
КуРсОвОй ТММ
.pdf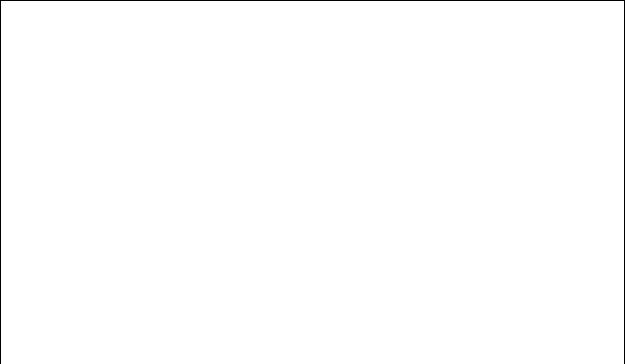
Продолжение Таблицы 5.4
Наименование параметра |
Обозн. |
Расчетная формула |
Значение |
|
|
|
|
|
|
|
dα1 |
dα1=d1+2·(h*a + x1-∆y)·m |
317,1687 |
|
Диаметр вершин зубьев |
|
|
|
|
dα2 |
dα1=d2+2·(h*a + x2-∆y)·m |
535,1687 |
||
|
||||
|
|
|
|
|
|
df1 |
dα1=d1-2·(h*a + c*- x1)·m |
228 |
|
Диаметр впадин |
|
|
|
|
df2 |
dα1=d2-2·(h*a + c*- x2)·m |
446 |
||
|
||||
|
|
|
|
|
Проверка вычислений |
|
|||
|
|
|
|
|
|
aw |
aw=c··m+0.5·( dα1+ df2) |
386,5843 |
|
Межосевое расстояние |
|
|
|
|
aw |
aw=c··m+0.5·( dα2+ df1) |
386,5843 |
||
|
||||
|
|
|
|
Таблица 5.5 - Расчет размеров для контроля взаимного положения разноименных профилей зубьев.
|
Sn1 |
Sn1=( |
|
+2·x1·tgα)·m |
37,9674 |
|
|
||||||
Нормальная толщина |
|
|
|
|
||
|
|
|
|
|
||
Sn2 |
Sn2=( |
|
+2·x2·tgα)·m |
29,96 |
||
|
||||||
|
|
|||||
|
|
|
|
|
||
|
|
|
|
|
|
Таблица 5.6 - Проверка качества зацепления по геометрическим показателям
Проверка отсутствия подрезания зубьев
Коэфф. наименьшего |
xmin1 |
xmin1=h*l - h*α-z1·sin2αt/(2·cosβ) |
0,2396 |
||||||||
Смещения шестерни |
|
|
|
|
|
|
|
|
|
|
|
Коэфф. наименьшего |
xmin2 |
xmin2=h*l-h*α-z2·sin2αt/(2·cosβ) |
-0,4622 |
||||||||
смещения колеса |
|
|
|
|
|
|
|
|
|
|
|
|
|
|
|
|
|
|
|
|
|||
Проверка отсутствия наложения зубьев |
|
||||||||||
|
|
|
|
|
|
|
|
|
|||
Радиус кривизны в |
ρl1 |
ρl1=0.5·d1·sinαt-m(h*l-h*α-x1)/sinαt |
12,3008 |
||||||||
граничной точке профиля |
|
|
|
|
|
|
|
|
|
|
|
|
ρl1=0.5·d1·sinαt-m(h*l-h*α-x1)/sinαt |
|
|||||||||
зуба |
ρl2 |
21,1813 |
|||||||||
|
|
|
|
|
|
|
|
|
|||
Коэфф. торцового |
εα |
εα= |
|
·(z1·tgαα1+ z2·tgαα2- zΣ·tgαtw) |
1,3739 |
||||||
перекрытия |
|
||||||||||
|
|
· |
|
|
|
|
|||||
|
|
|
|
|
|
|
|
|
|
|
|
|
|
|
|
|
|
|
+2·1· |
|
|
||
|
Snα1 |
Snα1=dα1·( |
2 |
+invαt-invαα1) |
7,8021 |
||||||
Нормальная толщина на |
|
|
1 |
|
|||||||
|
|
|
|
|
|
|
|
||||
|
|
|
|
|
|
|
|
|
|
|
|
поверхности вершин |
|
|
|
|
|
|
|
|
|||
Snα2 |
|
|
|
+ · · |
|
|
15,3832 |
||||
|
|
|
|
|
|
||||||
|
Snα2=dα2·( |
|
+invαt-invαα2) |
||||||||
|
|
|
|
|
|
|
|
|
|
|
|
|
|
|
|
|
|
|
|
|
|
|
31 |
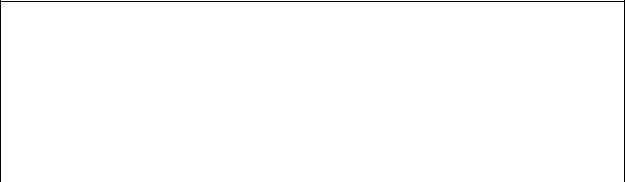
Таблица 5.7 - Расчет кинематических параметров.
