
2381
.pdfВ общих случаях в машиноприборостроении повышение точности обрабатываемых деталей и уменьшение параметров шероховатости поверхностей благоприятно влияют на эксплуатационные свойства изделий. Прежде всего это относится к этапам окончательной и финишной обработки деталей и узлов.
Основные виды отклонений формы деталей, обозначения
|
допусков и их значения даны в табл.П.4, П.5 , П.6. |
|
|
|
|
|
||||||||
СибАДИ |
||||||||||||||
|
Вместе с тем при организации производства изделий учитывают |
|||||||||||||
|
эконом ческ |
е |
стороны |
обеспечения |
требований |
качества. |
||||||||
|
Использован е конструкторских, технологических |
и других приемов |
||||||||||||
|
повышен я |
точности, |
уменьшения |
параметров |
|
шероховатости, |
||||||||
|
упрочнен я матер ала поверхностного слоя деталей как правило |
|||||||||||||
|
сопровождается повышением се естоимости изготовления отдельных |
|||||||||||||
|
деталей |
маш ны в целом. Это, в свою очередь, |
связано |
с |
||||||||||
|
использован ем |
о орудования |
с более |
высокими |
требованиями |
|||||||||
|
точности, пр менен ем |
|
средств |
измерений |
с |
более |
высокими |
|||||||
|
характер ст ками |
с |
другими |
расходами. |
Такие |
расходы и |
их |
|||||||
|
прогноз руемая доля в повышении себестоимости деталей в связи с |
|||||||||||||
|
повышен ем |
тре ований |
качества |
применительно |
к |
условиям |
||||||||
|
производства изделий (см. та л. 1.1 , 1.2) приведены в табл. 1.4. |
|
|
|||||||||||
|
|
|
|
|
|
|
|
|
|
|
|
Таблица 1.4 |
||
|
Дополнительные затраты на изготовление прецизионных деталей в связи с |
|||||||||||||
|
обеспечением повышенных требований их качества |
|
|
|
||||||||||
|
|
|
|
|
|
|
|
|
|
|
|
|||
|
|
|
Наименование затрат |
|
|
|
|
|
Доля |
|
|
|||
|
|
|
|
|
|
|
|
|
|
|
|
повышения |
|
|
|
|
|
|
|
|
|
|
|
|
|
|
расходов, |
|
|
|
|
|
|
|
|
|
|
|
|
|
|
% |
|
|
|
Применение дополнительного технологического оборудования, в том |
5–30 |
|
|
||||||||||
|
числе с более высоким классом точности |
более высокой |
|
|
|
|
|
|||||||
|
стоимостью |
|
|
|
|
|
|
|
|
|
|
|
|
|
|
Повышение эксплуатационных расходов на использование |
|
|
10–20 |
|
|
||||||||
|
оборудования с более высокой точностью |
|
|
|
|
|
|
|
|
|||||
|
Применение станочной оснастки с более высокими требованиями |
|
5–15 |
|
|
|||||||||
|
качества |
|
|
|
|
|
|
|
|
|
|
|
|
|
|
Использование инструментальных материалов с более высокими |
|
10–30 |
|
|
|||||||||
|
требованиями, в том числе увеличение доли алмазных материалов |
|
|
|
||||||||||
|
Применение средств измерений с более высокой точностью и средств |
10–20 |
|
|
||||||||||
|
их аттестации |
|
|
|
|
|
|
|
|
|
|
|
|
|
|
Повышение требований качества к предшествующей обработке |
|
5–20 |
|
|
|||||||||
|
Более высокая квалификация производственного персонала |
|
|
5–30 |
|
|
||||||||
|
Увеличение трудоемкости финишных операций технологического |
10–30 |
|
|
||||||||||
|
процесса изготовления деталей |
|
|
|
|
|
|
|
|
|
|
11
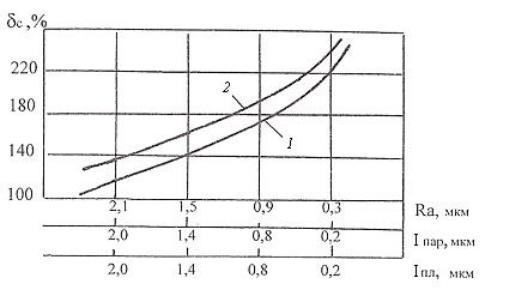
Результаты оценки относительного увеличения себестоимости изготовления золотниковой пары с плоскими поверхностями, приведенные на рис. 1.4, показывают, что обеспечение в процессе изготовлении деталей более высоких требований точности и шероховатости сопровождается повышением себестоимости деталей до
1,5–2 раз.
