
[SHipinsky_V.G.]_Oborudovanie_i_osnastka_upakovoch1(z-lib.org)
.pdfс рулона лента 4 охватывает последовательно натяжные 3 и располагающиеся над ними опорные ролики 5, образуя несколько компенсационных петель. Такие многопетлевые механизмы в сравнении с однопетлевыми при тех же габаритных размерах и небольшой амплитуде качания рычага 2 обеспечивают накопление большего запаса разматывающейся с рулона ленты 4, а также более мягкую амортизацию ее натяжения в процессе шаговой подачи. Имеются и другие конструктивные исполнения многопетлевых механизмов, например, с несколькими поступательно движущимися роликами или с несколькими качающимися рычагами. Применяются такие механизмы преимущественно в технологическом оборудовании, обеспечивающем высокоскоростную подачу разматываемой с рулона ленты с большими шагами.
Механизмы амортизации и натяжения наряду с основными функциями часто выполняют еще и дополнительные. Например, их качающийся рычаг, несущий натяжной ролик, связывают при необходимости с датчиками, контролирующими величину провисания компенсационной петли (рис.7.3а) или управляющими частотой вращения электродвигателя (рис.7.3д) в приводных механизмах вращения рулонов. Иногда он одновременно является и функциональным элементом в механизмах торможения разматываемого рулона. Так как при обрыве ленты, натяжные ролики обычно перемещаются в крайнее нижнее положение, то там они могут воздействовать на датчики, сигнализирующие об обрыве или окончании непрерывно подаваемой ленты и так далее.
7.7. Механизмы торможения разматываемого рулона
Механизмы торможения обеспечивают гашение сил инерции вращающегося рулона и его быструю остановку при прекращении подачи разматываемой ленты. По способу создания тормозного момента их условно можно разделить на следующие виды:
механизмы с независимым тормозным моментом;
механизмы, тормозной момент которых взаимосвязан с размером рулона (его наружным диаметром);
механизмы, тормозной момент которых взаимосвязан с натяжением разматываемой ленты.
Тормозной момент в этих механизмах обычно создается на цилиндрической или боковой поверхности специального тормозного диска, либо непосредственно на цилиндрической поверхности разматываемого рулона. При этом на некотором плече относительно оси вращения рулона возникает сила трения-скольжения в результате прижима специальным приводом, грузом, пружиной или другой упругой деталью тормозящего элемента к тормозному диску или непосредственно к разматываемому рулону.
Механизмы с независимым тормозным моментом характеризуются тем, что на их тормозном диске тормозящим элементом создается постоянный тормозной момент, не зависящий от параметров разматываемого рулона. Такие механизмы, в частности, содержат закрепленный на валу 1 (рис.7.8а) вращаемого рулона 2 тормозной диск 3 с конической боковой поверхностью которого сопрягается конусная тормозящая колодка 4, установленная на неподвижной оси 5 и поджимаемая к диску 3 через пружину 6 гайкой 7. В
111
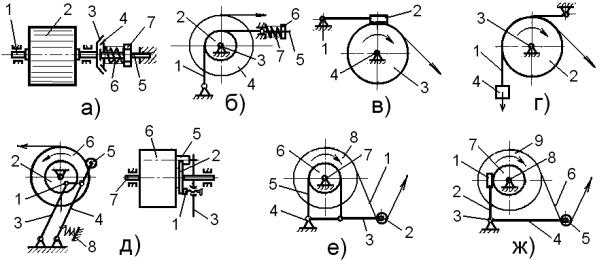
процессе размотки рулона 2 трением вращающегося диска 3 по сопрягающейся конической поверхности неподвижной колодки 4 создается постоянный тормозной момент, величина которого устанавливается вручную путем соответствующего сжатия пружины 6 перемещаемой по оси гайкой 7.
