
ТСМ II
.pdf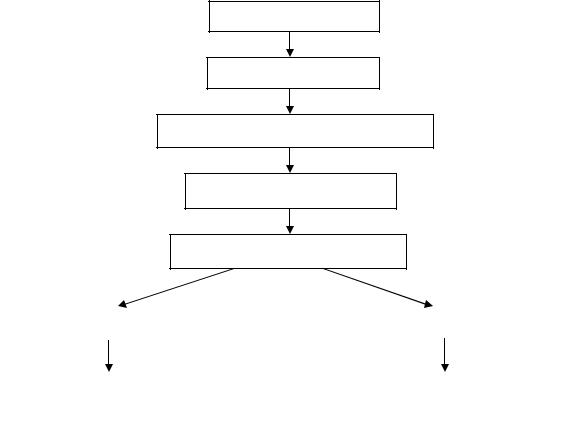
1)100-800 0С – в грануле образуются поры различных размеров, за счет удаления физической влаги и частично химически связанной воды, а также за счет частичного выгорания органических примесей;
2)800-1050 0С – в этом интервале происходит образование наружной спекшейся оболочки и дальнейшее развитие пористости. В материале развиваются твердо-фазовые реакции и происходит накопление жидкой фазы;
3)1050-1200 0С – интенсивно развиваются и завершаются процессы вспучивания, нарастает количество средних и крупных пор.
Восстановительная среда повышает вспучиваемость глин и понижает температуру их вспучивания, однако это не обуславливает необходимость вести процесс обжига с недостатком обжига для горения топлива. Важно,
чтобы COи H2,содержались не в печных газах, а в пузырьках, заполняющих поры гранул,что достигается наличием восстановительных реакций в обжигаемых гранулах.
Способы производства керамзитового гравия.
В зависимости от методов обработки глины и приготовления гранул различают 3 способа:
1)Сухой;
2)Пластичный;
3)Шликерный.
Сухой способ.
При этом способе гранулы не формуются, а образуются дроблением и рассевом карьерной глины.
Приемный бункер
Питатель
Дробилка (валково-зубчатая)
Сушильный барабан
Сортировочный грохот
|
Крупная фракция |
|
|
|
Мелкая фракция |
|
|
|
|
|
|
|
|
|
|
|
|
|
|
|
|
|
|
|
|
|
|
|
|
||
|
Обжиг во вращающейся |
|
|
Во вращающуюся печь |
|
|
|
|
печи |
|
|
(но другой режим) |
|
41 |
|
|
|
|
|
|
|
|
|
|
|
|
|
|
|
|
|
Гранулы подсушивают при карьерной влажности более 8%. Сухой способ более экономичен по капиталовложениям и эксплуатационным затратам.
Пластический способ.
При этом способе их формуют из пластичной глиняной массы. Гранулы поступающие в печь имеют влажность 12-14%. Пластический способ более сложный и дорогой чем сухой, но он допускает использование глин более распространенных разновидностей и дает возможность вводить в
глину добавки повышающие ее вспучиваемость.
42
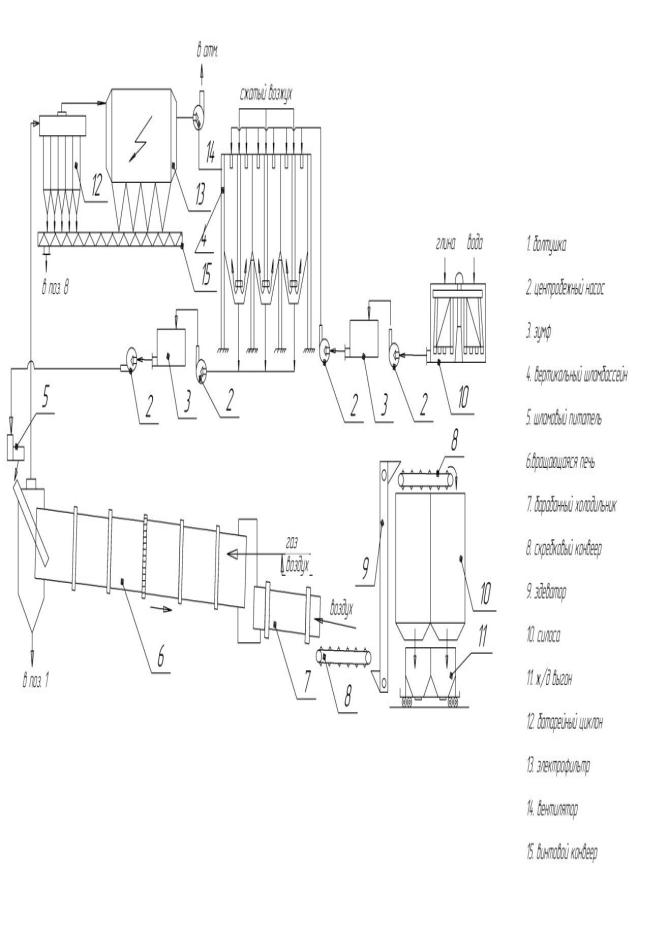
43
Шликерный способ.
