
ТСМ II
.pdfРАЗДЕЛ №12. Характеристика печных агрегатов для производства извести
1-ый тип: Шахтные печи
Достоинства:
-самая экономичная с точки зрения расхода топлива;
-высокая концентрация СО2 в отходящих газах (до 38%);
-низких расход электроэнергии;
-малый пылеунос (кусковой материал). Недостатки:
-низкое качество целевого продукта (куски крупные);
-в шахтных пересыпных печах налипание золы на продукт от горения топлива;
-непригодность для обжига рыхлых карбонатных пород (мел).
2-ой тип: Вращающаяся печь
Достоинства:
-более высокое качество извести при обжиге кусков материала;
-хорошее качество извести когда обжиг идет по мокрому способу. Недостатки:
-большая металлоемкость (3,6×110);
-большой расход электроэнергии;
-довольно значительный пылеунос.
3-ий тип: Печи кипящего слоя
Достоинства:
-более высокое качество извести за счет меньшего размера частиц, чем
увращающейся печи;
-самая высокая интенсивность процесса.
11
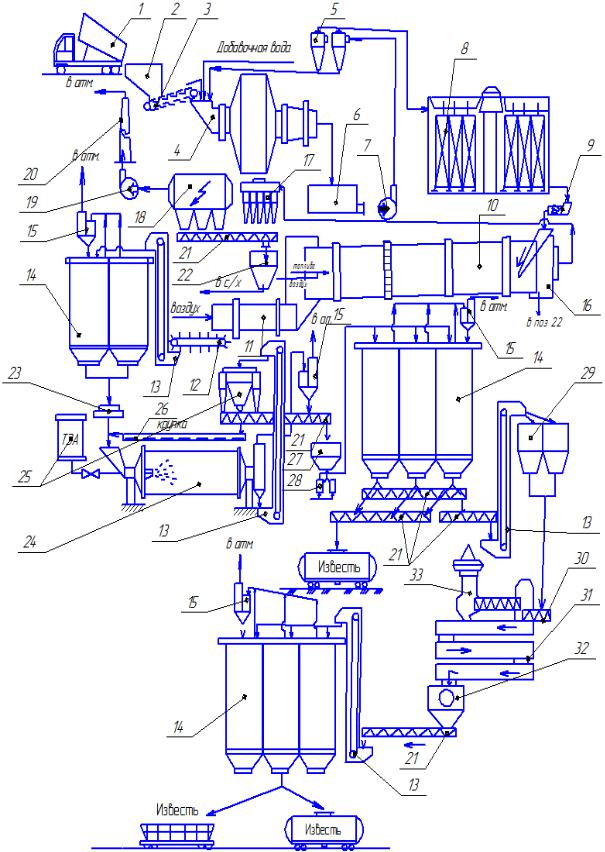
Принципиальная технологическая схема получения воздушной строительной извести по мокрому способу из переувлажненных мелов.
12
С промежуточного склада мел автомобильным транспортом (1) подается в приемный бункер (2) объемом около 20 м3, откуда пластинчатым питателем (3) загружается в полую цапфу мельницы самоизмельчения типа «ГИДРОФОЛ», одновременно добавляется вода и разжижающая смесь. Количество воды дозируется таким образом. Чтобы получить шлам с водосодержанием 38-40%. «Гидрофол», представляет собой короткий, опирающий на два цапфовых подшипника, барабан диаметром 7000 мм и длиной 2300 мм, футерованный внутри специальными броневыми плитами. Так как шлам может прокачиваться только при водосодержании около 4648%, то при снижении влажности до 40% для сохранения способности к перекачиваю добавляется 0,3-0,4% разжижающей смеси от массы шлама. Разжижающая смесь, состоящая из 50% раствора лигносульфоната технического и 50% воды, который приготавливается в указанном соотношении в специальном помещении (склад ЛСТ). Мельница самоизмельчения работает в замкнутом цикле, что позволяет предотвратить выход гальки, а также обеспечивает значительное повышение производительности по сравнению с установками открытого цикла.
