
2250
.pdf
Если rUS = + 1,0, между параметрами U и S существует полная прямая зависимость. Если rUS = – 1,0 – полная обратная зависимость.
Чем меньше численное значение величины rUS, тем меньше теснота связи величин U и S. При rU S = 0 связь между параметрами отсутствует, то есть параметры U и S независимы.
Считается, что при rUS ≥ 0,5 по абсолютному значению взаимная зависимость параметров достаточно велика. При rUS < 0,5 параметры можно считать независимыми.
Для проверки достоверности результатов оценки зависимости между параметрами вычисляют ошибку коэффициента корреляции:
mr= ± |
1−r2 |
(3.10) |
US , |
||
|
n |
|
где n – количество наблюдений.
Если rUS ≥ 3mr, результаты можно считать достоверными для решения практических задач.
Объективность диагностического параметра характеризуется нали-
чием связи между его величиной и уровнем работоспособности элемента. Например, давление масла на входе в двигатель однозначно характеризует величину зазора в подшипниках коленчатого вала, изменение скорости перемещения рабочего органа машины в заданных условиях характе-
ризует изменение подводимой к рабочему органу мощности. Перечисленные свойства необходимо учитывать при выборе диагности-
ческих параметров. При решении практических задач часто бывает трудно определить, существует ли зависимость изменения параметра, выбираемого в качестве диагностического, от параметра технического состояния.
В общем виде задача выбора совокупности диагностических параметров сводится к следующему /40/:
–рассматривают диагностическую систему, состоящую из двух под-
систем: объекта, техническое состояние которого подлежит оценке, и прибора (или совокупности приборов), с помощью которого осуществляют диагностирование;
–состояние диагностической системы определяют соотношением состояний подсистем: X, характеризующей пространство возможных технических состояний объекта, и У, определяющей пространство диагностических признаков;
–определяют энтропию состояний системы диагностирования;
–вычисляют взаимную информацию подсистем X и У;
–при соблюдении перечисленных свойств выбор диагностических па-
раметров производят из условия наибольшей информативности.
60
При выборе диагностического параметра необходимо также учитывать трудовые, материальные и энергетические затраты на измерение его в эксплуатации. Для такой технико-экономической оценки диагностического параметра может быть использован показатель Э /40/, представляющий собой отношение информативности параметра Ji к стоимости его из-
мерения Cgi:
Э = |
Ji |
. |
(3.11) |
|
|||
|
Cgi |
|
Величина Cgi включает в себя затраты на приобретение средств диагностирования, стоимость их монтажа и эксплуатации. При выборе диагностического параметра из совокупности параметров, в результате сравнительного анализа, выбирают тот, который отвечает всем вышеизложенным требованиям.
Контрольные вопросы к третьей главе
1.Как формулируются понятия:
–структурный параметр;
–параметры выходных процессов;
–прямые диагностические параметры;
–косвенные диагностические параметры?
2.Какая зависимость связывает между собой выходные характеристики (параметры) объекта диагностирования и его структурные параметры?
3.Какие примеры косвенных показателей степени износа механизмов
иузлов ДВС и трансмиссии можно привести для СДКМ?
4.Чем различаются между собой и что общее имеют:
–рабочие процессы объектов диагностирования;
–сопутствующие процессы объектов диагностирования?
5.В чем заключается сущность постановки диагноза в технической диагностике?
6.Какими показателями характеризуется структура агрегатов, механизмов и узлов машины?
7.Какие примеры можно привести для описания структуры ДВС и его механизмов?
8.Какие предельные значения могут принимать диагностические (структурные) параметры?
9.Что понимается в определениях:
–номинальное (начальное) значение диагностического (структурного) параметра;
61
–предельно допустимое значение диагностического (структурного) параметра?
10.Какое значение параметра характеризует качественный переход между исправным и неисправным состояниями объекта диагностирования?
11.Какое значение параметра характеризует отказ агрегата (узла)?
12.Какие примеры можно привести для сравнительной характеристики постепенных и внезапных отказов деталей узлов:
–валов редукторов и передач;
–шестерен редукторов и передач;
–резьбовых соединений?
13.Какой основной метод (общий) применяется в методиках оценки надежности и методиках технического диагностирования?
14.Какие формы связей существуют между структурными и диагностическими параметрами?
15.Какими принципами руководствуются при выборе диагностических параметров?
16.Какой порядок выбора диагностических параметров рекомендуется в технической диагностике?
17.Каким требованиям должны отвечать диагностические параметры (свойства диагностических параметров)?