Удельное скольжение
В нижней точке |
ϑp1 |
ϑp1= |
( − )·( + ) |
|
) |
2,3297 |
|||||||||
|
|
− ·( |
|
− |
|
||||||||||
активного профиля |
|
|
|
|
|
|
|
|
|
||||||
|
|
|
|
( − )·( + ) |
|
) |
|
||||||||
зуба |
ϑp2 |
ϑp2= |
|
3,1380 |
|||||||||||
|
− ·( |
|
− |
|
|||||||||||
|
|
|
|
|
|
|
|
|
|
||||||
|
ϑa1 |
ϑa1= |
( |
− ) |
· ( + |
|
) |
0,7583 |
|||||||
На вершине зуба |
|
|
|
|
|
||||||||||
|
|
|
|
|
|
|
|
|
|||||||
ϑa2 |
ϑa2= |
( |
− ) |
· ( + ) |
0,6997 |
||||||||||
|
|||||||||||||||
|
|
|
|
|
|||||||||||
|
|
|
|
|
|
|
|
|
|
|
|
Построение картины рабочего зацепления.
Выполненные расчеты позволяют построить картину рабочего зубчатого зацепления. Отметим оси О1 и О2 колес, расстояние между которыми определяет межосевое расстояние.
Из центров О1 и О2 проведем:
-начальные окружности (rw1 и rw2), соприкасающиеся в полюсе зацепления W;
-делительные окружности (r1 и r2), расстояние между которыми равно воспринимаемому смещению уm;
-окружности вершин (rа1 и rа2) и окружности впадин (rf1 и rf2),
расстояние между которыми соответственно определяет радиальные зазоры;
- основные окружности (rb1 и rb2), общая касательная к которым является линией зацепления N1N2 , проходящей через полюс зацепления
W. Точки Вp1 и Вp2 пересечения линии зацепления с окружностями вершин определяют активную линию зацепления.
После вычерчивания всех окружностей и линии зацепления, изобразим контуры профилей зубьев шестерни и колеса.
Вточках В1 и В2 изобразим рабочие профили зубьев в момент начала и
вмомент окончания зацепления зубьев.
Вычертим графики удельных скольжений профилей зубьев колес.
32
Положение линии зацепления N1N2 относительно общей касательной t-t
к начальным окружностям определяет угол зацепления αw. Измерим угол и получим αw =23032’.
Метод построения профиля зуба:
После того как построены, межосевое расстояние и все окружности из полюса (точки контакта) отложим половину толщины зуба по начальной окружности. Полученную точку соединим с центром колеса. От полученной прямой откладываем параллельные линии на расстояниях равным половине толщины зуба вершин, впадин и делительной окружности. Полученные точки соединим кривой и отобразим симметрично середины зуба, тем самым сформировав полную поверхность зуба. Далее путем копирования строим следующие зубья.