СибАДИРис.1.4. Изменение относительной се естоимости c изготовления золотниковой пары плоскими поверхностями в зависимости от требований шероховатости Ra,
допуска на плоскость Iпл и допуска на параллельность Iпар сопряженных поверхностей
При оценке экономической целесообразности обеспечения более высоких требований качества изготовления деталей принимают во внимание результирующие показатели качества изделий в целом: повышение ресурса, увеличение герметичности и другие.
Задания и порядок выполнения работы
Задание 1. Повышение эксплуатационных характеристик изделий путем повышения качества поверхностей деталей. учетом данных по влиянию качества поверхностей деталей (cм. табл. 1.1, 1.2, П.7 и П.8 ) на эксплуатационные характеристики изделий из числа трех деталей с определяющими плоскими, наружными и внутренними цилиндрическими поверхностями обоснованно назначить более высокие требования шероховатости и точности. Назначение более высоких требований качества должно преследовать повышение двух эксплуатационных характеристик изделий. Результаты выполнения этого задания привести в табл. 1.5.
12

Таблица 1.5
Назначение повышенных характеристик качества обрабатываемых деталей для увеличения их эксплуатационных свойств
|
Наимено– |
|
Сопря– |
Параметр |
Допуск, мкм |
|
Ожида– |
||||
|
вание |
|
женные |
шероховатости Ra , |
|
|
|
емые |
|||
|
|
СибАДИ |
|
||||||||
|
узла и |
|
поверх– |
мкм |
|
|
|
|
изменения |
||
|
детали |
|
ности |
существу– |
|
предла– |
сущест– |
предла– |
|
характери- |
|
|
|
|
|
ющие |
|
гаемые |
вующие |
гаемые |
|
стик |
|
|
Эск з детали |
Заключение по ожидаемому увеличению эксплуатационных |
|||||||||
|
|
|
|
|
|
|
характеристик каждой детали |
|
|||
|
|
|
|
1 |
|
|
|
|
|
|
|
|
|
|
|
2 |
|
|
|
|
|
|
|
|
|
|
|
3 |
|
|
|
|
|
|
|
|
Задан е 2. Повышение эксплуатационных характеристик изделий |
||||||||||
|
путем |
поверхностного пластического |
деформирования. |
Путем |
экспериментальных исследований решают следующие задачи:
1. Оценка возможности упрочнения поверхностного слоя непосредственно в процессе доводки.
2. Установление закономерности измерения микротвердости поверхностного слоя после упрочнения образцов.
Экспериментальные исследования приведены на стенде, дополнительно оснащенном электромеханическим вибратором типа ВДС-3. Одновременно с выполнением доводки цилиндрических образцов на стенде обеспечена возможность накопления упрочняющих вибраций в заданном режиме. Изменение микротвердости
поверхностного слоя у |
опытных образцов проводится по косым |
шлифам на микротвердомере ПМТ–3 по общепринятой методике. |
|
Исходные условия |
результаты измерений заносят в протокол в |
соответствии с табл.1.6. По результатам измерений составляют заключение о величине упрочнения и глубине упрочненного слоя.
