
Технол.станкостр.Метод.указ.к контр.раб
.pdf11
Расчет стоимости заготовок, полученных литьем или штамповкой, выполняется по формуле [2, 3]
Sзаг = [(Сi /1000) Q Кт Кс Кв Км Кп] – (Q – q)·Somx, |
(1.7) |
где Сi – базовая стоимость 1 т заготовок, р.;
Кт – коэффициент, зависящий от класса точности; Кс – коэффициент, зависящий от степени сложности; Кв – коэффициент, зависящий от массы заготовки; Км – коэффициент, зависящий от марки материала;
Кп – коэффициент, зависящий от объема выпуска заготовок. Масса заготовки определяется как сумма масс элементарных объе-
мов заготовки, на которые она условно разбивается. Размеры заготовки определяются с учетом установленных припусков.
На чертеже заготовки внутри заготовки тонкими линиями вычерчивается контур детали. На чертеже заготовки из проката проставляются диаметр заготовки и длина с предельными отклонениями [13]. Предельные отклонения на длину заготовки в зависимости от способа разрезания приведены в [13].
Для штампованных заготовок по ГОСТ 7505-89 устанавливаются: группа стали – М1–М3; степень сложности поковки – С1–С4; класс точности поковки – Т1–Т5; исходный индекс – 1–23.
По исходному индексу в том же стандарте определяются припуски на обрабатываемые поверхности и предельные отклонения размеров заготовки. На чертеже заготовки в технических требованиях записываются:
–исходная твердость;
–класс точности и степень сложности по ГОСТ 7505-89;
–радиусы закруглений наружных и внутренних углов;
–штамповочные уклоны;
–допускаемая величина остаточного облоя;
–допускаемое смещение по поверхности разъема штампа;
–допускаемая величина высоты заусенца.
1.2.4 Разработка маршрутного техпроцесса.
При разработке маршрутного техпроцесса предварительно определяется количество технологических операций (переходов) для обработки всех поверхностей детали на основе таблиц экономической точности [2, 3, 13]. После этого выбора формируются операции, т. е. отдельные переходы объединяются в технологические операции.
Одновременно с разработкой операций выбираются технологические базы. При этом необходимо стремиться к обеспечению в технологическом процессе принципов совмещения и постоянства баз.
Режущие инструменты выбираются в зависимости от видов обработки детали. В серийном производстве, как правило, используются стандарт-
12
ные режущие инструменты. В крупносерийном и массовом производстве наряду со стандартными могут использоваться и специальные режущие инструменты.
Металлорежущие станки выбираются в зависимости от видов обработки детали, требуемой точности обработки, размеров детали и типа производства. Приводится обоснование их выбора.
Следует помнить, что название операции определяется названием станка, а не видом обработки. Так, например, если на сверлильном станке выполняется зенкерование отверстия, операция называется сверлильной. Нумеруется операция, как правило, числами, кратными 5 или 10. Например, операция 05 – токарная, операция 10 – сверлильная и т. д.
Разработанный маршрутный техпроцесс в контрольной работе оформляется в виде таблицы 1.2, которую целесообразно разместить на развороте тетради и на маршрутных картах (МК) по ГОСТ 3.1404-86 (формы 2 и 2а).
Таблица 1.2 – Маршрутный техпроцесс изготовления вала КТС.00
Номер |
Наименование и краткое |
Модель |
Режущий инструмент, |
Технологическая |
|
операции |
содержание операции |
станка |
размеры, марка материала |
база |
|
|
|
|
|
|
|
05 |
Фрезерно-центроваль- |
МР-77 |
|
Поверхности |
|
|
ная: |
|
|
|
заготовки Ø40; |
|
фрезерование |
тор- |
|
Фреза торцовая Ø125, |
Ø60; торец |
|
цов (L = 280-1,3) |
|
|
Т5К10 |
|
|
сверление центро- |
|
Сверло центровочное |
|
|
|
вых отверстий Ø4 |
|
|
Ø4, Р6М5 |
|
10 |
Токарная с ЧПУ: |
|
16К20ФЗ |
|
Центровые |
|
черновое точение |
|
Резец проходной 16x25, |
отверстия |
|
|
поверхностей Ø37-0,25; |
|
Т5К10 |
|
|
|
Ø42-0,25; Ø50-0,62 |
|
|
Резец канавочный |
|
|
чистовое точение |
|
|
||
|
поверхностей Ø35-0,1; |
|
Т5К10 |
|
|
|
Ø40-0,1 |
фасок |
|
|
|
|
точение |
|
|
|
|
|
1,6×45° |
|
|
|
|
|
точение канавки |
|
|
|
|
|
Ø34×3 |
|
|
|
|
15 |
Вертикально-фрезерная: |
6М12П |
|
Цилиндричес- |
|
|
фрезерование шпо- |
|
Фреза шпоночная Ø12, |
кие поверхности |
|
|
ночного паза (b = 12N9, |
|
Р6М5 |
Ø35; Ø50; торец |
|
|
1 = 30) |
|
|
|
|
20 |
Термическая |
|
Печь |
|
|
… |
|
|
|
|
|
45 |
Контрольная |
|
Стол |
|
|
|
|
|
ОТК |
|
|
13
1.2.5 Расчет режимов резания.