Коэффициент смещения Х влияет на форму профиля зуба нарезаемого колеса, на толщину зуба, на радиусы окружностей, впадины и вершины колес.
Коэффициент смещения Х не влияет на диаметры основной и делительной окружности.
Если ХΣ = Х1 + Х2 > 0, то эта передача с положительным смещением инструмента относительно нарезаемого колеса, угол зацепления больше профильного угла зацепления, αw > α;
Если ХΣ = 0, то передача равносмещенная, αw = α, rw = r, aw = a.
Если ХΣ < 0, то передача отрицательная и угол зацепления меньше профильного угла зацепления, αw < α.
Сумма смещений влияет на межосевое расстояние ХΣ > 0, то aw -
увеличивается, ХΣ <0, то aw -уменьшается). Также, сумма смещений влияет на длину теоретической и активной линии зацеплений. Положительная сумма смещений приводит к уменьшению активной части линий зацеплений,
а, следовательно, и к уменьшению коэффициента торцевых перекрытий.
Х > 0, то rа, rf – увеличиваются, Sa – заостряется, Sb, Sw –
увеличиваются. Х < 0, то rа, rf – уменьшается. Толщина ножки зуба уменьшается.
33
5.2 Проектирование планетарного механизма.
Проектирование планетарного механизма сводится к выбору чисел зубьев колес по заданному передаточному отношению при выполнении условий соосности колес, сборки передачи и соседства сателлитов.
Определим число зубьев колес, и количества сателлитов планетарного механизма.
Рассчитываем с помощью ЭВМ, путем выбора кинематической схемы и заданному передаточному отношению.
Механизм состоит из: Водило - Н; Центральное колесо – 1; Сателлиты – 2;
Неподвижное колесо – 3.
Выполним расчет на ЭВМ, результатом вычисления будет представлена таблица решений с определенными числами зубьев и количество возможных сателлитов в планетарном механизме.
Из нескольких вариантов, учитывая КПД механизма, габариты,
массу, число сателлитов и точность воспроизведения передаточного отношения выберем оптимальный вариант:
Таблица 5.2 – Определение количества зубьев колес и количество сателлитов.
Z1 |
Z2 |
Z3 |
k |
kmax |
ireal |
∆ |
|
|
|
|
|
|
|
18 |
45 |
108 |
2 |
3 |
7 |
0 |
|
|
|
|
|
|
|
18 |
45 |
108 |
3 |
3 |
7 |
0 |
|
|
|
|
|
|
|
20 |
50 |
120 |
2 |
3 |
7 |
0 |
|
|
|
|
|
|
|
21 |
50 |
126 |
3 |
4 |
7 |
0 |
|
|
|
|
|
|
|
22 |
55 |
132 |
2 |
3 |
7 |
0 |
|
|
|
|
|
|
|
24 |
60 |
144 |
2 |
3 |
7 |
0 |
|
|
|
|
|
|
|
24 |
60 |
144 |
3 |
3 |
7 |
0 |
|
|
|
|
|
|
|
26 |
60 |
156 |
2 |
3 |
7 |
0 |
|
|
|
|
|
|
|
34
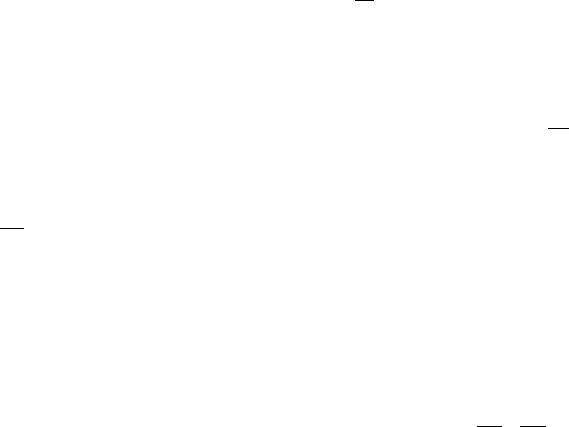
Из нескольких вариантов, учитывая КПД механизма, габариты,
массу, число сателлитов и точность воспроизведения передаточного отношения выберем оптимальный вариант.
