

vñê/vä = µñê, |
(4.17) |
ãäå µñê – степень скалывания.
Отношение скорости качения шарошки относительно забоя к переносной скорости (скорости вращения долота) определяет способность долота разрушать породу дроблением:
vø/vä = µäð, |
(4.18) |
ãäå µäð – степень дробления.
В реальных условиях работа шарошечного долота также зависит от формы деформируемого забоя.
СКОЛЬЖЕНИЕ ОТНОСИТЕЛЬНО ЗАБОЯ ШАРОШЕК СО СМЕЩЕННОЙ ОСЬЮ
Движение шарошки со смещенной в плане осью вращения происходит по радиусу, равному расстоянию от оси долота до наиболее удаленной точки шарошки B (рис. 4.12). Смещение осей повышает скольжение зубьев по забою и создает эффект скалывания породы по всей поверхности забоя.
Видно, что переносная скорость любой точки M на контактирующей с забоем образующей направлена по ходу вращения и перпендикулярна к радиусу вращения этой точки около центра 0, т.е. оси вращения долота.
Относительная скорость vø точки M направлена по ходу вращения ша-
рошки, перпендикулярно к ее оси вращения. Абсолютная скорость точки M составляет разность ее скоростей в относительном движении (вращение шарошки) и переносном (вращение долота) и направлена перпендикулярно к образующей шарошки.
Для определения скорости скольжения надо разложить переносную скорость vä на две составляющие: vä′ , направление которой совпадает с
направлением относительной скорости, и vä′′, имеющую направление образующей. Произведя сложение относительной скорости vø и поперечной составляющей переносной скорости vä′ , получим направление и значение поперечной составляющей скорости скольжения данной точки vñê′ . В нашем случае для точки M vø всегда будет меньше, чем vä′ , òàê êàê ïîïå-
речная скорость скольжения точки M, представляющая собой окружную скорость вращения вокруг мгновенной оси вращения (условно 0M), направлена в сторону движения.
Вектор vñê , полученный в результате сложения поперечной vñê′ и продольной vä′′ = vñê′ составляющих скоростей скольжения, покажет истинную
скорость скольжения рассматриваемой точки.
Видно (см. рис. 4.12), что относительное значение продольной состав-
ляющей скорости скольжения vñê′′ при данной скорости вращения долота
зависит только от значения смещения осей шарошек k, постоянно для всех точек шарошки и равно
vä′′ = vä sin θ = M0ωä sin θ = ωä k. |
(4.19) |
|
75 |

Рис. 4.12. Кинематика гладкой одноконусной шарошки со смещенными осями:
1 − шарошки; 2 − лапа долота
Поперечная составляющая скорости скольжения точки M
|
|
ñê′ = |
|
ä′ + |
|
ø = ωä R − ωø r. |
(4.20) |
v |
v |
v |
Суммарная скорость скольжения точки M по забою определяется по выражению
|
|
ñê = (vñê′ )2 +(vñê′′ )2 . |
(4.21) |
v |
При смещении осей шарошки в плане по направлению вращения долота радиальная составляющая скольжения направлена к вершине шарошки, а суммарная скорость скольжения отклоняется в сторону центра забоя скважины. Если vä′ > vø (ñì. ðèñ. 4.12), òî vñê направлена в сторону переносной скорости. В противном случае vñê направлена в сторону относительной скорости.
Движение шарошки с отрицательным смещением осей приводит к снижению эффективности работы периферийного венца. При этом калибрование скважины производится только за счет фрезерования породы зубьями, находящимися на обратном конусе шарошек. Суммарная нормальная реакция стенки скважины направлена против вращения шарошки.
76

Отрицательное смещение осей вращения на практике не применяется. У долот с отрицательным смещением осей шарошки скорость продольного скольжения vñê′′ = vä′′ направлена от вершины конуса шарошки к основанию, что увеличивает осевую силу, действующую на шарошку.
Значение скорости скольжения изменяется по нелинейному закону, увеличиваясь от вершины к основанию; направление зависит от вида смещения осей вращения шарошек. Скорость скольжения у всех долот возрастает с увеличением нагрузки.
СИЛЫ, ДЕЙСТВУЮЩИЕ НАШАРОШЕЧНОЕ ДОЛОТО
В процессе бурения на шарошечное долото действуют статиче- ские и динамические силы. Распределение нагрузок по различным элементам шарошечного долота зависит от конструктивных особенностей опор и вооружения шарошки, а также связано с физико-механическими свойствами разбуриваемых пород. Точное определение сил, действующих в различных точках, затруднено, поэтому ниже дается приближенный метод их определения.
