
[SHipinsky_V.G.]_Oborudovanie_i_osnastka_upakovoch1(z-lib.org)
.pdfдлины и продвигается в шаговом режиме через все технологические позиции линии. В частности, такой механизм содержит установленные на концах линии натяжной 1 (рис.7.4ж) и приводной 2 валы на звездочках 3 которых натянуты две параллельные бесконечные роликовые цепи 4, несущие механические захваты 5 и движущиеся вдоль линии в профильных направляющих 6. Захваты 5 закрепляются с определенным шагом на двух соседних осях 7 роликовой цепи 4 своим Г-образным кронштейном 8, имеющим опорную площадку 9, с которой сопрягается установленная в окне кронштейна на оси 10 подвижная губка 11 захвата, переходящая снизу в клинообразный хвостовик 12, поджимаемый пружиной 13. Пошаговое продвижение ленты 14 осуществляется прерывистым односторонним вращением вала 2 со звездочками 3 от связанного с ним через муфту свободного хода привода. При этом на натяжном 1 и приводном 2 валах хвостовики 12 находят своей клиновой поверхностью на расположенные рядом со звездочками 3 дисковые кулачки и, поворачиваясь на оси 10, отводят подвижные губки 11 от опорных площадок 9, раскрывая тем самым захваты 5. При этом поступающая с рулона лента 14 укладывается своими краями в зоне вала 1 на опорные площадки 9 раскрытых захватов и затем, при сходе хвостовиков 12 с дисковых кулачков, прижимается к ним подвижными губками 11, возвращающимися в исходное положение от пружин 13. На приводном же валу 2 из раскрывающихся аналогичным образом захватов 5 оставшиеся отходы ленты 14 отводятся, например, на наматывающую их катушку для последующей утилизации. В результате такие несущие механизмы подачи принимают на себя все механические нагрузки, возникающие в процессе шагового продвижения через технологические позиции автоматизированных линии непрочных лент, предохраняя их тем самым от недопустимых растяжений и повреждений.
7.4. Механизмы резки ленты
Механизмы резки обеспечивают разделение подаваемой ленты на отдельные заготовки. Обычно эти механизмы называют ножницами, а по конструктивным особенностям подразделяют на следующих три вида:
ножницы, обеспечивающие поперечную резку с остановкой ленты (с параллельными, наклонными (гильотинные), криволинейными и пилообразными ножами);
ножницы, обеспечивающие поперечную резку ленты на ходу («на лету») при ее движении с большой скоростью (барабанные, рычажно-кривошипные, планетарные и маятниковые летучие ножницы);
ножницы, обеспечивающие как поперечную, так и продольную резку непрерывно движущихся лент (одноножевые и дисковые ножницы).
Резка ленты осуществляется обычно двумя исполнительными органами ножниц, один из которых обязательно подвижный, а второй может быть как движущимся, так и неподвижным. Подвижный орган с острой режущей кромкой называется ножом. Неподвижный орган с острой режущей кромкой, противостоящий ножу, называется противоножом, а противостоящую подвижному ножу опорную поверхность или щель называют противоопорой. Режущая кромка ножа и противоножа в продольном направлении может быть прямой, криволинейной или пилообразной, а в поперечном сечении с
101
двухсторонней или односторонней заточкой под острым углом, или заточенной под прямым углом. Наиболее часто применяются ножи с прямолинейной режущей кромкой, поскольку они просты и технологичны в изготовлении. Ножи с криволинейной режущей кромкой обеспечивают постепенное врезание лезвия в материал, а также более плотное прилегание в зоне резания двух сопрягающихся режущих кромок. Пилообразные ножи обычно применяются совместно со щелевой противоопорой для разрезания натянутых лент. Они обладают более высокой износостойкостью и работают со значительно меньшим усилием резания. Недостатки этих ножей заключаются в более трудоемком изготовлении, несколько неровной (зубчатой) линии среза, оставляемой на материале, а также в необходимости натяжения разрезаемой ленты над щелью противоопоры, что усложняет конструкцию ножниц.