Рис.7.8. Конструктивные исполнения механизмов торможения рулона
В другом конструктивном исполнении такого механизма тормозящая лента 1 (рис.7.8б) постоянно прижимается к цилиндрической поверхности тормозного диска 2, закрепленного на валу 3 и вращающегося вместе с рулоном 4. При этом требуемый тормозной момент устанавливается вручную путем натяжения ленты 1 через соединенную с ней тягу 5, которая в свою очередь регулировочной гайкой 6 опирается на адекватно сжатую пружину 7.
Существенный недостаток таких механизмов заключается в том, что в процессе работы их тормозной момент остается неизменным, поэтому с уменьшением в несколько раз диаметра разматываемого рулона пропорционально будет возрастать усилие, требующееся для продвижения разматываемой ленты. А это отрицательно сказывается на работе других взаимосвязанных механизмов, например, снижает точность работы механизмов подачи ленты.
Этот недостаток отсутствует в механизмах, тормозной момент которых взаимосвязан с размером разматываемого рулона (его наружным диаметром). В частности, в одном из таких механизмов, тормозящая колодка 1 (рис.7.8д), взаимодействующая с боковой поверхностью тормозного диска 2, располагается на рычаге 3 шарнирного параллелограмма. При этом на конце второго рычага 4 этого параллелограмма установлен ролик 5, катящийся по цилиндрической наружной поверхности рулона 6, вращающегося вместе с тормозным диском на валу 7. В процессе работы ролик 5, взаимодействуя с цилиндрической поверхностью разматываемого рулона 6, отслеживает его уменьшающийся диаметр и через шарнирный параллелограмм, поджимаемый пружиной 8, изменяет плечо контакта тормозящей колодки 1 с вращающимся диском 2, адекватно уменьшая тормозной момент и обеспечивая тем самым постоянное усилие натяжения подаваемой ленты. Применяются такие тормозные механизмы обычно в устройствах, обеспечивающих равномерное разматывание рулонов правильной цилиндрической формы.
Постоянное усилие натяжения разматываемой ленты обеспечивает также механизм торможения, у которого закрепленная в шарнире 1 (рис.7.8в)
112
тормозящая колодка 2 непосредственно взаимодействует с наружной цилиндрической поверхностью разматываемого рулона 3, вращающегося на валу 4. Такой же эффект достигается и от взаимодействия тормозящей ленты 1 (рис.7.8г) с наружной поверхностью рулона 2 вращающегося на валу 3. При этом действующее усилие торможения определяется весом груза 4, подвешенного на ленте 1. В данных механизмах тормозящие элементы создают постоянную силу трения на постепенно уменьшающемся плече (радиусе) разматываемого рулона, обеспечивая тем самым пропорциональное уменьшение действующего тормозного момента и соответственно стабильное усилие натяжения подаваемой ленты, не зависящее от диаметра рулона. Недостатки таких механизмов заключаются в том, что их тормозящая колодка или лента непосредственно контактирует с разматываемым рулонным материалом, что отражается на его состоянии и не всегда допустимо. Эти механизмы не обеспечивают также экстренного торможения разматываемого рулона, например, в случаях обрыва ленты и блокирования ее подачи при отсутствии упаковываемого изделия, так как создаваемый тормозной момент у них не зависит от изменяющегося усилия натяжения продвигаемой ленты.
