
2250
.pdfПеред началом диагностирования выявляют внешним осмотром признаки предельного состояния агрегатов или отдельных составных частей машины. При диагностировании измеряют значения ресурсных параметров агрегатов (составных частей) машины Uи. Измеренные значения сравнивают с допускаемыми значениями Д1, Д2, Д3 параметров.
Значения Д 1, Д 2 , Д 3 соответствуют:
•Д1– оптимальному остаточному ресурсу t ост = 400 моточасов;
•Д2– оптимальному остаточному ресурсу t ост = 1000 моточасов;
•Д3– оптимальному остаточному ресурсу t ост = 2000 моточасов.
По полученным результатам принимают соответствующие реше-
ния по каждой из составных частей:
–когда Uи выходит за пределы Д1, а машина подлежит использованию по прямому предназначению с наработкой ресурса более 400 моточасов – составная часть требует ремонта; в противном случае агрегат (машина) может работать до первого ресурсного отказа;
–когда Uи не выходит за пределы Д1, но выходит за пределы Д2 – составная часть требует ремонта через 500 – 700 моточасов;
–когда Uи не выходит за пределы Д2, но выходит за пределы Д3 – составная часть пригодна к дальнейшей эксплуатации с последующим диагностированием после наработки до очередного ТО–3 (с целью последующего уточнения величины остаточного ресурса);
–когда Uи не выходит за пределы Д3 – составная часть пригодна к дальнейшей эксплуатации с последующим диагностированием после наработки машины до ТР или КР (в соответствии с нормируемой наработкой до соответствующих ремонтов).
Если наработка агрегата с начала эксплуатации неизвестна, решение принимается на основании сравнения измеренного значения параметра Uи
сдопускаемым значением параметра для наработки 4000 моточасов.
По полученным результатам диагностирования для всех составных частей принимают соответствующее решение /3/:
-машина требует капитального ремонта в том случае, когда требует капитального ремонта ее ДВС, а также два (и более) других агрегата или составных части (например, два агрегата трансмиссии);
-машина требует текущего ремонта, когда имеется потребность в ремонте менее трех ее составных частей, включая ДВС;
-машина не требует капитального и текущего ремонтов, если не требуют ремонта ее составные части.
Для примера, признаки предельного состояния основных агрегатов и узлов (составных частей) машины представлены в виде неполного перечня
втабл. 4.5 /3, 14/.
80
|
Таблица 4.5 |
|
Параметры предельного состояния составных частей СДМ |
||
|
|
|
Составные части |
Параметры предельного состояния |
|
(агрегаты, узлы) |
|
|
1 |
2 |
|
ДВС |
|
|
Механизмы ДВС |
|
|
Кривошипно-шатунный |
Неисправности, требующие замены или ремонта |
|
механизм |
блока цилиндров (с демонтажом и полной раз- |
|
|
боркой). |
|
|
Предельный износ или механические поврежде- |
|
|
ния коренных или шатунных шеек коленчатого |
|
|
вала, требующие его замены или шлифования. |
|
|
Предельный расход масла на угар или предель- |
|
|
ный расход картерных газов, не устраняемые за- |
|
|
меной комплекта поршневых колец (допускается |
|
|
одноразовая замена гильз и поршней не более |
|
|
25% цилиндров при остаточном ресурсе ДВС не |
|
|
менее 1000 моточасов) |
|
Газораспределительный |
Трещины в перемычках клапанных гнезд головки |
|
механизм |
блока цилиндров или предельное коробление |
|
Навесные агрегаты и узлы |
рабочей поверхности. |
|
Предельный износ гнезд клапанов |
|
|
ДВС |
|
|
Турбокомпрессор |
Неисправности корпуса турбины, среднего кор- |
|
|
пуса турбокомпрессора, при которых требуется |
|
|
его замена или ремонт (с демонтажом и полной |
|
|
разборкой). |
|
|
Предельный износ или трещины колеса турбины |
|
|
с валом (в том числе устраняемые механической |
|
|
обработкой). |
|
|
Предельный зазор в сопряжении вал колеса тур- |
|
|
бины – подшипник |
|
Топливный насос высокого |
Предельный износ не менее 50% плунжерных пар |
|
давления (ТНВД) в сборе с |
Предельный износ направляющих отверстий |
|
регулятором |
корпуса под толкатели плунжера и рейку. |
|
|
Предельный износ кулачков и опорных шеек ку- |
|
|
лачкового вала. |
|
|
Предельный износ сопряжений регулятора и ме- |
|
|
