
Формовочные материалы. Учебное пособие
.pdfопасных (по токсичности) веществ. Используется преимущественно в составах смесей по СО2-процессу после дополнительного концентрирования до содержания активного вещества 60–65% на сухой продукт. Позволяет уменьшить содержание жидкого стекла до 3–4 мас. ч. на 100 мас. ч. песка. Возможно использование ХТС с жидкими отвердителями.
7. Подготовка исходных материалов
Исходные формовочные материалы, применяемые в качестве компонентов смесей, перед использованием подвергают соответствующей подготовке. Формовочный песок сушат, а затем просеивают. Температуру сушки определяют исходя из содержания в песке глинистой составляющей. Для песков, в которых содержание глинистых составляющих более 10%, температура сушки не должна превышать
100

250–300°С. Пески с меньшим содержанием глинистой составляющей сушат при температуре 500°С. Сушку песка осуществляют в горизонтальных барабанных сушилах.
Рис. 7.1. Схема горизонтального барабанного сушила:
1– топка; 2 – течка для загрузки песка; 3 – дымосос; 4 – выходное отверстие; 5 – барабан; 6 – привод;
7 – винтовые насадки для распределения высушиваемого материала
Горизонтальное барабанное сушило показано на рис. 7.1. Загрузку песка в барабан 5 производят непрерывно. При вращении барабана, установленного под углом к горизонту, песок движется по наклону под действием собственной массы и распределяется внутри барабана по продольным каналам насадок 7. Высушенный песок поступает в ленточный транспортер, а после охлаждения – к месту потребления. Производительность горизонтальных барабанных сушил в зависимости от модели составляет до 45 т песка в час.
Схема установки для сушки песка в «кипящем» слое приведена на рис. 7.2.
101

Рис. 7.2. Схема установки для сушки и охлаждения песка в «кипящем» слое:
1 – сушильная камера; 2 – приемная воронка; 3 – транспортер; 4 – течка; 5 – газораспределительная решетка; 6 – топка; 7 – трубопровод;
8 – шибер; 9 – трубопровод; 10 – вентилятор; 11 – смесительная камера; 12 – воздухораспределительная решетка; 13 – транспортер;
14 и 16 – желоба; 15 – охладительная камера
Влажный песок по ленточному транспортеру 3, через приемную воронку 2 и течку 4 поступает в сушильную камеру 1 на газораспределительную решетку 5. Топливо подается по трубопроводу 7 и сжигается в топке 6. Из топки горячие газы поступают в смесительную камеру 11, в которой они частично охлаждаются холодным воздухом до 900–1000°С, а затем продуваются через газораспределительную решетку 5. При продувке песок переходит в состояние псевдокипения, в процессе которого зерна песка обдуваются горячими газами и трутся друг о друга, частично очищая свою поверхность от примазок других минералов. Высушенный горячий песок по желобу 16 поступает в охладительную камеру 15, в которой он повторно продувается через воздухораспределительную решетку 12, но уже холодным воздухом. К установке воздух нагнетается вентилятором 10 по трубопроводам 9. Регулирование подачи воздуха производят шиберами 8. Охлажденный песок по наклонному желобу 14 поступает на ленточный транспортер 13, а затем к месту потребления. Производитель-
102

ность установок для сушки песка в «кипящем» слое в зависимости от модели составляет от 3 до 24 т/ч.
Формовочные пески с высоким содержанием глинистой составляющей (более 10%) после сушки с целью разминания комьев подвергают дроблению с применением оборудования, предназначенного для грубого дробления формовочных материалов. К данному виду оборудования относятся щековые, валковые, молотковые и роторные дробилки.
Схема одного из видов этого оборудования – щековой дробилки – приведена на рис. 7.3. Материал, предназначенный для дробления, загружают в зазор 1, образованный подвижной 3 и неподвижной 2 щеками. Дробление кусков осуществляется с помощью эксцентрикового вала, передающего колебательное движение подвижной щеке через шатун 6, который, поднимаясь с помощью распорок 5, приближает ее к неподвижной щеке, а, опускаясь, позволяет ей под действием пружины отойти обратно. Загруженный кусковой материал при этом опускается и измельчается до величины, соответствующей наименьшему расстоянию 4 между щеками, после чего проваливается вниз. Производительность дробилок данного типа составляет до 5–6 м3/ч.
Рис. 7.3. Схема щековой дробилки:
1 – верхний зазор; 2 – неподвижная щека; 3 – подвижная щека; 4 – нижний зазор; 5 – распорки; 6 – шатун
Просеивание песка с целью отделения спекшихся комочков и мелких камней (гальки) производят с помощью полигональных барабанных сит или вибрационных установок (грохотов), имеющих размеры ячеек 3–5 мм.