Режимы резания рассчитываются на все операции, связанные с обработкой поверхностей, указанных в варианте задания.
Расчет режимов резания начинается с определения глубины резания t, мм. Для токарных операций весь припуск на поверхность необходимо разделить на черновую, чистовую и отделочную обработки, если последние необходимы. При этом на чистовую и отделочные обработки оставляется, как правило, 20–30 % общего припуска. Припуск на черновую обработку может быть снят за один или несколько рабочих ходов. Если припуск снимается за один рабочий ход, то глубина резания равна припуску на сторону, т. е. t = Zчерн. Если припуск снимается за несколько рабочих ходов, то глубина резания t, мм, равна:
t = Zчерн / i, |
(1.8) |
где i – количество рабочих ходов.
Подача на оборот Sо, мм/об (подача на зуб Sz, мм/зуб, при фрезеровании) выбирается в зависимости от глубины резания по [12, 15].
Справочное значение подачи корректируется и принимается окончательно по паспортным данным станка выбранной модели.
Скорость резания рассчитывается по формулам теории резания металлов [15] или нормативам [12]. По полученному значению скорости определяется расчетная частота вращения шпинделя np , мин-1:
np = 60000·Vp / (π·D), |
(1.9) |
где D – диаметр обрабатываемой поверхности или инструмента, мм; Vp – скорость резания, м/с.
Полученное значение частоты вращения корректируется по паспорту
станка и принимается окончательно пп, мин-1. По принятой частоте враще- |
|
ния пп , мин-1, определяется действительная скорость резания Vд, м/с: |
|
Vд = π·D·nп / 60000. |
(1.10) |
В заключение рассчитывается эффективная мощность резания Nэ и сравнивается с мощностью главного привода Nст.
1.2.6 Расчет нормы времени.
В крупносерийном и массовом производстве рассчитывается норма штучного времени:
tшm= to + tв + tобс + tотд, |
(1.11) |
где tо – основное время, мин;
tв – вспомогательное время, мин;
toбc – время на обслуживание рабочего места, мин; tотд – время на отдых, мин.
14
В мелко- и среднесерийном производстве рассчитывается норма штучно-калькуляционного времени:
tшт. к= tшт + tп.з. / n, |
(1.12) |
где tп.з. – подготовительно-заключительное время, мин; |
|
п – размер партии деталей (см. п. 1.2.1). |
|
Основное время tо, мин, рассчитывается по формуле |
|
tо = ((Lpeз + y) / (Sо ·n))·i, |
(1.13) |
где Lpeз – длина резания, мм; |
|
у – величина врезания и перебега, мм [12]; |
|
i – количество рабочих ходов.
Вспомогательное время tв, мин, состоит из затрат времени на отдель-
ные приемы [9, 10]: |
|
tв = tyc + tз.о. + tyn + tиз., |
(1.14) |
где tyc – время на установку и снятие детали, мин; |
|
tз.о. – время на закрепление и открепление детали, мин; |
|
tyn – время на приемы управления станком, мин; |
|
tиз – время на измерение детали, мин. |
|
Оперативное время tоп, мин, рассчитывается по формуле |
|
tоп = tо + tв. |
(1.15) |
Время на обслуживание и отдых iобс и tотд, мин, в серийном производстве по отдельности не определяется. В нормативах приводится сумма этих двух составляющих в процентах от оперативного времени tоп, мин [10].
В массовом производстве время на отдых tomд, мин, задается в процентах от оперативного времени tоп, мин [13].
Время на обслуживание toбc, мин, в массовом и крупносерийном производстве слагается из времени на организационное обслуживание topг, мин, и времени на техническое обслуживание tmeх, мин:
toбc = topг + tmeх. |
(1.16) |
Подготовительно-заключительное время tп.з., мин, состоит из ряда составляющих [10]:
–время на отладку станка и установку приспособления;
–время перемещений и поворотов рабочих органов станка;
–время на установку инструмента;
–время на получение инструментов и приспособлений до начала работы и их сдачи после её окончания.
Пример расчета норм времени приведен в [2].
