мплитудно- |
|
|
притира |
|
|
|
|
||
|
|
|
|
|
|
|
|
|
|
|
|
|
|
|||||
|
|
|
|
|
|
|
|
|
|
|
|
|
|
|
||||
|
|
|
|
Факторы |
|
|
притира |
|
|
частотные |
|
|
|
|
|
|
|
|
|
Наложение |
|
|
|
|
|
|
|
|
|
|
|||||||
|
|
|
технологиче- |
|
|
|
|
|
характеристи- |
|
|
|
|
|
|
|
|
|
|
|
|
|
|
|
|
|
|
|
|
|
|
|
|
||||
|
колебаний на |
|
|
ского |
|
|
|
|
|
ки процесса |
|
|
|
|
|
|
|
|
|
|
|
|
|
|
|
|
|
|
|
|
|
|
|
|
|||
|
деталь - |
|
|
|
|
|
|
|
|
|
|
|
|
|
|
|
||
|
|
|
наследования |
|
|
|
|
|
|
|
|
|
|
|
|
|
|
|
|
|
|
|
|
|
|
|
|
|
|
|
|
|
|
|
|
||
|
инструмент |
|
|
|
|
|
|
|
|
|
|
|
|
|
|
|
|
|
|
|
|
|
|
|
|
|
|
|
|
|
|
|
|
|
|
|
|
|
|
|
|
Рис.3.2. Факторы обеспечения выходных параметров процесса доводки |
|
|
||||||||||||
|
|
|
|
|
|
37

Таблица 3.2
Параметры шероховатости поверхности после чистовой абразивной обработки
|
Метод обработки |
Шероховатость |
v |
b |
P,% |
Рпоп , |
|
Sпоп |
|
|
|
СибАДИ |
град |
|
Rmax |
|
|||||
|
|
Ra |
|
|
|
|
|
|||
|
Шлифование плоское |
6 |
2,25 |
2,75 |
20 |
27 |
|
4,5 |
|
|
|
|
8 |
2,2 |
2,9 |
17 |
12 |
|
14 |
|
|
|
|
9 |
2 |
3,5 |
15 |
5 |
|
18 |
|
|
|
Шлифован е круглое |
7 |
2,6 |
2,3 |
18 |
25 |
|
5 |
|
|
|
|
9 |
2,3 |
2,8 |
17 |
11 |
|
15 |
|
|
|
|
10 |
2,2 |
3,5 |
15 |
5 |
|
22 |
|
|
|
Хонингован е |
8 |
2,2 |
1,5 |
19 |
13 |
|
9 |
|
|
|
|
9 |
2 |
3 |
16 |
11 |
|
25 |
|
|
|
|
11 |
1,9 |
4 |
14 |
3 |
|
45 |
|
|
|
Суперфин ш рован е |
9 |
2,3 |
3,2 |
16 |
3 |
|
19 |
|
|
|
|
10 |
1,8 |
3,5 |
14 |
2 |
|
40 |
|
|
|
|
11 |
1,4 |
3,7 |
12 |
1 |
|
65 |
|
|
|
Полирован е |
8 |
2,2 |
3 |
16 |
2 |
|
60 |
|
|
|
|
9 |
1,7 |
3,2 |
15 |
1 |
|
120 |
|
|
|
|
11 |
1,3 |
3,5 |
11 |
30 |
|
215 |
|
|
|
Доводка плоских |
10 |
3 |
1,5 |
25 |
5 |
|
48 |
|
|
|
поверхностей |
11 |
2,5 |
2,2 |
33 |
3 |
|
123 |
|
|
|
|
13 |
2,2 |
3 |
48 |
30 |
|
190 |
|
|
|
Доводка |
10 |
2,3 |
1,9 |
22 |
6 |
|
38 |
|
|
|
цилиндрических |
11 |
2,2 |
2 |
31 |
3 |
|
103 |
|
|
|
поверхностей |
13 |
1,5 |
2,5 |
42 |
30 |
|
182 |
|
|
При выборе методов финишной обработки деталей в производственных условиях приходится решать задачу определения наиболее рентабельного метода при условии обеспечения заданных выходных параметров. Данные табл.3.2 3.3 позволяют выбрать метод финишной обработки с учетом обеспечения требований качества. К числу этих методов отнесены: круглое чистовое и тонкое шлифование, бесцентровое чистовое и тонкое шлифование, хонингование, суперфиниширование, бесцентровая доводка, плоское шлифование, полирование эластичным кругом, плоская и ручная доводка.