Отчет по выполненной работе должен содержать:
-обоснованные предположения по выбору требований качества обработанных поверхностей, направленных на повышение их эксплуатационных характеристик;
-результаты исследования упрочнения поверхностного слоя образцов в процессе доводки;
-анализ результатов и выводы по каждому заданию.
13
Таблица 1.6
Определение упрочнения поверхностного слоя
|
|
|
|
Исходные условия |
|
|
|
|
Разме– |
|
Материал |
Исходная |
Условия |
Условия измерения |
|
|
ры |
|
|
микротвер– |
подготовки |
микротвердости |
|
|
образца |
|
|
дость ,HRC |
микрошлифа |
|
|
|
|
|
|
|
|
|
|
|
СибАДИ |
|
|||||
|
|
|
|
Результаты измерений |
|
|
|
|
№ |
|
Глуб на |
Отпечаток |
Микротвер– |
Заключение |
|
|
образца |
|
поверхност– |
пирамиды |
дость ,HRC |
|
|
|
|
|
ного слоя |
|
|
|
|
|
|
|
Контрольные вопросы и задания |
|
|
||
|
1.Как е эксплуатационные характеристики изделий зависят от |
||||||
|
точности |
шероховатости сопряженных поверхностей? Примеры. |
|||||
|
2. Возможности повышения эксплуатационных характеристик |
||||||
|
изделий |
путем повышения точности и снижения шероховатости |
сопряженных поверхностей.
3. Неразрывный характер требований точности и шероховатости поверхностей деталей при решении задач повышения эксплуатационных характеристик изделий машиноприборостроения.
4. Какова закономерность повышения эксплуатационных характеристик изделий за счет упрочнения поверхностного слоя пластическим деформированием?
5. Связь реализации приемов повышения точности и снижения шероховатости с экономическими показателями производства машин.
6. Понятие «давление страгивания» в пневматических и гидравлических системах машин.
7. Положительное отрицательное влияние повышения твердости конструкционной стали на эксплуатационные свойства деталей.
8. Закономерности связи параметров шероховатости контактных поверхностей деталей на герметичность соединений узлов.
14

Лабораторная работа 2
ТЕХНОЛОГИЧЕСКИЕ ВОЗМОЖНОСТИ МЕТОДОВ ОТДЕЛОЧНОЙ АБРАЗИВНОЙ ОБРАБОТКИ
СибАДИ |
|||||||
Цель работы: закрепить знания и получить навыки обоснования |
|||||||
выбора методов отделочной абразивной обработки с учетом конст- |
|||||||
рукторско-технолог ческих характеристик прецизионных деталей. |
|||||||
|
|
Краткие сведения |
|
|
|
||
Технолог |
ческ е схемы и условия процессов тонкой абра- |
||||||
|
|
зивной обработки |
|
|
|
||
Характерные о ъекты а разивной обработки даны в табл. П.1. |
|||||||
Бесцентровое |
шл фование. При многообразии процессов шли- |
||||||
фован я при обра отке цилиндрических бесступенчатых деталей и |
|||||||
сборочных ед н ц |
ез фланцев и уступов значительную часть зани- |
||||||
мают процессы |
есцентрового шлифования на проход. Схема такого |
||||||
шлифования приведена на рис. 2.1. |
|
|
|
|
|||
|
|
При |
есцентровом шлифовании обрабаты- |
||||
|
|
ваемая деталь 1 (см. рис. 2.1) устанавливается на |
|||||
|
|
опорный нож 4 между шлифовальным 2 и |
веду- |
||||
|
|
щим 3 кругами. Шлифовальный круг вращается |
|||||
|
|
со скоростью |
|
|
|
|
|
|
|
К = 30–60 м/с, а ведущий – со скоростью |
В |
||||
|
|
= 10–40 м/мин. Так как коэффициент трения ме- |
|||||
|
|
жду 3 деталью больше, чем между деталью и |
|||||
|
|
кругом 2, то ведущий круг сообщает детали вра- |
|||||
|
|
щение со скоростью круговой подачи В . |
|
||||
Рис. 2.1. Схема и рабочий цикл бесцентро- |
Продольная |
подача |
достигает |
||||
вого проходного шлифования: 1– шлифо- |
при повороте оси ведущего круга на |
||||||
вальный круг; 2– ведущий круг; 3– обра- |
угол . Окружная скорость ведущего |
||||||
батываемая деталь; 4– опорный нож; |
круга В |
разлагается на |
две состав- |
||||
lвх – передняя (направляющая ) часть |
|||||||
опорного ножа; l– длина обрабатываемой |
ляющие: |
скорость |
вращения |
детали |
|||
детали; lпр – задняя (приемная ) часть |
(круговую подачу) |
Д и продольную |
|||||
опорного ножа |
|
|
|
|
|
|
15

подачу s = В sin . Чтобы обеспечить линейный контакт ведущего круга с цилиндрической поверхностью детали, ведущему кругу в процессе правки придают форму гиперболоида.