Бесформовой – во вращающуюся печь подают глиняный шликер и гранулы образуются во вращающейся печи самопроизвольно, этот способ, применяют когда карьерная влажность глин выше формовочной.
Приготовленный глиняный шликер должен иметь растекаемость по прибору МХТИ-ТН-2 55-65 мм.
Этот способ является универсальным, так как позволяет использовать глины с широким диапазоном свойств, главный недостаток повышенный расход топлива и снижение производительности печи на 25-30%.
Технология тонкой керамики. Классификация изделий тонкой керамики.
По строению черепка изделия тонкой керамики подразделяются на два класса:
1)С мелкозернистым белым или равномерно окрашенным пористым и непрозрачным черепком пропускающим в неглазурованном виде воду; (полуфарфор – хозяйственные, технические; твердый фаянс – хозяйственная посуда, санитарно-технические изделия, облицовочная плитка; глинистый фаянс, известковый фаянс, шамотные фаянсовые изделия, майолика);
2)С плотным спекшимся черепком непропускающим воду и газы черепком с раковистым изломом (твердый фарфор: хозяйственный, технический, химический; мягкий фарфор: хозяйственный, художественный, костяной, тонкокаменные изделия (кислотоупорные); специальные технические керамические изделия: высокоглиноземистые, форстеритовые, корундизовые).
Сырье для изделий
Основными материалами, обеспечивающими пластические свойства тонкокерамических масс, а так же прочность сырца после сушки являются глинистые вещества: каолины и огнеупорные беложгущиеся глины.
Вкачестве отощающего сырья используют жильный кварц, кварцевые отходы, чистые кварцевые пески.
Вкачестве плавнейиспользуют калиево-натриевые полевые шпаты, пегматиты, перлит, и другие. В массы вводят для фаянса: мел, доломит, бор и фтор содержащие материалы.
Способы приготовления тонкокерамических масс.
Технологический процесс состоит:
1)Приготовление масс:
1.1) Обработка сырьевых материалов (дробление, измельчение, тонкий помол, каменистых сырьевых материалов; может быть еще и обогащение);
44
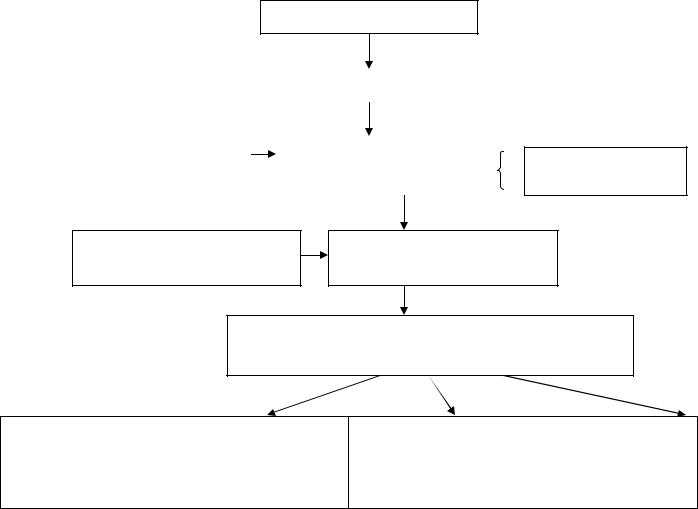
1.2) Приготовление шликера
Пластичное сырье
|
|
|
Грубое измельчение |
|
|
|
|
|
|
|
|
электролиты |
|
|
Распускание в воде |
|
|
|
(шаровые мельницы) |
|
|
||
|
|
|
|
Фаянс 65-70 Фарфор 55-60%
тонко измельченные непластичные материалы
Смешение компонентов (пропеллерная мешалка)
Очистка от крупных включений шликера (сита №008 или №016)
1.2.1. Приготовление массы для формования изделий методом водного литья в гипсовые формы
1.2.2. |
|
1.2.3. |
|
|
Приготовление |
массы |
Приготовление |
||
для |
пластического |
массы |
методом |
|
метода |
формования |
полусухого |
|
|
изделий |
|
|
прессования изделий |
45

Существует два способа приготовления |
При этом способе |
Обезвоживан |
|
|
шликера: беспрессовый и фильтр прессовый. |
шликер обезвоживают на |
ие и гранулирование |
||
При беспрессовом способе массу распускают в |
рамных фильтр-прессах. |
