
Технол.мат-лов.Лаб.практикум
.pdf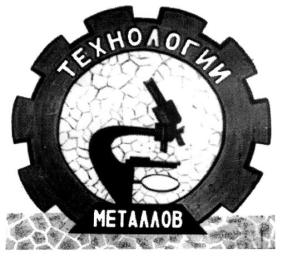
ГОСУДАРСТВЕННОЕ УЧРЕЖДЕНИЕ ВЫСШЕГО ПРОФЕССИОНАЛЬНОГО ОБРАЗОВАНИЯ
«БЕЛОРУССКО-РОССИЙСКИЙ УНИВЕРСИТЕТ»
Кафедра «Технологии металлов»
ТЕХНОЛОГИЯ МАТЕРИАЛОВ
Лабораторный практикум для студентов технических специальностей дневной и заочной форм обучения
ФОРМООБРАЗОВАНИЕ ЗАГОТОВОК ЛИТЬЕМ
Могилев 2010
УДК 621.7 ББК 32.9
Т 38
Рекомендовано к опубликованию учебно-методическим управлением
ГУ ВПО «Белорусско-Российский университет»
Одобрено кафедрой «Технологии металлов» «5» мая 2010 г., протокол № 10
Составители: канд. техн. наук Д. И. Якубович; ст. преподаватель А. И. Хабибуллин; ст. преподаватель И. А. Лозиков
Рецензент |
канд. техн. наук Н. С. Горлачев |
В данных указаниях приведены методики разработки технологических процессов получения отливок литьем в песчано-глинистые формы и кокили.
Учебное издание
ТЕХНОЛОГИЯ МАТЕРИАЛОВ
Ответственный за выпуск |
Д. И. Якубович |
|
Технический редактор |
А. Т. Червинская |
|
Компьютерная верстка |
И. А. Алексеюс |
|
Подписано в печать |
. Формат 60х84/16. Бумага офсетная. Гарнитура Таймс. |
|
Печать трафаретная. Усл.-печ. л. |
. Уч.-изд. л. |
. Тираж 71 экз. Заказ № |
Издатель и полиграфическое исполнение Государственное учреждение высшего профессионального образования
«Белорусско-Российский университет» ЛИ № 02330/375 от 29.06.2004 г. 212000, г. Могилев, пр. Мира, 43
©ГУ ВПО «Белорусско-Российский университет», 2010
3
1 Практическая работа № 1. Формообразование заготовок литьем в песчано-глинистые формы
Цель работы: ознакомление с методикой разработки технологического процесса получения отливок; ознакомление с последовательностью изготовления песчано-глинистых литейных форм; ознакомление с последовательностью изготовления отливок.
1 Оборудование:
–печь для плавки металла;
–формовочный инструмент;
–модель;
–формовочная смесь;
–опоки;
–шихта для выплавки металла.
2 Порядок проведения работы:
–начертить эскиз детали;
–выбрать положение отливки в форме и назначить плоскость разъема модели;
–назначить припуски на механическую обработку отливки;
–назначить формовочные уклоны модели;
–нанести припуски и уклоны на эскиз детали;
–определить конфигурацию стержней и знаковые части стержня;
–начертить эскиз модели;
–начертить эскиз литейной формы в сборе;
–получить модельный комплект отливки заданной детали, изготовить стержень и форму;
–получить отливку посредством заполнения формы расплавленным металлом.
3 Общие сведения. Сущность литейного производства, элементы литейной формы и контроль качества отливок.
Литейное производство – отрасль машиностроения, занимающаяся изготовлением фасонных заготовок путем заливки расплавленного металла в специальную ферму, полость которой имеет конфигурацию заготовки. При охлаждении металл затвердевает и в твердом состоянии сохраняет конфигурацию той полости, в которую он был залит.
Литейная форма – это система элементов, образующих полость, при заливке которой расплавленным металлом формируется отливка. На рисункеl, a показана литейная форма для получения деталей типа тройника (рисунок1, б). Форма обычно состоит из нижней 2 и верхней 6 полуформ, которые изготавливаютполитейныммоделям7 (рисунок1, г) влитейныхопоках3 и5.
