
[SHipinsky_V.G.]_Oborudovanie_i_osnastka_upakovoch1(z-lib.org)
.pdfвнутренние напряжения и не происходит ослабление материала околошовной зоны.
Таким образом, сварка пластмасс может осуществляться как с нагревом соединяемых поверхностей до вязкотекучего состояния, так и без их нагрева. Исходя из этого, существующие способы сварки пластмасс условно можно разделить на следующие три характерные группы.
В первой группе объединяются способы сварки, использующие энергию внешних источников тепла. Это сварка различными нагретыми инструментами, газовыми теплоносителями и нагретыми присадочными материалами. Тепло от внешних источников к свариваемым поверхностям передается в этих способах за счет конвекции, теплопроводности и частично лучеиспусканием.
Ко второй группе относятся способы сварки, при которых теплота генерируется в зоне соединения за счет преобразования различных видов энергии, поступающей от внешних источников. Это сварка токами высокой частоты, ультразвуком, трением, лазерным лучом, инфракрасным излучением, а
также ядерная сварка. |
|
В третью группу объединяются специальные |
способы сварки, |
осуществляемые без нагрева зоны соединительного шва до вязкотекучего состояния. Таковыми являются химическая сварка и сварка с помощью растворителей.
При выборе того или иного способа сварки необходимо учитывать химические, механические и теплофизические свойства пластмасс, толщину и конструктивное исполнение соединяемых элементов, предъявляемые к сварному соединению требования, специфику технологического процесса, производственные затраты и другие факторы, определяющие качество сварки, уровень автоматизации и экономическую эффективность процесса.
8.1. Сварка нагретыми инструментами
Сварка нагретыми инструментами является относительно простым, дешевым и надежным способом получения качественных неразъемных соединений между разнообразными конструктивными элементами изделий, изготовляемых из термопластичных материалов. Прочность получаемых сварных швов обычно достигает при этом 90—100% от прочности основных соединяемых материалов. Сам же процесс сварки легко поддается регулированию, контролю и автоматизации. Нагрев соединяемых поверхностей при такой сварке может осуществляться двумя способами:
непосредственным контактом соединяемых поверхностей с нагретым сварочным инструментом, введенным между ними (рис.8.1а-б);
при контакте нагретого сварочного инструмента с внешними сторонами соединяемых поверхностей (рис.8.1 в-е).
Непосредственным контактом соединяемых поверхностей с нагретым инструментом обычно сваривают стыковыми и угловыми швами толстостенные части пластмассовых изделий (рис.8.1а), а также трубы (рис.8.1б), и другие конструктивные элементы с прямоугольным, круглым и разнообразными фигурными поперечными сечениями.
121

Нагревом с внешней поверхности сваривают, как правило,
нахлесточными швами соединяемые части изделия, выполненные из тонколистовых и пленочных термопластичных материалов. При этом сварка тонколистовых частей производится путем их двустороннего нагрева, а пленочные материалы сваривают как двусторонним, так и односторонним нагревом. В зависимости от температурного состояния нагревательных элементов в течение цикла различают термоконтактный и термоимпульсный способы сварки.
Рис.8.1. Конструктивные схемы сварки нагретым инструментом
При термоконтактном способе сварки температура электронагревательных элементов сварочного устройства в течение всего периода его работы остается практически неизменной. Если такая сварка производится с односторонним нагревом, то соединяемые части 1 и 2 изделия (рис.8.1в) зажимаются с усилием Р между электронагревательной 3 и опорной 4 линейками сварочного устройства, нагреваются в зоне контакта до вязкотекучего состояния и свариваются. После этого электронагревательная линейка 3 отводится, а полученный сварной шов охлаждается на опорной линейке 4 до достижения материалом механической прочности. При сварке с двусторонним нагревом соединяемые части 1 и 2 изделия (рис.8.1г) зажимаются с усилием Р между двумя смыкающимися электронагревательными линейками 3 и 4 сварочного устройства, нагреваются ими в зоне контакта до вязкотекучего состояния и свариваются нахлесточным швом. После этого линейки 3 и 4 разводятся, а полученное сварное соединение охлаждается до достижения механической прочности на воздухе или в специальном теплоотводящем механизме. Для получения же непрерывных сварных нахлесточных швов значительной протяженности соединяемые части 1 и 2 изготовляемого изделия (рис.8.1д) пропускаются между двумя приводными синхронно вращающимися электронагревательными роликами 3 и 4, которые зажимают их с усилием Р, разогревают в зоне контакта до вязкотекучего состояния и, непрерывно продвигая, сваривают. Быстрое же охлаждение полученного сварного шва осуществляется следующей парой аналогичных
122
теплоотводящих роликов (не показаны) или же до достижения механической прочности шов охлаждается окружающим воздухом. При этом ширина получаемого сварного шва определяется шириной рабочей части роликов, которая может быть гладкой или рифленой. Ролики могут выполняться и достаточно широкими, то есть в виде валков, на поверхности которых, например, содержатся углубления под упаковываемые штучные изделия в виде таблеток. Для предотвращения налипания на нагревательные элементы сварочных устройств разогреваемого материала их металлические контактирующие поверхности обычно выполняются с антиадгезионным тефлоновым покрытием
или |
покрываются |
тонкой |
пленкой из |
фторопласта. |
Для |
непрерывной |
термоконтактной |
сварки |
применяются |
также устройства с |
ленточными |
транспортирующими механизмами.
