
Формовочные материалы. Учебное пособие
.pdf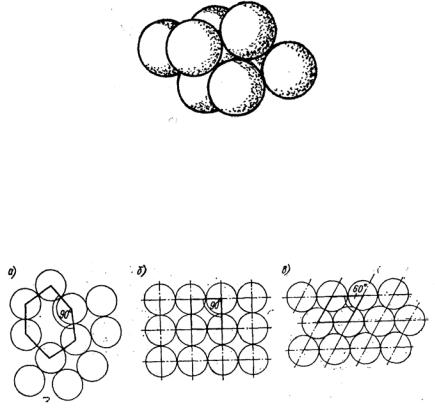
Такая модель далека от реальной формы, но дает возможность в первом приближении оценить структуру уплотненной формовочной смеси. К ней можно применить закон Пуазейля для течения жидкости в капиллярах.
Фиктивная модель смеси представляет собой набор шарообразных частиц равного диаметра (рис. 2.2).
Рис. 2.2. Структура фиктивной формовочной смеси
Эта модель ближе к реальной литейной форме. Для уяснения структуры смеси можно заменить ее моделью, состоящей из жестких сфер одинакового размера, скрепленных между собой точечными контактами через пленку связующей добавки. Расстояние между центрами любой пары соприкасающихся сфер равно их удвоенному радиусу.
Рис. 2.3. Микроструктура идеальной формовочной смеси при различных степенях уплотнения:
а – рыхлая смесь; б – кубическая упаковка; в – гексагональная упаковка
20

В неуплотненном состоянии сферы образуют рыхлую систему, в которой пористость составляет 70% (и более); в этом случае общая плотность при плотности кварцевых зерен 2,6 г/см3, будет около 1 г/см3, смежные сферы могут создавать многочисленные “арки” (рис. 2.3,а). При элементарном уплотнении сферы образуют кубическую систему. Ромбоэдр, построенный в плоскости, пересекающей центры соприкасающихся сфер, в этом случае является квадратом с углом 90о (рис. 2.3,б). При гексагональной упаковке ромбоэдр имеет острые углы 60о (рис. 2.3,в). Пористость уплотнений системы m зависит от угла ромбоэдра θ следующим образом:
m = 1 − |
π |
6(1 − cosθ) 1 + 2 cosθ . |
Расчеты показывают, что при кубической упаковке пористость составляет 0,476, а плотность смеси 1,3 г/см3; при гексагональной упаковке, соответственно, 0,259 и 1,85 г/см3. Приведенные цифры соответствуют плотности реальных формовочных смесей.
Реальная литейная форма, состоящая из зерен различной величины, имеет весьма сложную структуру. Однако благодаря упрощению структуры литейной формы удается раскрыть законы, управляющие процессами фильтрации газов и жидкостей через формовочные смеси, и дать протекающим при этом процессам количественную оценку.
Течение жидкости по капиллярам подчиняется закону Пуазейля
|
πr 4 |
t( p |
− p |
) |
|
|
Vк = |
|
1 |
2 |
|
, |
(2.1) |
|
8η l |
|
|
|||
|
|
|
|
|
|
где Vк – объем жидкости, протекающей через один капилляр; r – радиус капилляра;
t – время;
p1, p2 – давление на входе и выходе капилляра, соответственно; l – длина капилляра;
η – динамическая вязкость жидкости.
