
955
.pdfразмещение принятых товаров по местам хранения после приемки.
--- экстенсивное использование оборудования. Наибольшую производи-
тельность машин и механизмов достигают максимальной продолжительностью их использования в течение суток (года). На суточный фонд времени работы машин влияют простои машин по организационным и техническим причинам, а также потери времени от неполного использования смен [7,8,9]. Потери времени по организационным и техническим причинам может охарактеризовать коэффициент использования парка:
Ки.п = Н1/Н2 , где Н1 – число машин и механизмов, которые находились в эксплуатации; Н2 – списочное число машин и механизмов базы.
Потери времени от неполного использования смен и недостаточной сменности работы машин может охарактеризовать коэффициент использования машин в течение суток; Ки.с = Тсм/24, где Тсм – продолжительность времени работы машин в течение суток, ч; 24 – продолжительность суток.
Произведение коэффициента использования машин в течение суток на коэффициент использования парка машин и механизмов характеризует потенциальные возможности использования машин и механизмов во времени
– экстенсивную загрузку: |
|
Кэ = Ки.п· Ки.с = (Тсм·Н1)/(24·Н2). |
(2.1) |
Вчислителе формулы время фактической работы машин Тфакт = Тсм·Н1,
взнаменателе – максимально возможное время использования машин
Тмакс = 24·Н2 (ч). Поэтому коэффициент экстенсивной загрузки можно определить и так Кэ = Тфакт/ Тмакс. Таким образом, зная время фактической работы машин и механизмов, а также максимальное время использования машин, можно определить коэффициент экстенсивной загрузки без расчета
Ки.п и Ки.с.
При полном устранении потерь времени в ходе эксплуатации машин и механизмов во время пребывания их в сфере производства погрузочноразгрузочных работ можно получить максимум экономии времени экстенсивного вида. К перерывам в работе, которые учитывают при определении коэффициента экстенсивного использования машин и механизмов, как правило, не относят техническое и технологическое обслуживание, а также другие простои на протяжении смены.
---- пример экстенсивного использования оборудования, машин и ме-
ханизмов. Списочный состав погрузочно-разгрузочных механизмов на предприятии оптовой торговли составляет Н2 = 20 единиц, ежедневно эксплуатируют Н1 = 15 единиц. Время работы механизма Тсм = 8 ч. Необходимо определить коэффициент экстенсивной загрузки Кэ механизмов при следующих условиях:
1)при существующих показателях;
2)при увеличении числа выпуска погрузочно-разгрузочных механизмов
вэксплуатацию на 20 %, т.е. Н1 = 18 единиц;
53
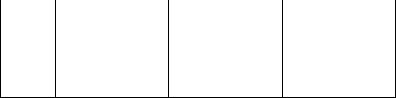
3)в случае увеличения времени работы механизма Тсм на 100 %;
4)при увеличении числа выпуска погрузочно-разгрузочных механизмов
вэксплуатацию на 20 % и увеличении времени их работы на 100 %. Коэффициент экстенсивной загрузки рассчитываем по формуле (2.1).
1.Кэ = (8·15)/(24·20)·100 % = 25 %. 3. Кэ = (16·15)/(24·20)·100 % = 50 %.
2.Кэ = (8·18)/(24·20)·100 % = 27 %. 4. Кэ = (16·18)/(24·20)·100 % = 60 %.
Таким образом, коэффициент экстенсивной загрузки увеличен: на 2 %
при увеличении числа выпуска механизмов в эксплуатацию; в 2 раза при увеличении времени работы машин и механизмов; в 2,4 раза при увеличении числа выпуска машин и механизмов и увеличении времени их работы. Следовательно, при экстенсивной загрузке техники, как видно из примера, большее значение имеет время работы механизма. Чем продолжительнее время работы машины, тем выше коэффициент экстенсивной загрузки и производительность используемой техники.
---- номограммный метод управления экстенсивным использованием оборудования. Определенную роль играет также экстенсивный фактор, т.е. время работы механизма: чем дольше работает машина, тем выше коэффициент экспансивной загрузки и, следовательно, производительность используемой техники [7]. Расчет произведен для одних суток. Приняты следующие области значений для обозначения. G – величина объема работ на определенный период, т. G = 5000 т; Т – продолжительность использования машин и механизмов в течение суток, ч; К – количество механизмов. К ={2,4,6,8} (единиц техники); Пр – часовая производительность, т/ч. Пр ={10,20,30} т/ч; Д – число рабочих дней. Д ={10,15,20}дней. Неизвестным является Т. В табл. 2.5 приведены значения произведений К·Пр.
