
[ТМиП]metodichka_part1
.pdf
Описанное устройство лишь приближенно имитирует нагрузки, действующие на заготовку в процессе резания, так как оно не создает вертикальной и осевой составляющих силы резания и крутящего момента.
Статическая жесткость станков обычно в 1,2 – 1,4 раза выше, чем работающих станков, поэтому более достоверные данные о жесткости дает производственный метод. Производственный метод основан на обработке заготовки с переменным припуском и некоторых расчетах. Для испытания, например, токарного станка, берут достаточно жесткую заготовку, имеющую два пояска диаметрами D1 и D2 , (рис.4.11, a). Пояски обрабатываются за один рабочий ход (рис.11, б) при неизменных условиях (подаче, скорости и т. д.). Уступ д d1 d2 , образовавшийся вследствие разных глубин резания и отжатий в технологической системе, будет меньше з D1 D2 .
81
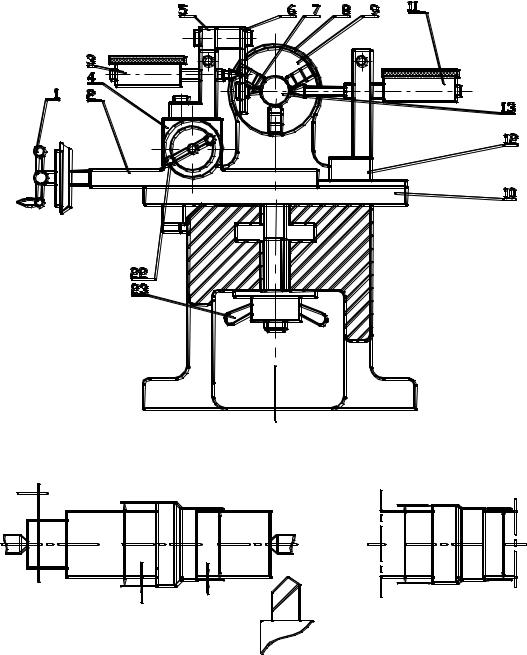
A-A |
Рис.4.10. Схема определения жесткости технологической системы
D1 |
t1
D1 |
t2 |
d1 |
d2 |
a) |
|
|
|
|
б) |
|
|
||||
Рис.4.11. Производственный метод определения жесткости станка |
|||||
Отношение З / д , называемое |
уточнением, показывает во |
сколько раз в результате обработки уменьшилась погрешность заготовки. Уточнение характеризует жесткость технологической системы
j CPz S 0,75 ,
где Pу / Pz ; С рZ - постоянный коэффициент, учитывающей условия обработки; S – подача, мм/об.
82
Метод пригоден для определения жесткости не только токарных, но и станков других типов. Например, жесткость фрезерного станка определяется после торцевого фрезерования ступенчатой заготовки за один рабочий ход.
Порядок выполнения работы
К выполнению экспериментальной части работы приступают после выполнения п.п. 2.1, 2.2 «Задач работы» и получения разрешения преподавателя.
1.Пользуясь торцевым ключом установить вал 13 (рис.4.10) в трехкулачковом патроне консольно. Длина зажимаемого кулачками участка вала 20 – 25 мм.
2.Отпустив гайку 23 установить суппорт 10 в положение, при котором наконечник 7 находится на расстоянии 40 – 50 мм от торца кулачка. Зафиксировать суппорт 10 гайкой 23, при этом планка 21 должна быть прижата к боковой поверхности направляющих 20. В начальном положении наконечник 7 не должен касаться вала и быть на одной линии с осью индикатора 11. При их несовпадении рукояткой 22 изменить положение наконечника вдоль оси вала в нужном направлении.
3.Линейкой измерить расстояние от наконечника 7 до торца кулачка. Для удобства отсчетов по индикаторам 3 и 11 их начальные показания установить на нуль.
4.Вращением рукоятки 1 по часовой стрелке переместить нагружающее устройства к оси вала 13, до момента, когда показания индикатора 3 будут равны 0,30 мм, что соответствует значению нормальной составляющей силы резания Py = 30 Н.