Это уравнение справедливо для капельных жидкостей, которые при постоянной температуре имеют практически неизменяемый объ-
21
ем. Для газов постоянной величиной является произведение V p. Для того, чтобы уравнение (2.1) можно было применить к газам, его левую часть следует умножить на p-давление, при котором определяется объем проходящего газа. При этом правая часть уравнения должна
быть, соответственно, умножена на |
p1 + p2 |
, т. е. на среднее давле- |
|
2 |
|||
|
|
ние, которое испытывает газ в образце. Кроме того, допускают, что капилляры расположены перпендикулярно поверхности образца и параллельно друг другу. Тогда длина капилляра l будет равна толщине образцов b. При этом формула (2.1) преобразуется
|
πr 4 |
t( p − p ) |
|
( p + p ) |
|
||
Vк p = |
|
1 |
2 |
|
1 |
2 |
, |
|
8η b |
|
|
2 |
|||
|
|
|
|
|
|
или
|
πr 4t( p − p |
) |
|
( p + p |
) |
|
|
||
Vк = |
1 |
2 |
|
|
1 |
2 |
|
. |
(2.2) |
8η b |
|
|
|
2p |
|
||||
|
|
|
|
|
|
|
|
Если исследуемый материал пронизан капиллярами в количестве N штук на 1 см2 площади поверхности f, то для получения общего расхода газа надо обе части уравнения (2.2) умножить на Nf:
|
|
πr 4 |
t N f |
( p −p |
) |
|
( p + p |
) |
|
|
Vк |
Nf = |
|
|
1 2 |
|
|
1 |
2 |
|
, |
|
8η b |
|
|
|
2p |
|
||||
|
|
|
|
|
|
|
|
|
или
|
|
πr 4N |
|
|
f t |
|
( p − p |
)( p + p |
) |
|
|
||||
Vк |
= |
|
|
|
|
|
|
|
1 |
2 |
1 |
2 |
|
, |
(2.3) |
8 |
|
η b |
|
2p |
|
|
|||||||||
|
|
|
|
|
|
|
|
|
|
||||||
где |
|
|
|
V = Vк N f. |
|
|
|
|
|
|
|||||
В уравнении (2.3) |
|
πr 4 |
N |
|
зависит от количества и размеров пор |
||||||||||
8 |
|
|
|||||||||||||
|
|
|
|
|
|
|
|
|
|
|
|
|
поэтому представляет собой некоторую величину, характеризующую данный материал, которая называется абсолютным коэффициентом проницаемости
G = |
η b |
|
|
V |
|
|
|
2p |
|
. |
(2.4) |
|
f t |
( p |
− p |
) |
( p |
+ p |
) |
||||||
|
|
|
|
|
||||||||
|
|
|
1 |
2 |
|
|
1 |
2 |
|
|
|
22
При малых перепадах давлений формулу (2.4) можно упростить
|
G = |
η b |
|
V |
, |
(2.5) |
|
f t |
p |
||||
|
|
|
|
|
||
где |
p = p1 – p2. |
|
|
В системе СИ единицей G является квадратный метр.
Формула для определения абсолютного коэффициента проницаемости выведена с условием фильтрации жидкостей как практически несжимаемых сред. При фильтрации газа значения V в формуле (2.5) следует заменить на средний объем газа Vср. Но так как
|
Vср pср = V2 p2, а |
p |
= |
p1 + p2 |
, |
||
|
|
||||||
|
|
|
– р |
2 |
|
||
|
|
|
|
|
|||
то |
G = |
2η V– р b |
|
. |
(2.6) |
||
f t( p2 |
− p2) |
||||||
|
|
1 |
2 |
|
|
|
|
Анализируя формулу (2.5), можно сделать следующие выводы.
Чем больше площадь поперечного сечения образца, необходимая для прохождения данного газа объемом V в данный промежуток времени t с данным перепадом давлений p, тем меньше абсолютный коэффициент проницаемости смеси. С уменьшением продолжительности прохождения газа объемом V через образец увеличивается абсолютный коэффициент проницаемости формовочной смеси. Увеличение высоты образца является одной из причин, препятствующих прохождению газа. Чем меньше высота образца, которая требуется для прохождения газа объемом V в данный промежуток времени t, тем ниже абсолютный коэффициент проницаемости смеси (сопротивление прохождению газов). Чем выше допустимая вязкость газа η, обеспечивающая прохождение его объема V через образец в течение времени t, тем больше абсолютный коэффициент проницаемости смеси. Последний не зависит от размеров образца и определяется только внутренней структурой материала. Так, например, при изменении величины b в формуле (2.5) абсолютный коэффициент проницаемости смеси G не меняется, а изменяются продолжительность прохождения газа t и разность давлений p.
