
Технол.станкостр.Метод.указ.к контр.раб
.pdf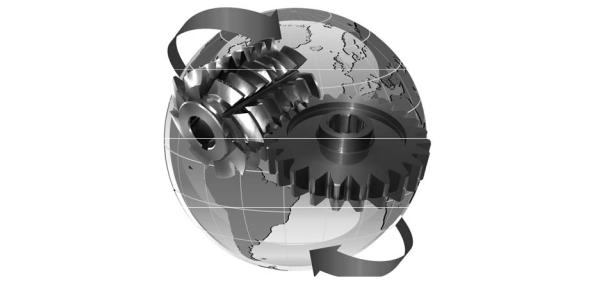
ГОСУДАРСТВЕННОЕ УЧРЕЖДЕНИЕ ВЫСШЕГО ПРОФЕССИОНАЛЬНОГО ОБРАЗОВАНИЯ
«БЕЛОРУССКО-РОССИЙСКИЙ УНИВЕРСИТЕТ»
Кафедра «Металлорежущие станки и инструменты»
ТЕХНОЛОГИЯ
СТАНКОСТРОЕНИЯ
Методические указания по выполнению контрольной работы для студентов специальности
1-36 01 03 «Технологическое оборудование машиностроительного производства» заочной формы обучения
Могилев2010
2
УДК 621.91 ББК 34.63
Т 74
Рекомендовано к опубликованию учебно-методическим управлением
ГУ ВПО «Белорусско-Российский университет»
Одобрено кафедрой «Металлорежущие станки и инструменты» «12» января 2010 г., протокол № 1
Составители: канд. техн. наук В. А. Логвин; канд. техн. наук, доц. П. Ф. Котиков
Рецензент д-р техн. наук, доц. В. М. Пашкевич
Приведена последовательность выполнения расчетов в контрольной работе.
Учебное издание
ТЕХНОЛОГИЯ СТАНКОСТРОЕНИЯ
Ответственный за выпуск |
В. А. Логвин |
Технический редактор |
А. А. Подошевко |
Компьютерная верстка |
Н. П. Полевничая |
Подписано в печать |
. Формат 60×84/16. Бумага офсетная. Гарнитура Таймс. |
||
Печать трафаретная. Усл.-печ. л. |
. Уч.-изд. л. |
. Тираж 87 экз. Заказ № |
Издатель и полиграфическое исполнение Государственное учреждение высшего профессионального образования
«Белорусско-Российский университет» ЛИ № 02330/375 от 29.06.2004 г. 212000 г. Могилев, пр. Мира, 43
© ГУ ВПО «Белорусско-Российский университет», 2010
3
1 Технология станкостроения
1.1 Теоретическая часть
Контрольную работу оформляют на основе форм, установленных соответствующими стандартами Единой системы конструкторской документации (ЕСКД) и Системы проектной документации для строительства (СПДС).
Контрольную работу выполняют одним из следующих способов:
–рукописным – чертежным шрифтом по ГОСТ 2.304-68 с высотой букв и цифр не менее 2,5 мм. Цифры и буквы необходимо писать четко черной пастой;
–с применением печатающих и графических устройств вывода ЭВМ (ГОСТ 2.004-88) с обязательным предоставлением электронной версии. Вписывать в текстовые документы, изготовленные машинописным способом, отдельные слова, формулы, условные знаки (рукописным способом),
атакже выполнять иллюстрации следует черными чернилами, пастой или тушью.
Расстояние от рамки формы до границ текста в начале и в конце строк – не менее 3 мм. Расстояние от верхней или нижней строки текста до верхней или нижней рамки должно быть не менее 10 мм. Абзацы в тексте начинают отступом 15–17 мм.
Вариант работы выбирается следующим образом: первый вопрос определяется по номеру алфавитного списка студентов группы; второй вопрос – по номеру первого плюс 20 (двадцать), третий вопрос – по номеру второго плюс 20 (двадцать) и четвертый вопрос – по номеру третьего плюс 20 (двадцать). Например, порядковый номер студента по алфавитному списку группы 13, значит студент отвечает на 13, 13 + 20 = 33, 33 + 20 = 53, 53 + 20 = 73 вопросы задания.