Выбор метода и условий доводки проводится с учетом отклонений детали на предыдущей обработке, как показано на рис.3.3.
Такое обоснование параметров доводки может быть проведено с помощью данных табл. 3.4
38
|
СибАДИ |
|
|
Таблица 3.3 |
|||||||||
|
|
|
Параметры качества обработки после финишных методов обработки |
|
|
|
|
|
|
||||
Метод |
Припуск |
Характер ст ка |
Режим резания |
Давле- |
Параметры качества поверхности |
|
|||||||
обработки |
на |
нструмента |
|
|
ние , |
ф , мм |
|
|
Параметр |
|
h, |
||
|
|
диаметр, |
|
|
|
кПа |
|
шероховатости, |
|
мм |
|||
|
|
мм |
|
|
|
|
|
|
|
|
мкм |
|
|
Круглое |
0,10– |
Круги: абраз вные |
t = 0,100–0,050 мм |
|
0,05–0,08 |
|
Rа |
= 3,5–1,25 |
|
|
|||
чистовое |
0,15 |
зерн стостью 40–25, 25–16; |
кр = 10–40 м/с |
– |
0,01–0,05 |
Rа |
|
= 1,25–0,64 |
|
0,040 |
|||
шлифование |
|
алмазные зерн стостью |
дет |
= 20–50 м/мин |
0,02–0,03 |
|
|
|
|
|
|||
|
|
|
25/15–5/3 |
|
= 0,5–0,7 м/мин |
|
Rа |
|
= 1,25–0,64 |
|
– |
||
|
|
|
|
Sпр |
|
0,005–0,01 |
|
|
0,010 |
||||
|
|
|
|
|
|
|
Rа |
|
= 1,25–0,32 |
|
|||
Круглое тонкое |
0,04– |
Круги: абразивные |
t = 0,050–0,025 мм |
|
0,03–0,05 |
|
Rа |
= 2,5–0,63 |
|
|
|||
шлифование |
0,10 |
зернистостью 12–14М; |
кр = 10–40 м/с |
– |
0,005–0,01 |
Rа |
|
= 0,32–0,08 |
|
0,030 |
|||
|
|
|
алмазные зернистостью |
дет |
= 10–50 м/мин |
|
|
|
|
|
|
||
|
|
|
40/28–5/3 |
Sпр |
= 0,3–0,5 м/мин |
|
0,01–0,015 |
Rа |
|
= 1,25–0,32 |
|
– |
|
|
|
|
|
|
|
|
0,005 |
||||||
|
|
|
|
|
|
|
0,002–0,005 |
Rа |
|
= 0,16–0,04 |
|
||
Бесцентровое |
0,05– |
Круги: абразивные |
дет |
= 20–60 м/мин |
|
0,05–0,01 |
|
Rа |
= 2,5–1,25 |
|
0,030 |
||
шлифование |
0,30 |
зернистостью 40–25, 25–16; |
кр = 10–40 м/с |
– |
|
|
|
|
|
|
|||
чистовое |
|
алмазные зернистостью |
|
|
|
|
|
|
|||||
|
|
|
63/50–28/20 |
|
|
|
0,002–0,005 |
|
|
|
|
|
– |
|
|
|
|
|
|
Rа |
|
= 1,25–0,63 |
|
0,005 |
|||
|
|
|
|
|
|
|
|
|
|||||
|
|
|
|
|
|
|
|
|
|
|
|
||
Бесцентровое |
0,04– |
Круги: абразивные |
дет |
= 20–60 м/мин |
– |