При термоимпульсном способе сварки в каждом цикле смыкающимися электронагревательными элементами сварочного устройства осуществляется как нагрев соединяемых частей изделия под действием подаваемого импульса электрического тока, так и последующее охлаждение выполненного сварного шва. Например, при такой сварке с двусторонним нагревом соединяемые части 1 и 2 изготовляемого изделия (рис.8.1е) зажимаются с усилием Р между смыкающимися линейками 3 и 4 сварочного механизма. После этого на покрытые антиадгезионными фторопластовыми прокладками 5 и 6 ленточные электронагревательные элементы сопротивления 7 и 8 этих линеек подается импульс электрического тока от трансформатора 9. От этого импульса они быстро нагреваются, одновременно нагревая в зоне контакта до вязкотекучего состояния и соединяемые части изделия. Затем ленточные элементы 7 и 8 также быстро охлаждаются, одновременно отводя тепло и от обжимаемого ими сварного шва. После достижения сварным швом требуемой механической прочности линейки 3 и 4 размыкаются, соединенные части изготовляемого изделия удаляются и цикл повторяется. Регулировка необходимой температуры сварки в таких устройствах осуществляется за счет изменения продолжительности и силы импульса подаваемого тока. Качественные же сварные швы получаются при оптимальных значениях усилия прижима сварочных линеек, температуры нагрева и времени сварки.
Длина электронагревательных линеек в устройствах термоимпульсной сварки может достигать 1000 мм и более, в зависимости от размеров частей изделий, соединяемых за один цикл. В автоматах же, изготовляющих пакеты из рукавной рулонной пленки и одновременно упаковывающих в них продукцию, электронагревательная линейка сварочного устройства за один цикл, как правило, выполняет сразу два поперечных соединительных шва и одновременно разрезает рукав между швами. Для этого на рабочей поверхности стеклотекстолитовой планки 1 (рис.8.2а) линейки укладывается два параллельных нагревательных элемента сопротивления 2 и 3, изготовляемых из нихромовой ленты шириной 3 – 5 мм, а между ними размещается термонож 4, выполняемый из нихромовой проволоки диаметром на 0,15 – 0,3 мм большим за толщину нагревательных элементов. Для предотвращения налипания разогреваемого материала рукава наружная рабочая поверхность нагревательных элементов и термоножа покрывается оболочкой 5 из фторопластовой пленки армированной стеклотканью, которая закрепляется на планке 1 накладками 6 с винтами 7.