Механизмы, тормозной момент которых взаимосвязан с натяжением разматываемой ленты, обычно содержат компенсационную петлю 1 (рис.7.8е) в вершине которой располагается свободно вращающийся ролик 2. Ось же этого ролика в свою очередь крепится на конце рычага 3 качающегося в шарнирной опоре 4 и подвешенного на тормозящей ленте 5, взаимодействующей с цилиндрической поверхностью тормозного диска 6, закрепленного на валу 7 и вращающегося вместе с разматываемым рулоном 8. При увеличении усилия натяжения разматываемой ленты, например в процессе ее шаговой подачи, компенсационная петля 1 будет уменьшаться, приподнимая ролик 2 вместе с качающимся рычагом 3. В результате этого пропорционально уменьшится вплоть до нуля сила натяжения тормозящей ленты 5 и обусловленный ее трением по диску 6 тормозной момент, обеспечивая тем самым свободное вращение рулона 8. При резкой же остановке продвижения ленты компенсационная петля 1 начнет увеличиваться за счет инерционного вращения рулона 8, при этом качающийся рычаг 3 вместе с роликом 2 опускается вниз, увеличивая тем самым усилие прижатия ленты 5 к вращающемуся диску 6 до тех пор, пока возрастающий тормозной момент не обеспечит быструю остановку рулона 8. Аналогично производится и экстренная остановка рулона 8 при обрыве продвигаемой ленты, причем максимальный тормозной момент будет обеспечиваться нагружающим ленту 5 весом качающегося рычага 4 с роликом 2 и, при необходимости, дополнительно закрепленной на рычаге гирей. Переменный тормозной момент в таких механизмах может также создаваться тормозящей колодкой 1 (рис.7.8ж), которая закреплена на втором плече 2, качающегося в шарнирной опоре 3 рычага 4. При этом свободно вращающийся ролик 5, установленный на конце рычага 4, располагается в вершине компенсационной петли 6, образованной из разматываемой ленты, а колодка 1 взаимодействует с цилиндрической поверхностью тормозного диска 7, закрепленного на валу 8 и вращающегося вместе с разматываемым рулоном 9. Работает данный тормозной механизм так же, как и предыдущий.
113
Тормозной момент, создаваемый в этих механизмах, изменяется в прямой зависимости от действующего усилия натяжения продвигаемой ленты, поэтому тормозящий элемент (лента, колодка) при определенном подъеме рычага отводится от тормозного диска, обеспечивая тем самым свободное вращение разматываемого рулона. При обратном опускании рычага тормозящий элемент может ударять в момент контакта по тормозному диску, ускоряя этим их износ. Если же тормозящие элементы в этих механизмах соединять с рычагом через пружину или другие упругие детали, то при любом подъеме рычага они не будут терять контакта с тормозным диском, обеспечивая тем самым безударное приложение тормозящего усилия и более мягкую стабилизацию натяжения ленты. Несомненным достоинством приведенных механизмов является то, что при простом конструктивном исполнении они выполняют одновременно несколько функций, обеспечивая торможение разматываемого рулона, натяжение ленты и амортизацию усилия ее продвижения.
Момент МТМ, который должен создавать тормозной механизм для остановки разматываемого рулона, может быть рассчитан по формуле (7.5), при этом момент инерции МИ останавливаемого рулона определяется по формуле (7.4), в которой вместо угла αР ускорения (разгона) рулона принимается угол αТ остановки (торможения) рулона. По вычисленному значению тормозного момента МТМ затем выбирается или проектируется требуемый тормозной механизм.
Кроме приведенных имеются и другие конструктивные исполнения механизмов торможения рулона.
7.8. Механизмы остановки ленты
Механизмы остановки ленты обеспечивают гашение сил инерции продвигаемой ленты, а также ее быструю остановку и точную фиксацию при прекращении движения. По способу действия их условно можно разделить на неприводные, постоянно взаимодействующие с продвигаемой лентой, и приводные, в которых для остановки ленты тормозящее-фиксирующее усилие создается специальным приводом. Эти механизмы могут контактировать с продвигаемой лентой по плоской поверхности, прямой, кривой и ломаной линии, а также вакуумными, самозаклинивающимися и другими тормозящеефиксирующими конструктивными элементами.
В частности, приводные механизмы обычно обеспечивают остановку и фиксацию ленты 1 (рис.7.9а), продвигаемой по направляющей поверхности 2, прижимаемой к ней приводной тормозной колодкой 3, имеющей плоскую или криволинейную (рис.7.9б) контактирующую поверхность. При этом плоской колодкой требуемое усилие торможения создается при малом удельном давлении на поверхность ленты. Колодки же с криволинейной поверхностью контактируют с лентой по линии или узкой поперечной площадке, создавая высокое удельное давление, поэтому их обычно используют для остановки достаточно прочных лент, к которым не предъявляются высокие требования по качеству отделки поверхности, так как на ней в результате взаимодействия с колодкой могут оставаться вмятины.
