
глава3
.pdf3.МОДЕЛИРОВАНИЕ ПРОЦЕССОВ И АППАРАТОВ
3.1.Процессы и аппараты сокращения крупности
3.1.1. Алгоритмический подход к моделям процессов сокращения крупности
Поскольку в дробильно-измельчительных машинах частицы подвергаются многократному разрушению, процессы дробления-измельчения следует рассматривать как итоговое воздействие многочисленных повторяющихся однократных событий, определяемых механикой работы машин. Процесс разрушения материала в аппарате состоит из повторяющихся шагов, каждый из которых может быть представлен двумя основными операциями: отбор материала для разрушения и последующее разрушение отобранного материала действием машины.
Количественно эти операции характеризуются вероятностью разрушения частиц на n-м шаге разрушения pn(D) и кумулятивным распределением F(D, d) в диапазоне крупности d<D, возникающими при разрушении единицы массы частиц размером D.
Поскольку каждая пара процессов отбора и разрушения составляет один шаг в последовательном процессе преобразования исходного материала в технологической операции, и каждым шагом функция Fn(D) характеризует распределение по крупности массы исходного материала, a Fn+1(d) = Fn+1(D) характеризует распределение после разрушения в n-м шаге и одновременно распределение исходного материала для ( n+1) шага, функцию, «воздействующую» на частицы, целесообразно записывать в виде F(D, d).
В этой модели гранулометрические составы питания и продукта дробления выражаются распределениями по n классам, с ростом n уменьшается размер класса.
При разрушении осколки могут попасть как в тот же, исходный, класс, так и в любой другой, меньший.
Процесс сокращения крупности в общем случае характеризуется таблицей материального баланса (табл. 3.1).
Элементы правой части таблицы pij где j – индекс полученного в результате разрушения класса, i – индекс класса питания.
Гранулометрический состав продукта можно определить, просуммировав элементы в последовательных строках правой части таблицы. Величина
n+1
∑fi = F
1
соответствует общей массе питания. Масса класса (n+1) находится как fn+1=F–fn. Элемент pij может быть представлен в виде:
pij= xij fi,
где xij – содержание i-го класса крупности питания перешедшего в j-й класс крупности продукта.
1
Таблица 3.1. – Материальный баланс процессов сокращения крупности
Класс |
|
Распределение |
|
|
|
|
|
Распределение продуктов по классам |
|
|||||||||||||||||
|
|
питания по |
|
|
|
|
|
|
|
|
|
|
|
|
|
|
|
|
|
|
|
|
|
|||
крупности |
|
|
|
|
|
1 |
|
|
|
2 |
|
|
… |
|
|
|
n |
|
|
|
n+1 |
|||||
|
|
|
классам |
|
|
|
|
|
|
|
|
|
|
|
|
|
|
|
|
|
|
|
|
|
||
1 |
|
|
|
f1 |
|
|
|
|
p1, 1 |
|
|
0 |
|
|
… |
|
|
|
0 |
|
|
|
0 |
|||
2 |
|
|
|
f2 |
|
|
|
|
p2, 1 |
|
|
p2, 2 |
|
|
… |
|
|
|
0 |
|
|
|
0 |
|||
… |
|
|
|
… |
|
|
|
|
… |
|
|
|
… |
|
|
… |
|
|
|
… |
|
|
… |
|||
… |
|
|
|
… |
|
|
|
|
… |
|
|
|
… |
|
|
… |
|
|
|
… |
|
|
… |
|||
n |
|
|
|
fn |
|
|
|
|
pn, 1 |
|
|
|
pn, 2 |
|
|
… |
|
|
|
pn, n |
|
|
… |
|||
n+1 |
|
|
|
fn+1 |
|
|
|
|
pn+1, 1 |
|
|
pn+1, 2 |
|
|
… |
|
|
pn+1, n |
|
pn+1, n+1 |
||||||
Матричная форма записи уравнения процесса сокращения крупности в |
||||||||||||||||||||||||||
краткой форме имеет вид: |
|
|
|
|
|
|
|
|
|
|
|
|
|
|
|
|
|
|
|
|||||||
|
|
|
|
|
|
|
|
|
|
|
|
|
p=xf, |
|
|
|
|
|
|
|
|
|
|
|
||
а в развернутом виде представляется так: |
|
|
|
|
|
|
|
|
|
|
|
|
||||||||||||||
x1,1 |
|
0 ... |
0 |
