
Формовочные материалы. Учебное пособие
.pdfТаблица 9.3
Состав водных противопригарных красок с органическими связующими материалами
|
|
|
|
|
Массовая доля составляющих, % |
|
|
|
|
|
|||||
|
|
|
|
|
|
|
|
|
|
|
|
|
|
|
, |
|
|
|
Наполнитель |
|
|
Связующий материал |
|
Растворитель(вода) |
|
||||||
|
|
|
|
|
|
|
|
|
|
|
|
|
|
3 |
|
|
|
Пылевидный кварц |
Циркон |
скрытоГрафиткристаллический |
кристалГрафитлический |
Тальк |
КБЖ |
Бентонит |
Декстрин |
КрепительКВ |
Патока |
Крахмалит |
КрепительДП |
/м |
|
Назначение |
Марка |
краскиПлотность 10 |
|||||||||||||
красок |
пасты |
|
|
|
|
|
|
|
|
|
|
|
|
|
кг |
|
|
|
|
|
|
|
|
|
|
|
|
|
|
|
3 |
|
|
|
|
|
|
|
|
|
|
|
|
|
|
|
|
Для стального литья |
СТ |
91–95 |
– |
– |
– |
– |
2–6 |
3 |
– |
– |
– |
– |
– |
25 |
1,40–1,45 |
|
|
|
|
|
|
|
|
|
|
|
|
|
|
|
|
Для массивного |
|
|
|
|
|
|
|
|
|
|
|
|
|
|
|
стального и |
ЦБ |
– |
92–96 |
– |
– |
– |
2–6 |
2 |
– |
– |
– |
– |
– |
16 |
1,8–2,0 |
чугунного литья |
|
|
|
|
|
|
|
|
|
|
|
|
|
|
|
|
|
|
|
|
|
|
|
|
|
|
|
|
|
|
|
Для чугунного литья |
ГП-2 |
– |
– |
84 |
– |
– |
– |
5 |
– |
5,5 |
5,5 |
– |
– |
35 |
1,3–1,35 |
|
ГП-1 |
– |
– |
89,2 |
3, 3 |
– |
3,3 |
3,1 |
– |
– |
– |
– |
1,1 |
35 |
1,28–1,30 |
|
|
|
|
|
|
|
|
|
|
|
|
|
|
|
|
Для отливок |
ТП-2 |
– |
– |
– |
– |
92,4 |
– |
1,8 |
3, 4 |
– |
– |
– |
2,4 |
36 |
1,40–1,42 |
из цветных сплавов |
ТП-1 |
– |
– |
– |
– |
92,5 |
– |
3,1 |
– |
– |
– |
1,6 |
2,8 |
35 |
1,35–1,40 |
|
|
|
|
|
|
|
|
|
|
|
|
|
|
|
|
Примечание. Для предупреждения процесса брожения в состав красок вводят формалин из расчета 40 г на 100 кг пасты. Данные составы красок приготавливаются из паст, которые поставляются централизованно.
150

Таблица 9.4
Составы водных противопригарных красок с неорганическими связующими материалами для чугунного и стального литья
|
|
|
|
Массовая доля составляющих, % |
|
|
|
|
|
|||
|
|
|
|
|
|
|
|
|
|
|
|
|
|
Наполнитель |
|
Связующий материал |
|
|
Растворитель |
|
|
||||
|
|
|
|
|
|
|
|
|
|
|
|
|
|
|
|
|
|
|
|
|
|
Водный раствор ПВС |
|
||
Наиме- |
|
|
|
Водные растворы |
|
|
или КМЦ вязкостью |
|
||||
|
|
|
|
|
|
|
|
по В 3–4, с |
Плотность |
|||
нова- |
|
|
|
|
|
|
|
|
||||
|
Дистен- |
|
|
|
|
|
|
|
|
|
краски, |
|
ние |
|
Жидкое |
|
|
|
Бен- |
|
|
|
|
||
|
|
|
|
|
|
|
|
103 кг/м3 |
||||
смеси |
Циркон |
силлима- |
стекло |
сульфата |
сульфата |
триполи- |
тонит |
Вода |
|
|
|
|
|
|
нит |
|
алюминия |
магния |
фосфата |
|
|
|
|
|
|
|
|
|
|
плот- |
плот- |
натрия |
|
|
20–22 |
35–40 |
50–55 |
|
|
|
|
|
ностью |
ностью |
плотностью |
|
|
|
|
|
|
|
|
|
|
1250 кг/м3 |
1200 кг/м3 |
1150 кг/м3 |
|
|
|
|
|
|
|
|
|
|
– |
|
|
|
|
|
|
|
|
1 |
68 |
– |
5 |
– |
– |
– |
– |
27 |
– |
– |
1,92–1,95 |
|
2 |
68 |
– |
– |
20 |
– |
– |
2 |
10 |
– |
– |
– |
1,95–2,00 |
3 |
68 |
– |
– |
– |
15 |
– |
– |
– |
– |
17 |
– |
1,90–1,95 |
4 |
– |
45 |
– |
– |
15 |
– |
– |
– |
40 |
– |
– |
1,45–1,50 |
5 |
68 |
– |
– |
– |
– |
15–20 |
– |
– |
– |
– |
12–17 |
1,90–1,95 |
|
|
|
|
|
|
|
|
|
|
|
|
|
151
Номенклатура и свойства наиболее распространенных промышленно выпускаемых водных противопригарных красок, а также рекомендации по их применению представлены в табл. 9.5.
