
[SHipinsky_V.G.]_Oborudovanie_i_osnastka_upakovoch1(z-lib.org)
.pdf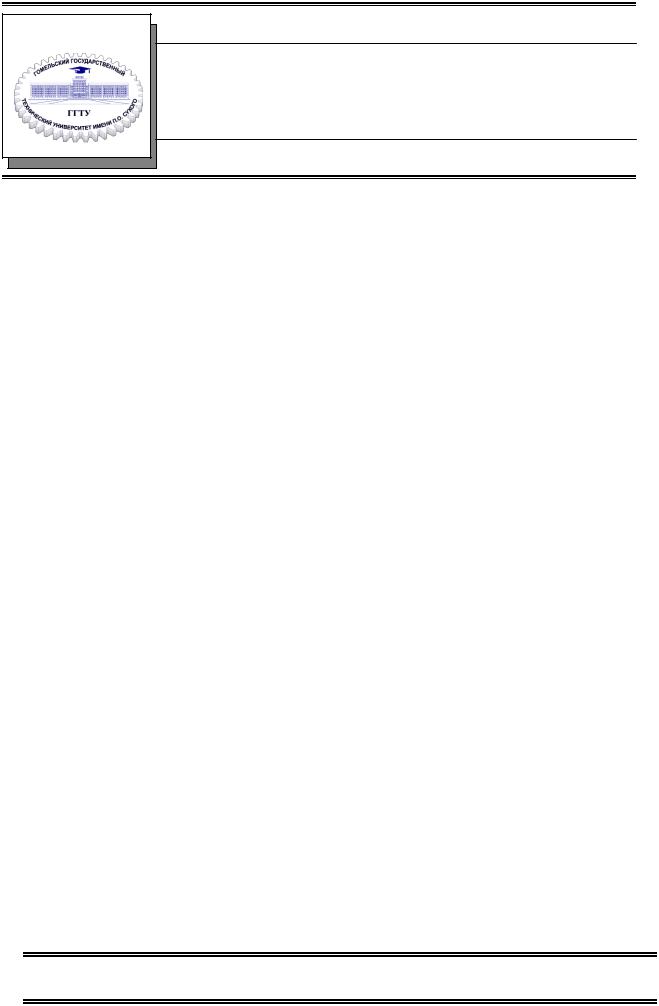
Министерство образования Республики Беларусь
Учреждение образования «Гомельский государственный технический университет имени П.О. Сухого»
Кафедра «Обработка материалов давлением»
В. Г. Шипинский
ОБОРУДОВАНИЕ И ОСНАСТКА УПАКОВОЧНОГО ПРОИЗВОДСТВА
Часть I. Структура и функциональные устройства упаковочных машин
УЧЕБНОЕ ПОСОБИЕ
для студентов специальности I-36 20 02-03 «Упаковочное производство (технологии и оборудование упаковочного производства)»
Гомель 2013
УДК 621. 798.06(075.8)
ББК 30.61я73
Ш65
Шипинский В. Г.
Ш65 Оборудование и оснастка упаковочного производства. Часть I.
Структура и функциональные устройства упаковочных машин/
В. Г. Шипинский. – Гомель: ГГТУ им. П.О. Сухого, 2013. 153 с.: ил.
Приводятся основные понятия о производственном и технологическом процессах; структурно-функциональной классификации технологических
машин, комплексов и линий; их основных технических характеристиках и применяемых системах управления. Содержатся основные конструктивные исполнения и необходимые методики проектировочных расчетов типовых функциональных устройств, обеспечивающих дозирование и фасование продукции, автоматическую загрузку штучных изделий, транспортирование объектов обработки, подачу рулонных материалов и сварку конструктивных элементов упаковки.
Книга предназначена для студентов высших учебных заведений, обучающихся по специальности «Упаковочное производство». Будет полезна для инженерно-технических работников, занимающихся упаковочным технологическим оборудованием, комплексной автоматизацией производственных процессов, технологиями и оснасткой тароупаковочного производства, созданием и производством самой упаковки, а также товарообращением.
