
2250
.pdfВнезапный отказ характеризуется качественным (скачкообразным) изменением одного или нескольких структурных параметров из-за накопления повреждений и неисправностей.
Постепенный отказ связан с плавным изменением одного или нескольких структурныхпараметров машины, ееагрегатов, механизмов, узлов.
Конструктивные отказы связаны с ошибками при конструировании, применением несовершенных методов конструирования, неправильным выборомкомплектующих изделий, материалов при изготовлении машин.
Производственные отказы связаны с нарушениями технологии изготовления деталей, узлов, агрегатов, использованием производственного оборудования, котороенеобеспечивает требуемой точности приихизготовлении.
Независимый отказ не обусловлен повреждениями и отказами других элементов агрегата (машины).
Зависимый отказ обусловлен повреждениями и отказами других элементовагрегата (машины).
Полный отказ – отказ, после которого использовать агрегат, узел, в том числе машину, невозможно или возможно, но с ограничениями её работоспособности.
Примеры постепенных и внезапных отказов с указанием их причин представлены втабл. 3.1.
|
|
Таблица 3.1 |
|
|
Примерыпостепенныхивнезапныхотказов |
||
|
|
|
|
Детали агрегатов, |
Характер, причины отказа |
||
узлов |
|
|
|
Постепенный |
Внезапный |
|
|
|
|
||
|
|
|
|
1 |
2 |
3 |
|
Валы |
Износ трущихся поверхно- |
Поломка усталостная или от |
|
|
стей шеек и цапф |
перегрузок |
|
|
Изгиб валов |
|
|
Подшипники |
Износ трущихся |
Выплавление |
|
скольжения |
поверхностей |
антифрикционного сплава |
|
Подшипники |
Износ рабочих поверхно- |
Схватывание |
|
качения |
стей шариков, роликов, |
|
|
|
колец |
|
|
|
Смятие, выкрашивание ра- |
Заклинивание из-за поломки |
|
|
бочих поверхностей |
сепараторов, колец |
|
|
шариков, роликов, колец |
|
|
Шестерни |
Износ, смятие зубьев |
Поломка зубьев |
|
|
Выкрашивание зубьев |
Заедание |
|
|
|
|
|
|
50 |
|
|
|
|
|
Окончание табл. 3.1 |
|
1 |
|
2 |
3 |
|
Шлицы, шпонки |
Износ, смятие рабочих |
Поломка |
|
|
|
|
поверхностей |
|
|
Резьбовые |
со- |
Ослабление затяжки |
Срыв резьбы |
|
единения |
|
|
Обрыв головки болта |
|
Трубопроводы, |
Изгиб, смятие трубок, |
Обрыв трубопроводов, |
|
|
шланги |
|
патрубков, шлангов |
шлангов |
|
|
|
Засорение трубопроводов, |
|
|
|
|
шлангов |
|
|
Предельное значение структурного параметра соответствует либо полной потере работоспособности агрегата (узла), либо такому снижению его технических характеристик и эксплуатационных свойств, при котором дальнейшая эксплуатация машины недопустима или экономически нецелесообразна.
Предельно допустимые значения показателей необходимы для того,
чтобы сделать вывод о возможности дальнейшей эксплуатации агрегатов, узлов, а также машины в целом или о направлении их в ремонт.
Для того чтобы прогнозировать работоспособность машин, кроме предельно допустимых значений показателей необходимо иметь данные о том, как изменяется величина показателей в процессе эксплуатации в зависимости от наработки машины. Весь комплекс работ технического диагностирования, начиная с выявления происходящих изменений в агрегатах, механизмах и узлах и заканчивая установлением предельно допустимых значений показателей, выполняется путем наблюдения за рабочими процессами, происходящими в агрегатах, механизмах, узлах в условиях, соответствующих условиям их эксплуатации, а также в ходе специальных испытаний (тестов).
В первом случае могут применяться статистические методы исследований, с помощью которых оценивается надежность агрегатов, механизмов и узлов. Следует отметить, что в методиках оценки надежности и методиках технического диагностирования используется один и тот же основной ме-
тод – метод наблюдения за изменениями, происходящими в агрегатах и узлах машины.