18.Какая зависимость описывает в общем виде характер изменения параметров в функции наработки машины (агрегата, узла)?
19.Каким свойством можно характеризовать одновременно численные значения диагностических параметров и точность средств диагностирования?
20.Какую относительную величину используют в качестве количественного показателя чувствительности диагностического параметра?
21.Каким свойством диагностического параметра оценивается количество информации о техническом состоянии объекта диагностирования?
22.Какой количественный показатель можно использовать для оценки разрешающей способности диагностических параметров в их сравнительном анализе?
23.Какие из диагностических параметров бензинового ДВС имеют большую и меньшую разрешающие способности?
24.В чем заключаются различия между такими свойствами диагностических параметров, как полнота оценки технического состояния объекта диагностирования и объективность диагностического параметра?
25.Какой показатель может быть использован для сравнительной технико-экономической оценки диагностических параметров?
62
4. МЕТОДЫ ТЕХНИЧЕСКОГО ДИАГНОСТИРОВАНИЯ
4.1. Система технического диагностирования
Как уже указывалось, диагностированием называют процесс определения технического состояния объекта без его разборки, по внешним признакам путем измерения величин, характеризующих его состояние и сопоставление этих величин с ТУ. Оно обеспечивает систему ТО и ремонта СДКМ необходимой информацией об их техническом состоянии и является неотъемлемой составной частью этой системы. Техническое диагностирование данного объекта (машины, ее агрегата или механизма) осуществляют в соответствии с разработанными алгоритмом (совокупностью последовательных операций) и (или) технологической картой, установленных технической документацией. Комплекс, включающий объект, средства и алгоритмы (технологические карты) диагностирования, образует совокупность элементов или систему технического диагностирования.
В полном составе систему технического диагностирования можно оп-
ределить как совокупность средств, методов и объекта диагностирования, а также исполнителей (машиниста, мастера, оператора), осуществляющих диагностические операции в соответствии с алгоритмами и (или) технологическими картами диагностирования (рис. 4.1).
Объект диагностирования системы характеризуется потребностью и возможностью его технического диагностирования.
Средствами диагностирования служат стенды, приборы, приспособления. Они могут быть внешними (стационарными, переносными) и встроенными (бортовыми), входящими в устройство составных частей машины. При диагностировании используют не только технические средства измерения и контроля параметров, но и субъективные способности машиниста (оператора), его органы чувств, умения, навыки. В технической эксплуатации для оценки состояния машины могут использоваться методы субъективного диагностирования (органолептические методы) /3, 8, 9, 18, 26, 35/. Для прогноза технического состояния машины, отыскания и локализации сложных отказов осуществляют объективное диагностирование с использованием измерительных технических средств.
Разделяют функциональные и тестовые системы диагностирования /2/. В функциональной системе диагностирование проводят в процессе работы машины (объекта), а в тестовой при измерении диагностических параметров работу машины (объекта) воспроизводят искусственно.
Системы диагностирования, которые предназначены для проведения нескольких различных по своему содержанию диагностических процессов являются универсальными по назначению, а системы диагностирования, обеспечивающие только один диагностический процесс, – специальными.
63
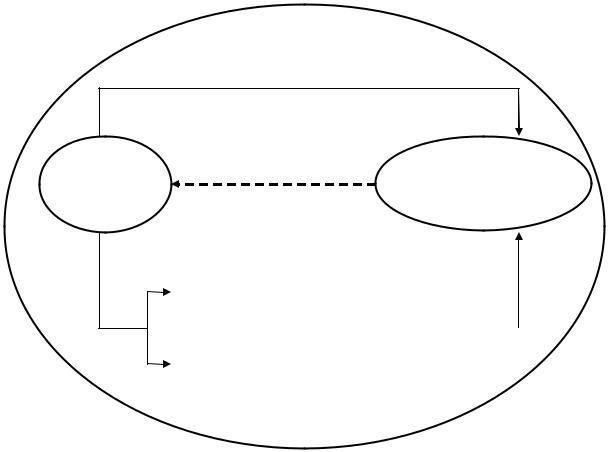
|
Функциональное воздействие на объект |
|
Параметры объекта |
|
Объект |
Оператор |
диагностирования |
Функциональное и тестовое воздействие на объект
Встроенные средства |
|
|
Алгоритм |
|
|
||||
|
|
|
|
|
|
|
|
|
|
|
|
|
|
|
Внешние средства |
|
|
|
|
|
|
|
|
|
Рис. 4.1. Структура системы диагностирования
Различают системы с непрерывным и периодическим диагностированием. В первой диагностирование осуществляется в процессе эксплуатации при помощи встроенных средств, а во второй – через определенные периоды наработки объекта перед ТО или ремонтом.