УДК 621. 798.06(075.8) ББК 30.61я73
Учреждение образования “Гомельский государственный технический университет имени П.О. Сухого”, 2013
2
ВВЕДЕНИЕ
Упаковывание продукции – это сложная многофункциональная задача, эффективное решение которой тесно связано с созданием и производством современных упаковочных материалов, функционально совершенной упаковки
исредств пакетирования грузов, разнообразного технологического оборудования, а также с производством самой продукции. Сложность технологического оснащения и комплексной автоматизации тароупаковочного производства обуславливается огромным разнообразием производимой продукции, видов упаковки и средств пакетирования грузов, их типоразмеров и конструктивных исполнений. Этими факторами, в свою очередь, определяется
ибольшая номенклатура разнообразных видов тароупаковочных машин, уровень универсальности, степень автоматизации, производительность и стоимость которых, как правило, зависят от широты номенклатуры и объемов выпуска упаковываемой продукции, то есть от типа производства.
Вструктуре производственного процесса операции упаковывания продукции и формирования из нее укрупненных грузовых единиц выполняются, как правило, на завершающих этапах. В обобщенном виде эта часть технологического процесса включает в себя такие этапы, как:
изготовление тары и других упаковочных средств;
подготовка тары, укупорочных средств и других элементов упаковки к упаковыванию;
подготовка к упаковыванию изготовленной продукции (изделий);
дозирование и фасование (укладка) продукции (изделий) в тару;
укупоривание тары, маркировка и оформление упаковочных единиц;
группирование упаковочных единиц и укладка в транспортную тару;
укупоривание транспортной тары и маркировка транспортных единиц;
подготовка средств пакетирования;
формирование из транспортных единиц с помощью средств пакетирования укрупненных грузовых единиц;
складирование укрупненных грузовых единиц и отгрузка товара потребителям.
Всвою очередь перечисленные этапы обычно состоят из нескольких последовательных операций, которые выполняются технологическими машинами, содержащими адекватные исполнительные устройства и механизмы. Эти машины часто объединяются сквозной транспортирующей системой, как между собой, так и с технологическим оборудованием по производству самой продукции, образуя работающие в едином технологическом ритме механизированные или автоматизированные комплексы и поточные линии, связанные общей системой управления.
1. СТРУКТУРНО-ФУНКЦИОНАЛЬНАЯ КЛАССИФИКАЦИЯ МАШИН УПАКОВОЧНОГО ПРОИЗВОДСТВА
Машина (франц. machine, от лат. machina) – механическое устройство с согласованно работающими частями, осуществляющее определенные целесообразные движения для преобразования энергии, материалов или
3
информации. Основное назначение машин – частичная или полная замена производственных функций человека с целью облегчения труда и повышения его производительности.
Машины, предназначенные для осуществления технологического процесса, называются технологическим оборудованием. Это оборудование можно классифицировать по функциональному назначению, уровню механизации и автоматизации технологического процесса и структуре построения.
Функциональная классификация технологического оборудования определяется выполняемыми на нем основными операциями или этапами упаковочного процесса. По функциональному назначению оно подразделяется, например, на оборудование, предназначенное для изготовления тары и других упаковочных средств, дозирования и фасования продукции (изделий) в тару, укупоривания тары, маркировки и декоративного оформления упаковочных единиц, упаковывания в транспортную тару, изготовления средств пакетирования, формирования укрупненных грузовых единиц и т. д.
По уровню механизации и автоматизации процесса технологическое оборудование подразделяется на оборудование с ручным управлением, а также полуавтоматическое и автоматическое оборудование.
В оборудовании с ручным управлением машиной производятся непосредственные воздействия на предметы труда, а человеком осуществляется загрузка исходных материалов или компонентов упаковки, выгрузка обработанных предметов труда, а также непосредственное управление рабочим циклом.