В ножницах, обеспечивающих поперечную резку с остановкой ленты, подвижные ножи совершают возвратно-поступательные или качательные движения, перекрывая во время резания зону движения ленты. В ножницах возвратно-поступательного действия лента 1 (рис.7.5а) разрезается, в
частности, двумя параллельными ножами, при этом нижний нож 2 крепится неподвижно, а верхний нож 3 совершает от привода циклические возвратнопоступательные движения. В гильотинных ножницах такого же типа верхний подвижный нож 1 (рис.7.5б) устанавливается с наклоном в 2—6° относительно неподвижного нижнего ножа 2 и этим достигается снижение усилия резания ленты 3. При работе ножниц лента вначале подается на заданный шаг через зазор между ножами. После этого верхний нож опускается и сопрягающимися режущими кромками ножей заготовка отрезается от ленты. Резка в таких ножницах может производиться без прижима ленты и отрезаемой заготовки, с прижимом только ленты и с прижимом к опорным поверхностям ленты и отрезаемой заготовки.
Усилие разрезки Рр ленты на ножницах с параллельными ножами (рис.7.5а) рассчитывается по формуле:
Р |
Р |
|
k
В
s
СР
, Н
(7.11)
где k – коэффициент, учитывающий условия резания (притупление режущих кромок ножей, неравномерность толщины материала, увеличение зазора между ножами и другие факторы); принимается k = 1,25;
В – ширина разрезаемой ленты, мм; s – толщина разрезаемой ленты, мм;
СР – сопротивление материала резанию, МПа.
Для ножниц же с наклонным ножом (гильотинных) необходимое усилие разрезки Рр ленты (рис.7.5б) определяется по формуле:
РР |
k |
|
s 2 |
|
СР , Н |
(7.12) |
|
tg |
|||||
|
2 |
|
|
|
где α – угол наклона ножа, град.
Иногда в таких ножницах подвижный ножевой блок в период резания перемещается на некотором участке вместе с лентой в направлении подачи, обеспечивая тем самым разрезание на заготовки непрерывно движущихся лент.
102

Однако этим существенно усложняется конструкция ножниц, а отрезка заготовок может осуществляться только при небольших скоростях движения ленты.
Рис.7.5. Конструктивные исполнения механизмов резки ленты
Для поперечной резки на ходу («на лету») быстро движущихся лент наиболее эффективны так называемые летучие ножницы, которые по конструктивному исполнению подразделяются на барабанные, рычажнокривошипные, планетарные и маятниковые. В частности, наиболее распространенные барабанные летучие ножницы характеризуются простотой конструкции и высокой надежностью в эксплуатации. Эти ножницы содержат два синхронно вращающихся барабана 1 (рис.7.5в) по образующим которых закреплены сопрягающиеся ножи 2 (по одному или несколько). В процессе работы лента 3 подающими валками 4 непрерывно перемещается с постоянной скоростью VЛ между синхронно вращающимися барабанами 1 и разрезается на мерные заготовки 5 их периодически сопрягающимися ножами 2. Для создания же зазоров между отрезанными заготовками скорость у роликов 6 выносящего рольганга должна быть большей скорости продвижения ленты валковой подачей 4. Эти ножницы обеспечивают резку ленточных материалов, непрерывно движущихся со скоростью до 15 м/с и более, в дух режимах:
в режиме периодических запусков и остановок, например, при обрезке переднего конца ленты или ее разрезке на длинные заготовки;
в режиме непрерывного вращения барабанов и подачи ленты с постоянной скоростью.