15 |
|
1.2.7 Расчет коэффициента загрузки станка. |
|
Коэффициент загрузки станка рассчитывается по формуле [2] |
|
ηз = ср / спр, |
(1.17) |
где ср – расчетное количество станков; |
|
спр – принятое количество станков. |
|
Расчетное количество станков ср определяется по формуле |
|
ср = N tшт. (шт. к) / (60 Fд ηз.н), |
(1.18) |
где N – годовой объем выпуска деталей, шт.;
tшт. (шт. к) – штучное (для массового и крупносерийного производства) или штучно-калькуляционное время (для мелко- и среднесерийного производства);
Fд – действительный годовой фонд времени, Fд = 4016 ч;
ηз.н – нормативный коэффициент загрузки оборудования. Среднее значение нормативного коэффициента загрузки оборудования ηз.н следует принимать: для мелкосерийного производства – 0,8–0,9; среднесерийного – 0,75–0,85; массового и крупносерийного – 0,65–0,75.
Принятое количество станков спр получается округлением расчетного количества до ближайшего большего целого числа.
Для мелко- и среднесерийного производства при получении коэффициента загрузки ηз меньше нормативного ηз.н решается вопрос о дозагрузке станков деталями такого же класса. Количество наименований обрабатываемых деталей при этом рассчитывается по формуле
Nдоз= ηзн / ηз. |
(1.19) |
Полученное значение округляется до ближайшего меньшего целого числа.
1.3 Оформление технологической документации
Вконтрольной работе оформляются маршрутная карта (МК), операционные карты (ОК) на две–три операции и карты эскизов (КЭ).
Маршрутная карта оформляется на бланках ГОСТ 3.1118-82 фор-
мы 1, 5а.
Операционная карта является описанием технологической операции
суказанием требований безопасности, переходов, режимов обработки и данных о средствах технологического оснащения.
Операционная карта оформляется в соответствии с ГОСТ 3.1404-86 по формам 3 и 2а.
Воперационной карте под символом «0» записывается содержание операции или перехода в повелительной форме, например «Точить по-
16
верхность, выдерживая размеры 1, 2», «Фрезеровать лыску, выдерживая размеры 5, 6, 7».
Запись переходов выполняется по всей длине строки. При необходимости запись переносится на следующую строку.
Все переходы нумеруются числами натурального ряда (1, 2, 3 и т. д.). Установы обозначаются прописными буквами русского алфавита (А,
Б, В и т. д.), например «Установ А».
Под символом «Т» в операционной карте указывается информация о применяемой при выполнении операции технологической оснастке в следующей последовательности:
–приспособление;
–вспомогательный инструмент;
–режущий инструмент;
–мерительный инструмент.
Запись выполняется по всей длине строки с возможностью переноса на следующую строку. Разделение информации по каждому средству технологической оснастки следует выполнять через знак «;».
Под символом «Р» записываются режимы резания в графах «D; В; L; Т; i; s; n; V». Все записи в ОК выполняются чертежным шрифтом.
Карта эскизов является графической иллюстрацией содержания технологической операции. Деталь на эскизах изображается в рабочем положении в любом масштабе. Обрабатываемые поверхности детали изображаются линией толщиной 2S.
Изображение детали должно содержать:
–размеры обрабатываемых поверхностей с предельными откло-
нениями;
–обозначение шероховатости;
–обозначение баз, опор и зажимов.
Эскизы обрабатываемой детали выполняются отдельно для всех установов или позиций, выполняемых на данной операции. При этом над эскизом делается запись «Установ А» или «Позиция 1». На одном листе КЭ допускается размещать несколько эскизов, относящихся к данной операции.
На эскизах все размеры обрабатываемых поверхностей условно нумеруются арабскими цифрами. Номер размера обрабатываемой поверхности проставляют в окружности диаметром 6–8 мм, расположенной на продолжении размерной линии.
17
Список литературы
1 Балабанов, А. Н. Краткий справочник технолога-машинострои- теля / А. Н. Балабанов. – М. : Изд-во стандартов, 1992. – 464 с.
2 Горбацевич, А. Ф. Курсовое проектирование по технологии машиностроения : учеб. пособие для машиностроительных специальностей вузов / А. Ф. Горбацевич, В. А. Шкред. – Минск : Выш. шк., 1983. – 256 с. : ил.
3 Горбацевич, А. Ф. Курсовое проектирование по технологии машиностроения / А. Ф. Горбацевич, А. А. Чеботарев, В. А. Шкред ; под общ. ред. А. А. Горбацевича. – Минск : Выш. шк., 1975. – 288 с. : ил.
4 Жолобов, А. А. Технология автоматизированного производства : учебник для вузов / А. А. Жолобов. – Минск : Дизайн ПРО, 2000. – 624 с.
5 Картавов, С. А. Технология машиностроения (спец. часть) / С. А. Картавов. – 2-е изд., перераб. и доп. – Киев : Вища шк., 1984. – 272 с.
