
- •Предисловие
- •1. Служебное назначение машины
- •2. Качество и экономичность машины
- •3. Понятие о точности детали и машины
- •4. Основные виды связей между поверхностями деталей машины и их графическое представление
- •5. Размерные цепи. Термины и определения
- •5.1. Основные понятия
- •5.2. Звенья размерных цепей
- •5.3. Виды размерных цепей
- •5.4. Размеры и отклонения
- •5.6. Методы достижения точности замыкающего звена
- •6. Порядок построения размерных цепей
- •6.1. Последовательность построения размерной цепи
- •6.2. Нахождение замыкающего звена, его допуска и координаты середины поля допуска
- •6.3. Выявление составляющих звеньев размерной цепи
- •7. Методика расчёта размерных цепей
- •7.3.1. Метод полной взаимозаменяемости
- •7.3.2. Метод неполной взаимозаменяемости
- •7.3.3. Метод групповой взаимозаменяемости
- •7.3.4. Метод пригонки
- •7.3.5. Метод регулирования с применением неподвижного компенсатора
- •7.4. Выбор метода достижения точности замыкающего звена размерной цепи
- •7.5.1. Метод максимума-минимума
- •7.5.2. Вероятностный метод
- •7.6. Коэффициенты, характеризующие рассеяние размеров.
- •7.7.1. Метод попыток
- •7.7.2. Метод равного квалитета
- •8.2. Цилиндрические зубчатые передачи
- •Размерная цепь β
- •Размерная цепь Б
- •8.3. Конические зубчатые передачи
- •Размерная цепь Б
- •Размерная цепь φ
- •Размерная цепь С
- •8.4. Червячные передачи
- •Размерная цепь γ
- •Размерная цепь Г
- •Размерная цепь Б
- •8.5.1. Служебное назначение узла
- •8.5.2. Выявление и анализ технических условий и норм точности
- •8.5.3. Выбор методов достижения точности
- •Размерная цепь А
- •Размерная цепь Б
- •9. Список литературы
- •10. Приложения
- •10.2. Принятые обозначения
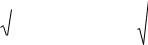
|
|
|
|
|
|
|
67 |
|
||||
Из ранее сказанного следует, что ТВ |
= ТБ2 = 0,14 мм. |
|||||||||||
Проверим, обеспечивают ли установленные допуски требуемую точ- |
||||||||||||
ность размера Г : |
|
|
|
|
|
|
|
|
|
|
||
|
|
|
|
|
|
|
|
|
|
|
|
|
|
|
|
|
|
|
|
) 3 |
1 |
|
|
||
Т |
Г |
t |
|
2 |
(T 2 |
T 2 |
(0,142 0,12 ) 0,17мм |
|||||
|
||||||||||||
|
|
i |
B |
A1 |
9 |
|
|
|||||
|
|
|
|
|
|
|
|
|
Таким образом, принятые значения допусков надѐжно обеспечивают требуемую точность размера Г , так как ТГ = 0,17 < 0,3 мм. Что касается размера 140 мм, то для достижения требуемой точности А допуск на операционный размер В должен быть задан более жѐстким (0,14 мм), чем это указано на чертеже детали.
Приняв во внимание, что А2 = − Б1 + Б2, а Б2 = В , получим А = А1 + Б1 − В1, а следовательно, для назначения координат середин полей допусков операционных размеров необходимо совместное решение уравнений координат:
0A 0A1 0Б1 0В , |
|
||||||
|
|
|
|
|
|
|
|
|
0Г |
0В |
0А1 |
|
|
||
|
|
|
|
|
|||
Чертѐж детали требует, |
чтобы |
0А = 0; |
0Г = −0,15мм и |
0В = −0,25 мм.
Учитывая это требование, необходимо установить:
0А1 = 0В
0Б1 = 0А + 0В
−0Г = −0,025 + 0,15 = −0,1 мм
−0А1 = 0 − 0,25 − (−0,10) = −0,15 мм
7.4. Выбор метода достижения точности замыкающего звена размерной цепи
Задачи достижения требуемой точности сборки решаются с использованием анализа размерных цепей собираемого изделия. Существует тесная связь между методами сборки и методами расчѐта размерных цепей − каждому методу сборки соответствует определѐнный метод расчѐта размерных цепей. Достичь необходимой точности сборки − значит получить замыкающее звено размерной цепи, не выходящее за пределы допускаемых отклонений.