Реальная формовочная смесь отличается от фиктивной следующими основными особенностями:
23

−частицы реальной смеси имеют различную крупность и отличаются по форме от сфер;
−частицы уплотненной смеси соприкасаются между собой не в точках, а на площадках;
−различные элементарные ячейки в пределах одного микроскопического объема формовочной смеси с той или иной степенью уплотнения имеют различную укладку частиц.
Абсолютный коэффициент проницаемости G обычно указывается применительно к определенному газу или жидкости (воздух, газ, вода). В этом случае из формулы (2.5) исключается вязкость, и такой параметр получает наименование коэффициента проницаемости, соответствующего тому газу или той жидкости, которые пропускаются через образец. Например, коэффициент воздухопроницаемости
K = |
V b |
. |
(2.7) |
|
|||
|
f p t |
|
Эта формула строго теоретически может быть применима лишь при ламинарном течении жидкости или газа через образец. В литейном производстве обычно пользуются термином “газопроницаемость формовочных смесей”. Под газопроницаемостью формовочной смеси подразумевается ее способность пропускать через имеющиеся поры воздух, газы и пары воды. Если p выразить в Н/м2, то единицей газопроницаемости будет м4/Н с.
Если давление на выходе принять равным единице, то газопроницаемость смеси
V b |
|
K = f p t . |
(2.8) |
3. Исходные материалы
24
Основной составляющей формовочных и стержневых смесей, применяемых в литейном производстве, является кварцевый песок. Кварцевый песок – природный минерал соединения кремния с кислородом (SiO2).
Пески образуются при разрушении горных пород, содержащих кварц. По происхождению формовочные пески относятся к осадочным горным породам. Важнейшей их характеристикой является время отложения и кратность переноса. Наиболее округлые и однородные по величине зерна имеют те пески, которые в течение длительного времени подвергались многократным переносам и повторным отложениям. Главным критерием при оценке качества формовочных песков по химическому составу является содержание в нем кремнезема SiО2. Чем выше его содержание, тем выше качество песка. Наряду с кремнеземом в формовочных песках почти всегда присутствуют различные примеси, ухудшающие его свойства.
3.1.Минералогический состав формовочных песков
Основной составляющей формовочного песка является кварц (SiO2), имеющий плотность ρ = 2650 кг/м3, температуру плавления tпл = 1713оС, твердость по шкале Маоса 7. Зерна кварца могут иметь различную окраску, обусловленную различными примесями. При нагреве кварц претерпевает ряд превращений. При 573оС α-кварц переходит в β-кварц. Объем изменяется ±2,4%; при 870оС β-кварц → β- тридимид, изменение объема 15,1%, при 1470оС β-тридимид → β-кристаболит, изменение объема 4,7%; при 1713оС β-кристаболит
→расплав, изменение объема 0,1%.
Полевые шпаты (MeO·Al2O3·6SiO2).
Полевые шпаты имеют твердость (6–6,5); температура плавления их 1170–1550оС, термическое расширение при 1000оС до 2,75%.
Слюда. Мусковит (К2О·3Al2O3·6SiO2·H2O).
Биотит (К2О·6(Mg,Fe)О·Al2O3·6SiO2·2H2O).
Температура плавления слюды 1150–1400оС, термическое расширение при 1000оС – 1,55%. Слюда ухудшает огнеупорность песка.
Оксиды железа содержат примеси:
25
−гематит Fe2O3, плотность 5000–5300 кг/м3, температура плавления 1560оС, устойчив при окислении;
−магнитный железняк FeO·Fe2O3; плотность 4900–5200 кг/м3, температура плавления 1540оС;
−ильменит FeO·TiO2, плотность 4720 кг/м3.
Гидраты оксидов железа nFe2O3·mH2O.