5.По индикатору 11 определить величину упругого перемещения вала 13 в данном сечении.
6.Вращением рукоятки 1 против часовой стрелки отвести наконечник 7 нагружающего устройства на расстояние 2…3 мм от вала 13.
7.Отпустив гайку 23 установить суппорт 10 в следующее положение (упругие перемещения вала определить еще в двух сечениях: посередине и вблизи его конца).
8.Рассчитать величину упругих перемещений вала в трех сечениях пользуясь формулой
83

y Рy x3i , 3EJ
где xi – расстояние от наконечника нагружающего устройства до торца кулачка.
9. Построить профили продольного сечения консольно закрепленного вала используя экспериментальные и теоретические данные. Определить вид отклонения профиля продольного сечения цилиндрической поверхности и его величину по формуле
|
dmax dmin |
dH 2 ymax dH 2 ymin y |
|
y |
|
, |
||
|
max |
min |
||||||
|
|
2 |
2 |
|
|
|||
|
|
|
|
|
|
|||
где dmax и dmin |
– |
максимальный и минимальный |
диаметры вала |
|||||
соответственно; dH |
– настроечный размер; ymax и ymin - максимальное и |
минимальное упругие перемещения вала.
10.Закрепить в трехкулачковый патрон 9 передний центр 24 (рис.
4.12, а).
11.Переместиться суппорт 10 к передней бабке 8 и закрепить его в положении, при котором расстояние от наконечника 7 до торца кулачка составляет 5 – 10 мм.
12.Переместить нагружающее устройство к оси центра до момента, когда показания индикатора 3 станут, равны 0,9 мм, что соответствует значению нормальной составляющей силы резания Py =80 Н. По
индикатору 11 определить величину смещения передней бабки 8 у переднего центра.
84

а) б)
Рис.4.12 Схемы измерения величины упругого перемещения передней (а) и задней (б) бабок.
13. Рассчитать жесткость передней бабки, измеренную на переднем центре
jп.ц Рy . yп.ц
14.Переместить суппорт 10 к задней бабке 19 и аналогичным образом определить величину смещения задней бабки 19 у заднего центра 14 (рис.4.12, б).
15.Рассчитать жесткость задней бабки, измеренную на заднем центре
jз.ц Ру . yз.ц
16. Установить вал 13 в центрах и измерить его упругие перемещения при Py = 80 Н в трех сечениях: на расстоянии 10 – 15 мм от левого торца, посередине и на расстоянии 10 -15 мм от правого торца.
17.Рассчитать величину упругих перемещений вала в трех сечениях с учетом упругих перемещений центров станка пользуясь формулой (4.13). Деформации суппорта и резца не влияют на погрешности профиля продольного сечения и при расчете их не учитывать.
18.Построить профили продольного сечения вала закрепленного в центрах используя экспериментальные и теоретические данные. Определить вид отклонения профиля продольного сечения цилиндрической поверхности и его величину.
85
Содержание отчета
1.Цели и задачи работы.
2.Результаты измерения величины упругих перемещений консольно закрепленного вала вызванных силой Py .
3.Результаты расчета величины упругих перемещений консольно закрепленного вала.
4.Профили продольного сечения консольно закрепленного вала.
5.Схемы и результаты измерения величины упругого перемещения передней и задней бабок.
6.Результаты расчета жесткости передней и задней бабок.
7.Результаты измерений и расчета величины упругих перемещений вала установленного в центрах.
8.Профили продольного сечения вала, установленного в центрах.
9.Выводы.
Контрольные вопросы
1.Каким образом неравномерный припуск и различие твердости материала заготовок влияет на точность и производительность обработки?
2.Жесткость и податливость технологической системы.
3.Объясните причины копирования формы поверхности заготовки на обработанную деталь.
4.Что такое уточнение и что оно показывает?
5.Из каких величин складывается упругое перемещение в технологической системе под воздействием силы резания?
6.Как определяется приведенный диаметр ступенчатых валов?