|
f1 |
|
x1,1 f1 + 0 + |
|
|
... |
0 |
|
|
|
p1 |
|
||||||||||
x |
x |
2,2 |
... |
0 |
|
f |
2 |
|
x |
f |
+ x |
f |
2 |
+ ... |
0 |
|
|
|
p |
|
||||||
|
2,1 |
|
|
|
|
|
|
|
|
2,1 1 |
2,2 |
|
|
|
|
|
|
|
2 |
|
||||||
|
... |
... ... |
0 |
|
... |
|
|
|
|
|
|
|
|
|
|
|
= |
... |
. |
|||||||
|
|
= ......................... ... ... |
|
|
||||||||||||||||||||||
... |
... ... |
... |
|
... |
|
.......................... ... ... |
|
|
|
... |
|
|||||||||||||||
|
|
|
|
|
|
|
|
|
|
|
|
|
|
+ x |
|
|
+ ... |
|
|
|
|
|
|
|
||
x |
x |
n,2 |
... |
x |
|
f |
n |
|
x |
f |
f |
2 |
x |
f |
|
|
p |
|
||||||||
|
n,1 |
|
|
n,n |
|
|
|
n,1 1 |
n,2 |
|
|
|
n,n |
|
n |
|
n |
|
Понятие функции отбора вводится в связи с тем, что частицы, попавшие в аппарат, разрушаются с определенной вероятностью, причем зависящей от их крупности. В каждый момент времени лишь часть частиц каждого класса отбирается для разрушения, оставшаяся же часть не разрушается.
Обозначим долю частиц класса, которые отбираются для разрушения si, тогда разрушенные частицы i-го класса составят sifi или в матричном виде:
s |
0 |
... |
0 |
|
|
f |
|
|
s |
f |
|
|
|
1 |
s2 |
... |
0 |
|
|
1 |
|
|
1 |
1 |
|
|
0 |
|
|
f2 |
= |
s2 f2 |
||||||
... |
... |
... |
... |
... |
|
... |
. |
|||||
|
|
|
||||||||||
|
0 |
0 |
... |
|
|
|
|
|
|
|
|
|
|
sn |
|
fn |
|
|
sn fn |
|
Итак, если s – матрица отбора, то разрушенные частицы представляются функцией sf. Общая масса частиц, прошедших через процесс неразрушенными, составит (1–s)f.
Обозначив долю частиц каждого класса, которые действительно оказываются разрушенными, как В (функция разрушения; в уравнениях – матрица В), запишем уравнение процесса в виде:
p=Bsf+1(1–s)f=(Bs+1–s)f. (3.1)
Учитывая многократность актов разрушения, в каждом из которых имеет место и отбор, и разрушение, и то, что после каждого акта разрушения частицы разной крупности перераспределяются в рабочей зоне аппарата по-разному перед тем, как некоторая доля вновь образованного продукта опять подвергнется разрушению, а часть его разгрузится без разрушения, можно допустить, что
2

практически в любом дробильно-измельчительном аппарате существует классификация частиц по крупности. Условно дополняя процесс сокращения крупности классификацией (рис 3.1) и оценивая результат классификации по готовому продукту как p = ( l – c ) q или р=(1– с)·(Bs + 1–s)m, с учетом m =f + cq получим:
m= f + c(Bs + 1–s), |
|
|
f m |
|
q |
|||
|
|
Разрушение |
||||||
f=[1- c(Bs + 1–s)m] |
|
|
|
|
|
|
||
|
|
|
|
|
|
|
||
или |
|
|
|
|
|
|
|
|
m=[1- c(Bs + 1–s)]-1f. |
|
|
Cq |
|
Классификация |
|
|
|
|
|
|
|
|
||||
Окончательно модель |
процесса со- |
|
|
|
|
|
||
|
|
p |
||||||
кращения крупности представим следую- |
|
|
||||||
Рис. 3.1. Символическое представ- |
||||||||
щим образом: |
|
|
||||||
|
-1 |
f. (3.2) |
ление процесса сокращения круп- |
|||||
р=(1– с)·(Bs + 1–s) [1- c(Bs + 1–s)] |
ности в дробильно-измельчи- |
|||||||
При незначительном влиянии клас- |
тельном |
аппарате как замкнутого |
||||||
сификации с→0 уравнение (3.2) приводит- |
цикла разрушения-классификации |
|||||||
ся к виду (3.1). |
|
|
|
|
|
|
|
|
Ввиду многократности |
последовательных актов разрушения конечные |
продукты процесса в целом, включающего υ последовательных актов, описываются уравнением
j=ϑ |
|
p = ∏ xi f , |
|
j=1 |
|
|
|
где xj характеризует акт разрушения, происходящий при j-м цикле.