В процессе проектирования необходимо выполнение условий сборки соосности и соседство сателлитов.
Выбираем исходные данные для расчетов из таблицы (5.2):
1)Определение передаточного отношения механизма, i1H = 7;
2)Выбор чисел зубьев и количества сателлитов.
Z1= 18; Z1=45; Z1=108; k = 3.
По рассчитанному передаточному отношению на ЭВМ выполним расчет планетарного механизма.
По выбранным значениям строим кинематическую схему планетарного механизма в двух проекциях в масштабе:
µI=1,
мм
Строим план скоростей на проекции кинематической схемы механизма.
Для звена 1 имеются две точки, скорости которых известны.
Линейная скорость в точке О равна нулю. Из точки А отложим вектор линейной скорости произвольной длинны. Соединим конец вектора Аа с
точкой О, а так же с точкой С. В точке С линейная скорость равна нулю , так как тоска принадлежит неподвижному колесу. Из точки В проводим вектор
до пересечения с только что построенной линией. Соединим полученную точку b с точкой О. Таким образом мы получили закон распределения линейных скоростей точек в механизме.
Сроим лучевую диаграмму:
Произвольно ставим точку Р. Строим координатные оси, по вертикали ось радиусов РR, по горизонтали ось линейных скоростей VP. Строим прямые проходящие через точку Р, параллельно векторам О и .
Произвольно на координатной прямой PR строим точку S. Из точки S
проводим перпендикуляр к PR так что бы были пересечены обе построенные
35
прямые, пересечения обозначим как H и 1.
Определим передаточное число планетарного механизма.
Передаточное отношение можно определить отношением тангенсов углов
«φ1» и «φH», или отношением полученных отрезков «1S» и «НS» из лучевой диаграммы.
Определим передаточное отношение: |
|
|
|
|
||||||||||
|
г |
|
= |
|
( ) |
, |
(5.1) |
|||||||
|
|
|
|
|
|
|
|
|||||||
|
|
Н |
|
|
( ) |
|
||||||||
|
|
|
|
|
|
|
||||||||
г |
= |
, |
|
|
= 6,9989 |
|
||||||||
|
|
|
|
|
||||||||||
Н |
|
|
, |
|
|
|
|
|||||||
|
|
|
|
|
|
|
||||||||
Относительная погрешность вычислений графических построений |
|
|||||||||||||
составляет: |
|
|
|
|
|
|
|
|
|
|
|
|
|
|
∆= |
|
− г Н |
|
·100% , |
(5.2) |
|||||||||
|
|
|
||||||||||||
|
|
|
|
|
|
|
||||||||
∆= |
−, |
·100% , |
|
|||||||||||
|
|
|
|
|||||||||||
|
|
|
|
|
|
|
||||||||
|
∆= 0,016% . |
|
||||||||||||
Проверим выполнение следующих условий: |
|
|||||||||||||
1) Соосности колес |
|
|
|
|
|
|
|
|
|
|
|
|
|
|
z3-z2=z1+z2 , |
(5.3) |
|||||||||||||
108 – 45 = 18 + 45. |
|
|||||||||||||
2) Соседства сателлитов |
|
|
|
|
|
|
|
|
|
|
|
|
|
|
(z1+z2)·sin |
|
>z2+2·h*α , |
(5.4) |
|||||||||||
|
||||||||||||||
|
|
|
|
|
|
|
|
|
|
|||||
где, k - число сателлитов; |
|
|
|
|
|
|
|
|
|
|
|
|
|
|
h*α -коэффициент высоты головки. |
|
|
|
|
|
|
|
|
|
|
|
|||
(18 + 45)∙ sin |
|
> 45 + 2∙1. |
|
|||||||||||
|
|
|||||||||||||
54,5596 > 47 |
|
|||||||||||||
3) Сборки передачи |
|
|
|
|
|
|
|
|
|
|
|
|
|
|
|
|
|
z1+ z3=ck, |
(5.5) |
||||||||||
где, с - целое число; |
|
|
|
|
|
|
|
|
|
|
|
|
|
|
18 + 108 = с ∙ 3,
с = 42.
