
- •Why CFD is Important for Modeling
- •How the CFD Module Helps Improve Your Modeling
- •Model Builder Options for Physics Feature Node Settings Windows
- •Where Do I Access the Documentation and Model Library?
- •Typographical Conventions
- •Quick Start Guide
- •Modeling Strategy
- •Geometrical Complexities
- •Material Properties
- •Defining the Physics
- •Meshing
- •The Choice of Solver and Solver Settings
- •Coupling to Other Physics Interfaces
- •Adding a Chemical Species Transport Interface
- •Equation
- •Discretization
- •Transport Feature
- •Migration in Electric Field
- •Reactions
- •Reactions
- •Initial Values
- •Initial Values
- •Boundary Conditions for the Transport of Concentrated Species Interface
- •Mass Fraction
- •Mass Fraction
- •Flux
- •Inflow
- •Inflow
- •No Flux
- •Outflow
- •Flux Discontinuity
- •Flux Discontinuity
- •Symmetry
- •Open Boundary
- •Physical Model
- •Transport Properties
- •Model Inputs
- •Fluid Properties
- •Diffusion
- •Migration in Electric Field
- •Diffusion
- •Model Inputs
- •Density
- •Diffusion
- •Porous Matrix Properties
- •Porous Matrix Properties
- •Initial Values
- •Initial Values
- •Domain Features for the Reacting Flow, Concentrated Species Interface
- •Boundary Conditions for the Reacting Flow, Concentrated Species Interface
- •Reacting Boundary
- •Inward Flux
- •Physical Model
- •Transport Properties
- •Fluid Properties
- •Migration in Electric Field
- •Porous Matrix Properties
- •Initial Values
- •Domain Features for the Reacting Flow, Diluted Species Interface
- •Boundary Conditions for the Reacting Flow, Diluted Species Interface
- •Pair and Point Conditions for the Reacting Flow, Diluted Species Interface
- •Multicomponent Mass Transport
- •Multicomponent Diffusion: Mixture-Average Approximation
- •Multispecies Diffusion: Fick’s Law Approximation
- •Multicomponent Thermal Diffusion
- •References for the Transport of Concentrated Species Interface
- •Domain Equations
- •Combined Boundary Conditions
- •Effective Mass Transport Parameters in Porous Media
- •Selecting the Right Interface
- •The Single-Phase Flow Interface Options
- •Laminar Flow
- •Coupling to Other Physics Interfaces
- •The Laminar Flow Interface
- •Discretization
- •The Creeping Flow Interface
- •Discretization
- •Fluid Properties
- •Fluid Properties
- •Mixing Length Limit
- •Volume Force
- •Volume Force
- •Initial Values
- •Initial Values
- •The Turbulent Flow, Spalart-Allmaras Interface
- •The Rotating Machinery, Laminar Flow Interface
- •Rotating Domain
- •Rotating Domain
- •Initial Values
- •Initial Values
- •Rotating Wall
- •Wall
- •Boundary Condition
- •Interior Wall
- •Boundary Condition
- •Inlet
- •Boundary Condition
- •Velocity
- •Pressure, No Viscous Stress
- •Normal Stress
- •Outlet
- •Boundary Condition
- •Pressure
- •Laminar Outflow
- •No Viscous Stress
- •Vacuum Pump
- •Symmetry
- •Open Boundary
- •Boundary Stress
- •Boundary Condition
- •Periodic Flow Condition
- •Flow Continuity
- •Pressure Point Constraint
- •Non-Newtonian Flow—The Power Law and the Carreau Model
- •Theory for the Pressure, No Viscous Stress Boundary Condition
- •Theory for the Laminar Inflow Condition
- •Theory for the Laminar Outflow Condition
- •Theory for the Slip Velocity Wall Boundary Condition
- •Theory for the Vacuum Pump Outlet Condition
- •Theory for the No Viscous Stress Condition
- •Theory for the Mass Flow Inlet Condition
- •Turbulence Modeling
- •Eddy Viscosity
- •Wall Functions
- •Initial Values
- •Wall Distance
- •Inlet Values for the Turbulence Length Scale and Intensity
- •Initial Values
- •The Spalart-Allmaras Turbulence Model
- •Inlet Values for the Turbulence Length Scale and Intensity
- •Pseudo Time Stepping for Turbulent Flow Models
- •References for the Single-Phase Flow, Turbulent Flow Interfaces
- •Selecting the Right Interface
- •Coupling to Other Physics Interfaces
- •Discretization
- •Fluid-Film Properties
- •Initial Values
- •Initial Values
- •Inlet
- •Outlet
- •Wall
- •Symmetry
- •Discretization
- •Initial Values
- •Initial Values
- •Fluid-Film Properties
- •Border
- •Inlet
- •Outlet
