
[SHipinsky_V.G.]_Oborudovanie_i_osnastka_upakovoch1(z-lib.org)
.pdf
ленты будет постепенно снижаться пропорционально уменьшению диаметра рулона, а усилие натяжения ленты – возрастать. Для обеспечения же постоянной скорости разматывания ленты такие рулоноразматыватели оснащают специальными системами управления приводом. В частности, наиболее простая такая система содержит петлю из разматываемой ленты, в вершине которой располагается ролик, качающийся рычаг которого связан с устройством управления частотой вращения электродвигателя. Рулоноразматыватели с горизонтальной осью вращения наиболее распространены и в зависимости от размеров и массы устанавливаемых рулонов выполняются одноопорными (консольными) (рис.7.3б) или двухопорными (рис.7.3а, в), то есть с размещением опор по обе стороны рулона. Двухстороннее размещение опор обеспечивает большую жесткость конструкции и предпочтительнее при фиксации тяжелых и широких рулонов. На опоры станины 1 (рис.7.3а) в таком рулоноразматывателе устанавливается съемный вал 2 с зафиксированным на нем рулоном 3 таким образом, чтобы разматываемый конец ленты 4 был направлен в сторону подачи и, проходя через направляющие ролики 5, образовывал петлю, в которой находится ролик 6 установленный на качающемся рычаге 7. При этом вал 2 через передаточные механизмы 8 приводится во вращение от электродвигателя 9, а второе плечо 10 качающегося рычага 7 располагается между датчиками 11 и 12, управляющими электродвигателем.
Рис.7.3. Конструктивные исполнения механизмов вращения рулонов
В процессе работы разматываемый рулон 3 вращается от электродвигателя 9 несколько быстрее линейной скорости подачи ленты 4, при этом находящийся в увеличивающейся петле ролик 6 опускается вместе с качающимся рычагом 7 вниз до тех пор, пока второе плечо 10 рычага не воздействует на датчик 12, выключающий электродвигатель. При этом размотка рулона прекращается, а подача осуществляется за счет запаса ленты, находящейся в петле. В результате этого петля уменьшается до тех пор, пока плечо 10 поднимающегося вверх рычага 7 не воздействует на датчик 11, включающий электродвигатель 9. При этом вращение рулона возобновляется, петля снова начинает увеличиваться, а в результате этого скорость принудительного вращения рулона подстраивается под скорость подачи ленты.
Одноопорные (консольные) рулоноразматыватели применяются для принудительного вращения нешироких рулонов. В них рулоны 1 (рис.7.3б)
91
фиксируются конусными втулками на горизонтальном стационарном валу 2, установленном в подшипниках на станине 3 и приводимом во вращение от электродвигателя 4 через редуктор 5. Регулирование же скорости размотки ленты обеспечивается аналогичным петлевым механизмом.
Рулоноразматыватели с вертикальной осью применяются для принудительного вращения узких рулонов при подаче разматываемой ленты в том же положении (например, в универсально-гибочные многоползунковые автоматы) или с последующим ее разворотом на 90° в горизонтальную плоскость. Данный рулоноразматыватель на своем основании 1 (рис.7.3д) содержит вращающуюся от электродвигателя планшайбу 2, на которую укладывается разматываемый рулон 3, базируемый на валу 4 планшайбы по осевому отверстию. При этом конец разматываемой ленты 5 укладывается на направляющий ролик 6, располагающийся на стойке 7, с разворотом на 90° в горизонтальную плоскость и образованием петли, в вершине которой располагается ролик 8 качающегося рычага 9. Ось же рычага 9, проходящая через стойку 7, связана с осью потенциометра 10, регулирующего частоту оборотов электродвигателя. Если в процессе подачи разматываемой ленты петля уменьшается из-за уменьшения диаметра рулона, то поднимающимся рычагом 9 ось потенциометра 10 повернется в направлении, обеспечивающем повышение оборотов электродвигателя, и соответственно увеличится скорость вращения рулона до ее синхронизации со скоростью подачи ленты в технологическое оборудование. При уменьшении скорости подачи ленты петля соответственно будет увеличиваться и опускающимся рычагом 9 ось потенциометра 10 повернется в направлении уменьшения оборотов электродвигателя, обеспечивая тем самым настройку скорости вращения рулона по скорости подачи разматываемой ленты. При невысоких скоростях подачи ленты планшайба таких рулоноразматывателей часто выполняется без базирующего вала 4 и этим упрощается установка рулонов на ее поверхность.