Неприводными являются, например, перегибающие механизмы, парные тормозные колодки 1 и 2 (рис.7.9в) которых выполняются с профилем в виде
114

ломаной линии, постоянно взаимодействующим с лентой 3 и заставляющим ее многократно упруго изгибаться в образованном лабиринте. При этом величина останавливающего тормозного усилия будет определяться жесткостью ленты, коэффициентом трения между контактирующими поверхностями, а также величиной и количеством перегибов. Требуемое же тормозное усилие устанавливается обычно путем изменения зазора между колодками механизма и соответственно величины упругого перегиба продвигаемой через него ленты.
Рис.7.9. Конструктивные исполнения механизмов остановки ленты
Тормозное усилие может также создаваться вакуумными механизмами, в которых контактирующая с лентой 1 (рис.7.9г) плоская или криволинейная поверхность полой тормозной колодки 2, соединенной с вакуумным насосом, перфорирована мелкими отверстиями 3. Величина создаваемого тормозного усилия будет определяться в этом случае площадью контакта сопрягающихся поверхностей, а так же разностью между атмосферным давлением воздуха и
давлением внутри колодки, создаваемым вакуумным насосом. |
|
|
||
Неприводными |
самоуправляемыми |
являются, |
в |
частности, |
заклинивающие механизмы, которые обеспечивают требуемое натяжение ленты в период шаговой подачи, а также ее фиксацию от самопроизвольного обратного смещения при остановке. Состоят они из стопора 1 подвешенного одним концом на шарнире 2, а вторым торцом опирающегося через продвигаемую ленту 3 на направляющую поверхность 4 так, чтобы образуемый ими угол со стороны размотки ленты был несколько меньше 90о. В период шаговой подачи лента 3 свободно продвигается под стопором 1 (показано стрелкой), прижимающим ее своим весом к направляющей 4 и создающим за счет трения требуемое натяжение. Если же лента после завершения подачи попытается сместиться в обратном направлении под воздействием, например, механизма амортизации и натяжения ленты, то стопор заклинится и зафиксирует ее в заданном положении. При этом фиксирующее усилие стопора, удерживающего ленту от смещения, будет изменяться пропорциональным усилию противонатяжения ленты вплоть до момента ее разрыва.
В механизмах остановки, так же как и в механизмах подачи ленты, исполнительными органами создаются тормозные или тяговые усилия, направленные по касательной к их контактным поверхностям и обеспечивающие растяжение ленты. Эти усилия создаются за счет трения ленты о контактирующие поверхности исполнительных органов этих механизмов, сжимающих их с определенным усилием. Поэтому к механизмам остановки ленты можно отнести все, что ранее было сказано о соответствующих способах силового взаимодействия в механизмах подачи ленты. Если же на каком-то участке необходимо обеспечить только определенное постоянное натяжение продвигаемой ленты, то для этого также используются рассмотренные механизмы остановки ленты, но работающие в бесприводном
115
режиме. При этом тормозные колодки 3 (рис.7.9а – б) прижимаются к ленте с адекватным постоянным усилием, в полости тормозной колодки 2 (рис.7.9г) создается постоянный вакуум, а парные тормозные колодки 1 и 2 (рис.7.9в) перегибающего механизма устанавливаются с требуемым зазором при неизменной жесткой взаимной фиксации.
7.9. Механизмы направления ленты
Направляющие механизмы, служат для сохранения или изменения направления движения подаваемой ленты. По целевому назначению они подразделяются на механизмы, обеспечивающие прямолинейное движение, изменяющие направление движения и ограничивающие поперечное смещение продвигаемой ленты. Эти механизмы выполняются как с неподвижными, так и с движущимися конструктивными элементами, которые способствуют продвижению ленты и одновременно ограничивают ее смещение. При этом контакт ленты с направляющими элементами может осуществляться по всей их поверхности (сплошные направляющие), а также по отдельным поддерживающим линиям или участкам и обеспечивается весом ленты, ее натяжением или с помощью второй дополнительной направляющей.