- •Conditions for Film Damping
- •The Reynolds Equation
- •Structural Loads
- •Gas Outflow Conditions
- •Rarefaction and Slip Effects
- •Geometry Orientations
- •References for the Thin-Film Flow Interfaces
- •Selecting the Right Interface
- •The Multiphase Flow Interface Options
- •The Relationship Between the Interfaces
- •Bubbly Flow
- •Coupling to Other Physics Interfaces
- •The Laminar Two-Phase Flow, Level Set Interface
- •Discretization
- •The Laminar Two-Phase Flow, Phase Field Interface
- •Domain Level Settings for the Level Set and Phase Field Interfaces
- •Fluid Properties
- •Mixing Length Limit
- •Initial Values
- •Initial Values
- •Volume Force
- •Volume Force
- •Gravity
- •Boundary Conditions for the Level Set and Phase Field Interfaces
- •Wall
- •Boundary Condition
- •Initial Interface
- •The Turbulent Flow, Two-Phase Flow, Level Set Interface
- •The Turbulent Two-Phase Flow, Phase Field Interface
- •Wall Distance Interface and the Distance Equation
- •Level Set and Phase Field Equations
- •Conservative and Non-Conservative Formulations
- •Phase Initialization
- •Numerical Stabilization
- •References for the Level Set and Phase Field Interfaces
- •Stabilization
- •Discretization
- •Level Set Model
- •Initial Values
- •Initial Values
- •Boundary Conditions for the Level Set Function
- •Inlet
- •Initial Interface
- •No Flow
- •Outlet
- •Symmetry
- •Discretization
- •Initial Values
- •Initial Values
- •Phase Field Model
- •Boundary Conditions for the Phase Field Function
- •Initial Interface
- •Inlet
- •Wetted Wall
- •Wetted Wall
- •Outlet
- •The Level Set Method
- •Conservative and Non-Conservative Form
- •Initializing the Level Set Function
- •Variables For Geometric Properties of the Interface
- •Reference for the Level Set Interface
- •About the Phase Field Method
- •The Equations for the Phase Field Method
- •Conservative and Non-Conservative Forms
- •Additional Sources of Free Energy
- •Variables and Expressions
- •Reference For the Phase Field Interface
- •The Laminar Bubbly Flow Interface
- •Reference Pressure
- •Discretization
- •The Turbulent Bubbly Flow Interface
- •Reference Pressure
- •Discretization
- •Fluid Properties
- •Slip Model
- •Initial Values
- •Initial Values
- •Volume Force
- •Volume Force
- •Gravity
- •Gravity
- •Mass Transfer
- •Mass Transfer
- •Boundary Conditions for the Bubbly Flow Interfaces
- •Wall
- •Liquid Boundary Condition
- •Gas Boundary Condition
- •Inlet
- •Liquid Boundary Condition
- •Gas Boundary Condition
- •Outlet
- •Liquid Boundary Condition
- •Gas Boundary Condition
- •Symmetry
- •Gas Boundary Conditions Equations
- •The Mixture Model, Laminar Flow Interface
- •Stabilization
- •Discretization
- •The Mixture Model, Turbulent Flow Interface
- •Stabilization
- •Mixture Properties
- •Mass Transfer
- •Mass Transfer
- •Initial Values
- •Initial Values
- •Volume Force
- •Volume Force
- •Gravity
- •Gravity
- •Boundary Conditions for the Mixture Model Interfaces
- •Wall
- •Mixture Boundary Condition
- •Dispersed Phase Boundary Condition
- •Inlet
- •Mixture Boundary Condition
- •Dispersed Phase Boundary Condition
- •Outlet
- •Mixture Boundary Condition
- •Symmetry
- •The Bubbly Flow Equations
- •Turbulence Modeling in Bubbly Flow Applications
- •References for the Bubbly Flow Interfaces
- •The Mixture Model Equations
- •Dispersed Phase Boundary Conditions Equations
- •Turbulence Modeling in Mixture Models
- •Slip Velocity Models
- •References for the Mixture Model Interfaces
- •Dispersed Phase
- •Discretization
- •Domain Conditions for the Euler-Euler Model, Laminar Flow Interface
- •Phase Properties
- •Solid Viscosity Model
- •Drag Model
- •Solid Pressure Model
- •Initial Values
- •Boundary, Point, and Pair Conditions for the Euler-Euler Model, Laminar Flow Interface
- •Wall
- •Dispersed Phase Boundary Condition
- •Inlet
- •Two-Phase Inlet Type
- •Continuous Phase
- •Dispersed Phase
- •Outlet
- •Mixture Boundary Condition
- •The Euler-Euler Model Equations
- •References for the Euler-Euler Model, Laminar Flow Interface
- •Selecting the Right Interface
- •The Porous Media Flow Interface Options