Впоследнем случае разрезка осуществляется через промежутки времени
τс, определяемые частотой вращения барабанов. Длина отрезаемых при этом заготовок рассчитывается по формуле:
L V |
|
2 V |
k |
|
|
С |
|
, м |
(7.13) |
||
Л |
Л |
|
|||
|
|
|
Н |
|
где k – коэффициент пропуска реза; он характеризует число оборотов барабана за время между двумя последовательными резами. Например, если рез
103
происходит за каждый оборот (рис.7.5в), то k = 1; если на барабанах по два ножа (рис.7.5г), то k = 0,5; если рез происходит через каждые два оборота барабана меньшего диаметра (рис.7.5д), то k = 2;
ω – угловая скорость приводного барабана меньшего диаметра (нижнего или верхнего), с-1;
VЛ – скорость движения ленты, м/с.
При окружной скорости режущих кромок ножей, равной или большей скорости VЛ движения ленты, такие ножницы в период резания не задерживают ленту. При постоянной же скорости движения ленты (VЛ = const) длина отрезаемых ими заготовок будет определяться угловой скоростью приводного барабана и коэффициентом пропуска реза.
Поперечная резка непрерывно движущихся тонких лент осуществляется также ножницами, в которых режущий блок содержит заостренный нож 1 (рис.7.5е) синхронно вращающийся с противоопорой 2. Разрезается же проходящая между ними лента 3 врезающимся в нее лезвием ножа 1 на поверхности противоопоры 2 в процессе их совместного движения с одинаковыми скоростями. Такие режущие пары могут встраиваться и в валковые подачи. При этом длина отрезаемых заготовок будет равна длине окружности приводного валка подачи.
Продольная и поперечная резка непрерывно движущихся лент осуществляется неподвижными остро заточенными ножами, а также
дисковыми ножницами, режущими органами в которых являются сопрягающейся пары синхронно вращающихся дисковых ножей.
Неподвижные ножи с остро заточенной под острым углом режущей кромкой (например, бритвенные лезвия) применяются для поперечной и продольной резки движущихся с натяжением тонких полимерных и бумажных лент, а также лент из других аналогичных непрочных материалов. Такие ножи закрепляются неподвижно в оправках режущего блока с расположением лезвия на встречу движущемуся с натяжением разрезаемому рулонному полотну.
Дисковые ножницы применяются для обрезки кромок и роспуска на полосы широких листов, а также для обрезки кромок и непрерывной продольной резки на более узкие ленты широких рулонных материалов. Сопрягающиеся пары дисковых ножей 1 (рис.7.5ж) в таких ножницах насаживаются на два приводных параллельных вала 2, синхронно вращающихся навстречу друг другу. Причем для обрезки кромок на листах и рулонном материале применяются однопарные и двухпарные дисковые ножницы, а для роспуска листов на полосы и продольной резки широкого рулонного полотна на ленты с одновременной обрезкой кромок – многопарные (многодисковые) ножницы. Дисковые ножи таких ножниц в поперечном сечении могут выполняться Г-образными (рис.7.5к), с односторонним расположением режущей кромки или Т-образными (рис.7.5л) с двусторонним расположением режущих кромок. Для предотвращения преждевременного затупления торцевая сторона режущей кромки дисковых ножей затачивается под углом β = 1 – 1,5°. Работающие в паре дисковые ножи устанавливаются с радиальным перекрытием режущих кромок на величину δ. Чем толще разрезаемый материал, тем меньше перекрытие ножей. Дисковые ножи 1 могут устанавливаться на параллельных валах 2 последовательно (рис.7.5ж)
104

или в обхват (рис.7.5з). В первом случае упрощается установка ножей, однако кромки у отрезаемых лент по линиям среза оказываются загнутыми в разные стороны, что часто нежелательно. Лучшие результаты достигаются при установке ножей в обхват, так как загибы кромок по линиям среза у каждой ленты получаются направленными в одну и ту же сторону, однако процесс установки и переточки ножей в этом случае более трудоемкий. Для улучшения продвижения отрезаемых лент и исключения их прогиба на валах между ножами устанавливаются попарно работающие резиновые фрикционные кольца 3 (рис.7.5з) или же разрезаемый материал подается к ножам в специальных направляющих.