Полуавтоматическим называется такое оборудование, на котором загрузка исходных объектов обработки в машину и выгрузка из нее обработанных предметов труда выполняются рабочим вручную, а процесс непосредственного воздействия на предметы труда в течение цикла осуществляется автоматически.
Автоматическим называется самоуправляющееся оборудование, на котором без непосредственного участия человека, то есть автоматически, выполняются все действия технологического цикла, для которых оно предназначено, включая и переход к следующему циклу. Человек здесь только контролирует процесс работы, периодически пополняет исходными объектами обработки питатель автомата, подналаживает оборудование и удаляет отходы.
Гибкий производственный модуль (ГПМ) – это единица технологического оборудования, оснащенная автоматизированными устройствами переналадки, программного управления и средствами автоматизации технологического процесса, автономно функционирующая, осуществляющая многократные циклы и имеющая возможность встраивания в систему более высокого уровня.
Если автоматическое оборудование создается на базе универсальной технологической машины путем оснащения ее дополнительными устройствами и передачи цикловых функций, выполняемых человеком, механическому устройству – промышленному роботу, то такое оборудование называют
робото-технологическим комплексом (РТК).
4

Промышленным роботом в свою очередь называется автоматическая машина, стационарная или подвижная, состоящая из исполнительного устройства в виде манипулятора, имеющего несколько степеней подвижности, а также устройства программного управления и предназначенная для выполнения в производственном процессе двигательных и управляющих функций.
По принципу перемещения объектов обработки, пользуясь классификацией С. И. Артоболевского, все упаковочное технологическое оборудование можно разделить на три класса.
В технологическом оборудовании I-го класса изготавливаемый объект занимает одну позицию и в течение цикла является неподвижным или совершает ограниченные перемещения в пределах этой позиции. Таковыми являются упаковочные машины, в которых, например, тара 1 (рис.1.1а) занимает постоянное положение на рабочей позиции, а упаковываемые изделия, укупорочные средства, этикетки и другие необходимые элементы упаковки подаются к ней соответствующими исполнительными механизмами 2 для формирования готовой упаковочной единицы.
Рис. 1.1. Структурные схемы технологического оборудования
Втехнологическом оборудовании II-го класса изготавливаемый объект в процессе обработки дискретно или непрерывно последовательно перемещается по всем его рабочим позициям, при этом исполнительные механизмы (орудия труда) неподвижны и занимают на каждой позиции заданное им положение. К таковому относится, например, карусельное оборудование в котором вращающийся или периодически поворачивающийся рабочий стол 1 (рис.1.1б) несет на себе закрепленные с заданным шагом объекты обработки 2, а исполнительные механизмы 3 при этом с адекватным шагом закрепляются на станине 4 машины и работают в каждом цикле по параллельной схеме действия. Время рабочего цикла в таком оборудовании определяется продолжительностью наиболее длительной операции.
Втехнологическом оборудовании III-го класса изготавливаемый объект в процессе обработки непрерывно перемещается совместно с исполнительным механизмом, производящим на него технологическое воздействие. К таковым относятся, например, роторные фасовочные автоматы, содержащие во вращающемся технологическом роторе 1 (рис.1.1в) несколько фасовочных блоков 2 с дозаторами. Тара 3 поочередно устанавливается в эти блоки синхронно вращающимся транспортным ротором 4, затем в процессе вращения ротора заполняется из дозатора упаковываемым продуктом, а в конце цикла
5
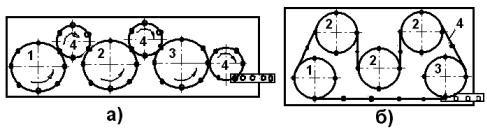
выводится из блока фасовочного ротора другим транспортным ротором 5. Оборудование этого класса обладает наиболее высокой производительностью, определяющейся количеством исполнительных блоков 2 в технологическом роторе 1.