4.2. Методы технического диагностирования
Методы диагностирования машин, их агрегатов и узлов характеризуются способом измерения и физической сущностью диагностических параметров. Принято выделять три основные группы /2/ средств технического измерения диагностических параметров, которые классифицируются в зависимости от их вида (рис. 4.2).
Средства первой группы в основном имитируют нагрузочные и скоростные режимы работы машины с целью определения при заданных условиях выходных параметров. С этой целью используются нагрузочные стенды и стенды с беговыми барабанами (для колесных машин) или
64
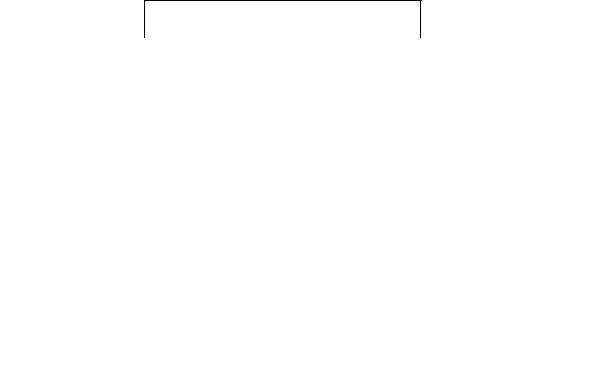
Средства диагностирования
|
|
|
|
|
|
|
|
|
|
|
|
|
|
|
|
|
|
|
|
|
|
|
|
|
|
|
|
|
|
|
|
|
|
|
|
|
|
Внешние |
|
|
|
|
Встроенные |
|
|
Средства, устанавливаемые |
|||||||
|
|
|
|
|
|
|
|
|
(бортовые) |
|
|
|
|
на машину |
|||
|
|
|
|
|
|
|
|
|
|
|
|
|
|
|
|
|
|
|
|
|
|
|
|
|
|
|
|
|
|
|
|
|
|
|
|
|
|
Стационарные |
|
|
|
|
Индикаторы предельного |
|
|
Информационно- |
|||||||
|
|
|
|
|
|
|
|
||||||||||
|
|
|
|
|
|
|
|
|
состояния |
|
|
|
рекомендующие |
||||
|
|
|
|
|
|
|
|||||||||||
|
|
|
|
|
|
|
|
|
|
|
|
|
|
|
|
|
|
|
|
|
|
|
|
|
|
|
|
|
|
|
|
|
|
|
|
|
|
Переносные |
|
|
|
|
Средства оценки парамет- |
|
|
|
|
||||||
|
|
|
|
|
|
|
|
|
|
||||||||
|
|
|
|
|
|
|
|
|
ров состояния |
|
|
|
|
|
|||
|
|
|
|
|
|
|
|
|
Средства съема и |
||||||||
|
|
|
|
|
|
|
|
|
|
|
|
|
|
|
|
||
|
|
|
|
|
|
|
|
|
|
|
|
|
|
||||
|
|
|
|
|
|
|
|
|
Средства, оснащенные |
|
|
|
хранения пара- |
||||
|
|
|
|
|
|
|
|
|
|
|
|
||||||
|
|
|
|
|
|
|
|
|
|
|
|
метров состояния |
|||||
|
|
|
|
|
|
|
|
|
устройствами съема диаг- |
|
|
||||||
|
|
|
|
|
|
|
|
|
|
|
|||||||
|
|
|
|
|
|
|
|
|
ностической информации |
|
|
|
|
||||
|
|
|
|
|
|
|
|
|
|
|
|
|
|
|
|
|
|
|
|
|
|
|
|
|
|
|
|
|
|
|
|
|
|
|
|
Рис. 4.2. Классификация средств технического диагностирования машин
параметры определяются в процессе работы машины при выполнении машиной технологических операций.
Средства второй группы позволяют оценивать по выходным параметрам степень износа механизмов и узлов машины, работоспособность ее составных частей и систем. Например, путем опрессовки или создания разрежения в контролируемом объеме, оценки интенсивности нарастания или падения давления в потоке жидкости (топлива, масла).
Средства третьей группы позволяют объективно измерять и оценивать геометрические параметры.
4.2.1. Методы функциональной технической диагностики
Различают экспресс-методы, позволяющие получить интегральную оценку состояния объекта диагностирования, и методы углубленного диагностирования, используемые для установления причин отказов и более точной (чем с помощью экспресс-методов) оценки технического состояния составных частей объекта диагностирования /3, 40/.