|
|
|
|
|
Таблица 9.5 |
||
|
Номенклатура готовых противопригарных красок |
|
|
||||
|
из порошков, выпускаемых промышленностью |
|
|
||||
|
|
|
|
|
|
|
|
Марка |
|
Влажность |
Свойства разведенных красок |
Область |
|||
противо- |
|
|
|
||||
Наполнитель |
порошка, %, |
Плотность |
Вязкость |
||||
пригарной |
|
не более |
разведенной |
условная, с, |
применения |
||
краски |
|
краски, кг/м3 |
не более |
|
|
||
|
|
|
|
||||
ГС-1М |
Графит |
9,0 |
1300–1320 |
25 |
Отливки |
||
|
|
|
|
|
из |
чугу- |
|
КГС-1 |
Кварц, графит |
4,0 |
1380–1430 |
18 |
|||
на, |
цвет- |
||||||
|
|
|
|
|
|||
ТС-1М |
Тальк |
9,0 |
1460–1520 |
25 |
|||
ные спла- |
|||||||
|
|
|
|
|
|||
ТГС-1М |
Тальк, графит |
9,0 |
1340–1380 |
25 |
вы |
|
|
|
|
|
|
|
|
|
|
ДСК-1 |
Дистен- |
4,0 |
1670–1680 |
25 |
|
|
|
силлиманит |
Стальные |
||||||
ЭС-1 |
Электрокорунд |
2,0 |
1810–1910 |
22 |
отливки |
||
|
|
|
|
|
|
|
|
ЭКС-1 |
Электрокорунд |
2,0 |
1940–1980 |
25 |
|
|
|
|
|
|
|
|
|
|
Они поставляются в виде порошкообразных композиций, содержащих все необходимые компоненты (наполнитель, связующее, стабилизаторы, технологические добавки). Для получения готовых к употреблению противопригарных красок эти порошки разводят в воде до нужной консистенции.
Втабл. 9.6 приведены составы самотвердеющих водных красок, которые не требуют подсушки.
Вкачестве связующего материала в них применяют сульфитнодрожжевую бражку. В качестве окислителя связующего, который придает краске способность к самотвердению, используется добавка
персульфата аммония [(NH4)2S2O8]. Для получения требуемой плотности при оптимальном количестве воды в состав краски вводят добавку технической мочевины. В отличие от обычных водных красок,
укоторых при сушке происходит испарение воды, из данных красок вода не испаряется, а лишь химически связывается, поэтому в отдельных случаях, во избежание вскипов жидкого металла, формы и
152
стержни целесообразно подсушивать. Водные самотвердеющие покрытия применяют для окраски форм и стержней, изготовленных из самотвердеющих смесей, при стальном и чугунном литье.