шликера |
|
|
воде один раз. При фильтр-прессовом способе |
Производительность |
производиться |
в |
|
массу распускают в в воде дважды. Первый раз |
фильтр-прессов до 500 |
распылительных |
|
|
шликер получают описанным выше способом, а |
кг/ч. Для фарфоровых |
сушилках. |
|
|
затем из него удаляют избыток влаги до 20-25% |
масс толщина коржа |
|
|
|
при помощи фильтр-прессования. Полученные |
около 30 мм, время |
|
|
|
из фильтр-пресса коржи разрезают на |
фильтрации 1,5-2 часа. |
|
|
|
небольшие куски (например в стругаче). |
Для фаянсовых масс 25- |
|
|
|
Измельченную массу снова загружают в |
30 мм, время фильтрации |
|
|
|
мешалку, куда предварительно добавляют воду |
2,3-3 часа. Скорость |
|
|
|
и электролиты в установленном количестве. |
фильтрации |
зависит от |
|
|
Готовый шликер сливают в сборники, а затем |
температуры, |
влажности |
|
|
подают в литейный цех. Прессовый шликер |
и рН суспензии. |
|
|
|
лучше беспрессового, т.к. вместе с водой в |
|
|
|
|
процессе фильтрации из него удаляются |
|
|
|
|
вредные соли (Na2SO4,CaSO4и др.). |
|
|
|
|
|
|
|
|
|
2)Сушка изделий
3.1) конвективная сушка. Осуществляется горячим воздухом или смесью воздуха и продуктов сгорания природного газа, а так же горячим воздухом из зоны охлаждения туннельных печей, она осуществляется в туннельных конвейерно-полочных, конвейерно-ленточных и роликовых сушилках;
3.2) конвективно-радиационная сушка. Применяется для сушки крупных изделий имеющие внутренние полости так как сушка наружных поверхностей происходит быстрее, поэтому применяют одновременно и радиационные нагреватели различных конструкций;
3.3) радиационная или инфракрасная;
3.4) акустическая;
3.5) сушка токами промышленной частоты (50Гц); 3.6) сушка токами высокой частоты (107 Гц).
4) Глазурирование изделий Применяют для придания им атмосфероустойчивости, химической
стойкости, улучшение внешнего вида.
Глазурь представляет собой стекловидное вещество, затвердевающее из расплавленного состояния на поверхности черепка в виде пленки толщиной 0,1-0,3 мм. По способу приготовления глазури бывают:
а) сырые (в них глазурный шликер приготавливают мокрым способом (помолом) и смешением нерастворившихся в воде компонентов; а сырьем для них служат поливо-шпатовые породы, CaCO3, MgCO3, каолин, глина,
46
фарфоровый бой (они нерастворимы в воде и не требуют предварительного сплавления).
б) Фритованные глазури – эти глазури предварительно сплавляют или фриттуют, для них в качестве основного сырья, кроме выше указанного, используют соли щелочныех и щелочно-земельных металлов, а так же оксиды свинца, буру и другие.
Приготовление глазурей.
Для приготовления сырых глазурей материалы природного происхождения предварительно измельчают и обогащают в соответствии с рецептурой, эти материалы смешивают с добавками и красителями и подвергают мокрому помолу в шаровых мельницах до прохождения без остатка через сито №0063.