В зависимости от содержания воды различают несколько разновидностей гидратов оксида железа, которые неустойчивы и при нагревании теряют воду, снижая свойства песка, и способствуют образованию легкоплавких силикатных сплавов, вызывающих пригар на отливках.
Карбонаты: кальцит CaCO3, магнезит MgCO3, доломит CaCO3·MgCO3, сидерит FeCO3 снижают огнеупорность формовочных песков, а разложение их при нагревании до 500–900°С способствует образованию различных дефектов в отливках.
Глинистые минералы. В формовочных песках встречается несколько глинистых минералов: каолинит, монтмориллонит, гидрослюды.
Все примеси в формовочных песках снижают его огнеупорность, физико-механические и технологические свойства, увеличивают пригар на отливках.
Всвязи с этим в последнее время все больше применяют обогащенные формовочные пески с минимальным содержанием примесей.
3.2.Классификация формовочных песков
Всоответствии с ГОСТ 2138–91 все формовочные пески, в зависимости от массовой доли глинистой составляющей (частиц глинистых материалов и обломков зерен кварца и других минералов размером менее 0,02 мм), подразделяют на кварцевые (К), тощие (Т) и жирные (Ж).
Кварцевые и тощие формовочные пески подразделяют на группы в зависимости от массовой доли глинистой составляющей, диоксида кремния, коэффициента однородности и среднего размера зерен,
26
жирные – от предела прочности при сжатии во влажном состоянии и среднего размера зерна.
Кварцевые пески (табл. 3.1–3.4) содержат до 2,0% глинистой составляющей.
Таблица 3.1
Массовая доля глинистой составляющей в кварцевых песках
|
Массовая доля |
|
Группа |
глинистой |
|
составляющей, |
||
|
||
|
%, не более |
|
|
|
|
1 |
0,2 |
|
2 |
0,5 |
|
3 |
1,0 |
|
4 |
1,5 |
|
5 |
2,0 |
|
|
|
Таблица 3.3
Коэффициент однородности формовочных песков
Группа |
Коэффициент однород- |
|
ности, % |
О1 |
Св. 80,0 |
О2 |
От 70,0 до 80,0 |
О3 |
>> 60,0 >> 70,0 |
О4 |
>> 50,0 >> 60,0 |
О5 |
До 50,0 |
Таблица 3.2
|
Массовая доля SiO2 |
||
|
в кварцевых песках |
||
|
|
Массовая доля |
|
Группа |
диоксида кремния, |
||
%, не менее |
|||
|
|
||
|
|
|
|
К1 |
|
99,0 |
|
К2 |
|
98,0 |
|
К3 |
|
97,0 |
|
К4 |
|
95,0 |
|
К5 |
|
93,0 |
|
|
|
Таблица 3.4 |
|
|
Средний размер зерен |
||
|
формовочных песков |
||
|
|
|
|
Группа |
Средний размер |
||
зерна, мм |
|||
|
|
||
|
|
|
|
О1 |
|
До 0,14 |
|
О16 |
|
От 0,14 до 0,18 |
|
О2 |
|
>> 0,19 >> 0,23 |
|
О25 |
|
>> 0,24 >> 0,28 |
|
О3 |
|
Св. 0,28 |
|
|
|
|
Тощие пески (см. табл. 3.3–3.6) содержат от 2,0 до 12,0% глинистой составляющей.
27

Таблица 3.5
Массовая доля глинистой составляющей тощих песков
|
Массовая доля |
|
Группа |
глинистой |
|
составляющей, |
||
|
||
|
%, не более |
|
|
|
|
1 |
4,0 |
|
2 |
8,0 |
|
3 |
12,0 |
|
|
|
Таблица 3.7
Предел прочности при сжатии во влажном состоянии
|
Предел прочности |
Группа |
при сжатии во влажном |
|
состоянии, МПа |
|
|
Ж1 |
Св. 0,08 |
Ж2 |
От 0,05 до 0,08 |
Ж3 |
До 0,05 |
Таблица 3.6
|
Массовая доля SiO2 |
|
|
|
тощих песков |
|
|
Массовая доля |
|
|
|
Группа |
|
диоксида кремния, |
|
%, не менее |
|
|
|
|
|
|
96,0 |
Т1 |
|
|
Т2 |
|
93,0 |
Т3 |
|
90,0 |
|
|
|
Жирные пески (см. табл. 3.4 и 3.7) содержат от 12,0 до 50,0% глинистой составляющей. Обозначение марок кварцевых и тощих песков состоит из обозначений групп по массовой доле глинистой составляющей, массовой доле диоксида кремния, коэффициенту однородности и среднему размеру зерна.