Если технологическое оборудование на производственном участке установлено в последовательности выполняемых операций технологического процесса, то оно образует поточную линию.
Поточная линия – это такой производственный участок, на котором постоянно или периодически изготовляется один или несколько видов изделий, при этом рабочие места (станки, стенды и т. д.) специализированы на выполнение одной или нескольких однотипных операций и расположены (обычно в линию) по ходу технологического процесса. Поточные линии
характеризуются |
прямоточностью |
и |
могут быть |
немеханизированными, |
|||
механизированными, |
конвейерными, |
автоматическими, |
и |
гибкими |
|||
автоматизированными. |
|
|
|
|
|
|
|
Автоматические поточные линии образуются, в частности, на базе |
|||||||
станков-автоматов |
работающих с |
единым ритмом |
от |
общей |
системы |
управления и объединенных автоматизированной транспортной системой. Разновидностью последних являются роторные и роторно-конвейерные линии.
Автоматические роторные линии имеют общую структуру, которая характеризуется наличием ротора питания 1 (рис. 1.2а), а также технологических (рабочих) 2, контрольных 3 и транспортных 4 роторов, объединенных в систему с синхронизированным транспортным движением объектов обработки и общим управлением. При этом в инструментальных блоках рабочих роторов осуществляются технологические воздействия на объекты обработки в процессе их совместного непрерывного движения.
Роторно-конвейерной линией называется автоматическое технологическое оборудование, содержащее загрузочный 1 (рис. 1.2б), технологические 2, выгрузочный 3 и другие роторы, объединенные в систему синхронизированного движения общим конвейером 4, обеспечивающим непрерывное транспортирование объектов в процессе их обработки.
Рис. 1.2. Структурные схемы роторной (а) и роторно-конвейерной (б) линий
В зависимости от вида выполняемых операций, их трудоемкости и других технологических факторов автоматические линии могут строиться по последовательной, последовательной многопоточной, параллельной и последовательно-параллельной (смешанной) схемам обработки.
Линии с последовательной схемой обработки (рис. 1.3а) применяются при изготовлении сложных изделий или упаковочных единиц. В них, например, производится подача из питателя бутылок, мойка и сушка стеклянной тары,
6
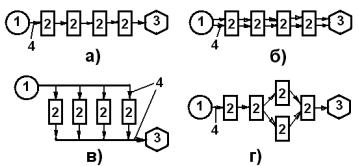
фасование в нее жидкой продукции, укупоривание тары, этикетирование и маркировка упаковочных единиц.
При возможности одновременного изготовления нескольких упаковочных единиц целесообразно применять линии с последовательной многопоточной обработкой (рис. 1.3б). На таких линиях, например, в подаваемом рулонном полотне формуют несколькими параллельными рядами стаканы, затем в них фасуют пастообразную продукцию, далее стаканы укупоривают герметично привариваемыми платинками и в конце готовые упаковочные единицы отделяют (вырубают) из отходов полотна.
Рис. 1.3. Структурные схемы автоматических линий: 1 – питатель; 2 – технологические автоматы; 3 – накопитель; 4 – транспортирующая система.
При выполнении простых упаковочных операций с малогабаритными предметами применяются линии с параллельной обработкой (рис. 1.3в), где подача объектов обработки производится из одного общего питателя сразу в несколько параллельно работающих автоматов и готовые упаковочные единицы принимаются из них в один общий накопитель. Этим достигается существенное упрощение линии. На таких линиях, например, упаковывают в обертку карамели.
Линии с последовательно-параллельной (смешанной) схемой обработки (рис. 1.3г) применяют в тех случаях, когда по ходу технологического процесса имеются отдельные операции, на выполнение которых требуется больше времени, чем на остальные. И чтобы исключить простои остального оборудования и повысить тем самым общую производительность линии на таких более продолжительных операциях соответственно устанавливаются параллельно работающие автоматы.