7.Каковы пути повышения жесткости технологической системы?
8.Назовите методы определения жесткости технологической системы
идайте им характеристику.
Литература
1.Колесов И.М. Основа технологии машиностроения: Учебник для машиностроит. специальных вузов. – М.: Высшая шк., 1999. – 591с.: ил. –
С. 331 – 349.
2.Технология машиностроения: В 2т. Т.1. Основы технологии машиностроения: Учебник для вузов/В.М. Бурцев, А.С. Васильев, А.М. Дальский и др.; Под редакцией А.М. Дальского. – М.: Издательство МГТУ им. Н.Э. Баумана, 1999. – 564с.: ил. – С. 117 – 127.
86
Лабораторная работа № 5
ВЛИЯНИЕ РАЗМЕРНОГО ИЗНОСА РЕЖУЩЕГО ИНСТРУМЕНТА НА ТОЧНОСТЬ ОБРАБОТКИ
Цель работы: Изучения видов изнашивания режущих инструментов; погрешностей, возникающих в результате размерного износа режущих инструментов и определение периодичности поднастройки инструмента для различных методов обработки.
ЗАДАЧИ РАБОТЫ
1. Определить влияние размерного износа инструмента на точность обработки партии заготовок.
2 Рассчитать периодичность поднастройки инструмента.
3. Инструмент, материалы и принадлежности
1 Микроскоп инструментальный БМИ-1 - 1 шт. 2 Штангенциркуль ШЦ – П ГОСТ 166-80 – 1 шт. 3 Комплект режущего инструмента – 1 шт.
Теоретическая часть
Влияние размерного износа на точность обработки
Интенсивный размерный износ режущего инструмента существенно влияет на точность деталей. Очень важным для практики обработки является исследование процессов деформирования и разрушение режущей части инструментов. В результате многочисленных исследований процесса резания установлено, что при взаимодействии инструмента и обрабатываемого материала в результате изнашивания на передней поверхности режущего лезвия образуется “лунка”, а на задней поверхности - “площадка”. Изнашивание происходит при резании любых материалов и при различных режимах обработки. В зависимости от условий резания и свойств материалов (обрабатываемого и инструментального) наибольшую интенсивность изнашивания может претерпевать передняя или задняя поверхность инструмента (Рис. 5.1 а, б). При одновременном изнашивании по передней поверхности фаска f (Рис. 5.1.в) уменьшается и происходит разрушение режущей кромки.
87

а) |
б) |
в) |
Рис 5.1 Характер изнашивания режущего лезвия:
а) изнашивание только по передней поверхности (lg; hл-длина и глубина лунки)
б) изнашивание только по задней поверхности ( hз-длина площадки) в) изнашивание одновременно по задней и передней поверхности (f-
фаска)
На |
основании |
исследований, |
появилась |
возможность |
|
систематизировать различные виды изнашивания |
и |
объяснить их |
|||
физическую природу: |
|
|
|
|
|
а) Абразивное изнашивание инструмента |
происходит путем |
||||
царапания и истирания |
отдельных поверхностей инструмента твердыми |
включениями, находящимися в обрабатываемом материале. Отделение частичек материала осуществляется путем микро резания, глубинного вырывания и поверхностного деформирования, приводящего к разрыхлению поверхностных слоев.
б) Адгезионное |
изнашивание |
связано с |
молекулярным |
|
взаимодействием |
поверхностных слоев |
режущего |
инструмента и |
обрабатываемого материала. Наличие в области контакта чистого трения значительно активизирует адгезионный износ (схватывание, прилипание, холодная сварка). При движении деформированного материала все время происходит процесс разрушения и возникновение “мостиков сварки” и адгезионных пятен на поверхности режущего клина. Частицы материала вырываются с поверхности инструмента и уносятся со стружкой.
88

в) |
Диффузионное |
растворение |
обрабатываемого |
и |
инструментального материала |
при резании |
на высоких скоростях |
при |
больших контактных температурах и давлениях.