Методы диагностирования классифицируют в зависимости от характера и физической сущности распознаваемых признаков и измеряемых параметров технического состояния объектов диагностирования (табл. 4.1).
65
|
|
Таблица 4.1 |
|
Методы технического диагностирования агрегатов и систем СДКМ |
|||
|
|
|
|
Методы |
Параметры |
Составные части, агрегаты, системы |
|
|
|
СДКМ |
|
Функциональные: |
|
|
|
физико-химические |
Обобщенные: |
ДВС, трансмиссия и системы, обеспе- |
|
|
мощностные; |
чивающие их работу |
|
|
экономические |
|
|
|
Герметичность |
|
|
|
рабочих объемов |
|
|
оптические |
Состав отработав- |
|
|
спектральные |
ших газов |
|
|
теплофизические |
Тепловое состоя- |
ДВС и системы, обеспечивающие его |
|
|
ние |
работу |
|
механические |
Динамические (хо- |
ДВС, трансмиссия, ходовая часть, ра- |
|
|
довые, тормозные) |
бочее оборудование и системы, обеспе- |
|
|
качества |
чивающие их работу |
|
|
Геометрические |
|
|
По составу масел: |
Концентрация, |
ДВС, трансмиссия и системы, обеспе- |
|
физико-химические |
дисперсионный и |
чивающие их работу |
|
оптические |
элементарный со- |
|
|
спектральные |
ставы механиче- |
|
|
радиометрические |
ских примесей, ки- |
|
|
активационные |
нематическая вяз- |
|
|
магнитные |
кость, кислотное и |
|
|
|
щелочное числа, |
|
|
|
содержание воды |
|
|
Акустические |
Уровень шума |
ДВС, трансмиссия, ходовая часть, ра- |
|
Виброметрические |
|
бочее оборудование, гидравлические, |
|
Уровень вибраций |
электрические приводы рабочего |
|
|
|
|
оборудования |
|
Функциональные методы диагностирования основаны на измерении косвенных параметров объекта диагностирования, характеризующих техническое состояние его элементов через уровень функционирования /12, 36, 40/.
В зависимости от характера распознаваемых признаков изменения технического состояния объекта диагностирование функциональными ме-
тодами может производиться по мощностным и технико-экономическим показателям, тепловому состоянию, герметичности рабочих объемов, тормозному пути.
Метод оценки технического состояния машин по мощностным и технико-экономическим показателям используют как для общего, так и для углубленного поэлементного диагностирования. В основе метода ле-
66
жат зависимости эффективности использования машины от технического состояния основных элементов. В качестве диагностических параметров в этом случае используют эффективную мощность двигателя, силу тяги, рабочую скорость, грузоподъемность. В зависимости от характера измеряемых диагностических параметров подбирают соответствующее диагностическое оборудование.
Методы диагностирования машин по тепловому состоянию и герметичности рабочих объемов имеют более узкую область применения. Их используют в основном для оценки технического состояния элементов двигателей и гидравлических систем.
Поскольку ни один из перечисленных методов не позволяет произвести полную оценку технического состояния машины, при углубленном техническом диагностировании часто используют комбинированные методы – акустические, виброметрические или совокупность функциональных методов.
Акустические методы /30, 35, 36, 40, 41/ технического диагностирования основаны на измерении амплитуды и частоты звуковых колебаний, излучаемых объектом диагностирования в процессе работы. Изменение технического состояния элементов машин в процессе работы – увеличение зазоров в сопряжениях, изменение нагрузочного, скоростного и теплового режимов работы деталей вследствие изнашивания, старения, коррозии вызывает соответствующие изменения параметров звуковых колебаний. Сопоставляя эмпирические значения звуковых сигналов с эталонными, можно судить о техническом состоянии объекта в данный момент времени и прогнозировать его изменение на некоторый период.
Поскольку в формировании звукового потока участвуют практически все подвижные детали объекта диагностирования, акустические методы позволяют оценить техническое состояние большинства основных элементов по величинам излучаемых ими звуковых сигналов. Основная сложность при этом состоит в выделении определенного сигнала из общего спектра и распознавании его принадлежности тому или иному элементу машины. Для оценки звукового сигнала (выделения его из общего спектра и измерения) используют специальные приборы – спектрометры, шумомеры, осциллографы.
Акустические методы диагностирования применяют в основном для оценки технического состояния элементов, силовых установок, механических и гидромеханических передач.