Таблица 2.5
Значения К·Пр
|
|
|
|
Для построения номо- |
|
К |
Пр=10 |
Пр=20 |
Пр=30 |
граммы формируем об- |
|
2 |
К·Пр=20 |
К·Пр=40 |
К·Пр=60 |
||
ласть значений Пр·К без |
|||||
4 |
К·Пр=40 |
К·Пр=80 |
К·Пр=120 |
||
повторений {20,40,60,80, |
|||||
6 |
К·Пр=60 |
К·Пр=120 |
К·Пр=180 |
||
120,160,180,240}. Время |
|||||
8 |
К·Пр=80 |
К·Пр=160 |
К·Пр=240 |
работы машин и механизмов определяется выражением Т = G /(К·Пр). Результат расчета для значений К·Пр приведен в табл. 2.6.
|
|
|
Таблица 2.6 |
|
Время работы в сутки машин и механизмов |
||
|
|
|
|
К*Пр |
Д=10 |
Д=15 |
Д=20 |
20 |
>24 |
Т=5000/(Д·К·Пр)=16,6 |
Т=5000/(Д·К·Пр)=12,5 |
40 |
Т=5000/(Д·К·Пр)=12,5 |
Т=5000/(Д·К·Пр)=8,3 |
Т=5000/(Д·К·Пр)=6,25 |
60 |
Т=5000/(Д·К·Пр)=8,3 |
Т=5000/(Д·К·Пр)=5,5 |
Т=5000/(Д·К·Пр)=4,2 |
|
|
54 |
|

80 |
Т=5000/(Д·К·Пр)=6,25 |
Т=5000/(Д·К·Пр)=4,2 |
Т=5000/(Д·К·Пр)=3,1 |
|
|
|
Окончание табл. 2.6 |
120 |
Т=5000/(Д·К·Пр)=4,2 |
Т=5000/(Д·К·Пр)=2,7 |
Т=5000/(Д·К·Пр)=2,1 |
160 |
Т=5000/(Д·К·Пр)=3,1 |
Т=5000/(Д·К·Пр)=2,1 |
Т=5000/(Д·К·Пр)=1,6 |
180 |
Т=5000/(Д·К·Пр)=2,7 |
Т=5000/(Д*К*Пр)=1,8 |
Т=5000/(Д·К·Пр)=1,4 |
240 |
Т=5000/(Д·К·Пр)=2,1 |
Т=5000/(Д·К·Пр)=1,4 |
Т=5000/(Д·К·Пр)=1,0 |
Номограмма расположена в двух квадрантах. По данным табл. 2.6 в левом квадранте построены три графика зависимости Пр·К = f(К)Пр={10,20,30}, в правом квадранте построены три графика Т = f(G)/(Пр·К·Д)Д={10,15,20}.
Исходя из количества механизмов, часовой производительности Пр и длительности рабочего периода Д, можно определить необходимую продолжительность использования машин в течение суток Т.
Рис. 2.2. Номограмма расчета С помощью этой номограммы можно решить и обратную задачу, т.е.
зная продолжительность использования машин в течение суток Т, длительность периода работы Д и часовую производительность механизмов Пр, можно определить необходимое количество механизмов К.
--- процессы грузопереработки на складе. Во время хранения продуктов на складе важную роль играет грузопереработка, составляющая крупный элемент общих издержек логистики. Неправильная технология грузопереработки может привести к значительным повреждениям товаров (чем реже груз подвергается обработке, тем меньше шансов нанести ему какой-то ущерб и тем выше эффективность складского хозяйства в целом).
Для облегчения и повышения производительности грузопереработки продукты, изначально упакованные в банки, бутылки и коробки, комплектуют в более крупные грузовые единицы. Первичной такой единицей служит стандартный упаковочный модуль, который обладает двумя важными свойствами. Во-первых, он защищает продукты от возможных поврежде-
55

ний во время погрузки, транспортировки, хранения и других логистических операций. Во-вторых, стандартный модуль облегчает грузопереработку, так как с одной крупной упаковкой обращаться проще. Для большей производительности грузопереработки и транспортировки стандартные модули обычно объединяют в еще более крупные грузовые единицы, к которым относят пакеты, формируемые на стандартных паллетах (поддонах), и контейнеры разных типов. Если складское хозяйство, грузопереработка и упаковка эффективно интегрированы в логистическую систему компании, то они существенно ускоряют и облегчают движение материальных потоков.