Если все акты разрушения идентичны, справедливо уравнение p=xυf.
В основе всех моделей дробления и разрушения лежит описание продукта однократного акта разрушения. Это функция трудноопределима экспериментально и неоднозначна, поскольку должна учитывать характеристики и аппарата, и материала.
Удобной формой распределения по крупности частиц после разрушения, по предположению Бродбента и Каллкотта, является модифицированное урав-
нение Розина–Раммлера
В(d, d 0 ) = ( 1 – e-d/d0)/(1–e-1).
Функция В(d, d0) представляет долю частиц исходного размера d0, появляющихся после разрушения в классах крупности мельче d. Эта функция не зависит от крупности разрушенной частицы, так как она выражена в относительных размерах частиц.
Функции разрушения могут быть получены и экспериментально. Келсалл для определения мгновенной функции разрушения применил метод трассирующего минерала (кварц в среде кальцита), частица рассматривалась как разрушенная в том случае, когда никакая ее часть не остается в исходном классе крупности. Опыты проводили в шаровой мельнице. В установившемся режиме трассирующий кварц подавали в виде импульса. При появлении кварца на выходе из мельницы был произведен отбор пробы, отделение кварца и его сито-
3
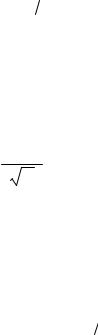
вой анализ. Относительная функция разрушения, полученная по этому экспе-
рименту, составила:
В(d, d 0 ) = ( d/d0)n,
где п=0,9–0,95.
3.1.2. Модели, вытекающие из геометрии дробящего пространства
Такие модели составляются при анализе простейших геометрических соотношений камеры дробления и служат для выбора конструктивных и режимных параметров дробилки.
Угол захвата (угол между подвижной и неподвижной щекой) в щековой дробилке регулируется изменением размера разгрузочной щели. Чем больше угол захвата α, тем выше степень дробления и меньше производительность дробилки. Его предельное значение находится из приравнивания вертикальных составляющих выталкивающей кусок вверх силы и силы трения куска о щеку, направленной в противоположную сторону.
Предельный угол захвата α0 равен 2φ (φ – угол трения). При α>2φ возможен выброс кусков материала вверх.
Частота вращения коленчатого вала выбирается по соображениям максимальной производительности дробилки, которая достигается при условии, что куски, расположенные на некоторой высоте камеры h, успели за один отход щеки пройти расстояние h под действием силы тяжести.
Приравнивая время отхода подвижной щели (время половины оборота
вала) t=30/n и время падения куска с высоты h t=(2h/g)l/2 , получают: n=30[g/(2h) ]1/2
или с учетом геометрических соотношений:
g tgα 1 2 |
|||
n = 30 |
|
|
, |
|
|||
|
2s |
|
где n – частота вращения коленчатого вала, s – длина хода подвижной щеки у разгрузочного отверстия.
При переходе к размеру загрузочной щели В и, вводя среднестатистический угол захвата 22°, можно вычислить наивыгоднейшую частоту вращения:
n = 182B,6 .
Наивыгоднейшая частота вращения эксцентрикового стакана конусной дробилки крупного дробления обеспечивает максимальную производительность дробилки. Вывод формулы производится из тех же соображений, что и в щековой. Учитывая, что угол захвата складывается из углов наклона образующих подвижного и неподвижного конусов к вертикали у1 и у2, теоретически частоту находят по формуле
g (tg y + tg y |
2 |
) 1 2 |
|||
n = 30 |
1 |
|
|
, |
|
2s |
|
|
|||
|
|
|
|
|
4
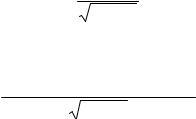
где s – ход дробящего конуса на горизонте разгрузочного отверстия, равный двойному эксцентриситету е.