Установка замкнутого цикла работает с гидроциклонами (5) следующим образом: шлам из мельницы поступает в промежуточную емкость (зумф) (6), откуда центробежным насосом (7) он транспортируется в группу циклонов (5). Благодаря классификации материала на крупные и мелкие фракции, осуществляемой в гидроциклонах, происходит выделение кондиционного шлама (верхний слив), который направляется в горизонтальный шламбассейн (8). Некондиционный шлам (нижний слив) из гидроциклонов сливается в мельницу «Гидрофол». Работа в замкнутом цикле производительность увеличивается на 50-100% и существенно снижается удельный расход электроэнергии.
Шламбассейн представляет собой железобетонную емкость диаметром 25-45 метров. В центре бассейна на железобетонной опорной колонне смонтировано поворотное основание с радиально расположенными мостами. Концы мостов опираются через ходовую тележку на кольцевой рельсовый путь, уложенный вокруг шламового бассейна. К каждому мосту подвешены грабли и донные скребки разрыхляют осадок на дне бассейна и помещают его к месту выгрузки в период ремонта или очистки шламового бассейна. Откорректированный по влажности шлам (W = 40%) подается в расходный бачек с щелевым расходомером (9) и по течке самотеком попадает во вращающуюся печь 3,6×110 метров (10).
Вращающуюся печь можно условно разделить на несколько зон: Первая зона – зона испарения. В данной зоне происходит удаление
механической влаги, находящейся в шламе. Для интенсификации процесса испарения (сушки) используются цепные завесы, которые играют роль внутренних теплообменных устройств. Они подвешиваются к корпусу печи,
13
при вращении ее на них налипает шлам, что позволяет значительно увеличить поверхность теплообмена. Влажность материала после выхода из цепной зоны должна составлять 12-14%. Именно в этом диапазоне влажности порошкообразные материалы способны гранулироваться.
Вторая зона – зона гранулирования. В данной зоне происходит грануляция материала (W = 12-14%). Эту влажность необходимо соблюдать, так как в случае продвижение материала в виде негранулированного продукта вызовет пыление и огромный пылевынос из печи. Если влажность материала 12-14% будет достигнута в середине цепной завесы, то гранулы будут разбиваться о цепи, что также вызовет повышенный пылевынос (это потеря товарного продукта и огромная нагрузка на пылеосадительные устройства).
Третья зона – зона подогрева. В этой зоне материал подогревается до температуры начала декарбонизации, т. е. до 800 0С.
Четвертая зона – зона декарбонизации. Температура обжига в заводских условиях лежит в области 1050-1200 0С, причем под температурой обжига (декарбонизации) понимают нетемпературу в печи, а температуру материала. Скорость диссоциации СаСО3 при 900 0С составляет 2 мм/ч, при 1100 0С – 14 мм/ч. Характер процессов декарбонизации карбонатных пород зависит от содержания в них примесей. При температуре 850-1100 0С образующийся СаО взаимодействует с оксидом кремния, алюминия и железа.
Количество этих фаз зависит от химического состава исходного сырья. Чем выше содержание глинистых и песчаных примесей, чем большая вероятность получения гидравлической извести.
Пятая зона – зона охлаждения. Температура материала понижается до
900 0С.
Продукт обжига выходя из печи направляется в холодильник (11). В нашем случае – это барабанный холодильник, который устанавливается под печью. Размер холодильника: длина 30 метров, диаметр 2,5 метра. Наполовину холодильник футерован шамотным кирпичом. Температура материала на входе в холодильник 850-900 0С. Выходит материал из холодильника с температурой 70-90 0С. Затем комовая известь скребковым конвейером (12) подается с помощью элеватора в силоса (14) из листовой стали, обеспыливание осуществляется рукавным фильтром (15) установленным на силосах. Уловленный продукт возвращается обратно в силоса.
Отработанные запыленные дымовые газы с температурой 250 0С, проходят трехступенчатую очистку: 1 ступень – холодная головка печи (16), 2 ступень – батарейный циклон (17), 3 ступень – электрофильтр (18). Очищенные дымовые газы с температурой около 200-250 0С хвостовым дымососом (19) через дымовую трубу (20) выбрасываются в атмосферу. Уловленная пыль, винтовым конвейером (21), подается в сборный бункер (22). Уловленный продукт некондиционный и его используют для известкования почв.
