
[SHipinsky_V.G.]_Oborudovanie_i_osnastka_upakovoch1(z-lib.org)
.pdfперемещаемыми изделиями 8, которые поступают в подъемник по нижнему желобу 9, а отводятся с него по верхнему гравитационному желобу 10.
Скорость движения ленты в таких подъемниках
Vл
2 Vи
, где Vи – линейная
скорость движения центра поднимаемого изделия 8.
Перемещать же ящики, коробки и другую аналогичную тару с упаковываемой продукцией позволяют транспортирующие системы, состоящие из двух параллельных ленточных конвейеров 1 (рис.5.7в), устанавливаемых обычно с вертикальным расположением транспортерных лент. При этом транспортируемые объекты 2 зажимаются между смежными синхронно движущимися ветвями этих лент и за счет усилия, обусловленного трением, перемещаются ими по опорной поверхности, обычно состоящей из параллельных свободно вращающихся роликов 3. Применяются такие транспортирующие системы, например, в технологических машинах, обеспечивающих автоматическое закрывание клапанов на заполненных картонных ящиках с одновременным их скреплением липкой укупорочной лентой.
Комбинированные транспортные системы, состоящие из пары параллельных синхронно вращающихся шнеков 1 (рис.5.7г), обеспечивают синхронное перемещение по опорной поверхности 2 разнообразных штучных изделий 3 с заданным шагом и ритмом, определяющимся угловой скоростью вращения их рабочих органов. В таких транспортерах вместо шнеков могут устанавливаться и парные стержневые рабочие органы винтовые рабочие канавки на цилиндрической поверхности, которых соответствуют сопрягающемуся профилю перемещаемых изделий.
Наряду с рассмотренными применяются и разнообразные другие комбинированные транспортирующие системы, например, сочетающие в себе функциональные элементы вибрационных и магнитных, пневматических и гравитационных транспортеров, а так же содержащие конвейеры, которые оснащаются или объединяются в единую систему дополнительными транспортирующими устройствами.
6. УСТРОЙСТВА ДЛЯ ИЗМЕНЕНИЯ НАПРАВЛЕНИЯ И ПЕРЕСТРОЙКИ ПОТОКОВ ИЗДЕЛИЙ
Применяются эти устройства для соединения между собой отдельных конвейеров (транспортеров) в комбинированные системы, а также для расширения функциональных возможностей транспортирующих систем. По выполняемым функциям они подразделяются на передающие, кантующие и поворачивающие изделия, изменяющие направление движения изделий, разделяющие поток и объединяющие несколько потоков изделий, группирующие изделия в ряды и другие.
В частности, перемещение изделий на конвейерах несколькими параллельными потоками с изменением направления движения обеспечивается обычно установкой над их транспортирующими элементами соответствующего комплекта неподвижных либо вибрирующих направляющих. Эти направляющие могут быть прямолинейными, криволинейными или
81
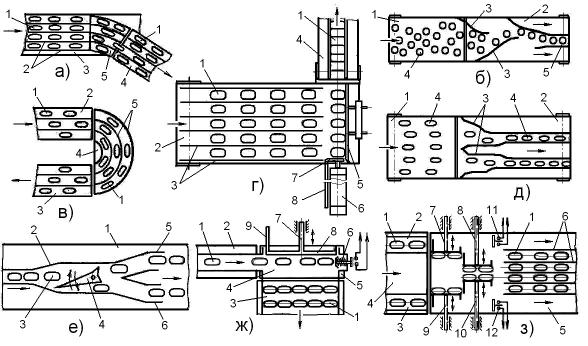
представлять собой комбинацию тех и других. Углы же изменения направления движения при этом способе небольшие и определяются величиной коэффициента трения между перемещаемыми изделиями и направляющими. Например, для передачи изделий 1, (рис. 6.1а) движущихся несколькими параллельными потоками между направляющими 2, с ленточного конвейера 3 на наклонный гравитационный лоток 4 применяется переходная вставка 5, содержащая сопрягающиеся с их каналами криволинейные направляющие. Иногда для поворота в плане потока перемещаемых изделий на угол более 90о используют вращающиеся диски (рис.6.1д-е). Для поворота же изделий 1 (рис.6.1в) на 180о и передачи их параллельных потоков с ленточного конвейера 2 на встречно движущийся конвейер 3 применяются полукруглые вибростолы 4 с концентричными дугообразными разделительными направляющими 5.