По согласованию с преподавателем студент может выполнять исследовательскую контрольную работу, постепенно переходящую в курсовой и дипломный проекты.
В конце работы приводится список использованных источников, оформленный по ГОСТ 7.1-2003.
Контрольные вопросы
1Особенности технологии сборки станков.
2Технологические виды и организационные формы сборки.
3Влияние служебного назначения и технологичности конструкции станка на порядок выполнения сборочных работ.
4Необходимость анализа соответствия технических требований и норм служебному назначению станка и выбор метода их достижения.
4
5 Выявление размерных цепей станка и установление их взаимных связей.
6 Порядок разработки последовательности сборки сборочных единиц и станка в целом.
7Схемы и технологическая карта сборки станка.
8Необходимость повышения производительности и выбор средств облегчения труда при выполнении сборочных работ при сборке станков.
9Особенности сборки прецизионных и тяжелых станков.
10Погрешности, возникающие при сборке, методы контроля и испытания станков.
11Необходимость и предпосылки автоматизации сборочных процессов станков.
12Применение сборочных машин и промышленных роботов для сборки станков.
13Решение задач, связанных с монтажом шпинделей.
14Сборка прямозубых зубчатых передач.
15Сборка косозубых зубчатых передач.
16Сборка червячных передач.
17Сборка конических зубчатых передач.
18Сборка валиков и втулок.
19Сборка валиков и рычагов.
20Сборка суппортов и кареток.
21Сборка и регулировка зазоров и натягов в винтовых передачах смешанного трения.
22Сборка и регулировка зазоров и натягов в винтовых передачах с трением качения.
23Испытание, регулировка и обкатка сборочных единиц станков.
24Документация технологического процесса сборки станков.
25Классификация деталей металлорежущих станков.
26Требования к технологичности и технологии изготовления валов.
27Материалы и способы получения заготовок для валов.
28Основные схемы базирования валов. Виды токарной обработки валов. Технологический процесс обработки валов.
29Обработка шлицев и шпоночных пазов на валах.
30Виды отделочной обработки наружных поверхностей валов.
31Методы повышения качества поверхностного слоя деталей.
32Виды отделочной обработки шлицев, резьбы и шпоночных пазов
на валах.
33Методы нарезания резьбы на валах. Контроль валов.
34Конструктивные разновидности шпиндельных узлов и требования, предъявляемые к ним.
35Конструктивные разновидности гильз и требования, предъявляемые к ним.
5
36Материалы и способы получения заготовок для шпинделей и
гильз.
37Основные этапы обработки шпинделей и гильз, способы базирования. Технологический процесс обработки шпинделей и гильз.
38Термические обработки шпинделей. Обработка поверхностей после термической обработки.
39Отделочные операции наружных и внутренних поверхностей шпинделя.
40Особенности обработки шпинделей прецизионных и тяжелых
станков.
41Балансировка шпинделей, их контроль.
42Назначение, разновидности винтовых передач и требования, предъявляемые к ним.
43Материалы, применяемые для изготовления ходовых винтов, и способыполучениязаготовок.
44Технологический процесс изготовления ходовых винтов. Основные этапы обработки ходовых винтов и технологические базы.
45Способы правки заготовок ходовых винтов. Типовой технологический маршрут изготовления упрочненных закалкой ходовых винтов.
46Особенности изготовления прецизионных и длинных ходовых винтов. Контроль ходовых винтов.
47Особенности изготовления гаек ходовых винтов. Контроль гаек
ивинтовых пар.
48Конструктивные разновидности, технические условия на изготовление цилиндрических зубчатых колес.
49Служебное назначение и характеристика зубчатых колес.
50Применяемые материалы и виды заготовок для зубчатых колес.
51Типовые технологические маршруты обработки цилиндрических зубчатых колес. Технологические базы.
52Обработка заготовок цилиндрических зубчатых колес. Зубофрезерование. Преимущества и недостатки зубофрезерования по сравнению с другими способами обработки зубьев.
53Обработка зубьев круглыми долбяками. Обработка зубьев гре-
бенками.
54Нарезаниезубьевспособамизуботочения. Накатказубьевшестерен.
55Отделочные виды обработки зубьев цилиндрических колес. Шевингование. Шлифование зубьев.