Склад обеспечивает сохранность материальных ценностей, позволяет аккумулировать необходимые товары и является одним из важнейших элементов логистической системы.
---внутрискладская транспортировка. Транспортировка предполагает перемещение груза между различными зонами склада, выполняется с помощью подъемно-транспортных механизмов при минимальной протяженности по сквозным «прямоточным» маршрутам. Правильная маршрутизация движения транспортных средств уменьшает повторные возвращения между переделами и повышает эффективность операций.
---управление запасами**. Запасы на складе служат для сглаживания конъюнктурных колебаний; в логистике рациональные запасы рассматриваются как необходимый фактор стабильных и надежных поставок материальных ресурсов с учетом колебаний спроса.
Всовременной «теории запасов» на смену традиционному управлению появился новый подход. Новый подход трактует запас как ширму, под которой скрыты многие недостатки производственно-хозяйственной деятельности: проблема качества, неспособность производить продукцию мелкими партиями, неумение правильно планировать и приобретать нужные товары, сбои в производстве и поставках продукции и т.д. [13].
- показатели работы склада. Различают технические и экономические показатели работы склада.
-- технические показатели работы склада. К техническим характеристи-
кам склада относят полезную площадь склада (площадь, непосредственно занятую хранимыми материалами), площадь, занятую приемочными и отпускными площадками, вспомогательную площадь (проезды, проходы).
---полезная площадь склада. Полезная площадь – это площадь, непосредственно занятая хранимым материалом, расположенным, например,
на стеллажах. Полезную площадь определяют двумя способами: либо по нагрузке, допустимой на 1м2 площади пола, либо на основании коэффициента заполнения объема.
---- полезная площадь склада по нагрузке. По нагрузке на пол площадь
max
gзап gmax
определяют по формуле sпол = , где зап – величина установленного за-
56
паса соответствующего материала на складе, т; – нагрузка на 1 м2 площади пола, т. В работе [8] приведены значения для разных складируемых
материалов, например, для литья и поковок = 2-3,5 т/м2, для инструмен-
та = 0,8-1,2 т/м2.
Пример. Определить размер полезной площади склада для хранения литья ( = 3) при коэффициенте ее использования к = 0,35. Грузооборот склада за год составляет G = 7200 т. Срок хранения груза t = 3 сут.
Решение. Среднесуточное поступление груза составит g = 7200/365 = = 20 т/сут; за трое суток величина груза составит 60 т. Величина полезной площади с учетом промежуточных величин:
sпол = (g·t)/( ·к) = 60/(3·0,35) = 57 м2.
---- полезная площадь по заполнению объема. Полезную площадь по за-
полнению объема склада определяют по формуле sпол = l·b·n (м2), где l – длина соответствующего оборудования для хранения, м; b – ширина, м; n
– потребное количество оборудования (ячеек, стеллажей, штабелей); n = gзамmax /gоб; gоб – вес материала, хранимого, например, на ячейках,
gоб = Vоб· · ; Voб – геометрический объем соответствующего оборудования, м3; – удельный вес материала или изделия, т/м3; – коэффициент заполнения объема (плотности укладки).
Пример. Определить полезную площадь склада, если в течение года на него поступают пиломатериалы объемом 50 000 м3. Пиломатериалы хранят в штабелях размером 6,5·6,5·5 м3, срок хранения пиломатериала t = = 6 сут.
Решение. Площадь одного штабеля s = 6,5·6,5 = 42,3 м2, емкость этого штабеля составила v = s·5=211,15 м3. С учетом коэффициента заполнения объема емкость одного штабеля составила v’ = v· = 169 м3 ( = 0,8). Количество пиломатериалов, поступающих за сутки, g = 50000/365 = 137 м3/сут; за шесть суток g’ = g·6 = 137·6 = 822 м3. Количество штабелей n = = g’/v’ = 822/169 = 5 шт.