Рис.6.1. Конструктивные схемы устройств для изменения направления и перестройки потоков изделий
Часто изготовляемые изделия 1 (рис.6.1г), например шоколадные батончики перемещаются на ленточном конвейере 2 несколькими параллельными потоками по каналам, образованным направляющими 3. Передача же этих изделий одним потоком на перпендикулярно расположенный конвейер 4, перемещающий их к заверточному автомату, обеспечивается дополнительным транспортирующим устройством, состоящим из регулируемой направляющей планки 5 и пневмоцилиндра 6, на штоке которого закреплен толкатель 7 совмещенный с перпендикулярной фиксирующей планкой 8. При контакте ближайшего ряда движущихся на конвейере 2 изделий 1 с направляющей планкой 5 срабатывает располагающийся в ней датчик, включающий в работу пневмоцилиндр 6. При этом шток пневмоцилиндра выдвигается и закрепленным на нем толкателем 7 перемещает этот ряд изделий на движущуюся ленту конвейера 4, а каналы, образованные направляющими 3, в это время перекрываются его фиксирующей планкой 8. Достигнув конечного положения, шток пневмоцилиндра 6 возвращается в исходное положение и далее цикл повторяется. Перестройка же нескольких потоков изделий в один,
82
при их переходе с конвейера 1 (рис.6.1б) на движущийся в том же направлении конвейер 2 может производиться с помощью комплекта криволинейных направляющих 3. При этом на конвейере 2, имеющем большую скорость, шаг между поступающими изделиями 4 увеличивается и за счет последовательного взаимодействия с криволинейными направляющими 3 они перестраиваются в один поток, подаваемый затем по каналу 5, например, к заверточному автомату. Аналогичным образом при переходе с конвейера 1 (рис.6.1д) на движущийся в том же направлении конвейер 2 с помощью комплекта вибрирующих криволинейных направляющих 3 можно перестраивать многорядное расположение транспортируемых изделий 4 в два параллельных потока, подаваемых по каналам 5. При этом несимметричной криволинейной формой входной части направляющих 3 изделия 4 перестраиваются в два потока без торможения и заклинивания на входе.
Разделить движущиеся одним потоком на конвейере 1 (рис.6.1е) между направляющими 2 изделия 3 на два одинаковых потока позволяет, например, простейший механизм в виде свободно качающейся на оси переводной стрелки 4. В процессе движения очередное изделие 3 взаимодействует с боковой поверхностью стрелки 4 и при выходе в свой отводящий канал 5 поворачивает на оси ее заостренную часть в сторону этого канала. Соответственно следующее изделие заходит на противоположную грань стрелки и при выходе во второй отводящий канал 6 возвращает ее в исходное положение и т. д. Таким образом, движущиеся в одном потоке изделия 3, поочередно переводя стрелку 4, направляются ею в каналы 5 и 6, разделяясь при этом на два равнозначных потока.