56Притирка зубьев зубчатых колес. Обработка торцовых поверхностей зубьев, формы зубозакругления и снятие заусенцев.
57Источники и контроль шума зубчатых колес.
58Особенности изготовления зубчатых колес и передач для микроэлектромеханических систем.
59Зубохонингование. Методы контроля.
6
60Проектирование процессов обработки конических зубчатых колес. Типы конических зубчатых колес. Технические условия на их изготовление. Материалы и виды заготовок.
61Способы нарезания конических колес с прямыми зубьями.
62Нарезание прямозубых конических колес двумя зубострогальными резцами по методу обката при последовательном делении.
63Нарезание способом кругового протягивания. Нарезание по методу копирования дисковыми и пальцевыми модульными фрезами.
64Нарезание конических зубчатых колес с криволинейными зубьями.
65Шлифование зубьев конических колес. Контроль.
66Проектирование процессов обработки деталей червячных передач.
67Служебное назначение и технические требования, предъявляемые к червячным передачам. Конструктивные формы и материал.
68Типовой технологический процесс обработки червяков типа валов из штампованной заготовки.
69Типовой технологический процесс обработки червяков типа втулки из штампованной заготовки.
70Нарезание цилиндрических червяков профильными резцами.
71Нарезание червяков червячными фрезами и долбяками.
72Вихревое нарезание червяков. Шлифование червяков. Контроль.
73Типовой технологический процесс обработки червячного колеса.
74Методы нарезания зубьев цилиндрических червячных колес.
75Способ нарезания червячных колес специальными червячными
фрезами.
76Способы отделки поверхностей червячных колес.
77Шевингование цилиндрических червячных колес. Контроль.
78Служебное назначение рычагов и вилок и особенности конст-
рукции.
79Технические условия на рычаги и вилки. Материал и заготовки для рычагов и вилок.
80Обработка рычагов и вилок. Основные правила выбора баз. Контроль рычагов и вилок.
81Служебное назначение и основные требования, предъявляемые к станинам и рамам.
82Материалы и способы получения заготовок станин и рам.
83Технологические базы при обработке станин.
84Способы уменьшения коробления базовых деталей станков.
85Типовые технологические маршруты базовых деталей станков.
86Основные схемы базирования и разметка станин. Первичная обработка основания. Чистовая обработка основания.
87Черновая и чистовая обработка верхних привалочных плоскостей и направляющих.
7
88 Обработка торцовых плоскостей. Обработка крепежных отвер-
стий.
89Особенности изготовления станин с накладными направляющими и составных станин.
90Упрочнение и отделочная обработка направляющих. Контроль
станин.
91Характеристика корпусных деталей станков. Технологические
задачи.
92Материалыиспособыполучениязаготовокдлякорпусныхдеталей.
93Базирование корпусов. Разметка корпусных деталей.
94Методы обработки наружных плоскостей корпусных деталей
станков.
95Разновидности основных отверстий корпусных деталей. Схемы, методы и режущий инструмент для обработки основных отверстий корпусных деталей.
96Методы обработки крепежных и других мелких отверстий.
97Методы отделки основных отверстий.
98Оборудование для обработки корпусных деталей, особенности обработки корпусных деталей тяжелых станков.
99Особенности и оборудование для обработки корпусных деталей прецизионных станков.
100Контроль корпусных деталей.
1.2 Практическая часть
Вариант контрольной работы выбирается по номеру алфавитного списка студентов группы из таблицы 1.1. В таблице указаны: номер детали, наименование детали, тип производства, годовой объем выпуска, поверхности, на обработку которых разрабатывается техническая документация и выполняются необходимые расчеты. Чертежи детали даны в приложении А.
В состав технической документации входят:
–чертеж детали (выполняется на листах формата A3 или А4);
–чертеж заготовки (выполняется на листах формата A3 или А4);
–титульный лист технологического процесса (выполняется на стандартном бланке по форме 2 ГОСТ 3.1105-84);
–маршрутная карта (выполняется на стандартном бланке по фор-
мам 1, 5а ГОСТ 3.1118-82);
–операционная карта (выполняется на стандартном бланке по фор-
мам 3, 2а ГОСТ 3.1404-86);
–карты эскизов (выполняются на стандартном бланке по формам 7, 7а ГОСТ 3.1105-84);
–операционная карта технического контроля (выполняется на стан-
8
дартном бланке по формам 2, 2а ГОСТ 3.1502-85).