Площадь склада с учетом коэффициента использования площади k = 0,35 составит S = (n·s)/k = 5·42,3/0,35 = 604,3 м2.
--- площадь, занятая приемочными и отпускными площадками. Пло-
щадь определяют по формуле sпр= Q·k·t/ (360· 1), где Q – годовое поступление материала, т; 1 – нагрузка на 1 м2 площади, т; k – коэффициент неравномерности поступления материала на склад (1,2–1,5); t – количество дней нахождения материала на приемочной площадке (до 2 дней).
Пример. Определить размер приемочной площадки склада для хранения литья ( =3) при коэффициенте ее использования k=0,35. Грузооборот склада составляет G = 7200 т/год. Срок хранения груза на складе 2 сут.
Решение. Среднесуточное поступление груза g = G/360 = 20 т. Площадь приемочной площадки при принятом коэффициенте неравномерно-
57
сти поступления груза k = 1,2 составит sпр=(g·k·t)/ = 16 м2. Площадь приемочной площадки склада с учетом коэффициента использования площади k = 0,35 составит sпр = sпр/k = 16/0,35 = 45,7 м2.
Размер отпускной площадки определяется по аналогичной формуле, при меньшем значении коэффициента неравномерности k.
--- cлужебная и вспомогательная площадь склада. Площадь конторы склада при штате склада до трех работников принимают по 5 м2 на каждого человека; при штате от 3 до 5 работников принимают 4 м2, при штате более 5 работников – по 3,25 м2.
Вспомогательные площади определяют в зависимости от габарита хранимых материалов, размеров грузооборотов, подъемно-транспортных средств. Для этой цели используют формулу А = 2·В + 3·С где А – ширина проезда, см; В – ширина транспортного средства; С – ширина зазоров между транспортными средствами и между ними и стеллажами по обе стороны проезда (принимается 15 – 20 см). В абсолютных величинах ширину главных проездов (проходов) принимают от 1,5 до 4,5 м. Ширина боковых проездов (проходов) – от 0,7 до 1,5 м.
Общая площадь будет равна S = sпол + sпр + sсл + sвсп (м2). При приближенных расчетах общую площадь складов S определяют в зависимости от полезной площади sпол через коэффициент использования, а по формуле
S = sпол /а, величину а определяют из [8]. Например, для литья и поковок коэффициент, а = 0,4 – 0,6, для инструмента – а = 0,3 – 0,35.
-- экономические показатели работы склада. В работе [9] рассмотрены технико-экономические показатели эффективности работы склада.
Первая группа показателей (показатели объема работы складского комплекса).
складской товарооборот (количество реализованной продукции за соответствующий период времени - месяц, квартал, год);
складской грузооборот (количество отпущенных материальнотехнических ресурсов в течение определенного времени);
грузопоток (количество грузов, проходящих через производственный участок склада в единицу времени);
грузопереработка (количество перегрузок и перевалок по ходу перемещения груза в объеме грузопотока);
коэффициент неравномерности поступления (отпуска) груза со склада (отношение максимального поступления или отпуска груза в тоннах за определенный период времени к его среднему поступлению или отпуску);
коэффициент оборачиваемости материалов (отношение годового или квартального оборота материалов к их среднему остатку на складе за тот же период времени).
Вторая группа показателей (показатели эффективности использования складских площадей и объемов).
58
использование площади складских помещений (отношение полезной площади, занятой хранимыми материалами, к общей площади склада);
средняя нагрузка, приходящаяся на 1 м2 складской площади (отношение количества хранимого материала на складе в тоннах к общей площади склада);
коэффициент использования объема склада (отношение полезного объема, занятого материалом, к общему объему склада);
Kv = vпол /V = (sпол·hпол)/(S·Н), где V – общий объем склада (м3); vпол – складской объем, занимаемый оборудованием, на котором хранится груз (м3); H
– высота складского помещения (м), hпол – используемая высота складского помещения под хранение груза (м);
грузонапряженность (произведение показателя использования пло-
щади складских помещений и коэффициента оборачиваемости грузов, измеряют в т/м2).
Третья группа показателей (показатели использования подъемнотранспортного оборудования).