Перестроить изделия 1 (рис.6.1ж) с однорядного потока на подающем конвейере 2 в многорядный поток на перпендикулярно расположенном отводящем конвейере 3 позволяет дополнительное перестраивающее устройство, содержащее на столе 4 направляющую планку 5 с контактным датчиком 6, а также линейный привод на штоке 7 которого закреплен толкатель 8, связанный с фиксирующей планкой 9. За счет создаваемого подающим конвейером 2 подпора поступающие изделия 1 продвигаются последовательной цепочкой по столу 4 этого устройства вдоль толкателя 8 до контакта с направляющей планкой 5 и датчиком 6. В момент взаимодействия изделия 1 с датчиком 6 его замыкающимися контактами включается линейный привод, который своим выдвигающемся штоком 7 с толкателем 8 перемещает находящийся на столе ряд изделий на отводящий конвейер 3. Канал же подающего конвейера в это время перекрывается связанной с толкателем фиксирующей планкой 9. Выполнив рабочий ход, толкатель 8 штоком 7 привода возвращается в исходное положение и цикл повторяется.
Если же, например, изделия 1 (рис.6.1з), движущиеся двухрядным потоком в каналах 2 и 3 подающего конвейера 4, необходимо перестроить в четырехрядный поток, движущийся на отводящем конвейере 5 между направляющими 6 в том же направлении, то для этого применяется и соответствующее перестраивающее устройство. Это устройство включает в себя пару толкателей 7 и 8, являющуюся продолжением внешней направляющей канала 2, и пару толкателей 9 и 10, являющуюся продолжением внешней направляющей канала 3, а также установленные за ними соосно
83

каналам 2 и 3 контактные датчики 11 и 12. В процессе работы изделия 1 переходят двумя потоками с каналов 2 и 3 подающего конвейера 4 на транспортирующую ленту отводящего конвейера 5 и движутся на ней до контакта со срабатывающими датчиками 11 и 12, которые останавливают конвейер 5 и включают привода толкателей 7, 8, 9 и 10. При этом толкателями 7
и9 расположенные перед ними изделия перемещаются на уровень внешних каналов, а толкателями 8 и 10 – на уровень внутренних каналов, образованных направляющими 6 на отводящем конвейере 5. Выходные же каналы 2 и 3 подающего конвейера в это время перекрываются связанными с толкателями 7
и9 фиксирующими планками. Выполнив рабочий ход, все толкатели возвращаются в исходное положение, а отводящий конвейер 5 приводится в движение. При этом передвинутые толкателями изделия входят в его соответствующие каналы, образованные направляющими 6 и далее цикл повторяется. За счет регулировки расстояния до датчиков 11 и 12, а так же установки необходимого количества толкателей такими устройствами можно перестраивать транспортируемые изделия на любое число потоков.
Несколько ориентированных потоков изделий из навала можно, в частности, создавать вибрационными многоканальными лотками или вибробункерными устройствами, с адекватным количеством винтовых рабочих дорожек на обечайке.
Втранспортирующих системах соответствующими дополнительными устройствами осуществляется также однослойное или многослойное группирование изделий, при их поштучной, однорядной или многорядной подаче на приемную позицию, обеспечивающую, например, при упаковывании групповую укладку изделий в тару.
Рис.6.2. Устройство для однослойного группирования изделий с укладкой в тару
В частности, при однорядной подаче изделий 1 (рис.6.2) транспортирующей системой, состоящей из двух параллельных ленточных конвейеров 2, группирование изделий в однослойный пакет 3 с его последующей укладкой в тару 4, подаваемую конвейером 5, обеспечивается устройством на столе 6 которого располагается приемный канал, состоящий из продольной 7 и поперечной 8 направляющих планок. При этом в планке 8 установлен контактный датчик 9, а боковой направляющей канала является упорная планка толкателя 10. Кроме этого на противоположной стороне стола 6 параллельно упорной планке толкателя 10 установлена продольная направляющая 11, содержащая контактные датчики 12 и переходящая с одной
84

стороны в подающий лоток 13, сопрягающийся с горловиной заполняемой тары 4, фиксируемой упором 14. Со второй же стороны этой направляющей располагается упорная планка толкателя 15, движущегося в пазу 16 стола 6.