Все требуемые условия выполнены.
36

Рисунок 5.1 – Кинематическая схема планетарного механизма Определили геометрические параметры эвольвентой зубчатой передачи
и построили картину рабочего зацепления. Спроектировали планетарный механизм, выбрав числа зубьев z1= 18, z2=45 , z3= 108, и три сателлита. Вычертили схему механизма и графическим путем определили передаточное
отношение планетарного механизма г =6,9989. Сравнили результаты и
Н
получили погрешность ∆= 0,016%. Проверили выполнение условий соосности колес, соседства сателлитов и сборки передачи.
37

6 Динамический синтез кулачкового механизма
Синтез кулачкового механизма заключается в определении основных геометрических параметров кулачкового механизма и построении профиля кулачка, обеспечивающего заданный закон движения толкателя. Основные геометрические параметры кулачкового механизма определяют по заданному закону движения и условию обеспечения допустимого угла давления для механизмов с роликовыми толкателями.
Для толкателя характерными являются 4 фазы движения:
1)фаза подъема (удаления), определяемая углом поворота кулачка φуд;
2)фаза верхнего выстоя – φв.в.;
3)фаза опускания (приближения) – φпр;
4)фаза ближнего стояния – φбс.
Выбор закона движения толкателя при подъеме и опускании является одним из важных этапов при проектировании современных машин.
Если задан закон движения толкателя в виде диаграмм изменения аналогов ускорения, то одно- и двукратным интегрированием ее получаем диаграммы аналогов скорости и перемещения. Для определения постоянных интегрирования задаемся начальными условиями. В начальный момент времени при t0 = 0 в нижнем положении толкателя его скорость и перемещение равны нулю.
Исходные данные для проектирования:
Ход толкателя hT = 0,025 м,
Угловая скорость вращения кулачка ωк = 10 радс ,
Угол удаления и приближения φуд = φпр = 1500,
Угол верхнего стояния φвв = 100, Рабочий угол раб = φуд + φвв + φпр = 3100, Угол давления αmax= 250.
38

6.1Построение кинематических диаграмм толкателя
По заданному закону движения толкателя в виде ускорений
2 = f(φk) вычертим диаграмму ускорений. Для этого определим масштаб μφ
2
по формуле:
|
|
|
|
|
|
|
|
|
|
|
|
|
раб ∙ |
|
|
|
|
|
|
|
|
|
|
|
|
|
|
|
||||||||
|
|
|
|
|
|
|
|
|
|
μφ = |
|
|
|
|
|
, |
|
|
|
|
|
|
|
|
|
|
|
|
|
|
(6.1) |
|||||
|
|
|
|
|
|
|
180 ∙ |
|
|
|
|
|
|
|
|
|
|
|
|
|
||||||||||||||||
где раб – рабочий угол поворота кулачка, раб = 3100; |
|
|
|
|
|
|||||||||||||||||||||||||||||||
|
|
L – отрезок на оси абсцисс в мм, соответствующий рабочему углу. |
||||||||||||||||||||||||||||||||||
Примем L = 155 мм. |
|
|
|
|
|
|
|
|
|
|
|
|
|
|
|
|
|
|
|
|
|
|
|
|
|
|
|
|
|
|
|