14
Получение молотой извести
Негашеная известь из силоса (14) с помощью тарельчатого питателя (23) загружается через питательную воронку в мельницу (24), имеющую следующие габаритные размеры 4×13,5 метров. Туда же из резервуара (25) через специальную установку распыления подается интенсификатор помола
– триэтаноламин, что позволяет повысить измельчение путем уменьшения налипания на мелющие тела тонкоразмолотого продукта, снижения температуры продукта, уменьшения изнашивания футеровки и мелющих тел. Мельница работает в замкнутом цикле. Размолотый продукт с помощью транспортирующих устройств (ленточных конвеейров, элеватора (13) направляется в циркуляционный сепаратор (25) с выносными циклонами. В результате классификации, осуществляемой сепаратором, материал разделяется на крупную фракцию (крупку) и готовый продукт – молотую известь. Крупная фракция по аэрожолобу (26) направляется обратно на домол в мельницу. Готовый продукт из выносных циклонов с помощью транспортирующих устройств (винтовой конвейер) направляется в приемный бункер (27), а из бункера пройдя через затвор-мигалку, известь загружается в пневмокамерный насос (28), который транспортирует ее в силоса (14). Далее отгружается потребителю.
Основные характеристики порошкообразной (молотой) негашеной извести 3-го представлены ниже:
-содержание активных CaO + MgO не менее 70 мас.%;
-время гашения не более 25 минут;
-количество непогасившихся зерен не более 11-14 мас.%;
-потери при прокаливании не более 5-7 мас.%;
-содержание СО2 не более 5-7 мас.%;
-тонкость помола при остатке на сите №02 не более 1,5%;
-тонкость помола при остатке на сите №008 не более 15%.
Производство гидратной (гашеной) извести
С помощью винтовых конвейеров и закрытого механического элеватора (13), порошкообразная известь подается в дозирующий бункер (29), откуда дозировано по шнековому конвейеру (30) загружается в трехкамерныйгидратор (31).
В верхней камере (камере предварительного гашения) осуществляется смешение порошкообразной извести с водой, количество которой отмеряется системой подачи воды и дозируется из резервуара пресной воды. Основной процесс гашения происходит в средней камере. В третьей камере (камере дополнительного гашения) Са(ОН)2 разрыхляется и перемешивается лопастями для того, чтобы остаточная влага могла улетучиваться за счет еще имеющегося тепла. Для очистки и улавливания тонко дисперсных продуктов предусмотрена камера мокрой пылеочистки (33).
15
После гашения известь дезагломерируется в стержневой мельнице (32) и с помощью механических транспортеров, элеватора подается на хранение в силоса (14).
Гидратная известь разгружается из силосов с дозировкой по объему и подается в известковозы через разгрузочное устройство с поднимаемым и опускаемым хоботом или же направляется на участок расфасовки в мешки и укладки их на поддоны.
Основные характеристики гидратной извести 2-го представлены ниже:
-активность не менее 60 мас.%;
-содержание СО не более 5 мас.%
-влажность не более 5 мас.%;
-дисперсность по остатку на сите №02 не более 1,5%; дисперсность по остатку на сите №008 не более 15%.
16
РАЗДЕЛ №13. Технология производства гидравлических вяжущих веществ
Технология производства портландцемента
Портландцемент – это гидравлическое вяжущее вещество твердеющее как в воде так и на воздухе получаемое путем совместного тонкого помола портландцементного клинкера и гипса (природный гипсовый камень), в водимого для регулирования сроков схватывания и повышения прочности. Портландцементный клинкер главный компонент цемента полученного путем высокотемпературного обжига до спекания сырьевой смеси tобжига= 1450-1500 0С, состоящей из 70-75% из карбонатного сырья и на 25-30% природного алюмосиликатного сырья (глин) и при необходимости до 5% корректирующих добавок, что обеспечивает преимущественное содержание высокоосновных и низкоосновных силикатов кальция.