Жесткость технологической системы бесцентровошлифовальных станков в 1,5–2 раза выше жесткости круглошлифо-
|
вальных станков, поэтому и режим резания при бесцентровом шли- |
|||||||||||||||||||
СибАДИ |
||||||||||||||||||||
|
фовании повышают примерно в 1,5–2 раза. Бесцентровое шлифование |
|||||||||||||||||||
|
обеспеч |
вает обработку деталей с точностью 5–6-го квалитета. |
||||||||||||||||||
|
Назначаемые |
|
выходные параметры бесцентрового шлифова- |
|||||||||||||||||
|
ния на проход пр ведены в табл. 2.1, 2.2. |
|
|
|
Таблица 2.1 |
|||||||||||||||
|
Ч сло о означение операций при бесцентровом шлифовании на |
|||||||||||||||||||
|
|
|
|
|
|
|
|
|
проход |
|
|
|
|
|
|
|
||||
|
Исходная |
|
|
|
|
|
|
|
Отклонения формы, мм |
|
|
|
|
|
||||||
|
точность |
|
|
|
|
|
|
|
|
|
|
|
|
|
|
|
|
|
|
|
|
формы, мм |
|
0,1– |
|
0,05–0,1 |
|
0,03– |
|
0,015– |
|
0,01– |
|
0,005– |
0,0025– |
|
|||||
|
|
|
0,15 |
|
|
|
|
|
0,05 |
|
|
0,03 |
|
0,015 |
|
0,01 |
|
0,005 |
|
|
|
|
|
|
|
|
|
|
|
Стали |
|
|
|
|
|
|
|
|
|
||
|
0,15–0,3 |
|
1; а |
|
2; а, |
|
3; а –в |
|
4; а – г |
|
5; а – д |
|
6; а – е |
7; а – ж |
|
|||||
|
0,10–0,15 |
|
– |
|
|
1; |
|
2; , в |
|
3; б – г |
|
4; б – д |
|
5; б – е |
6; б – ж |
|
||||
|
0,05–0,10 |
|
– |
|
|
– |
|
1; в |
|
2; в, г |
|
3; в – д |
|
4; в – е |
5; в – ж |
|
||||
|
0,03–0,05 |
|
– |
|
|
– |
|
– |
|
1; г |
|
2; г, д |
|
3; г – е |
4; г – ж |
|
||||
|
0,015–0,03 |
|
– |
|
|
– |
|
– |
|
– |
|
|
1; д |
|
2; д, е |
3; д – ж |
|
|||
|
0,01–0,015 |
|
– |
|
|
|
|
|
– |
|
– |
|
|
– |
|
1; е |
2; е, ж |
|
||
|
0,005–0,01 |
|
– |
|
|
|
|
|
|
|
|
|
|
|
– |
|
– |
1; ж |
|
|
|
Исходная |
|
|
|
|
|
|
|
Отклонения формы, мм |
|
|
|
|
|
||||||
|
точность |
|
|
|
|
|
|
|
|
|
|
|
|
|
|
|
|
|
|
|
|
|
0,05–0,10 |
|
0,03–0,05 |
|
|
0,01–0,03 |
|
0,005–0,010 |
|
0,0025– |
|
||||||||
|
формы, мм |
|
|
|
|
|
|
|||||||||||||
|
|
|
|
|
|
|
|
|
|
|
|
|
|
|
|
|
|
|
0,005 |
|
|
|
|
|
|
|
|
|
|
Чугуны |
|
|
|
|
|
|
|
||||
|
|
|
|
|
|
|
|
|
|
|
|
|
||||||||
|
0,15–0,3 |
|
1; а |
|
|
|
2; а, |
|
3; а – в |
|
4; а – г |
|
5; а – д |
|||||||
|
0,10–0,15 |
|
|
|
|
|
|
|
1; б |
|
2; б, в |
|
3; б – г |
|
4; б – д |
|
||||
|
0,05–0,10 |
|
|
|
|
|
|
|
– |
|
1; в |
|
2; в, г |
|
3; в – д |
|
||||
|
0,02–0,05 |
|
|
|
|
|
|
|
– |
|
– |
|
|
1; г |
|
2; г, д |
|
|||
|
0,005–0,02 |
|
|
|
|
|
|
|
– |
|
– |
|
|
– |
|
1; д |
|
16