В рулоноразматывателях принудительное вращение зафиксированного на горизонтальной оси 1 (рис.7.3в) рулона 2 может осуществляться и приводным механизмом, контактирующим с его наружной цилиндрической поверхностью. Состоит такой приводной механизм из установленных на качающейся раме 3 двух концевых барабанов 4 и 5, охватываемых бесконечной прорезиненной лентой 6. При этом приводной барабан 4 связан с валом электродвигателя 7, а усилие контакта ленты 6 с сопрягающейся поверхностью рулона 2 задается весом качающейся рамы 3. В этих рулоноразматывателях скорость подачи ленты 8 равна скорости движения контактирующего с ней приводного элемента 6 и не зависит от изменяющегося диаметра разматываемого рулона.
Наряду с рассмотренными широко применяются и механизмы вращения, в которых рулоны фиксируются и вращаются приводными элементами, контактирующими с их наружной цилиндрической поверхностью. Эти механизмы обеспечивают размотку рулонов различных размеров, при этом они компактнее и проще предыдущих, а также удобнее в эксплуатации, так как в них не нужно устанавливать и фиксировать рулон на валу, проходящем через осевое отверстие. В станине 1 (рис.7.3г) такого рулоноразматывателя по дугообразной кривой располагаются параллельные опорные ролики 2,
92
получающие синхронное вращение через передаточные механизмы от общего электродвигателя. Рулон 3 устанавливается на эти ролики так, чтобы конец разматываемой ленты 4 был направлен через направляющий ролик 5 в сторону подачи. В процессе работы приводные ролики 2 вращают рулон 3 за счет контакта с его наружной поверхностью, обеспечивая тем самым постоянную скорость разматывания ленты, не зависящую от изменяющегося диаметра рулона. Наружная поверхность таких роликов выполняется как металлической, так и с пластмассовым или резиновым покрытием. Для предотвращения смещения всего рулона в сторону размотки такие рулоноразматыватели дополнительно оснащают не приводными прижимными роликами 6 или другими фиксирующими конструктивными элементами.
Рулоноразматыватели работают как в непрерывном режиме, так и с остановками, обусловленными циклом подачи ленты в зону обработки. Для гашения же сил инерции при остановке рулона они оснащаются, как правило, разнообразными тормозными механизмами, быстро останавливающими рулон и предотвращающими самопроизвольное распушение верхних витков ленты, что ведет к ее неравномерному натяжению при подаче и даже к спаданию витков с рулона и запутыванию. Конструктивные исполнения механизмов торможения рассматриваются в одном из последующих разделов книги.
Крутящий момент МК, обеспечивающий вращение разматываемого рулона вычисляется по формуле:
М |
К |
М |
Т |
М |
И |
|
|
|
М |
ТМ |
|
, Н∙м
(7.1)
где МТ – момент сил трения в опорных подшипниках, воспринимающих вес рулона и вращающихся с ним частей, Н ∙м;
МИ – момент, обусловленный инерцией разгоняемого рулона и вращающихся с ним частей (вала, конусных втулок и др.), Н ∙м;
МТМ – момент, создаваемый тормозным устройством, Н ∙м.
В частности, для рулоноразматывателей с двухсторонним размещением
опор (рис.7.3а, в) момент сил трения в опорных подшипниках определяется по формуле:
М |
Т |
0,5 f |
Р d |
1 |
f |
2 |
Р d |
2 |
|
, Н ∙м |
(7.2) |
|
1 |
1 |
|
2 |
|
где Р1 и Р2 – абсолютная величина нормальной реакции в опорных подшипниках от веса разматываемого рулона и вращающихся с ним частей (вала, конусных втулок и др.), Н;
f1 и f2 – коэффициенты трения в опорных подшипниках;
d1 и d2 – диаметры подшипников по поверхности трения, м.
