
2308
.pdf
Таблица 4.1
Зависимость относительной концентрации сил на разноразмерных зернах
d, см |
d1, см |
d/d1, см |
d – d1, см |
r, см |
P*/P |
|
1,2 |
0,4 |
3,0 |
0,8 |
1,58 |
6,93 |
|
0,8 |
1,5 |
0,4 |
1,00 |
2,77 |
||
|
1,2 |
1,0 |
0,0 |
0,60 |
1,00 |
|
0,8 |
0,4 |
2,0 |
0,4 |
0,77 |
3,71 |
|
0,8 |
1,0 |
0,0 |
0,40 |
1,00 |
||
|
||||||
0,6 |
0,4 |
1,5 |
0,2 |
0,49 |
2,67 |
|
0,6 |
1,0 |
0,0 |
0,30 |
1,00 |
||
|
Рассмотрим теперь расчетную схему II, соответствующую потере устойчивости в форме горизонтального смещения шара (см. рис. 4.1, б) за счет отрыва и смятия подложки на половине боковой поверхности шарового сегмента и сопротивления сдвигу. Очевидно, это произойдет при σотр > Rрасч, σсж > Rсж (здесь Rрасч и Rсж – пределы прочности на растяжение и сжатие материала подложки). Поэтому условие устойчивости шара для схемы II представим как равенство момента от силы Q моменту от сил сопротивления отрыву, сжатию и сдвигу:
Q |
|
|
|
|
|
1 |
|
|
|
|
2 |
|
|
|
|
|
d |
|
d W R |
R |
|
|
3 |
|
24PE2 |
|
tg c h 2d h |
. (4.13) |
|||||||||
2 |
|
2π |
|
|
||||||||||||||
|
сж |
|
рост |
|
|
|
1 μ |
2 |
2d2 |
|
|
|
n |
n 4 |
||||
|
|
|
|
|
|
|
|
|
|
|
|
|
|
|
|
|
|
Расчетной схеме III свойственны явления отрыва, сжатия и среза по боковым граням пирамиды и сдвига по ее основанию. Поэтому, заменяя σотр = Rраст, σcж = Rсж и вводя срез Rср и сдвиг в форме τ = σcж tgφ+ с, получим равенство моментов от силы Q и всех сил сопротивления горизонтальному смещению пирамиды в подложке, то есть уравнение устойчивости, аналогичное уравнению (4.13).
Расчетной схеме IV свойственна потеря устойчивости положения в результате поворота ее вокруг ребра основания (cм. рис. 4.1, б) с преодолением сопротивления срезу τср, сжатию σcж и отрыву σотр. Полагая эти величины равными пределам прочности (τср = Rср; σcж = Rсж и σотр = Rотр), получим условие устойчивости. При введении в уравнения (4.12), (4.13) приемлемых значений d, hn можно установить производственную норму массы подложки на удельный измеритель и массу зерен, укладываемых в ряд. При этом учтем механические свойства материалов подложек, применяемых для устройства поверхностных обработок.
При расчете устойчивости вычислим коэффициент запаса, равный
отношению удерживающего момента к сдвигающему: Кз |
|
М |
уд |
. Удер- |
|
Мсдв |
|||||
|
|
|
живающие моменты представлены правой частью выражений (4.12) и
68
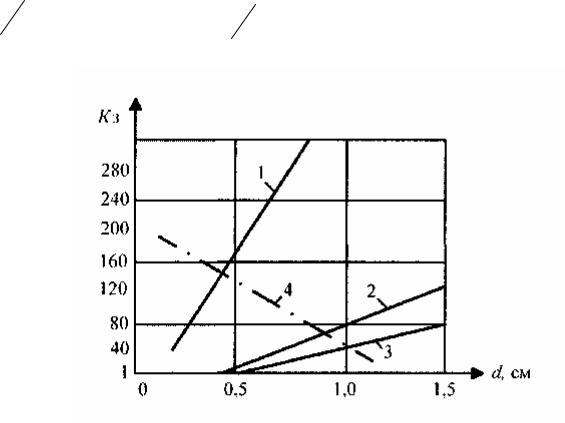
(4.13) для двух схем (см. рис. 4.1, б), а сдвигающие – левой частью этих же выражений.