В частности, сплошные прямолинейные направляющие 1 (рис.7.10а)
применяются для лент 2, продвигаемых без натяжения. Гарантированное же натяжение ленты само по себе обеспечивает ее прямолинейное продвижение на данном участке и без применения направляющей. Для предотвращения же чрезмерного провисания движущихся с натяжением массивных лент 1 (рис.7.10б) на больших прямолинейных участках устанавливаются с определенным шагом поперечные поддерживающие стержни или свободно вращающиеся ролики 2. Если же нежесткую ленту необходимо без натяжения продвигать, например, за толкающими механизмами подачи, то на таком участке можно установить прямолинейную желобообразную направляющую 1 (рис.7.10в), в которой с помощью профилирующего ролика 2 лента 3 в поперечном сечении упруго прогибается в дугообразную форму. В результате этого ее жесткость повышается в несколько раз по сравнению с плоской формой и тем самым обеспечивается надежное продвижение ленты по такой направляющей с высокой скоростью на значительные расстояния. Надежное прямолинейное продвижение ленты 1 (рис.7.10г) может обеспечить и пара приводных подающих валков 2, сопрягающиеся профильные рабочие поверхности которых упруго деформируют в поперечном сечении подаваемую ленту в волнообразную форму, делая тем самым ее консольный участок более жестким.
Для изменения направления движения ленты 1, находящейся под натяжением, применяют неподвижные криволинейные направляющие 2 (рис.7.10д) или свободно вращающиеся ролики 2 (рис.7.10е), а также сопрягающиеся пары принудительно вращающихся роликов 2 и 3 (рис.7.10ж). В последнем случае трение о приводные ролики способствует и продвижению ленты. Направление движения ненатянутой ленты 1 (рис.7.10з) изменяют в механизмах, содержащих основную неподвижную направляющую 2 и эквидистантную ей дополнительную направляющую 3 или пару сопрягающихся роликов (рис.7.10ж).
116

Рис.7.10. Конструктивные исполнения механизмов направления ленты
Механизмы, ограничивающие поперечное смещение продвигаемой ленты применяются, как правило, совместно с механизмами направления ленты. На неподвижных направляющих 1 (рис.7.10и) они выполняются в виде сплошных вертикальных буртиков 2, располагающихся по торцам продвигаемой ленты 3, а также в виде ограничительных бобышек 2 (рис.7.10к) или планок 2 (рис.7.10л), установленных вдоль направляющей 1 с определенным шагом. На подвижных направляющих эту функцию выполняют, например, диски 1 (рис.7.10м), закрепляемые по торцам продвигаемой ленты 2 на вращающихся роликах 3, обеспечивающих изменение направления ее движения.
7.10. Дополнительные механизмы
Дополнительные механизмы в устройствах подачи рулонных материалов выполняют как цикловые контрольные, блокирующие и регулирующие функции, так и различные внецикловые функции.
К дополнительным механизмам относятся, например, датчики контроля рулона и подаваемой ленты. В частности, датчики контроля рулона блокируют включение технологической машины в работу без установленного рулона, а также автоматически останавливают ее при расходовании всей находящейся в рулоне ленты. Такие контактные датчики обычно содержат закрепленный в шарнире 1 (рис.7.11а) рычаг 2 на втором конце которого располагается свободно вращающийся ролик 3, опирающийся на цилиндрическую поверхность разматываемого рулона 4. При расходовании в процессе работы всей находящейся в рулоне ленты рычаг 2 перемещается в нижнее конечное положение и, воздействуя на кнопку выключателя 5, отключает питание привода машины. То же самое происходит и при неустановленном рулоне. Бесконтактные же оптические датчики состоят из излучателя 1 (рис.7.11б) и фотодиода 2, расположенных на одной линии с двух сторон разматываемого рулона 3 и соединенных с электронным управляющим модулем. При окончании разматываемого рулона или его отсутствии из излучателя 1 световой луч попадает на фотодиод 2 и тот через управляющий
117

модуль останавливает технологическую машину, а также подает сигнал о необходимости установки нового рулона.