При симметричном расположении рулона на приводном валу рулоноразматывателя и одинаковых опорных подшипниках вала, момент сил трения определяется по формуле:
МТ 0,5 g М d f , Н ∙м |
(7.3) |
где g – ускорение свободного падения, м/с2;
М – масса разматываемого рулона и вращающихся с ним частей (вала, конусных втулок и др.), кг;
d – диаметр опорного подшипника по поверхности трения, м;
93
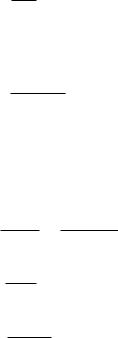
f – коэффициент трения в опорном подшипнике.
Момент, обусловленный инерцией разгоняемого рулона и вращающихся с ним частей (вала, конусных втулок и др.), определяется по формуле:
М И J J |
115 v2 |
, Н ∙м |
(7.4) |
|||
D |
2 |
|
|
|||
|
р |
Р |
|
|
||
|
|
|
|
|
где
J |
|
J |
Р |
J |
В |
|
|
|
– суммарный момент инерции рулона и вращающихся с ним
частей
J |
Р |
|
mР RР
J |
В |
|
(вала, конусных втулок и др.)
|
m |
р |
R |
2 |
r |
2 |
|
|
2 |
|
|
|
|
||||||||
|
2 |
|
Р |
Р |
|
– момент инерции разматываемого рулона, кг∙м ; |
||||
|
|
|
|
|
|
|
|
|||
– масса рулона, кг; |
|
|||||||||
и rР – радиусы рулона и его осевого отверстия соответственно, м; |
||||||||||
|
m |
|
|
R |
|
|
|
|
|
|
|
|
|
|
2 |
|
|
|
|
|
|
|
В |
В |
|
– суммарный момент инерции вала и вращающихся с ним |
||||||
|
|
|
||||||||
|
|
|
|
2 |
|
|||||
|
|
|
|
|
|
|
|
|
|
частей рулоноразматывателя, кг∙м2;
mВ – масса вала и вращающихся с ним частей (конусных втулок, колец подшипников, шкива передачи вращения и др.), кг;
RВ – радиус вала, м;
|
|
|
|
|
|
2 |
|
|
2 |
|
|
|
t |
||
|
|
|
|
2 v |
|
D |
|
|
|
Р |
|
|
|
|
115 v |
2 |
|
|||
|
|
-2 |
||||
|
|
|
|
|||
D |
2 |
|
– угловое ускорение, с ; |
|||
|
||||||
|
Р |
Р |
|
|||
|
|
|
|
– угловая скорость, с-1;
|
|
|
|
Р |
|
|
|||
|
|
|
|
|
|
t |
|
180 |
|
|
|
|
– угловой путь, пройденный радиусом за время t, рад;
t – время углового ускорения, с;
v – наибольшая скорость разматывания ленты, м/с; DР – наружный диаметр рулона, м;
αР – угол ускорения (разгона) рулона, град.
Момент, создаваемый тормозным устройством, для остановки разматываемого рулона, может быть определен по формуле:
М |
ТМ |
М |
И |
М |
Т , Н ∙м |
(7.5) |
|
|
|
где МИ – момент инерции останавливаемого рулона; может быть определен по формуле (7.4), в которой вместо угла αР ускорения (разгона) рулона, принимают угол αТ остановки (торможения) рулона.
По вычисленному значению МТМ выбирается или проектируется соответствующий тормозной механизм рулоноразматывателя.
Мощность привода рулоноразматывателя определяется по формуле:
N Д |
k |
M |
К |
|
|
|
|
|
|
, Вт |
(7.6) |
||
|
|
|
||||
|
|
|
|
|
|
где k – коэффициент запаса по мощности привода; k = 1,1 – 1,3;
МК – крутящий момент, обеспечивающий вращение разматываемого рулона, Н ∙м;
94
ω – угловая скорость разматываемого рулона, с-1;
η– общий КПД привода.
Аналогичным образом выполняются проектировочные расчеты и для
других конструктивных схем приведенных рулоноразматывателей.