Критериями выбора целесообразного метода технического диагностирования и соответствующих средств диагностирования являются размер материальных затрат, стоимость его проведения, вид и форма носителя информации, характеристики информативных и диагностических параметров объекта диагностирования.
51
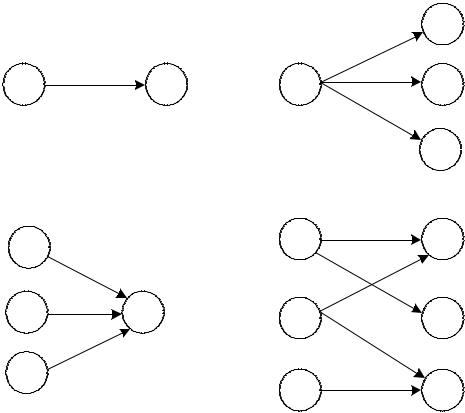
3.3. Выбор диагностических параметров
Выбор диагностических параметров осуществляют, как правило, на стадии проектирования диагностической системы, когда известен объект диагностирования и необходимо решение, по каким параметрам целесообразно оценивать изменение его технического состояния в эксплуатации.
В целях обоснованного выбора диагностических параметров системы предварительно устанавливают характер их связей с параметрами технического состояния (рис. 3.4) /40/.
|
1) |
2) |
U1 |
|
|
|
|
S |
U |
S |
|
|
|
|
... |
|
|
4) |
Un |
|
3) |
|
|
S1 |
S1 |
|
U1 |
|
|
||
|
|
|
|
|
U |
|
|
... |
... |
|
... |
Sm |
Sm |
|
Un |
|
|
Рис. 3.4. Формы связей структурных и диагностических параметров:1 – единичная; 2 – множественная;
3 – неопределенная; 4 – смешанная (комбинированная)
Диагностическими могут быть параметры, которые относятся к 1-й и (или) 2-й группе. Параметры 3-й и 4-й групп не отвечают условию однозначности и могут быть использованы только в качестве интегральных диагностических показателей.
Выбор диагностических параметров объекта диагностирования осуществляют, руководствуясь известными принципами /22, 40/:
• первый – структурные и выходные параметры объекта диагностирова-
ния должны обеспечивать оценку его технического состояния без разборки
52
(диагностическими параметрами могут быть параметры рабочих и сопутствующих процессов);
•второй – диагностические и структурные параметры должны иметь однозначную зависимость между собой (монотонно-возрастающее или мо-
нотонно-убывающее, а не скачкообразное увеличение или уменьшение в процессе наработки машины);
•третий – диагностический параметр должен быть стабильным, что означает нахождение его значений в заданном интервале;
•четвертый – диагностический параметр должен отвечать требованиям чувствительности;
•пятый – диагностический параметр должен отвечать требованиям информативности.
Следуя вышеизложенным принципам, при техническом диагностировании осуществляется выбор диагностических параметров объектов диагно-
стирования в соответствии с рекомендуемым порядком:
–по результатам подконтрольной или обычной эксплуатации опреде-
ляют наиболее часто встречающиеся виды отказов и повреждений;
–выполняют анализ, как отражается неработоспособное состояние элементов объекта диагностирования на параметры его выходных рабочих и сопутствующих процессов;
–составляют структурную схему причинно-следственных связей в по-
следовательности агрегат (сборочная единица) – элемент (сопряжение) – структурный параметр – характер неисправности – симптом (признак неисправности) – диагностический параметр.
3.4. Основные требования, предъявляемые к диагностическим параметрам
Как следует из изложенных выше принципов выбора диагностических параметров, они должны удовлетворять основным требованиям (обладать свойствами) /4, 5, 19, 22, 35, 36, 40/ однозначности, стабильности, чувст-
вительности, информативности. Их определение должно быть доступным в различных условиях эксплуатации.
Между изменением параметра технического состояния и изменением соответствующих диагностических параметров должно быть строгое од-
нозначное соответствие. Однозначная зависимость (соответствие) по-
казателя технического состояния от уровня работоспособности обеспечивается в первую очередь соответствующей методикой проведения испытания (теста).