Рис.7.11. Конструктивные исполнения датчиков контроля рулона и подаваемой ленты
Датчики контроля ленты останавливают работу технологического автомата при прекращении поступления ленты в рабочую зону, а также при ее разрыве, смятии или выявлении других контролируемых дефектов. При этом датчиком на соответствующем участке контролируется, как наличие самой ленты, так и величина ее натяжения. Чаще всего такой датчик содержит закрепленный над лентой 1 (рис.7.11в) в шарнире 2 рычаг 3, взаимодействующий с кнопкой выключателя 4. При продвижении разматываемой с рулона ленты 1 с заданным натяжением отклоненный рычаг 3 скользит своим нижним концом по ее поверхности, не касаясь при этом кнопки выключателя 4. При окончании ленты, ее обрыве или отсутствии натяжения рычаг 3 теряет опору и поворачивается на шарнире 2 в вертикальное положение, надавливая при этом на кнопку выключателя 4, останавливающего работу автомата. В другом конструктивном исполнении такой датчик состоит из опирающегося на натянутую ленту 1 (рис.7.11г) ролика 2, поджимаемого пружиной 3. При потере опоры этот ролик перемещается вниз и надавливает на кнопку замыкающую контакты в выключателе 4, установленном под ним в окне направляющей 5. Для контроля лент, обладающих диэлектрическими свойствами, скользящий по ней щуп и направляющая могут включаться в электрическую схему управления автоматом. При отсутствии между ними продвигаемой ленты щуп соединяется с направляющей, замыкая при этом электрическую цепь, обеспечивающую приостановку работы автомата.
Дополнительные механизмы, которые блокируют подачу ленты, при отсутствии упаковываемого изделия работают как с цикловыми, так и внецикловыми устройствами загрузки изделий в технологические автоматы. Основным их исполнительным элементом обычно является щуп, взаимодействующий с загружаемыми изделиями. При отсутствии на контролируемой позиции поданного изделия такой щуп перемещается на большую величину, чем при его наличии и от этого блокируется срабатывание механизма подачи ленты.
К дополнительным относятся также фотоцентрирующие механизмы, обеспечивающие корректировку шага подачи ленты по нанесенному на нее рисунку или знакам. Осуществляется это с помощью фотоэлектронных датчиков, которые контролируют положение специальных меток на ленте в цикловой связи с работой механизма ее разрезания на отдельные заготовки. При несоответствии положения меток опорным сигналам, поступающим от
118
механизма разрезания, фотоэлектронный датчик обеспечивает адекватную корректировку шага подачи ленты.
Дополнительные внецикловые механизмы заправки ленты включаются в работу только при установке нового рулона или разрывах продвигаемой ленты и, как правило, выполняют свои функции в режиме безостановочной работы технологического автомата.
В устройствах для подачи рулонных материалов используются также разнообразные дополнительные механизмы, выполняющие определенные узкоспециализированные действия. К таковым, например, относятся механизмы, формирующие комплекты из двух и более заготовок, отрезаемых с различной длиной от лент, разматываемых с нескольких рулонов. Применяются они в автоматах, упаковывающих конфеты в комбинированную обертку, включающую этикетку с подверткой или этикетку, фольгу и подвертку.
8. УСТРОЙСТВА ДЛЯ СВАРКИ ПЛАСТМАСС
Изготовление всего многообразия пластмассовой упаковки неразрывно связано с нагревом и сваркой полимерных материалов в соответствующем технологическом оборудовании.
Сварка пластмасс – это способ получения неразъемного соединения в результате диффузии частей молекулярных цепей через границу раздела из одного объема материала в другой (диффузионная сварка), или вследствие их химического взаимодействия (химическая сварка). В сварных соединениях полностью (или почти полностью) исчезает граница раздела между контактирующими поверхностями, а по прочности и физическим свойствам соединительный шов приближается, а иногда и остается равным свойствам свариваемого материала. Образование же качественного сварного шва происходит в области вязкого течения полимера, когда при малом давлении достигается хороший контакт свариваемых поверхностей и высокая прочность соединения. При этом интенсивность диффузии молекулярных цепей через свариваемые поверхности определяется силами межмолекулярного взаимодействия, совместимостью соединяемых полимеров и условиями, при которых осуществляется сварка. В частности, температура сварки должна быть выше температуры плавления (Тпл) для кристаллических полимеров или температуры текучести (Тт) для аморфных полимеров, но ниже температур их деструкции. При кратковременном нагреве продолжительностью 0,05 – 0,2с температура сварки может даже несколько превышать температуру деструкции.