Минимальный диаметр дисковых ножей Dmin, обеспечивающий захват и протягивание разрезаемого материала, рассчитывается по формуле:
|
|
s |
|
|
|
|
|
|
|
Dmin |
|
1 f |
2 |
|
, мм |
(7.14) |
|||
|
|
|
|
|
|
||||
|
|
|
|
|
|
||||
|
1 f 2 1 |
|
|||||||
|
|
|
|
|
|
где s – толщина разрезаемого материала, мм;
δ - радиальное перекрытие режущих кромок дисковых ножей, мм; f – коэффициент трения между разрезаемым материалом и ножами.
7.5. Механизмы правки ленты
Ленты, разматываемые с рулонов, имеют остаточную кривизну, препятствующую получению плоских заготовок с точными размерами, а также затрудняющую работу подающих и других функциональных механизмов. Из-за этого разматываемые ленты необходимо править и с увеличением их толщины потребность в правке возрастает. Устраняется же кривизна на лентах, листах, сортовом прокате и разнообразных плоских заготовках различными способами: знакопеременным изгибом, растяжением, кручением, сжатием. Разматываемые рулонные материалы обычно правят знакопеременным изгибом, осуществляемым в многовалковых механизмах и машинах.
Правка знакопеременным изгибом основана на упругопластическом знакопеременном изгибе ленточного материала 1 (рис.7.6а) при его движении между двумя рядами валков 2, расположенных в шахматном порядке. При этом каждый участок ленты подвергается многократному изгибу в противоположных направлениях, а возникающие в ленте напряжения растяжения превышают предел текучести материала. С увеличением количества валков, через которые проходит лента, качество правки улучшается. Причем для получения прямолинейной ленты ее знакопеременный поперечный изгиб в многовалковом механизме должен последовательно уменьшаться от второго валка к последнему. При этом под первым и последним валками механизма лента не деформируется и моменты М1 и Мn равны нулю. Под вторым, третьим и четвертым валками механизма все сечение ленты
подвергается пластическому изгибу, а моменты М2, М3 и М4 |
определяются по |
|||
формуле: |
|
|
|
|
М П Т |
b h2 |
, Н∙мм |
(7.15) |
|
4 |
||||
|
|
|
где Т – предел текучести материала ленты, МПа;
105

b и h – ширина и толщина ленты, мм.
Под предпоследними тремя валками (n-3, n-2 и n-1) механизма все сечение ленты деформируется упруго и моменты Мn-3, Мn-2 и Мn-1 определяются по формуле:
|
|
|
|
|
b h |
|
|
|
|
|
2 |
М |
У |
|
Т |
|
6 |
|
|
|
|||
|
|
|
|
|
, Н∙мм
(7.16)
Под остальными промежуточными валками механизма значение момента изгиба среднее между пластическим и упругим моментами.
Исходя из этого, суммарное давление Р, действующее на все верхние и нижние валки правильного механизма можно вычислить по формуле:
Р |
5 |
n 2 Т |
|
b h2 |
, Н |
(7.17) |
|
3 |
t |
||||||
|
|
|
|
|
где n – число правильных валков; t – шаг валков, мм.
Исследованиями установлено, что максимальное усилие будет воспринимать третий валок; определить же это усилие можно по формуле:
|
|
|
|
b h |
|
|
|
|
2 |
Р |
2 |
Т |
|
|
3 |
|
|
t |
|
|
|
|
|
, Н
(7.18)
Крутящий момент Мдеф и мощность Nдеф, необходимые для привода всех (n-2) валков правильного механизма (кроме первого и последнего, которые не изгибают ленту), определяют по формулам:
М деф
N |
деф |
|
Т2
4 E
2 Т
2 E
b h D
V b h
kдеф , Н∙мм
k |
деф , Вт |
|
(7.19);
(7.20)
где Е – модуль упругости (модуль Юнга) материала ленты, МПа; D – диаметр правильных валков, мм;
V – скорость правки ленты, м/с;
kдеф – результирующий (суммарный) коэффициент пластической деформации при правке ленты:
|
|
|
|
|
1 |
|
|
|
|
|
k |
|
k 2 |
|
|
|
k |
|
n 3 |
|
|
деф |
|
|
2 |
(7.21) |
||||||
|
2 |
|
k2 |
|
|
|||||
|
|
|
|
1 |
|
|
|
|
где k2 = 0,6 – 0,8 – коэффициент проникновения пластической деформации под вторым валком.