коэффициент использования по грузоподъемности (отношение веса поднимаемого и перемещаемого груза к номинальной грузоподъемности механизма);
коэффициент использования по времени (отношение времени нахождения механизма в работе к общему времени работы складского комплекса);
фактическое время простоя подвижного состава под грузовыми операциями (отношение количества груза в одной подаче, подлежащего переработке, погрузке или выгрузке, к часовой производительности механизма).
Четвертая группа показателей (показатели производительности труда складского персонала).
Пятая группа показателей (показатели сохранности материальных ценностей и качества обслуживания потребителей).
размер естественной убыли материально-технических ресурсов (отношение суммы расхода грузов за отчетный период и их остатка на данное число, умноженной на средний период хранения и норму естественной убыли в процентах, к сроку хранения);
бесперебойность обеспечения потребителей материальнотехническими ресурсами; уровень централизованной доставки грузов со склада (отношение количества грузов в тоннах, доставляемых централизованно за определенный период времени – месяц, квартал, год, к общему количеству отпущенных со склада грузов в тоннах).
Шестая группа показателей (показатели размера капиталовложений
исебестоимости переработки грузов).
59
абсолютные данные о размере капиталовложений; коэффициент удельных капиталовложений по отдельным вариантам механизации складских работ (отношение размера капиталовложений к годовому грузообороту);
себестоимость складской переработки 1 т грузов (отношение общей величины годовых эксплуатационных расходов к общему количеству переработанного за год груза в тоннах). С = Oз /Q, где Оз – сумма единовременных и текущих затрат; Q – вес товара, размещенного на оборудовании склада (т). Оз = Э + К ·0,29 (руб./т), где Э – величина текущих затрат (руб./т); К – величина единовременных затрат (руб./т); 0,29 – коэффициент эффективности капитальных вложений.
Э= А/(n·Q), где А – затраты, связанные с амортизацией, эксплуатацией и ремонтом оборудования склада (руб.); n – оборачиваемость товара (365 дн. /t3 дн.), здесь t3 – средняя продолжительность срока хранения товара на складе (товарный запас в днях); К = Ct /(n·Q), где Сt – стоимость оборудования, размещенного на складе.
С позиции логистики основными показателями эффективности определены используемая вместимость склада, оборачиваемость товарных запасов и величина полных затрат на переработку груза.
-- пути повышения эффективности работы склада. Для повышения эф-
фективности работы склада необходимо [1]:
произвести разделение склада на основные рабочие зоны. Определить последовательности прохождения грузов через эти зоны;
сократить количество складских операций до минимума и ликвидировать возвратные грузопотоки;
создать комплекс моделей движения материального и информационного потока на входе, выходе и внутри склада по его рабочим зонам;
увязать прохождение грузов через склад с моделью материального потока на его входе и выходе;
использовать наилучшим образом вместимость склада;
согласовать техническое оснащение склада с моделями движения материального потока на его входе, выходе и внутри склада;
скоординировать функции служб закупок и продаж с функциями, выполняемыми внутри склада. Координация этих функций обеспечивает эффективное решение многих задач. На оперативном уровне она позволяет осуществить планомерную поставку товаров на склад и тем самым производить “регулирование” процессов на складе.
Большой проблемой на складе является прогноз величины материального и информационного потоков в реальном масштабе времени и их сопряжение между собой, а также сопряжение модели возникновения материального потока на входе/выходе с характеристиками технических средств, участвующих в процессах разгрузки и погрузки [4].
60
-издержки на складе. Различают пять типов издержек, оказывающих влияние на выбор стратегии функционирования склада.
-- издержки поставок. Эти издержки обычно разделяют на две части. Первая часть связана с оплатой поставщику стоимости товара, вторая часть – издержки самой системы склада. Эта часть издержек связана с зарплатой работников склада, оформлением и обработкой заказа, составлением отчетной документации, транспортными расходами и т.д.
-- издержки содержания запаса. Данный тип издержек классифицируют на издержки, зависящие от размера заказа, и издержки, не зависящие от него. Ко второму типу издержек относят издержки на страховку, налоги, арендную плату за складское помещение, стоимость эксплуатации помещения и т.д. В некоторых случаях наиболее важны не прямые издержки, а косвенные потери, возникающие из-за того, что деньги вкладывают в запасы и не используют их в других сферах. Потери от этого равны наибольшей прибыли, которую склад мог бы получить от размещения денег в другую, более выгодную сферу деловой активности. Если деньги инвестируют в складское хозяйство, то тем самым отказываются от прибыли.