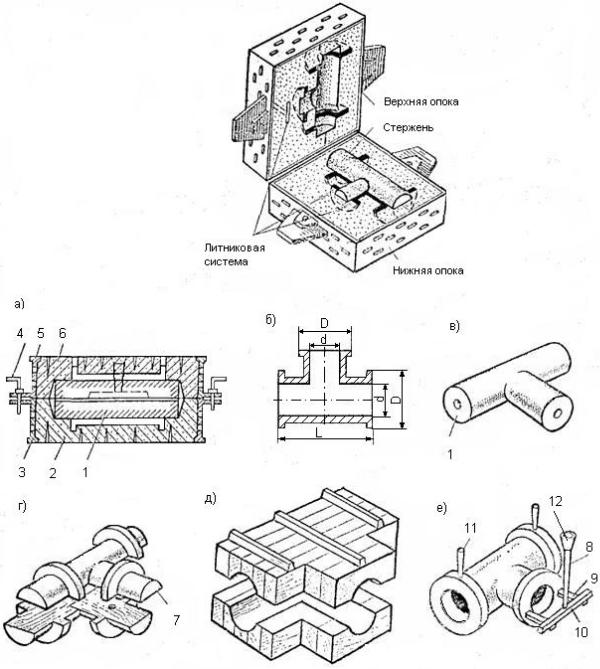
4
а) |
б) |
в) |
||
|
|
|
|
|
|
|
|
|
|
|
|
|
|
|
г) |
|
д) |
|
е) |
|
|
|
|
|
а – литейная форма; б – тройник; в – литейный стержень; г – литейная модель; д – стержневой ящик; е – отливка с литниковой системой
Рисунок 1 – Литейная форма и ее элементы
Литейная опока – приспособление для удержания формовочной смеси при изготовлении формы. Верхнюю и нижнюю полуформы взаимно ориентируют с помощью металлических штырей 4, вставляемых в центрирующие ушки. Для образования отверстий в отливках в формы устанавливают литейные стержни 1, которые фиксируются с помощью выступов (стержневых знаков), входящих в соответствующие впадины в литейной форме. Литейные стержни изготавливают по стержневым ящикам (рису-
5
нок 1, д). Для подвода расплавленного металла в полость литейной формы используют литниковую систему 8–11.
Литниковая система – это совокупность каналов, по которым расплав поступает из разливочного ковша в полость формы. Основными элементами ее являются:
–литниковая чаша (конус) 12 – служит для приема расплавленного металла и подачи его в стояк;
–стояк 8 – вертикальный канал для подачи металла из литниковой чаши в шлакоуловитель;
–шлакоуловитель 10 – служит для удержания шлака и других неметаллических примесей;
–питатель 9 – служит для подвода расплавленного металла в полость литейной формы;
–выпор или прибыль 11 – служат для вывода газов, контроля заполнения формы расплавленным металлом и питания отливки расплавом при
еезатвердевании.
После заливки расплавленного металла, его затвердевания и охлаждения форму разрушают, извлекая отливку (рисунок 1, е).
Модельный комплект – это совокупность технологической оснастки и приспособлений, необходимых для образования в форме полости, соответствующей контурам отливки. В модельный комплект включают модели, модельные плиты, стержневые ящики, модели элементов литниковой системы и другие приспособления.
Литейная модель (рисунок 2, а) – приспособление, при помощи которого в литейной форме получают полость с формой и размерами близкими к конфигурации получаемой отливки.
Модельная плита (рисунок 2, б) – металлическая плита с закрепленными на ней моделями и элементами литниковой системы.
Стержневой ящик (рисунок 2, в) – формообразующее приспособление, имеющее рабочую полость для получения в ней литейного стержня нужных размеров и очертаний из стержневой смеси.
Формовочные материалы – совокупность природных и искусственных материалов, используемых для приготовления формовочных и стержневых смесей. В качестве огнеупорной составляющей смеси используют формовочный кварцевый песок, а для соединения частиц песка между собой применяют формовочные глины, смолы и другие связующие.