ханизма управления подачей топлива |
|
Масляный насос системы |
Неисправности корпуса, при которых требуется |
|
смазки |
его замена или ремонт (с демонтажом и полной |
|
|
разборкой). |
|
|
Предельный износ шестерен |
|
|
81 |
|
|
Продолжение табл. 4.5 |
|
1 |
2 |
|
|
|
|
Водяной насос |
Неисправности корпуса, при которых требуется |
|
|
его замена или ремонт (с демонтажом и полной |
|
|
разборкой). |
|
|
Повреждения вала насоса, требующие его замены |
|
|
или ремонта |
|
Пусковой двигатель |
Предельный износ или механические поврежде- |
|
с редуктором |
ния коренных или шатунных шеек коленчатого |
|
вала, требующие его замены или ремонта. |
|
|
|
|
|
|
Неисправности картера редуктора, при которых |
|
|
требуется его замена или ремонт (с демонтажом |
|
|
и полной разборкой). |
|
|
Предельный износ шлицев и посадочных мест |
|
|
под подшипники вала |
|
|
|
|
Гидравлическая система |
|
|
Насос |
Предельное значение подачи |
|
Распределитель |
Предельные внутренние утечки |
|
Гидроцилиндр |
Износ и коррозия поверхности штока. |
|
|
Изгиб штока |
|
|
|
|
Трансмиссия |
|
|
Сцепление в сборе |
Неисправности корпуса, кожуха, при которых |
|
|
требуется их замена или ремонт (с демонтажом и |
|
|
полной разборкой). |
|
|
Предельный износ или разрушение ведущего |
|
|
диска (кроме среднего). |
|
|
Предельный износ шлицев или посадочных мест |
|
|
под подшипники на валу. |
|
|
Излом вала (при наработке более 2000 моточа- |
|
|
сов) |
|
Коробка передач |
Неисправности картера, при которых требуется |
|
|
его замена или ремонт (с демонтажом и полной |
|
|
разборкой). |
|
|
Предельное состояние более двух шестерен по- |
|
|
стоянного зацепления. |
|
|
При наработке более 2000 моточасов: |
|
|
– предельное состояние одного и более ва- |
|
|
ла (предельный износ шлицев, наличие |
|
|
трещин, предельный изгиб); |
|
|
– предельное состояние одной шестерни и |
|
|
более вторичного вала; |
|
|
– предельное состояние или разрушение |
|
|
подшипников вторичного вала |
|
|
|
|
|
82 |
|
|
Окочание табл. 4.5 |
|
1 |
2 |
|
|
|
|
Раздаточная коробка, |
Неисправности картера, при которых требуется |
|
бортовые (колесные) ре- |
его замена или ремонт (с демонтажом и полной |
|
дукторы, ведущие мосты |
разборкой). |
|
|
При наработке более 2000 моточасов: |
|
|
– предельное состояние одной шестерни и |
|
|
более постоянного зацепления; |
|
|
– предельное состояние одного и более вала |
|
|
(предельный износ посадочных мест под |
|
|
подшипники, шлицев, наличие трещин, пре- |
|
|
дельный изгиб) |
|
Ходовая часть |
|
|
Подвеска |
Предельное состояние одной и более тележки или |
|
|
не менее двух балансирных кареток. |
|
|
Предельный износ или разрушение оси качания |
|
|
или одного и более балансира. |
|
|
Предельное состояние сварной рамы тележки |
|
Движитель |
Предельное состояние не менее трех опорных кат- |
|
|
ков или двух катков на разных осях. |
|
|
Предельный износ ободов опорных катков или по- |
|
|
садочных мест под подшипники (более 50%). |
|
|
Предельный износ ободов направляющих колес, |
|
|
посадочных мест под подшипники. |
|
|
Предельное увеличение шага гусеницы. |
|
|
Предельное состояние (разрушение, износ) доро- |
|
|
жек (более 20% звеньев). |
|
|
Разрушение каркаса шины или расслоение корда |
|
Несущая система |
Предельное состояние рамы. |
|
|
Трещины ланжеронов или поперечных брусьев и |
|
|
их сварных соединений. |
|
|
Ослабление (более 50%) заклепок в одном и более |
|
|
соединений ланжеронов с поперечными брусья- |
|
|
ми. Предельное состояние передней полурамы. |
|
|
Предельный износ поверхностей отверстий под |
|
|
оси или втулки шарниров. |
|
|
Излом проушин шарниров |
|
Из всех составных частей СДМ можно выделить ДВС, как сложный по конструктивному исполнению агрегат силовой установки машины, ответственный по своему назначению и соответственно требующий в процессе эксплуатации значительного объема диагностирования механизмов и узлов обслуживающих систем (рис. 4.5). Кроме особенностей этого агрегата, изложенных выше, следует особо указать на тот факт, что ресурс ДВС в значительной степени определяет ресурс машины в целом.
