
[SHipinsky_V.G.]_Oborudovanie_i_osnastka_upakovoch1(z-lib.org)
.pdfматериалов и штучных изделий. Они характеризуются высокой механической прочностью, безотказностью в эксплуатации и долговечностью.
5.3. Конвейеры не замкнутые
Конвейеры не замкнутые содержат транспортирующие механизмы, перемещающие грузы от их начала к концу. По принципу действия и особенностям конструктивного исполнения этих механизмов не замкнутые конвейеры подразделяются на роликовые (рольганги), шнековые, винтовые, валковые и вибрационные.
Роликовые конвейеры (рольганги) применяются для перемещения штучных крупногабаритных грузов и представляют собой устройства, у которых транспортирующая поверхность образована из установленных на раме с определенным шагом вращающихся роликов. Различают рольганги неприводные и приводные, выполняемые с цельными или секционными рамами.
По неприводным горизонтальным рольгангам изделия принудительно перемещаются от толкающего или тянущего усилия, создаваемого человеком или соответствующими механизмами. При этом величина усилия, необходимого для продвижения груза, не превышает 2 – 3 % его веса и в 8 – 10 раз меньше усилия, необходимого для перемещения этого груза при его скольжении по плоской поверхности.
В приводных рольгангах транспортируемые изделия перемещаются за счет наличия сил трения между грузом и роликами, которые принудительно вращаются с заданной скоростью от соответствующего группового или индивидуального привода. Передача вращения роликам от группового привода может осуществляться коническими зубчатыми шестернями, роликовыми и втулочными цепями, канатно-барабанными и фрикционными передающими механизмами. Наибольшее распространение получили рольганги с цепными и коническими зубчатыми передающими механизмами. Приводной рольганг, в частности, состоит из рамы 1 (рис.5.3а) на которой с заданным шагом в подшипниках установлены параллельные цилиндрические ролики 2, несущие транспортируемые изделия 3. Валы же этих роликов через конические зубчатые передачи 4 кинематически связаны с распределительным валом 5, приводимым во вращение от электродвигателя 6 через редуктор и клиноременную передачу 7. Ширина рольганга обычно принимается на 50 – 100 мм большей поперечного размера транспортируемого груза, а необходимый шаг tр установки роликов определяется из соотношения:
0,2 lг |
t р 0,45 lг |
(5.5) |
где lг – размер перемещаемого груза в направлении движения, мм. Максимальный шаг между роликами допускается таковым, чтобы
транспортируемые изделия в процессе движения одновременно опирались не менее чем на два ролика.
В ряде случаев конвейеры фрикционного действия могут выполняться из двух параллельных встречно вращающиеся валков 1 (рис.5.3б), по поверхности которых в продольном направлении движутся транспортируемые изделия 2.
71
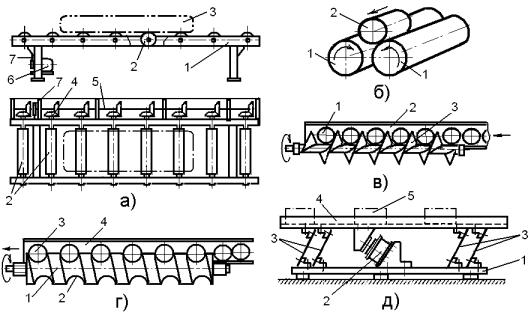
Рис.5.3. Конструктивные исполнения конвейеров не замкнутых
Шнековые конвейеры широко применяются для транспортирования сыпучей, мелкокусковой и пластичной продукции, а также штучных изделий, как в горизонтальной плоскости, так и с подъемом, включая вертикальное направление. Продукция в таких конвейерах перемещается вращающимся шнеком, состоящим из прямолинейного вала и присоединенных к нему кольцевых дисков, образующих винтовую транспортирующую поверхность. Штучные изделия 1 (рис.5.3в) в таком конвейере поступательно перемещаются с заданным шагом по направляющему лотку 2 между винтовыми дисками шнека 3, вращающегося относительно продольной оси. Достоинства шнековых конвейеров заключаются в простоте конструктивного исполнения, компактности и в возможности герметичного транспортирования пылящих и интенсивно испаряющихся грузов. К недостаткам относят высокий расход энергии, интенсивный износ шнека и желоба, из-за постоянного трения о них продукции, а также измельчение и истирание при транспортировании самих грузов.