Формовка – совокупность технологических операций изготовления литейных форм и стержней, способных выдерживать воздействие расплавленного металла и сообщать ему свои очертания. Основными операциями формовки являются наполнение опоки формовочной смесью, уплотнение ее, извлечение модели и сборка формы.
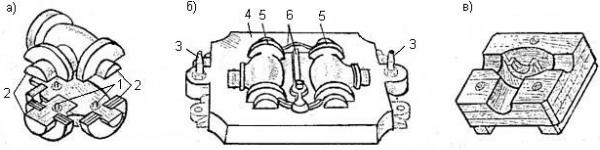
6
а) |
б) |
в) |
|
||
|
|
|
|
|
|
а – модельная плита; б – стержневой ящик; в – для корпуса вентиля; 1 – центрирующие шипы; 2 – стержневые знаки; 3 – центрирующие штыри; 4 – металлическая плита; 5 – модели отливок; 6 – модели элементов литниковой системы
Рисунок 2 – Литейная модель
Заливку форм расплавленным металлом производят из конических, барабанных и других ковшей, футерованных огнеупорным материалом. Температура заливаемого металла зависит от рода сплава, толщины стенок отливки, их конфигурации и т. п. Заливку форм ведут непрерывно до полного заполнения литниковой чаши.
Выбивку отливок из литейных форм осуществляют на вибрационных решетках. От вибрации форма разрушается, смесь просыпается сквозь решетку, а опоки с отливкой остаются на решетке. Удаление стержней производится пневматическими вибрационными машинами или вымыванием мощной струей воды.
Обрубку и зачистку отливок от остатков питателей, заусенцев и заливов производят шлифовальными кругами, дековыми пилами, газокислородной резкой или на обрезных прессах.
Очистка отливок от пригара осуществляется в очистных вращающихся барабанах или дробеметных установках.
Контроль качества производят с целью обнаружения брака отливок, основными видами и причинами которого являются:
–газовые раковины и пористость в отливках. Причины: малая газопроницаемость или повышенная влажность формовочной смеси;
–усадочные раковины и пористость в отливках. Причины: неправильный подвод жидкого металла в форму; слишком высокая температура заливаемого металла;
–песчаные и шлаковые раковины (полости в теле отливки, заполненные формовочной смесью или шлаком). Причины: слабая набивка формы; плохая конструкция шлакоуловителя;
–холодные трещины. Причина: неодинаковая скорость охлаждения различных сечений отливки, что приводит к возникновению внутренних напряжений;
–горячие трещины (имеют темную окисленную поверхность). Причины: малая податливость стержней и формы; резкие переходы от тонкой
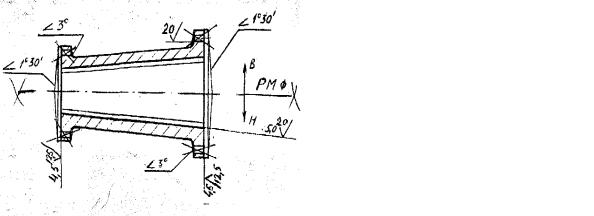
7
части отливки к толстой;
–коробление (изменение формы и размеров отливки под влиянием внутренних напряжений, возникающих при неравномерном охлаждении равных частей отливки). Причины: высокая скорость охлаждения; недостаточная податливость формы; нерациональная конструкция отливки;
–заливы (тонкие выступы вдоль разъема формы). Причина: недостаточная нагрузка формы;
–недолив (неполная отливка). Причины: плохая жидкотекучесть сплава; низкая температура расплава; малое сечение питателей; утечка расплава из формы.
4 Последовательностьразработкитехпроцессаполученияотливки.
Исходным документом для разработки чертежа отливки является чертеж детали (рисунок 3), на котором указываются:
–разъем модели и формы;
–положение отливки в форме при заливке;
–припуски на механическую обработку;
–формовочные уклоны;
–расположение стержней и размеры стержневых знаков. Поверхность разъема модели и формы должна обеспечивать свобод-
ное извлечение модели из формы при минимальном числе стержней и отъемных частей. При этом обрабатываемые поверхности отливки должны находиться преимущественно в нижней полуформе, что гарантирует получение плотной (без пористости) обрабатываемой части отливки. На чертеже отливки поверхность разъема модели и формы обозначают линией РМФ и стрелками направления верха (В) и низа (Н) (рисунок 4).