Диффузионное растворение приводит к разрушению тонких поверхностных слоев режущего инструмента и на передней поверхности образуется лунка. В условиях активного охлаждения зоны резания и газонасыщения контактных слоев возможно также наличие абразивнохимического износа (“окислительный”, “коррозионный” износ).
Для количественной оценки величины износа инструмента существуют различные методы:
а) Измерение линейных размеров следов износа на передней и задней поверхностях инструмента, а также определение объема и веса удаленного металла;
б) Косвенные методы оценки величины износа, связанные с увеличением шероховатости обработанной поверхности, увеличением размеров изделия (“размерный износ”), увеличением сил резания и
температуры резания; |
|
|
|
|
в) Метод |
радиоактивных |
изотопов |
путем |
измерения |
радиоактивности стружки (сложность оборудование и необходимость тщательного соблюдения техники безопасности снижают возможности применения этого метода).
При размерном износе инструмента его режущая кромка занимает новое положение, вызывая погрешность обработки. В зависимости от конкретных условий обработки, режущая кромка может округляться, выкрашиваться, скалываться. Этот процесс протекает непрерывно в течении всего периода стойкости ин6струмента.
И,мкм
|
|
|
|
|
|
|
|
|
|
|
|
|
|
|
|
|
|
III |
||
|
a |
|
|
|
|
|
|
|
|
|
|
|
|
|
|
|
|
|
а |
|
|
|
|
|
|
|
|
|
|
|
|
|
|
|
|
|
|
||||
|
|
|
|
|
|
|
|
|
|
|
|
|
II |
|
|
|
|
|||
Ин |
I |
|
|
|
|
|
|
|
|
|||||||||||
|
|
|
|
|
|
|
|
|
|
|
|
|||||||||
|
|
|
|
|
|
|
|
|
|
|
|
|
|
|
|
|
||||
|
|
|
|
|
|
|
|
|
|
|
|
|
|
|
|
|
|
|
L, м |
|
|
|
|
|
L1 |
|
|
|
|
|
|
L2 |
|
|
|
|
L3 |
||||
|
|
|
|
|
|
|
|
|
|
|
|
|
|
|||||||
|
|
|
|
|
|
|
|
|
|
|
|
|
|
|
|
|
|
|
|
|
Рис 5.2 Кривая изнашивания режущего инструмента.
89
В очень многих случаях зависимость износа И от пути L резания представляется кривой, показанной на рис. 5.2. Такая кривая меняет три участка. При прохождении в относительном движении сравнительно небольшого пути L1 инструмент изнашивается наиболее интенсивно (зона I). Это происходит в связи с быстрым износом микронеровностей инструмента, оставшихся после затачивания. В начале работы поверхности инструмента прирабатываются, и несколько округляется режущая кромка. Постепенно величина износа достигает определенного значения, допустимого без ухудшения шероховатости и точности обработки (зона
II).
На пути резания L2 изменяется по линейному закону. Дальнейшая работа приводит к резкому возрастанию износа по задней и передней поверхности и разрушению режущего лезвия(III зона – “катастрофического” износа). Если не допускать работу инструмента в зоне III, то срок его службы значительно увеличится.
Интенсивность размерного износа Иo определяют на линейном участке пути резания;
Иo=И2/L2 (5.1)
где И2 – износ инструмента на участке L2. Интенсивность размерного износа называют относительным.
Для того, чтобы учесть износ инструмента в зоне I, принимают следующее положение. Линейный участок кривой изнашивания (зона II) условно увеличивают, проводя линию аа’. Тогда на оси ординат отсекается участок Ин, называемый начальным износом, который также оценивается в микрометрах. Размерный износ с достаточной степенью точности для пути резания L можно определить по формуле:
н=Ин+И0 L/106 (5.2)
Формула 5.2 может быть трансформирована: для различных методов обработки, для продольного точения
н=Ин+Иo·( ·п·d·L)/106 ·S (5.3)
где d - диаметр заготовки, l-длина обрабатываемой поверхности, S-подача.
Для строгания
н=Ин+Иo·(L·B)/106 ·S ( 5.4)
90