В контрольной работе выполняются следующие разделы:
–анализ технологичности конструкции детали;
–расчет такта выпуска или количества деталей в партии;
–выбор метода получения заготовки;
–разработка маршрутного техпроцесса;
–расчет режимов резания на две-три операции;
–расчет норм времени на две-три операции;
–расчет коэффициентов загрузки на две-три операции.
1.2.1 Анализ технологичности конструкции детали.
Вэтом разделе описывается назначение детали и проводится качественный анализ технологичности ее конструкции. Технологичной считается деталь, если ее конструкция:
– имеет хорошие базовые поверхности и позволяет обеспечить принцип совмещения баз;
– достаточно жесткая и позволяет вести обработку на нормативных режимах резания;
– позволяет вести обработку проходными резцами; имеет правильной формы канавки;
– имеет простой формы центральные отверстия.
Взаключении делается вывод о технологичности детали, отмечаются нетехнологичные элементы. Более подробно последовательность проведения анализа технологичности приведена [2, 3, 18, 19]. Заканчивается раздел таблицами с химическим составом и механическими свойствами материала детали.
1.2.2 Расчет такта выпуска.
При массовом типе производства рассчитывается такт выпуска деталей te, мин, по формуле
te = (F·60) / N, |
(1.1) |
где F – годовой фонд времени работы оборудования, F = 4016 ч; N – годовой объем выпуска деталей, шт.
При серийном производстве определяется величина партии деталей п, шт., по формуле
п = (N·a) / m, |
(1.2) |
где N – годовой объем выпуска деталей, шт.; m – количество рабочих дней в году;
а – периодичность запуска деталей, дн.
Рекомендуется следующая периодичность запуска изделий: для крупных деталей – 3 дн., для средних – 6 дн., для мелких – 24 дн.
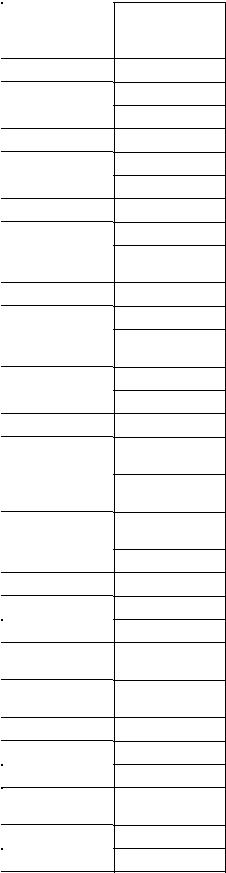
9
Таблица 1.1 – Варианты заданий
|
Номер |
Наименование |
|
Годовой |
|
Вариант |
Тип производства |
объем выпуска, |
|||
детали |
детали |
||||
|
|
|
|
шт. |
|
1 |
КТС 01 |
Крышка |
Серийное |
6000 |
|
2 |
КТС 02 |
Втулка |
Массовое |
300000 |
|
3 |
КТС 03 |
Колесо зубчатое |
Массовое |
240000 |
|
4 |
КТС 04 |
Втулка |
Массовое |
250000 |
|
5 |
КТС 05 |
Колесо зубчатое |
Серийное |
12000 |
|
6 |
КТС 06 |
Винт |
Массовое |
270000 |
|
7 |
КТС 07 |
Колесо зубчатое |
Серийное |
20000 |
|
8 |
КТС 08 |
Гильза |
Массовое |
320000 |
|
9 |
КТС 09 |
Вилка переклю- |
Массовое |
260000 |
|
чения (левая) |
|||||
10 |
КТС 10 |
Колесо зубчатое |
Массовое |
275000 |
|
11 |
КТС 11 |
Колесо зубчатое |
Серийное |
14000 |
|
12 |
КТС 12 |
Вилка переклю- |
Серийное |
25000 |
|
чения (левая) |
|||||
13 |
КТС 13 |
Колесо зубчатое |
Серийное |
30000 |
|
14 |
КТС 14 |
Колесо зубчатое |
Массовое |
285000 |
|
15 |
КТС 15 |
Крышка |
Массовое |
260000 |
|
16 |
КТС 16 |
Крышка |
Серийное |
5000 |
|
сквозная |
|||||
|
|
|
|
||
17 |
КТС 17 |
Корпус |