Рисунок 3 – Чертеж детали |
Рисунок 4 – Чертеж отливки |
Припуск на механическую обработку (см. рисунок 4) – слой металла, удаляемый в процессе механической обработки отливки с ее обрабатываемых поверхностей для обеспечения заданной геометрической точности и
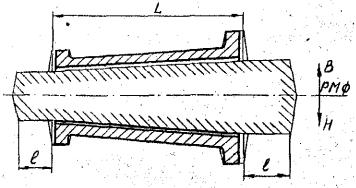
8
качества поверхности детали. На чертежах припуск на механическую обработку показывают тонкой линией и указывают его величину. Величина припуска определяется по ГОСТ 26645-85 (приложение А).
Формовочные уклоны (см. рисунок 4) служат для удобства извлечения модели из формы без ее разрушения. Уклоны выполняют в направлении извлечения модели из формы. Величину уклона определяют по ГОСТ 3212-92 (приложение Б) и указывают его на чертеже.
Конфигурация и размеры стержневых знаков должны обеспечивать легкую установку в форму и устойчивость стержней; определяются по ГОСТ 3606-85 (приложение В). Стержни повторяют конфигурацию внутренней полости отливки и в разрезе штрихуются только у контурных линий (рисунок 5). Для стержней с переменным сечением для определения размеров знаков принимается больший диаметр.
Рисунок 5 – Обозначение контура стержней.
Галтели – округления внутренних углов поверхностей модели. Галтели облегчают извлечение модели из формы, предотвращают
появление трещин и усадочных раковин в отливке. Радиус галтели принимают от 1/5 до 1/3 средней арифметической толщины стенок, образующих угол модели.
После назначения припусков, уклонов и размеров стержневых знаков вычерчивается эскиз литейной формы в сборе в вертикальном разрезе (рисунок 6).
Последовательность разработки технологического процесса изготовления отливки состоит из следующих этапов.
1Изучение чертежа детали.
2Выбор положения плоскости разъема модели и формы.
3Назначение припусков на обрабатываемые поверхности.
4Назначение уклонов на вертикальные стенки.
5Размещение стержней и определение величины стержневых знаков (при необходимости).
6Увеличение линейных размеров контура отливки на величину линейной усадки (в данной лабораторной работе не выполняется).
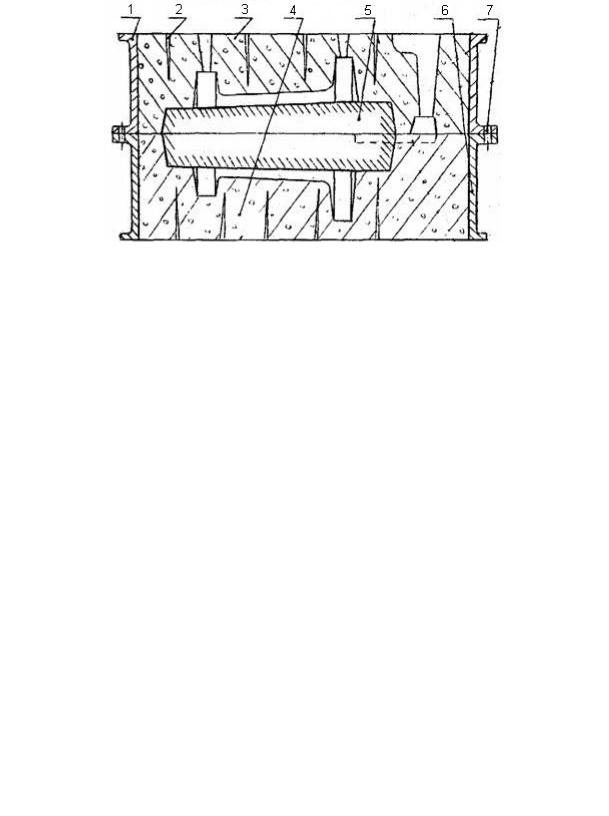
9
7 Изготовление чертежа модели на основе полученных контуров и размеров.