Винтовые конвейеры применяются для транспортирования штучных изделий с заданным шагом и ритмом, определяющимся угловой скоростью вращения их рабочих органов, которые по конструктивному исполнению подразделяются на стержневые и витые. Стержневой транспортирующий орган 1 (рис.5.3г) такого конвейера выполняется прямолинейным и с винтовой рабочей канавкой 2 на цилиндрической поверхности, профиль которой, как правило, соответствует поперечному сечению изделий 3, находящихся в этой канавке и движущихся с заданным шагом по прямолинейной направляющей 4, при его вращении относительно продольной оси.
Широкое распространение также получили вибрационные инерционные конвейеры, в которых перемещение изделий или сыпучей продукции обеспечивается виброколебаниями от соответствующего привода на наклонных стержневых пружинах жесткого транспортирующего элемента с частотой от 7,5 до 100 циклов в секунду и амплитудами от 0,1 до 15 мм. При этом грузы продвигаются с отрывом или без отрыва от транспортирующей поверхности конвейера в результате взаимодействия сил инерции, тяжести и трения. В
72

частности, такие конвейеры с электромагнитным приводом состоят из основания 1 (рис.5.3д), к которому крепятся электромагнитный привод 2 и наклонные стержневые или плоские пружины (рессоры) 3, несущие жесткий прямолинейный лоток 4, продвигающий своими виброколебаниями находящиеся на нем изделия 5. Эти конвейеры универсальны, конструктивно просты, надежны, долговечны и экономичны. Они обеспечивают транспортирование грузов с углом подъема к горизонту до 5 – 8о, а также бесступенчатое регулирование скорости движения в широком диапазоне.
5.4. Транспортеры круговые
Транспортеры круговые обеспечивают перемещение грузов по кольцевой траектории. По принципу действия и особенностям конструктивного исполнения они подразделяются на дисковые, карусельные, роторные и вибрационные.
В карусельных транспортерах исполнительным механизмом является рабочий стол (планшайба) (рис.5.4а), вращающийся или дискретно поворачивающийся в требуемом ритме на заданный шаг (угол поворота) вместе с расположенными на нем изготовляемыми изделиями. При этом объекты обработки закрепляются в приспособлениях, установленных с заданным шагом на рабочей поверхности стола или фиксируются непосредственно в его гнездах.
Рис.5.4. Конструктивные исполнения транспортеров круговых
Роторные транспортеры содержат расположенные с определенным шагом по окружности вращающегося корпуса захватные устройства (механические, электромагнитные, вакуумные), синхронно переносящие изготовляемые изделия между исполнительными механизмами, например, в
73
роторных автоматических линиях. В частности, транспортный ротор, обеспечивающий одновременную переориентацию деталей 1 (рис.5.4б) состоит из цилиндрического основания 2, в котором на вращающемся валу 3 движутся цилиндрические корпуса 4 и 5. При этом в радиальных отверстиях верхнего корпуса 5 располагаются державки 6 механических захватов 7, шестерни 8 которых находятся в зацеплении с зубчатыми рейками 9, штоки 10 которых располагаются в каналах нижнего корпуса 4 и получают вертикальные перемещения от своих кулачков 11, движущихся в профильном пазу неподвижного основания 2. В процессе работы этот транспортный ротор своими механическими захватам 7 забирает детали 1 на исходной позиции и в процессе вращения переносит их, а затем отдает, например, в приемные механизмы синхронно вращающегося технологического ротора. При этом кулачками 11, движущимися в профильном пазу основания 2, штоки 10 перемещаются вертикально и связанными с ними зубчатыми рейками 9 через шестерни 8 вращают державки 6 с захватами 7, обеспечивая одновременную переориентацию удерживаемых деталей на 180о.
Вдисковых транспортерах главным исполнительным механизмом, перемещающим изделия, является вращающийся на вертикальном валу диск. Подразделяются дисковые транспортеры на центробежные, фрикционные и с гнездами.
Вцентробежных дисковых транспортерах изделия 1 (рис.5.4в)
подаются обычно по лотку 2 в среднюю зону поверхности быстро вращающегося на валу 3 диска 4 и далее под действием центробежных сил смещаются по ее конической поверхности к кольцевому наружному буртику 5,
азатем систематизированным потоком за счет силы трения направляются с диска по отводящему транспортеру 6 в исполнительные механизмы технологических машин.