- •Coupling to Other Physics Interfaces
- •Discretization
- •Fluid and Matrix Properties
- •Mass Source
- •Mass Source
- •Initial Values
- •Initial Values
- •Boundary Conditions for the Darcy’s Law Interface
- •Pressure
- •Pressure
- •Mass Flux
- •Mass Flux
- •Inflow Boundary
- •Inflow Boundary
- •Symmetry
- •No Flow
- •Discretization
- •Fluid and Matrix Properties
- •Volume Force
- •Volume Force
- •Forchheimer Drag
- •Forchheimer Drag
- •Initial Values
- •Initial Values
- •Mass Source
- •Boundary Conditions for the Brinkman Equations Interface
- •Discretization
- •Fluid Properties
- •Porous Matrix Properties
- •Porous Matrix Properties
- •Forchheimer Drag
- •Forchheimer Drag
- •Volume Force
- •Volume Force
- •Initial Values
- •Initial Values
- •Boundary Conditions for the Free and Porous Media Flow Interface
- •Microfluidic Wall Conditions
- •Boundary Condition
- •Discretization
- •Domain, Boundary, and Pair Conditions for the Two-Phase Darcy’s Law Interface
- •Fluid and Matrix Properties
- •Initial Values
- •Initial Values
- •No Flux
- •Pressure and Saturation
- •Pressure and Saturation
- •Mass Flux
- •Inflow Boundary
- •Inflow Boundary
- •Outflow
- •Pressure
- •Darcy’s Law—Equation Formulation
- •About the Brinkman Equations
- •Brinkman Equations Theory
- •References for the Brinkman Equations Interface
- •Reference for the Free and Porous Media Flow Interface
- •Darcy’s Law—Equation Formulation
- •The High Mach Number Flow, Laminar Flow Interface
- •Surface-to-Surface Radiation
- •Discretization
- •Initial Values
- •Initial Values
- •Shared Interface Features
- •Fluid
- •Dynamic Viscosity
- •Inlet
- •Outlet
- •Consistent Inlet and Outlet Conditions
- •Pseudo Time Stepping for High Mach Number Flow Models
- •References for the High Mach Number Flow Interfaces
- •Selecting the Right Interface
- •The Non-Isothermal Flow Interface Options
- •Coupling to Other Physics Interfaces
- •The Non-Isothermal Flow, Laminar Flow Interface
- •Discretization
- •The Conjugate Heat Transfer, Laminar Flow Interface
- •The Turbulent Flow, Spalart-Allmaras Interface
- •Fluid
- •Dynamic Viscosity
- •Wall
- •Boundary Condition
- •Initial Values
- •Pressure Work
- •Viscous Heating
- •Dynamic Viscosity
- •Turbulent Non-Isothermal Flow Theory
- •References for the Non-Isothermal Flow and Conjugate Heat Transfer Interfaces
- •Selecting the Right Interface
- •The Heat Transfer Interface Options
- •Conjugate Heat Transfer, Laminar Flow
- •Conjugate Heat Transfer, Turbulent Flow
- •Coupling to Other Physics Interfaces
- •Accessing the Heat Transfer Interfaces via the Model Wizard
- •Discretization
- •Heat Transfer in Solids
- •Translational Motion
- •Translational Motion
- •Pressure Work
- •Heat Transfer in Fluids
- •Viscous Heating
- •Dynamic Viscosity
- •Heat Source
- •Heat Source
- •Initial Values
- •Initial Values
- •Boundary Conditions for the Heat Transfer Interfaces
- •Temperature
- •Temperature
- •Thermal Insulation
- •Outflow
- •Symmetry
- •Heat Flux
- •Heat Flux
- •Inflow Heat Flux
- •Inflow Heat Flux
- •Open Boundary
- •Periodic Heat Condition
- •Surface-to-Ambient Radiation
- •Boundary Heat Source
- •Boundary Heat Source
- •Heat Continuity
- •Pair Thin Thermally Resistive Layer
- •Pair Thin Thermally Resistive Layer
- •Thin Thermally Resistive Layer
- •Thin Thermally Resistive Layer
- •Line Heat Source
- •Line Heat Source
- •Point Heat Source
- •Convective Cooling
- •Out-of-Plane Convective Cooling
- •Upside Heat Flux
- •Out-of-Plane Radiation
- •Upside Parameters
- •Out-of-Plane Heat Flux
- •Domain Selection
- •Upside Inward Heat Flux
- •Change Thickness
- •Change Thickness
- •Porous Matrix
- •Heat Transfer in Fluids
- •Thermal Dispersion
- •Dispersivities
- •Heat Source
- •Equation Formulation
- •Activating Out-of-Plane Heat Transfer and Thickness

T = ˜ fv1
The default values for the modeling parameters are:
cb1 = 0 |
.1355 |
cb2 = 0.622 |
cv2 = 7.1 = 2 3 |
cw2 = 0.3 |
cw3 = 2 |
v = 0.41 |
Pseudo Time Stepping for Turbulent Flow Models is the default applied to the stationary form of the Spalart-Allmaras model.