Классификация цементов
По вещественному составу цементы на основе портландцементного клинкера подразделяются на 5 типов:
1)Портландцемент бездобавочный или с добавками до 5%;
2)Портландцемент с минеральными добавками до 35%;
3)Шлака-портландцемент с содержанием доменного гранулированного шлака от 36-80%;
4)Путцалановый цемент с содержание минеральных добавок от21
до50%;
5)Композиционный портландцемент с содержанием добавок 21 до
60%.
По прочности в возрасте 28 суток цемент подразделяется на марки:
300, 400, 500, 550, 600.
И классы 22,5, 32,5, 42,5, 52,5 (это предел прочности в возрасте 28 суток по европейскому стандарту EN-196-1).
Состав портландцемента
А) по оксидному составу:
CaO – 63-68 мас.%,SiO2 – 21-24мас.%; Al2O3 – 4-8%; Fe2O3 – 2- 4%;примеси: MgO, R2O (K2O + Na2O), TiO2, P2O5.
Б) по минералогическому составу:
-3СaO·SiO2 – его твердый раствор называется аллит(52-62%);
-2СaO·SiO2(двухкальцивый силикат) – беллит(15-22%);
-3СaO·Al2O3 (трехкальцивый алюминат) – (5-8%);
-4СaO·Al2O3·Fe2O3 – целит (12-15%).
17
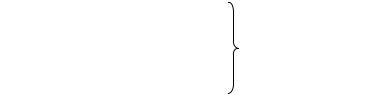
Сырьевые материалы для производства цемента
1-ая группа: карбонатное сырье (известняк(44-46% СаО), мел(44-46% СаО), мергель(40-44% СаО)):
А) мягкие, те которые размучиваются водой(мел, и некоторые мергеля);
Б) мягкие и средней твердости, не размучиваемые водой (известнякракушечник и известковый туф);
В) плотные (плотные известняки).
2-ая алюмосиликатное или глинистое (поставщик глинозема, и кремнезема и частично примесей):
А) каолинитовые;
Б) галлуазитовые; Глины В) монтмориллонитовые;
Г) гидрослюдистые.
3-ая корректирующие добавки:
- пиритные огарки, для введение оксида железа (III) (около 80% оксида).
Свойства портландцемента
1)Плотность и объемная масса:
-3-3,2 г/см3бездобавочный(ПЦ500Д-0);
-2,7-2,9г/см3добавочный(ПЦ500Д20, ШПЦ400);
объемная масса в рыхлом 900-1100 кг/м3и в уплотнонем 1400-1700 кг/м3 состоянии.
2)Водопотребность и нормальная густота.
Водопотребность цементного теста характеризуют количеством воды затворения выраженным в процентах от массы цемента, обычно эта величина 25-28% у портландцемента, и 30-35% ШПЦ и ППЦ (шлакопортландцемент и путцоланновый портландцемент).
3)Сроки схватывания определяются: конец – 10 часов, начало – не позднее 45 мин.
4)Тонкость помола.
Оценивается по остатку на сите не более 15% на сите №008, по величине удельной поверхности(2800-3000 (Беларусь), 4000 см2/г США) чем тонко измельчен тем раньше теряет свою активность.
5)Равномерность изменения объема.
Оценка равномерности изменения объема заключается в наблюдении за образцом цемента изготовленных в виде лепешек диаметром 7-8см и толщиной 1 см которые подвергли кипячению в течение 4 часов через одни
18
сутки с момента их изготовления. С чем это связано (вызывают неравномерность):
А) гидратация свободного CaO;
Б) гидратация MgO, выделившего виде периклаза;
В) образование в цементе гидросульфоалюмината кальция, за счет избытка в цементе гипса.
6)Тепловыделение при твердении.
Теплота выделяется в ходе процесса гидратации клинкерных минералов (реакции экзотермические), она зависит от минералогического состава цемента. Наибольшее тепловыделение наблюдается у C3AиС3S (3CaO·Al2O3и 3CaO·SiO2).
7)Прочность цементного камня.