Таблица 2.2
Глубина шлифования (мм), характеристика круга и параметр шероховатости поверхности при бесцентровом шлифовании на проход стальных
и чугунных деталей
|
Обо |
Удвоенная |
Характеристика круга при обработке деталей |
|
Ra, мкм, |
||||||||||
|
зна- |
СибАДИ |
при обра- |
||||||||||||
|
глубина шли- |
|
|
|
|
|
|
|
|
|
|
||||
|
че- |
фован |
я дета- |
|
стальных |
|
|
|
Чугунных |
|
|
ботке де- |
|||
|
ние |
лей |
|
|
|
|
|
|
|
|
|
|
талей |
|
|
|
опе |
|
|
|
|
|
|
|
|
|
|
|
|
|
|
|
ра- |
|
|
|
|
|
|
|
|
|
|
|
|
|
|
|
ции |
|
|
|
|
|
|
|
|
|
|
|
|
|
|
|
|
таль- |
чугун |
зерна Матер ал |
Зерн стость |
Твердость |
Структура |
Связка |
зерна Материал |
Зернистость |
Твердость |
Структура |
Связка |
тальных C |
Чугунных |
|
|
ных |
-ных |
|
|
|
|
|
|
|
|
|
|
|
|
|
а |
0,20– |
0,2– |
|
50 |
СТ2 |
|
|
|
50 |
СТ1 |
|
|
1,6– |
0,8– |
|
|
0,35 |
0,35 |
|
40 |
СТ1 |
|
|
|
40 |
С2 |
|
|
3,2 |
1,6 |
|
б |
0,15– |
0,15– |
|
40 |
С2 |
|
|
|
40 |
С1 |
|
|
0,8– |
0,8 |
|
|
0,2 |
0,2 |
|
|
СТ1 |
|
|
|
|
|
|
|
1,6 |
|
|
в |
0,10– |
0,10– |
|
25 |
С1 |
|
|
54С |
25 |
СМ2 |
|
|
0,8 |
0,4 |
|
|
0,15 |
0,15 |
|
|
С2 |
|
|
|
|
С1 |
5 |
К |
|
|
|
г |
0,05– |
0,05– |
15А |
16 |
С1 |
5 |
К8 |
|
16 |
СМ2 |
|
|
0,4– |
0,2– |
|
|
0,1 |
0,1 |
|
25 |
С2 |
|
|
|
|
С1 |
|
|
0,8 |
0,4 |
|
д |
0,03– |
0,015 |
|
12 |
С1 |
|
|
63С |
12 |
СМ2 |
|
|
0,4 |
0,2– |
|
|
0,05 |
–0,03 |
|
16 |
С2 |
|
|
|
|
С1 |
|
|
|
0,4 |
|
е |
0,015– |
– |
|
10 |
С1 |
|
|
|
– |
– |
|
|
0,2– |
– |
|
|
0,03 |
|
|
12 |
С2 |
|
|
|
|
|
|
|
0,4 |
– |
|
ж |
0,01– |
– |
63 |
М40 |
С1 |
|
Б1 |
– |
– |
– |
|
|
0,1– |
|
|
|
0,015 |
|
|
М28 |
С2 |
|
ГФ |
|
|
|
|
|
0,2 |
|
|
|
|
|
|
|
|
|
|
|
|
|
|
|
|
|
|
|
|
|
|
|
|
|
|
|
|
|
|
|
|
|
17

Для тонкого шлифования характерны припуски 0,04–0,06 мм на диаметр с назначением чистового режима резания:
- скорость круга, м/с – 35 - скорость детали, м/мин – 20–45
Продольная подача в долях ширины круга на 1 оборот детали составляет 0,1–0,2 мм. Поперечная подача – 0,005–0,01 мм.
СибАДИПри назначении условий тонкого шлифования обязательным критер ем выбора является предотвращение дефектов поверхностей и матер ала поверхностного слоя обрабатываемых изделий. Эти дефекты могут проявляться в виде прижогов, дроблений поверхностей и изменен й состоян я материала поверхностного слоя обрабатываемого издел я.