7.3. Механизмы подачи ленты
Механизмы подачи обеспечивают непрерывное или пошаговое продвижение разматываемой с рулона ленты к исполнительным механизмам технологического оборудования. По месту расположения относительно рабочей зоны машины эти механизмы могут быть толкающими, тянущими и несущими ленту, а также сдвоенными (толкающее-тянущими). Механизмы подачи толкающего типа используются при поперечном безотходном раскрое ленты. Применяются они для продвижения достаточно жестких лент, не допускающих прогибов передних участков и снижения из-за этого точности шага подачи. Тянущие подачи захватывают ленту за передний край или сетку, остающуюся после вырубки из ленты изготовляемых изделий. Для их надежной работы, остающаяся от ленты сетка (отход) должна иметь достаточно прочные перемычки. Продвижение же с высокой точностью не жестких лент обеспечивается сдвоенными толкающее-тянущими подачами. Однако для достижения их синхронной работы требуется более тщательная и трудоемкая настройка. В несущих подачах удерживающие ленту конструктивные элементы (захваты) перемещаются вместе с нею через всю рабочую зону машины. Применяются такие подачи для продвижения через рабочую зону многопозиционных автоматов непрочных лент.
Механизмы подачи состоят из основных и дополнительных функциональных элементов. Последние способствуют расширению их технологических возможностей, например, облегчают заправку ленты, кинематически связывают толкающий и тянущий блоки сдвоенной подачи, контролируют наличие ленты и т. д. Основными же функциональными элементам подач являются привод, механизмы передачи движения, а так же исполнительные механизмы, непосредственно продвигающие ленту. Работа подач осуществляется как от индивидуального привода (электрического, пневматического или гидравлического), так и от кинематически связанных с ними функциональных механизмов обслуживаемой машины, например, ее основного электродвигателя или распределительного вала. В зависимости от конструкции исполнительных элементов, непосредственно продвигающих ленту, различают валковые, валково-секторные, ролико-клиновые, клещевые и несущие механизмы подачи.
Наиболее компактными и универсальными являются валковые подачи, обеспечивающие в широких пределах как непрерывное, так и пошаговое продвижение ленты, зажатой между парой вращающихся валков. Выполняются они с одним приводным и одним прижимным валками или двумя приводными синхронно вращающимися валками. По характеру движения привода и продвигающих ленту валков эти подачи подразделяются на три типа:
подачи с постоянным односторонним вращением привода и валков;
подачи с постоянным односторонним вращением привода и прерывистым вращением валков;
95

подачи |
с возвратно-поворотным движением привода и прерывистым |
вращением валков. |
|
Подачи |
с постоянным односторонним вращением привода и валков |
обеспечивают как непрерывное, так и пошаговое продвижение разматываемой с рулона ленты. В частности такая подача состоит из пары вращающихся валков, между которыми зажимается подаваемая лента 1 (рис.7.4в). При этом нижний постоянно вращающийся валок 2 связан с валом электродвигателя, а верхний валок 3, установленный на конце закрепленного в шарнире 4 коромысла 5, поджимается пружиной 6 к нижнему валку. Второе же плечо коромысла 5, несущее на себе колодку 7 фиксатора 8, сопрягается с торцевой поверхностью программного кулачка 9, связанного с приводом. Если кулачок 9 не воздействует на сопрягающееся плечо коромысла 5, то вращающимися валками 2 и 3 осуществляется непрерывное продвижение ленты 1. При вращении же с заданной скоростью программного кулачка 9, он периодически нажимает своей торцевой поверхностью большего радиуса на сопрягающееся плечо коромысла 5. При этом второе плечо коромысла 5, сжимая пружину 6, приподнимается вместе с роликом 3 и одновременно колодка 7 прижимает ленту 1 к фиксатору 8. С этого момента валок 2 начинает свободно вращаться под лентой 1, остановленной фиксатором 8. Когда же вращающийся кулачок 9 поворачивается к контактирующему плечу коромысла 5 поверхностью меньшего радиуса, то опускающимся валком 3 лента снова прижимается к вращающемуся валку 2 и продвигается ими вперед на следующий шаг. Требуемое же соотношение между периодами выстоя и шагового продвижения ленты программируется соответствующим профилем торцевой поверхности кулачка 9, а величина шага и скорость продвижения ленты 1 определяются в этой подаче скоростями вращения кулачка 9 и приводного валка 2.