Виброметрические методы /30, 36, 38, 40/ основаны на измерении параметров вибрации объекта диагностирования. Уровень вибрации объекта в процессе работы определяют техническим состоянием его основных элементов: размерами зазоров в сопряжениях, износом деталей. Поэтому, измеряя параметры вибрации (частоту, амплитуду, ускорение) и сравнивая
67
их с эталонными значениями, можно оценить техническое состояние объекта диагностирования в данный момент времени и прогнозировать его изменение на некоторый период.
Поскольку параметры вибрации, используемые в качестве диагностических, являются широкоинформативными и формируются в результате функционирования большого числа элементов объекта диагностирования, основной сложностью при диагностировании виброметрическими методами является, как и в предыдущем случае, распознавание принадлежности сигнала к определенному элементу.
Виброметрические методы используют для диагностирования элементов силовых установок, механических и гидромеханических передач.
Методы технического диагностирования по составу масел /18, 35, 36, 38/ наиболее универсальны и широко применяются для экспресс-оценки состояния двигателей, элементов трансмиссии, гидравлических систем управления, а также в оценке качества смазочных материалов и рабочих жидкостей.
Основными диагностическими параметрами в этих случаях являются концентрация, дисперсионный и элементарный составы механических примесей, кинематическая вязкость масла, кислотное и щелочное числа, а также содержание воды в масле. С точки зрения диагностирования состояния основных составных частей машины (двигателя, трансмиссии, гидравлической системы управления) наиболее информативны первые три показателя.
Для анализа содержания механических примесей в масле используют химический, спектральный, радиометрический, активационный и оптикофизический методы.
Методы диагностирования также классифицируют по трудоемкости поиска и локализации неисправностей или отказов. Так, например, суще-
ствующие методы диагностирования гидравлических приводов СДКМ по их трудоемкости можно условно разделить на пять групп /35, 41/:
–статопараметрический метод – наиболее трудоемкий, требующий отвода из гидравлической системы потока рабочей жидкости;
–методы амплитудно-фазовых и переходных характеристик и тер-
модинамический, требующие установки в гидравлическую систему датчиков, имеющих контакт с рабочей жидкостью;
–методы спектрального анализа и индикации продуктов износа и инородных примесей, то есть методы, требующие отбора проб рабочей жидкости (по составу рабочей жидкости);
–акустический, виброакустический, силовой и метод измерения скорости нарастания усилия на исполнительном элементе, то есть методы,
требующие установки датчиков, не имеющих контакта с рабочей жидкостью;
68
– кинематический метод, наименее трудоемкий, не требующий установки специальных датчиков.
На основе наиболее распространенных в практике эксплуатации СДКМ функциональных методов и их разновидностей разработано большое число стационарных, переносных, встроенных (бортовых) средств диагностирования, в том числе средства диагностирования с использованием ЭВМ (микропроцессоров, цифровых устройств передачи, хранения и отображения информации).
4.2.2. Функционально-статистические методы прогнозирования ресурса машин
Техническое обслуживание (ТО) и ремонт строительных, дорожных и коммунальных машин (СДКМ) на предприятиях, осуществляющих их эксплуатацию, сопровождаются выбором и принятием управленческих реше-
ний. В системе управления технической эксплуатацией (УТЭ) СДКМ процесс выбора, принятия и реализации решений включает /1/ (рис. 4.3):
–обоснование решения с учетом предупреждения предельных состояний машин, отказов других элементов системы УТЭ, в том числе из-за отсутствия потребного количества запасных частей и материалов, при условии оценки ее эффективности с использованием показателей технической готовности машин;
–оценку условий принятия решения на основе постоянной, достовер-
ной и полной диагностической информации о техническом состоянии парка машин;
–последовательный порядок принятия решения с указанием цели и за-
дач, выявлением ограничений и альтернатив в сопоставляемых моделях возможных вариантов, выбором критерия эффективности УТЭ и реализацией принятого по критерию эффективности решения на практике в заданных условиях;
–обеспечение реализации решения с документальным его отображени-
ем, использованием средств диагностики, технических средств УТЭ СДКМ и персонала.
Вкачестве показателей эффективности эксплуатации парка машин, в
том числе уровня организации использования их по назначению, а также режима работы в течение года и эффективности функционирования технических служб предприятия приняты известные технико-экономические показатели /14, 16, 21, 37, 40, 41/:
–годовая выработка списочного состава средств механизации Wг;
–удельная годовая выработка на среднесписочную машину Wуд;
–коэффициент использования парка машин Кип.
69