Пример: 2К1О302 – кварцевый формовочный песок с массовой долей глинистой составляющей от 0,2 до 0,5% (см. табл. 3.1), массовой долей диоксида кремния не менее 99,0% (см. табл. 3.2), коэффициентом однородности от 60,0 до 70,0% и средним размером зерна от 0,19
до 0,23% (см. табл. 3.4).
Обозначение марок жирных песков состоит из обозначений групп по пределу прочности при сжатии во влажном состоянии и среднему размеру зерна.
Пример: Ж2О16 – жирный формовочный песок с пределом прочности при сжатии во влажном состоянии от 0,05 до 0,08 МПа (см. табл. 3.7) и средним размером зерна от 0,14 до 0,18 мм
(табл. 3.4).
28
3.3.Технологические требования
кформовочным пескам
По массовой доле влаги, концентрации водородных ионов водной вытяжки (pH), массовой доле вредных примесей и форме зерен кварцевые пески подразделяют на группы, указанные в табл. 3.8 – 3.10.
Коэффициент угловатости определяет степень отклонения формы зерен от сферической, выражается отношением теоретической удельной поверхности к действительной. Теоретическую удельную поверхность песков (м2/кг) определяют по данным ситового анализа на основе предположения, что все зерна имеют круглую форму.
Действительная удельная поверхность является важной характеристикой многих формовочных материалов, дающей возможность определить коэффициент угловатости, а также иметь представление о дисперсности материала, что в случае сухих связующих, например, цемента, определяет их активность, расход воды и жидких связующих для получения оптимальных свойств смесей.
|
|
|
|
|
|
|
Таблица 3.8 |
||
|
|
Массовая доля влаги кварцевых песков |
|||||||
|
|
|
|
|
|
|
|
|
|
|
|
Группа |
|
Массовая доля влаги, |
|
pH |
|
|
|
|
|
|
%, не менее |
|
|
|
|||
|
|
|
|
|
|
|
|
|
|
|
|
|
|
|
|
|
|
|
|
|
|
Сухие |
|
0,5 |
|
– |
|
|
|
|
|
Влажные |
|
4,0 |
|
|
|
||
|
|
Сырые |
|
6,0 |
|
|
|
|
|
|
|
Кислые |
|
|
|
До 6,2 |
|
|
|
|
Нейтральные |
|
– |
|
От 6,2 до 7,0 |
|
|
||
|
Щелочные |
|
|
|
Св. 7 |
|
|
||
|
|
|
|
|
|
|
|
Таблица 3.9 |
|
|
Массовая доля вредных примесей кварцевых песков |
||||||||
|
|
|
|
|
|
|
|||
Группа |
|
|
|
Массовая доля вредных примесей, %, не более |
|
||||
|
|
|
|
|
|
|
|||
Содержание |
|
|
Оксиды щелочных |
|
Оксиды железа (III) |
|
|||
примесей |
|
и щелочноземельных металлов |
|
(Fe2O3) |
|
||||
|
|
|
|
(Na2О, К2О, СаО, MgO) |
|
|
|
|
|
Очень низкое |
|
0,40 |
|
0,20 |
|
|
|||
Низкое |
|
|
0,80 |
|
0,40 |
|
|
||
Среднее |
|
|
1,20 |
|
0,60 |
|
|
||
Высокое |
|
|
1,60 |
|
0,80 |
|
|
||
Очень высокое |
|
2,00 |
|
1,00 |
|
|
29