По компоновке и организации потока автоматические линии подразделяются на линии с жесткой и линии с гибкой передачей объектов обработки.
Если в автоматической линии автоматы сблокированы в единую неразрывную цепь с жесткой передачей предметов обработки (рис. 1.4а), то при сбое в работе, хотя бы одного из них останавливается работа всей линии и соответственно снижается ее действительная производительность. Следовательно, по такой схеме целесообразно выполнять линии, включающие небольшое число надежно работающих технологических автоматов и других устройств.
Надежность работы более сложных многооперационных линий повышают за счет установки между автоматами промежуточных приемниковнакопителей с определенным запасом полуфабрикатов. Если такие приемники-
7

накопители гибко связывают между собой все входящие в линию автоматы (рис.1.4б), то в этом случае каждая единица оборудования превращается в независимый технологический модуль. И если в такой линии кратковременно выходит из строя или останавливается какой-либо автомат, то остальные автоматы продолжают работать за счет имеющихся запасов полуфабрикатов в их приемниках-накопителях.
Рис. 1.4. Структурные схемы автоматических линий: 1 – питатель; 2 – технологические автоматы; 3 – приемник-накопитель; 4 – накопитель; 5 – транспортирующая система.
Однако приемники-накопители существенно усложняют конструктивное исполнение линии, увеличивают ее размеры и стоимость. Поэтому наибольшее распространение получили автоматические линии, в которых жесткие связи устанавливаются в пределах коротких участков (рис. 1.4в), соединенных между собой гибкой связью, обеспечиваемой промежуточными приемникаминакопителями.
1.1. Системы управления автоматическим оборудованием
Системы управления обеспечивают выполнение функциональными устройствами автоматических машин определенных взаимосвязанных действий, предусмотренных заранее установленной программой. По степени участия человека в управлении автоматическое технологическое оборудование подразделяется на цикловое, рефлекторное и самонастраивающееся.
В цикловых автоматах и линиях выполняется жестко заданная программа технологического цикла без контроля (разомкнутые системы) или с контролем (замкнутые системы) за процессом ее выполнения. При этом под циклом понимается совокупность элементарных действий, осуществляемых в определенной повторяющейся последовательности при выполнении машиной рабочих функций.
Разомкнутые цикловые системы автоматического управления (САУ)
вырабатывают управляющие сигналы (действия) по истечении определенного промежутка времени (т. е. в функции времени) либо при достижении рабочими органами определенных положений (т. е. в функции положения). В частности, наиболее характерным примером такой системы управления в функции
времени являются командоаппараты |
с |
непрерывно |
или периодически |
вращающимся распределительным валом. |
При этом |
установленные на |
распределительном валу кулачки непосредственно, либо через механические, гидравлические, пневматические, электрические и другие связи управляют всеми исполнительными механизмами машины. Привод распределительного вала 1 (рис.1.5а) такого командоаппарата осуществляется через редуктор 2 от
8
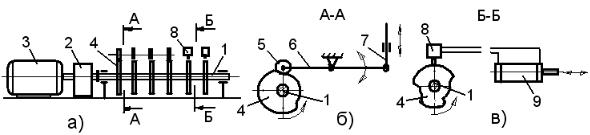
индивидуального электродвигателя 3 или через систему передачи вращения непосредственно от основного привода автомата. На распределительном валу закрепляются кулачки 4, профиль торцевой поверхности которых адекватен цикловым перемещениям соответствующих исполнительных механизмов автомата.