Она оценивается пределом прочности при сжатии и изгибе и определяется на образцах палочках 40×40×160 мм; выполненных из цементного раствора состоящего из одной весовой части цемента и трех весовых частей стандартного песка.
Факторы, влияющие на величину прочности
1.Минералогический состав портландцементного клинкера;
2.Водоцементное отношение;
3.Тонкость помола и гранулометрический состав цемента;
4.Температура (повышение температуры до 80-900С благоприятно сказывается на увеличение темпа набора прочности);
5.Использование химических добавок;
6.Продолжительность хранения цемента перед употреблением;
7.Условия твердения;
Выбор способа производства цемента
Способ производства цемента определяется в зависимости от особенностей приготовления сырьевых смесей и по этому признаку различают 4 способа:
1.Мокрый способ (тонкое измельчение сырьевой смеси производят
вводной среде с получением шихты виде водной суспензии шлама);
2.Сухой способ (сырьевую шихту готовят виде тонко измельченного сухого порошка поэтому перед помолом или в процессе его сырьевые материалы высушивают);
3.Полусухой (после приготовления сырьевой смеси по сухому способу последняя гранулируется с добавлением 12-14% шихты и поступает виде гранул диаметром 10-15 мм на обжиг);
4.Комбинированный(сырьевую смесь готовят по мокрому способу виде шлама а затем обезвоживают на пресс-фильтре до влажности 18-20% и подают на обжиг виде полусухой массы).
19
Выбор способа приготовления сырьевой смеси определяется:
1)Свойствами сырья (однородностью и влажностью);
2)Наличие топливной базы в районе предприятия.
Сухой способ производства портландцементного клинкера
Для получения цемента по сухому способу используют короткие вращающиеся печи с эффективными запечными теплообменными устройствами (циклонными теплообменниками и декарбонизаторами), то есть печные установки такого типа состоят из вращающейся печи и системы запечных циклонных теплообменников и карбанизатора.
Таблица – Техническая характеристика печных агрегатов сухого способа производства
|
|
|
|
Вращающиеся печи |
|
||
|
|
|
С |
циклонными |
С |
циклонными |
|
Показатели |
|
теплообменниками и |
|||||
|
теплообменниками |
|
|||||
|
|
|
декарбонизаторами |
|
|||
|
|
|
|
|
|
||
|
|
|
4,5×80 |
|
7/6,4×95 |
5×75 |
4×60 |
Производительность, |
|
3000 |
|
3000 |
1700 |
1000 |
|
тонн/сутки |
|
|
|
||||
|
|
|
|
|
|
|
|
Расход |
теплоты |
на |
|
|
|
|
|
получение |
клинкера, |
3460 |
|
3460 |
3772 |
3770 |
|
кДж/(кг·К·л) |
|
|
|
|
|
|
|
Количество опор печи, |
4 |
|
4 |
3 |
3 |
||
штук |
|
|
|
|
|
|
|
Уклон корпуса печи, |
4 |
|
3,5 |
3,5 |
3,5 |
||
град. |
|
|
|
|
|
|
|
Масса печного агрегата |
2400 |
|
3800 |
1750 |
1020 |
||
(без футеровки), тонн |
|
|
|||||
|
|
|
|
|
|
||
Диаметр |
циклонов |
в |
|
|
|
|
|
свету, мм: |
|
|
|
|
|
|
|
I ступень |
|
|
5800 |
|
6460 |
4300 |
4800 |
II ступень |
|
|
5800 |
|
5960 |
4300 |
4800 |
III ступень |
|
5600 |
|
5560 |
4300 |
4800 |
|
IV ступень |
|
2×3500 |
|
2×2800 |
2×2800 |
2×2800 |
Схема печного агрегата с циклонными теплообменниками и декарбанизатором
Циклоны и газоходы первых трех ступеней (I,II,III), декарбанизаторотфутерованный огнеупором и снабжены тепловой изоляцией. Вся установка работает под разряжением создаваемым дымососом и должна быть герметична. В основу конструкции печей с циклонным теплообменником положен принцип теплообмена между отходящими газами и сырьевой мукой во взвешенном состоянии, этот способ
20