Полагая, что реально конусные дробилки крупного дробления работают с числом оборотов в 2 раза меньше теоретического и принимая s = 0,02В + 0,01, окончательно получают:
|
n = |
240 . |
|
|
2B + 1 |
Производительность с учетом геометрии дробящего пространства опре- |
||
деляют по формуле: |
420,5B3 + 195,8B2 − 7,2B kρ. |
|
n = |
||
|
|
2B + 1 |
Полученные таким образом модели не учитывают свойств дробимого материала и не позволяют выполнять прогноз характеристик продуктов дробления. Они пригодны лишь для ориентировочного выбора и оценки параметров дробилок.
3.2.Процессы и аппараты обогащения
3.2.1.Получение информации из анализа простых моделей процессов
Для большинства процессов существуют простые модельные представле-
ния о механизме процесса. Эти модели не служат решению фундаментальной задачи моделирования – прогнозу скорости протекания процесса, а способствуют пониманию сути процесса, позволяют выявить новые закономерности, установить условия его осуществления и т. д.
Рассмотрим лишь некоторые из них.
Прекрасным примером простейшей модели, при анализе которой получают определенные технологические выводы, является вероятностная модель прохождения зерен через отверстия сита.
На первом этапе сито полагается с квадратными отверстиями размером l, образованными из бесконечно тонкой проволоки. Предполагают также, что шарообразные зерна диаметром d при грохочении падают перпендикулярно к плоскости сита. Беспрепятственный проход частиц через отверстие имеет место в том случае, когда частицы не касаются проволоки, т. е. проекция центра зерна отстоит от проволоки на расстоянии больше чем d/2.
Если принять, что общее число вариантов падения частицы на единичное отверстие пропорционально площади отверстия l2, а число вариантов падения с последующим беспрепятственным прохождением пропорционально площади (l-d)2, то вероятность беспрепятственного прохождения зерна через отверстие:
p = |
(l − d )2 |
= 1− d |
2 . |
|
|
l2 |
|
l |
|
Вероятное число отверстий N, которое встретит зерно, чтобы пройти сквозь сито, есть величина, обратная р:
5
N = |
l 2 |
||
|
|
. |
|
l − d |
Исследование влияния соотношения d/l на величину N приводит к заключению, что возрастание d/l свыше 0,7 приводит резкому увеличению необходимого числа отверстий. Таким образом, частицы с d/l> 0,7 считают «трудными». Справедливость теоретически полученного вывода полностью подтверждается многочисленными экспериментами и практикой работы.
Учтем толщину проволоки а, тогда вероятность прохождения зерна сквозь сито составит:
p = |
(l − d )2 |
= |
l2 |
|
− |
d 2 |
||
|
|
1 |
|
|
, |
|||
(l + a)2 |
(l + a)2 |
|
||||||
|
|
|
|
l |
|
где l2/(l + a)2 = L – коэффициент живого сечения сита.
Необходимое число отверстий для гарантированного прохождения зерна сквозь сито можно вычислить:
N = |
l2 |
|
|
. |
|
L(l − d )2 |
Предположим, что встреча зерна этим числом отверстий обеспечивается временем грохочения t. Пусть время грохочения недостаточно и равно t1<t. Тогда для данного класса в подрешетный продукт перейдет не N, a N1< N частиц и извлечение в подрешетный продукт (эффективность грохочения по классу) составит:
|
N N L(l − d )2 |
|
|
|
d 2 |
|||
η = |
1 |
= |
1 |
= LN |
1 |
− |
|
. |
N2 |
l2 |
|
||||||
|
|
1 |
|
l |
Таким образом, получена модель эффективности грохочения, анализ которой позволяет сделать технологические выводы: эффективность возрастает с увеличением продолжительности грохочения, коэффициента живого сечения сита и падает с увеличением крупности частиц.
Трактовке принципов разделения в гравитационных аппаратах служит энергетическая модель (гипотеза). Взвесь минеральных частиц рассматривается как механическая система тел, находящаяся в поле силы тяжести в неустойчивом равновесии и стремящаяся занять такое положение, так распределить частицы, чтобы потенциальная энергия системы стала минимальной.
При равномерном распределении частиц плотности ρт1 и ρт2 по высоте взвеси потенциальная энергия системы определяется выражением
E0 = 0,5SσgH02 ,
где S – площадь горизонтального сечения; σ=(1-m)(ρт – ρж) – относительная плотность взвеси; m – объемное содержание жидкости во взвеси; ρт и ρж – плотность соответственно твердого (средневзвешенная) и жидкого; H0 – высота взвеси.