|
|
|
|
|
|
|
|
|
Таблица 9.6 |
||
|
Составы самотвердеющих противопригарных красок |
|
|||||||||
|
|
|
|
|
|
|
|
|
|
|
|
|
|
Массовая доля составляющих, % |
|
|
|
||||||
|
|
|
|
|
|
|
|
|
|
|
|
|
|
Наполнитель |
|
|
Добавки |
|
|
||||
|
|
|
|
|
Связующий КБЖматериал |
|
|
|
Растворитель )вода( |
Плот- |
|
Наимено- |
Циркон |
Пылевидный кварц |
скрытоГрафит-- кристаллический |
-крисГрафит таллический |
Техническая мочевина |
цинкаОксид |
Персульфат аммония |
||||
ность |
|||||||||||
|
|
|
|
|
|
|
|
|
|||
вание |
|
|
|
|
|
|
|
|
|
||
|
|
|
|
|
|
|
|
|
краски |
||
краски |
|
|
|
|
|
|
|
|
|
||
|
|
|
|
|
|
|
|
|
103 кг/м3 |
||
|
|
|
|
|
|
|
|
|
|
|
|
Для |
72,5–73,5 |
– |
– |
– |
8,0 |
0–0,5 |
0–0,5 |
4,0 |
14–19 |
2,0–2,2 |
|
стального |
|||||||||||
50 |
22,5–23,0 |
– |
– |
8,0 |
0–0,5 |
0–0,5 |
4,0 |
14–19 |
1,8–2,0 |
||
литья |
|
|
|
|
|
|
|
|
|
|
|
Для |
– |
– |
33,0–33,5 |
16,5 |
10,0 |
10–15 |
0–0,5 |
2,5 |
25–30 |
1,35–1,40 |
|
чугунного |
|||||||||||
– |
– |
46,0–50,0 |
– |
10,0 |
10–15 |
0–0,5 |
2,5 |
25–30 |
1,35–1,40 |
||
литья |
|
|
|
|
|
|
|
|
|
|
9.2.2. Самовысыхающие противопригарные краски
Данный тип красок имеет быстроиспаряющиеся неорганические растворители, для возгонки которых нет необходимости применять сушку. Самовысыхающие покрытия применяют для форм и стержней, изготовляемых из самотвердеющих смесей.
Втабл. 9.7 приведены составы самовысыхающих противопригарных красок.
Вкачестве связующих материалов в состав красок вводят древесный пек, нитролаки 644 и 68, поливинилбутираль, причем нитролаки
иполивинилбутираль одновременно с основным своим назначением выполняют также функцию стабилизатора. В качестве растворителей в состав красок вводят этиловый спирт, уайт-спирит или растворитель 646. Краски № 1 и 2 с цирконовым наполнителем применяют при стальных отливках. Краски № 3, 4, 5 и 6 на графитовом наполнителе применяют при чугунном, а краску № 7 на тальковом наполнителе – при цветном литье.
153
Таблица 9.7
Составы самовысыхающих красок с органическими связующими материалами
|
|
|
Массовая доля составляющих, % |
|
|
|
|
|||||
|
|
|
|
|
|
|
|
|
|
|
|
|
краскиНомер |
|
Наполнитель |
|
Связующий материал |
Растворитель |
|
||||||
|
|
|
|
|
|
|
|
|
|
|
|
|
Циркон |
скрыГрафиттокристаллический |
кристалГрафитлический |
Тальк |
Древесныйпек |
Нитролак644 |
Нитролак68 |
Поливинилбутираль |
Растворитель |
спиртЭтиловый |
спиритУайт- |
Плотность, |
|
|
|
|
|
|
|
|
|
|
|
|
|
103 кг/ м3 |
|
|
|
|
|
|
|
|
|
|
|
|
|
1 |
53 |
– |
– |
– |
– |
10 |
– |
– |
37 |
– |
– |
1,80–1,90 |
2 |
60 |
– |
– |
– |
– |
– |
– |
2,5 |
– |
37,5 |
– |
1,75–1,85 |
3 |
– |
37 |
13 |
– |
– |
– |
37 |
– |
– |
– |
13 |
1,25–1,30 |
4 |
– |
30 |
12 |
– |
– |
– |
41 |
– |
17 |
– |
– |
1,25–1,28 |
5 |
– |
45 |
5 |
– |
5,5 |
– |
– |
– |
– |
44,5 |
– |
1,25–1,28 |
6 |
10 |
35 |
– |
– |
– |
– |
– |
2,5 |
– |
52,5 |
– |
1,15–1,25 |
7 |
– |
– |
– |
42 |
– |
– |
– |
2,5 |
– |
55,5 |
– |
1,75–1,85 |
|
|
|
|
|
|
|
|
|
|
|
|
|
Противопригарные самовысыхающие краски в виде готовых к употреблению суспензий на основе связующего форлака выпускаются централизованно (ТУ 4191−004−00224656−00) (табл. 9.8). Эти краски наиболее эффективны при использовании холоднотвердеющих смесей.