103
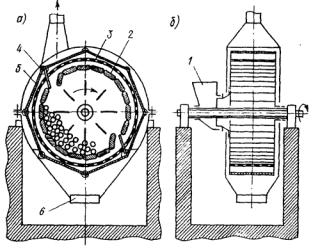
Все высокоогнеупорные наполнители формовочных смесей и противопригарных красок (хромит, хромомагнезит, магнезит и др.) должны иметь такой зерновой состав, который соответствовал бы их назначению. В противном случае их перед применением измельчают (дробят, размалывают) и просеивают. Например, хромитовые пески применяют обычно таких групп: 01, 016 и 02. Кусковой хромит подвергают измельчению в дробильно-размольных машинах: щековых и конусных дробилках, а затем в размольных вальцах или бегунах с просеиванием на ситах до получения фракции 3,2–0,5 мм. Измельчение хромита до размера зерен менее 0,06 производят в трубных мельницах.
Формовочную глину используют в сухом молотом состоянии или в виде водной суспензии. Подготовка глины заключается в следующем. Комовую глину сначала подвергают сушке в барабанных сушилках. Температура сушки обычной глины не должна превышать 200–250°С, а бентонитовой – 150–180°С. При более высоких температурах глина будет терять свою связующую способность. Дробление и размол глин обычно происходит в две стадии: грубое и тонкое дробление. Для тонкого дробления используют шаровые мельницы (рис. 7.4).
Рис. 7.4. Схема шаровой мельницы:
1 – загрузочная воронка; 2 – барабан из стальных пластин; 3, 5 – сита; 4 – лопатки для повторного сбрасывания в барабан крупных частиц; 6 – разгрузочное окно
104
В барабан вместе со стальными шарами загружают глину, которая, прошла стадию грубого дробления. Во время движения барабана шары размалывают глину, которая, проходя через решетчатые стенки, выходит наружу через разгрузочное окно. Глина, не прошедшая через решетчатые стенки барабана, специальными лопастями повторно направляется в барабан для дробления. С целью увеличения производительности шаровые мельницы оснащаются специальными проточными сепараторами, которые улучшают процесс отделения недомолотой глины для повторного размалывания. Производительность шаровых мельниц составляет до 6–7 т/ч.
Глинистую суспензию приготавливают следующим образом. Сначала комовую глину замачивают в баках с водой в соотношениях по массе 1:2 – для обычных и 1:4 – для бентонитовых глин. После истечения срока, достаточного для разбухания глины, ее размешивают в лопастном смесителе до получения однородной суспензии плотностью 1,2–1,3 г/см3. Преимуществом использования глинистой суспензии является устранение операций сушки и размалывания, сопровождающихся обильным пылевыделением.
Каменноугольную пыль приготавливают в шаровых или молотковых мельницах. Тонкость помола угля должна соответствовать фракциям 005 и 0063, сумма которых должна составлять не менее 70%. Для приготовления песчано-глинистых смесей, предназначенных для чугунного литья, используют глиняно-угольную суспензию, получаемую путем смешивания глинистой суспензии с каменноугольной пылью в соответствующих пропорциях.
Сульфитно-спиртовую бражку марки КБЖ разводят в воде до плотности (1,27÷1,30)103 кг/м3, а бражку марки КБТ сначала растворяют в котле водой (на 100 кг бражки 50 л воды), после чего подвергают нагреву. Температура нагрева не должна превышать 90°С, так как при более высокой температуре частично теряется ее связующая способность. Плотность полученной после охлаждения жидкости должна составлять (1,27÷1,30)103 кг/м3.
Помимо рассмотренных выше основных компонентов смесей (песка и глины) и способов их подготовки, в качестве основного компонента смесей широко используются также оборотная смесь и
105
регенерированный песок. Оборотную смесь получают из отработанной песчано-глинистой смеси, а регенерированный песок – из отработанных формовочных и стержневых смесей.
106
8. Формовочные и стержневые смеси
Качество и стоимость отливок в значительной степени зависят от правильного выбора состава и технологических свойств формовочных и стержневых смесей. Состав смесей зависит от назначения, рода заливаемого сплава, сложности и ответственности отливок, наличия необходимых исходных материалов, серийности производства, технологии изготовления и сборки форм и стержней, планируемой себестоимости отливок.
По роду заливаемого сплава различают смеси для стального, чугунного и цветного литья. Смеси для стального литья должны выдерживать температуру заливки сплава 1480–1540°С, для чугуна – 1380–1420°С и цветных сплавов – ниже 1200°С.
По назначению смеси разделяют на формовочные и стержневые, а также на единые, облицовочные и наполнительные. Стержневые смеси в отличие от формовочных должны обладать большей газопроницаемостью, прочностью, податливаемостью, огнеупорностью и т. д.
Единые смеси применяют главным образом при изготовлении мелких и средних форм в условиях высокомеханизированного производства. При использовании в эти смеси вводится значительное количество свежих материалов для поддержания прочности и газопроницаемости смеси в заданных пределах.
Облицовочные смеси применяются для крупных стальных и чугунных отливок в условиях серийного и единичного производства. Они наносятся вокруг модели слоем 15–20 мм и более, в зависимости от толщины стенки отливки. Для улучшения технологических свойств облицовочных смесей в них могут вводить более 50% свежих материалов. Облицовочные смеси используют в тех случаях, когда применение единых смесей дает значительный брак отливок по вине формовочной смеси.