Вфрикционных дисковых транспортерах изделия 1 (рис.5.4г),
поступающие из конвейера 2, удерживаются за счет силы трения на поверхности вращающегося диска 3 и перемещаются им без смещений по круговой траектории, а затем передаются на отводящий транспортер 4, движущийся в требуемом направлении.
Таким образом, подаваемые изделия могут перемещаться по поверхности вращающегося диска или оставаться на ней неподвижными. Все зависит от соотношения действующих на них сил трения и инерции. В частности, изделие будет перемещаться по поверхности вращающегося диска в том случае, если выполняется следующее условие:
G |
r |
2 cos f |
|
sin G sin f |
|
cos 0 |
(5.6) |
|
д |
д |
|||||
g |
0 |
|
|
|
|||
|
|
|
|
|
|
|
где G – вес изделия, Н;
g – ускорение свободного падения, м/с2;
r0 – расстояние от центра вращения диска до центра тяжести, находящегося на нем изделия, м;
fд – коэффициент трения изделия о поверхность диска; ω – угловая скорость вращения диска, с-1;
74
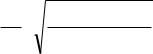
γ – угол наклона конической поверхности диска, град.
Если же левая часть неравенства отрицательная – то изделие не будет перемещаться по поверхности вращающегося диска, что характерно для фрикционных дисковых транспортеров.
При известных конструктивных размерах диска, таких как r0 и γ, частоту вращения, обеспечивающую перемещение изделий по его поверхности, можно вычислить по формуле:
n |
|
|
|
30 |
|||
|
|
g tg |
д |
|
|
r |
|
0 |
|
, об/мин. |
(5.7) |
где ρд – угол трения между изделием и поверхностью диска, град.
Если поверхность диска в диаметральном сечении имеет обратную конусность (наклонена к оси), то в подкоренном выражении данной формулы вместо знака «минус» ставится знак «плюс».
Круговые транспортеры, у которых по периметру рабочих дисков 1 (рис.5.4д) располагаются с определенным шагом гнезда 2 различного вида (профильные, карманчиковые, щелевые) обеспечивают перемещение в них изделий 3, например, из питающего лотка 4 на отводящий конвейер 5 не только в зафиксированном положении, но и с заданным шагом независимо от частоты вращения диска. В этом и заключается главное отличие транспортеров с гнездами в диске от аналогичных центробежных и фрикционных круговых транспортеров.
5.5. Транспортеры возвратно-поступательного действия
Транспортеры возвратно-поступательного действия применяются для периодического шагового перемещения непосредственно изделий или изделий находящихся в приспособлениях-спутниках от одной позиции к другой с помощью рабочих органов, совершающих в пространстве возвратнопоступательные движения. По особенностям конструктивного исполнения они подразделяются на штанговые (с поворотными и клавишными толкателями) и грейферные.
Штанговые транспортеры с поворотными толкателями состоят из опорной плоской поверхности 1 (рис.5.5а) на которой располагаются изделия 2, периодически продвигаемые вперед на заданный шаг толкателями 3, опирающимися на упоры 4 и шарнирно закрепленными на штанге 5, движущейся от кривошипно-шатунного привода 6. При обратном же ходе штанги 5 шарнирные толкатели 3 от взаимодействия с изделиями отклоняются вниз и проходят под ними, а затем под действием своих противовесов снова возвращаются в исходное вертикальное положение и цикл повторяется. Транспортеры с клавишными толкателями состоят из опорной плоской поверхности 1 (рис.5.5б) на которой располагаются изделия 2, периодически продвигаемые вперед на заданный шаг парными толкателями 3, шарнирно закрепленными на параллельных штангах 4 и удерживаемыми в рабочем положении пружинами 5. При обратном же ходе штанг 4 толкатели 3 от взаимодействия с неподвижными изделиями 2 расходятся, сжимая пружины 5, а затем возвращаются ими в исходное рабочее положение и цикл повторяется.