При определении мощности электродвигателя Nдв, обеспечивающего привод правильного механизма наряду с Nдеф необходимо учитывать потери мощности на трение в подшипниковых опорах валков NП и мощность трения качения NК всех n валков по ленте, а также КПД механизмов передачи вращения от привода валкам. Следовательно:
106

N |
|
|
N |
деф |
N |
П |
N |
К |
|
|
|
|
|||||
дв |
|
|
|
|
|
|
||
|
|
|
|
|
|
|
||
|
|
|
|
|
|
|
|
, Вт
(7.22)
Потери мощности на трение в подшипниковых опорах NП всех n рабочих валков правильного механизма вычисляются по формуле:
N |
П |
|
0,5 Р d
, Вт
(7.23)
где Р – суммарное давление, действующее на все верхние и нижние валки правильного механизма, Н;
µ– коэффициент трения в подшипниковых опорах валков; d – диаметр трения в подшипниковых опорах валков, м;
ω – угловая скорость вращения валков, с-1.
Мощность трения качения NК всех n рабочих валков по ленте определяется по формуле:
N |
K |
|
10 |
3 |
Р f |
|
, Вт
(7.24)
где f – коэффициент трения качения, мм; с учетом возможного проскальзывания между валками и лентой его принимают: для стальных лент f = 0,8 – 1 мм; для лент из цветных металлов f = 0,9 – 1,2 мм.
Шаг t и диаметр D правильных валков принимают, основываясь на накопленных экспериментальных данных. Наибольший шаг валков обычно выбирается из условия: tmax = (25 – 30)∙hmax. Наименьшее значение шага валков определяется условиями прочности их шеек под подшипники и не допущением смятия ленты валками. Из условия прочности шейки валка при передаче им
наибольшего крутящего момента:
t |
|
2,6 3 |
b h |
2 |
min |
|
|||
|
|
max |
. Обычно tmin = (10 –
20)∙hmax. Диаметр валков принимается из условия: D = (0,85 – 0,95)∙t. Синхронное вращение на рабочие валки правильного механизма передается шарнирными шпинделями, связанными с электродвигателем через шестеренную клеть или через систему взаимосвязанных зубчатых колес. В современных конструкциях правильных машин вместо громоздких шестеренных клетей и редукторов с цилиндрическими колесами стали применять планетарные редукторы, обеспечивающие снижение массы привода и его габаритов.
Правильные и рулоноразматывающие механизмы часто объединяют в единую конструкцию, называемую правильно-разматывающей машиной, которая работает от индивидуального привода. Состоит такая машина из станины 1 (рис.7.6б) на которой располагаются механизм 2 фиксации и размотки рулона 3, задающая 4 и тянущая 5 валковые подачи, а также правильная клеть, верхний ряд валков 6 которой располагается на качающейся в шарнире 7 раме 8. Положение же рамы 8 регулируется вращением винта 9 с помощью ручки 10, при этом просвет между рядами валков устанавливается несколько меньшим толщины выпрямляемой ленты 11. Привод всех функциональных механизмов машины осуществляется от электродвигателя 12 постоянного тока через редуктор 13, цепную передачу 14 и систему взаимосвязанных зубчатых колес. Диаметры DВ валков задающей 4 и тянущей 5
107
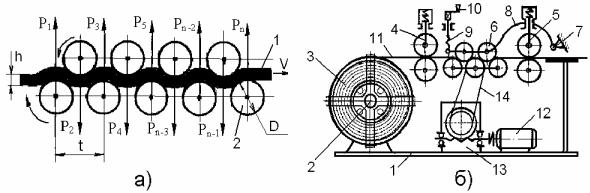
подач в таких устройствах рекомендуется принимать большими диаметра правильных валков D, соблюдая соотношение DВ = (1,2 – 1,8) D.