W A L L B O U N D A R Y C O N D I T I O N S
The Spalart-Allmaras model is consistent with a no-slip boundary condition, that is
u 0. Since, there can be no fluctuations on the wall, the boundary condition for is
0.
The Spalart-Allmaras model can be considered to be well resolved at a wall if lc* in order of unity. lc* is the distance, measured in viscous units, from the wall to the center of the wall adjacent cell and can be evaluated as the boundary variable
Dimensionless distance to cell center. See also Wall for boundary condition details.
I N I T I A L V A L U E S
The default initial values for the Spalart-Allmaras interface are
u = 0 p = 0
˜
= --
Inlet Values for the Turbulence Length Scale and Intensity
A value of 0.1% is a low turbulence intensity IT. Good wind tunnels can produce values of as low as 0.05%. Fully turbulent flows usually have intensities between five and ten percent.
The turbulent length scale LT is a measure of the size of the eddies that are not resolved. For free-stream flows these are typically very small (in the order of
T H E O R Y F O R T H E TU R B U L E N T F L O W I N T E R F A C E S | 157

centimeters). The length scale cannot be zero, however, because that would imply infinite dissipation. Use the following table as a guideline when specifying LT (Ref. 3):
TABLE 4-9: TURBULENT LENGTH SCALES FOR TWO-DIMENSIONAL FLOWS
FLOW CASE |
|
LT |
L |
Mixing layer |
|
0.07L |
Layer width |
|
|
|
|
Plane jet |
|
0.09L |
Jet half width |
|
|
|
|
Wake |
|
0.08L |
Wake width |
|
|
|
|
Axisymmetric jet |
|
0.075L |
Jet half width |
|
|
|
|
Boundary layer ( p x 0) |
|
lw 1 – exp –lw+ 26 |
|
– Viscous sublayer and log-layer |
|
Boundary layer |
|
– Outer layer |
|
0.09L |
thickness |
|
|
|
|
Pipes and channels |
|
0.07L |
Pipe diameter or |
(fully developed flows) |
|
|
channel width |
|
|
|
|
where lw is the wall distance, and lw+ |
= lw l* is the wall distance in viscous units. |
Pseudo Time Stepping for Turbulent Flow Models
Pseudo time stepping is per default applied to the turbulence equations for stationary
problems, both for 2D models as well as 3D models. The turbulence equations use the
same ˜ as the momentum and continuity equations. t
If the automatic expression for CFLloc is
1.3min niterCMP-1 9 +
if niterCMP 25 9 1.3min niterCMP – 25 9 0 + if niterCMP 50 90 1.3min niterCMP – 50 9 0
for 2D and
1.3min niterCMP-1 9 +
if niterCMP 30 9 1.3min niterCMP – 30 9 0 + if niterCMP 60 90 1.3min niterCMP – 60 9 0
for 3D.
158 | C H A P T E R 4 : S I N G L E - P H A S E F L O W B R A N C H

References for the Single-Phase Flow, Turbulent Flow Interfaces
1.D.C. Wilcox, Turbulence Modeling for CFD, 2nd ed., DCW Industries, 1998.
2.D.M. Driver and H.L. Seegmiller, “Features of a Reattaching Turbulent Shear Layer in Diverging Channel Flow,” AIAA Journal, vol. 23, pp. 163–171, 1985.