При конструировании изделий требуемая точность замыкающего звена обычно устанавливается из условий эксплуатации изделия и его служебного назначения. В зависимости от объекта производства, характера продукции, а
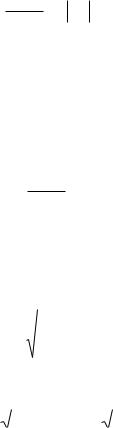
68
также точности обработки деталей она может быть достигнута несколькими методами: полной, неполной (частичной) и групповой взаимозаменяемости, пригонки и регулирования (табл. 7.6). При проектировании и изготовлении даже одной и той же машины часто используют сочетание различных методов достижения точности замыкающих звеньев размерных цепей.
Метод достижения заданной точности замыкающего звена выбирается в зависимости от допуска, установленного на него, и числа составляющих звеньев размерной цепи. При этом учитываются конструктивные и технологические особенности изделия, его служебное назначение, себестоимость изготовления и другие факторы [7].
Предварительно метод обеспечения заданной точности замыкающего звена выбирается по среднему допуску составляющих звеньев. Для этого по номинальным значениям составляющих звеньев размерной цепи определяется их среднее значение:
1 m 1 Aср m 1 i 1 Ai ,
выбирается метод расчѐта размерной цепи; в зависимости от принятого метода расчѐта, заданного допуска замыкающего звена и числа составляющих звеньев цепи определяется среднее значение допуска Тср для каждого звена.
При расчѐте на максимум-минимум:
Tср T
m 1
При расчѐте вероятностным методом (табл. 7.7):
Tср |
|
|
T |
|
|
|
|
|
|
||||
|
|
|
|
|
|
|
|
|
|
|
|
||
|
|
m 1 |
|
|
|
|
|
|
|||||
|
|
|
|
|
|
|
|
|
|
||||
|
|
t |
i2 2i |
|
|
|
|
|
|
||||
|
|
|
|
i 1 |
|
|
|
|
|
|
|||
или Tср |
|
T |
|
|
|
|
|
|
T |
, |
|||
|
|
|
|
|
|
|
|
|
|
|
|||
Ki |
|
|
|
|
|
|
m 1 |
||||||
|
|
m 1 1,2 |
|
|
|
(7.19)
(7.20)
где Т − допуск замыкающего звена размерной цепи А; t − коэффициент риска брака (см. табл. 7.1); ξi − передаточное отношение i-го звена размерной цепи А; λi − относительное среднее квадратическое отклонение, характеризующее форму теоретической кривой рассеяния значений i-го звена размерной цепи; m − общее число звеньев в размерной цепи, включая и замыкаю-
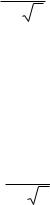
69
щее звено; (m − 1) − количество составляющих звеньев размерной цепи; Ki − приведѐнный коэффициент относительного рассеяния, для проектных расчѐ-
тов Ki = 1,2.
Исходя из полученных значений величин Аср определяют ближайший квалитет точности замыкающего звена.
Полученный средний допуск или средний квалитет точности составляющих звеньев оценивается с точки зрения выполнения их на производстве. При этом учитываются сложность и габаритные размеры деталей, предполагаемый технологический процесс изготовления и прежде всего предполагаемые методы обработки поверхностей деталей.
Рассчитанный средний допуск Тср является приемлемым, если он соответствует средне-экономическим нормам точности используемых методов обработки поверхностей [9] [8].
Если допуск Тср приемлем, а допуск Т больше 8−11-го квалитетов точности, следует применять метод полной взаимозаменяемости. Если допуск Т точнее − необходимо использовать метод неполной взаимозаменяемости. Для размерных цепей высокой точности (Т < ТIT6, т.е. допуск Т меньше 6-го квалитета) при малом числе звеньев ((m − 1) ≤ 5) применяют метод групповой взаимозаменяемости; если ((m − 1) > 6) − метод пригонки или регулирования.