Таблица 9.8
Номенклатура готовых самовысыхающих противопригарных красок на основе форлака
Марка противо- |
Наполнитель |
Плотность |
Вязкость, |
Время |
Область приме- |
|
пригарной |
краски, |
с |
высыхания, |
нения |
||
краски |
|
кг/м3 |
мин, не более |
|||
|
|
|
|
|
Отливки из |
|
ПГС-1А |
Графит |
1050–1000 |
22–26 |
60 |
чугуна и цвет- |
|
|
|
|
|
|
ных сплавов |
|
|
|
|
|
|
|
|
ПДС-1А |
Дистен- |
1280–1320 |
28–32 |
60 |
Стальные |
|
силлиманит |
отливки |
|||||
|
|
|
|
|
|
|
ПТС-1А |
Тальк |
1220–1250 |
26–30 |
60 |
Отливки |
|
из чугуна |
||||||
|
|
|
|
|
||
|
|
|
|
|
|
154
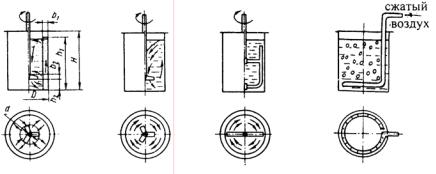
Лак представляет собой раствор модифицированного высокополимерного связующего в органическом растворителе, после испарения которого формируются прочные эластичные пленки. Растворителем лака служит растворитель антипригарных красок, состоящий из спирта этилового, ацетона и бензина-растворителя.
9.3.Приготовление противопригарных красок
Влитейных цехах для приготовления покрытий, а также при разведении централизованно поставляемых противопригарных композиций, обычно применяют краскомешалки, основные типы которых представлены на рисунке.
Наилучшее качество перемешивания обеспечивают лопастные мешалки с отражательными перегородками и частотой вращения рабочего вала 100−200 об/мин. Использование таких аппаратов позволяет существенно сократить длительность процесса приготовления покрытий.
При выборе или изготовлении мешалок рекомендуются следующие соотношения основных геометрических параметров установок
(см. рисунок, а): D/d = 1,6 ÷ 3; D/b1 = 10 ÷ 12; d/h2 = 1 ÷ 6; H/d = 1 ÷ 1,3; H/h1 = 1,2 ÷ 1,4; d/b2 = 5 ÷ 10.
а |
б |
в |
г |
Схемы основных типов краскомешалок:
а– лопастная с отражательными перегородками (n = 100÷300 об./мин);
б– лопастная (n = 60÷100 об./мин); в – рамная или якорная (n = 30÷60 об./мин);
г– краскомешалка, работающая на сжатом воздухе
155
Иногда применяют барботажные аппараты (см. рисунок, г), в которых перемешивание обеспечивается сжатым воздухом, пропускаемым через слой суспензии. Однако данный способ малоэффективен, приводит к насыщению покрытия пузырьками воздуха.
При разведении централизованно выпускаемых покрытий в мешалку следует сначала заливать воду (30−60% от ее оптимального содержания), затем отдельными порциями загружать поставляемый концентрат (пасту, порошок или гранулированный продукт). Массу перемешивают в течение 30−60 мин, выдерживают 60−120 мин, перемешивают снова 30−60 мин и добавляют воду до необходимой плотности.
Однородность полученной суспензии оценивают путем нанесения на стеклянную пластинку. На пластинке не должны присутствовать включения, выступающие над слоем покрытия. При изготовлении покрытий из отдельных компонентов рекомендуется сначала готовить жидкую композицию, т. е. раствор связующего, суспензирующего и других веществ, образующих истинные или коллоидные растворы. Рецептуру этой композиции необходимо рассчитывать таким образом, чтобы содержание в ней растворителя было на 20−30% меньше того количества, которое требуется для получения суспензии с заданной плотностью. Затем в жидкую систему вводят наполнитель, тщательно перемешивают и добавляют остальной растворитель.
При получении самовысыхающих покрытий целесообразно предварительно изготовлять жидкую композицию (лак) с содержанием растворителя, позволяющего при совмещении этой композиции с самотвердеющим количеством наполнителя создавать суспензию необходимой плотности. Такая технология обеспечивает сокращение операций, связанных с дозированием летучих растворителей, и получила распространение при использовании компонентов, для растворения которых требуется длительное время (несколько часов), например в случае применения поливинилбутираля.