Составные части глазурной фритты измельчают и перемешивают, а затем подвергают варке во вращающихся периодического действия или ванных печах непрерывного действия, из печи расплавления фритта по лотку сливается в гранулятор, гранулятор– это металлический резервуар наполненный водой, в дно которого вмонтирован ковшовый элеватор, для выгрузки охлажденной и сгранулированной фритты и подачи ее на конвейер к бункерам запаса. Полученная гранулированная фритта, вместе с добавками измельчается с водой в шаровой мельнице тонкого помола и в виде глазурного шликера подается для глазурования изделий.
Нанесение глазурей:
1)Погружением изделий в глазурный шликер;
2)Распылением глазурной суспензии с помощью сжатого воздуха через форсунки или с помощью дисковых центробежных распылителей;
3)Способ полива (чаще используется для полива строительной плитки), чтобы глазурь лучше прилипала к черепку(для увеличения адгезионной прочности) в него вводят клей карбомецилцелюлоза(КМЦ).
Основные характеристики глазури:
1)Температура разлива – характеризуется точкой полного плавления глазури (для простых глазурей равна 800-900 0С, для сложных
1000-11000С);
2)Вязкость глазури;
3)Поверхностное натяжение, от величины поверхностного натяжения глазури зависит заплывание наколов на глазури, углублений от всплывающих и лопнувших газовых пузырьков, а так же определяет растекание глазури по изделию;
4)Смачивающая способность – смачиваемость керамического черепка зависит от состава глазури от природы смачиваемой поверхности;
47
5) Термический коэффициент линейного расширения – представляет собой относительное удлинение материала при нагревании на 1 градус, он должен соответствовать или быть близким ТКЛР керамического черепка.
Пороки глазурного покрытия.
1)Цек глазури – сетка мелких волостных трещин. Причина: несоответствие ТКЛР глазури и черепка, т. е. у глазури больше чем у черепка;
2)Отслаивание глазури – возникает когда ТКЛР глазури меньше чем у черепка;
3)Сборка – глазурь стягивается при расплаве в капельки и складки;
4)Наколы – образование на поверхности глазури точечных впадин не заполненных таковой;
5)Плохой разлив, волнистость, слабый блеск, могут появляться при низкой температуре обжига недостаточно мелком помоле при плохом приплавление фритты;
6)Сухость – тонкий слой глазури с недостаточным блеском;
7)Натеки – местные утолщения глазури, виде полос или пятен;
8)Пузыри, прыщи и вспучивание глазури, местные выпуклости на поверхности глазурного слоя с образованием под ними пустот;
9)Слипышь прилипание изделий друг к другу;
10)Засорка, мушка – прилипание к поверхности глазури частиц шамота или темные пятна на поверхности, от железистых примесей на поверхности материала.
По просвечиваемости глазури бывают: а) прозрачные; б) глухие или белые.
Глушение обусловлено наличием в глазурном слое кристаллов вызывающих сильное расслаивание и отражение света (вводят ZnO, TiO2, CaF2) или наличием границ расслоения, т. е. ликвацией в глазурном слое.
Некоторые виды керамических изделий (тонкостенные фарфоровые изделия) перед глазурованием подвергают утильному обжигу, назначением которого восновном является закрепление формы черепка, чтобы в процессе глазурования тонкостенные изделия не деформировались и не размокали.
5. Обжиг изделий.
Можно разделить на следующие стадии:
1.Досушка сырца, т. е. удаление механической влаги;
2.Нагрев сырца удаление гидратной воды, разложение углекислых
исернокислых солей;
48
3.Окислительная выдержка;
4.Восстановительная выдержка;
5.Спекание черепа, за счет образования новых кристаллических фаз и жидкой фазы;
6.Охлаждение изделий до начала затвердевания жидкой фазы, тела изделия, а затем и глазури;
7.Окончательное охлаждение изделий при затвердевшей жидкой
фазе;
6. Декарирование изделий.