75

Рис.5.5. Конструктивные исполнения транспортеров возвратнопоступательного действия
Вгрейферных транспортерах рабочими органами являются совершающие возвратно-поступательные движения грейферные линейки, которыми изделия перемещаются в шаговом режиме с одной позиции на другую с их захватом (клещами или зажимными колодками) или без захвата (например, полуоткрытыми трафаретами). В зависимости от решаемой задачи грейферные линейки у таких транспортеров могут совершать одно-, двух- и трехкоординатные цикловые движения.
Воднокоординатных транспортерах грейферные линейки совершают только продольное цикловое возвратно-поступательное движение с продвижением изделий, например, клавишными захватами, аналогичными приведенным на рис. 5.5б.
Вдвухкоординатных транспортерах грейферные линейки совершают вертикальное или встречное горизонтальное движения для захвата изделий, далее продольное движение, для шагового перемещения изделий с позиции на позицию, и, завершая цикл, возвращаются в исходное положение. В частности, шаговое перемещение, например, сортового проката 1 (рис.5.5в) различных сечений и других изделий с их подачей на приемную позицию 2 обеспечивается двухкоординатным грейферным транспортером, содержащим несколько параллельных опорных зубчатых реек 3, сопрягающихся с магазином 4, между которыми аналогичные зубчатые грейферные линейки 5 совершают цикловые качательно-поступательные движения от кривошипных механизмов 6, установленных на приводах 7. В процессе вращения кривошипных механизмов 6 грейферные линейки 5 при вертикальном подъеме забирают с опорные реек 3 изделия 1 и последующим продольным ходом переносят на шаг вперед, а затем опускаются и возвращаются в исходное положение. При этом первое изделие укладывается на приемную позицию 2, а в освободившуюся выемку последних зубьев реек 3 из магазина 4 соскальзывает очередное изделие. После укладки по наклонным поверхностям неподвижных реек 3 изделия 1 соскальзывают к вертикальным опорным частям зубьев и точно позиционируются по ним для выполнения следующего цикла.
Для взятия же изделий 1 (рис.5.5г) механическими захватами 2, грейферные линейки 3 в двухкоординатных транспортерах совершают вначале встречное горизонтальное движение, а затем продольным движением вперед
76

продвигают их на шаг по плоской опорной поверхности 4. После этого грейферные линейки 3 расходятся и обратным продольным движением возвращаются в исходное положение.
В трехкоординатных транспортерах встречным движением грейферных линеек 1 (рис.5.5д) осуществляется взятие захватами 2 транспортируемых изделий, вертикальным движением – их извлечение из гнезд (трафаретов) и обратная укладка, а продольным – шаговое перемещение изделий с позиции на позицию. Трехкоординатные грейферы наиболее универсальны, поэтому их можно применять для шагового перемещения изделий практически любой формы. Поскольку транспортирующие механизмы этих транспортеров более массивные и работают от одного общего или нескольких автономных приводов, то их скорости перемещений обычно несколько ниже, чем у грейферов других типов.
Требуемое число позиций n в транспортерах возвратно-поступательного действия определяется по формуле:
n L l |
х |
|
(5.8)
где L – расстояние между осями исходной и приемной позиции, связываемых технологических объектов (машин), м;
lх – величина продольного хода штанги или грейферных линеек транспортера, м; принимается в зависимости от наибольшего размера транспортируемого изделия lи в направлении подачи из условия: lх 1,1 1,35 lи .
5.6. Транспортеры пневматические
Пневматические транспортеры эффективны и экономически оправданы для перемещения штучных изделий и сыпучей продукции, характеризующейся сравнительно небольшой плотностью материала, развитыми опорными поверхностями или значительной поверхностью обтекания. Подразделяются эти транспортеры на открытые и закрытые струйные, а также закрытые инжекторные.
В частности, струйные пневмотранспортеры открытого типа успешно применяются для перемещения на воздушной подушке изделий с низкими прочностными характеристиками (в том числе с легко повреждаемым поверхностным слоем) или с высокими фрикционными свойствами. Такой транспортер представляет собой камеру 1 (рис.5.6а) требуемой длины, в верхней стенке 2 которой, выполненной с ограничительными буртиками 3, расположены наклонные сопла 4. Сжатый воздух, вытекая из камеры через эти сопла, образует над верхней стенкой воздушную прослойку, обеспечивающую перемещение находящихся на ней изделий 5 за счет сил вязкого трения и давления, исключая истирание поверхностей, как самих изделий, так и транспортера.