Пример расчѐта. Пусть Т = 1200 мкм, (m – 1) = 6, Аср = 90 мм. Для вероятностного метода расчѐта (метод неполной взаимозаменяемости) допуск
Tср 1,212006 408 мкм
Полученное значение находится между 12 и 13-м квалитетами точности. Следовательно, в этом случае требуется применять метод неполной взаимозаменяемости.
Если допуск Т = 120 мкм, (m – 1) = 6 и Аср = 90 мм, то допуск
Tср 1,21206 41 мкм
Значение 41 мкм лежит между 7 и 8-м квалитетами точности. Учитывая высокую точность изготовления деталей, в этом случае следует принять метод пригонки или регулирования.
Ориентировочно метод достижения точности замыкающего звена можно выбрать также по соотношению ожидаемого поля рассеяния ω этого звена и его допуска Т , заданного на чертеже или в технических условиях

70
(табл. 7.8). Величину Т определяют, суммируя средне-экономические нормы точности используемых методов получения составляющих звеньев (прил. 1).
Для определения метода достижения заданной точности замыкающего звена необходимо составить размерную цепь, в которую входит данное замыкающее звено, и установить возможность применения метода полной взаимозаменяемости. Для этого в зависимости от принятого метода обработки назначают точность составляющих звеньев выявленной размерной цепи и
определяют величины ω (7.12) и |
0ωΔ (7.9): |
|
|
|
|||
|
|
m 1 |
|
|
i |
|
|
|
|
|
|||||
|
|
|
|
|
|
i |
|
|
|
i 1 |
|
|
|
||
|
|
m 1 |
|
|
|
||
|
0 i 0 i |
||||||
|
|
i 1 |
|
|
|
||
Если величины ω ≤ T и |
0ωΔ = |
0 , то сборка методом полной взаимо- |
заменяемости осуществима при заданных допусках составляющих звеньев. Если 0ωΔ ≠ 0 необходимо сдвинуть в ту или иную сторону полученную координату середины поля допуска замыкающего звена. Сдвиг осуществляется изменением номинального значения одного из составляющих звеньев на необходимую величину.
|
|
|
Таблица 7.6 |
|
Характеристика методов достижения требуемой точности |
||||
|
замыкающего звена |
|
||
|
|
|
|
|
Характеристика |
Преимущества |
Недостатки |
Область приме- |
|
метода |
нения |
|||
|
|
|||
1 |
2 |
3 |
4 |
|
|
Метод полной взаимозаменяемости |
|
||
|
|
|
|
|
Детали соединя- |
Простота и эко- |
Допуски состав- |
Крупносерийное |
|
ют без пригонки, |
номичность |
ляющих звеньев |
и массовое про- |
|
регулирования и |
сборки; возмож- |
получаются |
изводство, при |
|
подбора. При |
ность организа- |
меньшими (при |
малом допуске |
|
любом сочетании |
ции поточной |
прочих равных |
замыкающего |
|
размеров дета- |
сборки, широко- |
условиях), чем |
звена и неболь- |
|
лей, изготовлен- |
го кооперирова- |
при всех осталь- |
шом числе (до |
|
ных в пределах |
ния производ- |
ных методах, что |
пяти) составля- |
|
расчѐтных до- |
ства; простота |
может оказаться |
ющих звеньев |
|
пусков, автома- |
изготовления за- |
неэкономичным |
размерной цепи; |
|
тически обеспе- |
пасных частей и |
|
многозвенные |
71
1 |
2 |
3 |
4 |
чивается требуе- |
снабжения ими |
|
размерные цепи |
мая точность за- |
потребителей; |
|
при большом до- |
мыкающего зве- |
выборочный кон- |
|