В процессе работы изделия 1 подаются однорядным потоком с ленточных конвейеров 2 в приемный канал устройства и за счет создаваемого подпора продвигаются по нему вдоль продольной планки 7 до контакта с датчиком 9, который кратковременно останавливает подающие конвейеры 2 и включает привод толкателя 10. При этом ряд изделий, находящийся перед его опорной планкой продвигается толкателем 10 по столу 6 на заданный шаг вдоль поперечной направляющей планки 8 на место ближайшего ряда формируемого однослойного пакета 3. Затем толкатель 10 возвращается в исходное положение, перед ним в канале формируется следующий ряд изделий и по команде датчика 9 он перемещает их по столу на место предыдущего ряда, который при этом подаваемыми изделиями тоже продвигается на шаг вперед. Эти циклы повторяются до тех пор, пока при очередном срабатывании толкателя 10 первый ряд группируемых изделий не достигнет продольной направляющей 11 и установленных в ней контактных датчиков 12. При этом срабатывающими датчиками 12 включается привод толкателя 15, и он своей упорной планкой перемещает сгруппированный пакет изделий по лотку 13 в тару 4, фиксируемую упором 14. После этого толкатели 10 и 15, а также фиксирующий упор 14 возвращаются в исходное положение, а в это время конвейером 5 к лотку 13 подается следующая пустая тара 4, которая фиксируется перемещающимся к ней упором 14, и далее цикл повторяется.
Рис.6.3. Устройство для многослойного группирования изделий с укладкой в тару
Группирование многослойных пакетов 1 (рис.6.3) из изделий 2, подаваемых в один ряд конвейером 3 на приемный лоток 4, производится, например, с помощью элеваторного устройства 5, на бесконечном транспортирующем элементе которого с шагом равным толщине изделий закреплены полки 6, адекватные по ширине формируемому пакету 1. При этом за элеваторным устройством располагается конвейер 7, в шаговом режиме подающий к его загрузочному патрубку 8 тару 9 фиксируемую упором 10, а перед устройством 5 соосно патрубку 8 установлен толкатель 11, имеющий
85
прорези для полок 6. В процессе работы изделия 2 с конвейера 3 поступают однорядным потоком на приемный лоток 4 и за счет создаваемого подпора продвигаются по нему на сопрягающуюся полку 6 элеваторного устройства 5.
После заполнения эта полка по команде соответствующего датчика поднимается устройством 5 на шаг, далее поступающие изделия заполняют его следующую полку и эти циклы повторяются до тех пор, пока на смежных полках не сгруппируется заданное количество слоев, формируемого пакета 1. После этого включается в работу толкатель 11, который, проходя между полками 6, выталкивает сгруппированный пакет через патрубок 8 в тару 9, фиксируемую упором 10. Далее фиксирующий упор 10 и толкатель 11 возвращаются в исходное положение, а в это время конвейером 7 к патрубку 8 подается следующая пустая тара 9, которая возвращающимся упором 14 совмещается с патрубком 10 и фиксируется, а затем цикл повторяется.
Наряду с рассмотренными устройствами применяются и многие другие схемы построения группирующих устройств, которые обеспечивают как формирование пакетов из разнообразных штучных изделий с их укладкой в тару, так и группирование из транспортных единиц (в ящиках, мешках и т. д.) однослойных и многослойных транспортных пакетов, например, на поддонах или скрепляемых другими средствами пакетирования (стропами, стяжками, обвязками).
7. УСТРОЙСТВА ДЛЯ ПОДАЧИ РУЛОННЫХ МАТЕРИАЛОВ
Многие исходные упаковочные материалы (бумага, картон, жесть, фольга, пленки) устанавливаются в технологические автоматы упаковочного производства в виде сложенных в стопу листовых заготовок или смотанной в рулон ленты. Устройства же, обеспечивающие подачу этих материалов в автоматах соответственно подразделяются на флатовые и рулонные.