|||||
Подставим числовые значения в формулу (6.1) получим: |
|
|
|
|
|
|||||||||||||||||||||||||||||||
|
|
|
|
|
|
μφ = |
310 ∙ 3,14 |
= 0,035 |
|
рад |
|
|
|
|
|
|
|
|
||||||||||||||||||
|
|
|
|
|
|
|
|
|
|
|
|
|
|
|
|
|
|
|
|
|
|
|
|
|
|
|
||||||||||
|
|
|
|
|
|
180 ∙155 |
|
|
|
|
мм |
|
|
|
|
|
|
|
|
|||||||||||||||||
|
|
Интегрируем графически диаграмму |
2 |
= |
|
2 |
|
( ) , получаем график |
||||||||||||||||||||||||||||
|
|
2 |
|
2 |
|
|||||||||||||||||||||||||||||||
|
= |
|
|
, проинтегрировав так же зависимость |
|
|
= |
|
|
, получим |
||||||||||||||||||||||||||
|
|
|
|
|
||||||||||||||||||||||||||||||||
|
|
|
|
|
|
|
|
|
|
|
|
|
|
|
|
|
|
|
|
|
|
|
|
|
|
|
|
|
|
|||||||
диаграмму перемещений толкателя S=S(φ). |
|
|
|
|
|
|
|
|
|
|
|
|
|
|
|
|||||||||||||||||||||
|
|
Определим масштабы диаграмм. |
|
|
|
|
|
|
|
|
|
|
|
|
|
|
|
|
|
|
|
|
|
|
|
|||||||||||
|
|
Масштаб оси ординат диаграммы перемещений определим по формуле: |
||||||||||||||||||||||||||||||||||
|
|
|
|
|
|
μs = |
|
|
|
, |
|
|
|
|
|
|
|
|
|
|
|
|
|
|
|
|
|
|
|
(6.2) |
||||||
|
|
|
|
|
|
|
|
|
|
|
|
|
|
|
|
|
|
|
|
|
|
|
|
|
|
|
||||||||||
|
|
|
|
|
|
|
|
|
|
|
|
|
|
|
|
|
|
|
|
|
|
|
|
|
|
|
|
|
|
|
|
|
|
|||
где |
|
|
- отрезок на оси ординат, изображающий максимальное |
|||||||||||||||||||||||||||||||||
|
|
|
|
|
|
|
|
|
|
|
|
|
|
|
|
|
|
|
|
|
|
|
|
|
|
|
|
|
|
|
|
|
|
|
||
перемещение, |
= 45,01 мм; |
|
|
|
|
|
|
|
|
|
|
|
|
|
|
|
|
|
|
|
|
|
|
|
|
|
|
|||||||||
|
|
|
|
|
|
|
|
|
|
|
|
|
|
|
|
|
|
|
|
|
|
|
|
|
|
|
|
|
|
|
|
|
|
|
|
|
|
|
- ход толкателя, = 0,025 м. |
|
|
|
|
|
|
|
|
|
|
|
|
|
|
|
|
|
|
|
|
|
|||||||||||||
Подставим, получим: |
|
|
|
|
|
|
|
|
|
|
|
|
|
|
|
|
|
|
|
|
|
|
|
|
|
|
||||||||||
|
|
|
|
|
|
μs = |
0,025 |
= 0,000555 |
м |
. |
|
|
|
|
|
|
|
|
||||||||||||||||||
|
|
|
|
|
|
45,01 |
мм |
|
|
|
|
|
|
|
|
|||||||||||||||||||||
|
Масштаб оси ординат диаграммы аналога скорости |
|
|
= |
|
|
||||||||||||||||||||||||||||||
|
|
|
|
|||||||||||||||||||||||||||||||||
|
|
|
|
|
|
|
|
|
|
|
|
|
|
|
|
|
|
|
|
|
|
|
|
|
|
|
|
|
|
|
|
|
||||
определим по формуле: |
|
|
|
|
|
|
|
|
|
|
|
|
|
|
|
|
|
|
|
|
|
|
|
|
|
|
||||||||||
|
|
|
|
|
|
|
|
|
= |
|
|
|
|
|
; |
|
|
|
|
|
|
|
|
|
|
|
|
|
(6.3) |
|||||||
|
|
|
|
|
|
|
|
|
|
|
|
|
|
|
|
|
|
|
|
|
|
|
|
|
||||||||||||
|
|
|
|
|
|
|
|
|
|
|
|
|
|
|
|
|
|
|
|
|
|
|
|
|
|
|||||||||||
|
|
|
|
|
|
|
|
|
|
|
|
|
∙ |
|
|
|
|
|
|
|
|
|
|
|
|
|
|
|
||||||||
|
|
|
|
|
|
|
|
|
|
|
|
|
|
|
|
|
|
|
|
|
|
|
|
|
|
|
||||||||||
|
|
|
|
|
|
|
|
|
|
|
|
|
|
|
|
|
|
|
|
|
|
|
|
|
|
|
|
|
|
|
|
|
|
|
||
|
где |
- полюсное расстояние при интегрировании графика скорости. |
Примем = 25 мм.