8Изготовление модели.
9Проектирование литейной формы и ее изготовление.
1 – верхняя опока; 2 – газоотводные каналы; 3 – верхняя полуформа; 4 – нижняя полуформа; 5 – стержень; 6 – нижняя опока; 7 – центрирующее ушко
Рисунок 6 – Литейная форма в сборе
5 Последовательность изготовления формы при формовке в двух опоках.
При формовке по цельной модели необходимо соблюдать следующий порядок операций. Модель очищают от формовочной смеси, припыливают и кладут гладкой поверхностью на модельную плиту. Затем на модельную плиту ставят нижнюю опоку, через сито насеивают слой облицовочной смеси, после чего в несколько приемов слоями толщиной 50–70 мм засыпают наполнительную смесь и утрамбовывают ее. Излишек смеси сверху опоки срезают линейкой и душником делают наколы, не доходящие до модели на 10–15 мм.
Набитую опоку поворачивают на 180о и ставят на выровненную поверхность почвы или на верстак. Затем плоскость разъема опок заглаживают гладилкой, посыпают разделительным песком и модель накрывают верхней опокой. После этого вверхней опоке размещают модели стояка и выпоров с таким расчетом, чтобы они были достаточно удалены от стенок опоки. После уплотнения смеси в верхней опоке и извлечения из формы модели стояка опоку поднимают и кладут на ребро или поворачивают на 180о.
После удаления модели форму исправляют, обдувают и припыливают, при необходимости ставят стержни. Затем верхнюю опоку по штырям осторожно ставят на нижнюю.
Точное центрирование при спаривании опок производится с помощью контрольных штырей, вставляемых в отверстия центрирующих ушек.
10
Во избежание прорыва металла через плоскость разъема во время заливки опоки скрепляют металлическими скобами или накладыванием груза.
При формовке в двух опоках по разъемной модели на модельную плиту устанавливают нижнюю часть модели лицевой стороной кверху и на эту же доску ставят нижнюю опоку плоскостью разъема вниз. Модель, предварительно протертую керосином, припыливают припылом и заполняют тонким слоем (15–20 мм) облицовочной смеси. Затем наполняют опоку наполнительной смесью и утрамбовывают вначале клиновой трамбовкой по углам, а затем плоской трамбовкой по всей поверхности. Набитую опоку накалывают душником, переворачивают на 180о и ставят на выровненный слой земли. На нижнюю половину модели кладут верхнюю половину и плоскость разъема формы посыпают сухим разделительным песком. После этого на нижнюю опоку ставят верхнюю, припыливают модель, устанавливают модели литников и заформовывают верхнюю опоку в таком же порядке, как и нижнюю. После накаливания душником вентиляционных каналов вытаскивают из верхней опоки модели стояка и расширяют верхнюю часть стояка в виде чаши. Затем снимают верхнюю опоку, устанавливают ее плоскостью разъема вверх, прорезают питатели на нижней полуформе и смачивают кромки обеих полуформ в местах соприкосновения их с половинками моделей для предупреждения осыпания формовочной смеси при выемке модели. После этого, расшатав половинки модели, вынимают их из полуформ, исправляют возможные повреждения, припыливают и приглаживают поверхности, устанавливают стержень и, наконец, собирают форму для заливки, опуская верхнюю опоку на нижнюю по направляющим штырям.
6 Последовательность изготовления отливки.
6.1Приготовить форму согласно п.5.
6.2Установить тигель с шихтой в печь, выдержать при температуре 90 оС не менее 10 мин.
6.3Извлечь тигель с помощью клещей и заполнить форму расплавленным металлом до появления его в выпорах.
6.4После кристаллизации и охлаждения выбить отливку из формы и стержень из отливки. Отработанную формовочную смесь высыпать в специальную емкость.
6.5Удалить литниковую систему и очистить отливку.
6.6Произвести контроль размеров и качества отливки.
7 Содержание отчета.
Начертить эскизы детали; отливки с размерами припусков, уклонов и стержневых знаков; формы в сборе. Сделать выводы по результатам контроля отливки.