83
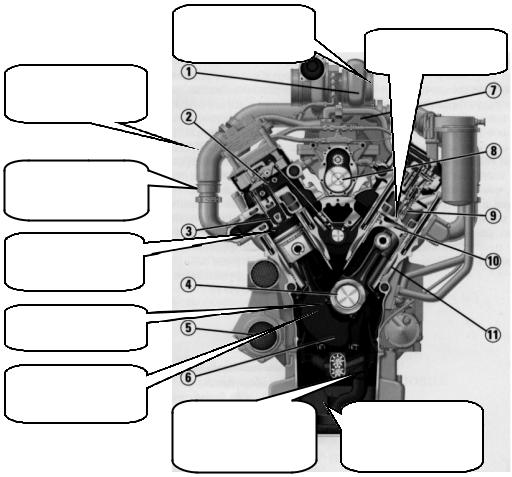
Разрежение |
|
на впуске |
Компрессия |
Тепловые
параметры
Шум и вибрации
Утечки сжатого воздуха
Давление масла
Прорыв газов в картер
Анализ Угар масла картерного
масла
Рис. 4.5. Параметры диагностирования ДВС: 1 − турбонагнетатель; 2 − механизм газораспределения (ГРМ); 3 − клапаны (ГРМ);
4 − шатун; 5 − маслоохладитель; 6 − коленчатый вал; 7 − охладитель воздуха; 8 − привод ТНВД; 9 − форсунка; 10 − поршень; 11 − гильза цилиндра
Вывод о потребности в ремонте ДВС делается по совокупности результатов диагностирования. При этом оцениваются его обобщенные (мощностные, топливная экономичность), интегральные (угар картерного масла, расход картерных газов) параметры и состояние отдельных цилиндров (равномерность или эффективность работы, компрессия или относительная компрессия, разрежение в цилиндрах). Также оцениваются состояние механизмов и узлов: подшипников коленчатого вала (давление масла в главной смазочной магистрали), шумы и стуки от ударов в сопряжениях изношенных деталей и узлов при работе ДВС и параметры вибрации (см. рис. 4.5).
84
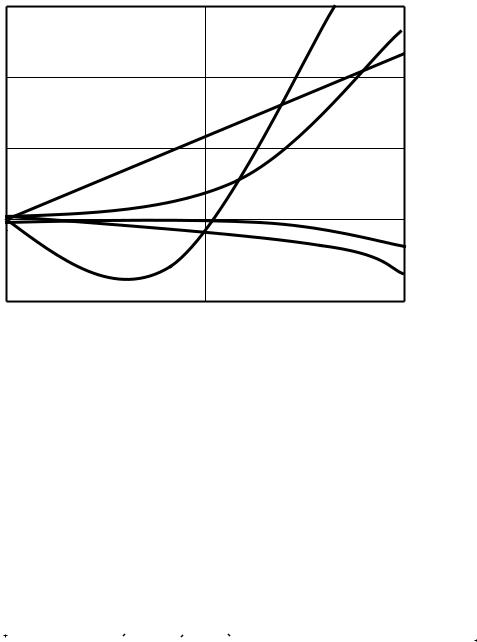
Основным интегральным параметром, по величине которого определяют состояние основных механизмов ДВС, в частности КШМ, является угар картерного масла. Недостатки использования этого параметра известны. В эксплуатации невозможно учесть утечки масла через неплотности сальников коленчатого вала и разъемов картера. Кроме того, угар масла в течение длительной наработки ДВС изменяется незначительно и лишь при большом износе деталей цилиндро-поршневой группы (ЦПГ) КШМ начинает интенсивно возрастать. Необъективность и такой характер изменения параметра в зависимости от наработки затрудняет его использование не только для определения состояния ДВС, но и прогнозирования величины остаточного ресурса (рис. 4.6).
U(t), |
5 |
% |
300
4
200
3
2
100
1
0 |
100 |
t, час |
Рис. 4.6. Изменение диагностических параметров U(t) в зависимости от наработки ДВС (бензиновый ДВС; наработка в часах при форсированных испытаниях): 1 – компрессия; 2 – разрежение; 3 – расход картерных газов (прорыв газов в картер); 4 – утечка сжатого воздуха при положении поршня в ВМТ; 5 – угар масла
В практике диагностирование ДВС по интегральным параметрам на-
чинают с измерения расхода картерных газов и давления масла в главной магистрали. В целях сокращения трудоемкости операции выполняют на работающем ДВС и после его остановки в соответствии с порядком,
представленным на рис. 4.7. Измерение разрежения в цилиндрах ДВС ре-
комендуется проверять во всех случаях, связанных с измерением суммарного зазора в сопряжениях КШМ.