123
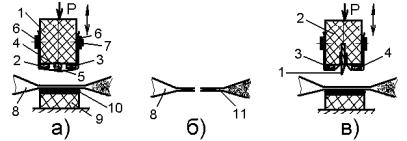
Рис. 8.2. Конструктивная схема электроимпульсной сварки двойным швом
Впроцессе работы рукавный материал 8 зажимается с усилием Р между опускающейся электронагревательной линейкой и опорной линейкой 9, содержащей на рабочей поверхности прокладку 10 из фторопласта-4. В момент их смыкания на нагревательные элементы 2 и 3 подаются импульсы электрического тока, обеспечивающие быстрый нагрев контактирующего материала до вязкотекучего состояния. Одновременно на термонож 4 подается более мощный импульс, который обеспечивает за то же время расплавление и разрезку контактирующего рукава между соединительными швами. После охлаждения полученных сварных швов до состояния достижения материалом механической прочности электронагревательная линейка поднимается приводом в исходное положение. На рукаве же 8 остается два поперечных сварных шва, один из которых укупоривает отделенный пакет 11 (рис.8.2б), а второй – образует на конце рукава дно следующего пакета. При работе с многослойными рукавными материалами, содержащими бумагу или алюминиевую фольгу, в таких линейках для разрезания рукава между сварными швами используются ленточные просечные ножи 1 (рис.8.2в), которые закрепляются в продольном пазу стеклотекстолитовой планки 2 между ленточными нагревательными элементами сопротивления 3 и 4.
Взависимости от толщины и свойств свариваемых материалов продолжительность термоимпульсного нагрева зоны шва может составлять от
десятых долей секунды до десяти секунд, а удельное давление сжатия соединяемых поверхностей устанавливается в пределах от 0,01 до 0,3 МПа.
8.2. Сварка нагретым присадочным материалом
Сварка нагретым присадочным материалом является разновидностью способов сварки, использующих энергию внешних источников тепла. Сущность этого метода заключается в том, что нагрев и неразъемное соединение сопрягающихся поверхностей осуществляется за счет введения между ними расплавленного присадочного материала. При этом тепло передается от присадочного материала к сопрягающимся поверхностям за счет теплопроводности, в результате этого они оплавляются и после охлаждения вместе с присадочным материалом образуют сварной шов. Интенсивность же диффузии молекулярных цепей через свариваемые поверхности определяется силами межмолекулярного взаимодействия, совместимостью соединяемых полимеров и условиями, при которых осуществляется сварка. Соединяемые части изделий, выполненные из пластмасс легко переходящих в вязкотекучее состояние, сваривают идентичным или совместимым расплавленным
124

присадочным материалом. Если же соединяемые части изготовлены из пластмасс, характеризующихся малой скоростью диффузии даже в интервале вязкотекучего состояния (материалы с большим молекулярным весом или высокой полярностью), то их целесообразно сваривать пластифицированным присадочным полимером малого молекулярного веса, легко переходящим в вязкотекучее состояние и обладающим более высокой скоростью диффузии.
Данная сварка может производиться двумя способами:
периодической подачей расплавленного присадочного материала;
непрерывной подачей расплавленного присадочного материала (экструдированием присадки).
Периодической подачей расплавленного присадочного материала выполняются стыковые, угловые, тавровые и нахлесточные швы ограниченной длины. При этом в зависимости от доступности свариваемых мест частей 1 и 2 изделия разделку их соединяемых торцов производят со скосом одной (рис.8.3б) или двух (рис.8.3в) сопрягающихся кромок.
Рис. 8.3. Конструктивная схема сварки нагретым присадочным материалом
После разделки кромок, соединяемые части 1 и 2 изделия (рис.8.3а) стыкуют на подвижном столе 3 сварочного агрегата так, чтобы выполняемый шов располагался точно под соплом 4 пластификатора. Пластификатор же обычно состоит из материального цилиндра 5, охватываемого по наружной поверхности электронагревательными элементами сопротивления 6, и закрепленной на нем загрузочной воронки 7, соединяющейся через высыпное окно с бункером 8, в который загружается гранулированный присадочный материал 9. Над материальным цилиндром соосно установлен плунжер 10, перемещающийся вертикально в направляющей втулке 11 от соответствующего привода, а на нижнем фланце цилиндра 5 крепится переходная втулка 12, фиксирующая сменное сопло 4. К этому же фланцу цилиндра 5 шарнирно присоединяется и кронштейн 13, одно плечо которого взаимодействует с пружиной 14, при этом на втором плече кронштейна крепится ось со свободно вращающимся роликом 15. Когда плунжер 10 пластификатора находится в верхнем исходном положении, то полость цилиндра 5 заполняется через образовавшийся зазор гранулированным присадочным материалом 9, пересыпающимся в воронку 7 из бункера 8. Здесь гранулы быстро нагреваются от стенок цилиндра и плавятся, а затем опускающимся плунжером 10 пластифицированный материал выдавливается из цилиндра 5 через сопло 4 непрерывной вязкотекучей струей 16 на состыкованные кромки частей 1 и 2 изделия, синхронно перемещаемые под соплом столом 3. Далее нанесенный присадочный материал сразу же прикатывается к
125
соединяемым поверхностям роликом 15, поджимаемым пружиной 14. При этом контактирующие поверхности оплавляются, соединяются с присадочным материалом и далее полученный сварной шов охлаждается. Максимальная длина сварного шва, выполняемого за один цикл, определяется объемом порции присадочного материала, пластифицируемого в материальном цилиндре 5. Качество же полученного сварного шва зависит от температуры нагрева присадочного материала и создаваемого роликом 15 прикатывающего удельного давления, значения которых должны быть оптимальными.