Рис.7.6. Конструктивные исполнения механизмов правки ленты
В процессе работы устройства разматываемая лента 11 пропускается между двумя рядами валков 6 правильной клети и подвергается ими упругопластическому знакопеременному поперечному изгибу с последовательно уменьшающейся амплитудой. Протягивание и поддержание же ленты в плоскости правки обеспечивается задающей 4 и тянущей 5 валковыми подачами. На лентах из низкоуглеродистой стали такой правкой разрушается цементитная сетка, возникающая в результате старения проката, и этим улучшаются свойства материала, а также снимаются заусенцы на торцах ленты, что способствует повышению точности работы механизмов подачи.
Основными узлами правильных машин являются правильная клеть с валками и механизмом регулировки их положения, а также привод с механизмами передачи движения и система управления. Кроме этого правильные машины часто оснащаются дополнительными устройствами, такими как: валковые подачи с механизмами прижима и подъема верхнего валка, которые устанавливаются на входе, выходе или по обеим сторонам правильной клети; перегибающие механизмы; опорные ролики, предотвращающие прогиб правильных валков; направляющие проводки для ленты; а также индикаторы, отсчетные шкалы и циферблаты для контроля за правильностью регулировки правильных валков и других механизмов машины. Наименьшее число правильных валков, обеспечивающее удовлетворительную правку, равно пяти. Широкое же распространение получили семивалковые и девятивалковые правильные клети, обеспечивающие вполне приемлемое качество правки для широкой номенклатуры применяемых лент. В отдельных случаях для повышения качества правки число валков увеличивают до 11 — 17 и более, причем наибольшее число валков принимают для правки тонких и широких лент (b > 1000 мм).
7.6. Механизмы амортизации и натяжения ленты
Механизмы амортизации и натяжения обеспечивают снижение силы инерционного натяжения разматываемой ленты при ее ускорениях в процессе подачи, а также накопление определенного запаса ленты в компенсационной петле (рис.7.7) с требуемым постоянным натяжением. Такие механизмы особенно необходимы при пошаговой подаче ленты, так как действующие ускорения подачи при значительном моменте инерции разматываемого рулона
108
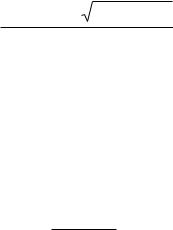
создают в ней повышенные растягивающие напряжения, приводящие к разрывам, а также снижающие точность работы самих подач. В определенных условиях эти механизмы могут также обеспечивать и предварительную правку разматываемой ленты за счет ее обратного упругопластического перегиба в вершине компенсационной петли. По конструктивному исполнению они подразделяются на механизмы со свободной и принудительно натянутой компенсационной петлей, а по количеству петель – на однопетлевые и многопетлевые.
Механизмы амортизации и натяжения со свободной петлей
(рис.7.7а-б) состоят из двух вращающихся опорных роликов 1, удерживающих расположенную между ними компенсационную петлю 2 из разматываемой с рулона ленты. Применяются они в тех случаях, когда лента с рулона разматывается одним механизмом, а на дальнейшую обработку продвигается другим механизмом подачи, то есть свободная петля используется для накопления запаса ленты между разматывающим и подающим механизмами, обеспечивая при этом заданное натяжение ленты, определяемое весом компенсационной петли. В качестве разматывающего механизма в таких устройствах, в частности, может использоваться вертикально подвешенный пневмоцилиндр 3 (рис.7.7б) шток 4 которого несет на себе свободно вращающийся ролик 5. Перед подачей ленты на следующий шаг, опускающийся шток 4 срабатывающего пневмоцилиндра 3 надавливает роликом 5 на находящуюся под ним ленту, при этом она разматывается с неприводного рулона и накапливается между опорными роликами 1 в виде компенсационной петли 2. После этого ролик 5 поднимается в верхнее исходное положение, а удерживающая ленту подача продвигает ее вперед на заданный шаг за счет созданного в петле запаса и далее цикл повторяется. Механизмы со свободной петлей конструктивно предельно просты, однако для создания значительного постоянного натяжения ленты их петли должны иметь довольно большую величину провисания Н (рис.7.7а).