Значения диагностических параметров Д1, Д2, Д3 расхода картерных газов дизельных ДВС СДМ представлены в табл. 4.6 /3/.
85
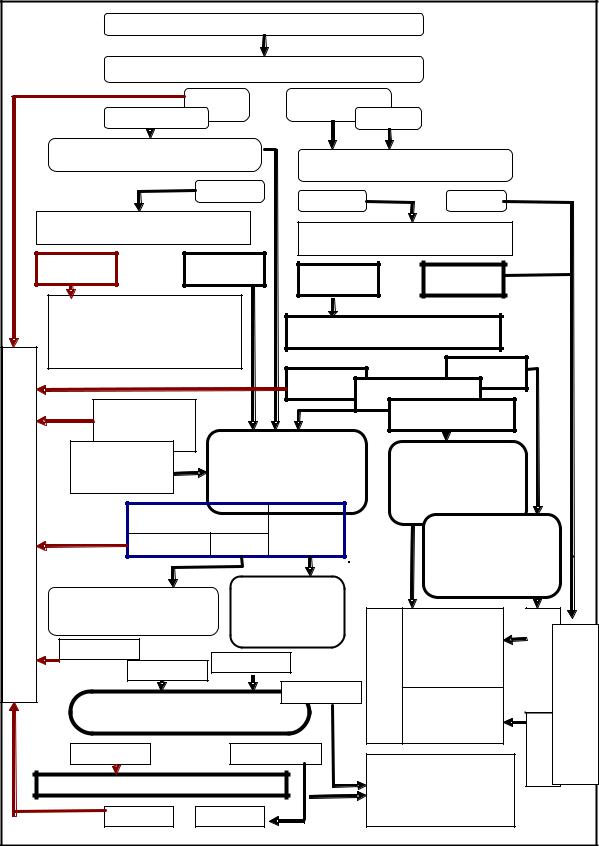
Рис. 4.7. Порядок диагностирования ДВС |
86
Таблица 4.6
Допускаемые значения Д1, Д2, Д3 расхода картерных газов дизельных ДВС СДМ
|
Расход картерных газов, л / мин (не более), при |
||||||
ДВС |
|
|
наработке |
|
|
|
|
2000 моточасов |
|
4000 моточасов |
|||||
|
|
||||||
|
Д1 |
Д2 |
Д3 |
|
Д1 |
Д2 |
Д3 |
ЯМЗ – 240Б |
207 |
184 |
136 |
|
226 |
209 |
175 |
ЯМЗ – 238 НБ |
147 |
131 |
102 |
|
158 |
148 |
120 |
СМД – 62 |
131 |
117 |
85 |
|
141 |
132 |
106 |
А – 01М, СМД – 60 |
127 |
112 |
83 |
|
138 |
128 |
101 |
Д – 160 |
111 |
98 |
74 |
|
121 |
112 |
89 |
Д – 240Т, Д – 240ТЛ |
100 |
85 |
62 |
|
108 |
100 |
78 |
СМД – 18Н |
93 |
80 |
58 |
|
101 |
93 |
73 |
А – 41, СМД – 14НГ, |
88 |
76 |
56 |
|
95 |
88 |
69 |
СМД –14АН |
|
|
|
|
|
|
|
Д – 108-7, Д – 240, Д – 240Л |
79 |
68 |
50 |
|
86 |
79 |
62 |
Д – 241, Д – 241Л |
75 |
65 |
48 |
|
82 |
75 |
59 |
Д – 144-07, Д – 144-10 |
70 |
60 |
43 |
|
77 |
70 |
54 |
Д – 144-36 |
63 |
56 |
42 |
|
69 |
63 |
50 |
Д – 65Н, Д – 65М |
60 |
53 |
39 |
|
66 |
60 |
47 |
Д – 50, Д – 50Л |
56 |
48 |
35 |
|
60 |
56 |
44 |
Д – 21А1 |
41 |
36 |
26 |
|
45 |
41 |
32 |
87
Оптимизация ресурса машины с использованием функционально-статистических методов
Созданная в отрасли система управления качеством и ресурсами организаций, осуществляющих эксплуатацию СДМ, основывается на разработке каждым предприятием регламентных нормативов – стандартов предприятия (СТП) /1, 41/. В области механизации строительных работ типовые стандарты предприятия по эксплуатации машин разработаны Центральным научно-исследовательским институтом организации, механизации и технической помощи строительству (ЦНИИОМТП). В его рекомендациях по разработке и внедрению системы управления качеством эксплуатации строительных машин (УКЭСМ) предусматривается разработка комплекса СТП, подразделяющихся на следующие группы:
–основополагающий стандарт, определяющий основные (общие) положения, цели и задачи системы, структуру и функции управления, их распределение между звеньями организационной структуры, порядок взаимодействия подсистем и элементов, принятие управляющих решений;
–стандарты по организации планирования качества эксплуатации и расчета экономической эффективности функционирования системы УКЭСМ;
–стандарты по организации технологической подготовки производства, эксплуатации машин и контроля качества эксплуатации, то есть мате- риально-технического и метрологического обеспечения, подготовки и обучения кадров, информационного обеспечения, стимулирования персонала за повышение качества работы, а также правового обеспечения.