-- издержки выполнения заказов потребителей. Эти издержки обычно состоят из издержек учетных операций (составление накладной, записи в журнале, информации о положении дел и т.д.), зарплаты соответствующих работников склада, издержек на упаковку и транспортирование, если они оплачиваются складом.
Несмотря на изменение издержек при колебаниях интенсивности спроса, они не зависят от стратегии управления запасами. Поэтому их не учитывают при определении издержек, которые меняются с изменением стратегии функционирования склада. С другой стороны, издержки, связанные с дефицитом запасов на складе, зависят от стратегии его функционирования, поскольку именно от стратегии зависит время дефицита запаса.
-- издержки, связанные с дефицитом. Их трудно определить, однако при отсутствии товара на складе теряется покупательский спрос на него. Покупатель в будущем может отказаться от услуг этого склада.
-- издержки по сбору и обработке данных. Издержки связаны со сбором информации о спросе на продукцию, ее анализом, учетом и прогнозом покупательского спроса и т.д. Использование этих издержек возможно при выработке приемлемой стратегии функционирования склада. Критерием выбора может быть минимум издержек.
-стратегия функционирования склада. Под стратегией понимают при-
нятие решений о времени и количестве заказываемой продукции и решении следующих вопросов.
Какой уровень ресурсов следует иметь на складе для обеспечения требуемого уровня обслуживания потребителей?
Какими ресурсами должен располагать каждый передел?
61
В чем состоит компромисс между уровнем обслуживания потребителя и уровнем материальных ресурсов на складе?
Должны ли товары отгружаться непосредственно с предприятия?
Каково значение компромисса между выбранным способом перевозки и величиной запаса?
Каков общий уровень материальных запасов, связанный со спецификой уровня обслуживания?
Как и где надо размещать страховые запасы?
Как изменятся затраты на содержание товара в зависимости от числа складов на полигоне?
В сети распределения товаров потребителям есть несколько маршрутов (физических каналов), каждый из которых по-разному воздействует на уровень обслуживания потребителя и на уровень запасов в системе. Так, товары с заводского склада могут непосредственно поступать на региональный склад, или/и локальные склады региона, или/и предприятия розничной торговли. Такую систему взаимодействия складов называют системой с разветвленной (иерархической) структурой. В корне такого дерева расположен заводской склад. Данная структура не имеет единую систему управления, так как разные уровни подчинены разным организациям (владельцам). Менеджер любого уровня управляет только своим предприятием и складом.
Библиографический список
1.Гаджинский А.М. Логистика. – М.: Дашков и Ко, 2004.
2.Денисов А.А., Колесников Д.Н. Теория больших систем управления: Учебное пособие для вузов. – Л.: Энергоиздат. Ленингр. отд-ние, 1982.
3.Дыбская В. В. Логистический взгляд на оптовый склад//Логистика. – 2000 - №2 – С. 30–31.
4.Зеваков А.М. Логистика материальных запасов и финансовых активов. – СПб.: Питер, 2005.
5.Институциональная экономика: Учеб пособие/Под рук. акад. Д.С. Львова. – М.: ИНФРА-М, 2001.
6.Лафта Дж. К. Менеджмент: Учебник. – М.: ПБОЮЛ Григорян А.Ф., 2002.
7.Логистика: Учебник/Под ред. Б.А. Аникина. – М.: ИНФРА-М, 2000.
8.Неруш Ю.М. Коммерческая логистика: Учебник для вузов. – М.: Банки и биржи, ЮНИТИ, 1997.
9.Практикум по логистике: Учеб. пособие/Под ред. Б.А. Аникина. – М.: ИНФРА- М, 2000.
10.Парсонс Т. Понятие общества. Компоненты и их взаимоотношения // Реферативный журнал «Социология». – 1993. – № 3–4.
11.Пустобаев В.П. Инфраструктура понятия эксперимента: Учеб. пособие для студентов технических и экономических вузов. – Омск: Изд-во ОмГПУ, 1999.
12.Радугин А.А., Радугин К.А. Социология. – М.: Центр, 2000.
13.Хруцкий Е.А., Сокович В.А., Колесов С.П. Оптимизация хозяйственных связей и материальных запасов. – М.: Экономика, 1977.
62