Эффект вным приемом предотвращения дефектов является применен е смазочно-охлаждающих технологических сред (СОТС).
Хон нгован е. Процесс хонингования обеспечивает жесткое взаимодейств е а раз вных зерен обрабатывающего инструмента и обрабатываемой поверхности детали. Схема процесса приведена на рис. 2.2.
а
Рис. 2.2. Схемы хонингования: а – схемы резания при хонинговании; б – схемы установки и крепления детали и инструмента при хонинговании
Хонингование снижает отклонения формы и повышает размерную точность, уменьшает параметр шероховатости поверхности, сохраняет микротвердость и структуру поверхностного слоя, увеличивает несущую поверхность и остаточные сжимающие напряжения.
18
Наибольшая эффективность достигается алмазным хонингованием. Износ алмазно-металлических брусков по сравнению с абразивными уменьшается в 150–250 раз, благодаря чему упрощается наладка и стабилизируется качество обработки. Хонингованием обрабатываются детали из стали, чугуна и цветных металлов, преимущест-
|
венно отверстия (сквозные и гладкие, с гладкой и прерывистой по- |
|||||||||
СибАДИ |
||||||||||
|
верхностью, цилиндрические и конические, круговые и некруговые) |
|||||||||
|
диаметром 6–1 500 мм, длиной от 10 мм до 2 000 мм. |
Таблица 2.3 |
||||||||
|
|
|
Пр пуск |
операции при хонинговании отверстий |
||||||
|
Отклоне- |
Параметр |
|
Опера- |
Припуск |
Отклонения |
Параметр |
|
||
|
ние формы |
шероховато- |
|
ция |
на опе- |
формы от- |
шероховато- |
|
||
|
отверст |
я |
сти поверх- |
|
|
рацию, |
верстия по- |
сти поверх- |
|
|
|
в исход- |
ности в |
с- |
|
|
мкм |
сле хонинго- |
ности после |
|
|
|
ном со- |
|
ходном со- |
|
|
|
вания, мкм |
хонингования |
|
|
|
стоян |
, |
стоян |
Ra, |
|
|
|
|
Ra, мкм |
|
|
мкм |
|
мкм |
|
|
|
|
|
|
|
|
100–150 |
3,2–6,3 |
|
Первая |
150–200 |
15–20 |
0,8–1,6 |
|
||
|
|
|
|
|
|
Вторая |
20–30 |
6–10 |
0,2–0,4 |
|
|
|
|
|
|
|
Третья |
12–15 |
4–5 |
0,1–0,2 |
|
|
50–90 |
|
|
|
|
Первая |
80–120 |
10-18 |
0,8–1,6 |
|
|
|
|
|
|
|
Вторая |
15–25 |
5–9 |
0,2–0,4 |
|
|
|
|
|
|
|
Третья |
8–12 |
3–4 |
0,1–0,2 |
|
|
25–40 |
|
1,6–3,2 |
|
Первая |
50–70 |
8–12 |
0,4–0,8 |
|
|
|
|
|
|
|
|
Вторая |
12–15 |
4–6 |
0,2–0,4 |
|
|
|
|
|
|
|
Третья |
6–12 |
2–3 |
0,1–0,2 |
|
|
12–20 |
|
0,63–2,5 |
|
Первая |
20–35 |
5–9 |
0,2–0,8 |
|
|
|
|
|
|
|
|
Вторая |
10–12 |
2–3 |
0,1–0,2 |
|
|
|
|
|
|
|
|
|
|
|
|
|
6–12 |
|
|
|
|
Первая |
15–20 |
2–4 |
0,2–0,4 |
|
|
|
|
|
|
|