Например, величина давления в конце такта сжатия определяет износ ЦПГ ДВС неоднозначно, так как оно зависит еще и от вязкости масла
53
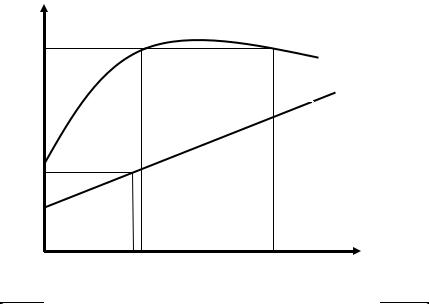
(температуры масла в системе смазки), скорости перемещения поршня (частоты вращения коленчатого вала) и герметичности клапанов механизма газораспределения(герметичности камерысгорания).
Чтобы получить однозначную зависимость, необходимо исключить влияние неосновных факторов. Так, например, при диагностировании ЦПГ дизельного ДВС это достигается проведением испытаний в определенных условиях, при заданных (эксплуатационных) значениях температуры масла и охлаждающей жидкости (85 – 95°С) и одинаковой (приведенной) частоте вращения коленчатого вала. Влияние степени герметичности клапанов (камер сгорания) оценивается величиной давления газов в картере двигателя.
Каждому значению структурного параметра, характеризующего техническое состояние объекта диагностирования, должно соответствовать только одно, вполне определенное значение параметра выходного процесса
(рис. 3.5).
U
U2
1
2
U1
0 |
S 1 S 2 / |
S 2 // |
S |
Рис. 3.5. Зависимость выходного параметра U от величины структурного параметра S: 1 – параметры связаны неоднозначной зависимостью; 2 – параметры связаны однозначной зависимостью
На рис. 3.5 видно, если между структурным и выходным параметрами зависимость линейная (2), то она полностью удовлетворяет требованию однозначности (монотонно возрастает). Каждому значению структурного параметра S1 соответствует единственное значение выходного параметра U1 . Для зависимости 1 требование однозначности не выполняется. Одному значению параметра U2 соответствуют два значения S2’ и S2’’ структурного параметра.
54
Диагностические параметры, изменение которых во времени происходит по линейной зависимости, относят к группе линейных параметров. Их преимущества – простота измерения и последующего анализа. Примерами линейного диагностического параметра может служить износ (величина зазора) фрикционных элементов муфты сцепления или износ накладок колодок тормозов (величина зазора между накладкой и тормозным барабаном). В примерах диагностический параметр изменяется во времени по зависимости, в большинстве случаев близкой к линейной.
Большее число диагностических параметров агрегатов, механизмов, систем и узлов СДКМ изменяется во времени по нелинейным зависимостям (см. рис. 3.5). В общем виде характер изменения параметров может быть представлен выражением /21, 37, 41/
U(t) = V |
c |
t α + U |
н |
, |
(3.1) |
|
|
|
|
где Uн – начальное значение параметра; Vc – коэффициент, характеризующий скорость изменения параметра (зависит от условий эксплуатации и режимов работы объекта диагностирования); α – показатель степени (зависит от свойств, структуры и геометрических параметров объекта диагностирования: при α = 1 параметр изменяется (рис.3.6) по линейной зависимости 2; при α > 1 зависимость изменения параметра монотонно возрастающая (1), скорость изменения также возрастает; при α < 1 зависимость изменения параметра монотонно возрастающая (3), скорость изменения убывает).
Таким образом, изменению параметра технического состояния должно однозначно соответствовать и изменение соответствующих диагностических параметров. Монотонному возрастанию (убыванию) параметра технического состояния объекта диагностирования должно соответствовать монотонное изменение (возрастание или убывание) диагностического параметра без перегибов и разрывов функции:
U= f (S). (3.2)
При этом необязательно, чтобы величина U возрастала с увеличением величины S. Зависимость U = f (S) может быть и обратной.
Поскольку диагностический параметр всегда является случайной величиной, его измеряемые значения имеют определенный разброс, отклонения от среднего статистического значения. Величина разброса значений или стабильность диагностического параметра может быть охарактеризована /34, 40/ величиной средней квадратической ошибки измерения (дисперсией ошибки), стандартной ошибкой или просто «стандартом» − коэффициентом вариации.