Во флатовых подающих устройствах упаковочный материал находится в виде стопы заранее нарезанных плоских заготовок, подаваемых ими в питаемый автомат поштучно. Выполняются обычно эти устройства на базе рассмотренных ранее кассетных шиберных (рис.5.23; рис.5.24) или шахтных (рис.5.25) питателей. Производительность таких подающих устройств не превышает 150 циклов в минуту, так как они, как правило, содержат исполнительные механизмы возвратно-поступательного действия.
Рулонные подающие устройства в процессе работы питаемых автоматов производят размотку ленты с установленных в них рулонов, ее пошаговую или непрерывную подачу, разрезку на отдельные заготовки, подачу заготовок в исполнительные механизмы автомата и другие действия. Состоят они, как правило, из сбалансированных взаимосвязанных ротационных механизмов и поэтому с точки зрения повышения производительности предпочтительнее флатовых. По важности выполняемых действий входящие в эти устройства механизмы условно подразделяются на основные, вспомогательные и дополнительные (рис.7.1).
Основные механизмы имеются во всех подающих устройствах. Они обеспечивают подачу ленты из рулона и ее разделение на заготовки. К ним относятся:
86
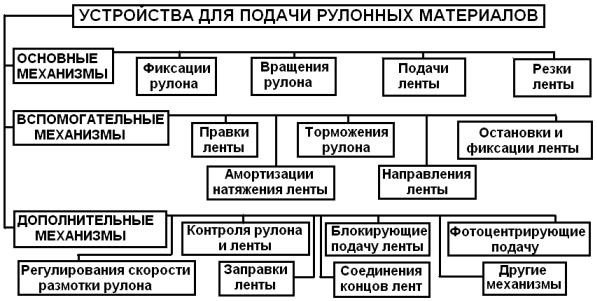
механизмы фиксации, обеспечивающие закрепление рулонов в машине;
механизмы вращения рулонов, обеспечивающие размотку с них ленты;
механизмы подачи (продвижения) ленты, обеспечивающие пошаговую или непрерывную подачу ленты к исполнительным механизмам машины;
режущие механизмы, обеспечивающие разделение ленты на отдельные заготовки.
Рис.7.1. Обобщенная структурная схема устройств подачи рулонных материалов
Вспомогательные механизмы обеспечивают работу основных механизмов подающих устройств в зависимости от назначения машины, вида рулонного материала, характера и скорости подачи (продвижения) ленты. К ним относятся:
механизмы правки, устраняющие кривизну в разматываемой с рулона ленте для получения с нее плоских штучных заготовок;
механизмы амортизации, обеспечивающие при подаче уменьшение усилия натяжения ленты за счет ее накопления между рулоном и подающим механизмом;
механизмы торможения рулона, уменьшающие инерционное вращение разматываемого рулона;
механизмы остановки ленты, гасящие инерцию и фиксирующие ее при остановке движения;
направляющие механизмы, служащие для сохранения или изменения направления движения подаваемой ленты.
Дополнительные механизмы в устройствах подачи рулонных материалов выполняют контрольные, блокирующие, регулирующие и различные внецикловые функции. К ним, в частности, относятся:
датчики контроля наличия рулона и целостности подаваемой ленты;
механизмы, блокирующие подачу ленты, при отсутствии на исполнительной позиции машины, например, упаковываемого изделия;
фотоцентрирующие датчики, корректирующие шаг подачи ленты по нанесенному на нее рисунку или знакам;
87

механизмы регулирования скорости размотки рулона по скорости подачи (продвижения) ленты;
механизмы автоматической заправки ленты при ее обрыве или установке нового рулона;
механизмы, соединяющие концы лент заканчивающегося и нового рулона и другие.
Все основные и вспомогательные механизмы при работе в устройствах подачи рулонных материалов непосредственно воздействуют на ленту или рулон. Из дополнительных механизмов первые четыре выполняют контрольные функции, взаимодействуя с основными и вспомогательными механизмами. Остальные дополнительные механизмы непосредственно воздействуют на ленту, но при этом выполняют не технологические, а внецикловые функции, связанные с ее заправкой при смене рулонов. Далее рассмотрим наиболее распространенные конструктивные исполнения названных механизмов, применяемых в устройствах подачи рулонных материалов.