Вторым определяющим фактором процесса сварки является контактное давление, которым обеспечивается сближение соединяемых поверхностей на расстояние возникновения межмолекулярного взаимодействия. Оно существенно влияет на прочность сварных швов, особенно при пониженных температурах и кратковременном нагреве. Величина контактного давления зависит от вязкости расплава полимера и температуры его размягчения. Чем выше вязкость расплава, тем большее должно быть удельное давление прижима. Сваркой также можно соединять и многие разнородные совместимые термопластичные материалы, то есть такие, которые способны образовывать устойчивые твердые растворы. При этом по вязкости расплавов соединяемые
119
поверхности должны быть достаточно близкими. Материалы с различной вязкостью расплавов не могут образовывать прочного соединения: более вязкий материал не диффундирует в менее вязкий, а выдавливает его из сварного шва. Поэтому при сварке большое внимание должно уделяться и равномерности разогрева соединяемых поверхностей.
Диффузионной сваркой можно соединять составные части пластмассовых изделий и без нагрева материала в зоне шва выше температуры текучести, но при условии введения между контактирующими поверхностями органических растворителей. При этом молекулы растворителя диффундируют в межмолекулярные пустоты, непрерывно образующиеся в поверхностных слоях вследствие гибкости макромолекул материала. Заполнив все пустоты, молекулы растворителя начинают давить на макромолекулы полимера, уменьшая тем самым их межмолекулярное сцепление. Эту стадию процесса растворения называют набуханием или пластифицированием. После ее завершения протекает вторая стадия процесса – взаимная диффузия частей молекулярных цепей через границу раздела и образование сварного шва. Процесс же пластифицирования позволяет таким образом снижать температуру текучести полимера, а также усиливать подвижность его молекул в вязкотекучем состоянии, обеспечивая тем самым улучшение свариваемости материалов, повышение прочности и однородности сварного шва. Если же полимеры обладают малой скоростью диффузии даже в интервале вязкотекучего состояния (материалы с большим молекулярным весом или высокой полярностью), то их целесообразно сваривать присадочными материалами, в качестве которых можно использовать пластифицированные полимеры или полимеры с малым молекулярным весом, обладающие более высокой скоростью диффузии. Внутренние напряжения, возникающие в соединениях от диффузионной сварки, снимаются обычно термической обработкой. Она заключается в нагреве и выдержке сварной конструкции при температуре, близкой к температуре стеклования полимера, с последующим ее охлаждением.
Высококристаллические и хорошо ориентированные полимеры, наиболее рационально соединять путем сшивания их контактирующих поверхностей химическими связями. Такой способ образования соединительных швов называется химической сваркой. Применяется такая сварка и в тех случаях, когда нагревание полимеров до вязкотекучего состояния нежелательно из-за возможного нарушения их кристаллической структуры, потери ориентации и по другим причинам. Осуществляется химическая сварка путем нанесения на соединяемые поверхности веществ, которые интенсивно образуют химические связи с активными звеньями макромолекул поверхностного слоя свариваемых деталей. При этом температура в зоне сварки может быть ниже температуры плавления полимера, когда подвижность его макромолекул еще незначительна. Плотный же контакт между соединяемыми поверхностями обеспечивается приложением внешних сжимающих усилий. Такой сваркой, в частности, соединяют пластмассы на основе фенолоформальдегидных, кремнийорганических, эпоксидных и отверждающихся полиэфирных смол. Получаемые сварные швы по своей структуре и свойствам существенно не отличаются при этом от основного материала; в них отсутствуют значительные
120