Водные покрытия можно готовить в два этапа. На первом этапе осуществляется совмещение компонентов с получением пастообразной массы. Для этого используют чашечный смеситель (бегуны). На втором этапе пасту разводят водой до необходимой плотности. Обработку компонентов в бегунах целесообразно осуществлять в такой
156
последовательности: загрузка и предварительная гомогенизация – смешение сыпучих материалов и введение веществ, обладающих по- верхностно-активными свойствами (например, ЛСТ), загрузка жидких составляющих и доведение массы до пастообразного состояния.
Покрытия, изготовляемые по данной технологии, отличаются более высоким качеством, поскольку в чашечном смесителе наряду со сдвиговым обеспечивается раздавливающее воздействие, а тем самым – эффективное диспергирование.
Для получения паст можно использовать и другие типы смесителей, например, двухвальные смешивающие установки с Z-образными лопастями. Противопригарные пасты и натирки обычно готовят в смешивающих бегунах в той же последовательности, что и покрытия.
9.4. Нанесение и сушка противопригарных покрытий
Традиционными методами, широко используемыми в литейных цехах, являются окраска кистью и пневматическим распылением. В условиях массового производства широкое распространение получила технология нанесения покрытия окунанием.
На формы и стержни для тонкостенных отливок массой до 300−500 кг покрытия обычно наносят одним слоем; при производстве отливок большей массы следует применять двухразовую окраску. В последнем случае для первого слоя надо использовать покрытие с более низкой плотностью, чем для второго слоя.
При использовании традиционных покрытий одноразовая окраска обеспечивает создание слоя толщиной 300−500 мкм, а двухразовая – до 800 мкм (имеется в виду толщина отвержденного покровного слоя).
Водные покрытия, в том числе самотвердеющие, наносят кистью, распылением, окунанием; самовысыхающие – кистью. Перед окраской покрытие должно быть тщательно перемешано, при необходимости отфильтровано.
Тепловая сушка водных покрытий должна осуществляться при температуре, не вызывающей деструкцию связующего. Покрытия с
157
органическими связующими (крахмалитом, декстрином и др.) следует сушить при 200−250°С.
Для повышения эффективности сушки и предотвращения возможного перегрева покрытия (с органическим связующим) сушильные камеры надо оборудовать вентиляционными установками (вытяжной и рециркуляционной).
10. Регенерация отработанных смесей
158
Различают регенерацию песков и регенерацию смесей. При регенерации смесей стремятся к сохранению активного связующего на зернах формовочного песка, а при регенерации песков – к удалению пленок отработанного связующего с зерен песка. Регенерация смеси возможна при обратимом характере затвердевания связующего материала, что характерно для монтмориллонитовых и каолинитовых глин и применяется при литье отливок в песчано-глинистые формы.
Регенерации подвергают отработанные смеси с участков выбивки форм и стержней, в том числе из гидрокамер, а также отвальные смеси из различных точек литейного цеха. К числу основных операций процесса регенерации отработанных смесей относят: дробление комьев смеси, отделение металлических включений, отсев спекшихся комочков смеси, отделение инертных наслоений с поверхности зерен песка, удаление пылеобразных веществ и охлаждение полученного продукта до температуры окружающей среды. Основные операции процесса регенерации осуществляются как в воздушной, так и в водной среде. Помимо основных, в процессе регенерации отработанных смесей осуществляются также и побочные операции, в частности, осветление сточных вод и сгущение шлама.
Технологические схемы процессов регенерации
На рис. 10.1 приведена технологическая схема переработки пес- чано-глинистых смесей, поступающих с выбивных решеток.
Конечным продуктом по этой схеме является оборотная смесь. Из-под выбивной решетки 1 смесь поступает на ленточный конвейер 3 и далее, пройдя через магнитный сепаратор 2, транспортируется в дезинтегратор 4, где разрыхляется и передается на грохот 5 для отсева спекшихся комочков. Подготовленная таким образом смесь поступает в бункер 6, − а затем в гомогенизатор 7. В гомогенизаторе смесь сначала увлажняется, а затем поступает в испарительноохладительную установку 8, где она по температуре и влажности доводится до требуемых норм. Из охладителя смесь через элеватор 9
159