7.1.Механизмы фиксации рулонов
Воборудовании упаковочного производства обычно применяются механизмы фиксации, обеспечивающие крепление рулонов за их горизонтально расположенное осевое отверстие. В зависимости от размеров и массы устанавливаемых рулонов эти механизмы выполняются одноопорными (консольными) или двухопорными, то есть с размещением опор по обе стороны рулона. Двухстороннее размещение опор обеспечивает большую жесткость конструкции и предпочтительнее при фиксации тяжелых и широких рулонов. По особенностям конструктивного исполнения они также подразделяются на
механизмы фиксации без съемных деталей и механизмы фиксации со съемными деталями. Механизмы без съемных деталей более удобны в эксплуатации и позволяют быстрее устанавливать рулон, чем механизмы со съемными деталями. Механизмы фиксации, не содержащие съемных деталей, всегда выполняются с размещением опорных кронштейнов 1 и 2 (рис. 7.2а) по обе стороны фиксируемого рулона 3.
Рис.7.2. Конструктивные исполнения механизмов фиксации рулонов
При этом рулон удерживается на вдавливаемых с двух сторон в его осевое отверстие конусных втулках 4, одна из которых свободно вращается на
88
закрепленной в кронштейне 1 полуоси 5, а вторая – на полуоси 6, поступательно перемещаемой в резьбовом отверстии кронштейна 2 при ее вращении рукояткой 7. Стопорится же полуось 6 от самоотвинчивания из рабочего положения с помощью контргайки 8. Такое фиксирование рулонов двумя конусными втулками, вдавливаемыми в их осевое отверстие, широко применяется и во всех других механизмах.
Механизмы фиксации со съемными деталями выполняются как с двусторонним, так и с односторонним (консольным) размещением опор. В частности, консольные механизмы фиксации содержат ось 1 (рис. 7.2б), которая одним концом закрепляется в опорном кронштейне 2 станины машины. На этой оси размещается свободно вращающаяся на подшипниках труба 3, содержащая неподвижную 4 и съемную 5 конусные втулки. При установке рулона конусная втулка 5 снимается с трубы 3 и после этого на нее осевым отверстием насаживается рулон 6. Затем на трубу обратно устанавливается конусная втулка 5 и от поджимающего усилия руки рулон 6 фиксируется между нею и неподвижной втулкой 4, входящими в его осевое отверстие. После этого съемная втулка 5 стопорится вворачиваемым в ее радиальное отверстие винтом 7. Стопорение на трубе 1 (рис.7.2в) съемных конусных втулок 2 обеспечивается и другими конструктивными элементами. Таковым, например, является установленный в пазу конусной втулки 2 на оси 3 самозаклинивающийся рычаг 4, который поджимается пружиной 5. Для снятия втулки этот рычаг отводят от трубы 1 нажатием на его выступающую часть пальцем руки. А после установки и фиксации этой втулкой рулона она самостопорится, за счет пружины 5, постоянно поджимающей к трубе нижнюю заклинивающую часть рычага 4. Быстрое и надежное стопорение на трубе 1 (рис.7.2г) съемной конусной втулки 2 обеспечивается также установленным в ней фиксатором 3, который пружиной 4 постоянно вдавливается в один из кольцевых пазов, выполненных на сопрягающейся поверхности этой трубы в зоне стопорения втулки. При снятии такой конусной втулки 2 с трубы 1 ее фиксатор 3 приподнимается вверх за выступающую головку 5. Иногда в таких консольных механизмах узкие рулоны с одной стороны фиксируют по плоской боковой поверхности, а со второй стороны в их осевое отверстие вдавливается съемная конусная втулка.