На рис. 4.13 дана схема одноконусной шарошки. На шарошку действуют сосредоточенные силы: осевое усилие подачи Q, вызывающее вдавливание зубьев шарошки в породу, и окружная сила P, создающая вращательное движение, в процессе которого происходит скалывание породы. Эти усилия передаются шарошке через ее опоры цапфой долота.
Крутящий момент, действующий при вращении долота, можно представить следующим выражением
Mä = 3Pa, |
(4.22) |
ãäå P – движущая сила, приложенная к цапфе лапы долота; a – расстояние от оси долота до точки приложения силы.
При равномерном движении шарошки из условия равновесия сил активные нагрузки приравниваются силам реакции:
P = F; Q = T, |
(4.23) |
ãäå F – сила сопротивления перекатыванию шарошек; T – реакция забоя.
Сила сопротивления перекатыванию шарошки может быть определена
через осевую нагрузку следующим образом: |
|
|||
P = T(f |
+ f ) + |
T |
b, |
(4.24) |
|
||||
1 |
2 |
2 |
|
|
|
|
|
|
ãäå f1 è f2 – коэффициенты сопротивления качению и скольжению шарошки; b – плечо действия силы реакции, распределенной на два зуба венца шарошки.
В соответствии со схемой, представленной на рис. 4.14, можно запи-
ñàòü
b = rø sin ψ .
2
Тогда
P = T (f1 + f2 ) +
rø |
|
ψ |
(4.25) |
|
|
sin |
|
. |
|
|
|
|||
2 |
|
2 |
|
|
|
|
|
|
77 |

Рис. 4.13. Схема к расчету сил, действующих на различные элементы шарошки:
1 − лапа долота
Силы сопротивления скольжению могут быть определены с учетом действия распределенной осевой нагрузки q. Для случая, когда нескользящей точкой на образующей шарошки является точка À, можно получить следующие выражения
F1 = 2f1qc; F2 = 2f2ql, |
(4.26) |
ãäå c, l – расстояние от точки A до сил соответственно F1 è F2; q – распределенная нагрузка на образующую шарошки.
Для случая равномерного вращения шарошки
F1r1 = F2r2,
ãäå r1, r2 – соответственно радиусы шарошки в точках приложения сил F1 è F2.
78
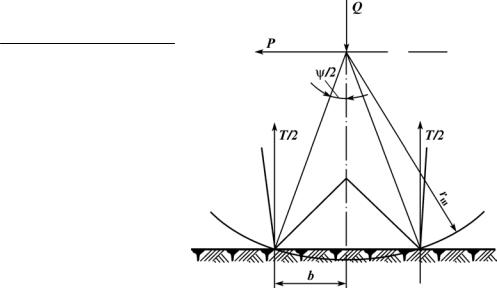
Рис. 4.14. Схема действия сил при опоре шарошки на зубча- тые венцы
Из геометрических построений (см. рис. 4.13), видно, что
|
|
c |
|
|
|||||
r1 |
= |
|
|
|
|
|
+ l sin α; |
|
|
|
|
|
|
||||||
|
|
2 |
|
|
|||||
r2 |
= |
l |
sin α. |
|
|||||
|
|
|
|
||||||
|
|
2 |
|
|
|
|
|
||
Тогда |
|
|
|
|
|
||||
|
|
c |
|
|
|||||
F1 |
= |
|
|
+ l sin α − |
|
||||
|
|
||||||||
|
|
2 |
|
|
|||||
−F |
l |
sin α = 0. |
(4.27) |
||||||
|
|
|
|
|
|
||||
|
2 |
2 |
|
|
|
|
|
|
При подстановке |
â |
||
уравнение (4.27) значений |
|||
F1 è F2 из выражения (4.26) с учетом l ≈ R – c, получают |
|||
c2 − 2cR + |
R2 |
= 0. |
(4.28) |
|
|||
2 |
|
|
Решение уравнения (4.28) дает возможность определить c è b, а следовательно, точки приложения сил F1 è F2, создающих момент сопротивления проворачиванию шарошек вокруг точки A в горизонтальной плоскости.