0,03–0,05 |
Rа |
|
= 1,25–0,63 |
|
0,010 |
||
шлифование |
0,10 |
зернистостью 12–14М; |
кр = 10–40 м/с |
|
|
|
|
|
|
||||
тонкое |
|
|
алмазные зернистостью |
|
|
|
|
|
|
|
|||
|
|
|
40/28–5/3 |
|
|
|
0,001–0,003 |
|
|
|
|
|
– |
|
|
|
|
|
|
Rа |
|
= 0,63–0,32 |
|
0,003 |
|||
|
|
|
|
|
|
|
|
|
|||||
|
|
|
|
|
|
|
|
|
|
|
|
|
|
39
СибАДИ |
|
|
|
|||||||
|
|
|
|
|
|
|
Продолжение табл.3.3 |
|||
Метод |
Припуск |
Характер ст ка |
Режим резания |
Давле- |
Параметры качества поверхности |
|||||
обработки |
на |
нструмента |
|
|
ние , |
ф , мм |
|
Параметр |
h, |
|
|
диаметр, |
|
|
|
кПа |
|
шероховатости, |
мм |
||
|
мм |
|
|
|
|
|
|
|
мкм |
|
Хонингование |
0,2–0,03 |
Бруски: абраз вные |
окр |
= 20–80 м/мин |
400–800 |
0,05–0,09 |
|
Rz = 40–10 |
|
|
|
0,02– |
зерн стостью 16–6, М5–5; |
пост = 3–22 м/мин |
|
0,03–0,004 |
Rа |
= 0,32–0,08 |
|
||
|
0,005 |
|
S = 0,4–3 мкм/дв.ход |
|
0,03–0,05 |
Rа |
= 2,5–1,25 |
|
||
|
|
|
|
|
|
0,002–0,003 |
|
|
(за три |
– 0,020 |
|
|
|
|
|
|
Rа |
= 0,32–0,08 |
|
||
|
|
|
|
|
|
(за три |
|
|
|
|
|
|
алмазные |
|
|
|
операции) |
|
операции) |
0,005 |
|
|
0,2–0,3 |
зернистостью250/200– |
|
|
800– |
0,006–0,015 |
Rа |
= 2,5–0,63 |
||
|
63/50, 80/63–20/14 |
|
|
1500 |
0,001–0,003 |
Rа |
= 0,32–0,08 |
|
||
|
0,02– |
|
|
|
200–400 |
|
||||
|
|
|
|
(за две |
(за две операции) |
|
||||
|
0,005 |
|
|
|
|
|
||||
|
|
|
|
|
операции) |
|
|
|
|
|
|
|
|
|
|
|
|
|
|
|
|
Суперфиниши– |
|
Бруски: абразивные |
осц = 400–3000 |
100–500 |
0,003–0,005 |
|
Rz = 20–10 |
|
||
рование |
0,01– |
зернистостью 8–5, М40– |
дв.ход/мин с |
|
0,0005– |
Rа |
= 1,25–0,63 |
–0,020 |
||
|
0,025 |
М5; |
амплитудой 2–5мм; |
|
0,001 |
Rа |
= 1,25–0,32 |
|||
|
0,003– |
алмазные зернистостью |
в.п |
– 2–20м/мин; |
|
При |
||||
|
0,003– |
80/63–20/14 |
|
суперфини- |
R |
а |
= 0,32–0,08 |
0,005 |
||
|
дет |
= 10–80 м/мин |
|
|||||||
|
0,008 |
100/80–63/50, |
|
|
|
размерном |
R |
а |
= 0,16–0,08 |
|
|
0,008 |
|
|
|
|
шировании |
Rа |
= 0,08–0,02 |
|
|
|
|
|
|
|
|
|
|
40