Вторая |
4–6 |
1–2 |
0,1–0,2 |
|
|
При хонинговании |
абразивным бруском совершаются возврат- |
||||||||
|
но-поступательное |
вращательное движения, в результате которых |
на обработанной поверхности абразивными зернами образуются царапины.
При хонинговании в резании одновременно участвует большое число абразивных зерен, в результате чего обеспечиваются высокая производительность, низкие давление и температура в зоне резания (50–150 С) и, как следствие, сохранение исходной структуры поверх-
19
ностного слоя. Бруски работают в условиях самозатачивания и не требуют правки.
Назначаемые условия хонингования и выходные параметры процесса приведены в табл. 2.3, 2.4.
Таблица 2.4
СибАДИ |
||||
|
Припуск при хонинговании отверстий в зависимости от параметра |
|||
|
|
шероховатости поверхности |
||
|
Параметр шероховатости |
Рекомендуемый припуск, мкм |
|
|
|
поверхности Ra, мкм |
|
|
|
|
в исходном |
тре уемый |
|
|
|
состоян |
|
|
|
|
2,5–10 |
0,63–2,5 |
30–40 |
|
|
1,25–5 |
0,32–1,25 |
25–30 |
|
|
0,32–1,25 |
0,16–0,63 |
15–20 |
|
|
0,16–0,63 |
0,08–0,32 |
10–15 |
|
|
0,08–0,32 |
0,04–0,16 |
5–10 |
|
Снимаемый припуск и вы ор операций зависят от того, насколько нужно повысить точность формы отверстия и уменьшить параметр шероховатости. Если основная цель операции сводится к уменьшению отклонений формы отверстия, припуск устанавливается по разности между отклонениями формы отверстия в исходном состоянии с заданными отклонениями. После установления общего припуска назначают число операции, распределяют припуск по операциям и подбирают характеристику режущих брусков. Обработка в несколько операций вызвана невозможностью обеспечить большой съем металла и одновременно низкий параметр шероховатости поверхности одними теми же брусками. Большой припуск при хонинговании можно снять крупнозернистыми брусками, которые, срезая металл, сохраняют параметр шероховатости поверхности, необходимый для самозатачивания брусков. Поэтому основной припуск следует снимать на первой операции. На чистовых операциях припуск должен быть достаточным лишь для удаления шероховатости поверхности после предварительного хонингования. Параметр шероховатости поверхности Ra=0,4– 0,8 мкм надежно обеспечивается одной операцией хонингования.
Алмазный инструмент на металлической связке применяют для обработки деталей из чугунов, закаленных сталей со снятием боль-
20