Рис.7.4. Конструктивные исполнения механизмов подачи ленты
Прерывистое вращение подающих валков при постоянном одностороннем вращении привода достигается также путем применения
96
соответствующих передаточных механизмов. Таковым является, например, кулачково-цевочный редуктор фирмы Ferguson (США), кулачковый вал 1 (рис.7.4а) которого, соединенный с электродвигателем, своим винтовым пазом 2 взаимодействует с роликами 3 цевочного колеса 4, связанного с подающим валком 5. При этом продвигаемая в шаговом режиме лента 6 постоянно прижимается к подающему валку 5 свободно вращающимся валком 7 подачи. Таким образом, в этом механизме за один оборот вала 1 связанное с ним цевочное колесо 4 поворачивается с высокой точностью на угол, соответствующий шагу между его роликами 3. Требуемый же шаг в таких подачах обеспечивается за счет установки подающего валка 5 соответствующего диаметра.
Широкое распространение получили валковые подачи, привод которых осуществляется через кривошипно-рычажный передаточный механизм от постоянно вращающегося вала обслуживаемой технологической машины. Для этого на приводном валу 1 машины (рис.7.4б) крепится планшайба 2, палец 3 которой может радиально смещаться вращением винта 4. Через этот палец планшайба 2 шарнирно соединена шатуном 5 с аналогичным пальцем на корпусе роликовой обгонной муфты 6, закрепленной на конце вала приводного валка 7 в механизме подачи 8, а на втором конце этого вала установлен постоянно действующий фрикционный тормоз 9. К приводному валку 7 блоком пружин 10 прижимается такой же валок 11, связанный с ним через зубчатую передачу 12. При этом валок 11 может приподниматься вместе со своей подвижной кареткой 13 от привода 14 для заправки подаваемой ленты. При работе машины постоянное вращение планшайбы 2 через шатун 5 преобразуется во вращательно-колебательные движения корпуса обгонной муфты 6, амплитуда которых регулируется величиной смещения пальца 3 винтом 4 (эксцентриситетом). Обгонная же роликовая муфта 6 вращательноколебательные движения своего корпуса преобразует в прерывистое одностороннее вращение пары взаимосвязанных валков 7 и 11, продвигающих с заданным шагом зажатую между ними ленту. При этом фрикционный тормоз 9 гасит силы инерции и фиксирует валки при обратных ходах корпуса муфты 6. Для получения сдвоенной (толкающее-тянущей) подачи второй аналогичный валковый механизм 8 устанавливают соосно продвигаемой ленте со второй стороны машины, а корпуса их обгонных муфт 6 кинематически связывают соединительной тягой 15, обеспечивающей синхронную передачу движения. В валковых подачах с кривошипно-рычажным передаточным механизмом амплитуда вращательных колебаний корпуса обгонной муфты 6 не должна превышать 120о. В противном случае увеличиваются вибрации звеньев и динамические нагрузки в шарнирных соединениях механизма. Выполняется же это требование тогда, когда диаметр приводного валка DВ больше или равен максимальному шагу подачи ленты Lmax, то есть когда DВ Lmax .
Тяговое же усилие Тп, которое должен развивать механизм подачи для продвижения ленты без проскальзывания, определяется выражением:
Тп NЗ f z k Pmax , Н |
(7.7) |
где NЗ – сила зажатия ленты захватным органом (валками) подачи, Н;
97
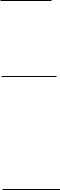
f – коэффициент трения скольжения между захватным органом (валками) и продвигаемой лентой;
z – число приводных подающих органов (валков) в подаче;
k – коэффициент запаса тянущего усилия подачи (k = 1, 2 – 1, 3); Рmax – максимальная сила сопротивления продвижению ленты, Н.