Если Кз > 1, то устойчивость положения обеспечена. Если Кз < 1, то устойчивость предельна или отсутствует. Примем в расчетах qx = 0,6 МПа; τу = 0,3 МПа; W = 0; Е0 = 5000 МПа; μ0 = 0,2; tgφ = tg30°; с = 0,01 МПа; d = 0,4; 0,6; 0,8; 1,0 и 1,2 см. Учтем, что в выражениях (4.12), (4.13) при разноразмерных шарах вместо Р подставляется Р* в соответствии с табл. 4.1. Результаты расчетов, приведенные на рис. 4.2, показывают, что потеря устойчивости положения путем проворота шара в подложке вокруг центра наблюдается только у зерен размером 4 мм и менее (Кз < 1). Зерна диаметром 12 мм и более также неустойчивы (Кз < 1), однако потеря положения здесь наблюдается уже по схеме II (см. рис. 4.1, б), то есть путем горизонтального смещения. Поэтому одноразмерные шары диаметром от 4 до 12 мм устойчивы в подложках с минимальной толщиной 0,05...0,1мм. Введение в ряд одноразмерных шаров диаметром d1 хотя бы одного шара диаметром d (причем d > d1) обязательно приводит к потере его устойчивости по схеме I за счет концентрации вертикальных и касательных сил на нем и разгрузки окружающих его шаров меньшего диаметра. Так, при
hn d = 0,05, d = 0,6...1,2 см и d d1 = 1…3 значения Кз составляют 0,2…0,5,
и не приближаются к единице.
Рис. 4.2. Зависимость коэффициента запаса устойчивости зерна в подложке от диаметра: 1, 2, 3 – для схемы I (см.рис. 4.1, б) при hn/d = 0,5; 0,1 и 0,05; 4 – для схемы II (см.рис. 4.1, б) при hn/d = 0,05
69

Поверхностные обработки изношенных покрытий автомобильных дорог, устроенные путем приклеивания к ним зерен минеральных или искусственных материалов или втапливания, с течением времени и под влиянием многократного загружения способны к постепенному погружению в слой покрытия. Это возможно при достаточной толщине покрытия, недостаточной насыщенности его основным минеральным материалом и пластическими свойствами. При полном погружении зерен поверхностной обработки в покрытие исчезает ее основное предназначение – обеспечение сцепления колеса с дорогой, время на это погружение можно считать сроком службы. Рассмотрим условие погружения зерна диаметром d, загруженного силой Р в слой толщиной h и обладающего модулем деформации Ед и коэффициентом Пуассона ν. На границе слоя с зерном возникнут максимальные напряжения
|
16РЕ2 |
Е2 |
|
1 |
|
|
|
3 |
|
||||
0,388 |
1 |
0 |
|
, |
(4.14) |
|
Е1 Е0 2 d2 |
||||||
|
|
|
|
здесь Р = 0,25gπd2; gx = 0,6 МПа – вертикальное давление под колесом пневматической шины расчетного грузового автомобиля; Е1 – модуль упругости зерна.