Защитить от повреждений у перемещаемых изделий 5 не только нижнюю, но и верхнюю плоскость позволяет струйный пневмотранспортер закрытого типа, который отличается от предыдущего (рис.5.6а) тем, что его транспортирующий канал закрыт по всей длине верхней крышкой 6 (рис.5.6б), которая выполняется обычно из прозрачного материала. При этом шаг S между соплами транспортера и другие конструктивные параметры принимаются из
77

условия обеспечения поджима выходящих наклонных воздушных струй к транспортирующей поверхности канала за счет так называемого эффекта Коанда. Суть этого эффекта заключается в том, что к транспортирующей поверхности стенки 2 поджим выходящей из наклонного сопла 4 воздушной струи 7 происходит за счет ее эжектирующего действия, в результате которого появляется разность давлений р между областями над (ра) и под (рi) струей. Это происходит потому, что вытекающая с большой скоростью струя 7 увлекает за собой прилегающие частицы воздуха из расположенной под ней замкнутой области 8 и там образуется зона пониженного давления (рi < ра), изгибающая и притягивающая эту струю к поверхности стенки 2. В результате обеспечивается перемещение изделий 5 в воздушном потоке без соприкосновения как с поверхностью стенки 2, так и с крышкой 6 канала пневмотранспортера.
Если же изделия достаточно жесткие, то в модифицированном струйном пневмотранспортере закрытого типа (в виде трубы) можно осуществлять их перемещения при разнообразных пространственных изгибах трассы, включающей как крутонаклоненные, так и вертикальные участки. В частности, такой транспортер, перемещающий изделия 1 (рис.5.6в) между двумя станками 2, в зависимости от конфигурации трассы 3 содержит установленные определенным образом сопла 4 и 5, через которые в его канал подается сжатый воздух. При этом изделия будут ускоряться в канале транспортера струями сжатого воздуха, подаваемого через сопла 4 в направлении движения, а на выходе из канала притормаживаться встречно направленной струей, выходящей из сопла 5. Процесс же перемещения изделий 2 обеспечивается тремя последовательно сменяемыми этапами движения. На первом этапе перед соплом 4 они движутся по каналу 3 под воздействием перепада давлений, возникающего от эжектирующего (всасывающего) действия выходящей из сопла струи. На втором этапе изделия ускоряются под соплом от импульсного воздействия на них направленной воздушной струи, а затем на третьем этапе продвигаются в канале по инерции до следующего сопла.
Рис.5.6. Конструктивные исполнения транспортеров пневматических
Перемещение газообразной, жидкой, сыпучей и мелкоштучной продукции обеспечивается также транспортерами закрытого типа, содержащими пневмоструйные (инжекторные) насосы – устройства в которых осуществляется передача кинетической энергии от одной воздушной среды,
78
движущейся с большей скоростью к другой в процессе их смешивания. Например, такой пневмотранспортер, обеспечивающий загрузку гранулированного материала 1 (рис.5.6д) из технологической тары 2 в питающие бункеры технологического оборудования, состоит из всасывающего шланга 3, соединенного с пневмоструйным насосом 4, а также из присоединенных к нему питающей магистрали 5 и напорного трубопровода 6. При этом пневмомагистраль 5 через фильтр 7 и электропневмоклапан управления 8 соединяется с соплом 9 насоса (рис.6.8г), располагающимся в приемной камере 10, которая в свою очередь соединяется с всасывающим шлангом 3 через патрубок 11, а также с напорным трубопроводом 6 через соосную смесительную камеру 12 и диффузор 13. Сужающееся сопло 9 в таких насосах выполняется обычно с углом конусности в 10 – 12о (сопло Лаваля) и обеспечивает увеличение скорости поступающего из магистрали 5 воздушного потока с уменьшением давления и увеличением объема, то есть в нем потенциальная энергия воздушного (газового) потока преобразуется в кинетическую энергию. Диффузор же 13 насоса представляет собой расширяющуюся часть воздушного канала, при движении по которой увеличивается давление и уменьшается скорость воздушного (газового) потока, то есть в нем осуществляется обратный процесс – кинетическая энергия воздушного потока преобразуется в потенциальную энергию.