Максимальная сила сопротивления продвижению ленты определяется в свою очередь по формуле:
P |
P P |
P |
P |
|
max |
1 |
2 |
3 |
4 |
P5
, Н
(7.8)
где Р1 g m1 f1 – сила сопротивления, обусловленная трением продвигаемого участка ленты по опорной поверхности, Н;
g – ускорение свободного падения, м/с2;
m1 – масса продвигаемого участка ленты, кг;
f1 – коэффициент трения между продвигаемой лентой и опорной поверхностью;
Р |
m |
a |
– сила сопротивления, обусловленная ускорением (инерцией) |
2 |
1 |
|
продвигаемого участка ленты при подаче, Н; а – ускорение продвигаемого участка ленты в цикле подачи, м/с2;
Р |
|
J |
B |
|
B |
|
|
|
|
||||
|
|
|
|
|
||
3 |
|
|
R |
|
|
|
|
|
|
B |
|
||
|
|
|
|
|
|
– сила сопротивления, обусловленная ускорением (инерцией)
неприводного прижимного валка подачи, Н;
|
|
|
m |
|
R |
|
J |
|
|
|
|
2 |
|
|
|
В |
В |
– момент инерции неприводного прижимного валка подачи, |
||
|
|
|
|
|||
|
В |
|
|
|
2 |
|
|
|
|
|
|
|
|
кг∙м2; |
|
|
|
|
|
|
mВ – масса неприводного прижимного валка подачи, кг; RВ – радиус неприводного прижимного валка подачи, м;
Р |
|
|
g m |
2 |
– сила сопротивления, обусловленная компенсационной |
|
|
||||
|
|
|
|
||
|
4 |
|
2 cos |
||
|
|
|
|
петлей, при ее наличии между механизмом вращения рулонов и подачи ленты
(рис.7.3а, д), Н;
m2 – масса ленты, образующей компенсационную петлю и находящегося в петле ролика, кг;
φ – угол между вертикалью и линией, соединяющей нижнюю точку компенсационной петли с осью верхнего направляющего ролика, град.;
Р5 |
|
М |
К |
– сила, обусловленная сопротивлением разматываемого рулона, |
|
RР |
|||||
|
|
|
если он установлен в неприводном рулоноразматывателе, Н; МК – крутящий момент, обеспечивающий вращение разматываемого
рулона, Н∙м; вычисляется по формуле (7.1); Rp – радиус разматываемого рулона, м.
Максимальное удельное усилие прижима руд.max, обеспечивающее подачу ленты парой валков, кинематически соединенных зубчатой передачей (рис.7.4б), определяется по формуле:
98
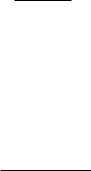
р |
|
|
k P |
|
|
|
|
max |
|||
|
|
|
|
||
|
уд.max |
|
2 |
f |
B |
|
|
|
, Н/м
(7.9)
где В – ширина продвигаемой ленты, м.
Для недопущения пластической деформации материала ленты подающими валками максимальное удельное усилие прижима руд.max должно быть меньше допустимого удельного усилия прижима [руд.], которое определяется из формулы Герца - Беляева:
|
р |
|
|
4,8 |
2 |
R |
|
|
|
|
|
|
|
|
|
|
|||
|
|
|
|
Т |
В |
, Н/м |
(7.10) |
||
|
|
|
|
|
|
||||
|
|
уд |
|
Е |
|
|
|||
|
|
|
|
|
|
|
|
||
где Т |
- предел текучести материала ленты, Н/м2; |
|
Е – модуль упругости (модуль Юнга) материала ленты, Н/м2; RВ – радиус приводного валка подачи, м.
В подачах с возвратно-поворотным движением привода в качестве преобразующих механизмов, обеспечивающих прерывистое одностороннее вращение их валков, применяются муфты свободного хода и, в частности, роликовые обгонные муфты (рис.4.13б).
Ввалково-секторных подачах прерывистое продвижение ленты осуществляется в период ее зажатия между валком и синхронно вращающимся сектором. При этом приводными могут быть как валок, так и сектор или одновременно валок и сектор. Такие механизмы подачи являются толкающими
иприменяются для продвижения достаточно жестких лент, не допускающих прогибов передних участков и снижения из-за этого точности шага подачи.
Для продвижения тонких и нежестких лент более предпочтительными являются тянущие подачи, в которых лента захватывается исполнительным органом и поступательно перемещается вместе с ним. Таковым является,
например, подающий механизм челюстного (клещевого) типа (рис.7.4г),
который захватывает своим челюстным (клещевым) зажимом 1 ленту 2 за передний торец и, двигаясь поступательно в направляющей втулке 3, протягивает на заданный шаг, а после отрезки поданного куска ленты, отпускает его и возвращается обратно в исходное положение для выполнения следующего цикла.