Непрерывной подачей расплавленного присадочного материала обычно сваривают между собой полимерные ленты при производстве многослойных комбинированных рулонных материалов. В качестве присадочного материала при этом используются идентичные или совместимые термопласты, у которых температурный интервал вязкотекучего состояния составляет более 50 оС, то есть такие термопласты, которые легко переходят в вязкотекучее состояние при сравнительно низких температурах и при экструзии могут нагреваться значительно выше температуры текучести без заметной деструкции.
8.3. Сварка газовыми теплоносителями
Сварка газовыми теплоносителями является относительно простым, дешевым и распространенным способом получения неразъемных соединений, в котором используется энергия внешних источников тепла. Сущность этого метода заключается в том, что сопрягающиеся поверхности свариваемых частей изделия нагреваются в зоне соединительного шва вместе с присадочным материалом или без него направленной струей горячего газа до температуры вязкотекучего состояния с одновременным обеспечением контакта между ними. Такой сваркой можно выполнять все типы сварных швов, включая нахлесточные, стыковые, угловые и тавровые. При этом свариваемые торцы деталей 1 и 2 (рис.8.4а) значительной толщины (более 2 мм), как правило, разделываются со скосом одной или двух сопрягающихся кромок, а сварка производится с применением присадочного материала 3. Изготовляют присадочный материал в форме прутков диаметром 2 – 6 мм из термопластичных полимеров, которые по своим свойствам идентичны или совместимы с материалом свариваемых деталей. Требуемый же диаметр прутка 3 выбирается в зависимости от толщины и способа разделки соединяемых кромок, причем перед сваркой горячим газом, подаваемым из сопла мундштука 4, эти кромки рекомендуется очищать и обезжиривать. В качестве газового теплоносителя используется азот, аргон, углекислый газ, а также воздух и другие газовые смеси, которые разогреваются электрическими или газопламенными нагревателями. Электрические нагреватели находят более широкое применение, так как они проще и безопаснее в работе. Эти нагреватели в каналах подачи газового теплоносителя содержат спиральные элементы сопротивления, которые, разогреваясь от электрического тока, отдают свое тепло потоку обтекающего газа, направляемого затем с требуемой скоростью через сопло мундштука в зону сварки. Необходимая же форма выходящему потоку горячего газа придается соответствующей конфигурацией сопла нагревателя. Требуемая температура газового теплоносителя в таких
126

нагревателях легко устанавливается за счет изменения величины электрического тока в нагревательных элементах сопротивления, а также регулировкой скорости выходящего газового потока.
В процессе ручной сварки, обезжиренные сопрягающиеся кромки соединяемых деталей 1 (рис.8.4б) нагреваются вместе с подаваемым присадочным материалом 2 горячей струей 3 газового теплоносителя, выходящего с определенной скоростью из сопла мундштука 4 газопламенного нагревателя, плавно перемещаемого вдоль шва рукою сварщика. При этом поверхности соединяемых кромок оплавляются и присадочный материал, разогреваемый до вязкотекучего состояния, соединяется с ними, заполняя одновременно своей массой всю выемку. Далее полученное монолитное сварное соединение охлаждается естественным путем или в потоке теплоотводящего холодного воздуха. В полуавтоматических сварочных агрегатах подача прутка 1 (рис.8.4в) из присадочного материала производится специальным подающим механизмом, который разматывает его с бунта и, непрерывно продвигая по гибкому шлангу, выводит через штуцер 2 в зону сварки. При этом штуцер 2 закрепляется на мундштуке 3 нагревателя, обеспечивающем подачу в зону сварки горячего газа 4. Непрерывное же продвижение такой сварочной головки вдоль соединяемых торцов пластмассовых деталей 5 может производиться как рукою сварщика, так и соответствующим механизмом.