После полного разделения потенциальная энергия уменьшится на вели-
чину
6
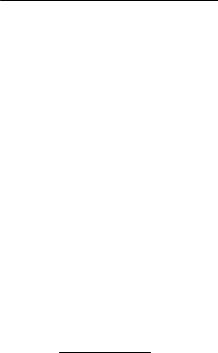
E = (0,5σH02 − 0,5σ1H12 − σ2 (H1 + 0,5H2 )H2 )gS,
где σ1, σ2 – относительная плотность слоев частиц с плотностью твердого ρт1 и ρт2 во взвесях после разделения; H1 и H2 – высота слоев взвеси.
Качественную оценку гравитационного процесса разделения можно выполнять по величине относительной убыли потенциальной энергии в случае полного разделения:
E
E0
где k1=(1-m1)/(1-m2) – отношение объемных содержаний твердого во взвесях после разделения; p=(ρт1– ρж)/(ρт2– ρж); δ=ρт1/ρт2; α – массовое содержание компонента плотностью ρт1 в исходной смеси (ρт1>ρт2), д. е.
Эта модель позволяет сформулировать некоторые общие принципы гравитационного разделения: при увеличении разности плотности (при постоянных размерах) разделение улучшается, т. е. Е/Е0 возрастает с ростом р и δ; поскольку зависимость Е/Е0 от α имеет максимум при некотором среднем значении содержания, руды с малым или большим содержанием одного из компонентов обогащаются с меньшей эффективностью, чем содержащие среднее его количество.
Сделанные выводы по простейшей модели подтверждаются практикой обогащения.
Основной акт флотации – закрепление частицы на пузырьке воздуха или газа. Модель убыли свободной поверхностной энергии записывается в виде:
F = σж−г Sж−г − Sж′ −г ,
Sт−г − cosθ
где σж-г – свободная поверхностная энергия границы поверхности раздела жид- кость–газ; Sж-г и S'ж-г – соответственно площади поверхности раздела жидкость– газ до и после прилипания пузырьков к твердой поверхности; Sт-г – площадь поверхности раздела твердое–газ; cosθ=(σт-г–σт-ж)/ σж-г, здесь σт-г и σт-ж – соответственно свободная поверхностная энергия единицы поверхности раздела твердое тело–газ и твердое тело–жидкость.
Поскольку при пенной флотации размеры частиц малы по сравнению с размерами пузырьков, то (Sж-г – S'ж-г)/Sт-г≈1 и выражение для F принимает вид:
F = σж-г(1– cosθ).
Анализируя последнее выражение, которое показывает, что убыль свободной энергии системы тем больше, чем больше краевой угол смачивания θ, приходим к основному качественному соотношению флотации: чем гидрофобнее поверхность минерала, тем лучше его прилипание к пузырьку газа.
На анализе модели проявления молекулярных сил при сухом магнит-
ном обогащении основан выбор мероприятий для улучшения эффективности процесса.
Проявление молекулярных сил особенно заметно для тонких частиц. Сила молекулярного притяжения F(H) между двумя сферическими частицами определяется из равенства Дерягина:
F=2Аπd1d2σп/(d1+d2),
7
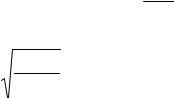
где А – коэффициент, учитывающий площадь соприкосновения частиц, наличие влаги и другие факторы; d1 и d2 – диаметры частиц; σп – свободная поверхностная энергия частиц на границе их раздела с воздухом.
При допущении о равенстве диаметров частиц имеем:
F=Аπdσп,
откуда при силе сцепления, равной силе тяжести G = πd6 3 ρg (здесь ρ – плот-
ность частиц; g – ускорение свободного падения), можно получить:
d = 6Aσп .
ρg
Поэтому частицы диаметра, меньшего, чем d, притягиваются в виде агрегатов, состоящих из магнитных и немагнитных частиц, к рабочим органам сепараторов. Закрепление возможно, если суммарная удельная магнитная восприимчивость частиц достаточна для притяжения всего агрегата. В ином случае агрегаты попадают в немагнитный продукт.
Если материал содержит значительное количество мелких частиц, необходимо принимать меры к повышению эффективности процесса сухой магнитной сепарации. Это может быть предварительное обеспыливание материала, увеличение скорости вращения барабана или валка, применение добавок, способствующих диспергации частиц при сухом обогащении тонкого материала.
Итак, даже самые простые модельные представления о процессе позволяют сделать полезные для практики выводы.