пуске на замы- |
на |
троль |
|
кающее звено |
|
Метод неполной взаимозаменяемости |
|
|
|
|
|
|
Детали соединя- |
То же и эконо- |
Возможны до- |
Серийное и мас- |
ются без пригон- |
мичность изго- |
полнительные за- |
совое производ- |
ки, регулирова- |
товления деталей |
траты на замену |
ства; при малом |
ния и подбора. |
за счѐт расши- |
деталей собран- |
допуске замыка- |
При этом у не- |
ренных полей |
ных изделий; не- |
ющего звена и |
большого (зара- |
допусков |
обходим |
относительно |
нее принятого) |
|
100%-ный кон- |
большом числе |
количества изде- |
|
троль. Возможен |
составляющих |
лий значения за- |
|
брак |
звеньев |
мыкающих зве- |
|
|
|
ньев могут вый- |
|
|
|
ти за установ- |
|
|
|
ленные пределы |
|
|
|
|
Метод групповой взаимозаменяемости |
|
|
|
|
|
|
Детали соединя- |
Возможность до- |
Увеличение объ- |
Массовое и |
ются без пригон- |
стижения высо- |
ѐма незавершѐн- |
крупносерийное |
ки и регулирова- |
кой точности за- |
ного производ- |
производства; |
ния. Расчѐтное |
мыкающего зве- |
ства; дополни- |
малозвенные (3-4 |
значение допуска |
на при целесооб- |
тельные затраты |
звена) размерные |
составляющего |
разных допусках |
на проверку и |
цепи с высокой |
звена увеличива- |
составляющих |
маркировку дета- |
точностью замы- |
ется в несколько |
звеньев |
лей; некоторое |
кающего звена |
раз до экономи- |
|
усложнение |
|
чески целесооб- |
|
снабжения за- |
|
разного произ- |
|
пасными частями |
|
водственного |
|
|
|
допуска. После |
|
|
|
изготовления де- |
|
|
|
тали рассортиро- |
|
|
|
вываются по |
|
|
|
действительным |
|
|
|
размерам на ряд |
|
|
|
групп в пределах |
|
|
|
расчѐтного до- |
|
|
|
пуска и собира- |
|
|
|

72
1 |
2 |
3 |
4 |
ются по соответ- |
|
|
|
ствующим груп- |
|
|
|
пам по методу |
|
|
|
полной взаимо- |
|
|
|
заменяемости |
|
|
|
|
Метод пригонки |
|
|
|
|
|
|
Требуемая точ- |
Возможность до- |
Значительное |
Единичное мел- |
ность достигает- |
стижения высо- |
удорожание |
косерийное про- |
ся за счѐт при- |
кой точности за- |
сборки и удлине- |
изводства, мно- |
гонки заранее |
мыкающего зве- |
ние еѐ сроков; |
гозвенные раз- |
намеченной де- |
на при экономи- |
трудность нор- |
мерные цепи с |
тали (компенса- |
чески целесооб- |
мирования и ме- |
замыкающим |
тора), на кото- |
разных произ- |
ханизации; |
звеном высокой |
рую при механи- |
водственных до- |
усложнение пла- |
точности |
ческой обработке |
пусках звеньев |
нирования про- |
|
(под сборку) |
|
изводства |
|
устанавливают |
|
|
|
определѐнный |
|
|
|
припуск |
|
|
|
|
Метод регулирования |
|
|
|
|
|
|
Требуемая точ- |
Возможность ре- |
Возможность |
Все виды произ- |
ность достигает- |
гулирования за- |
усложнения кон- |
водства; цепи |
ся за счѐт изме- |
мыкающего зве- |
струкции изде- |
высокой точно- |
нения компенси- |
на не только при |
лия; увеличение |
сти |
рующего звена с |
сборке, но и в |
(в некоторых |
|
помощью специ- |
эксплуатации |
случаях) количе- |
|
альных компен- |
(для компенса- |
ства деталей; |
|