Рис. 8.4. Конструктивные схемы сварки газовыми теплоносителями
Газовыми теплоносителями без применения присадочного материала обычно сваривают нахлесточными швами части изделий, которые выполнены из пленочных и тонколистовых термопластичных материалов. Когда сваривают этим способом по сопрягаемым поверхностям листы 1 и 2 (рис.8.4д) в многослойные комбинированные материалы, то газовый теплоноситель 3 подают из нагревателя через щелевое сопло мундштука 4 в зону схождения этих листов перед валками 5 и 6 подающе-обжимного механизма. При этом сопрягающиеся поверхности листов оплавляются горячим газом, а затем сдавливаются вращающимися валками 5 и 6 и свариваются между собой.
127
Следующей же парой сжимающих валков 7 и 8 подающе-обжимного механизма обеспечивается охлаждение выполненного сварного соединения. Таким образом соединяют в многослойные материалы листы из поливинилхлорида и других пластмасс, а также пленки из полиамида, полиэтилена низкой плотности, полиэтилентерефталата и других полимерных материалов. При непрерывной же сварке рулонных лент нахлесточными швами их боковые концы 1 и 2 (рис.8.4г) укладывают друг на друга на опорной подложке 3 и продвигают по ней с постоянной скоростью под соплом мундштука 4, подающим струю горячего газа 5. Этой струей соединяемые части прижимаются с небольшим усилием к подложке 3 в зоне шва, совместно нагреваются до вязкотекучего состояния и свариваются непрерывным нахлесточным швом, который затем охлаждается окружающим воздухом.
8.4.Ультразвуковая сварка
Вустройствах ультразвуковой сварки нагрев контактирующих поверхностей пластмассовых деталей до вязкотекучего состояния осуществляется за счет преобразования в зоне соединительного шва энергии механических колебаний ультразвуковой частоты (16-50 кГц) в тепловую энергию.
Ультразвуковое сварочное устройство содержит магнитострикционный преобразователь, который располагается под кожухом 1 (рис.8.5а), охлаждаемым проточной водою 2, и питается переменным током ультразвуковой частоты от генератора 3. Сердечник 4 магнитострикционного преобразователя обычно состоит из двух стержней, которые выполняются из ферроили ферримагнетиков, при этом их концы соединяются между собой поперечными накладками, образующими замкнутый магнитопровод. Обмотка 5 наносится на эти стержни таким образом, чтобы в них индуцировались противоположно направленное переменное магнитное поле, вызывающее главным образом линейную магнитострикцию – продольную деформацию стержней при изменении их магнитного состояния. Ток ультразвуковой частоты генератора 3, проходя через обмотку 5 преобразователя, приводит к изменению
стакой же частотой размеров стержней сердечника 4, в результате чего электрические колебания преобразуются в механические с амплитудой смещения 3—5 мкм. Излучаются же эти колебания со стороны поперечных накладок сердечника. При одностороннем излучении неработающая накладка сердечника 4 соединяется с кожухом 1 через экранирующую подушку 6, выполняемую обычно из пористой резины. Амплитуду же колебаний рабочей накладки увеличивают путем жесткого присоединения к ней широким концом стержневого концентратора 7, представляющего собой твердый стержень переменного сечения. При этом максимальный линейный размер D присоединяемого конца концентратора должен быть меньше λ/2 (где λ – длина
волны в материале концентратора). Принцип действия стержневого концентратора основан на увеличении амплитуды колебательного смещения частиц жесткого стержня вследствие уменьшения его поперечного сечения и соответственно массы, так как из закона сохранения количества движения следует:
128

|
|
2 |
|
|
m |
|
d U |
1 |
|
|
|
|||
|
|
|
|
|
1 |
|
dt |
2 |
|
|
|
|
|
|
|
2 |
|
|
m |
|
d U |
2 |
|
|
|
|||
|
|
|
|
|
2 |
|
dt |
2 |
|
|
|
|
|
,
(8.1)
где m1 и m2 |
– масса широкой верхней и узкой нижней частей стержневого |
концентратора соответственно; |
|
d 2U1 dt 2 |
и d 2U2 dt 2 – ускорения, с которыми движутся массы m1 и m2 |
соответственно.