Чувствительность параметра (показателя) обусловливается величи-
ной изменения его численных значений за установленную наработку и точностью средств диагностирования, доступных для использования в процессе эксплуатации машин (рис. 3.7). При этом большему изменению струк-
55
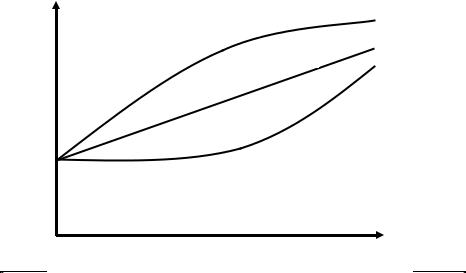
турного параметра должно соответствовать большее изменение выходного параметра.
U (t) |
3 |
|
|
|
2 |
1
U н
0 t
Рис. 3.6. Типы зависимостей диагностических параметров: 1 – нелинейная монотонно возрастающая с увеличением скорости изменения (коррозионное изнашивание); 2 – линейная монотонно возрастающая (износ фрикционных накладок дисков сцепления, фрикционных элементов тормозов); 3 – нелинейная монотонно возрастающая с уменьшением скорости изменения(усталостное и кавитационное
изнашивание)
На рис. 3.7 для линейных зависимостей 1 и 2 между выходными и структурными параметрами видно, что при одном и том же изменении ∆S, выходной параметр U1 изменяется на большую величину, чем параметрU2, то есть ∆U1 больше ∆U2. Следовательно, параметр U1 чувствительнее параметра U2, и по его изменению точнее можно установить величину изменения ∆ S структурного параметра.
Таким образом, чувствительность диагностического параметра может характеризовать соотношение ∆U / ∆ S. Чем больше это соотношение, тем более чувствителен параметр, то есть тем больше изменение величины сигнала Ui соответствует единице изменения параметра Si.
Экспериментальные зависимости чувствительности диагностических параметров получают при форсированных износных испытаниях.
56
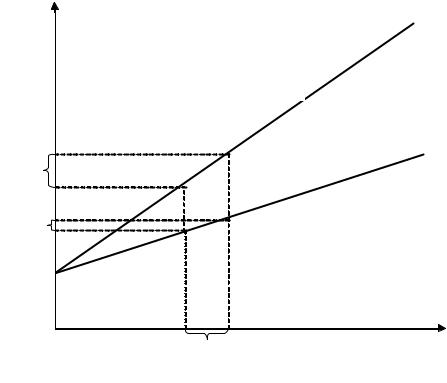
U
1
2
∆U 1
∆U 2
U н
0 |
S1 ∆ S S2 |
S |
Рис. 3.7. Зависимость чувствительности выходного параметра U от величины структурного параметра S: параметры связаны однозначной зависимостью 1; параметры связаны
однозначной зависимостью 2
В общем виде для непрерывных величин показатель чувствительности диагностического параметра с учётом выражения (3.1) можно представить следующим образом:
r = dU/dS. |
(3.3) |
В качестве количественного показателя чувствительности диагностического параметра может быть использована относительная величина /40/
(см. рис. 3.7) |
|
|
|
|
|
|
|
|
|
|
∆U = |
|
Uпрi −Uнi |
|
= |
|
Uпрi |
−1 |
|
. |
(3.4) |
|
|
|
|
|||||||
|
Uнi |
|
||||||||
|
|
|
|
Uнi |
|
|
|
Информативность диагностического параметра оценивается количе-
ством информации о техническом состоянии объекта, которое содержит этот параметр /40/:
Ji = H(U) – Hi, |
(3.5) |
где Н(U) – полная энтропия объекта диагностирования,
57
Н(U) = – ∑Pj logPj , |
(3.6) |
здесь Pj – вероятность возникновения в объекте j-й неисправности, обнаруживаемой с помощью диагностирования;
Нi – энтропия системы после технического диагностирования.
Чем больше информации о техническом состоянии объекта диагностирования содержится в диагностическом параметре, тем меньше энтропия объекта Нi после диагностирования и, следовательно, тем больше будет информативность диагностического параметра Ji.