3.H.K. Versteeg and W. Malalasekera, An Introduction to Computational Fluid Dynamics, Prentice Hall, 1995.
4.A. Durbin, “On the k- Stagnation Point Anomality,” International Journal of Heat and Fluid Flow, vol. 17, pp. 89–90, 1986.
5.A, Svenningsson, Turbulence Transport Modeling in Gas Turbine Related Applications,” doctoral dissertation, Department of Applied Mechanics, Chalmers University of Technology, 2006.
6.C. H. Park and S.O. Park, “On the Limiters of Two-equation Turbulence Models,”
International Journal of Computational Fluid Dynamics, vol. 19, No. 1, pp. 79– 86, 2005.
7.J. Larsson, Numerical Simulation of Turbulent Flows for Turbine Blade Heat Transfer, doctoral dissertation, Chalmers University of Technology, Sweden, 1998.
8.L. Ignat, D. Pelletier, and F. Ilinca, “A Universal Formulation of Two-equation Models for Adaptive Computation of Turbulent Flows,” Computer Methods in Applied Mechanics and Engineering, vol. 189, pp. 1119–1139, 2000.
9.D. Kuzmin, O. Mierka, and S. Turek, “On the Implementation of the k-
Turbulence Model in Incompressible Flow Solvers Based on a Finite Element Discretization,” International Journal of Computing Science and Mathematics, vol. 1, no. 2–4, pp. 193–206, 2007.
10.H. Grotjans and F.R. Menter, “Wall Functions for General Application CFD Codes,” ECCOMAS 98, Proceedings of the Fourth European Computational Fluid Dynamics Conference, John Wiley & Sons, pp. 1112–1117, 1998.
11.K. Abe, T. Kondoh, and Y. Nagano, “A New Turbulence Model for Predicting Fluid Flow and Heat Transfer in Separating and Reattaching Flows—I. Flow field calculations,” International Journal of Heat and Mass Transfer, vol. 37, no. 1, pp. 139–151, 1994.
12.The Spalart-Allmaras Turbulence Model, http://turbmodels.larc.nasa.gov/spalart.html.
T H E O R Y F O R T H E TU R B U L E N T F L O W I N T E R F A C E S | 159
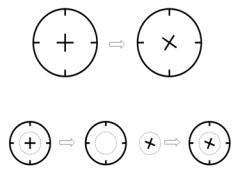
T h e o r y f o r t h e R o t a t i n g M a c h i n e r y I n t e r f a c e s
The Single-Phase Flow, Rotating Machinery Interfaces models moving rotating parts in, for example, stirred tanks, mixers, and pumps. The interfaces formulate the Navier-Stokes equations in a rotating coordinate system. Parts that are not rotated are expressed in the fixed material coordinate system. The rotating and fixed parts need to be coupled together by an identity pair, where a flux continuity boundary condition is applied.
Use these interfaces where it is possible to divide the modeled device into rotationally invariant geometries. The operation can be, for example, to rotate an impeller in a baffled tank, as in Figure 4-7 where the impeller rotates from position 1 to 2. The first step is to divide the geometry into two parts that are both rotationally invariant, as shown in Step 1a. The second step is to specify the parts to model using a rotating frame and the ones to model using a fixed frame (Step 1b). The predefined coupling then automatically does the coordinate transformation and the joining of the fixed and moving parts (Step 2a).
1 |
2 |
|
1a |
1b |
2a |
Figure 4-7: The modeling procedure in the Rotating Machinery, Fluid Flow interface.
It is straightforward to use the coupling. First draw the geometry using two separate domains for the fixed and rotating parts. Then activate the assembly (using an assembly instead of a union) and create an identity pair, which makes it possible to treat the two domains as separate parts in an assembly. After this, specify which part uses a rotating frame. Once this is done, proceed to the usual steps of setting the fluid properties, boundary conditions, and then mesh and solve the problem.
160 | C H A P T E R 4 : S I N G L E - P H A S E F L O W B R A N C H
5
T h i n - F i l m F l o w B r a n c h
The fluid flow interfaces are grouped by type under the Fluid Flow main branch. The interfaces described in this section are found under the Thin-Film Flow branch () in the Model Wizard. The Mechanisms for Modeling Thin-Film Flow Interfaces helps you choose the best one to start with.
In this chapter
•The Lubrication Shell Interface
•The Thin-Film Flow Interface
•Theory for the Thin-Film Flow Interfaces
161