саторов с непре- |
ции износа); воз- |
усложнение |
|
рывным или пе- |
можность обес- |
сборки из-за |
|
риодическим пе- |
печения автома- |
необходимости |
|
ремещением де- |
тического регу- |
регулирования и |
|
талей либо под- |
лирования точ- |
изменений |
|
бором последних |
ности |
|
|

73
Таблица 7.7
Значения средних допусков, мкм, составляющих звеньев при расчѐте размерных цепей вероятностным методом [10]
Допуск замыкающего звена |
|
|
|
Средний допуск составляющего звена при (m−1) |
|
|
|
||||||||||
4 |
5 |
6 |
7 |
8 |
9 |
10 |
11 |
12 |
13 |
14 |
15 |
16 |
17 |
18 |
19 |
20 |
|
|
|
|
|
|
|
|
|
|
|
|
|
|
|
|
|
|
|
|
|
|
|
|
|
|
|
|
|
|
|
|
|
|
|
|
|
0,01 |
4 |
4 |
3 |
3 |
3 |
3 |
3 |
2 |
2 |
2 |
- |
- |
- |
- |
- |
- |
- |
0,02 |
8 |
7 |
7 |
6 |
6 |
5 |
5 |
5 |
5 |
4 |
4 |
- |
- |
- |
- |
- |
- |
0,03 |
12 |
11 |
10 |
9 |
9 |
8 |
8 |
7 |
7 |
7 |
7 |
6 |
- |
- |
- |
- |
- |
0,04 |
16 |
14 |
13 |
12 |
11 |
11 |
10 |
10 |
9 |
9 |
9 |
8 |
8 |
8 |
8 |
7 |
7 |
0,05 |
20 |
18 |
17 |
16 |
15 |
14 |
13 |
12 |
12 |
11 |
11 |
11 |
11 |
10 |
10 |
9 |
9 |
0,06 |
25 |
22 |
20 |
19 |
17 |
16 |
16 |
15 |
14 |
14 |
13 |
13 |
12 |
12 |
12 |
11 |
11 |
0,07 |
29 |
25 |
24 |
22 |
20 |
19 |
18 |
17 |
17 |
16 |
15 |
15 |
14 |
14 |
14 |
13 |
13 |
0,08 |
33 |
29 |
27 |
25 |
23 |
22 |
21 |
20 |
19 |
18 |
18 |
17 |
16 |
16 |
16 |
15 |
15 |
0,09 |
37 |
33 |
30 |
28 |
26 |
25 |
23 |
22 |
21 |
20 |
20 |
19 |
18 |
18 |
17 |
17 |
17 |
0,1 |
41 |
36 |
33 |
31 |
29 |
27 |
26 |
25 |
24 |
23 |
22 |
21 |
21 |
20 |
19 |
19 |
18 |
0,2 |
82 |
72 |
67 |
62 |
58 |
55 |
52 |
49 |
47 |
46 |
44 |
42 |
41 |
40 |
39 |
38 |
38 |
0,3 |
123 |
109 |
100 |
93 |
87 |
82 |
78 |
74 |
71 |
68 |
66 |
64 |
62 |
60 |
58 |
57 |
55 |
0,4 |
165 |
145 |
134 |
124 |
116 |
110 |
105 |
100 |
95 |
91 |
88 |
85 |
82 |
80 |
77 |
75 |
74 |
0,5 |
205 |
180 |
170 |
155 |
145 |
140 |
130 |
125 |
120 |
115 |
110 |
105 |
103 |
10 |
97 |
94 |
92 |
0,6 |
146 |
220 |
200 |
185 |
170 |
165 |
155 |
150 |
140 |
137 |
131 |
127 |
124 |
119 |
116113110 |
||
0,7 |
287 |
250 |
235 |
220 |
200 |
190 |
180 |
170 |
166 |
160 |
150 |
148 |
144 |
140 |
135132129 |
||
0,8 |
328 |
290 |
270 |
250 |
230 |
220 |
207 |
198 |
190 |
182 |
175 |
170 |
165 |
159 |
154150147 |
||
0,9 |
370 |
325 |
300 |
280 |
260 |
246 |
230 |
220 |
213 |
205 |
197 |
191 |
185 |
180 |
174170166 |
||
1,0 |
410 |
360 |
335 |
310 |
290 |
270 |
260 |
250 |
240 |
230 |
220 |
210 |
206 |
200 |
190190184 |
||
1,5 |
600 |
550 |
500 |
470 |
430 |
400 |
390 |
370 |
350 |
340 |
320 |
310 |
300 |
300 |
290280270 |
||
2,0 |
820 |
725 |
670 |
620 |
580 |
550 |
520 |
490 |
470 |
460 |
440 |
420 |
410 |
400 |
390380380 |
||
2,5 |
1000 |
910 |
840 |
780 |
720 |
670 |
650 |
610 |
600 |
570 |
550 |
520 |
510 |
490 |
480470460 |
||
3,0 |
123010901000 |
930 |
870 |
820 |
780 |
740 |
710 |
680 |
660 |
640 |
620 |
600 |
580565550 |
||||
4,0 |
1640145013401240116011001040 |
|
980 |
950 |
910 |
880 |
850 |
820 |
800 |
770750740 |
|||||||
5,0 |
20501810168015501450137012901230118011401100106010301000970940920 |