При работе данного пневмотранспортера в приемную камеру 10 насоса 4 из питающей магистрали 5 непрерывным потоком подается сжатый воздух, скорость которого в сужающемся сопле 9 резко возрастает со снижением давления. Этот ускоренный поток, проходя через приемную камеру 10, увлекает за собой находящийся в ней воздух, в результате чего в камере и присоединенном к ней шланге 3 создается давление ниже атмосферного. Под действием разности давлений через шланг 3 в приемную камеру 10 из технологической тары 2 засасывается гранулированный материал 1 вместе с атмосферным воздухом. Далее в смесительной камере 12 потоки, поступающие из сопла 9 и шланга 3, перемешиваются между собой и, в результате обмена количеством движения между их частицами, выравнивается скорость и давление в совмещенном потоке. Затем из смесительной камеры 12 совмещенный поток направляется в диффузор 13, где снижается его скорость и увеличивается давление, обеспечивающее нагнетание движущейся среды в присоединенный напорный трубопровод 6, по которому гранулированный материал и доставляется в движущемся воздушном потоке к месту назначения.
Таким образом, действие пневмоструйного насоса складывается из следующих трех основных последовательных процессов:
преобразования в сопле 9 потенциальной энергии рабочей воздушной среды в кинетическую, благодаря чему в приемной камере 10 и шланге 3 создается разрежение, обеспечивающее всасывание подаваемой среды;
обмена количеством движения в смесительной камере 12 между частицами воздушной рабочей и подаваемой среды, в результате чего происходит выравнивание скоростей и давлений в совмещенном потоке;
преобразования в диффузоре 13 кинетической энергии совмещенного потока в потенциальную, в результате чего обеспечивается его нагнетание в напорный трубопровод 6 транспортера.
79
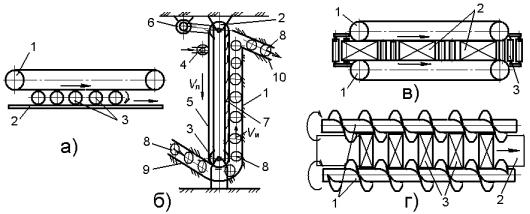
Эффективная работа пневмоструйного насоса достигается оптимизацией конструктивного исполнения его сопла, диффузора, приемной и смесительной камеры, а также адекватной регулировкой зазоров между ними. Если эти насосы предназначены для нагнетания прокачиваемой среды, то их называют инжекторными. Если же они предназначены для откачивания воздуха (газа), например, при создании вакуума в присосках пневматических захватов, то такие насосы называют эжекторными. Пневмоструйные насосы просты по устройству, надежны и долговечны в эксплуатации, однако их КПД не превышает 30 %. К недостаткам такого способа получения вакуума и транспортирования продукции можно отнести значительный расход питающего сжатого воздуха и шумность от его прохождения по каналам насоса и пневмомагистрали.
5.7.Комбинированные транспортирующие системы
Вкомбинированных транспортирующих системах рассмотренные
ранее конвейеры применяются в различных сочетаниях или совместно с другими устройствами, расширяющими их функциональные возможности. Примером таких наиболее распространенных транспортирующих систем могут служить парные ленточные фрикционные конвейеры и парные винтовые (шнековые) транспортеры, а также ленточные и винтовые конвейеры, работающие в паре с линейкой (плоскостью) и другие. В частности ленточный конвейер 1 (рис.5.7а), работающий в паре с опорной линейкой 2 или плоскостью применяется для транспортирования изделий 3 в форме тел вращения. При этом движущейся транспортерной лентой конвейера 1 изделия 3 прижимаются к опорной поверхности линейки 2 и катятся по ней в направлении подачи.
Рис.5.7. Конструктивные схемы комбинированных транспортирующих систем
Такие комбинированные конвейеры широко применяются, в частности, для вертикального подъема консервных банок или их корпусов в гравитационных транспортирующих системах автоматизированного жестебаночного производства. Они состоят из вертикальной направляющей плоскости 1 (рис.5.7б) и вертикально расположенного ленточного конвейера между ведущим 2 и ведомым 3 шкивами которого натянута с помощью поджимающего ролика 4 бесконечная прорезиненная лента 5, приводимая в движение от электродвигателя 6. При этом рабочая ветвь ленты 5 опирается на плоские пружины 7, обеспечивающие ее постоянный контакт с
80