Загружение слоя покрытия через зерно-шар будет осуществляться через круговую площадку радиусом а:
|
2 |
|
1 |
|
|
3 |
|
|
|||
а |
31 |
Pd |
|
, |
(4.15) |
8E |
|
|
|||
|
|
|
|
|
поэтому напряжение сжатия на глубине h составит, по М.Б. Корсунскому,
h |
|
|
max |
|
, |
(4.16) |
||
|
|
h 2 |
|
|||||
|
|
|
|
|||||
|
|
1 1,85 |
|
|
|
|
||
|
|
|
||||||
|
|
|
|
2a |
|
|
||
|
|
|
|
|
|
|
|
а среднее напряжение в слое ср max h |
2. |
|
|||||||||||
Очевидно, что к концу загружения зерна-шара на глубину d напряже- |
|||||||||||||
ния сжатия будут h P1,57d2 , а на глубине h = d они составят |
|
||||||||||||
h |
|
1 |
|
d |
2 |
d |
2 |
|
|||||
|
|
|
1 1,85 |
|
|
|
|
. |
(4.17) |
||||
|
|
|
|
|
|||||||||
1,57 |
|
|
d |
|
|
|
|||||||
|
|
|
|
|
|
|
|
|
|
|
|
|
|
Среднее напряжение в слое под зерном к концу нагружения составит |
|||||||||||||
|
|
|
|
|
|
2 |
|
|
|
|
|||
|
|
|
|
d |
|
|
|
|
|||||
|
|
|
1 1,85 |
|
|
P |
|
||||||
|
|
|
|
||||||||||
ср |
|
|
d |
|
|
. |
(4.18) |
||||||
|
d2 |
|
|
|
|
|
|||||||
|
|
|
|
|
|
|
|
|
|
|
|
Среднее напряжение в слое под зерном в процессе нагружения
ср 0,50,5 max h ср
70

|
|
|
|
|
|
|
|
|
|
|
|
|
1 |
|
|
|
|
|
|
|
|
|
|
|
|
|
|
|
0,5P |
|||
0,25 max 1 |
|
|
|
|
|
|
|
|
1 |
|
|
|
h 2 |
|
d2 |
||||||
|
|
|
|
|||||||
|
1 1,85 |
|
|
|
|
|
|
|
||
|
|
|
||||||||
|
|
2a |
|
|
|
|||||
|
|
|
|
|
|
|
|
|||
|
|
|
|
|
|
|
|
|
|
|
|
|
|
|
1 |
|
|
|
|
|
|
|
|
|
|
||
|
|
|
|
|
. |
|
|
d 2 |
|
||||
|
||||||
1 1,85 |
|
|
|
|
||
|
||||||
|
d |
|
||||
|
|
|
|
|
(4.19)
Рассчитаем σmax и σср для двух видов асфальтового бетона (из горячей и холодной смесей) и для диаметров зерен 4,8 и 12 мм. Расчет сведем в табл. 4.2 при gx = 0,6 МПа и h = 5 см. Деформативные и механические свойства материалов покрытий, на которых устраивается поверхностная обработка, примем по нормалям дорожной отрасли. Учтем также, что число нагружений полосы наката проезжей части дорог расчетной колесной нагрузкой за 10 лет на дорогах III технической категории может достигать 6,0 млн, а число месяцев в году, когда асфальтобетонное покрытие достаточно пластично, чтобы не препятствовать погружению зерен, достигает 6…8 месяцев. Определим теперь срок службы поверхностной обработки в предположении, что концом этого срока можно считать вдавливание зерна в асфальтобетонное покрытие на глубину h = d при общем числе нагружений Nобщ напряжениями σcpi. По аналогии с методологией Н.Н. Иванова, допускающей накопление остаточных деформаций,
Ед |
|
cpi |
К |
|
|
|
|
, |
(4.20) |
||
|
|
||||
|
|
2 |
|
здесь λ – относительная остаточная деформация, равная d/h. При полном погружении зерна d = h, λ = 1; Ед – модуль деформации асфальтового бетона покрытия; μ – коэффициент неоднородности асфальтового бетона покрытия; К – коэффициент, учитывающий многократность нагружения, определяемый по формуле
12 Nобщ
К 0,5 0,65 lg , (4.21)365Ti
где Nобщ – общее количество нагружений дорожной одежды расчетной колесной нагрузкой за 10 лет; i – число теплых месяцев в году с температурой покрытия выше 0 °С; γ – коэффициент, принимаемый для двухполосной проезжей части равным 1, для четырехполосной γ = 0,75.
Таблица 4.2
Максимальные и средние напряжения сжатия под зерном-шаром, погружаемым в покрытие
Материал покрытия |
Eд, МПа |
d, см |
P, кгс |
σmax, МПа |
а, см |
σср, МПа |
|
Асфальтобетон плотный I-II |
5000 |
0,4 |
0,75 |
199,82 |
0,012 |
51,0 |
|
0,8 |
3,01 |
199,82 |
0,240 |
51,0 |
|||
марки (БНД 40/60) |
|||||||
|
1,2 |
6,78 |
199,82 |
0,036 |
51,0 |
||
|
|
||||||
Асфальтобетон холодный |
1800 |
0,4 |
0,75 |
107,9 |
0,016 |
26,5 |
|
|
|
0,8 |
3,01 |
107,9 |
0,032 |
26,5 |
|
|
|
71 |
|
|
|
|

1,2 6,78 107,9 0,048 26,5
Срок службы поверхностной обработки Т определяется подстановкой
(4 .2 1 ) в (4 .20) из равенства
|
12γNобщ |
|
2E |
д |
λ |
|
||
lg |
|
|
|
|
|
. |
(4.22) |
|
|
|
|
|
|||||
|
356Ti |
|
|
cpi |
|
|||
|
|
|
|
Расчеты по этому равенству при Ед = 300 МПа; d = 0,4 см; μ = 1,2; Nобщ = 6 млн автомобилей; i = 6 месяцев показывают, что Т = 3,28 года. При E0 = 180 МПа, d =1,2 см; μ =1,2; Nобщ = 6 млн автомобилей получаем
Т = 0,656 года.