Наполнительная смесь наносится поверх облицовочной и занимает остальной объем формы. Наполнительная смесь приготавливается из отработанной смеси с небольшой добавкой свежих материалов или без них и должна обладать высокой прочностью и газопроницаемостью.
107
Естественные смеси. В настоящее время эти смеси применяются редко для изготовления мелких отливок из чугуна и цветных сплавов. Нестабильность состава и свойств этих смесей не гарантирует получения качественных отливок. Глина, входящая в состав естественных смесей, имеет малую связующую способность и низкую огнеупорность.
Смеси, в состав которых глина входит как самостоятельная добавка, называются синтетическими. На практике широко применяют синтетические смеси в связи с высокими технологическими свойствами, простотой приготовления, легкостью поддержания постоянного состава и качества смеси.
При производстве крупных толстостенных отливок сырые песча- но-глинистые формы не могут обеспечить получения качественного литья. На отливках образуется повышенный пригар, возможна деформация формы по причине ее недостаточной прочности, интенсивный прогрев формы существенно увеличивает газотворность и вероятность образования газовых раковин в отливках. В связи с этим формы сушат либо подсушивают с поверхности газовыми горелками, что позволяет повысить поверхностную прочность формы, уменьшить её газотворную способность, снизить затраты и время на изготовление формы. Классификация смесей для изготовления форм и стержней по типу, виду и характеру твердения приведена в табл. 8.1.
|
|
|
Таблица 8.1 |
|
Классификация смесей по типу, виду и характеру твердения |
||||
|
|
|
|
|
Тип |
Вид смеси |
Категория смеси (по характеру |
Область применения смеси |
|
смеси |
|
твердения форм и стержней) |
(ориентировочная) |
|
|
|
|
|
|
Песчано- |
Пластичная |
Не подвергающаяся тверде- |
Для форм и стержней |
|
глинистая |
нию |
(средних и крупных) |
||
|
|
Теплового твердения |
||
|
|
|
||
|
|
|
|
|
|
|
Воздушного твердения |
|
|
|
Пластичная |
|
|
|
Песчано- |
Теплового твердения |
Для форм и стержней |
||
Химического твердения |
||||
|
|
|||
жидкостеколь- |
|
|
||
|
|
|
||
|
Самотвердеющая |
|
||
ная |
|
|
||
|
|
|
||
|
Жидкая |
Теплового твердения |
Для крупных форм и |
|
|
|
стержней |
||
|
Самотвердеющая |
|||
|
|
|
|
108
|
|
|
Окончание табл. 8.1 |
|
|
|
|
|
|
Тип |
Вид смеси |
Категория смеси (по характеру |
Область применения смеси |
|
смеси |
|
твердения форм и стержней) |
(ориентировочная) |
|
|
|
|
|
|
|
Сыпучая |
Теплового твердения |
Для оболочковых форм и |
|
|
|
|
стержней |
|
|
|
|
|
|
Песчано - |
|
Теплового твердения |
Для мелких стержней |
|
Пластичная |
|
|
||
|
Для мелких, средних |
|||
смоляная |
Самотвердеющая |
|||
|
и крупных стержней |
|||
|
|
|
||
|
|
|
|
|
|
Жидкая |
Теплового твердения |
Для средних стержней |
|
|
Самотвердеющая |
|||
|
|
|
||
|
|
|
|
|
|
Пластичная |
Теплового твердения |
Для мелких стержней |
|
Песчано- |
Самотвердеющая |
|
||
|
|
|||
сульфитная |
|
|
Для средних форм |
|
Жидкая |
Теплового твердения |
|||
|
||||
|
Самотвердеющая |
|
||
|
|
|
||
|
|
|
|
|
Песчано- |
Пластичная |
|
Для крупных форм и |
|
цементная |
|
Самотвердеющая |
стержней |
|
Жидкая |
||||
|
|
|
|
|
Песчано- |
|
|
Для мелких и средних |
|
масляная |
Пластичная |
Теплового твердения |
||
стержней |
||||
(стержневая) |
|
|
||
|
|
|
||
|
|
|
|
8.1. Песчано-глинистые смеси
Технология изготовления отливок в сырых песчано-глинистых формах является основной в современных автоматизированных чугуно-сталелитейных цехах крупносерийного и массового производства. Доля литья, получаемого в сырых формах, составляет, %: Японии и ФРГ – 40; Англии – 39; Франции – 29; Италии – 30; России > 60. Формовочные смеси для изготовления сырых форм имеют низкую стоимость и минимальные отходы, так как отработанные смеси легко восстанавливаются, что позволяет сократить расход формовочного песка до 0,4 т на 1 т годных отливок.
Максимальная масса отливок из чугуна, полученных в сырых формах из единых песчано-глинистых смесей, составляет 500 кг, а из стали – 400 кг. Опыт отечественных и зарубежных литейных цехов показал, что развитие технологии литья в сырые формы идет в направлении использования высокопрочных смесей с пониженной
109