Смещение же U вдоль оси x произвольной точки в идеальной среде в любой момент времени t описывается следующим выражением:
U A sin t kx ,
где А – амплитуда колебаний; ω – круговая частота;
k 2 – волновое число;
(8.2)
λ – длина волны.
Так как m1 > m2 и концентратор колеблется с одинаковой частотой ω = ω1 = ω2, то с учетом выражения (8.2) приходим к заключению, что А2 > А1 ,
где А1 и А2 – амплитуды колебаний масс m1 и m2 концентратора соответственно.
Распространяющиеся в концентраторе упругие волны переносят энергию, которая в процессе колебаний периодически переходит из потенциальной в кинетическую и наоборот. Полная же средняя энергия в бегущей волне определяется зависимостью:
Е
0,5 |
2 |
|
|
А2
,
(8.3)
где ρ – плотность среды.
Таким образом, из приведенных формул (8.1 – 8.3) следует, что амплитуда колебаний нижней узкой части стержневого концентратора будет существенно большей, чем у широкой верхней части, а энергия, подводимая в зону сварки через его узкую часть, будет значительно превышать энергию излучателя.
Рис. 8.5. Конструктивные схемы ультразвуковых сварочных устройств
129
К соединяемым пластмассовым частям 8 и 9, уложенным внахлестку на опорной поверхности пассивного отражателя 10, ультразвуковые колебания поступают либо через присоединяемый к стержневому концентратору инструмент-волновод 11, содержащий на рабочем торце наконечник 12, либо непосредственно от нижнего торца стержневого концентратора 7, оснащенного наконечником 12. В зависимости от формы и расположения сварного шва сменные инструмент-волноводы изготовляются прямыми или изогнутыми, а также с адекватной выполняемому шву конфигурацией рабочей торцевой поверхности. Сварочный же наконечник, испытывающий переменные механические и тепловые нагрузки, должен обладать высокой усталостной стойкостью, а также антиадгезионными свойствами к контактирующим материалам. Этим требованиям удовлетворяют наконечники, которые выполняются из материалов с малой теплопроводностью и высокой механической прочностью. Поскольку магнитострикционный преобразователь, концентратор и инструмент-волновод работают в резонансе, то крепление всего этого акустического устройства к корпусу установки должно осуществляется в месте, где амплитуда его колебаний равна нулю (в узле колебаний). При этом длина магнитострикционного преобразователя обычно принимается равной полуволне, а длина стержневого концентратора с инструмент-волноводом – кратной целому числу полуволн.
В процессе ультразвуковой сварки соединяемые части 8 и 9 изготовляемого изделия зажимают с усилием Р между торцом инструментволновода 11 с наконечником 12 и опорной поверхностью пассивного
отражателя 10, |
который выполняется из материала, хорошо |
гасящего |
ультразвуковые |
колебания – резины, древесины и других. Затем генератором 3 |
подается переменный ток ультразвуковой частоты на обмотку 5 магнитострикционного преобразователя и в нем возбуждаются продольные высокочастотные механические колебания, которые через стержневой концентратор 7, инструмент-волновод 11 и наконечник 12 вводятся в материал соединяемых частей 8 и 9 изготовляемого изделия. Здесь энергия механических колебаний преобразуется в тепловую энергию, что приводит к нагреву зоны контакта до температуры вязкотекучего состояния и свариванию деталей по сопрягающимся поверхностям за время от 0,1 до 10 с в зависимости от их толщины. Механические колебания и усилие Р действуют при этом по одной оси, перпендикулярной к свариваемым поверхностям.
Уменьшить потери ультразвуковой энергии, переходящей в станину сварочной установки из инструмент-волновода 1 (рис.8.5б) через наконечник 2, а также соединяемые детали 3 и 4, позволяет настроенный отражатель 5, который выполняется из стального стержня, закрепленного на резиновой подложке 6. При этом высота настроенного отражателя составляет приблизительно четверть длины волны воздействующих ультразвуковых колебаний и уточняется экспериментально.
Цикл ультразвуковой сварки пластмасс включает в себя механическое сжатие и колебание соединяемых поверхностей, их нагрев в условиях вязкоупругости, передачу теплоты, течение и смачивание, межмолекулярную диффузию. При этом не исключена возможность механической деструкции полимера, способствующей его течению при температурах более низких, чем
130