Нормальное усилие, действующее на цапфу со стороны забоя,
Q = T cos α. |
(4.29) |
Осевая составляющая нагрузки |
|
N = T sin α. |
(4.30) |
При калибровании ствола скважины на тыльную часть шарошки действует сила реакции G со стороны стенки скважины, которая направлена вдоль оси шарошки на расстоянии rø от ее оси и создает момент MG, стремящийся повернуть шарошку в вертикальной плоскости:
MG = Grø cos α. |
(4.31) |
Значение реакций опор Á è Ñ (см. рис. 4.13) определяется с учетом |
|
действия эквивалетной нагрузки: |
|
RÁ′ = mRÁ , RÁ′′ = mRÑ , |
(4.32) |
ãäå RÁ, RC – реакции опор при приложении нагрузки T в точке A; m – коэффициент эквивалентности, учитывающий смещение точки A в зависимо-
79
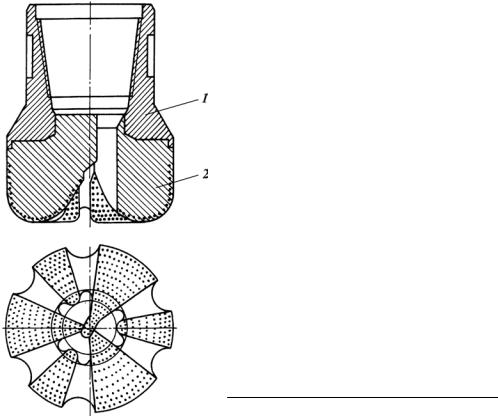
сти от приложения нагрузки. Перекатывание венца шарошки создает ударное действие зубьев по породе забоя. Динамическая составляющая осевой нагрузки на долото определяют по формуле
Qä = aF, |
(4.33) |
ãäå a – коэффициент, зависящий от статической нагрузки; |
|
F = näzi/60. |
(4.34) |
4.3. АЛМАЗНЫЕ ДОЛОТА
Алмазные долота, применяемые для бурения скважин сплошным забоем, представляют собой цельный стальной корпус 1 с присоединительной конической резьбой, к которому прикрепляется фасонная алмазонесущая головка-матрица 2 (рис. 4.15). По характеру закрепления и размещения алмазов в матрице различают долота одно-, многослойные и импрегнированные (с объемным размещением мелких алмазов в теле матрицы).
По форме торца алмазные долота разделяются на плоские, выпуклые, вогнутые, выпукло-вогнутые, выпукло-конусные, двоякоконусные, ступен- чато-конусные, комбинированные. В свою очередь, выпуклые и выпукловогнутые долота могут быть сфериче- скими или грушевидными. Профиль долота должен соответствовать форме естественного износа. При бурении абразивных пород этой форме соответствует профиль выпукло-конусных долот. Поэтому эта форма получила наибольшее
распространение.
Современные конструкции алмазных долот имеют обратный конус в центральной части с углом при вершине от 55 до 120°. Конусный керн, образующийся при бурении, разрушается от вибрации и выносится через промывочные канавки. Однако при бурении крепких пород зависание долота на керне приводит к разрушению центра долота, так как резание породы в центральной части забоя практически отсутствует.
Периферийная часть алмазного долота представляет собой сферическую поверхность, переходящую по мере удаления от торца в цилиндрическую. Цилиндрическая часть производит калибровку стенок скважины. Диаметр алмазных долот на 1,5–2,5 мм меньше диамет-
Рис. 4.15. Алмазное долото
80

ра шарошечных и лопастных долот тех же номинальных размеров. Это объясняется тем, что при бурении шарошечными долотами на стенках скважины образуются спиралевидные выступы, уменьшающие проходное сечение скважины.
Алмазные долота различаются также по форме промывочных каналов. Известны долота с центральной или торцовой промывкой; с сужающимися
èрасширяющимися промывочными каналами; радиальными, касательными
èспиральными промывочными каналами. Форма промывочных каналов и их сечение выполняются так, чтобы обеспечить хорошее удаление частиц
выбуренной породы, охлаждение и очистку рабочей части головки долота. Наиболее современными, с точки зрения охлаждения алмазов, являются долота со ступенчатой поверхностью и радиальными сужающимися каналами.
По расположению алмазов на рабочей поверхности различают долота с радиальной, шахматной, концентрической, спиральной схемами размещения. Выбор схемы размещения определяется механическими свойствами породы, системой промывки, размерами, формой и сортностью алмазов.
Рабочая поверхность долота оснащается алмазами различных размеров. Размеры их для калибрующей части 0,1–0,25 карата1; для торцовых поверхностей 0,2–0,34 карата; для конусных поверхностей 0,1–0,25 карата. Количество зерен алмазов, устанавливаемых на поверхности долота диаметром 140 мм, составляет 1000–1100; в долотах диаметром 212 мм – до 2000. На одно долото расходуется от 200 до 700 карат алмазов.