Таким образом, поверхностная обработка из мелкого камня d = 0,4 см может иметь срок службы до 3,28 года на асфальтобетонном покрытии из горячей плотной смеси. На покрытии из холодной асфальтобетонной смеси обработка камнем диаметром до 1,2 см служит лишь 6 месяцев. Следует подчеркнуть, что указанные сроки службы вычислены только из условия полного втапливания каменных частиц в слой изношенного покрытия и потери им сцепных свойств с колесом.
На этом основании можно сделать выводы, регламентирующие размер зерен поверхностных обработок, их массы и нормы распределения клеящей подложки:
1.Шаровидные зерна диаметром менее 4 мм при толщине подложки 0,05...0,1 диаметра неустойчивы под одновременным действием горизонтальных и вертикальных сил от колесной нагрузки грузового автомобиля. Неустойчивость их проявляется в повороте вокруг центра шара без горизонтального смещения.
2.Шаровидные зерна диаметром более 12 мм при толщине подложки 0,05 диаметра неустойчивы. Неустойчивость проявляется в горизонтальном смещении зерна.
3.При толщине подложки от 0,1 до 0,5 диаметра зерна любых размеров устойчивы к горизонтальному смещению. При толщине подложки более 0,2 диаметра зерна любых размеров устойчивы к повороту вокруг центра зерна.
4.Наличие в ряду одноразмерных зерен диаметром d1 хотя бы одного зерна большего диаметра d (d > d1) приводит к потере его устойчивости за счет перераспределения горизонтальных и вертикальных давлений от колесной нагрузки и концентрации их на зерне большего диаметра.
5.Устройство поверхностных обработок как способ ремонта изношенных покрытий дорог возможно из щебня, дробленого гравия или искусственных материалов из частиц шаровидной, пирамидальной или произвольной формы, вписывающихся в шар диаметром 4, 6, 8, 10, и 12 мм. При этом норма равномерного распределения частиц в один ряд должна
72
составлять соответственно 5,2; 8,2; 11,2; 20,6; 30 кг/м2, а норма розлива битума 0,4; 0,6; 0,8; 1,0 и 1,2 л/м2.
6. Срок службы поверхностных обработок дорог может достигать 3 и 0,5 года для покрытий из горячей плотной и холодной асфальтобетонных смесей соответственно.
Дополнительно к этим выводам инж. Д.Н. Рыспаев и Д.Н. Перешивко определили теоретически и экспериментально область устойчивости шероховатой поверхностной обработки дорог (ШПО), устроенной путем приклеивания щебня правильной геометрической формы с помощью битума. Последний при отрицательной температуре приобретает хрупкие свойства.
Автомобильное колесо соприкасается с поверхностью покрытия не по всей площади контакта, а только в местах выступов шероховатости. Этими выступами являются отдельные минеральные зёрна. Поэтому считается, что нагрузка от колеса автомобиля распределяется на то количество щебёнок, которые попадают в площадь контакта.
Нагрузку, приходящуюся на одну щебёнку, определяют по формулам:
P |
P |
|
m k ; |
(4.23) |
|
|
|||||
|
|
N |
|
||
Q |
Qд |
m k , |
(4.24) |
||
|
|||||
|
|
N |
|
где P – вертикальная нагрузка на одну щебёнку; Q – касательное усилие, приложенное к одной щебёнке; N – количество минеральных зёрен, попавших в площадь контакта; m – коэффициент, учитывающий неравномерность распределения нагрузки между щебёнками из-за их переменной формы и размера. Принимает значения, близкие к 1, если для устройства поверхностной обработки использован щебень узких фракций; k – коэффициент неравномерности распределения нагрузки в площади контакта.