С целью обеспечения планирования и контроля качества эксплуатации в организациях, осуществляющих использование СДМ, система УКЭСМ разрабатывается и внедряется в соответствии с требованиями ГОСТ 25646-95. Рекомендации по организации ТО и ремонта строи-
тельных машин МДС 12-8.2000, которые разработаны в соответствии с ГОСТ 25646-95 «Эксплуатация строительных машин. Общие требова-
ния», а также ГОСТ 40.9001-88 и ГОСТ 40.9002-88 нормируют:
•виды ТО и ремонтов машин, их периодичность, продолжительность
итрудоемкость;
•перечень диагностических работ, выполняемых одновременно с объемом работ номерных видов ТО;
•трудоемкость диагностических работ, выполняемых при ТО-1,
ТО-2, ТО-3.
Типовые нормы периодичности, продолжительности и трудоемкости ТО и ремонтов определены на основе обработки статистических данных. При использовании машин в различных условиях эксплуатации, которые могут существенно отличаться от условий, принятых для типовых норм,
88
показатели продолжительности и трудоемкости ТО и ремонтов подлежат корректировке для местных условий ( ±10% ) /14/.
Система управления качеством эксплуатации машин предусматривает выполнение технического диагностирования в составе ТО и ремон-
тов, обеспечивая их проведение по фактическому техническому состоянию СДМ. Диагностирование организуется в соответствии с требованиями ГОСТ 25044-81. В результате технического диагностирования прогно-
зируется техническое состояние машины и ее остаточный ресурс.
Всоответствии с требованиями ГОСТ 25646-95 текущий ремонт должен обеспечивать наработку машины до очередного ремонта, а капитальный ремонт обеспечивать полный или близкий к полному ресурс машины.
Вбольшинстве случаев местные условия эксплуатации машин требуют корректировки нормируемых показателей, приведенных в Реко-
мендациях МДС 12-8.2000. При этом не обязательно нормируемый показатель должен приниматься с учетом предельно допустимых значений диагностических параметров технического состояния или прогнозируемой величины остаточного ресурса машины.
При оптимизации ресурса машины целесообразно учесть затраты на
ееэксплуатацию Сэ с учетом прибыли за счет продления ресурса на величину, превышающую нормативное значение, или с учетом дополнительных затрат за счет уменьшения ресурса на величину, меньшую чем нормативное значение. Прогнозируемый ресурс машины можно определить, исходя из критерия минимума затрат, выраженных целевой функцией:
Суд(t) = Сэ(t) +CР(t) →min, |
(4.4) |
где Суд(t) – удельные затраты на эксплуатацию машины с учетом прибыли (затрат) за счет продления (снижения) ресурса с учетом местных усло-
вий;Сэ(t) = Са(t) +Cэм(t)+Cэч(t) – удельные затраты на эксплуатацию машины, как сумма удельных затрат на ее приобретение Са(t), расходуемые
эксплуатационные материалы Cэм(t), а также затраты на ТО, текущий ремонт и запасные части Cэч(t); CР(t) – удельные затраты (прибыль) за счет снижения (переработки) нормативного ресурса машины.
На рис. 4.8 поясняется оптимизация прогнозируемого ресурса машины по критерию минимума удельных затрат на эксплуатацию машины.
Как видно, прогнозируемая величина ресурса t э |
сравнивается с величи- |
||
ной нормируемого ресурса t н с использованием коэффициента |
|||
Кр = |
tэ |
. |
(4.5) |
|
|||
|
tн |
|
Полученное (пример на рис. 4.8) в результате оптимизации прогнозируемого ресурса машины значение Кр = 0,9 принимается как нормативное для местных условий, исходя из критерия минимума удельных затрат Суд на ее эксплуатацию.
89