Вролико-клиновом механизме подачи содержатся две каретки с заклинивающимися роликовыми захватами. При этом неподвижная каретка обеспечивает фиксацию ленты, а подвижная – ее продвижение вперед на заданный шаг. В приведенном конструктивном исполнении такого механизма (рис.7.4д) неподвижная каретка 1, содержащая в своем клиновом окне пару роликов 2, установлена на корпусе пневмоцилиндра 3, а вторая подвижная каретка 4, несущая пару таких же роликов 5, закреплена на штоке 6 этого же пневмоцилиндра. Требуемый шаг подачи ленты 7, проходящей между роликами 2 и 5 кареток устанавливается с помощью регулировочного винта 8, ограничивающего обратный ход поршня 9 пневмоцилиндра. При рабочем ходе подвижной каретки 4 ее ролики 5 закатываются в сужающееся окно от трения с лентой 7 и прижимаются там к ее поверхности, обеспечивая таким заклиниванием надежный захват ленты, продвигаемой на заданный шаг вместе
99
с кареткой штоком 6 пневмоцилиндра. При этом ролики 2 в неподвижной каретке 1, выкатываясь в расширяющуюся часть окна, расклиниваются и свободно пропускают через себя протягиваемую ленту 7. При обратном же ходе подвижной каретки 4 ее ролики 5 расклиниваются и свободно пропускают через себя неподвижную ленту, которая на этот период фиксируется заклинившимися роликами 2 неподвижной каретки 1 и далее цикл повторяется. Такие подачи конструктивно просты, а в действие могут приводиться как от автономного привода, так и через передаточные механизмы от привода обслуживаемой технологической машины. Они обеспечивают относительно невысокую точность шага подачи и применяются для продвижения жестких лент, на поверхности которых допускаются следы, которые могут оставлять заклинивающие ролики кареток.
Клещевые механизмы подачи по принципу действия во многом схожи с ролико-клиновыми подачами. Только продвигаемая лента в их каретках удерживается не заклинивающимися роликами, а приводными клещевыми захватами, не оставляющими следов на поверхности ленты и более точно ее фиксирующими. Такие широко распространенные подачи можно применять для шагового продвижения более тонких лент, а также имеющих высокое качество отделки поверхностей. Точность подачи ленты этими механизмами достигает ±0,01 мм при скоростях движения до 1,33 м/с и мало зависит от величины шага подачи, обычно не превышающего 300 мм. В приведенном конструктивном исполнении такого механизма (рис.7.4е) неподвижная каретка 1, содержащая в своем окне зажимную планку 2, установлена на корпусе пневмоцилиндра 3, а вторая подвижная каретка 4, несущая такую же зажимную планку 5, закреплена на штоке 6 этого же пневмоцилиндра. Требуемый шаг подачи ленты 7, проходящей между планками 2 и 5 кареток устанавливается с помощью регулировочного винта 8, ограничивающего обратный ход поршня 9 пневмоцилиндра. При рабочем ходе подвижной каретки 4 опускающаяся планка 5 прижимает к ее поверхности ленту, обеспечивая тем самым надежный захват и продвижение ленты на заданный шаг вместе с кареткой штоком 6 пневмоцилиндра. При этом планка 2 в неподвижной каретке 1 остается приподнятой, и свободно пропускают через себя протягиваемую ленту 7. При обратном же ходе подвижной каретки 4 ее планка 5 приподнимается, и свободно пропускают через себя неподвижную ленту, которая на этот период фиксируется опускающейся вниз планкой 2 неподвижной каретки 1 и далее цикл повторяется.
Несущие механизмы подачи применяются для продвижения через рабочую зону многопозиционных автоматов гибких и непрочных (полимерных, бумажных, тканевых) лент. Удерживающие конструктивные элементы (захваты) этих подач перемещаются вместе с продвигаемой лентой через всю рабочую зону машины. Например, в многопозиционных формовочноупаковочных линиях для пошагового продвижения через их рабочую зону непрочных полимерных лент применяются несущие подачи, на двух бесконечных транспортирующих роликовых цепях которых с определенным шагом установлены захваты в виде прокалывающих ленту игл или механических зажимов. Ими подаваемый ленточный материал захватывается за края вначале несущего механизма, удерживается на протяжении всей его
100