|
|
|
|
74
|
|
|
|
|
|
Таблица 7.8 |
|
|
К выбору метода достижения точности замыкающего звена |
||||||
|
|
|
|
||||
Соотношение |
Метод достижения точности для производства |
||||||
между величинами |
единичного и |
серийного |
массового |
||||
|
Т и ω |
|
мелкосерийного |
||||
|
|
|
|
||||
|
|
|
|
При m = 3 |
|
||
Т |
∕ ω |
≥ 1 |
Полной взаимозаменяемости |
||||
2 ∕ 3 ≤ Т |
∕ ω |
< 1 |
Полной взаимо- |
Неполной взаимозаменяемости |
|||
заменяемости |
|||||||
|
|
|
|
|
|
||
Т |
∕ ω |
< 2 ∕ 3 |
Пригонки |
Групповой взаимозаменяемости |
|||
|
|
|
|
При m > 3 |
|
||
Т |
∕ ω |
≥ 1 |
Полной взаимозаменяемости |
||||
|
|
|
|
|
|
Групповой вза- |
|
2 ∕ 3 ≤ Т |
∕ ω |
< 1 |
Пригонки |
Регулирования |
имозаменяемо- |
||
|
|
|
|
|
|
сти |
|
|
|
|
|
|
Регулирования |
Групповой вза- |
|
|
|
|
|
|
или групповой |
||
1 ∕ 3 ≤ Т ∕ ω |
< 2 ∕ 3 |
Пригонки |
имозаменяемо- |
||||
взаимозаменяе- |
|||||||
|
|
|
|
|
сти |
||
|
|
|
|
|
мости |
||
|
|
|
|
|
|
||
Т |
∕ ω |
< 1 ∕ 3 |
Пригонки и ре- |
Регулирования |
|||
гулирования |
|||||||
|
|
|
|
|
|
Если Т > ω , то для возможности сборки методом полной взаимозаменяемости необходимо уменьшить допуски составляющих звеньев. В большинстве случаев это нецелесообразно, так как удорожает изготовление деталей. После этого проверяют возможность применения метода неполной взаимозаменяемости. Для этого поле рассеяния замыкающего звена ω' и координата середины этого поля '0ωΔ определяются на основе вероятностного метода. Если ω' ≤ Т , то сборка методом неполной взаимозаменяемости возможна. Остаѐтся при необходимости сдвинуть координату середины поля рассеяния замыкающего звена.
Если ω' > Т , то для сборки методом неполной взаимозаменяемости необходимо уменьшить допуски составляющих звеньев или принять большую степень риска. При этом необходимо провести экономический расчѐт, так как и то, и другое приводит к повышению затрат на изготовление изделия:
при уменьшении допусков увеличиваются затраты на изготовление деталей;
при увеличении степени риска увеличиваются затраты на исправление брака при сборке изделия.
75
Если размерная цепь малозвенная (например, трѐхзвенная), а требуемую точность замыкающего звена нельзя обеспечить методом полной или неполной взаимозаменяемости даже при изготовлении собираемых деталей по 6-му квалитету точности, применяют метод групповой взаимозаменяемости, если размерная цепь многозвенная − метод пригонки или регулирования.
7.5. Выбор метода расчѐта размерной цепи
Размерные цепи можно рассчитывать следующими методами [7]:
методом максимума-минимума, при котором учитываются только предельные отклонения составляющих звеньев и самые неблагоприятные их сочетания;
вероятностным методом, при котором учитываются законы рассеяния размеров деталей и случайный характер их сочетания при сборке;
методом статистических испытаний, при котором моделируют случайные
значения звеньев.
При выборе метода расчѐта сборочной размерной цепи нужно исходить из конкретных условий для каждого случая (рис. 7.6).