Алмаз является самым твердым из всех известных минералов и искусственных веществ. Непревзойденная твердость и высокая износостойкость обусловили его широкое применение в технике. По химическому составу алмаз является чистым углеродом. Плотность его колеблется от 3470 до 3540 кг/м3. Алмаз довольно хрупок. При высоких температурах (2000– 3000 °С) алмаз без доступа кислорода превращается в графит. В воздухе алмаз сгорает при температуре 850–1000 °С.
Алмазы в первую очередь разделяются на ювелирные и технические. В природе значительно чаще встречаются агрегатные разновидности алмазов: борт, карбонадо, баллас, конго. В бурении обычно применяют агрегатные разновидности алмазов.
Карбонадо, тонкозернистые плотные агрегаты буровато-черного цвета, имеют наибольшую прочность и встречаются очень редко. С точки зрения использования в бурении они стоят на первом месте. На втором месте стоят бесцветные и желтоватые балласы, имеющие большую крепость благодаря наружной твердой оболочке толщиной около 1 мм. Третье место занимает борт, обладающий небольшой крепостью вследствие трещиноватости кристаллов. В настоящее время борт – основное сырье для изготовления буровых долот, так как он встречается часто и имеет невысокую цену, идет в основном на изготовление абразивного сырья.
Используется три способа изготовления алмазных долот: чеканка крупных алмазов, заливка и метод порошковой металлургии.
Чеканка является старейшим способом изготовления кольцевых коронок и представляет собой ручное закрепление алмазов в заранее приготовленные гнезда в металлической основе. Чеканка малопроизводительна и в настоящее время используется редко.
1 Один карат равен по массе 0,2 г.
81
Способ заливки заключается в том, что в угольную или графитовую форму по определенной схеме раскладываются алмазы, а затем форму заливают легкоплавким сплавом. Отлитое кольцо-матрица припаивается к готовому корпусу долота или непосредственно при его литье. Недостатком способа является низкое качество матриц.
Способ порошковой металлургии – наиболее прогрессивный. Изготовление алмазных долот по этому способу сводится к следующим операциям.
Готовят смесь порошков-шихты, раскладывают алмазы в разборную пресс-форму, засыпают шихту в пресс-форму, прессуют шихту, спекают матрицу, обрабатывают долото.
Для изготовления шихты в качестве основного материала обычно используется карбид вольфрама (90–95 %), а связывающим металлом является кобальт (5–20 %). В качестве основного металла используются также порошковый вольфрам, ферромолибден, никель. Связывающими материалами могут быть сплавы меди и цинка в различных соотношениях.
Раскладка алмазов в пресс-форму проводится вручную с помощью пинцета или вакуумного карандаша по определенной схеме. Выбор схемы раскладки зависит от конструктивных особенностей алмазного долота.
После засыпки шихты в пресс-форму и прессования долото помещают в электрическую печь и разогревают до определенной температуры в водородной среде в зависимости от состава матрицы. Обычно температура спекания 650–1300 °С, выдержка 1–2 ч.
После остывания долото подвергается механической обработке: обта- чивают корпус, нарезают резьбу, изготовляют промывочные каналы. Иногда рабочая поверхность алмазных долот обрабатывается пескоструйным аппаратом для получения нужного оголения алмазов. Абсолютное значение оголения находится в пределах 0,1–0,75 мм.
Корпус алмазного долота изготовляют из конструкционной углеродистой или хромистой стали марки 40Х с содержанием углерода 0,35– 0,4 %.
4.4. ЛОПАСТНЫЕ ДОЛОТА
Лопастные долота могут быть режущего и истирающережущего типов.
РЕЖУЩИЕ ЛОПАСТНЫЕ ДОЛОТА
Лопастные долота режущего типа выпускаются двух основных видов: двухлопастные 2Л и трехлопастные 3Л.