39
Подставим числовые значения в формулу (6.3) получим:
|
|
= |
0,000555 |
= 0,000636 |
м |
. |
||||||||||||
|
|
|
|
|
|
|
||||||||||||
|
|
|
|
0,035 ∙ 25 |
|
|
|
|
|
|
|
|
мм |
|||||
|
|
|
|
|
|
|
|
|
|
|
|
|||||||
|
|
|
|
|
|
|
|
|
|
|
|
|
|
|
|
|
|
|
|
|
|
|
|
|
|
|
2 |
|
2 |
|
|
||||||
Масштаб оси ординат диаграммы |
|
|
|
|
= |
|
|
( ) определим по формуле: |
||||||||||
|
2 |
2 |
||||||||||||||||
|
|
|
|
|
|
|
|
|
|
|
|
|
|
|
|
|||
|
|
|
|
2 |
= |
|
|
|
|
|
, |
|
(6.4) |
|||||
|
|
|
|
|
∙ |
|
|
|||||||||||
|
|
|
|
|
2 |
|
|
|
|
|
|
|
|
|
||||
|
|
|
|
|
|
|
|
|
|
|
|
|
|
|
|
|
||
где |
- полюсное расстояние при интегрировании графика ускорений, |
= 25 мм.
Подставим числовые значения в формулу (6.4) получим:
|
|
|
|
|
|
|
2 = |
0,000636 |
= 0,000729 |
м |
. |
||
|
|
|
|
|
|
|
|
|
|||||
|
|
|
|
|
|
|
|
|
|
0,035 ∙ 25 |
|
мм |
|
|
|
|
|
|
|
|
|
2 |
|||||
|
|
|
|
|
|
|
|
|
|
|
|
||
|
Угловую скорость кулачка принимаем постоянной (ωk=const). При этом |
||||||||||||
условии φ = ω ∙ t |
и оси абсцисс являются также осями времени, а диаграммы |
||||||||||||
|
= |
|
, |
2 |
= |
2 |
( ), являются диаграммами скорости и ускорения |
||||||
|
|
2 |
2 |
толкателя. |
|
|
|
|
|
|
|
||||
Тогда масштаб времени: |
|
|
|
|
|
|
|
||||
|
|
|
|
|
|
= |
|
, |
(6.5) |
||
|
|
|
|
|
|
|
|||||
|
|
|
|
|
|
|
|
к |
|
||
|
|
|
|
|
|
|
|
|
|||
где ωк = 10 рад/с. |
|
|
|
|
|
|
|
||||
|
|
|
= |
0,035 |
= 0,0035 с/мм |
||||||
|
|||||||||||
|
|
|
|
|
|
|
10 |
|
|
|
|
Масштаб скорости толкателя: |
|
|
|
|
|
||||||
μv = ∙ ωк = 0,00636 |
(мс-1)/мм |
||||||||||
|
|
|
|
|
|
|
|
|
|
||
Масштаб ускорений толкателя: |
|
|
|
|
|
||||||
μа = 2 |
∙ к2 |
= 0,0729 (мс-2)/мм |
|||||||||
|
|
2 |
|
|
|
|
|
|
|
|
40