При декорирование керамических изделий применяют специальные керамические краски (оксиды металлов, силикаты, шпинели, окрашенные стекла, фритты),способные при нагревание до высокой температуры создавать устойчивую окраску изделий, по характеру применения керамические краски делят:
а) подглазурные – их наносят на неглазурованный, не обожженный, или обожженный на утиль черепок который затем покрывают глазурью;
б) надглазурный – их наносят на глазурованный и обожженный черепок, затемони закрепляются (выжигаются при новом обжиге при температуре 600-900 0С).
Высокотемпературные процессы происходящие при получении фарфора.
Фарфоровый полуфабрикат поступающий на обжиг имеет следующие фазы, относительно крупные зерна кварца и полевого шпата, которые равномерно распределены в тонко зернистом глинистом веществе в температурном интервале 500-600 0С заканчивается дегидратация глинистого вещества в частности каолинита в результате чего образуется метакаолинит.
Al2O3·2SiO2·2H2O → Al2O3·2SiO2 + 2H2O
При дальнейшем нагревании полевой шпат с другими компонентами шиты образует легкоплавкие эвтектики.
Между компонентами массы протекают твердофазовые реакции, в результате которых при температуре 800-900 0C материал приобретает некоторую прочность.
Полевой шпат начинает плавиться при температуре около 1150 0C, полное плавление наступает при температуре 1250 0C. В температурном интервале 1100-1250 0Cпроисходит переход в муллит ранее образовавшегося метакаолинита (мулитизация).
3(Al2O3·2SiO2) → 3Al2O3·2SiO2 + 4SiO2
Образующие мелкие иглоподобные кристаллики первичного муллита, пронизывают массу обжигаемого материала создавая в нем армирующий каркас. Присутствующие в материале зерна кварца, в плоть до температуры 1250 0C не претерпевают изменений. При более высокой температуре
49
количество жидкой фазы заметно увеличивается, в результате ее взаимодействие с ранее образовавшимся метакаолинитом, первичным муллитом и аморфным кремнеземом. Начинается так же взаимодействие зерен кварца в жидкой фазе. В интервале температур от1250 до 1450 в материале наблюдается непрерывное увеличение муллита.
Что обусловлено:
1.Увеличением числа размеров кристаллов первичного муллита;
2.Перемещением жидкой фазы приводящим к кристаллизации из нее вторичного муллита, в этом же температурном интервале продолжается растворение зерен кварца и их превращение в кристобалит (кристобалитизация) к моменту завершения обжига фарфор состоит:
А) из жидкой фазы образующей при охлаждении стекловидную фазу; Б) муллита; В) остатков не растворившихся зерен кварца;
Г) закрытых пор (2-5 об. %).
Соотношение между фазами входящими в состав фарфора предопределяет его важнейшие свойства, от муллита и его содержания в фарфоре зависят механическая прочность термостойкость химическая стойкость нерастворившиеся зерна кварца и муллит образуют армирующий скелет препятствующий деформации изделий на завершающей стадии обжига, стекловидная фаза до 60 об.% обеспечивает просвечиваемость художественных изделий, их жаростойкость и диэлектрические свойства.
Поры несколько снижают просвечиваемость и прочность изделий, конечный состав фарфоровых изделий можно менять изменяя:
1.Состав массы;
2.Используя минерализаторы;
3.Увеличивая тонкость помола непластичного сырья;
4.Варьируя режим обжига;
Существенное значение на состав фарфора оказывает не только температурно-временной режим обжига изделий, но и создание определенной газовой среды в различных периодах обжига. По характеру газовой среды различают 3 периода обжига фарфора.
1-ый период: нагрев до 1040 0С; в печи создают окислительную среду (концентрация СO2 составляет около 10-12%). Цель окислительного периода обжига, предупредить осаждение сажистого С, образующегося при сгорании топлива в порах изделия. Однако, примеси соединений Fe, содержащиеся в массе приобретают желтоватую окраску;
2-ой период: 1040-1250 0С: создают восстановительную среду, поддерживая концентрацию СО в продуктах сгорания топлива на уровне 2- 6%. В данном периоде оксиды Fe восстанавливаются до FeOеще до закрытия пор, благодаря чему существенно повышается белизна изделия. Закисные соединения Fe (FeO) имеют голубоватую окраску;
3-ий период: 1250 0С: в печи поддерживается нейтральная газовая среда.
50