Введение коэффициентов m и k позволяет определять максимально возможные усилия при заданных условиях. Задача о расчёте устойчивости каменного материала в слое поверхностной обработки сводится к определению предельного касательного усилия, которое может выдержать одна наиболее загруженная щебёнка. Это определяет выбор расчётной схемы: рассматривается одиночная щебёнка в слое битума (при отрицательной температуре воздуха), на которую действуют силы P и Q. Для расчётной схемы выбрана форма щебня в виде прямоугольного параллелепипеда со сторонами a, b и c.
Расчётные схемы приведены на рис. 4.3 и 4.4 (для наглядности щебёнка изображена в устойчивом и неустойчивом положениях).
По приведённым расчётным схемам можно определить предельное касательное усилие, которое может быть воспринято щебёнкой без её отрыва (то есть максимальное удерживающее усилие) Qудерж. Сила Qудерж определяется из условия равенства нулю суммы моментов всех действующих на щебёнку усилий относительно точки О:
73

|
|
|
|
|
|
МО 0. |
|
|
|
|
|
|
|
|
(4.25) |
|||||||
Из этого условия следует |
|
|
|
|
|
|
|
|
|
|
|
|
|
|
|
|
||||||
|
|
1а |
|
2 a2 |
b |
|
2 |
а |
|
|
a b h |
|
2 |
а |
|
4 a2 |
h |
|
|
|||
Qудерж |
3 c |
|
|
|
c |
3 c |
, |
(4.26) |
||||||||||||||
|
|
|
|
|
|
|
|
|
||||||||||||||
|
|
|
|
|
|
|
|
|
|
|
|
|
|
|
|
|
||||||
|
|
|
|
|
|
|
|
|
1 |
|
h |
|
|
|
|
|
|
|
|
|
|
|
|
|
|
|
|
|
|
|
|
|
|
|
|
|
|
|
|
|
|
c
где σ1а – предельное напряжение на границе приклеивания каменного материала к битуму при отрыве, Н/см2; σ2а – предельное напряжение на границе приклеивания каменного материала к битуму на срез, Н/см2. Предельное удерживающее усилие рассчитано по (4.26) и вместе с экспериментальными данными приведено на рис. 4.5–4.7.
Рис. 4.3. Устойчивое положение минерального зерна в слое поверхностной обработки: а – размеры расчётной щебёнки; б – расчётная схема
Рис. 4.4. Неустойчивое положение минерального зерна в слое поверхностной обработки: а – размеры расчётной щебёнки; б – расчётная схема
Предельное удерживающее усилие Qудерж, кгс
Рис. 4.5. Теоретическая (а) и экспериментальная (б) зависимости предельной
74
удерживающей силы Qудерж от толщины плёнки битума h
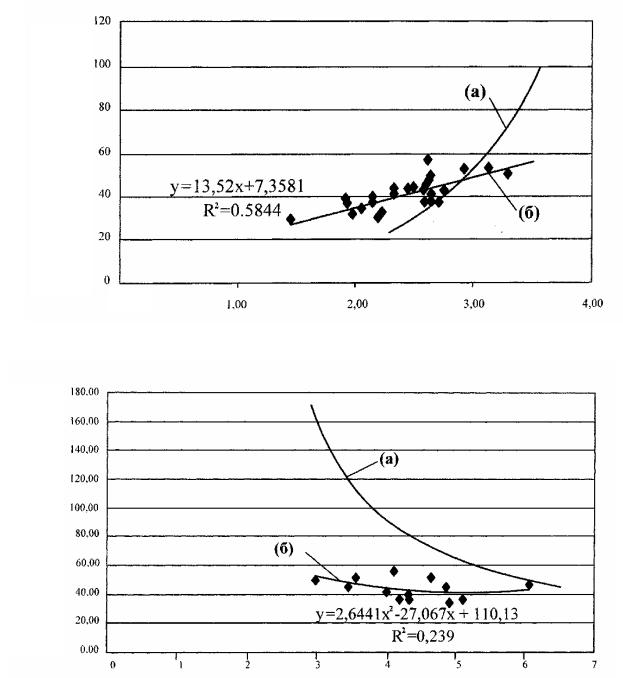
Предельное удерживающее усилие Qудерж, кгс
0
Рис. 4.6. Теоретическая (а) и экспериментальная (б) зависимости предельной удерживающей силы Qудерж от площади контакта щебёнки с битумом
Предельное удерживающее усилие Qудерж, кгс
Рис. 4.7. Теоретическая (а) и экспериментальная (б) зависимости предельной удерживающей силы Qудерж от высоты минерального зерна в слое ШПО
Из результатов совпадения экспериментов с теоретическим уравнением (4.26) следует, что отдельное зерно (щебенка) не будет вырвано из хрупкой пленки битума толщиной не менее 1 мм, а размер кубовидного зерна – не менее 7 мм. Это частично совпадает с предыдущими выводами, но одновременно требует более углубленного анализа и решения задач устойчивости механики зернистой среды.