Массовое |
310000 |
|
подшипника |
|||||
|
|
|
|
||
18 |
КТС 18 |
Валик |
Серийное |
12000 |
|
кулачковый |
|||||
|
|
|
|
||
19 |
КТС 19 |
Вал–шестерня |
Серийное |
17000 |
|
20 |
КТС 20 |
Подшипник |
Массовое |
320000 |
|
21 |
КТС 21 |
Муфта |
Серийное |
18000 |
|
22 |
КТС 22 |
Стержень |
Массовое |
310000 |
|
23 |
КТС 23 |
Стакан |
Серийное |
19500 |
|
подшипника |
|||||
|
|
|
|
||
24 |
КТС 24 |
Стакан |
Серийное |
11000 |
|
подшипника |
|||||
|
|
|
|
||
25 |
КТС 25 |
Упор |
Массовое |
150000 |
|
26 |
КТС 26 |
Шестерня |
Массовое |
230000 |
|
27 |
КТС 27 |
Колесо зубчатое |
Серийное |
14000 |
|
28 |
КТС 28 |
Крышка |
Серийное |
18500 |
|
проходная |
|||||
|
|
|
|
||
29 |
КТС 29 |
Колесо зубчатое |
Массовое |
215000 |
|
30 |
КТС 30 |
Колесо зубчатое |
Массовое |
200000 |
Обрабатываемая
поверхность
А, Б, В
Б
Б
А
Б
А
Б
Г
А, Б, В
Б
Б, В
А, Б, С
В
Б
Г
В
Б
В
В
В
Б
А
В
Б
Б
Б
Д
Б
Б, В
Б
10
1.2.3 Выбор метода получения заготовки.
В зависимости от типа производства, формы и материала детали выбирается метод получения заготовки, приводится ее краткое описание, применяемое оборудование, преимущества перед другими методами (точность, производительность и т. д.).
Расчет стоимости заготовки из проката вычисляется по формуле
S3aг = M + ΣCо.з, |
(1.3) |
где М – затраты на материал заготовки, р.;
ΣCо.з – техническая себестоимость правки, калибрования прутков,
разрезки.
Расчет затрат на материалы и технической себестоимости выполня-
ется по формуле |
|
M = Q·S – (Q – q)·Somx, |
(1.4) |
где Q – масса заготовки, кг;
S – цена 1 кг материала заготовки, р.; q – масса детали, кг;
Sотx – цена 1 кг отходов, р.
Масса заготовки Q рассчитывается как масса цилиндра. Размеры цилиндра (диаметр и длина) определяются с учетом припусков на обработку,
которые могут быть определены по [1]. |
Плотность стали ρ = 7860 кг/м3. |
|
Со.з.=[Сп.з ·tшт. |
(шт. к)] / 60, |
(1.5) |
где Сп.з – приведенные затраты на рабочем месте, р./ч;
tшm. (шт. к) – штучное или штучно-калькуляционное время выполнения заготовительной операции, мин.
Цены на материалы S и отходы Somx можно взять из [2], увеличив их пропорционально росту цен.
Примерные значения приведенных затрат на рабочем месте Сп.з. представлены [1, с. 30]. Их значение также следует увеличить.
Штучное или штучно-калькуляционное время tшm. (шт.к), мин, рассчитывается по формуле
tшт. (шт. к) = [(Lрез + у) / Sм] φ, |
(1.6) |
где Lpeз – длина резания при разрезании проката на штучные заготовки (может быть принята равной диаметру проката: Lрез = D), мм;
у – величина врезания и перебега (при фрезеровании дисковой пилой у = 6–8 мм);
Sм – временная подача при разрезании, Sм = 50–80 мм/мин);
φ – коэффициент, показывающий долю вспомогательного времени в штучном (φ = 1,84 – для мелко- и среднесерийного производства; φ = 1,51 – для крупносерийного и массового производства).