3.2.2. Моделирование движения частиц под действием характерных сил в рабочей зоне аппарата
Модели движения частиц под действием приложенных к ним сил – это модели динамики. Их практическое использование можно продемонстрировать как на основе решения уравнений динамики в общем виде, так и исходя из получающихся в частном случае уравнений баланса сил для установившихся или предельных режимов.
Модели такого рода справедливы для идеальных условий движеия частиц без взаимодействия между собой. Однако, несмотря на условность применения, их анализ позволяет делать практические выводы при создании аппаратов – выбирать допустимые конструктивные и режимные параметры.
Ранее был выполнен анализ модели свободного падения шарообразных частиц в среде разделения:
m |
dv |
= G − A − P = |
πd 3 |
δg − |
πd 3 |
g − ψv2d 2 . |
|
dt |
6 |
6 |
|||||
|
|
|
|
Его решение при достижении телом конечной скорости при dv/dt=0 дает выражения конечной скорости падения шарообразных частиц (формулы Стокса v0C, Алена v0А, Риттингера v0Р):
8

v |
= |
d 2 (δ − |
)g |
|
|
при d < 0,1 мм; |
|||||
|
|
|
|
|
|
|
|
|
|||
0C |
|
|
|
18μ |
|
|
|
|
|
|
|
|
|
|
|
|
|
|
|
|
|
|
|
|
|
|
|
8g 2 |
|
(δ − |
)2 |
13 |
|||
v |
= d |
|
|
|
|
|
|
|
при0,1 ≤ d ≤ 1 мм; |
||
|
|
μ |
|
||||||||
0А |
|
|
|
30 |
|
|
|
|
|
||
|
|
|
|
|
|
|
|
|
|
|
|
v |
= |
8d(δ − |
|
)g 12 |
|
|
при≤ d > 1 мм. |
||||
|
|
|
|
|
|
|
|
|
|||
0Р |
|
3 |
|
|
|
|
|
|
|||
|
|
|
|
|
|
|
|
|
|
Полученные выражения применимы для расчета конечных скоростей при гидравлической классификации с весьма малой концентрацией частиц. Их используют, например, для ориентировочного расчета расхода воды Q для создания восходящего потока в гидравлических классификаторах при известной площади зеркала классификатора S и заданных плотности частиц δ и крупности граничного зерна разделения dгр. Требуемый расход воды находят из условий равенства v0 = u, здесь u – скорость восходящего потока. Тогда
Q= S ·u= S v0(dгр, δ, , μ).
Тело неправильной геометрической формы можно идеализировать, сведя к одному из тел правильной геометрической формы, и определить v0 более точно:
v0 =pvэ,
где vэ – скорость падения шара, эквивалентного по объему падающему телу; p – поправочный коэффициент, учитывающий форму тела и зависящий от коэффи-
циента сферичности ω, рассчитываемого по формуле
ω=πd3/S=4,82 V2/3/S,
где S – площадь поверхности тела; V= πdэ3/6 – объем тела; dэ – диаметр равновеликого по объему шара.
Значения коэффициентов сферичности и поправочных коэффициентов (p1 при Re<20, p2>500) для тел разной формы приведены в таблице 3.2. Если 20≤ Re=vd /μ≤500, следует прибегать к интерполяции в определении p.
Частицы минералов и горных пород имеют специфическую, подчас значительно меняющуюся форму. Для некоторых из них ω и p1, p2 определены экспериментально (таблица 3.3).
Стесненное движение частиц часто характеризуют формулой: vст = v0θn,
где θ – коэффициент пористости, θ=Vж/(Vж+Vт), здесь Vж, Vт – соответственно объем жидкого и твердого во взвешенном слое, n – показатель степени, зависящий от числа Рейнольдса Re и формы частиц. Модели динамики движения кусков в магнитных сепараторах принято записывать не в виде дифференциальных уравнений. Обычно определяют необходимую удельную магнитную силу fм для извлечения или удержания магнитных частиц на барабане. Ее находят из уравнения баланса сил для установившегося режима и в предположении о монослойном питании сепаратора. Сепараторы отличаются спецификой условий разделения и величиной сил действующих на частицу.