6 Клименков, С. С. Проектирование и производство заготовок в машиностроении : учебник / С. С. Клименков. – Минск : Техноперспекти-
ва, 2008. – 407 с.
7 Колев, К. С. Технология машиностроения : учеб. пособие для ву-
зов / К. С. Колев. – М. : Высш. шк, 1977. – 256 с.
8 Новиков, М. П. Основы технологии сборки машин и механизмов / М. П. Новиков. – М. : Машиностроение, 1969. – 632 с.
9 Общемашиностроительные нормативы вспомогательного времени
ивремени на обслуживание рабочего места и подготовительно-заключи- тельного для технического нормирования. Массовое производство. – М. : Машиностроение, 1988. – 368 с.
10 Общемашиностроительные нормативы вспомогательного времени
ивремени на обслуживание рабочего места и подготовительно-заключи- тельного для технического нормирования. Серийное производство. – М. : Машиностроение, 1974. – 424 с.
11 Проектирование металлорежущих станков и станочных систем : справочник-учебник в 3 т. / Под общ. ред. А. С. Проникова. – М. : МГТУ им. Н. Э. Баумана ; Машиностроение, 1994. – Т. 1–2.
12 Режимы резания металлов : справочник / Под ред. Ю. В. Барановского. – М. : Машиностроение, 1972. – 408 с.
13 Справочник технолога-машиностроителя : в 2 т. / Под ред. А. Г. Косиловой и Р. К. Мещерякова. – М. : Машиностроение, 1985. – Т. 1. – 656 с.
14 Справочник технолога-машиностроителя : в 2 т. / Под ред. А. Г. Косиловой и Р. К. Мещерякова. – М. : Машиностроение, 1985. – Т. 2. – 496 с.
15 Технология автоматизированного машиностроения (спец. часть) / Под ред. А. А. Жолобова. – Минск : Дизайн ПРО, 1997. – 624 с.
18
16 Технология машиностроения : учебник для вузов в 2 т. Т. 2 : Производство машин / В. М. Бурцев [и др.] ; под ред. Г. Н. Мельникова. – 2-е изд., стереотип. – М. : МГТУ им. Н. Э. Баумана, 2001. – 640 с. : ил.
17 Технология машиностроения (спец. часть) : учебник для машиностроительных специальностей вузов / А. А. Гусев [и др.]. – М. : Машино-
строение, 1986. – 480 с. : ил.
18 Технология машиностроения : учеб. пособие / М. Ф. Пашкевич [и др.] ; под ред. М. Ф. Пашкевича. – Минск : Новое знание, 2008. – 478 с. : ил.
19 Технология машиностроения. Курсовое и дипломное проектирование : учеб. пособие / М. Ф. Пашкевич [и др.] ; под ред. М. Ф. Пашкевича. – Минск : Изд-во Гревцова, 2010. – 400 с. : ил.
20 Якобсон, М. О. Технология станкостроения / М. О. Якобсон. – 2-е изд., перераб. и доп. – М. : Машиностроение, 1966. – 475 с.
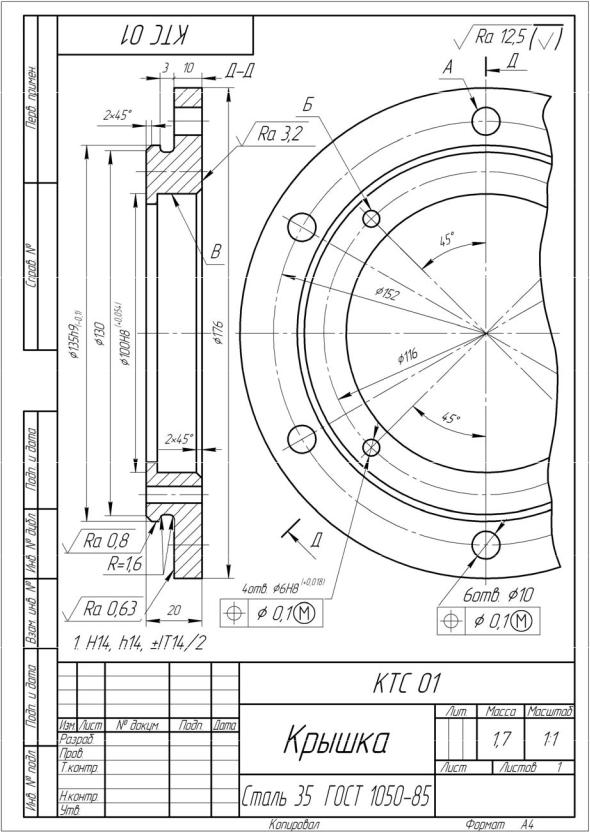
19
Приложение А
(справочное)
Рисунок А.1

20
Рисунок А.2