
pidruchnik
.pdf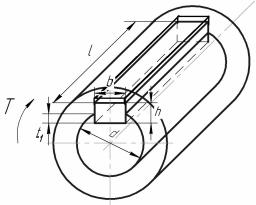
Рис. 4.23. Розрахункова схема ненапруженого шпонкового з’єднання
Допустимі напруження для ненапружених нерухомих шпонко вих з’єднань вибираються за рекомендаціями, виробленими прак тикою:
за спокійного навантаження; під час перехідних посадок маточини на вал [σ]зм = (100...120) МПа (стальна маточина) і [σ]зм = (70...80) МПа (чавунна маточина); під час посадок з
гарантованим натягом [σ]зм = (160...180) МПа (стальна мато чина) і [σ]зм = (110...130) МПа (чавунна маточина);
за помірних коливань навантаження допустимі напру ження зменшуються на 30%, за значних коливань і удар них навантажень – на 60%.
4.2.3. Розрахунок напружених шпонкових з’єднань
У результаті запресовування клинової шпонки на її робочих гранях (верхній та нижній) виникають рівномірно розподілені на пруження зминання.
Для спрощення розрахунку приймають, що під час передачі шпонковим з’єднанням обертального моменту Т напруження зми нання за шириною поверхні робочих граней шпонки розподіля
391
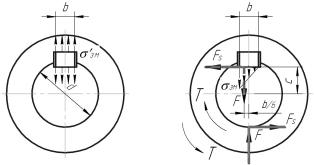
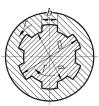
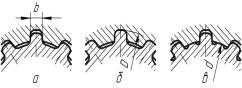
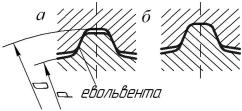
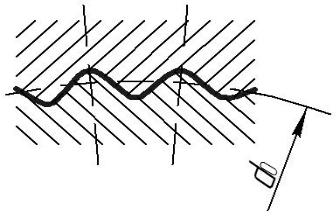
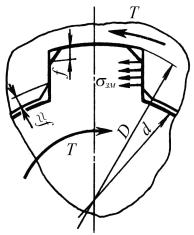