Для установки тяжелых и широких рулонов применяются механизмы фиксации со съемной осью и двусторонним размещением опор. Съемная ось 1 (рис.7.2д) такого механизма вставляется в пазы опорных кронштейнов 2 и 3 станины машины закрепленными на ее концах опорными втулками 4 и 5, неподвижно фиксирующими ось. На оси 1 между опорными втулками размещается труба 6, свободно вращающаяся на подшипниках и несущая конусные втулки 7 и 8, которыми фиксируется рулон 9. При этом с втулкой 8 ее подвижный конус 10 соединяется резьбою, а стопорятся эти втулки имеющимися разрезанным кольцевым зажимами, которые затягиваются на трубе 6 винтами 11. При установке рулона 9 ось 1 снимается с опорных кронштейнов 2 и 3, а затем отпусканием винта 11 расслабляется кольцевой зажим конусной втулки 8 и она снимается с трубы 6. Далее свободным концом ось вместе с трубою вставляется в отверстие рулона до контакта его с конусной втулкой 7. Затем на трубу 6 обратно устанавливается конусная втулка 8,
89
которая после частичного введения в отверстие рулона стопорится своим кольцевым зажимом, стягиваемым на труде винтом 11. После этого перемещением подвижного конуса 10 по резьбе втулки 8 рулон надежно фиксируется на трубе 6 за счет создаваемого осевого усилия, а затем грузозахватным устройством он поднимается и устанавливается через ось 1 на опорные кронштейны 2 и 3 машины. Рассмотренные механизмы фиксации обеспечивают свободное вращение установленных рулонов. Однако для обеспечения нормальной работы технологического оборудования в них часто дополнительно встраиваются механизмы принудительного вращения и торможения рулонов, рассматриваемые далее.
7.2. Механизмы вращения рулонов
В неприводных механизмах фиксации разматываемые рулоны вращаются от усилий, создаваемых различными механизмами пошаговой или непрерывной подачи ленты. При этом от разматываемого рулона лента получает дополнительное натяжение могущее привести к ее повреждению или даже разрыву, а также снижающее точность работы самих механизмов подачи. Из-за этого в неприводных механизмах фиксации устанавливают только небольшие рулоны, из которых достаточно прочная лента подается в технологическом оборудовании с невысокими скоростями. Для тяжелых же рулонов (массой до 40т) применяются механизмы, осуществляющие их фиксацию на позиции размотки и принудительное вращение от индивидуального привода в соответствии с требуемой скоростью подачи разматываемой ленты (полотна). Такими механизмами вращения рулонов (рулоноразматывателями) обеспечивается снижение и стабилизация усилия натяжения ленты, что позволяет осуществлять ее подачу на высоких скоростях, а также создаются благоприятные условия для более точной работы подающих механизмов.
Конструктивно рулоноразматыватели выполняются с горизонтальным, вертикальным или наклонным расположением оси устанавливаемого рулона. По принципу же фиксации и вращения рулона они подразделяются на три типа:
механизмы, в которых рулоны фиксируются на приводном вращающемся валу, проходящем через их осевое отверстие (рис.7.3а, б, д);
механизмы, в которых рулоны фиксируются на валу, проходящем через их осевое отверстие, а вращаются приводными элементами, контактирующими с наружной цилиндрической поверхностью рулона
(рис.7.3в);
механизмы, в которых рулоны фиксируются и вращаются приводными элементами, контактирующими с их наружной цилиндрической поверхностью
(рис.7.3г).
Вмеханизмах вращения с фиксацией рулонов на приводном валу достигается хорошая балансировка рулона и малое сопротивление его вращению, обусловленное трением вала в подшипниках. Выполняются такие рулоноразматыватели с горизонтальным, вертикальным или наклонным расположением оси устанавливаемого рулона. В этих механизмах при неизменной угловой скорости вращения рулона линейная скорость подаваемой
90