Лопастное долото состоит из стального штампованного или литого корпуса с конической присоединительной резьбой и лопастей, отштампованных или отлитых вместе с корпусом, присоединенных или приваренных к нему (рис. 4.16). Лопасти выполняются со скосом боковых граней под углом 3–5°, направленным в сторону, противоположную вращению. В зависимости от твердости пород лопасти заправляются под различными уг-
82
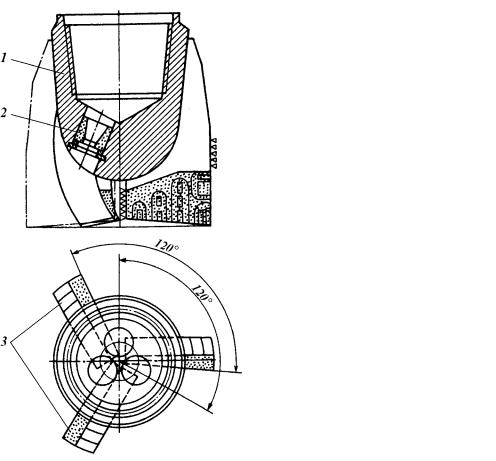
Рис. 4.16. Лопастное долото:
1 − корпус; 2 − насадка; 3 − лопасти
лами, отличающимися формой передней грани, ее наклоном относительно плоскости, перпендикулярной к оси долота. Угол наклона грани относительно этой плоскости называется углом резания. В центре долота делается вырез для улучшения его работы, так как разрушение породы в этой зоне затруднено.
Корпус и лопасти долота выполняются из среднеуглеродистых нелегированных или малолегированных конструкционных сталей. Передняя и боковая грани лопастей для увеличения стойкости армируются твердым сплавом. После приварки лопастей к корпусу на передней и боковой гранях ее вырезают канавки, дно которых наплавляется крупкой зернистого твердого сплава – релит. В армированные пазы укладываются твердосплавные пластины. Для этого применяют твердый сплав на основе карбида вольфрама типа ВК8. Затем поверхности лопасти и пластины твердого сплава заплавляют чугунным припоем с крупкой твердого сплава с помощью ацетилено-
кислородного пламени. Для снятия напряжений после сварки и наплавки долото подвергают нормализации. После этого на корпусе долота нарезают присоединительную резьбу, производят подгонку размера по диаметру и заправку лезвий долота в соответствии с назначением.
Трехлопастные долота типа 3ЛГ диаметром от 118 до 445 мм имеют три промывочных канала, в которые могут быть установлены гидромониторные насадки. Двухлопастные долота типа 2Л выпускают диаметром от 76 до 161 мм. Для упрощения изготовления и удобства при эксплуатации лопастные долота 3Л и 2Л нескольких размеров изготовляют с одинаковым корпусом.
Разновидностью лопастных долот являются долота типа РХ (рыбий хвост), изготовляемые больших диаметров (от 490 до 640 мм) по требованию заказчика для бурения мягких и средних пород. Долото типа РХ представляет собой поковку из стали марки 40. Верхняя часть долота снабжена замковой резьбой для присоединения к колонне бурильных труб. В нижней части долото имеет форму лезвия, заправленного в виде рыбьего хвоста. Лопасти долота армируются твердым сплавом.
83

Долото типа РХ поддается реставрации по мере износа рабочего лезвия и поэтому используется многократно.
ИСТИРАЮЩЕ-РЕЖУЩИЕ ДОЛОТА
Долота истирающе-режущего действия предназначены для бурения вязких, мягких и средних по твердости пород с абразивными пропластками.
Долото типа ИР (рис. 4.17) состоит из корпуса 1, приваренных к нему шести лопастей, из которых три нижние – 2, 8 è 9 имеют нормальную высоту и три верхние 5, 6, 7 – укороченную. Режущие кромки лопастей армированы цилиндрическими зубками из твердого сплава типа ВК8. Промежутки между штырями и передняя грань всех лопастей армируются зернистым твердым сплавом – релит. Боковые грани лопастей, калибрующие стенки скважины, также армируются твердосплавными штырями и слоем релита.
Промывочная жидкость на забой поступает через минералокерамиче- ские насадки 4, вставляемые в дно корпуса долота. Насадки крепятся в корпусе при помощи пружинных колец, которые удерживают их от выпадения в корпус при транспортировке. Насадки герметизируются резиновыми кольцами 3.
Долота типа ИР (с обыч- ной промывкой) и типа ИРГ (с гидромониторной промывкой) выпускаются диаметром от 76 до 269 мм. Присоединительные резьбы выполняются шести типоразмеров.
Долота типов ДСГ3ЛИР истирающе-режущего и ДСГ3ЛР режуще-скалываю- щего действия обладают преимуществами трехлопастных и долот типа ИР. Поэтому при бурении роторным способом перемежающихся мягких и средней твердости пород они показали лучшие результаты по сравнению с шарошечными долотами.
Отличительной особенностью долот типов ДСГ3ЛИР и ДСГ3ЛР является то, что они снабжены тремя лопастями, имеющими три или четыре
Рис. 4.17. Долото типа ИР
84