9
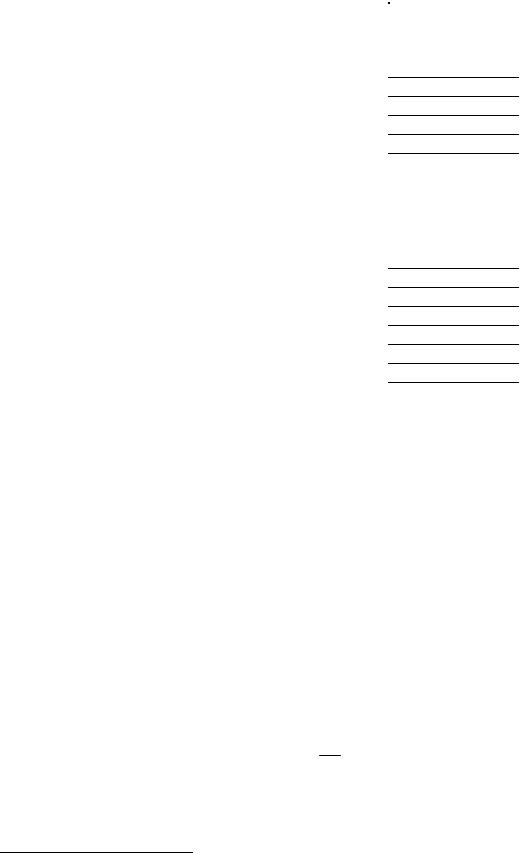
Таблица 3.2. – Значения коэффициентов ω, p1, p2
Форма частицы |
Эквивалентный |
Коэффициент |
Поправочные |
коэффициенты |
|
|
диаметр, dэ |
сферичности, ω |
p1 |
p2 |
|
Шар |
d |
|
1,000 |
1,000 |
1,000 |
Усеченный |
2,78a |
2 |
0,906 |
0,952 |
0,706 |
октаэдр1 |
|
||||
Октаэдр |
0,966a |
0,846 |
0,920 |
0,611 |
|
Куб |
1,241a |
0,806 |
0,890 |
0,563 |
|
Тетраэдр |
0,608a |
0,670 |
0,819 |
0,450 |
|
Параллелепипед: |
|
|
|
0,875 |
|
а·а·2а |
1,563a |
0,767 |
0,525 |
||
а·2а·2а |
1,970a |
0,761 |
0,872 |
0,520 |
|
а·2а·За |
2,253a |
0,725 |
0,851 |
0,490 |
|
а·а·0,2а |
0,726a |
0,591 |
0,770 |
0,420 |
|
а·а·0,1а |
0,576a |
0,435 |
0,660 |
0,321 |
|
а·а·0,05а |
0,457a |
0,298 |
0,546 |
0,254 |
|
Цилиндр: |
|
|
|
0,912 |
|
h=2d3 |
1,442d |
0,831 |
0,592 |
||
h=1,5d |
1,310d |
0,858 |
0,926 |
0,627 |
|
h=d |
1,145d |
0,875 |
0,935 |
0,652 |
|
h=0,5d |
0,909d |
0,826 |
0,909 |
0,586 |
|
h=1,5d |
0,608d |
0,570 |
0,755 |
0,390 |
Таблица 3.2. – Значения коэффициентов ω, p1, p2 для частиц минералов и горных пород
Минерал или порода |
Коэффициент |
Поправочные коэффициенты |
||
сферичности |
p1 |
p1 |
||
|
||||
Уголь |
0,650 |
0,806 |
0,437 |
|
Антрацит |
0,377-0,666 |
0,630-0,816 |
0,302-0,477 |
|
Кварц дробленый |
0,710 |
0,843 |
0,478 |
|
Песок кварцевый |
0,833-0,855 |
0,913-0,925 |
0,464-0,623 |
|
окатанный |
||||
|
|
|
||
Сланец |
0,286-0,315 |
0,535-0,561 |
0,249-0,263 |
|
Касситерит |
0,710 |
0,843 |
0,479 |
|
Галенит |
0,806 |
0,890 |
0,563 |
|
Слюда |
0,280 |
0,529 |
0,246 |
При верхней подаче на барабанный сепаратор (рис. 3.2) необходимая для удержания магнитных частиц удельная отнесенная к массе т (FM/m = fM) магнитная сила без учета силы трения равна:
fМ = v2 − g cosϕ,
Rб
где v – скорость вращения барабана; Rб – радиус барабана; φ – угол (от вертикали), определяющий положение магнитной частицы на поверхности барабана.
1Многогранник, образованный 8 правильными шестиугольниками и 6 квадратами;
2a – размер наименьшего ребра тела;
3h – высота цилиндра; d – диаметр его основания.
10