Для оценки чувствительности и информативности технического диагностирования составных частей машины различными методами ис-
пользуется коэффициент разрешающей способности параметра Кп /1/,
который показывает изменение значений параметра в функции наработки и сравнивает между собой их предельные величины с различной физической природой:
Кп = |
Umax −Umin |
=1 − |
Umin |
, |
(3.7) |
Umax |
|
||||
|
Umax |
|
где Umax, Umin – максимальное и минимальное значения параметра.
Если изменение в техническом состоянии не происходит, то есть Umax = Umin , то никакой информации при техническом диагностировании не
поступает и Кп = 0. В случае, когда Umin → 0 , а Umax → ∞ , Кп →1. Соответственно растет и разрешающая способность средств диагностирова-
ния.
Принято считать удовлетворительным Кп≥ 0,5 . При оценке технического состояния ЦПГ длительно работающего бензинового ДВС Кп изменяется в пределах от 0,112 до 0,945 в зависимости от выбранных методов и параметров диагностирования (табл. 3.2) /1/.
|
|
|
|
Таблица 3.2 |
|
Разрешающая способность диагностических параметров ДВС |
|||||
|
|
|
|
|
|
|
Единица |
Значения параметров |
|||
Диагностический параметр |
измерения |
Umax |
Umin |
Кп |
|
|
|
(Uп) |
(Uн) |
|
|
Угар масла из картера ДВС |
г/ч |
180 |
10 |
0,945 |
|
Давление газов в конце такта сжатия |
кПа |
80 |
55 |
0,313 |
|
Прорыв газов в картер ДВС |
л/мин |
250 |
74 |
0,704 |
|
Разрежение всасывания воздуха |
мм рт. ст. |
450 |
400 |
0,112 |
|
Утечка сжатого воздуха из цилиндров |
% |
85 |
25 |
0,706 |
|
ДВС |
|
|
|
|
|
С учетом эффективности и информативности при повышении Кп могут быть использованы менее чувствительные диагностические средства и менее квалифицированный оператор. Однако необходимо иметь в виду,
58
что средства диагностирования не позволяют иногда использовать в качестве диагностических параметры с максимальным значением Кп, так как для сбора информации в одном случае значительно возрастает время диагностирования, а в другом – нет достаточно надежных и дешевых средств диагностирования.
Диагностические параметры также должны обладать такими свойст-
вами, как полнота оценки технического состояния и незатухаемость. Полнота оценки технического состояния объекта диагностирования
достигается в результате измерения диагностического параметра и может быть оценена отношением информативности этого параметра к полной энтропии /40/:
П = |
Ji |
= |
H (U ) − Hi |
=1 |
− |
Hi |
. |
(3.8) |
H (U ) |
|
H (U ) |
||||||
|
|
H (U ) |
|
|
|
Диагностические параметры связаны с параметрами технического состояния функциональной зависимостью. Изменения параметра технического состояния машины должны вызывать соответствующие изменения значения диагностического параметра. Эта закономерность не должна нарушаться во времени. Если при определенных значениях параметра технического состояния соответствующие значения диагностического параметра стабилизируются, асимптотически стремятся к определенной величине, затухают, оценка технического состояния объекта по величине диагностического параметра становится невозможной. Поэтому одним из основных требований к диагностическому параметру является свойство незатухае-
мости.
Перечисленные свойства необходимо учитывать при выборе диагностических параметров. При решении практических задач часто бывает трудно определить, существует ли зависимость изменения параметра, выбираемого в качестве диагностического, от параметра технического состояния.
Оценка взаимной связи этих двух случайных величин производится с помощью корреляционного анализа. Мерой тесноты связи случайных величин является коэффициент корреляции. В зависимости от характера связи случайных величин различают линейную и нелинейную корреляции.
Коэффициент линейной корреляции, характеризующий взаимосвязь значений параметров S и U, вычисляют по формуле /40/
rUS |
= |
∆U∆S , |
(3.9) |
|
|
σUσS |
|
где ∆U = Ui – U, ∆S = Si – S – разность i-го и среднего значений соответствующих параметров;σU , σS – средние квадратические отклонения значе-
ний параметров.
59