Сила же тяжести G, создаваемая компенсационной петлей, |
определяется |
||||||||
по формуле: |
|
|
|
|
|
|
|
|
|
|
|
L 2 |
H |
4 H |
2 |
2 |
|
|
|
G b h |
|
|
L |
|
, Н |
(7.25) |
|||
|
|
|
2 |
|
|
|
|||
|
|
|
|
|
|||||
|
|
|
|
|
|
|
|||
|
|
|
|
|
|
|
|
|
|
где b и h – ширина и толщина ленты, мм;
ρ – удельный вес материала ленты, Н/мм3; Н – величина провисания ленты в компенсационной петле, мм;
L – расстояние между осями опорных роликов, мм.
Сила сопротивления продвижению ленты Рс, обусловленная весом компенсационной петли будет при этом составлять:
Рc |
G |
|
2 cos , Н |
(7.26) |
где φ – угол между вертикалью и линией, соединяющей нижнюю точку компенсационной петли с осью верхнего опорного ролика, град.
109

В механизмах с принудительно натянутой компенсационной петлей
рабочий орган, создающий натяжение, располагается в вершине петли. Им обычно является свободно вращающийся на оси ролик, а иногда и охватываемый лентой гладкий стержень. Применяются эти механизмы как в тех случаях, когда лента с рулона разматывается одним механизмом, а на дальнейшую обработку продвигается другим механизмом, так и при выполнении функций разматывания рулона и продвижения ленты только одним механизмом подачи. В последнем случае при продвижении ленты подающим механизмом на заданный шаг компенсационная петля уменьшается и вместе с ней вверх перемещается рабочий орган, создавая при этом такое натяжение, которое после завершения подачи обеспечивает вращение рулона с накоплением
разматываемой ленты в петле |
до достижения им исходного нижнего |
положения. |
|
Рис.7.7. Конструктивные исполнения механизмов амортизации и натяжения ленты
Натяжным рабочим органом в таких механизмах является располагающийся в компенсационной петле 1 (рис.7.7в) ролик 2, который свободно вращается на оси, перемещающейся в вертикальных направляющих 3. Ось такого ролика 1 (рис.7.7г), находящегося в вершине петли 2, может крепиться и на конце рычага 3, качающегося на оси вращения разматываемого рулона 4. Создать более высокое усилие натяжение компенсационной петли 1 (рис.7.7д), удерживаемой на вращающихся опорных роликах 2, позволяет рабочий орган, свободно вращающийся ролик 3 которого располагается в вершине петли и крепится на конце качающегося в шарнире 4 рычага 5, дополнительно нагружаемого амортизирующей пружиной 6. В некоторых конструкциях рабочих органов рычаг выполняется из двух параллельных пластинчатых пружин, на одном конце которых крепится с двух сторон ось натяжного ролика, при этом вторые их концы устанавливаются на оси шарнира или жестко закрепляются в несущей опоре. Таким рабочим органом обеспечивается более мягкая амортизация подаваемой ленты за счет дополнительно упругого изгиба образующих рычаг двух пластинчатых пружин.
Многопетлевой механизм на качающемся в шарнире 1 (рис.7.7е) рычаге 2 несет группу установленных с определенным шагом натяжных роликов 3, последний из которых располагается на конце рычага. При этом разматываемая
110