Рис. 1.5. Схема циклового кулачкового командоаппарата
Например, при механической передаче движения ролик 5 (рис. 1.5б) в процессе вращения вала 1 прокатывается по профильной торцевой поверхности кулачка 4, и все ее радиальные отклонения передает через качающийся рычаг 6 на адекватно перемещающееся исполнительное звено 7. Точность работы машины при этом полностью определяется точностью физического моделирования программы ее механизмами и устройствами (т. е. точностью изготовления кулачков, копиров и других звеньев передачи движений). При пневматической связи кулачок 4 (рис.1.5в) своей профильной торцевой поверхностью воздействует на шток распределителя 8, обеспечивающего подачу сжатого воздуха в соответствующие полости пневмоцилиндра 9, осуществляющего адекватные перемещения связанного с ним исполнительного звена автомата. При электрических связях вместо распределителя 8 с кулачком 4 взаимодействует кнопочный или бесконтактный электропереключатель, обеспечивающий адекватное включение и выключение электропривода исполнительного звена и т. д. Продолжительность полного цикла таких автоматов определяется временем, за которое распределительный вал совершает полный оборот. Эти системы управления применяются обычно в узкоспециализированных автоматах, характеризующихся жестким ритмом процесса.
Функционирующие по временному принципу разомкнутые САУ выполняются также на командоаппаратах, содержащих несколько реле времени (таймеров). Включение в работу и отключение соответствующих исполнительных механизмов автомата осуществляется этими реле, отсчитывающими запрограммированную выдержку времени.
Характерным примером разомкнутой САУ в функции положений являются, например, системы, снабженные путевыми контактными переключателями. В них каждый последующий исполнительный механизм включается в работу по сигналу, поступающему от предыдущего механизма и свидетельствующему об окончании предшествующего этапа цикла.
Иногда рассмотренные разомкнутые САУ комбинируют, то есть одними исполнительными механизмами машины управляют в функции времени, а другими – в функции положения.
9
Замкнутые цикловые САУ характеризуются наличием обратной связи, то есть они вырабатывают запрограммированные управляющие сигналы на исполнительные механизмы автомата только при поступлении от них заданного обратного потока информации (информации обратной связи). В этих системах переход от выполненного этапа цикла к следующему зависит от требуемого положения или состояния соответствующих исполнительных органов, которые контролируются устройствами обратной связи. В качестве последних широко применяются различные путевые микропереключатели, тактильные, оптические и другие датчики. Наиболее распространенными в настоящее время являются САУ, основанные на использовании управляющих вычислительных машин. Такие гибко программируемые специализированные электронные управляющие системы называются программируемыми
контроллерами (ПК).
Рефлекторные САУ обеспечивают работу оборудования в соответствии с заданной программой, а также осуществляют непрерывный контроль над ходом процесса по потоку информации обратной связи и путем сопоставления задающей программы с фактически реализуемой непрерывно вырабатывают сигнал рассогласования, корректирующий ошибку. Таким образом, рефлекторное автоматическое оборудование освобождает человека, как от функции управления, так и от функции контроля над выполняемым технологическим процессом и качеством производимой продукции.
В самонастраивающемся технологическом оборудовании по заданным конечным параметрам процесса и в зависимости от совокупности фактических условий автоматически изыскивается и производится оптимальное управление процессом, то есть человек освобождается (целиком или частично) и от функции программирования.
2. ОСНОВНЫЕ ХАРАКТЕРИСТИКИ УПАКОВОЧНОГО ОБОРУДОВАНИЯ
Работа технологического оборудования характеризуется рабочими циклами – интервалами времени между одноименными срабатываниями его основных исполнительных механизмов при бесперебойной работе машины. Рабочий цикл оборудования складывается из длительности рабочих и холостых ходов.
Рабочим ходом называют такое перемещение исполнительного механизма машины, при котором производится непосредственное технологическое воздействий на объект обработки.
К холостым ходам относятся все вспомогательные движения, которые служат для подготовки условий, необходимых для выполнения рабочего хода. Это перемещения исполнительных механизмов без воздействия на объект обработки, например, такие как возвращение исполнительного механизма в исходное положение, зажим или фиксация изделия, транспортирование и расфиксация изделия после выполнения рабочего хода и другие.
Работа технологического оборудования характеризуется периодическим повторением в заданной последовательности всех необходимых рабочих и холостых ходов, то есть периодическим повторением рабочего цикла. Время
10