75
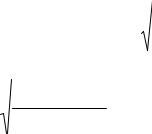
5. ДОРОЖНЫЕ КОНСТРУКЦИИ КАК КОЛЕБАТЕЛЬНЫЕ СИСТЕМЫ
Реальные конструкции дорог и аэродромов имеют чаще всего неоднородные грунтовые основания, состоящие из насыпей, искусственно уплотненных, и грунтов естественного сложения. Последние могут быть слабыми (например, торфяные грунты), искусственно промороженными или из вечномерзлых грунтов. В зависимости от целей расчета дорожных конструкций (например, расчет на допустимую осадку грунтовой конструкции от собственной массы, расчет покрытия на прочность от действия временной подвижной нагрузки и т. д.) эти сложные конструкции земляного полотна (табл. 5.1) могут быть представлены механическими колебательными системами, а их поведение – соответствующим математическим представлением. В этом случае колебательная система – это массы, связанные между собой упругими связями (пучинами).
Число масс, сосредоточенных в точке, равно числу слоев, на которые разделяется конструкция по признаку однородности свойств. Иногда в дополнение к пружинам могут быть добавлены элементы, имитирующие вязкость и пластичность отдельных слоев.
Рассмотрим примеры составления механических моделей грунтовых конструкций как колебательных систем с целью определения прогиба поверхности. При этом предположим, что модели упруги, инерционны и представляют собой систему пружин с жесткостью Сi, связывающих точки с массой mi . Число пружин и учитываемых масс может быть сколько угодно большим, однако не меньше числа слоев грунтовой конструкции.
Колеблющиеся массы слоев сосредоточены в центрах масс, для чего производят предварительное приведение в «точку» распределенных масс по методу проф. Г.И. Глушкова. При этом учитываются сопротивления слоев изгибу. Если верхний слой представляет собой бетонную плиту толщиной hn с модулем упругости Еп и удельной массой δn и уложен на слой грунтовой насыпи толщиной ha hn , характеризуемой коэффициентом постели С0 и удельной массой δ0, то нагрузка Q будет распределена по кругу радиусом R и практически убывает до нуля на глубине активной зоны ha. При этом приведенная масса (по Г. И. Глушкову) составит
|
1 |
|
|
|
|
|
0 |
h h |
R2 |
|
||||||||||
m |
|
|
|
|
|
h |
|
|
a |
n |
|
|
|
|
|
|
, |
(5.1) |
||
|
|
|
|
|
|
|
|
|
|
|
|
|
||||||||
|
|
n |
|
|
|
|
|
|
|
|||||||||||
1 |
|
g |
|
n |
|
|
|
2 |
|
C0 |
|
|
|
|
||||||
|
|
|
|
|
|
|
|
|
|
2R2 |
|
1 |
|
|||||||
|
|
|
|
|
|
|
|
|
|
|
|
|
|
|||||||
а радиус распределения нагрузки Q |
En hn |
|
||||||||||||||||||
|
|
|
|
|
||||||||||||||||
|
|
|
|
|
|
|
|
|
|
|
|
|
|
|
|
|
|
|
||
|
|
R 3,8 4 |
|
|
|
Enhn3 |
|
|
|
|
|
2 |
|
|
||||||
|
|
|
12C0 1 n2 ; g = 9,81 м/с . |
(5.2) |
||||||||||||||||
|
|
|
|
|
|
|
|
|
|
|
76 |
|
|
|
|
|
|
77